GPU Acceleration Benefits for Applied CAE Axel Koehler, Senior Solutions Architect HPC, NVIDIA HPC Advisory Council Meeting, April 2014 , Lugano Outline
Total Page:16
File Type:pdf, Size:1020Kb
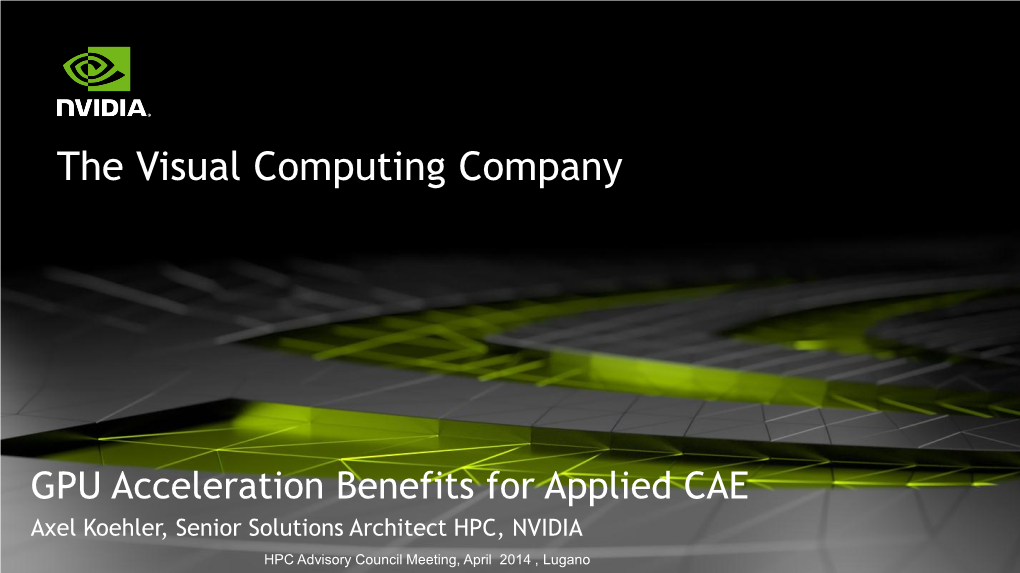
Load more
Recommended publications
-
Download the PLM Industry Summary (PDF)
PLM Industry Summary Christine Bennett, Editor Vol. 13 No.17 Friday 29 April 2011 Contents Acquisitions _______________________________________________________________________ 2 Dassault Systèmes Acquires Enginuity PLM to Accelerate Innovation for Formulated Products __________2 ESI Group Acquires Comet Technology’s IP, Including “COMET Acoustics” Software for Low Frequency Noise and Vibration Modeling _____________________________________________________________4 Lawson Software Enters into Definitive Agreement to be Acquired by an Affiliate of Golden Gate Capital and Infor ______________________________________________________________________________4 CIMdata News _____________________________________________________________________ 6 CIMdata in the News: “CIMdata Evaluates PLM-Market in 2010 and Gives Optimistic Forecasts” _______6 YouTube: Oracle Agile PLM Team Interviews CIMdata Analyst _________________________________6 Company News _____________________________________________________________________ 6 CGTech and VMH International Announce Joint Partnership _____________________________________6 Delcam Wins Third Queen’s Award for International Sales Success _______________________________7 500 Technical Paper and Presentations on Multiphysics Simulation are Available from COMSOL________8 POLYTEDA Joins Si2’s Design for Manufacturability Coalition __________________________________9 PTC Holds the Inaugural FIRST Tech Challenge in China to Inspire Student Innovation ______________10 Seven Universities Sign on with Altium: From the -
Reference Manual Ii
GiD The universal, adaptative and user friendly pre and postprocessing system for computer analysis in science and engineering Reference Manual ii Table of Contents Chapters Pag. 1 INTRODUCTION 1 1.1 What's GiD 1 1.2 GiD Manuals 1 2 GENERAL ASPECTS 3 2.1 GiD Basics 3 2.2 Invoking GiD 4 2.2.1 First start 4 2.2.2 Command line flags 5 2.2.3 Command line extra file 6 2.2.4 Settings 6 2.3 User Interface 7 2.3.1 Top menu 9 2.3.2 Toolbars 9 2.3.3 Command line 12 2.3.4 Status and Information 13 2.3.5 Right buttons 13 2.3.6 Mouse operations 13 2.3.7 Classic GiD theme 14 2.4 User Basics 16 2.4.1 Point definition 16 2.4.1.1 Picking in the graphical window 17 2.4.1.2 Entering points by coordinates 17 2.4.1.2.1 Local-global coordinates 17 2.4.1.2.2 Cylindrical coordinates 18 2.4.1.2.3 Spherical coordinates 18 2.4.1.3 Base 19 2.4.1.4 Selecting an existing point 19 2.4.1.5 Point in line 19 2.4.1.6 Point in surface 19 2.4.1.7 Tangent in line 19 2.4.1.8 Normal in surface 19 2.4.1.9 Arc center 19 2.4.1.10 Grid 20 2.4.2 Entity selection 20 2.4.3 Escape 21 2.5 Files Menu 22 2.5.1 New 22 2.5.2 Open 22 2.5.3 Open multiple.. -
Calculix USER's MANUAL
CalculiX USER’S MANUAL - CalculiX GraphiX, Version 2.7 - Klaus Wittig February 18, 2014 Figure 1: A complex model made from scratch using second order brick elements 1 Contents 1 Introduction 7 2 Concept 7 3 File Formats 8 4 Getting Started 9 5 Program Parameters 13 6 Input Devices 14 6.1 Mouse ................................. 14 6.2 Keyboard ............................... 15 7 Menu 16 7.1 Datasets................................ 16 7.1.1 Entity ............................. 17 7.2 Viewing ................................ 17 7.2.1 ShowElementsWithLight . 17 7.2.2 ShowBadElements . 17 7.2.3 Fill............................... 17 7.2.4 Lines.............................. 17 7.2.5 Dots.............................. 18 7.2.6 ToggleCullingBack/Front . 18 7.2.7 ToggleModelEdges . 18 7.2.8 ToggleElementEdges . 18 7.2.9 ToggleSurfaces/Volumes . 18 7.2.10 Toggle Move-Z/Zoom . 18 7.2.11 Toggle Background Color . 19 7.2.12 ToggleVector-Plot . 19 7.2.13 ToggleAdd-Displacement . 19 7.3 Animate................................ 19 7.3.1 Start.............................. 19 7.3.2 Tune-Value .......................... 19 7.3.3 StepsperPeriod ....................... 20 7.3.4 TimeperPeriod ....................... 20 7.3.5 ToggleRealDisplacements . 20 7.3.6 ToggleDatasetSequence. 20 7.4 Frame ................................. 20 7.5 Zoom ................................. 20 7.6 Center................................. 20 7.7 Enquire ................................ 21 7.8 Cut .................................. 21 7.9 Graph ................................. 21 7.10Orientation .............................. 21 2 7.10.1 +xView............................ 21 7.10.2 -xView ............................ 21 7.10.3 +yView............................ 21 7.10.4 -yView ............................ 21 7.10.5 +zView............................ 21 7.10.6 -zView ............................ 22 7.11Hardcopy ............................... 22 7.11.1 Tga-Hardcopy ........................ 22 7.11.2 Ps-Hardcopy ......................... 22 7.11.3 Gif-Hardcopy . -
Development of a Coupling Approach for Multi-Physics Analyses of Fusion Reactors
Development of a coupling approach for multi-physics analyses of fusion reactors Zur Erlangung des akademischen Grades eines Doktors der Ingenieurwissenschaften (Dr.-Ing.) bei der Fakultat¨ fur¨ Maschinenbau des Karlsruher Instituts fur¨ Technologie (KIT) genehmigte DISSERTATION von Yuefeng Qiu Datum der mundlichen¨ Prufung:¨ 12. 05. 2016 Referent: Prof. Dr. Stieglitz Korreferent: Prof. Dr. Moslang¨ This document is licensed under the Creative Commons Attribution – Share Alike 3.0 DE License (CC BY-SA 3.0 DE): http://creativecommons.org/licenses/by-sa/3.0/de/ Abstract Fusion reactors are complex systems which are built of many complex components and sub-systems with irregular geometries. Their design involves many interdependent multi- physics problems which require coupled neutronic, thermal hydraulic (TH) and structural mechanical (SM) analyses. In this work, an integrated system has been developed to achieve coupled multi-physics analyses of complex fusion reactor systems. An advanced Monte Carlo (MC) modeling approach has been first developed for converting complex models to MC models with hybrid constructive solid and unstructured mesh geometries. A Tessellation-Tetrahedralization approach has been proposed for generating accurate and efficient unstructured meshes for describing MC models. For coupled multi-physics analyses, a high-fidelity coupling approach has been developed for the physical conservative data mapping from MC meshes to TH and SM meshes. Interfaces have been implemented for the MC codes MCNP5/6, TRIPOLI-4 and Geant4, the CFD codes CFX and Fluent, and the FE analysis platform ANSYS Workbench. Furthermore, these approaches have been implemented and integrated into the SALOME simulation platform. Therefore, a coupling system has been developed, which covers the entire analysis cycle of CAD design, neutronic, TH and SM analyses. -
AMI Import and Export Revision 1, 21 March 2012
Autodesk® Moldflow® Insight 2012 AMI Import and Export Revision 1, 21 March 2012. This document contains Autodesk and third-party software license agreements/notices and/or additional terms and conditions for licensed third-party software components included within the product. These notices and/or additional terms and conditions are made a part of and incorporated by reference into the Autodesk Software License Agreement and/or the About included as part of the Help function within the software. Contents Chapter 1 Supported model import formats. 1 Supported model import formats. 3 Importing a CAD model. 3 Importing an ASCII model file. 3 Importing a model of the core from a CAD program. 4 Importing a Moldflow Plastics Insight 2.0 project. 5 Supported model import formats . 5 Import—Create New Project dialog. 6 Import dialog. 6 Autodesk Moldflow Design Link . 6 Autodesk Moldflow Design Link. 7 Autodesk Moldflow Design Link. 7 Chord angle. 8 Mesh on assembly contact faces. 8 Supported IGES entities. 9 Supported STEP entities. 10 Using models imported from Autodesk Simulation products. 12 Using models imported from Autodesk Simulation products. 13 iii Importing IGES model files. 14 Importing IGES model files. 16 Importing STL model files. 17 Importing STL model files. 19 Importing ANSYS model files. 20 Importing IDEAS universal model files. 20 Importing NASTRAN bulk data model files. 22 Importing PATRAN neutral model files. 22 Importing a C-MOLD *.fem file. 23 Importing a C-MOLD *.fem file. 23 Chapter 2 Exporting models and files. 28 Exporting models and files. 30 Exporting files. 30 Exporting the project to a ZIP file. -
Getting Started with NX Nastran 3
SIEMENS NX Nastran 10 Getting Started Tutorials Contents Proprietary & Restricted Rights Notice . 5 Performing an Analysis Step-by-Step . 1-1 Defining the Problem . 1-1 Specifying the Type of Analysis . 1-2 Designing the Model . 1-3 Creating the Model Geometry . 1-3 Defining the Finite Elements . 1-5 Representing Boundary Conditions . 1-9 Specifying Material Properties . 1-10 Applying the Loads . 1-11 Controlling the Analysis Output . 1-12 Completing the Input File and Running the Model . 1-12 NX Nastran Output . 1-14 Reviewing the Results . 1-18 Additional Examples . 2-1 Cantilever Beam with a Distributed Load and a Concentrated Moment . 2-1 The Finite Element Model . 2-2 NX Nastran Results . 2-5 Rectangular Plate (fixed-hinged-hinged-free) with a Uniform Lateral Pressure Load . 2-9 The Finite Element Model . 2-10 NX Nastran Results . 2-14 Gear Tooth with Solid Elements . 2-21 The Finite Element Model . 2-21 NX Nastran Results . 2-24 Getting Started with NX Nastran 3 Proprietary & Restricted Rights Notice © 2014 Siemens Product Lifecycle Management Software Inc. All Rights Reserved. This software and related documentation are proprietary to Siemens Product Lifecycle Management Software Inc. Siemens and the Siemens logo are registered trademarks of Siemens AG. NX is a trademark or registered trademark of Siemens Product Lifecycle Management Software Inc. or its subsidiaries in the United States and in other countries. NASTRAN is a registered trademark of the National Aeronautics and Space Administration. NX Nastran is an enhanced proprietary version developed and maintained by Siemens Product Lifecycle Management Software Inc. -
The Virtual Parts Functionalities in Catia V5, Finite Element Aspects
University of Windsor Scholarship at UWindsor Electronic Theses and Dissertations Theses, Dissertations, and Major Papers 9-27-2018 The Virtual Parts Functionalities in Catia v5, Finite Element Aspects Hamoon Ramezani Karegar University of Windsor Follow this and additional works at: https://scholar.uwindsor.ca/etd Recommended Citation Ramezani Karegar, Hamoon, "The Virtual Parts Functionalities in Catia v5, Finite Element Aspects" (2018). Electronic Theses and Dissertations. 7563. https://scholar.uwindsor.ca/etd/7563 This online database contains the full-text of PhD dissertations and Masters’ theses of University of Windsor students from 1954 forward. These documents are made available for personal study and research purposes only, in accordance with the Canadian Copyright Act and the Creative Commons license—CC BY-NC-ND (Attribution, Non-Commercial, No Derivative Works). Under this license, works must always be attributed to the copyright holder (original author), cannot be used for any commercial purposes, and may not be altered. Any other use would require the permission of the copyright holder. Students may inquire about withdrawing their dissertation and/or thesis from this database. For additional inquiries, please contact the repository administrator via email ([email protected]) or by telephone at 519-253-3000ext. 3208. The Virtual Parts Functionalities in Catia v5, Finite Element Aspects By Hamoon Ramezani Karegar A Thesis Submitted to the Faculty of Graduate Studies through the Department of Mechanical, Automotive and Materials Engineering in Partial Fulfillment of the Requirements for the Degree of Master of Applied Science at the University of Windsor Windsor, Ontario, Canada 2018 © 2018 Hamoon Ramezani The Virtual Parts Functionalities in Catia v5, Finite Element Aspects by Hamoon Ramezani Karegar APPROVED BY: ______________________________________________ M. -
Autodesk® Simulation Moldflow® Comparison Matrix
Autodesk® Simulation Moldflow® Comparison Matrix Autodesk® Simulation Moldflow® injection molding simulation software provides tools that can help manufacturers validate and optimize the design of plastic parts and injection molds and study the injection molding process. Compare the features of Autodesk Simulation Moldflow products to learn how Autodesk® Simulation Moldflow® Adviser and Autodesk® Simulation Moldflow® Insight software can help meet the needs of your organization. Autodesk Autodesk Autodesk Autodesk Autodesk Autodesk Simulation Simulation Simulation Simulation Simulation Simulation Moldflow Moldflow Moldflow Moldflow Moldflow Moldflow LEGEND Adviser Adviser Adviser Insight Insight Insight Feature supported Standard Premium Ultimate Standard Premium Ultimate MESHING TECHNOLOGY Dual Domain™ 3D Midplane CAD INTEROPERABilitY Direct Modeling with Autodesk® Inventor® Fusion Defeaturing with Inventor Fusion Multi-CAD Data Exchange CAD Solid Models Parts Assemblies SimulatiON CapaBilitiES Thermoplastic Filling Part Defects Gate Location Molding Window Thermoplastic Packing Runner Balancing Cooling Warpage Fiber Orientation Insert Overmolding Two-Shot Sequential Overmolding Core Shift Control MOLDING PROCEssES Thermoplastic Injection Molding Reactive Injection Molding Microchip Encapsulation Underfill Encapsulation Gas-Assisted Injection Molding Injection-Compression Molding Co-Injection Molding MuCell® Birefringence -
Manage Engineering Data Complex Models and Simulations Yield a Torrent
NX 8 for Design. Smarter decisions, better products. Learn more on page 11 DtopEng_banner_NXCAD_MAR2012.indd 1 3/8/12 11:02 AM April 2012 / deskeng.com Origin 8.6 Overview P.22 Direct Modeling and FEA P.24 TECHNOLOGY FOR DESIGN ENGINEERING Manage Engineering Data Complex models and simulations yield a torrent of data to seize and control. P.16 RACING AHEAD WITH CLUSTERS P.35 REVIEW: HP Z10 WORKSTATION P.38 P.40 PREPARING 3D MODELS de0412_Cover_Darlene.indd 1 3/15/12 12:20 PM Objet.indd 1 3/14/12 11:17 AM DTE_0412_Layout 1 2/28/12 4:36 PM Page 1 Data Loggers & Data Acquisition Systems iNET-400 Series Expandable Modular Data Acquisition System • Directly Connects to Thermocouple, RTD, Thermistor, Strain Gage, Load Complete Cell, Voltage, Current, Resistance Starter and Accelerometer Inputs System $ • USB 2.0 High Speed Data Acquisition 990 Hardware for Windows® ≥XP SP2, Vista or 7 (XP/VS/7) • Analog and Digital Input and Outputs • Free instruNet World Software Visit omega.com/inet-400_series © Kutt Niinepuu / Dreamstime.com Stand-Alone, High-Speed, 8-Channel High Speed Voltage Multifunction Data Loggers Input USB Data Acquisition Modules OM-USB-1208HS Series Starts at $499 High Performance Multi-Function I/O USB Data Acquisition Modules OMB-DAQ-2416 Series OM-LGR-5320 Series Starts at Starts at $1100 $1499 Visit omega.com/om-lgr-5320_series Visit omega.com/om-usb-1208hs_series Visit omega.com/omb-daq-2416 ® omega.com ® © COPYRIGHT 2012 OMEGA ENGINEERING, INC. ALL RIGHTS RESERVED Omega.indd 1 3/14/12 10:54 AM Degrees of Freedom by Jamie J. -
A Three-Dimensional Finite Element Mesh Generator with Built-In Pre- and Post-Processing Facilities
INTERNATIONAL JOURNAL FOR NUMERICAL METHODS IN ENGINEERING Int. J. Numer. Meth. Engng 2009; 0:1{24 Prepared using nmeauth.cls [Version: 2002/09/18 v2.02] This is a preprint of an article accepted for publication in the International Journal for Numerical Methods in Engineering, Copyright c 2009 John Wiley & Sons, Ltd. Gmsh: a three-dimensional finite element mesh generator with built-in pre- and post-processing facilities Christophe Geuzaine1, Jean-Fran¸cois Remacle2∗ 1 Universit´ede Li`ege,Department of Electrical Engineering And Computer Science, Montefiore Institute, Li`ege, Belgium. 2 Universite´ catholique de Louvain, Institute for Mechanical, Materials and Civil Engineering, Louvain-la-Neuve, Belgium SUMMARY Gmsh is an open-source three-dimensional finite element grid generator with a build-in CAD engine and post-processor. Its design goal is to provide a fast, light and user-friendly meshing tool with parametric input and advanced visualization capabilities. This paper presents the overall philosophy, the main design choices and some of the original algorithms implemented in Gmsh. Copyright c 2009 John Wiley & Sons, Ltd. key words: Computer Aided Design, Mesh generation, Post-Processing, Finite Element Method, Open Source Software 1. Introduction When we started the Gmsh project in the summer of 1996, our goal was to develop a fast, light and user-friendly interactive software tool to easily create geometries and meshes that could be used in our three-dimensional finite element solvers [8], and then visualize and export the computational results with maximum flexibility. At the time, no open-source software combining a CAD engine, a mesh generator and a post-processor was available: the existing integrated tools were expensive commercial packages [41], and the freeware or shareware tools were limited to either CAD [29], two-dimensional mesh generation [44], three-dimensional mesh generation [53, 21, 30], or post-processing [31]. -
Finite Element Software for Rubber Products Design
International Journal of Engineering and Management Sciences (IJEMS) Vol. 3. (2018). No. 1. DOI: 10.21791/IJEMS.2018.1.2. Finite Element Software for Rubber Products Design D. HURI Department of Mechanical Engineering, Faculty of Engineering, University of Debrecen, [email protected] Abstract: Automotive rubber products are subjected to large deformations during working conditions, they often contact with other parts and they show highly nonlinear material behavior. Using finite element software for complex analysis of rubber parts can be a good way, although it has to contain special modules. Different types of rubber materials require the curve fitting possibility and the wide range choice of the material models. It is also important to be able to describe the viscoelastic property and the hysteresis. The remeshing possibility can be a useful tool for large deformation and the working circumstances require the contact and self contact ability as well. This article compares some types of the finite element software available on the market based on the above mentioned features. Introduction Finite element simulation of rubber parts is still a demanding task for engineers thanks to the combined effect of several factors. The first one is the elastic modulus of the rubber which depends on the rubber recipe, the shape of the rubber and the size of the deformation as well. The rubber shows nonlinear behavior, therefore the software has to have nonlinear solver ability. While the producers handle the rubber recipe as an industrial secret the mechanical properties have to be determined by laboratory measurements. In most cases the rubber behaves as an elastic, isotropic and nearly incompressible material and it can undergo large deformation. -
DS LLC Engineering AD-12.Vp
Engineering Analysis & Design Wet Electrostatic Precipitator - Temperature, Thermal Expansion, & Stress Autonomous Undersea Vehicle (AUV) Structural Analysis DeepSoft, LLC Engineering Analysis Engineering Analysis & Design TurboSonic, Inc., retained DeepSoft, LLC. (DSL) to provide a detailed Nastran Finite Element Analysis (FEA) of their Wet Electrostatic Precipitators which are shown on the cover. Analyses included heat transfer, thermal expansion & stress, buckling, and structural stress. For Duratek, Inc.'s nuclear waste vitrification melters Algor FEA analyses included heat transfer, thermal expansion and stress, structural stress, and coolant loop pressure drop. Battelle Laboratories required a dynamic modal FEA to determine resonant frequencies, and a dynamic drop impact analysis of their portable ultrasonic cleaner developed for the US Army. For DHS Systems DSL performed a FEA dynamic impact stress analysis of their tow bar for a US Army Ultrasonic Cleaner - Modal Analysis trailer. Some projects may be best served by manual calculations alone without a FEA. Preparation for FEA may involve 20-30 pages of fluid dynamic, thermodynamic, heat transfer, and structural calculations to determine loads, boundary conditions, concentrated mass, and material properties. These are typically automated with Mathcad, Excel, or a C/C++ computer program. Stone Aerospace, developer of the Endurance Autonomous Underwater Vehicle (AUV), retained DSL to create 3D SolidWorks parts, assemblies, and drawings of their science package winch design for a series of Antarctic dives. Inventor or SolidWorks are used for new designs - SpaceClaim allows Nuclear Waste Melter Base - Displacement importing almost any 3D model geometry for design changes or FEA preparation. The principal has also designed a diver propulsion vehicle and a diver's decompression computer.