Microstructure Design of Low Alloy Transformation-Induced
Total Page:16
File Type:pdf, Size:1020Kb
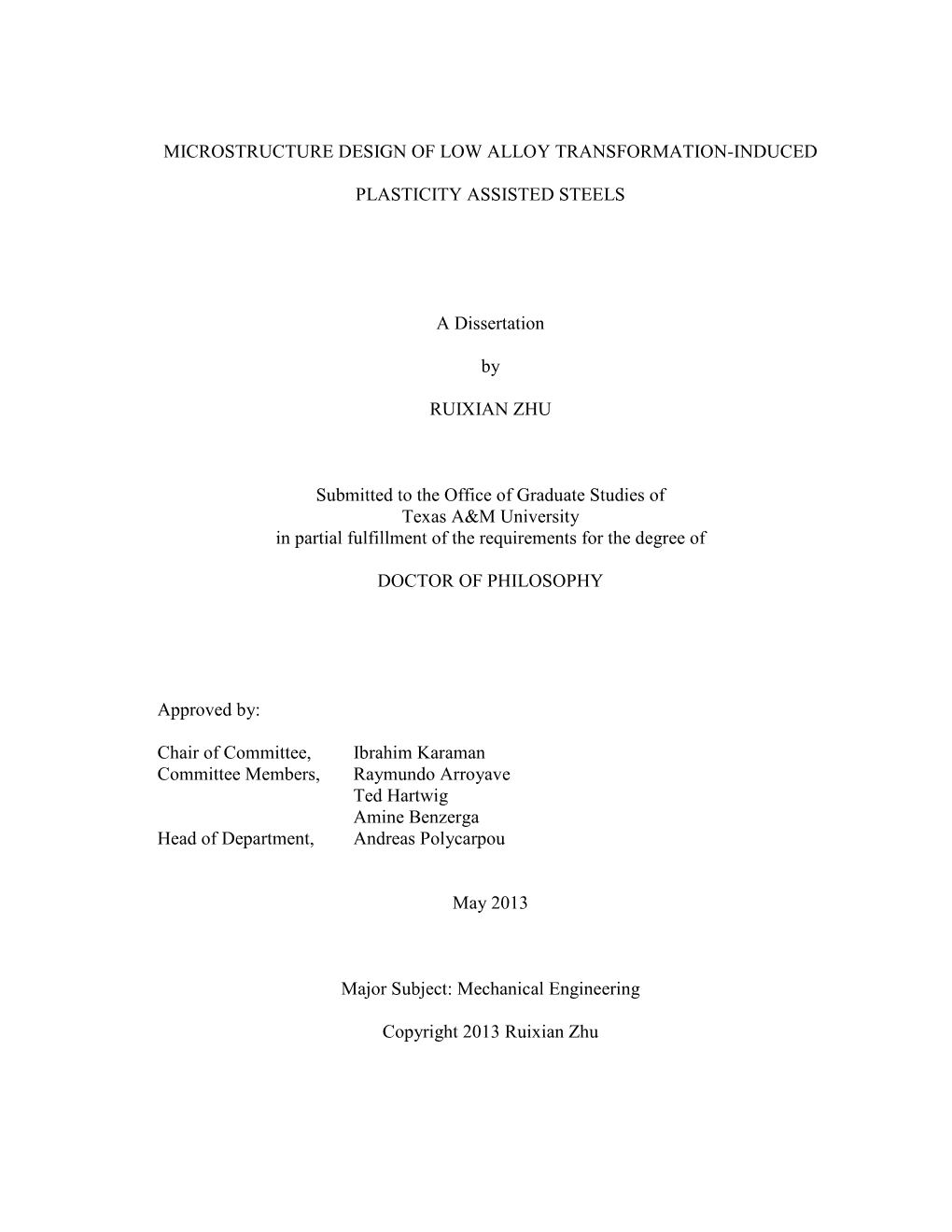
Load more
Recommended publications
-
High-Carbon Steels: Fully Pearlitic Microstructures and Applications
© 2005 ASM International. All Rights Reserved. www.asminternational.org Steels: Processing, Structure, and Performance (#05140G) CHAPTER 15 High-Carbon Steels: Fully Pearlitic Microstructures and Applications Introduction THE TRANSFORMATION OF AUSTENITE to pearlite has been de- scribed in Chapter 4, “Pearlite, Ferrite, and Cementite,” and Chapter 13, “Normalizing, Annealing, and Spheroidizing Treatments; Ferrite/Pearlite Microstructures in Medium-Carbon Steels,” which have shown that as microstructure becomes fully pearlitic as steel carbon content approaches the eutectiod composition, around 0.80% carbon, strength increases, but resistance to cleavage fracture decreases. This chapter describes the me- chanical properties and demanding applications for which steels with fully pearlitic microstructures are well suited. With increasing cooling rates in the pearlite continuous cooling trans- formation range, or with isothermal transformation temperatures ap- proaching the pearlite nose of isothermal transformation diagrams, Fig. 4.3 in Chapter 4, the interlamellar spacing of pearlitic ferrite and cementite becomes very fine. As a result, for most ferrite/pearlite microstructures, the interlamellar spacing is too fine to be resolved in the light microscope, and the pearlite appears uniformly dark. Therefore, to resolve the inter- lamellar spacing of pearlite, scanning electron microscopy, and for the finest spacings, transmission electron microscopy (TEM), are necessary to resolve the two-phase structure of pearlite. Figure 15.1 is a TEM mi- crograph showing very fine interlamellar structure in a colony of pearlite from a high-carbon steel rail. This remarkable composite structure of duc- © 2005 ASM International. All Rights Reserved. www.asminternational.org Steels: Processing, Structure, and Performance (#05140G) 282 / Steels: Processing, Structure, and Performance tile ferrite and high-strength cementite is the base microstructure for rail and the starting microstructure for high-strength wire applications. -
2000 Stainless Steels: an Introduction to Their Metallurgy and Corrosion
Dairy, Food and Environmental Sanitation, Vol. 20, No. 7, Pages 506-517 Copyright© International Association for Food Protection, 6200 Aurora Ave., Suite 200W, Des Moines, IA 50322 Stainless Steels: An Introduction to Their Metallurgy and Corrosion Resistance Roger A. Covert and Arthur H. Tuthill* and why they sometimes do not. In most cases, selection of the proper stainless steel leads to satisfactory performance. COMPOSITION, NOMEN- CLATURE AND GENERAL PROPERTIES Most metals are mixtures of a primary metallic element and one or more intentionally added other ele- This article has been peer-reviewed by two professionals. ments. These mixtures of elements are called alloys. Stainless steels are alloys, as are brasses (copper + zinc), bronzes (copper + tin), the many alu- INTRODUCTION better understanding of stainless minum alloys, and many other me- Worldwide, in industry, in busi- steels, especially to the non-metal- tallic materials. In general, solid ness and in the home, metals called lurgist. metals and alloys consist of randomly stainless steels are used daily. It is Industries are concerned with oriented grains that have a well-de- important to understand what these integrity of equipment and product fined crystalline structure, or lattice, materials are and why they behave purity. To achieve these, stainless within the grains. In stainless steels, the way they do. This is especially steels are often the economical and the crystalline structures within the true because the word “stainless” is practical materials of choice for pro- grains have been given names such as itself somewhat of a misnomer; these cess equipment. However, before ferrite, austenite, martensite, or a materials can stain and can corrode intelligent decisions can be made mixture of two or more of these. -
Carbon Steel
EN380 12-wk Exam Solution Fall 2019 Carbon Steel. 1. [19 pts] Three compositions of plain carbon steel are cooled very slowly in a turned-off furnace from ≈ 830◦C (see phase diagram below). For each composition, the FCC grains of γ−austenite (prior to transformation) are shown in an optical micrograph of the material surface. Sketch and label the phases making up the microstructures present in the right hand micrograph just after the austenite has completed transformation (note: the gray outlines of the prior γ grains may prove helpful). (a) [4 pts] C0 = 0:42% C (by wt). 830◦C 726◦C EN380 12-wk Exam Solution Page 1 Fall 2019 EN380 12-wk Exam Solution Fall 2019 (b) [4 pts] C0 = 0:80% C (by wt). 830◦C 726◦C (c) [4 pts] C0 = 1:05% C (by wt). 830◦C 726◦C (d) [7 pts] For the composition of part (c), C0 = 1:05% C (by wt), calculate the fraction of the solid that is pearlite at 726◦C. CF e3C − C0 6:67% − 1:05% Wpearlite = Wγ at 728◦C = = = 95:74% Pearlite CF e3C − Cγ 6:67% − 0:8% EN380 12-wk Exam Solution Page 2 Fall 2019 EN380 12-wk Exam Solution Fall 2019 2. [11 pts] Write in the correct term for each of the following related to carbon steels[1 pt each] (terms will be used exactly once): This material features carbon content in excess of Cast Iron 2:0% and is known for its excellent hardness, wear resistance, machinability and castability. -
Preparation and Mechanical Behavior of Ultra-High Strength Low-Carbon Steel
materials Article Preparation and Mechanical Behavior of Ultra-High Strength Low-Carbon Steel Zhiqing Lv 1,2,*, Lihua Qian 1, Shuai Liu 1, Le Zhan 1 and Siji Qin 1 1 Key Laboratory of Advanced Forging & Stamping Technology and Science, Ministry of Education of China Yanshan University, Qinhuangdao 066004, China; [email protected] (L.Q.); [email protected] (S.L.); [email protected] (L.Z.); [email protected] (S.Q.) 2 State Key Laboratory of Metastable Material Science and Technology, Yanshan University, Qinhuangdao 066004, China * Correspondence: [email protected] Received: 16 December 2019; Accepted: 14 January 2020; Published: 18 January 2020 Abstract: The low-carbon steel (~0.12 wt%) with complete martensite structure, obtained by quenching, was cold rolled to get the high-strength steel sheets. Then, the mechanical properties of the sheets were measured at different angles to the rolling direction, and the microstructural evolution of low-carbon martensite with cold rolling reduction was observed. The results show that the hardness and the strength gradually increase with increasing rolling reduction, while the elongation and impact toughness obviously decrease. The strength of the sheets with the same rolling reduction are different at the angles of 0◦, 45◦, and 90◦ to the rolling direction. The tensile strength (elongation) along the rolling direction is higher than that in the other two directions, but the differences between them are not obvious. When the aging was performed at a low temperature, the strength of the initial martensite and deformed martensite increased with increasing aging time during the early stages of aging, followed by a gradual decrease with further aging. -
Structure/Property Relationships in Irons and Steels Bruce L
Copyright © 1998 ASM International® Metals Handbook Desk Edition, Second Edition All rights reserved. J.R. Davis, Editor, p 153-173 www.asminternational.org Structure/Property Relationships in Irons and Steels Bruce L. Bramfitt, Homer Research Laboratories, Bethlehem Steel Corporation Basis of Material Selection ............................................... 153 Role of Microstructure .................................................. 155 Ferrite ............................................................. 156 Pearlite ............................................................ 158 Ferrite-Pearl ite ....................................................... 160 Bainite ............................................................ 162 Martensite .................................... ...................... 164 Austenite ........................................................... 169 Ferrite-Cementite ..................................................... 170 Ferrite-Martensite .................................................... 171 Ferrite-Austenite ..................................................... 171 Graphite ........................................................... 172 Cementite .......................................................... 172 This Section was adapted from Materials 5election and Design, Volume 20, ASM Handbook, 1997, pages 357-382. Additional information can also be found in the Sections on cast irons and steels which immediately follow in this Handbook and by consulting the index. THE PROPERTIES of irons and steels -
Chapter 12: Phase Transformations
Chapter 12: Phase Transformations ISSUES TO ADDRESS... • Transforming one phase into another takes time. Fe Fe C Eutectoid 3 γ transformation (cementite) (Austenite) + α C FCC (ferrite) (BCC) • How does the rate of transformation depend on time and temperature ? • Is it possible to slow down transformations so that non-equilibrium structures are formed? • Are the mechanical properties of non-equilibrium structures more desirable than equilibrium ones? AMSE 205 Spring ‘2016 Chapter 12 - 1 Phase Transformations Nucleation – nuclei (seeds) act as templates on which crystals grow – for nucleus to form rate of addition of atoms to nucleus must be faster than rate of loss – once nucleated, growth proceeds until equilibrium is attained Driving force to nucleate increases as we increase ΔT – supercooling (eutectic, eutectoid) – superheating (peritectic) Small supercooling slow nucleation rate - few nuclei - large crystals Large supercooling rapid nucleation rate - many nuclei - small crystals AMSE 205 Spring ‘2016 Chapter 12 - 2 Solidification: Nucleation Types • Homogeneous nucleation – nuclei form in the bulk of liquid metal – requires considerable supercooling (typically 80-300 °C) • Heterogeneous nucleation – much easier since stable “nucleating surface” is already present — e.g., mold wall, impurities in liquid phase – only very slight supercooling (0.1-10 °C) AMSE 205 Spring ‘2016 Chapter 12 - 3 Homogeneous Nucleation & Energy Effects Surface Free Energy- destabilizes the nuclei (it takes energy to make an interface) γ = surface tension ΔGT = Total Free Energy = ΔGS + ΔGV Volume (Bulk) Free Energy – stabilizes the nuclei (releases energy) r* = critical nucleus: for r < r* nuclei shrink; for r > r* nuclei grow (to reduce energy) Adapted from Fig.12.2(b), Callister & Rethwisch 9e. -
New Extremely Low Carbon Bainitic High-Strength Steel Bar Having Excellent Machinability and Toughness Produced by TPCP Technology*
KAWASAKI STEEL TECHNICAL REPORT No. 47 December 2002 New Extremely Low Carbon Bainitic High-Strength Steel Bar Having Excellent Machinability and Toughness Produced by TPCP Technology* Synopsis: A non heat-treated high strength steel bar for machine structural use through a thermo-mechanical precipita- tion control process (hereafter, referred to as TPCP) has been developed. The newly developed TPCP is a tech- nique for controlling the strength of the steel by precipi- tation hardening effected with the benefit of an extremely low carbon bainitic microstructure. The carbon content Kazukuni Hase Toshiyuki Hoshino Keniti Amano of the steel is decreased to below 0.02 mass% for realiz- Senior Researcher, Dr. Eng., Senior Dr. Eng., General Plate, Shape & Joining Researcher, Plate, Manager, Plate, Shape ing the proper microstructure, which improves both the Lab., Shape & Joining Lab., & Joining Lab., notch toughness and machinability. In order to make the Technical Res. Labs. Technical Res. Labs. Technical Res. Labs. microstructure bainitic and to obtain effective precipita- tion hardening, some micro-alloying elements are added. The developed steel manufactured with these advanced techniques showed a higher impact value, higher yield strength and better machinability than those 1 Introdution of the quenched and tempered AISI 4137 steel. The impact value of the steel is 250 J/cm2 or more at room In the fields of automobiles and industrial machines temperature. The problem of the reduction in yield ratio, where carbon steels and low alloy steels -
Materials Technology – Placement
MATERIAL TECHNOLOGY 01. An eutectoid steel consists of A. Wholly pearlite B. Pearlite and ferrite C. Wholly austenite D. Pearlite and cementite ANSWER: A 02. Iron-carbon alloys containing 1.7 to 4.3% carbon are known as A. Eutectic cast irons B. Hypo-eutectic cast irons C. Hyper-eutectic cast irons D. Eutectoid cast irons ANSWER: B 03. The hardness of steel increases if it contains A. Pearlite B. Ferrite C. Cementite D. Martensite ANSWER: C 04. Pearlite is a combination of A. Ferrite and cementite B. Ferrite and austenite C. Ferrite and iron graphite D. Pearlite and ferrite ANSWER: A 05. Austenite is a combination of A. Ferrite and cementite B. Cementite and gamma iron C. Ferrite and austenite D. Pearlite and ferrite ANSWER: B 06. Maximum percentage of carbon in ferrite is A. 0.025% B. 0.06% C. 0.1% D. 0.25% ANSWER: A 07. Maximum percentage of carbon in austenite is A. 0.025% B. 0.8% 1 C. 1.25% D. 1.7% ANSWER: D 08. Pure iron is the structure of A. Ferrite B. Pearlite C. Austenite D. Ferrite and pearlite ANSWER: A 09. Austenite phase in Iron-Carbon equilibrium diagram _______ A. Is face centered cubic structure B. Has magnetic phase C. Exists below 727o C D. Has body centered cubic structure ANSWER: A 10. What is the crystal structure of Alpha-ferrite? A. Body centered cubic structure B. Face centered cubic structure C. Orthorhombic crystal structure D. Tetragonal crystal structure ANSWER: A 11. In Iron-Carbon equilibrium diagram, at which temperature cementite changes fromferromagnetic to paramagnetic character? A. -
Cast Irons$ KB Rundman, Michigan Technological University, Houghton, MI, USA F Iacoviello, Università Di Cassino E Del Lazio Meridionale, DICEM, Cassino (FR), Italy
Cast Irons$ KB Rundman, Michigan Technological University, Houghton, MI, USA F Iacoviello, Università di Cassino e del Lazio Meridionale, DICEM, Cassino (FR), Italy r 2016 Elsevier Inc. All rights reserved. 1 Metallurgy of Cast Iron 1 2 Solidification of a Hypoeutectic Gray Iron Alloy With CE¼4.0 3 3 Matrix Microstructures in Graphitic Cast Irons – Cooling Below the Eutectic 3 4 Microstructure and Mechanical Properties of Gray Cast Iron 4 5 Effect of Carbon Equivalent 5 6 Effect of Matrix Microstructure 5 7 Effect of Alloying Elements 5 8 Classes of Gray Cast Irons and Brinell Hardness 5 9 Ductile Cast Iron 5 10 Production of Ductile Iron 6 11 Solidification and Microstructures of Hypereutectic Ductile Cast Irons 6 12 Mechanical Properties of Ductile Cast Iron 7 13 As-cast and Quenched and Tempered Grades of Ductile Iron 8 14 Malleable Cast Iron, Processing, Microstructure, and Mechanical Properties 8 15 Compacted Graphite Iron 9 16 Austempered Ductile Cast Iron 9 17 The Metastable Phase Diagram and Stabilized Austenite 9 18 Control of Mechanical Properties of ADI 10 19 Conclusion 10 References 11 Further Reading 11 Cast irons have played an important role in the development of the human species. They have been produced in various compositions for thousands of years. Most often they have been used in the as-cast form to satisfy structural and shape requirements. The mechanical and physical properties of cast irons have been enhanced through understanding of the funda- mental relationships between microstructure (phases, microconstituents, and the distribution of those constituents) and the process variables of iron composition, heat treatment, and the introduction of significant additives in molten metal processing. -
The Effect of Tempering on the Microstructure and Mechanical
applied sciences Article The Effect of Tempering on the Microstructure and Mechanical Properties of a Novel 0.4C Press-Hardening Steel Oskari Haiko 1,* , Antti Kaijalainen 1 , Sakari Pallaspuro 1 , Jaakko Hannula 1, David Porter 1, Tommi Liimatainen 2 and Jukka Kömi 1 1 Materials and Mechanical Engineering, Centre for Advanced Steels Research, University of Oulu, 90014 Oulu, Finland; antti.kaijalainen@oulu.fi (A.K.); sakari.pallaspuro@oulu.fi (S.P.); jaakko.hannula@oulu.fi (J.H.); david.porter@oulu.fi (D.P.); jukka.komi@oulu.fi (J.K.) 2 Raahe Works, SSAB Europe, 92100 Raahe, Finland; [email protected] * Correspondence: oskari.haiko@oulu.fi Received: 12 September 2019; Accepted: 4 October 2019; Published: 10 October 2019 Featured Application: Potential wear-resistant steel for harsh environments in agricultural sector, i.e., chisel ploughs and disc harrows. Abstract: In this paper, the effects of different tempering temperatures on a recently developed ultrahigh-strength steel with 0.4 wt.% carbon content were studied. The steel is designed to be used in press-hardening for different wear applications, which require high surface hardness (650 HV/58 HRC). Hot-rolled steel sheet from a hot strip mill was austenitized, water quenched and subjected to 2-h tempering at different temperatures ranging from 150 ◦C to 400 ◦C. Mechanical properties, microstructure, dislocation densities, and fracture surfaces of the steels were characterized. Tensile strength greater than 2200 MPa and hardness above 650 HV/58 HRC were measured for the as-quenched variant. Tempering decreased the tensile strength and hardness, but yield strength increased with low-temperature tempering (150 ◦C and 200 ◦C). -
The Role of Alloying Elements on the Fabricability of Austenitic Stainless Steel
The Role of Alloying Elements on the Fabricability of Austenitic Stainless Steel John C. Tverberg, P.E. Metals and Materials Consulting Engineers Mukwonago, Wisconsin How many times have fabrication problems developed when a new coil or a new heat of steel is put in production? The problems can be tearing, cracking, scratching, poorer weld penetration, poor electropolished surface or a host of other problems. The usual procedure to determine the source of the problem is a hardness test, tensile test, and metallographic cross section and to review the mill test reports. Sometimes the source of the problem is spotted, but most often nothing out of the ordinary is found. In these cases the problem lies in the composition of the steel even when the alloy is within the specified composition of the steel. Alloy Design Austenitic stainless steels are designed to give corrosion resistance in many environments, resistance to hydrogen and 885º F (475º C) embrittlement, good strength, good ductility and low hardness. In its simplest form stainless steel is iron with 12% minimum chromium. This is what makes stainless steel rust resistant and allows the passive film to develop. Stainless steel exists in three metallurgical conditions depending on composition and heat treatment: ferritic, martensitic and austenitic. These names refer to the crystallographic structure: ferrite is body-centered cubic, austenite is face-centered cubic and martensite is a distorted tetragonal which is the distorted face-centered cubic structure being changed into a body-centered structure. The characteristics of these structures are tabulated in Table I and are illustrated in Figure 1. -
Retained Austenite
rial H THE HEAT TREAT DOCTOR • • T Daniel H. Herring | 630.834.3017 | [email protected] H A Discussion of Retained Austenite hat is retained austenite temperature; that is, low enough to form How does RA behave? and how does it affect 100% martensite. Because the Mf is Martensite is hard, strong and brittle the properties of a com- below room temperature in alloys con- while austenite is soft and tough. In ponent? How much, if taining more than 0.30% carbon, signifi- some instances, when combined, the any, retained austenite should be present cant amounts of untransformed, or mixture of austenite and martensite cre- in a particular component microstruc- retained austenite, may be present, inter- ates a composite material that has some ture? Is the presence of retained austenite mingled with martensite at room temper- of the benefits of each, while compensat- in a microstructure a good thing or a con- ature (Fig. 1). Retained austenite is a spe- ing for the shortcomings of both. cern? These are questions that metallur- cific crystalline form of iron and steel. The For any given application, mechanical gists have spent countless dark-colored needles shown are tempered properties are affected by a high percent- hours debating. What do we martensite crystals and the light-colored age of retained austenite content. For as heat treaters need to areas are retained austenite crystals. The example, retained austenite affects the know about retained austen- amount of retained austenite is a function following properties of bearing steels: ite and how is retained of the carbon content, alloy content austenite viewed by various (especially nickel and manganese), quen- • Dimensional stability: Retained industries? Let's learn more.