Best Management Practices (Bmps) for Soils Treatment Technologies
Total Page:16
File Type:pdf, Size:1020Kb
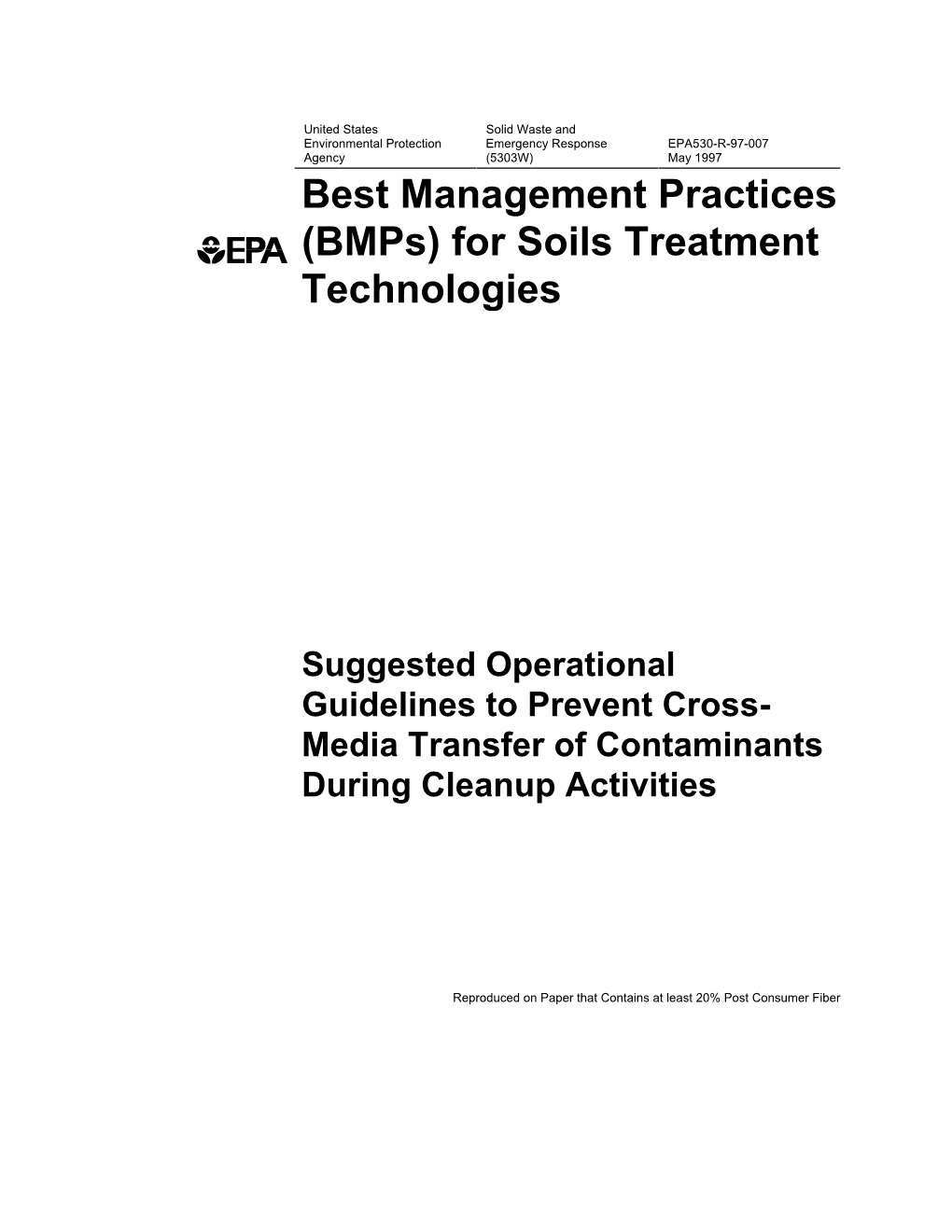
Load more
Recommended publications
-
Keynote: Soil Conservation for C Sequestration R
This paper was not peer-reviewed. Pages 459-465. In: D.E. Stott, R.H. Mohtar and G.C. Steinhardt (eds). 2001. Sustaining the Global Farm. Selected papers from the 10th International Soil Conservation Organization Meeting held May 24-29, 1999 at Purdue University and the USDA-ARS National Soil Erosion Research Laboratory. Keynote: Soil Conservation For C Sequestration R. Lal* ABSTRACT fragile ecosystems such as the Himalyan-Tibean ecoregion, The atmospheric concentration of greenhouse gases the Andeas, the West African Sahel, East African Highlands, (GHG) is increasing at the rate of 0.5% yr-1 (3.2 Pg C and the Caribbean region (Scherr and Yadav, 1995; Scherr, -1 -1 -1 yr ) for CO2, 0.6% yr for CH4 and 0.25 ppbv yr for 1999). In addition to effects on productivity, soil erosion N2O. The global radiative forcing due to three GHGs is also profoundly impacts the environment. contributed by 20% due to agricultural activities and Two principal impacts of erosion on environment include 14% to change in land use and attendant deforestation. reduction in quality of water and air through pollution and Principal agricultural activities that contribute to eutrophication of surface water, and emissions of emission of GHGs include plowing, application of radioactively-active gases (e.g., CO2, CH4 and N2O) to the fertilizers and manures, soil drainage, biomass burning, atmosphere. Increasing atmospheric concentration of -1 -1 residue removal. The loss of soil C is accentuated by soil radioactively-active gases (0.5% yr for CO2, 0.6% yr for -1 degradation (due to erosion, compaction, salinization CH4, 0.25% yr for N2O) (IPCC, 1995) necessitates etc.) and the attendant decline in soil quality. -
Vision 2030 Maharashtra
Overview of the State ………………………………………………………….. 01 Demographic Profile ……………………………………………………………….. 03 State Economy ………………………………………………………………………. 04 Key Challenges ……………………………………………………………………... 08 Way forward ……………………………………………………………………. 13 Core five pillars (themes) of Vision 2030 …………………………………………… 15 Vision Statement & Components …………………………………………... 17 Agriculture & Allied activities Current Scenario …………………………………………………………………… 21 Vision Elements and Targets ………………………………………………………. 26 Action Points ………………………………………………………………………. 30 Industry & Services Current Scenario ……………………………………………………………………. 47 Vision Elements and Targets ……………………………………………………….. 50 Action Points ……………………………………………………………………... 52 Infrastructure Current Scenario ………………………………………………………………….. 62 Vision Elements and Targets ……………………………………………………... 65 Action Points ………………………………………………………………………. 68 Social Sectors Current Scenario ..…………………………………………………………………. 74 Vision Elements and Targets ……………………………………………………… 84 Action Points ……………………………………………………………………… 92 Governance Current Scenario …………………………………………………………………… 113 Vision Elements and Targets ……………………………………………………… 117 Action Points ……………………………………………………………………… 123 Environment Current Scenario …………………………………………………………………… 128 Vision Elements and Targets ……………………………………………………… 129 Action Points ……………………………………………………………………… 130 Implementation Strategy……………………………………………………….. 131 OVERVIEW OF THE STATE Maharashtra occupies the western and central part of the country and has a long coastline stretching nearly 720 km along the Arabian Sea. The -
Evaluating Vapor Intrusion Pathways
Evaluating Vapor Intrusion Pathways Guidance for ATSDR’s Division of Community Health Investigations October 31, 2016 Contents Acronym List ........................................................................................................................................................................... 1 Introduction ........................................................................................................................................................................... 2 What are the potential health risks from the vapor intrusion pathway? ............................................................................... 2 When should a vapor intrusion pathway be evaluated? ........................................................................................................ 3 Why is it so difficult to assess the public health hazard posed by the vapor intrusion pathway? .......................................... 3 What is the best approach for a public health evaluation of the vapor intrusion pathway? ................................................. 5 Public health evaluation.......................................................................................................................................................... 5 Vapor intrusion evaluation process outline ............................................................................................................................ 8 References… …...................................................................................................................................................................... -
Soil Contamination and Human Health: a Major Challenge For
Soil contamination and human health : A major challenge for global soil security Florence Carre, Julien Caudeville, Roseline Bonnard, Valérie Bert, Pierre Boucard, Martine Ramel To cite this version: Florence Carre, Julien Caudeville, Roseline Bonnard, Valérie Bert, Pierre Boucard, et al.. Soil con- tamination and human health : A major challenge for global soil security. Global Soil Security Sympo- sium, May 2015, College Station, United States. pp.275-295, 10.1007/978-3-319-43394-3_25. ineris- 01864711 HAL Id: ineris-01864711 https://hal-ineris.archives-ouvertes.fr/ineris-01864711 Submitted on 30 Aug 2018 HAL is a multi-disciplinary open access L’archive ouverte pluridisciplinaire HAL, est archive for the deposit and dissemination of sci- destinée au dépôt et à la diffusion de documents entific research documents, whether they are pub- scientifiques de niveau recherche, publiés ou non, lished or not. The documents may come from émanant des établissements d’enseignement et de teaching and research institutions in France or recherche français ou étrangers, des laboratoires abroad, or from public or private research centers. publics ou privés. Human Health as another major challenge of Global Soil Security Florence Carré, Julien Caudeville, Roseline Bonnard, Valérie Bert, Pierre Boucard, Martine Ramel Abstract This chapter aimed to demonstrate, by several illustrated examples, that Human Health should be considered as another major challenge of global soil security by emphasizing the fact that (a) soil contamination is a worldwide issue, estimations can be done based on local contamination but the extent and content of diffuse contamination is largely unknown; (b) although soil is able to store, filter and reduce contamination, it can also transform and make accessible soil contaminants and their metabolites, contributing then to human health impacts. -
Contaminated Soil in Gardens
Contaminated Soil in Gardens How to avoid the harmful effects EUR/ICP/LVNG 03 01 02(A) E64737 EUROPEAN HEALTH21 TARGET 11 HEALTHIER LIVING By the year 2015, people across society should have adopted healthier patterns of living (Adopted by the WHO Regional Committee for Europe at its forty-eighth session, Copenhagen, September 1998) Abstract In many cities, gardens are located on old, abandoned landfills and dumping sites. Cities have expanded by filling up spaces around the city with garbage, rubble and earth. The places where old landfills were have often become gardens where citizens can get away and enjoy the open air away from the noise and racket of cities. Normal garbage and rubble in landfills do not present a problem, however industrial and chemical waste can present a health hazard, especially when concentrations of contaminants are above acceptable limits. Some special precautions are proposed in this booklet so that the potential ill effects of contaminated soil can be avoided. Keywords SOIL POLLUTANTS RISK MANAGEMENT GUIDELINES URBAN HEALTH Contents The soil is contaminated – what then? .......................................................1 What is in the ground under us?.................................................................2 How harmful substances may affect the body ............................................3 How to reduce the risk................................................................................4 The best way to garden..............................................................................5 -
Agricultural Soil Compaction: Causes and Management
October 2010 Agdex 510-1 Agricultural Soil Compaction: Causes and Management oil compaction can be a serious and unnecessary soil aggregates, which has a negative affect on soil S form of soil degradation that can result in increased aggregate structure. soil erosion and decreased crop production. Soil compaction can have a number of negative effects on Compaction of soil is the compression of soil particles into soil quality and crop production including the following: a smaller volume, which reduces the size of pore space available for air and water. Most soils are composed of • causes soil pore spaces to become smaller about 50 per cent solids (sand, silt, clay and organic • reduces water infiltration rate into soil matter) and about 50 per cent pore spaces. • decreases the rate that water will penetrate into the soil root zone and subsoil • increases the potential for surface Compaction concerns water ponding, water runoff, surface soil waterlogging and soil erosion Soil compaction can impair water Soil compaction infiltration into soil, crop emergence, • reduces the ability of a soil to hold root penetration and crop nutrient and can be a serious water and air, which are necessary for water uptake, all of which result in form of soil plant root growth and function depressed crop yield. • reduces crop emergence as a result of soil crusting Human-induced compaction of degradation. • impedes root growth and limits the agricultural soil can be the result of using volume of soil explored by roots tillage equipment during soil cultivation or result from the heavy weight of field equipment. • limits soil exploration by roots and Compacted soils can also be the result of natural soil- decreases the ability of crops to take up nutrients and forming processes. -
Sustainable Use of Soils and Water: the Role of Environmental Land Use Conflicts
sustainability Editorial Sustainable Use of Soils and Water: The Role of Environmental Land Use Conflicts Fernando A. L. Pacheco CQVR – Chemistry Research Centre, University of Trás-os-Montes and Alto Douro, Quinta de Prados Ap. 1013, Vila Real 5001-801, Portugal; [email protected] Received: 3 February 2020; Accepted: 4 February 2020; Published: 6 February 2020 Abstract: Sustainability is a utopia of societies, that could be achieved by a harmonious balance between socio-economic development and environmental protection, including the sustainable exploitation of natural resources. The present Special Issue addresses a multiplicity of realities that confirm a deviation from this utopia in the real world, as well as the concerns of researchers. These scholars point to measures that could help lead the damaged environment to a better status. The studies were focused on sustainable use of soils and water, as well as on land use or occupation changes that can negatively affect the quality of those resources. Some other studies attempt to assess (un)sustainability in specific regions through holistic approaches, like the land carrying capacity, the green gross domestic product or the eco-security models. Overall, the special issue provides a panoramic view of competing interests for land and the consequences for the environment derived therefrom. Keywords: water resources; soil; land use change; conflicts; environmental degradation; sustainability Competition for land is a worldwide problem affecting developed as well as developing countries, because the economic growth of activity sectors often requires the expansion of occupied land, sometimes to places that overlap different sectors. Besides the social tension and conflicts eventually caused by the competing interests for land, the environmental problems they can trigger and sustain cannot be overlooked. -
Aerobic Biodegradation of Oily Wastes a Field Guidance Book for Federal On-Scene Coordinators Version 1.0, October 2003
Aerobic Biodegradation of Oily Wastes A Field Guidance Book For Federal On-scene Coordinators Version 1.0, October 2003 U.S. Environmental Protection Agency Region 6 South Central Response and Prevention Branch EXECUTIVE SUMMARY This field guidance document was produced specifically as an aid for Federal On-scene Coordinators (FOSC) in U.S. Environmental Protection Agency (EPA) Region 6. It is intentionally limited in scope to best serve the requirements of the Region 6 Oil Program. Typically, Oil Program projects are completed quickly and efficiently and often do not require more than half a year to complete. Because of the nature of the Oil program, only aerobic land treatment was considered. Ongoing consultation with state and local officials during the land treatment process is assumed and essential to success. The level of detail provided in this field guide may be less than required for each project, but is sufficient to adequately diagnose technical problems should they occur. The writers of this field guide are aware that the users come from a variety of backgrounds and possess a wide range of field experience. In an attempt to develop a tool that may be used easily by both experienced and less-experienced users, minimum information is provided and an extensive bibliography section including web sites is included. Once the users have read and become familiar with the field guide, small shaded boxes or tables adjacent to a “pumpjack” icon help in locating key points throughout the document. This field guide consists of three parts complemented by appendices. The first part provides information to help evaluate the nature of the environment where land treatment is considered and a summary of the existing regulations and policies in Region 6. -
Topsoil Characterization for Sustainable Land Management 1
DRAFT FOOD AND AGRICULTURE ORGANIZATION OF THE UNITED NATIONS TOPSOIL CHARACTERIZATION FOR SUSTAINABLE LAND MANAGEMENT Land and Water Development Division Soil Resources, Management and Conservation Service Rome 1998 2 ACKNOWLEDGEMENTS This study is based upon earlier work by O.C. Spaargaren "Framework for Characterization and Classification of Topsoils in the World" (1992 unpublished) and A. Hebel "Soil Characterization and Evaluation System (SCE) with Emphasis on Topsoils and their Fertility-related Characteristics" (1994 unpublished). We would also like to acknowledge the cooperation of the University of Hohenheim, especially Dr. Gaiser and Prof. Stahr for testing the system, and various contributions, suggestions and constructive criticism received from Ms L.M. Jansen, Ms A Bot, Mr F. Nachtergaele, and last but not least, Mr M.F. Purnell. CONTENTS 1. Introduction 1 2. Topsoil Characterization Within Existing Soil Classification Systems 3 2.1 Introduction 3 2.2 Fertility Capability Classification (FCC) 3 2.3 Soil Classification Systems 3 3. Factors Influencing Topsoil Properties 7 3.1 Climate 7 3.2 Vegetation and Organic Matter 7 3.3 Topography and Physiography 8 3.4 Mineralogical Soil Constituents 9 3.5 Surface Processes 9 3.6 Biological Activity 10 3.7 Human Activity 10 4. Definition of Topsoil Properties and Modifiers 13 4.1 Texture 13 4.2 Organic Material 13 4.3 Organic Matter Status 14 4.4 Physical Features 16 4.5 Chemical Features 18 4.6 Biological Features 20 4.7 Drainage Features 21 4.8 Land Use 21 4.9 Erosion or Degradation 23 4.10 External Physical Conditions 25 4.11 Slope 26 4.12 Examples of Topsoil Characterization 26 5. -
Soils and Soil-Forming Material Technical Information Note 04 /2017 30Th November 2017
Soils and Soil-forming Material Technical Information Note 04 /2017 30th November 2017 Contents 1. Introduction to Soils ........................................................................................................................ 2 2. Components and Properties of Soil ................................................................................................ 7 3. Describing and Categorising soils .................................................................................................. 29 4. Policy, Regulation and Roles ......................................................................................................... 34 5. Soil Surveys, Handling and Management ..................................................................................... 40 6. Recommended Soil Specifications ................................................................................................ 42 7. References .................................................................................................................................... 52 “Upon this handful of soil our survival depends. Husband it and it will grow our food, our fuel, and our shelter and surround us with beauty. Abuse it and the soil will collapse and die, taking humanity with it.” From Vedas Sanskrit Scripture – circa 1500 BC The aim of this Technical Information Note is to assist Landscape Professionals (primarily landscape architects) when considering matters in relation to soils and soil-forming material. Soil is an essential requirement for providing -
Addressing Pasture Compaction
Addressing Pasture Compaction Weighing the Pros and Cons of Two Options UVM Project team: Dr. Josef Gorres, Dr. Rachel Gilker, Jennifer Colby, Bridgett Jamison Hilshey Partners: Mark Krawczyk (Keyline Vermont) and farmers Brent & Regina Beidler, Guy & Beth Choiniere, John & Rocio Clark, Lyle & Kitty Edwards, and Julie Wolcott & Stephen McCausland Writing: Josef Gorres, Rachel Gilker and Jennifer Colby • Design and Layout: Jennifer Colby • Photos: Jennifer Colby and Rachel Gilker Additional editing by Cheryl Herrick and Bridgett Jamison Hilshey Th is is dedicated to our farmer partners; may our work help you farm more productively, profi tably, and ecologically. VT Natural Resources Conservation Service UVM Center for Sustainable Agriculture http://www.vt.nrcs.usda.gov http://www.uvm.edu/sustainableagriculture UVM Plant & Soil Science Department http://pss.uvm.edu Financial support for this project and publication was provided through a VT Natural Resources Conservation Service (NRCS) Conservation Innovation Grant (CIG). We thank VT-NRCS for their eff orts to build a 2 strong natural resource foundation for Vermont’s farming systems. Introduction A few years ago, some grass-based dairy farmers came to us with the question, “You know, what we really need is a way to fi x the compaction in pastures.” We started digging for answers. Th is simple request has led us on a lively journey. We began by adapting methods to alleviate compac- tion in other climates and cropping systems. We worked with fi ve Vermont dairy farmers to apply these practices to their pastures, where other farmers could come and observe them in action. We assessed the pros and cons of these approaches and we are sharing those results and observations here. -
Preventing Soil Compaction Preserving and Restoring Soil Fertility
Preventing Soil Compaction Preserving and Restoring Soil Fertility Including the Classification Key for Detection and Evaluation of Harmful Soil Compaction in the Field www.umwelt.nrw.de Content Preface ............................................of the minister 2 1. Introduction ...................................................... 4 2. The importance of soil structure......................... 6 3. Causes of harmful soil compaction..................... 13 4. Effects of harmful soil compaction...................... 18 5. Detecting harmful soil compaction..................... 21 6. Preserving and improving soil structure ................ 25 7. What to do, if the soil is already compacted?...... 32 8. Final remarks.................................................... 36 Literature .............................................................. 37 4 1. Introduction Agricultural soil cultivation and harvest inevitably cause slight soil compaction. Especially detrimental is soil compaction which occurs deep in the subsoil, as this compaction cannot be reversed with normal soil cultiva- tion. Due to expected future warmer winters in Germany as a result of climate change, fewer and shorter frost periods are to be expected and with that the so-called “frost action” with its soil loosening effect will occur less frequently. This means that a natural way to loosen soil structure will be lost. Field traffic, with heavy loads on wet soils, is an especially critical contributor to severe soil compaction. With the increasing “just in time” harvest practice of farmers, this is a potential source of conflict. To address this, improved techniques to reduce soil pressure and to understand actual soil water content can be helpful. The steady increase in weight of agricultural machinery and field traffic frequency – both have increased by three- to fourfold within the last 40 years – in combina- tion with the technical ability to drive on increasingly wet soils, has led to ever greater compaction of our soils.