Procuring Single-Use Injection Equipment and Safety Boxes
Total Page:16
File Type:pdf, Size:1020Kb
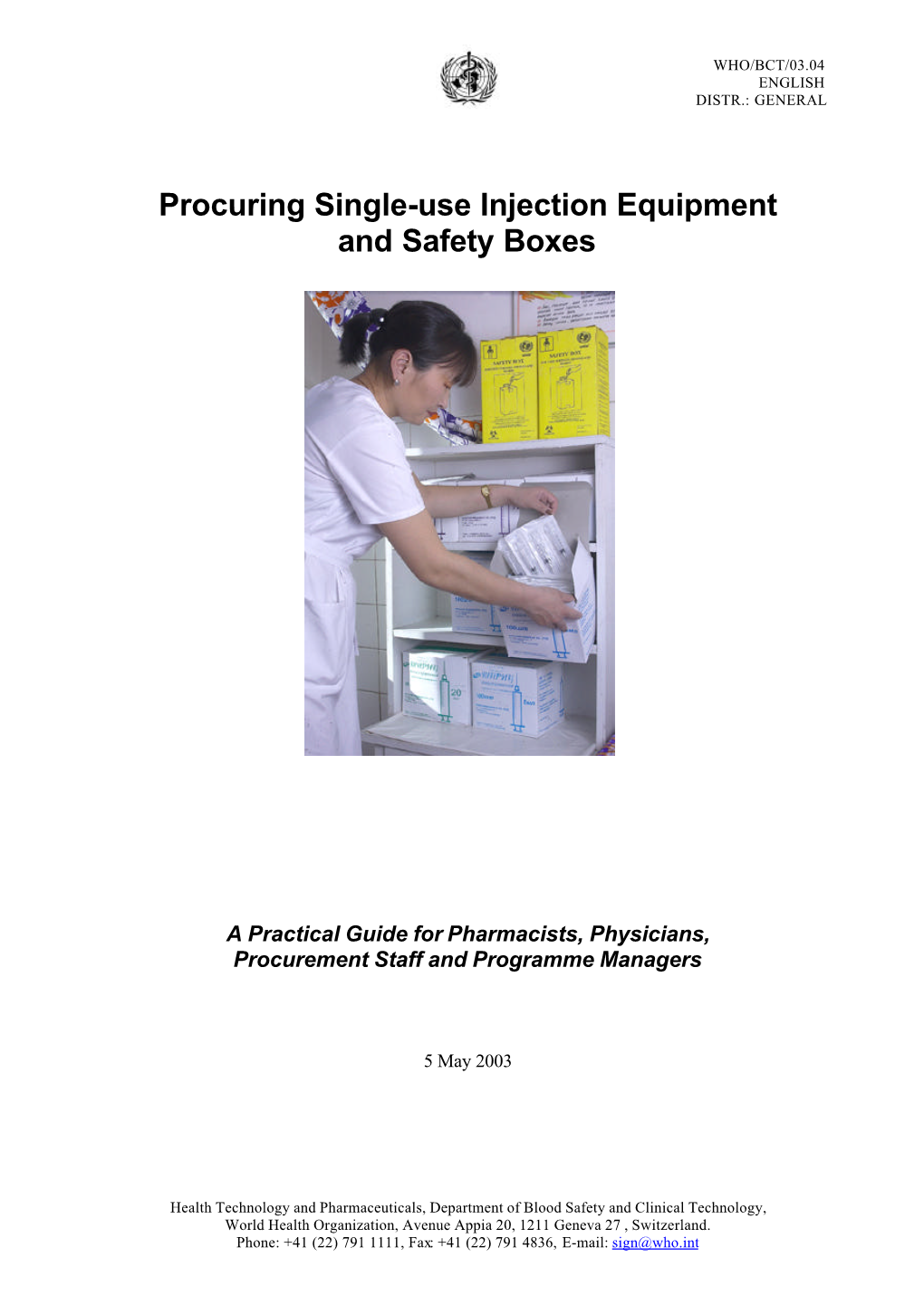
Load more
Recommended publications
-
Infection Prevention Policy Safe Use, Handling and Disposal of Sharps
Infection Prevention Policy Safe Use, Handling and Disposal of Sharps Author: Anne Tateson (Infection Prevention Nurse) Owner: Vicki Parkin Publisher: Compliance Unit Date of first issue: March 2010 Version: 3 Date of version issue: February 2012 Approved by: HIPCC Date approved: February 2012 Review date: February 2015 Target audience: All Trust staff Relevant Regulations and Standards Executive Summary This policy aims to provide all trust staff with the relevant information about the safe use, handling and disposal of sharps. Safe Use, Handling and Disposal of Sharps Version Number: 3 Issue Date: February 2012 0 Version History Log Version Date Version Status & Details of significant Approved Author location changes 1 Jane Infection Balderson Prevention audit & surveillance Nurse 2 Jane Infection Appendix 1 added Balderson Prevention Audit & Surveillance Nurse 3 Anne Infection Appendix amended Tateson Prevention A,B,C,D,E,F. Nurse Removal of Appendix 1 Safe Use, Handling and Disposal of Sharps. Version Number: 3 Issue Date: February 2012 Page 1 of 19 Contents Number Heading Page 1 Introduction & Scope 3 2 Definitions / Terms used in policy 3 3 Policy Statement 4 4 Equality Impact Assessment 4 5 Accountability 5 Consultation, Assurance and Approval 6 5 Process 7 Review and Revision Arrangements 5 8 Dissemination and Implementation 6 8.1 Dissemination 6 8.2 Implementation of Policies 6 9 Document Control including Archiving 6 10 Monitoring Compliance and Effectiveness 6 Process for Monitoring Compliance and 10.1 6 Effectiveness 10.2 Standards/Key Performance Indicators 7 11 Training 8 12 Trust Associated Documentation 8 13 External References 8 14 Appendices 9 Safe Use, Handling and Disposal of Sharps. -
Training Health Workers in the Management of Sharps Waste
Training Health Workers in the Management of Sharps Waste Guide for Training of Waste Handlers Contents 1. Training Overview................................................................................................................43 2. Sharps Waste Overview........................................................................................................45 3. Health Worker Safety ...........................................................................................................48 4. Segregation of Waste ............................................................................................................51 5. Handling, Storage, and Transport of Safety Boxes...............................................................56 6. Overview of Sharps Treatment, Destruction, and Disposal..................................................58 7. Treatment of Sharps: Liquid Disinfection ............................................................................60 8. Treatment of Sharps: Autoclave/Shredding..........................................................................62 9. Treatment of Sharps: Encapsulation .....................................................................................66 10. Treatment and Destruction of Sharps: Incineration..............................................................68 11. Disposal of Removed Needles: Protected Sharps Pit ...........................................................73 12. Disposal of Removed Needles: Protected Sharps Barrel......................................................78 -
Needle Remover Technical Overview
Needle Remover Technical Overview Background Each year, more than 16 billion injections are administered worldwide.1 In some regions, 17 percent to 75 percent are estimated to be with reused, unsterilized injection equipment.2 Unsafe reuse of syringes is estimated to cause 20 million hepatitis B infections, 2 million hepatitis C infections, and 250,000 HIV infections annually.3 The main tools to prevent reuse of unsterile syringes and needles are safety syringes such as autodisable and retractable devices. However, most syringes currently in use do not prevent reuse and therefore, safe, appropriate disposal of sharps and syringe waste plays a critical role in safe injection and reuse prevention. World Health Organization (WHO) guidelines recommend disposal of used syringes and needles in cardboard safety boxes. These safety boxes must then be further treated for disposal, for example, by burial, incineration, or autoclaving and shredding. In developing countries, where reuse is most prevalent, policies and practices regarding safe disposal of sharps waste are inadequate. Safe injection is impaired by the lack of policies about disposal of sharps, lack of appropriate equipment, and lack of Figure 1. A busy immunization session in India evidence of cost-effective systems. Currently, in most areas of the developing world, sharps waste is dangerous to the community, and health care workers and waste handlers are not protected from hazardous sharps when collecting, storing, transporting, or disposing of sharps waste. 4,,5 6 Several needle removal technologies exist that are designed to disable syringes immediately after the injection. These include devices requiring battery or electric power and others that are manually operated. -
Infection Prevention Guidelines Safe Use, Handling & Disposal of Sharps
Infection Prevention Guidelines Safe Use, Handling & Disposal of Sharps Author: Anne Tateson Owner: Infection Prevention Team Publisher: Infection Prevention Date of Version Issue: February 2015 Version: 4 Review date: February 2018 Summary This guideline aims to provide all Trust Staff with the relevant information about the safe use, handling and disposal of sharps. Safe Use, Handling & Disposal of Sharps Version Number: 4 Issue Date: February 2015 Contents Number Heading Page 1 Introduction & Scope 2 2 Definitions 2 3 Overview 3 4 Trust Associated Documentation 4 5 External References 4 6 Appendices 5 Safe Use, Handling & Disposal of Sharps. Version Number: 4 Issue Date: February 2015 Page 1 of 9 1 Introduction & Scope This guideline applies to all Trust Staff. It addresses the requirements of the Trust in relation to the Health and Social Care Act 2008 criterion 8 regarding safe handling and disposal of sharps including: • Assembling, storage and disposal of sharps bins • Preventing sharps’ injuries Needlestick and injury from a sharp object can occur in clinical and non clinical settings. They are avoidable when good practice and procedure are employed during the handling and disposal of sharps. For the management of sharps’ injuries refer to the Occupational Health Policy ‘Needlestick/ Accidental Contamination’ policy. 2 Definitions Sharps – Any object that has an edge or point that could penetrate, puncture or lacerate skin. This includes needles, broken glass, surgical instruments, scalpels and body parts such as broken bones and teeth. Sharps can be clean or contaminated with blood or body fluid. Sharps Injury – When sharps penetrate the skin. Needlestick Injury – Where the sharps injury is caused by hollow bore or solid needle. -
Reducing the Risk of Injuries to Staff from Insulin Pens
CLINICAL DEVELOPMENT Reducing the risk of injuries to staff from insulin pens author Carmel Edwards, MA, RGN, SEN, is sen- associated with the use of insulin pen devices be- ior infection control nurse; Lesley Metcalfe BSc, tween 1 February 2003 and 31 January 2004. Out RGN, is diabetes specialist nurse and clinical risk of 80 sharps injuries to staff, 15 were related to the adviser; Joe Allan, BSc, RN, DipHE, is infection control use of insulin pen devices (Tables 1 and 2). nurse; Andre Haynes, Dip Occupational Health The infection control nurses (ICNs) were unfamil- and Safety and Environmental Management, iar with insulin pen devices and decided that fur- is health and safety adviser; all at Wirral Hospital ther investigation was necessary. They were con- NHS Trust, Merseyside. cerned that when patients were unable to abstract Edwards, C. et al (2005) Reducing administer their insulin this procedure was under- the risk to staff from insulin pens. Nursing Times; taken by health care workers who then had to dis- 101: 25, 34–36. pose of the needle. This article describes problems in the use and The consequences of patients receiving a needle- disposal of sharps used in the administration of stick injury from their own devices are not signifi- insulin therapy in a hospital setting. Subsequent cant. However, health care workers may be at risk investigation and action taken to reduce the risk of developing BBV following an injury from a of needlestick injuries in staff who administer contaminated needle. insulin therapy with an insulin pen delivery sys- Staff reported that injuries were often sustained tem are also discussed. -
A Healthtech Report
A HealthTech Report Evaluation of a Disposable Needle-Removal Device in Uganda September 2005 Contact: Nancy Muller PATH 1455 NW Leary Way Seattle, WA 98107-5136 USA Tel: 206.285.3500 Fax: 206.285.6619 www.path.org PATH October 2005 Table of Contents Executive Summary ................................................................................................iii Introduction ..............................................................................................................1 Background ............................................................................................................1 Strategy ..................................................................................................................2 Methods ....................................................................................................................2 Goals and Objectives..............................................................................................2 Study Materials.......................................................................................................3 Study Design ..........................................................................................................3 Participants.............................................................................................................4 Training...................................................................................................................4 Monitoring and Data Collection ..............................................................................5 -
Training Health Workers in the Management of Sharps Waste
Training Manual Training Health Workers in the Management of Sharps Waste Version 1 October 2005 1455 NW Leary Way Seattle, WA 98107-5136 USA Tel: 206.285.3500 Fax: 206.285.6619 www.path.org Training Health Workers in the Management of Sharps Waste Acknowledgements and Copyright These materials were developed at PATH with support from the US Agency for International Development (USAID) HealthTech program under Cooperative Agreement #GPH-A-00-01- 00005-00 and the Making Medical Injections Safer Project. The opinions expressed herein are those of the authors and do not necessarily reflect the views of USAID. Copyright © 2005, Program for Appropriate Technology in Health (PATH). All rights reserved. The material in this document may be freely used and adapted for educational or noncommercial purposes, provided that the material is accompanied by an acknowledgement line. Suggested citation: PATH. Training Health Workers in the Management of Sharps Waste. Version 1. Seattle: PATH; 2005. For more information contact: Program for Appropriate Technology in Health (PATH) 1455 NW Leary Way Seattle, WA 98107-5136 USA Phone: 206-285-3500 Fax: 206-285-6619 Email: [email protected] Web: http://www.path.org Version 1 PATH October 2005 iii Training Health Workers in the Management of Sharps Waste Table of Contents Guide for Facilitation 1. Description of Training Materials...........................................................................................3 2. Adaptation...............................................................................................................................5 -
Development of a Community Sharps Collection Pilot Program for the Town of Northampton, Massachusetts: a Review of the Barriers
Rochester Institute of Technology RIT Scholar Works Theses 2007 Development of a community sharps collection pilot program for the town of Northampton, Massachusetts: a review of the barriers Carmela (Deb) Laino Follow this and additional works at: https://scholarworks.rit.edu/theses Recommended Citation Laino, Carmela (Deb), "Development of a community sharps collection pilot program for the town of Northampton, Massachusetts: a review of the barriers" (2007). Thesis. Rochester Institute of Technology. Accessed from This Thesis is brought to you for free and open access by RIT Scholar Works. It has been accepted for inclusion in Theses by an authorized administrator of RIT Scholar Works. For more information, please contact [email protected]. Thesis: Development of a Community Sharps Collection Pilot Program for the Town of Northampton, Massachusetts: A Review of the Barriers Carmela (Deb) Laino November 1, 2007 Department of Civil Engineering Technology Environmental Management & Safety Rochester Institute of Technology Rochester, NY Thesis submitted in partial fulfillment of the requirements of the degree of Master of Science in Environmental, Health and Safety Management Approved by: _______________________________________ ____________ Department EH&S Management Program Chair Date _______________________________________ ____________ Dr. Jennifer Schneider, CIH Date Thesis Permissions Page • Print Reproduction Permission Denied I, Carmela (Deb) Laino, hereby give permission to the Wallace Library of the Rochester Institute of Technology to reproduce my print thesis or dissertation in whole or in part. Signature of Author: Date: 2 Inclusion in the RIT Digital Media Library Electronic Thesis & Dissertation (ETD) Archive I, Carmela (Deb) Laino, additionally grant to the Rochester Institute of Technology Digital Media Library (RIT DML) the non exclusive license to archive and provide electronic access to my thesis or dissertation in whole or in part in all forms of media in perpetuity. -
Evaluation of Injection Safety and Health Care Waste Management in Nigeria
EVALUATION OF INJECTION SAFETY AND HEALTH CARE WASTE MANAGEMENT IN NIGERIA 2009 COMPARISON REPORT SEPTEMBER 2009 This publication was produced for review by the United States Agency for International Development. It was prepared by the Making Medical Injections Safer (MMIS) project. Acknowledgements The MMIS team is grateful to the Federal Ministry of Health (FMOH) for their permission and cooperation during the time of data collection and to the management of the health centers involved in this assessment for allowing the data collectors access to their facilities and staff. Special thanks go to the MMIS/Nigeria team under the leadership of Dr. Abimbola Sowande, MMIS/Nigeria Country Director, for their participation in training, supervision, and logistical coordination. A very big thank you to the local consultants who served as study coordinators—Taiwo Adekanmbi and Toyin Akpan and to the teams of data collectors. Additional thank you to Ms. Karen Van Roekel, Senior Monitoring and Evaluation Advisor, for serving as Principal Investigator for this study as well as other staff from MMIS/HQ, Ms. Deepa Bhat Shanadi, Monitoring and Evaluation Consultant; Mr. Ethan Collins, M&E Advisor; Ms. Megan Noel, M&E Technical Officer; and Dr. Iqbal Hossain, MMIS Technical Officer,. MMIS thanks USAID and the President’s Emergency Plan for AIDS Relief whose financial support has made the survey and the MMIS interventions in Nigeria possible. This study would not have been possible without the participants who provided the information upon which the report is based. Our gratitude goes to all the service providers, supervisors, waste handlers, and patients. Assessment Team Members 2005 Data collectors Data collectors Data collectors Lagos Kano FCT Dr. -
Biosafety in Microbiological and Biomedical Laboratories—6Th Edition
Biosafety in Microbiological and Biomedical Laboratories 6th Edition Centers for Disease Control and Prevention National Institutes of Health Inside front cover Biosafety in Microbiological and Biomedical Laboratories 6th Edition U.S. Department of Health and Human Services Public Health Service Centers for Disease Control and Prevention National Institutes of Health Revised June 2020 Foreword Biosafety in Microbiological and Biomedical Laboratories (BMBL) has served as the cornerstone of biosafety practice in the United States since its initial release. We wish to emphasize that the sixth edition of BMBL remains an advisory document recommending best practices for the safe conduct of work in biomedical and clinical laboratories from a biosafety perspective. The BMBL is not intended to be a regulatory document although we recognize that some may use it in that way. The core principle of this document is protocol-driven risk assessment; it is not possible for a single document to identify all of the possible combinations of risks and mitigations feasible in biomedical and clinical labora- tories. The BMBL should be used as a tool in the assessment and proposed mitigation steps in biomedical and clinical laboratories. This edition of BMBL includes revised sections, agent summary statements, and appendices. We harmonized the recommendations included in this edition with guidance issued and regulations promulgated by other organizations and federal agencies. Wherever possible, we clarified both the language and intent of the information provided. In order to serve the needs of our community better, this edition includes new appendices on the following topics: inactivation and verification; laboratory sustainability; large-scale biosafety; and clinical laboratory biosafety. -
Safe Management of Wastes from Health-Care Activities
Safe management of wastes from health-care activities Second edition Edited by Yves Chartier, Jorge Emmanuel, Ute Pieper, Annette Prüss, Philip Rushbrook, Ruth Stringer, William Townend, Susan Wilburn and Raki Zghondi Safe management of wastes from health-care activities 2nd edition WHO Library Cataloguing-in-Publication Data Safe management of wastes from health-care activities / edited by Y. Chartier et al. – 2nd ed. 1.Medical waste. 2.Waste management. 3.Medical waste disposal – methods. 4.Safety management. 5.Handbook. I.Chartier, Yves. II.Emmanuel, Jorge. III.Pieper, Ute. IV.Prüss, Annette. V. Ru s h b r o o k , Philip. VI.Stringer, Ruth. VII.Townend, William. VIII.Wilburn, Susan. IX.Zghondi, Raki. X.World Health Organization. ISBN 978 92 4 154856 4 (NLM classification: WA 790) © World Health Organization 2014 All rights reserved. Publications of the World Health Organization (WHO) are available on the WHO web site (www.who.int) or can be purchased from WHO Press, World Health Organization, 20 Avenue Appia, 1211 Geneva 27, Switzerland (tel.: +41 22 791 3264; fax: +41 22 791 4857; e-mail: [email protected]). Requests for permission to reproduce or translate WHO publications –whether for sale or for non-commercial distribution– should be addressed to WHO Press through the WHO web site (www.who.int/about/licensing/copyright_form/en/index.html). The designations employed and the presentation of the material in this publication do not imply the expression of any opinion whatsoever on the part of the WHO concerning the legal status of any country, territory, city or area or of its authorities, or concerning the delimitation of its frontiers or boundaries. -
Revised Injection Safety Assessment Tool (Tool C – Revised) W O R L D H E a L T H O R G a N I Z a T I O N
REVISED INJECTION SAFETY ASSESSMENT TOOL (TOOL C – REVISED) W O R L D H E A L T H O R G A N I Z A T I O N WHO/EHT/08.08 REVISED INJECTION SAFETY ASSESSMENT TOOL (TOOL C – REVISED) Tool for the Assessment of Injection Safety and the Safety of Phlebotomy, Lancet Procedures, Intravenous Injections and Infusions World Health Organization © World Health Organization 2008 All rights reserved. Publications of the World Health Organization can be obtained from WHO Press, World Health Organization, 20 Avenue Appia, 1211 Geneva 27, Switzerland (tel.: +41 22 791 3264; fax: +41 22 791 4857; e-mail: [email protected]). Requests for permission to reproduce or translate WHO publications – whether for sale or for noncommercial distribution – should be addressed to WHO Press, at the above address (fax: +41 22 791 4806; e-mail: [email protected]). The designations employed and the presentation of the material in this publication do not imply the expression of any opinion whatsoever on the part of the World Health Organization concerning the legal status of any country, territory, city or area or of its authorities, or concerning the delimitation of its frontiers or boundaries. Dotted lines on maps represent approximate border lines for which there may not yet be full agreement. The mention of specific companies or of certain manufacturers’ products does not imply that they are endorsed or recommended by the World Health Organization in preference to others of a similar nature that are not mentioned. Errors and omissions excepted, the names of proprietary products are distinguished by initial capital letters.