A Review of Coupling Mechanism Designs for Modular Reconfigurable
Total Page:16
File Type:pdf, Size:1020Kb
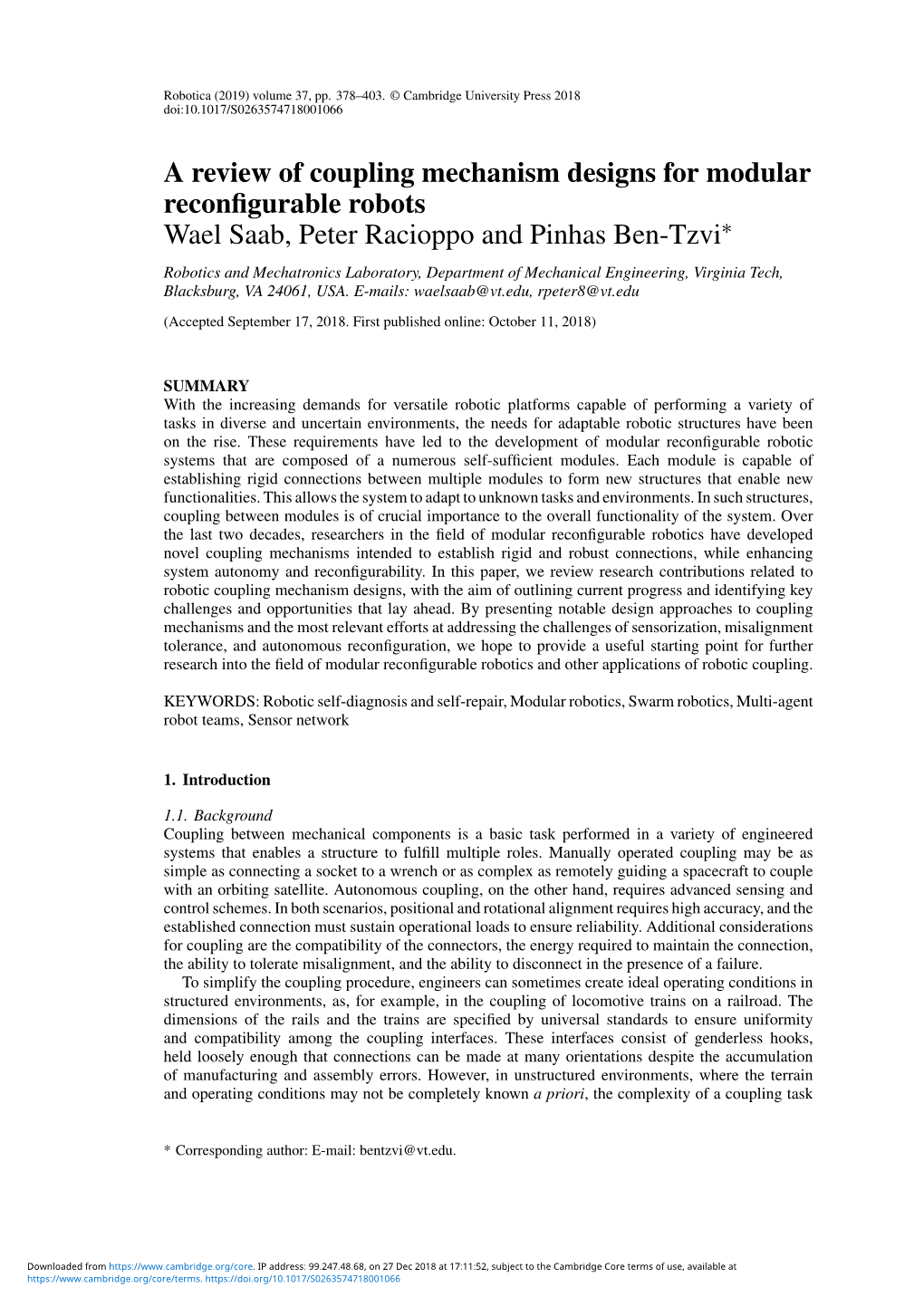
Load more
Recommended publications
-
Claytronics - a Synthetic Reality D.Abhishekh, B.Ramakantha Reddy, Y.Vijaya Kumar, A.Basi Reddy
International Journal of Scientific & Engineering Research, Volume 4, Issue 3, March‐2013 ISSN 2229‐5518 Claytronics - A Synthetic Reality D.Abhishekh, B.Ramakantha Reddy, Y.Vijaya Kumar, A.Basi Reddy, Abstract— "Claytronics" is an emerging field of electronics concerning reconfigurable nanoscale robots ('claytronic atoms', or catoms) designed to form much larger scale machines or mechanisms. Also known as "programmable matter", the catoms will be sub-millimeter computers that will eventually have the ability to move around, communicate with each others, change color, and electrostatically connect to other catoms to form different shapes. Claytronics technology is currently being researched by Professor Seth Goldstein and Professor Todd C. Mowry at Carnegie Mellon University, which is where the term was coined. According to Carnegie Mellon's Synthetic Reality Project personnel, claytronics are described as "An ensemble of material that contains sufficient local computation, actuation, storage, energy, sensing, and communication" which can be programmed to form interesting dynamic shapes and configurations. Index Terms— programmable matter, nanoscale robots, catoms, atoms, electrostatically, LED, LATCH —————————— —————————— 1 INTRODUCTION magine the concept of "programmable matter" -- micro- or which are ringed by several electromagnets are able to move I nano-scale devices which can combine to form the shapes of around each other to form a variety of shapes. Containing ru- physical objects, reassembling themselves as we needed. An dimentary processors and drawing electricity from a board that ensemble of material called catoms that contains sufficient local they rest upon. So far only four catoms have been operated to- computation, actuation, storage, energy, sensing & communica- gether. The plan though is to have thousands of them moving tion which can be programmed to form interesting dynamic around each other to form whatever shape is desired and to shapes and configurations. -
Smart Dust: Communicating with a Cubic- Millimeter Computer
COVER FEATURE Smart Dust: Communicating with a Cubic- Millimeter Computer The Smart Dust project is probing microfabrication technology’s limitations to determine whether an autonomous sensing, computing, and communication system can be packed into a cubic-millimeter mote to form the basis of integrated, massively distributed sensor networks. Brett ecreasing computing device size, increased • monitoring environmental conditions that affect Warneke connectivity, and enhanced interaction with crops and livestock; the physical world have characterized com- • building virtual keyboards; Matt Last puting’s history. Recently, the popularity of • managing inventory control; Brian Dsmall computing devices, such as handheld • monitoring product quality; Liebowitz computers and cell phones, burgeoning Internet • constructing smart-office spaces; and growth, and the diminishing size and cost of sensors— • providing interfaces for the disabled. Kristofer S.J. especially transistors—have accelerated these trends. Pister The emergence of small computing elements, with SMART DUST REQUIREMENTS University of sporadic connectivity and increased interaction with Smart Dust requires both evolutionary and revolu- California, the environment, provides enriched opportunities to tionary advances in miniaturization, integration, and Berkeley reshape interactions between people and computers energy management. Designers can use microelectro- and spur ubiquitous computing research.1 mechanical systems (MEMS) to build small sensors, The Smart Dust project2 is exploring whether an optical communication components, and power sup- autonomous sensing, computing, and communication plies, whereas microelectronics provides increasing system can be packed into a cubic-millimeter mote (a functionality in smaller areas, with lower energy con- small particle or speck) to form the basis of integrated, sumption. Figure 1 shows the conceptual diagram of massively distributed sensor networks. -
Kent Academic Repository Full Text Document (Pdf)
Kent Academic Repository Full text document (pdf) Citation for published version Arief, Budi and Blythe, Phil and Fairchild, Richard and Selvarajah, Kirusnapillai and Tully, Alan (2008) Integrating Smartdust into Intelligent Transportation System. In: 10th International Conference on Application of Advanced Technologies in Transportation (AATT 2008), 27-31 May 2008, Athens, Greece. DOI Link to record in KAR https://kar.kent.ac.uk/58716/ Document Version UNSPECIFIED Copyright & reuse Content in the Kent Academic Repository is made available for research purposes. Unless otherwise stated all content is protected by copyright and in the absence of an open licence (eg Creative Commons), permissions for further reuse of content should be sought from the publisher, author or other copyright holder. Versions of research The version in the Kent Academic Repository may differ from the final published version. Users are advised to check http://kar.kent.ac.uk for the status of the paper. Users should always cite the published version of record. Enquiries For any further enquiries regarding the licence status of this document, please contact: [email protected] If you believe this document infringes copyright then please contact the KAR admin team with the take-down information provided at http://kar.kent.ac.uk/contact.html INTEGRATING SMARTDUST INTO INTELLIGENT TRANSPORTATION SYSTEMS Budi Arief1, Phil Blythe2, Richard Fairchild3, Kirusnapillai Selvarajah4, Alan Tully5 ABSTRACT. The last few years have seen the emergence of many new technologies that can potentially have major impacts on Intelligent Transportation Systems (ITS). One of these technologies is a micro-electromechanical device called smartdust. A smartdust device (or a mote) is typically composed of a processing unit, some memory, and a radio chip, which allows it to communicate wirelessly with other motes within range. -
A Novel Concept for the Study of Heterogeneous Robotic Swarms
Swarmanoid: a novel concept for the study of heterogeneous robotic swarms M. Dorigo, D. Floreano, L. M. Gambardella, F. Mondada, S. Nolfi, T. Baaboura, M. Birattari, M. Bonani, M. Brambilla, A. Brutschy, D. Burnier, A. Campo, A. L. Christensen, A. Decugni`ere, G. Di Caro, F. Ducatelle, E. Ferrante, A. F¨orster, J. Martinez Gonzales, J. Guzzi, V. Longchamp, S. Magnenat, N. Mathews, M. Montes de Oca, R. O’Grady, C. Pinciroli, G. Pini, P. R´etornaz, J. Roberts, V. Sperati, T. Stirling, A. Stranieri, T. St¨utzle, V. Trianni, E. Tuci, A. E. Turgut, and F. Vaussard. IRIDIA – Technical Report Series Technical Report No. TR/IRIDIA/2011-014 July 2011 IRIDIA – Technical Report Series ISSN 1781-3794 Published by: IRIDIA, Institut de Recherches Interdisciplinaires et de D´eveloppements en Intelligence Artificielle Universite´ Libre de Bruxelles Av F. D. Roosevelt 50, CP 194/6 1050 Bruxelles, Belgium Technical report number TR/IRIDIA/2011-014 The information provided is the sole responsibility of the authors and does not necessarily reflect the opinion of the members of IRIDIA. The authors take full responsibility for any copyright breaches that may result from publication of this paper in the IRIDIA – Technical Report Series. IRIDIA is not responsible for any use that might be made of data appearing in this publication. IEEE ROBOTICS & AUTOMATION MAGAZINE, VOL. X, NO. X, MONTH 20XX 1 Swarmanoid: a novel concept for the study of heterogeneous robotic swarms Marco Dorigo, Dario Floreano, Luca Maria Gambardella, Francesco Mondada, Stefano Nolfi, Tarek Baaboura, -
Pairbot: a Novel Model for Autonomous Mobile Robot Systems
Pairbot:ANOVEL MODEL FOR AUTONOMOUS MOBILE ROBOT SYSTEMS CONSISTING OF PAIRED ROBOTS APREPRINT Yonghwan Kim Yoshiaki Katayama Koichi Wada Department of Computer Science Department of Computer Science Department of Applied Informatics Nagoya Institute of Technology Nagoya Institute of Technology Hosei University Aichi, Japan Aichi, Japan Tokyo, Japan [email protected] [email protected] [email protected] October 1, 2020 ABSTRACT Programmable matter consists of many self-organizing computational entities which are autonomous and cooperative with one another to achieve a goal and it has been widely studied in various fields, e.g., robotics or mobile agents, theoretically and practically. In the field of computer science, programmable matter can be theoretically modeled as a distributed system consisting of simple and small robots equipped with limited capabilities, e.g., no memory and/or no geometrical coordination. A lot of theoretical research is studied based on such theoretical models, to clarify the relation between the solvability of various problems and the considered models. We newly propose a computational model named Pairbot model where two autonomous mobile robots operate as a pair on a grid plane. In Pairbot model, every robot has the one robot as its unique partner, called buddy, each other. We call the paired two robots pairbot. Two robots in one pairbot can recognize each other, and repeatedly change their geometrical relationships, long and short, to achieve the goal. In this paper, as a first step to show the feasibility and effectiveness of the proposed Pairbot model, we introduce two simple problems, the marching problem and the object coating problem, and propose two algorithms to solve these two problems, respectively. -
Smart Dust Technology
250, Mini-Project Report Amy Haas Smart Dust Technology Smart dust is an emerging technology with a huge potential for becoming an internationally successful commercial venture. Now is the best time to invest in smart dust – right at the point at which the scientific community is close to perfecting the technology and its applications but its potential has not yet been realized by the capitalist market. Fundamental Concept Smart dust is a theoretical concept of a tiny wireless sensor network, made up of microelectromechanical sensors (called MEMS), robots, or devices, usually referred to as motes, that have self-contained sensing, computation, communication and power1. According to the smart dust project design created by a team of UC Berkeley researchers2, within each of these motes is an integrated package of “MEMS sensors, a semiconductor laser diode and MEMS beam-steering mirror for active optical transmission, a MEMS corner-cube retroreflector for passive optical transmission, an optical receiver, signalprocessing and control circuitry, and a power source based on thick-film batteries and solar cells.” The intent is that these motes will eventually become the size of a grain of sand or a dust particle, hence the name “smart dust”, but the technology still has a long way to go to achieve its target size. In current sensor technology, the sensors are about the size of a bottle cap or small coin. As with most electronic devices or technologies, the biggest challenges in achieving actual smart dust are the power consumption issues and making the batteries small enough. Although there is a lot of work being done on solar cells to keep the motes self-sustaining, the components are just not small enough yet to actually be considered smart dust. -
Jul 2 7 2000
THE SNAP! TOOLKIT FOR DEVELOPING SENSOR NETWORKS AND APPLICATION TO XC SKIING BY MATTHEW B. DEBSKI Submitted to the Department of Electrical Engineering and Computer Science in Partial Fulfillment of the Requirements for the Degrees of Bachelor of Science in Electrical Engineering and Computer Science and Master of Engineering in Electrical Engineering and Computer Science at the MASSACHUSETTS INSTITUTE OF TECHNOLOGY May 2000 2 20C: MASSACHUSETTS INSTITUTE © Massachusetts Institute of Technology 2000. All rights reserved. OF TECHNOLOGY JUL 2 7 2000 LIBRARIES Author Department of Electrical Engineering and Computer Science May 18, 2000 Certified by MichaelJ. Hawley Assistant Prolssor of Media Arts and Sciences Alex Dreyfoos Jr. (1954) Career Development Professor of Media Arts and Sciences Thesis Supervisor Accepted by Arthur C. Smith Chairman, Department Committee on Graduate Theses ' pT THE SNAP! TOOLKIT FOR DEVELOPING SENSOR NETWORKS AND APPLICATION TO XC SKIING BY MATTHEW B. DEBSKI Submitted to the Department of Electrical Engineering and Computer Science in Partial Fulfillment of the Requirements for the Degrees of Bachelor of Science in Electrical Engineering and Computer Science and Master of Engineering in Electrical Engineering and Computer Science May 18, 2000 ABSTRACT Athletes, health professionals, animal specialists, meteorologists, and other investigators increasingly employ small, human-scale sensor networks in their disciplines. The sensor networks used by each field and study have unique requirements. Regardless, these networks all collect and store data, and often display or transmit them. The Snap! toolkit takes advantage of the similarities among sensor networks to make prototyping them fast and easy. Simultaneously, it acknowledges their inherent differences, remaining flexible in order to accommodate the needs of different systems. -
Survey on Terahertz Nanocommunication and Networking
1 Survey on Terahertz Nanocommunication and Networking: A Top-Down Perspective Filip Lemic∗, Sergi Abadaly, Wouter Tavernierz, Pieter Stroobantz, Didier Collez, Eduard Alarcon´ y, Johann Marquez-Barja∗, Jeroen Famaey∗ ∗Internet Technology and Data Science Lab (IDLab), Universiteit Antwerpen - imec, Belgium yNaNoNetworking Center in Catalunya (N3Cat), Universitat Politecnica` de Catalunya, Spain zInternet Technology and Data Science Lab (IDLab), Ghent University - imec, Belgium Email: fi[email protected] Abstract—Recent developments in nanotechnology herald Communication and coordination among the nanodevices, nanometer-sized devices expected to bring light to a number of as well as between them and the macro-scale world, will groundbreaking applications. Communication with and among be required to achieve the full promise of such applications. nanodevices will be needed for unlocking the full potential of such applications. As the traditional communication approaches Thus, several alternative nanocommunication paradigms have cannot be directly applied in nanocommunication, several alter- emerged in the recent years, the most promising ones being native paradigms have emerged. Among them, electromagnetic electromagnetic, acoustic, mechanical, and molecular commu- nanocommunication in the terahertz (THz) frequency band is nication [2]. particularly promising, mainly due to the breakthrough of novel In molecular nanocommunication, a transmitting device materials such as graphene. For this reason, numerous research efforts are nowadays targeting THz band nanocommunication releases molecules into a propagation medium, with the and consequently nanonetworking. As it is expected that these molecules being used as the information carriers [3]. Acoustic trends will continue in the future, we see it beneficial to nanocommunication utilizes pressure variations in the (fluid summarize the current status in these research domains. -
Bringing Reality to Evolution of Modular Robots: Bio-Inspired Techniques for Building a Simulation Environment in the SYMBRION Project
Bringing reality to evolution of modular robots: bio-inspired techniques for building a simulation environment in the SYMBRION project Martin Saska and Vojtechˇ Vonasek´ and Miroslav Kulich and Daniel Fiserˇ and Toma´sˇ Krajn´ık and Libor Preuˇ cilˇ Abstract— Two neural network (NN) based techniques for building a simulation environment, which is employed for evolution of modular robots in the Symbrion project, are presented in this paper. The methods are able to build models of real world with variable accuracy and amount of stored information depending upon the performed tasks and evolu- tionary processes. In this paper, the presented algorithms are verified via experiments in scenarios designed to demonstrate the process of autonomous creation of complex artificial organ- Fig. 1. A modular robot overcoming a pit between two ramps. isms. Performance of the methods is compared in experiments with real data and their employability in modular robotics is discussed. Beside these, the entire process of environment data acquisition and pre-processing during the real evolutionary cess of simulation environment building. These required fea- experiments in the Symbrion project will be briefly described. tures will be verified and discussed in the experimental part Finally, a sketch of integration of gained models of environment of this paper. The first requirement is precision of the gained into a simulator, which enables to fasten the evolution of a real complex modular robot, will be introduced. model. Only simulations realised with models matching the reality are meaningful for trials with real robots. Here, one I. INTRODUCTION should mention that important aspects of the model precision are not limited to shape and size of objects in the robots’ A valuable representation of environment is an important workspace only but also additional properties important for part of modular systems aiming to employ evolutionary the simulation of movement and friction of robots on objects’ principles for creating a complex robot from simple au- surfaces need to be considered. -
Interactive Robots in Experimental Biology 3 4 5 6 Jens Krause1,2, Alan F.T
1 2 Interactive Robots in Experimental Biology 3 4 5 6 Jens Krause1,2, Alan F.T. Winfield3 & Jean-Louis Deneubourg4 7 8 9 10 11 12 1Leibniz-Institute of Freshwater Ecology and Inland Fisheries, Department of Biology and 13 Ecology of Fishes, 12587 Berlin, Germany; 14 2Humboldt-University of Berlin, Department for Crop and Animal Sciences, Philippstrasse 15 13, 10115 Berlin, Germany; 16 3Bristol Robotics Laboratory, University of the West of England, Coldharbour Lane, Bristol 17 BS16 1QY, UK; 18 4Unit of Social Ecology, Campus Plaine - CP 231, Université libre de Bruxelles, Bd du 19 Triomphe, B-1050 Brussels - Belgium 20 21 22 23 24 25 26 27 28 Corresponding author: Krause, J. ([email protected]), Leibniz Institute of Freshwater 29 Ecology and Inland Fisheries, Department of the Biology and Ecology of Fishes, 30 Müggelseedamm 310, 12587 Berlin, Germany. 31 32 33 1 33 Interactive robots have the potential to revolutionise the study of social behaviour because 34 they provide a number of methodological advances. In interactions with live animals the 35 behaviour of robots can be standardised, morphology and behaviour can be decoupled (so that 36 different morphologies and behavioural strategies can be combined), behaviour can be 37 manipulated in complex interaction sequences and models of behaviour can be embodied by 38 the robot and thereby be tested. Furthermore, robots can be used as demonstrators in 39 experiments on social learning. The opportunities that robots create for new experimental 40 approaches have far-reaching consequences for research in fields such as mate choice, 41 cooperation, social learning, personality studies and collective behaviour. -
Introduction to Modular Robots
Introduction to modular robots Speakers Houxiang Zhang Juan González Gómez Houxiang Zhang 1 Houxiang Zhang 2 Outline of today’s talk ● What is a modular robot? ● Review of modular robots – Classification – History of modular robots – Challenging ● From Y1 to GZ -I, our modular robot – Y1 modular robot and related research – GZ-I module ● Control hardware realization ● Locomotion controlling method ● Current research Houxiang Zhang 3 Acknowledgments ● ““BioinspirationBioinspirationand Robotics: Walking and Climbing Robots” Edited by: Maki K. Habib, Publisher: I-Tech Education and Publishing, Vienna, Austria, ISBN 978-3-902613-15-8. – http://s.i-techonline.com/Book/ ● Other great work and related information on the internet – http://en.wikipedia.org/wiki/Self- Reconfiguring_Modular_Robotics Houxiang Zhang 4 Lecture material ● Modular Self-Reconfigurable Robot Systems: Challenges and Opportunities for the Future , by Yim, Shen, Salemi, Rus, Moll, Lipson, Klavins & Chirikjian, published in IEEE Robotics & Automation Magazine March 2007. ● Self-Reconfigurable Robot: Shape-Changing Cellular Robots Can Exceed Conventional Robot Flexibility, by Murata & Kurokawa, published in IEEE Robotics & Automation Magazine March 2007. ● Locomotion Princippfles of 1D Top pgyology Pitch and Pitch-Yaw-Connecting Modular Robots, by Juan Gonzalez-Gomez, Houxiang Zhang, Eduardo Boemo, One Chapter in Book of "Bioinspiration and Robotics: Walking and Climbing Robots", 2007, pp.403- 428. ● Locomotion Capabilities of a Modular Robot with Eight Pitch-Yaw-Connecting -
Wolfbot: a Distributed Mobile Sensing Platform for Research and Education
Proceedings of 2014 Zone 1 Conference of the American Society for Engineering Education (ASEE Zone 1) WolfBot: A Distributed Mobile Sensing Platform for Research and Education Joseph Betthauser, Daniel Benavides, Jeff Schornick, Neal O’Hara, Jimit Patel, Jeremy Cole, Edgar Lobaton Abstract— Mobile sensor networks are often composed of agents with weak processing capabilities and some means of mobility. However, recent developments in embedded systems have enabled more powerful and portable processing units capable of analyzing complex data streams in real time. Systems with such capabilities are able to perform tasks such as 3D visual localization and tracking of targets. They are also well-suited for environmental monitoring using a combination of cameras, microphones, and sensors for temperature, air-quality, and pressure. Still there are few compact platforms that combine state of the art hardware with accessible software, an open source design, and an affordable price. In this paper, we present an in- depth comparison of several mobile distributed sensor network platforms, and we introduce the WolfBot platform which offers a balance between capabilities, accessibility, cost and an open- design. Experiments analyzing its computer-vision capabilities, power consumption, and system integration are provided. Index Terms— Distributed sensing platform, Swarm robotics, Open design platform. I. INTRODUCTION ireless sensor networks have been used in a variety of Wapplications including surveillance for security purposes [30], monitoring of wildlife [36], [25], [23], Fig 1.WolfBot mobile sensing platform and some of its features. and measuring pollutant concentrations in an environment [37] [24]. Initially, compact platforms were deployed in order to As the number of mobile devices increases, tools for perform low-bandwidth sensing (e.g., detecting motion or distributed control and motion planning for swarm robotic recording temperature) and simple computations.