Fe2o3-Based Oxygen Carriers for Gaseous and Solid-Fueled Chemical Looping Processes
Total Page:16
File Type:pdf, Size:1020Kb
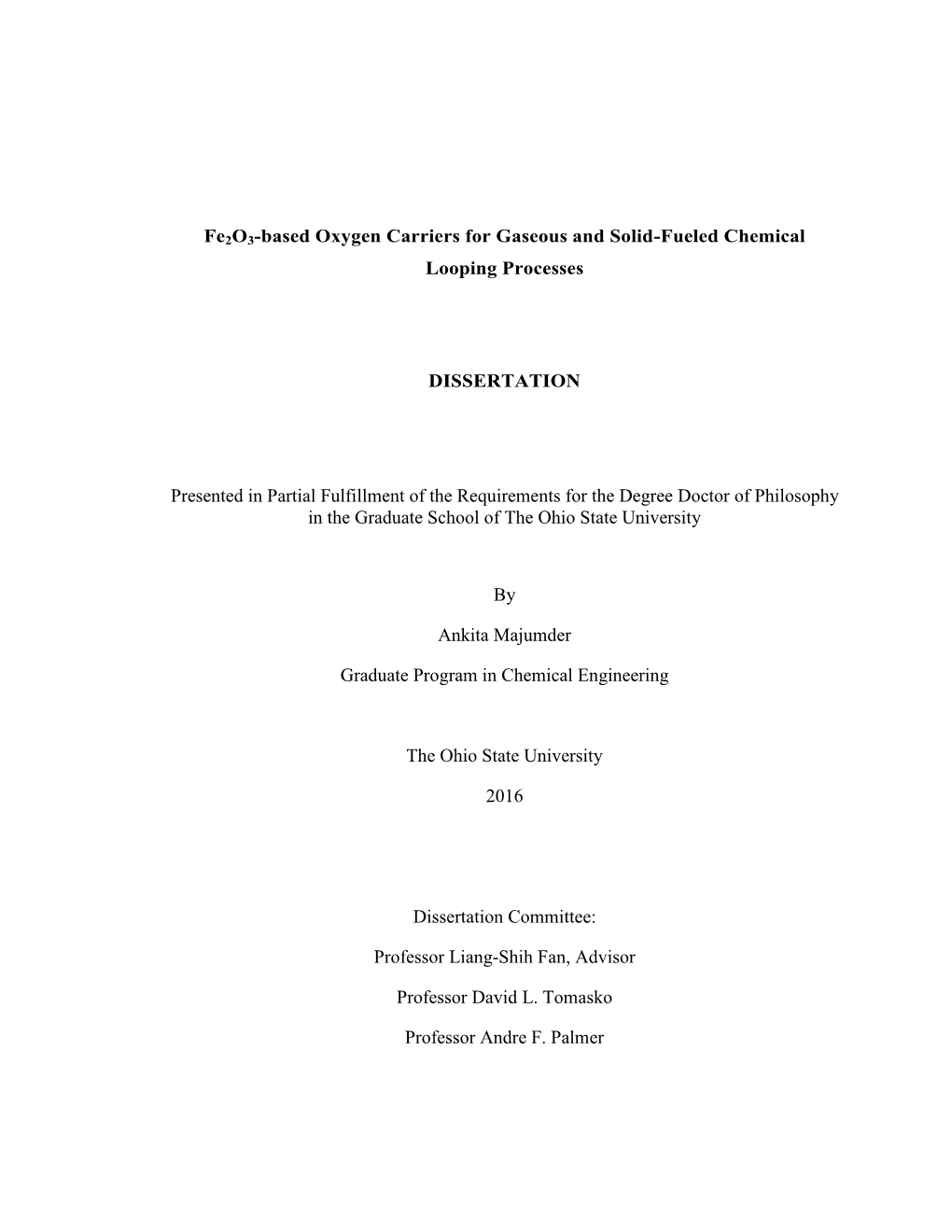
Load more
Recommended publications
-
Iron (III) Oxide Anhydrous
Material Safety Data Sheet Iron (III) Oxide Anhydrous MSDS# 11521 Section 1 - Chemical Product and Company Identification MSDS Name: Iron (III) Oxide Anhydrous Catalog Numbers: I116-3, I116-500 Synonyms: Ferric Oxide Red; Iron (III) Oxide; Iron Sesquioxide; Red Iron Oxide. Fisher Scientific Company Identification: One Reagent Lane Fair Lawn, NJ 07410 For information in the US, call: 201-796-7100 Emergency Number US: 201-796-7100 CHEMTREC Phone Number, US: 800-424-9300 Section 2 - Composition, Information on Ingredients ---------------------------------------- CAS#: 1309-37-1 Chemical Name: Iron (III) Oxide %: 100 EINECS#: 215-168-2 ---------------------------------------- Hazard Symbols: None listed Risk Phrases: None listed Section 3 - Hazards Identification EMERGENCY OVERVIEW Warning! May cause respiratory tract irritation. May cause mechanical eye and skin irritation. Inhalation of fumes may cause metal-fume fever. Causes severe digestive tract irritation with pain, nausea, vomiting and diarrhea. May corrode the digestive tract with hemorrhaging and possible shock. Target Organs: None. Potential Health Effects Eye: Dust may cause mechanical irritation. Skin: Dust may cause mechanical irritation. May cause severe and permanent damage to the digestive tract. May cause liver damage. Causes severe pain, Ingestion: nausea, vomiting, diarrhea, and shock. May cause hemorrhaging of the digestive tract. The toxicological properties of this substance have not been fully investigated. Dust is irritating to the respiratory tract. Inhalation of fumes may cause metal fume fever, which is characterized Inhalation: by flu-like symptoms with metallic taste, fever, chills, cough, weakness, chest pain, muscle pain and increased white blood cell count. Chronic: Chronic inhalation may cause effects similar to those of acute inhalation. -
Research Article the Oxygen Generation Performance of Hollow-Structured Oxygen Candle for Refuge Space
Hindawi Journal of Chemistry Volume 2018, Article ID 7469783, 9 pages https://doi.org/10.1155/2018/7469783 Research Article The Oxygen Generation Performance of Hollow-Structured Oxygen Candle for Refuge Space Weixiang Wang,1,2 Longzhe Jin,1,2 Na Gao ,1,2 Jianlin Wang,1 and Mingyang Liu1 1School of Civil and Resource Engineering, University of Science and Technology Beijing, Beijing 100083, China 2Mine Emergency Technology Research Center, Beijing 100083, China Correspondence should be addressed to Na Gao; [email protected] Received 26 May 2018; Revised 27 August 2018; Accepted 22 October 2018; Published 2 December 2018 Academic Editor: Albert Demonceau Copyright © 2018 Weixiang Wang et al. ,is is an open access article distributed under the Creative Commons Attribution License, which permits unrestricted use, distribution, and reproduction in any medium, provided the original work is properly cited. To improve oxygen generation performance, we dissected and analyzed the incompletely reacted oxygen candles and thus proposed the concept of the hollow-structured oxygen candle. We calculated the surface area ratio and designed the mold for hollow-structured oxygen candles at a radius of 0, 5, 9, 12, 15.5, and 20 mm. ,e structural stability of the oxygen candles was tested by the loading experiment. ,e oxygen generation rate (OGR) and other properties were explored by combustion ex- periments. ,e composition of the oxygen candles and the residual solids after combustion were observed with scanning electron microscope (SEM). ,e results show that, with the increase of the hollow-structure radius (r), the stability of the hollow-structured oxygen candles gradually weakens, and the oxygen candles cannot be made when r is 20 mm. -
Depositional Setting of Algoma-Type Banded Iron Formation Blandine Gourcerol, P Thurston, D Kontak, O Côté-Mantha, J Biczok
Depositional Setting of Algoma-type Banded Iron Formation Blandine Gourcerol, P Thurston, D Kontak, O Côté-Mantha, J Biczok To cite this version: Blandine Gourcerol, P Thurston, D Kontak, O Côté-Mantha, J Biczok. Depositional Setting of Algoma-type Banded Iron Formation. Precambrian Research, Elsevier, 2016. hal-02283951 HAL Id: hal-02283951 https://hal-brgm.archives-ouvertes.fr/hal-02283951 Submitted on 11 Sep 2019 HAL is a multi-disciplinary open access L’archive ouverte pluridisciplinaire HAL, est archive for the deposit and dissemination of sci- destinée au dépôt et à la diffusion de documents entific research documents, whether they are pub- scientifiques de niveau recherche, publiés ou non, lished or not. The documents may come from émanant des établissements d’enseignement et de teaching and research institutions in France or recherche français ou étrangers, des laboratoires abroad, or from public or private research centers. publics ou privés. Accepted Manuscript Depositional Setting of Algoma-type Banded Iron Formation B. Gourcerol, P.C. Thurston, D.J. Kontak, O. Côté-Mantha, J. Biczok PII: S0301-9268(16)30108-5 DOI: http://dx.doi.org/10.1016/j.precamres.2016.04.019 Reference: PRECAM 4501 To appear in: Precambrian Research Received Date: 26 September 2015 Revised Date: 21 January 2016 Accepted Date: 30 April 2016 Please cite this article as: B. Gourcerol, P.C. Thurston, D.J. Kontak, O. Côté-Mantha, J. Biczok, Depositional Setting of Algoma-type Banded Iron Formation, Precambrian Research (2016), doi: http://dx.doi.org/10.1016/j.precamres. 2016.04.019 This is a PDF file of an unedited manuscript that has been accepted for publication. -
Earth Systems Science Grades 9-12
Earth Systems Science Grades 9-12 Lesson 2: The Irony of Rust The Earth can be considered a family of four major components; a biosphere, atmosphere, hydrosphere, and geosphere. Together, these interacting and all-encompassing subdivisions constitute the structure and dynamics of the entire Earth. These systems do not, and can not, stand alone. This Module demonstrates, at every grade level, the concept that one system depends on every other for molding the Earth into the world we know. For example, the biosphere could not effi ciently prosper as is without gas exchange from the atmosphere, liquid water from the hydrosphere, and food and other materials provided by the geosphere. Similarly, the other systems are signifi cantly affected by the biosphere in one way or another. This Module uses Earth’s systems to provide the ultimate lesson in teamwork. March 2006 2 JOURNEY THROUGH THE UNIVERSE Lesson 2: The Irony of Rust Lesson at a Glance Lesson Overview In this lesson, students will investigate the chemistry of rust—the forma- tion of iron oxide (Fe2O3)—within a modern context, by experimenting with the conditions under which iron oxide forms. Students will apply what they have learned to deduce the atmospheric chemistry at the time that the sediments, which eventually became common iron ore found in the United States and elsewhere, were deposited. Students will interpret the necessary formation conditions of this iron-bearing rock in the context of Earth’s geochemical history and the history of life on Earth. Lesson Duration Four 45-minute class periods plus 10 minutes a day for maintence and observation for two weeks Core Education Standards National Science Education Standards Standard B3: A large number of important reactions involve the transfer of either electrons (oxidation/reduction reactions) or hydrogen ions (acid/base reactions) between reacting ions, molecules, or atoms. -
Banded Iron Formations
Banded Iron Formations Cover Slide 1 What are Banded Iron Formations (BIFs)? • Large sedimentary structures Kalmina gorge banded iron (Gypsy Denise 2013, Creative Commons) BIFs were deposited in shallow marine troughs or basins. Deposits are tens of km long, several km wide and 150 – 600 m thick. Photo is of Kalmina gorge in the Pilbara (Karijini National Park, Hamersley Ranges) 2 What are Banded Iron Formations (BIFs)? • Large sedimentary structures • Bands of iron rich and iron poor rock Iron rich bands: hematite (Fe2O3), magnetite (Fe3O4), siderite (FeCO3) or pyrite (FeS2). Iron poor bands: chert (fine‐grained quartz) and low iron oxide levels Rock sample from a BIF (Woudloper 2009, Creative Commons 1.0) Iron rich bands are composed of hematitie (Fe2O3), magnetite (Fe3O4), siderite (FeCO3) or pyrite (FeS2). The iron poor bands contain chert (fine‐grained quartz) with lesser amounts of iron oxide. 3 What are Banded Iron Formations (BIFs)? • Large sedimentary structures • Bands of iron rich and iron poor rock • Archaean and Proterozoic in age BIF formation through time (KG Budge 2020, public domain) BIFs were deposited for 2 billion years during the Archaean and Proterozoic. There was another short time of deposition during a Snowball Earth event. 4 Why are BIFs important? • Iron ore exports are Australia’s top earner, worth $61 billion in 2017‐2018 • Iron ore comes from enriched BIF deposits Rio Tinto iron ore shiploader in the Pilbara (C Hargrave, CSIRO Science Image) Australia is consistently the leading iron ore exporter in the world. We have large deposits where the iron‐poor chert bands have been leached away, leaving 40%‐60% iron. -
Combustion of Iron Wool – Student Sheet
Combustion of iron wool – Student sheet To study Iron is a metal. Iron wool is made up of thin strands of iron loosely bundled together. Your teacher has attached a piece of iron wool to a see-saw balance. At the other end of the see-saw is a piece of Plasticine. Iron wool can combust. Your teacher is going to make the iron wool combust by heating it. If there is a change in mass, the see-saw will either tip to the left or to the right. To discuss or to answer 1 What do you think will happen? ............................................................................................................................................................. 2 Why do you think this will happen? ............................................................................................................................................................. ............................................................................................................................................................. 3 What do you see happen when it is demonstrated? ............................................................................................................................................................. 4 Was your prediction correct? ............................................................................................................................................................. Nuffield Practical Work for Learning: Model-based Inquiry • Combustion of iron wool • Student sheets page 1 of 4 © Nuffield Foundation 2013 • downloaded from -
Iron Oxide Pigments Data Sheet
90 IRON OXIDE PIGMENTS (Data in metric tons unless otherwise noted) Domestic Production and Use: Iron oxide pigments (IOPs) were mined domestically by two companies in two States. Mine production, which was withheld to avoid disclosing company proprietary data, decreased in 2019 from that of 2018. Five companies, including the two producers of natural IOPs, processed and sold about 38,000 tons of finished natural and synthetic IOPs with an estimated value of $52 million, significantly below the most recent sales peak of 88,100 tons in 2007. About 59% of natural and synthetic finished IOPs were used in concrete and other construction materials; 11% in plastics; 7% in coatings and paints; 5% in foundry sands and other foundry uses; 3% each in animal food, industrial chemicals, and glass and ceramics; and 9% in other uses. Salient Statistics—United States: 2015 2016 2017 2018 2019e Mine production, crude W W W W W Sold or used, finished natural and synthetic IOP 53,500 48,500 47,300 48,200 38,000 Imports for consumption 176,000 179,000 179,000 179,000 160,000 Exports, pigment grade 8,930 15,800 13,500 11,100 9,900 Consumption, apparent1 221,000 212,000 213,000 216,000 190,000 Price, average value, dollars per kilogram2 1.46 1.46 1.46 1.58 1.40 Employment, mine and mill 55 60 60 60 55 Net import reliance3 as a percentage of: Apparent consumption W W W W W Reported consumption >50 >50 >50 >50 >50 Recycling: None. Import Sources (2015–18): Natural: Spain, 43%; Cyprus, 36%; Austria, 10%; France, 9%; and other, 2%. -
05/2203 Iron Oxide Extraction from Lunar and Martian Regoliths
05/2203 Iron oxide extraction from lunar and Martian regoliths Type of activity: Medium Study (4 months, 25 KEUR) Background The Reformer iron Sponge Cycle (RESC) has been proposed as a valid process to produce highly pure hydrogen from virtually any kind of hydrocarbon fuel on a bed of iron oxide (magnetite Fe3O4), present in the soils of the Moon and Mars. The process has been investigated in the frame of the Ariadna Call for Proposals 04/01 in view of future long-term manned lunar and Martian exploration. The process permits to operate a hydrogen-oxygen fuel cell for electrical power generation by producing hydrogen from either high energy density fuels brought from Earth or from fuels produced in situ (e.g. methane from the Sabatier process of from biomass decomposition). Fuels are converted into a mixture of hydrogen and carbon monoxide in a reforming reactor. In the following Iron Sponge Cycle iron oxide (magnetite/wuestite) is initially reduced by hydrogen and carbon monoxide to a lower oxide or down to iron metal with production of water steam and carbon dioxide. In a second step water steam is passed on the formed iron metal bed; iron oxide is replenished and water steam is reduced to highly pure hydrogen which can be fed without further purification treatments to the anodic compartment of a fuel cell for electrical power generation. The contact mass (iron/iron oxide) properties as size, porosity and composition of the pellets are very critical. The use of pure iron would theoretically maximise the efficiency of the cycle; the lifetime of the pellets is however limited by sintering effects. -
Oxygen Carriers
Oxygen Carriers Prof. Ramesh Chandra Department of Chemistry University of Delhi The main function of red blood cell is - Transfer of O2 from lungs to tissue. Transfer of CO2 from tissue to lungs. To accomplish this function red cells has Oxygen carriers. All aerobic forms of life depends on Oxygen Carriers. The transport and storage of Oxygen is extremely important physiological function and this is done by oxygen carriers. Various types of oxygen carriers occurring in living systems are - Oxygen Found in Metal Present Function carriers Hemoglobin All Mammals Fe(II) Carrier (Hb) Hemerythrin Various marine Fe(III) Carrier (Hr) invertebrates Myoglobin All Mammals Fe(II) Storage (Mb) Hemocyanin Arthropods & Cu(II) Carrier (Hc) Molluscs Dioxygen as Ligand Under appropriate circumstances, Dioxygen molecule become a ligand and this process is called OXYGENATION in which oxygen molecule retains its identity. 1 In ground state of oxygen molecule, it has two unpaired electrons in *(2py) and 1 *(2px) antibonding molecular orbitals. The degeneracy of -molecular orbital leads to Biradical Character of oxygen molecule. The binding of dioxygen by a transition metal involves electron transfer reaction from metal to dioxygen forming a coordinated superoxide ion. The coordinated superoxide ion binds to the metal in an angular as opposed to a perpendicular fashion and usually has a partial negative charge concentrated on the terminal oxygen atom. This superoxide ligand may be stabilized by an electrophile in the distal cavity, for example, the formation of a hydrogen bond. What are the Oxygen Carriers?? Oxygen carriers are compounds which can take up and release the oxygen reversibly. -
Synthetic Oxygen Carriers Related to Biological Systems
Synthetic Oxygen Carriers Related to Biological Systems ROBERT D. JONES, DAVID A. SUMMERVILLE, and FRED BASOLO" Department of Chemistry, North western University, E vanston, lllinois 6020 1 Received September 29, 1978 Confenfs early part of 1978, no attempt has been made to totally cover all aspects of the problem. Rather we have tried to approach the I. Introduction 139 subject in such a way as to complement the other reviews al- II. Nomenclature 139 ready available.2-18Specifically we have largely restricted our 111. Nature of 02 139 attention to the synthetic approaches that have been made to IV. Nature of Bound Dioxygen 140 observe metastable metal-dioxygen complexes of biological V. Natural Oxygen Carriers 143 importance. A. Heme-Containing Proteins, Hb and Mb 143 B. Hemerythrin 146 /I. Nomenclafure C. Hemocyanin 146 VI. Synthetic 02 Carriers 147 The terminology used in this review, referring to oxygen in its A. Porphyrins 147 various forms, is similar to that used by Vaskai5 in his recent B. Schiff Bases 148 review. The term molecular oxygen as used here refers only to VII. Cobalt-Dioxygen Carriers 148 the free uncombined O2 molecule. Unless otherwise specified, A. Early Work 148 it will be used to mean the ground (32g-)state of the molecule. 6. Recent Studies on Cobalt-Dioxygen Complexes The term dioxygen has been used as a generic designation for in Nonaqueous Solutions 149 the O2 moiety in any of its several forms, and can refer to 02 in C. Cobalt-Dioxygen Complexes in either a free or combined state. The only criterion for use of this Aqueous Solution 160 term is the presence of a covalent bond between the oxygen D. -
Iron Oxide Pigments
IRON OXIDE PIGMENTS By Michael J. Potter Domestic survey data and tables were prepared by Richelle J. Ellis, statistical assistant, and the world production table was prepared by Regina R. Coleman, international data coordinator. Natural iron oxides are derived from hematite, which is a red not included in tables 1, 2, and 4. iron oxide mineral; limonites, which vary from yellow to brown, Bayer Corp. introduced two new yellow grades of synthetic such as ochers, siennas, and umbers; and magnetite, which is IOPs, which were geared toward use in standard solvent-based black iron oxide. Synthetic iron oxide pigments are produced paints and coatings, as well as high solids and water-based from basic chemicals. The three major methods for the paints. One of the pigments was being manufactured at the manufacture of synthetic iron oxides are thermal decomposition company’s new iron oxide unit at New Martinsville, WV, and of iron salts or iron compounds, precipitation of iron salts the other yellow pigment was being made at Bayer’s facility usually accompanied by oxidation, and reduction of organic near Sao Paulo, Brazil, specifically for sale in North American compounds by iron (Podolsky and Keller, 1994, p. 765, 772). markets (Bayer Corp., October 23, 2000, Bayer Corp. introduces two new yellow grades of synthetic iron oxide Production pigments for use in architectural paints and coatings, accessed June 21, 2001, at URL http://www.bayerus.com/new/2000/ U.S. output of finished natural (mined) iron oxide pigments 10.23.00.html). (IOPs) sold by processors in 2000 was 87,800 metric tons (t), Laporte plc announced its intention to sell its pigments and about 5% less than in 1999; this category accounted for 51% of additives companies to K-L Holdings Inc., a company the tonnage and 15% of the value of total IOP output. -
Analyses of High-Iron Sedimentary Bedrock and Diagenetic Features Observed with Chemcam at Vera Rubin Ridge, Gale Crater, Mars: Calibration and Characterization G
Analyses of High-Iron Sedimentary Bedrock and Diagenetic Features Observed With ChemCam at Vera Rubin Ridge, Gale Crater, Mars: Calibration and Characterization G. David, A. Cousin, O. Forni, P.-y. Meslin, E. Dehouck, N. Mangold, J. l’Haridon, W. Rapin, O. Gasnault, J. R. Johnson, et al. To cite this version: G. David, A. Cousin, O. Forni, P.-y. Meslin, E. Dehouck, et al.. Analyses of High-Iron Sedimentary Bedrock and Diagenetic Features Observed With ChemCam at Vera Rubin Ridge, Gale Crater, Mars: Calibration and Characterization. Journal of Geophysical Research. Planets, Wiley-Blackwell, 2020, 125 (10), 10.1029/2019JE006314. hal-03093150 HAL Id: hal-03093150 https://hal.archives-ouvertes.fr/hal-03093150 Submitted on 16 Jan 2021 HAL is a multi-disciplinary open access L’archive ouverte pluridisciplinaire HAL, est archive for the deposit and dissemination of sci- destinée au dépôt et à la diffusion de documents entific research documents, whether they are pub- scientifiques de niveau recherche, publiés ou non, lished or not. The documents may come from émanant des établissements d’enseignement et de teaching and research institutions in France or recherche français ou étrangers, des laboratoires abroad, or from public or private research centers. publics ou privés. David Gaël (Orcid ID: 0000-0002-2719-1586) Cousin Agnès (Orcid ID: 0000-0001-7823-7794) Forni Olivier (Orcid ID: 0000-0001-6772-9689) Meslin Pierre-Yves (Orcid ID: 0000-0002-0703-3951) Dehouck Erwin (Orcid ID: 0000-0002-1368-4494) Mangold Nicolas (Orcid ID: 0000-0002-0022-0631) Rapin William (Orcid ID: 0000-0003-4660-8006) Gasnault Olivier (Orcid ID: 0000-0002-6979-9012) Johnson Jeffrey, R.