Standard Dokument for Kongsberg
Total Page:16
File Type:pdf, Size:1020Kb
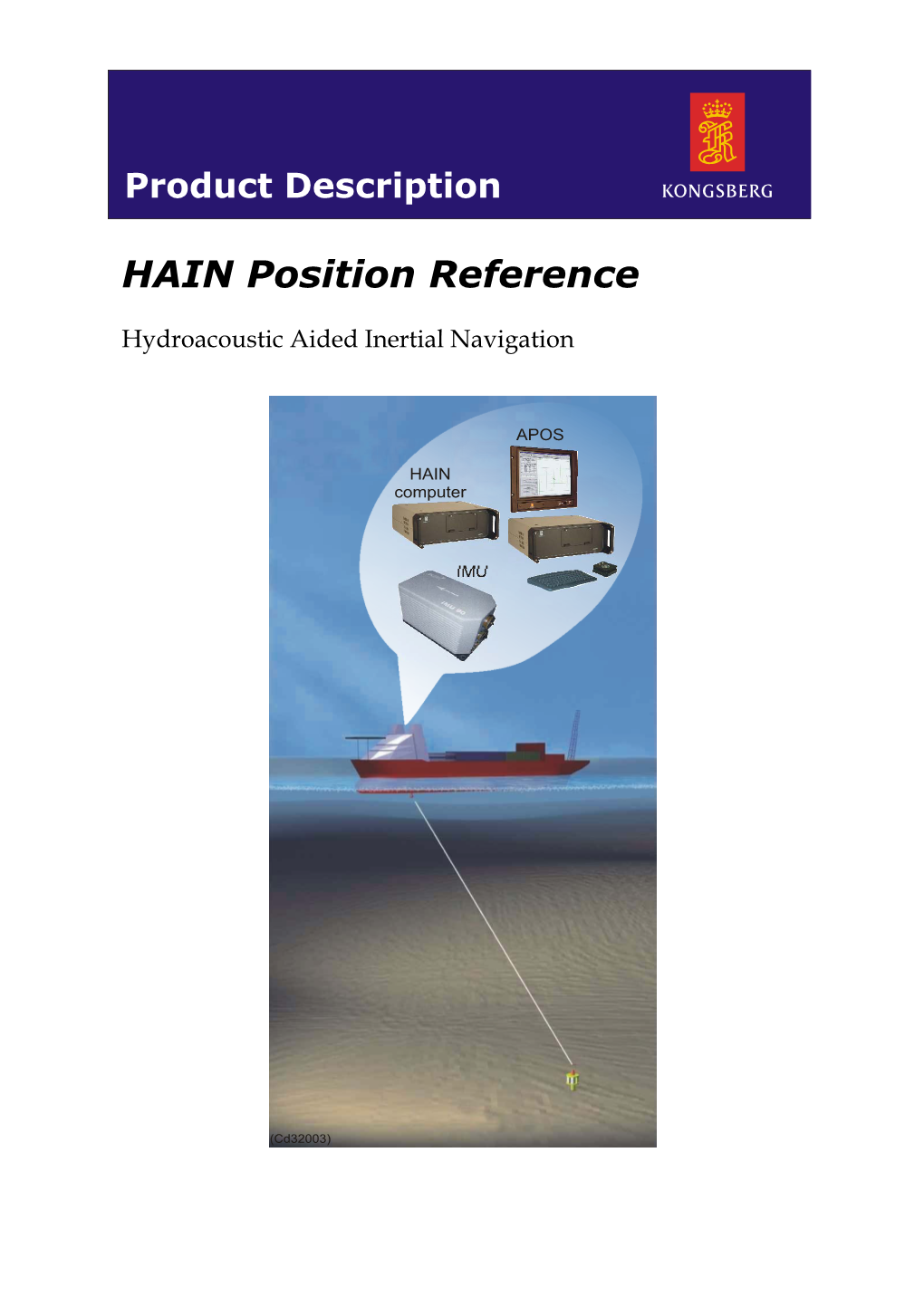
Load more
Recommended publications
-
Problems of Handling Ships Equipped with Azipod Propulsion Systems
PRACE NAUKOWE POLITECHNIKI WARSZAWSKIEJ z. 95 Transport 2013 Lech Kobyliski Foundation for Safety of Navigation and Environment Protection PROBLEMS OF HANDLING SHIPS EQUIPPED WITH AZIPOD PROPULSION SYSTEMS The manuscript delivered, March 2013 Abstract: Large ships, mainly large cruise vessels, built during last two decades are quite often equipped with revolutionary propulsion devices known under the name AZIPODs. There are many reasons for choosing AZIPODs as main propulsion units, the main reason being excellent manoeuvring characteristics achieved. However in case of large propulsion units, having power of 15-25 MW, used for propulsion there are also some disadvantages and limitations, the last mainly related to operational factors. Handling of ships equipped with AZIPODS is different from handling conventional ships and in certain manoeuvring situations safety of the ship and of the propulsion units might be endangered.. Therefore some limitations imposed on handling procedures are necessary and it is essential that pilots and masters of ships fitted with AZIPODs must be specially trained. Keywords: ship manoeuvrability, podded propulsion, handling of ships with Azipods 1. INTRODUCTION During recent times the new type of vessel has been introduced to the world shipping fleet in large numbers. This type is passenger cruise vessel. Statistics of ships in operation and on order reveals that more than 750 ships of different size that could be defined as cruise ships are recently in operation, more than about 50 of them are large ships of more than 250 metres in length and carrying sometimes as much as 6000 passengers. According to the definition cruise ship is usually a very large passenger ship that makes a roundtrip with several en route stops and takes passengers only at the port where trip begins and ends. -
Optimal Thrust Allocation Methods for Dynamic Positioning of Ships
Delft University of Technology Faculty of Electrical Engineering, Mathematics and Computer Science Delft Institute of Applied Mathematics Optimal Thrust Allocation Methods for Dynamic Positioning of Ships A thesis submitted to the Delft Institute of Applied Mathematics in partial fulfillment of the requirements for the degree MASTER OF SCIENCE in APPLIED MATHEMATICS by CHRISTIAAN DE WIT Delft, the Netherlands July 2009 Copyright © 2009 by Christiaan de Wit. All rights reserved. MSc THESIS APPLIED MATHEMATICS “Optimal Thrust Allocation Methods for Dynamic Positioning of Ships” CHRISTIAAN DE WIT Delft University of Technology Daily supervisor Responsible professor Dr. J.W. van der Woude Prof. dr. K.I. Aardal Other thesis committee members M. Gachet, Ingenieur ENSTA Dr. R.J. Fokkink July 2009 Delft, the Netherlands Optimal Thrust Allocation Methods for Dynamic Positioning of Ships Christiaan de Wit July 2009 Environment from Abstract The first Dynamic Positioning (DP) systems emerged in the 1960’s from the need for deep water drilling by the offshore oil and gas industry, as conventional mooring systems, like a jack-up barge or an anchored rig, can only be used in shallow waters. GustoMSC has been developing DP drill ships since the early 1970’s and it is still one of their core businesses. DP systems automatically control the position and heading of a ship subjected to environmental and external forces, using its own actuators. The thrust allocator of a DP system is responsible for the thrust distribution over the actuators of the ship. Apart from minimizing the power consumption an ideal thrust allocator can also take other aspects into account, such as forbidden/spoil zones and thruster relations. -
Integrating INS and GNSS Sensors to Provide Reliable Surface Positioning
Author’s Name Name of the Paper Session DYNAMIC POSITIONING CONFERENCE October 9-10, 2012 SENSORS I SESSION Integrating INS and GNSS Sensors to Provide Reliable Surface Positioning By David Russell VERIPOS David Russell, VERIPOS Integrating INS and GNSS Sensors to Provide Reliable Surface Positioning ABSTRACT The ideal surface positioning system will provide a constant, stable, accurate and repeatable position in real-time which is essential to safe and productive operations. In perfect conditions, GNSS along with augmentation data can deliver this performance and with the modernization of existing constellations and the imminent arrival of new satellite constellations the performance and availability of GNSS should improve. However, while additional observations will be available, the satellite signals are still susceptible to effects of ionosphere scintillation and interference whether intentional or un-intentional plus signal blockage can occur when working close to platforms and this will result in degraded positioning. Inertial Navigation involves determining a position through dead reckoning using gyros and accelerometers to calculate changes in position, velocity and attitude. Inertial Navigation Systems (INS) are completely self contained and inherently robust providing output with exceptional good short term accuracy but the position accuracy will drift with time. INS and GNSS are complementary sensors and when combined can deliver constant, stable, accurate and repeatable positioning. The integration of GNSS and inertial technologies exploits the long term accuracy and precision characteristics of GNSS positioning with the continuous availability and fast update rate of inertial sensors. The resulting integrated system can bridge GNSS disruptions (e.g. ionospheric scintillation, physical obstructions, etc.) as well as detecting position outliers due to common mode failures which can affect vessel GNSS systems simultaneously which is particularly advantageous for DP operations. -
DYNAMIC POSITIONING ACCREDITATION and CERTIFICATION SCHEME STANDARD January 2017
DYNAMIC POSITIONING ACCREDITATION AND CERTIFICATION SCHEME STANDARD Effective Date 1st January 2017 DISCLAIMER While every effort has been made to ensure that all the information in this document is updated and correct, The Nautical Institute cannot be held responsible for any loss, financial or otherwise, direct or indirect, resulting from use of this information. Likewise, The Nautical Institute cannot be held responsible for any damage to property, trainers or operators while following these guidelines. This information is produced in good faith, but we cannot guarantee the accuracy and/or completeness of the information which is produced for guidance purposes only. DYNAMIC POSITIONING ACCREDITATION AND CERTIFICATION SCHEME STANDARD January 2017 © The Nautical Institute 2016 202 Lambeth Road, London, SE1 7LQ - United Kingdom Tel: +44 (0) 207 928 1351 Fax: (0) 207 401 2817 www.nautinst.org www.nialexisplatform.org DPACCSTD-v1.1-Jan 2017 CONTENTS 1. INTRODUCTION TO THE DYNAMIC POSITIONING OPERATOR TRAINING STANDARD ........................... 2 2. OFFSHORE TRAINING SCHEME ............................................................................................................ 6 3. SHUTTLE TANKER TRAINING SCHEME ................................................................................................ 10 4. ACCREDITATION ................................................................................................................................ 13 APPENDIX A - MINIMUM QUALIFICATION REQUIREMENT ............................................................................ -
Saipem Constellation Ultra-Deep Water Rigid & Flexible Pipelay, Heavy Lift, Construction Dp 3 Vessel Saipem Constellation
VESSEL SAIPEM CONSTELLATION ULTRA-DEEP WATER RIGID & FLEXIBLE PIPELAY, HEAVY LIFT, CONSTRUCTION DP 3 VESSEL SAIPEM CONSTELLATION ULTRA-DEEP WATER RIGID & FLEXIBLE PIPELAY, HEAVY LIFT, CONSTRUCTION DP 3 VESSEL VERSATILITY CAPABILITY RELIABILITY HIGH MANOEUVRABILITY ULTRA-DEEP WATER RIGID DP 3, ICE CLASS, HELIDECK AND TRANSIT SPEED REELED/ FLEXIBLE PIPELAY, HEAVY LIFT AND CONSTRUCTION TECHNICAL SPECIFICATIONS* MAIN FEATURES DYNAMIC POSITIONING PIPELAY EQUIPMENT Length overall: 178 m DP 3 system: Kongsberg K-Pos DP Type: combined pipelay tower for reel Moulded breadth: 46 m Position Reference Interface lay and flex lay over a moon pool Moulded depth: 15 m Taut Wire Tensioners: 2 x 400 t (rigid) Draft max.: 10.5 m summer draft 3 DGPS or 2 x 260 t Pipelay type: rigid and flex systems, 1 x Radius Hang-off module: 900 t through moon pool 1 x Spot Track Pipe storage: 8 x 1,200 t reels Pipelay capacity: rigid: 4” - 16” OD Acoustic Reference: 2 for rigid pipe (4 onboard – 4 ashore) flexible: 4” - 24” OD Gyro: 3 2 x 1,250 t under-deck carousels Anemometer: 3 for flexible pipe CLASSIFICATION VRU: 3 A&R system: 2 x 600 t traction winches Det Norske Veritas single or tandem use through moonpool DNV 1A1 Ship Shaped Pipelaying Vessel, POWER GENERATION single through STBD AHC Fairlead Dynpos Autro, ICE-1A, Clean Design 37 MW through 12 gensets (removable) IMO: 9629756 in 4 engine rooms Steel wire rope capacity: 2 x 4,500 m Call sign: C6DW9 Flag: Bahamas CARGO DECK ROVs Deck area: 4,200 m2 (without reels) 2 x Schilling HD work class systems, DESIGN 150 HP, launchable from ROV hangars Held-SH, Crane, EC0, BIS, COMF ACCOMMODATIONS with dedicated moon pools (V3, C3), NAUT-OSV (A) Berth/Cabin: 239 x 1 berth cabin LARS: 2 x launch and recovery systems Total: 239 persons inside the ROV hangars, water depth PROPULSION / DP 4,000 m Stern azimuth thruster aft onboard: DECK EQUIPMENT 2 x Rolls Royce Aquamaster, 6,000 kW ea. -
Dynamic Positioning Nonlinear Control System of the Dredger Based on Profinet IO
JOURNAL OF COMPUTERS, VOL. 8, NO. 2, FEBRUARY 2013 455 Dynamic Positioning Nonlinear Control System of the Dredger Based on Profinet IO Yu-hua Zhang1, 2 1Key Lab of Control of Power Transmission and Transformation, Ministry of Education, Shanghai Jiaotong University, Shanghai, China 2School of Electrical Engineering and Automation, Henan Polytechnic University, Jaozuo, China Email: [email protected] Jian-guo Jiang and Yan-jun Jiang Key Lab of Control of Power Transmission and Transformation, Ministry of Education, Shanghai Jiaotong University, Shanghai, China Email: [email protected], [email protected] Abstract— A dredger’s dynamic positioning system (DPS) is 1st-order wave motions from the low frequency (LF) designed with real-time Profinet IO structure and nonlinear positions while reconstructing LF velocities [4, 5]. All control algorithm. Real-time industrial Ethernet is used in these have been realized by using linear Kalman filter. this system to improve the real-time performance. Unfortunately, the results of Kalman filter are only valid Noise-free estimates of the position and the velocity are locally. This motivates the research on nonlinear ship produced by the observer, and the adaptive dynamic surface control. Backstepping method is the first attempt towards control (ADSC) algorithm is adopted to solve the special problem of the dredger with strong disturbances. nonlinear output feedback control of dynamic positioning Disturbances can be estimated and compensated by system. And a passive nonlinear observer is proposed in adaptive arithmetic. This work solves the contradiction Ref. [6]. between the real-time control requirement and complex Dynamic surface control technique is an improved control algorithms well. -
Dp Operations Guidance
DP OPERATIONS GUIDANCE DP OPERATIONS GUIDANCE PREPARED THROUGH THE DYNAMIC POSITIONING COMMITTEE OF THE MARINE TECHNOLOGY SOCIETY TO AID IN THE SAFE AND EFFECTIVE MANAGEMENT OF DP OPERATIONS PART 2 APPENDIX 1 - DP MODUS APRIL 2021 DP OPERATIONS GUIDANCE - PART 2 - APP 1 (Rev3 - Apr21) MODU 1 DP OPERATIONS GUIDANCE This Dynamic Positioning Guidance was created by the Dynamic Positioning Committee of the Marine Technology Society. The guidelines have been developed from regulations, codes, guidance and industry practice existing at the time of publication, and their purpose is to aid in the safe management of DP operations. This publication was designed and intended as a resource for dynamic positioning professionals. For any other use beyond personal, research or educational purposes, please contact the Marine Technology Society. All rights reserved © Marine Technology Society. 2 DP OPERATIONS GUIDANCE - PART 2 - APP 1 (Rev3 - Apr21) MODU DP OPERATIONS GUIDANCE DISCLAIMER AND LIMITATION OF LIABILITY The information presented in this publication of the Dynamic Positioning Committee of the Marine Technology Society (“DP Committee”) is made available for general information purposes without charge. The DP Committee does not warrant the accuracy, completeness, or usefulness of this information. Any reliance you place on this publication is strictly at your own risk. We disclaim all liability and responsibility arising from any reliance placed on this publication by you or anyone who may be informed of its contents. IN NO EVENT WILL THE DP -
The International Marine Contractors Association ~Yf, F-J F ,‘I’ Y;
.Ly ;y!--)!~ -“I 1 MCA The International Marine Contractors Association ~yf, f-J F ,‘I’ y;. r*:*t:;pQ~p$Tjo)j Represents offshore, marine and underwa er~~rne~r~--qQ~an~es.a.-& __.. i+...,,r 21 September 1998 Docket Management Facility (USCG-1998-37861) - 3 7 US Department of Transportation Room PL-40 1 400 Seventh Street SW Washington DC 20590-00 1 USA Attn: Joseph J Angelo Dear Sir Commercial Diving Operations I art-r responding to the invitation to respond to the Advance notice of proposed rule- making. IMCA, as was its forerunner the Association of Offshore Diving Contractors (AODC), is an international industry association representing offshore Diving and offshore Construction Contractors operating in 30-plus countries. It issues guidance to its members on safe diving practices and safe operation of DP vessels. This guidance is based on 20-plus years’ diving experience from 50-plus diving support vessels. The notice addressed two issues on which IMCA members have considerable expertise: i> diving from dynamically positioned vessels ii) diving supervisors. The enclosed copy of IMCA Guidance document DO10 - ‘Diving Operations from vessels operating in dynamic positioning mode’ - relates to the first. This is the third version of our guidance on this topic - the most recent revision was prompted by a fatal accident on the UK Continental Shelf. The US Coastguard might like to consider the advice contained therein should it decide to regulate in this area. cant/.... Carlyle House, 235 Vauxhall Bridge Road, London, UK, SWlV 1EJ Tel: t44 (0)171-931 8171 Fax: t44 (0)171-931 8935 E-mail: imcaeimca-int.com Inmwmratinrr AON! nnri IIPVOA -2- A copy of the IMCA offshore diving supervisor and life support technician schemes is also enclosed. -
DNVGL-RP-E307: Dynamic Positioning Systems
RECOMMENDED PRACTICE DNVGL-RP-E307 Edition July 2015 Dynamic positioning systems - operation guidance The electronic pdf version of this document found through http://www.dnvgl.com is the officially binding version. The documents are available free of charge in PDF format. DNV GL AS FOREWORD DNV GL recommended practices contain sound engineering practice and guidance. © DNV GL AS July 2015 Any comments may be sent by e-mail to [email protected] This service document has been prepared based on available knowledge, technology and/or information at the time of issuance of this document. The use of this document by others than DNV GL is at the user's sole risk. DNV GL does not accept any liability or responsibility for loss or damages resulting from any use of this document. CHANGES – CURRENT General This document supersedes DNV RP-E307, January 2011. Text affected by the main changes in this edition is highlighted in red colour. However, if the changes involve a whole chapter, section or sub-section, normally only the title will be in red colour. On 12 September 2013, DNV and GL merged to form DNV GL Group. On 25 November 2013 Det Norske Veritas AS became the 100% shareholder of Germanischer Lloyd SE, the parent company of the GL Group, and on 27 November 2013 Det Norske Veritas AS, company registration number 945 748 931, changed its name to DNV GL AS. For further information, see www.dnvgl.com. Any reference in this document to “Det Norske Veritas AS”, “Det Norske Veritas”, “DNV”, “GL”, “Germanischer Lloyd SE”, “GL Group” or any other legal entity name or trading name presently owned by the DNV GL Group shall therefore also be considered a reference to “DNV GL AS”. -
Saipem Constellation
SAIPEM CONSTELLATION ULTRA DEEPWATER RIGID & FLEXIBLE PIPELAY, HEAVY LIFT, CONSTRUCTION DP 3 VESSEL spm_broCON_L12_18_05_02.indd 1 03/05/18 14:09 SAIPEM CONSTELLATION ULTRA DEEPWATER RIGID & FLEXIBLE PIPELAY, HEAVY LIFT, CONSTRUCTION DP 3 VESSEL VERSATILITY CAPABILITY RELIABILITY HIGH MANOEUVRABILITY ULTRA DEEPWATER RIGID REELED/ DP3, ICE-CLASS, HELIDECK AND TRANSIT SPEED FLEXIBLE PIPE LAY, HEAVY LIFT AND CONSTRUCTION TECHNICAL SPECIFICATIONS* SPECIFICATIONS DYNAMIC POSITIONING PIPE LAY EQUIPMENT Length Overall: 178.0 m DP 3 System: KONGSBERG Type: Combined pipelay tower for reel Breadth Moulded: 46.0 m DP Position Reference Interface lay and flex lay over a moonpool Depth Moulded: 15.6 m Taut Wire Tensioners: 2 x 400 mt (Rigid) or Draft Max: 10.5 m DGPS: 2 2 x 260 mt Deck Area: 4,200 m2 Laser Reference: 1 x CyScan, Hang-off Clamp: 900 mt without reels 1 x RadarScan Pipe Storage: 4 x 1,200 mt reels for DP Dynpos Autro Acoustic Reference: 2 rigid pipe (removable) (DP3) Cranes: 1 x 3,000 mt Huisman Gyro: 3 2 x 1,250 mt under-deck Offshore Mast Crane Anemometer: 3 carousels for flexible pipe Pipe Lay Type: Rigid and Flex Systems, VRU: 3 A & R System: 2 x 600 mt traction through moonpool winches, single or tandem use Pipe Lay Capacity: Rigid: 4” - 16” OD ELECTRIC POWER GENERATOR Steel Wire Rope Capacity: 3,800 m x Flexible: 4” - 24” OD 37MW through 12 gensets in 4 engine 125 mm (Ø) each winch rooms CLASSIFICATION ROV Det Norske Veritas CARGO DECK 2 Shilling HD work class systems, DNV 1A1 Ship Shaped Pipelaying Deck Area: 4,200 m2 (without -
IMCA's Work Programme Continues
Issue 68 – September 2013 news from the International Marine Contractors Association Lifting: IMCA’s work programme continues PLUS LATEST SAFETY STATISTICS SPOTLIGHT ON CARL ANNESSA MORE SUCCESSFUL COMPETENCE SEMINARS THE MARITIME LABOUR CONVENTION COMES INTO FORCE Image: Seaway Heavy Lifting International Marine Contractors Association www.imca-int.com From the President issue 68 CONTENTS Massimo Fontolan, Saipem IMCA President 2013 As the industry moves inexorably forward and looks further into the future, evolution is of course inevitable. In addition to working in new geographies and topographies, there are also changes to regulation, legislation and the environment, including the political one. These issues combine to make our contracting activities increasingly difficult; ever more complex, challenging and risk laden. This requires us all to deliver to high standards, and places an emphasis on the need for sustainable and viable contractors in all segments of the market. 3 4 Whilst the business is high profile and often high value, that profile is not FEATURE IMCA always recognised, firstly by our clients and outside the energy sector itself. Recently though, there are signs that the financial world is taking more of an interest in our activities, with the advent of financial investors seeking to take a stake in the funding and control of offshore construction. Although greater involvement and understanding from the wider world is to be welcomed, there should also perhaps be a word or two of caution due to the sensitive nature of the work we are engaged in, as, particularly in the environmental sense, the need for a greater emphasis on safety becomes more and more fundamental to all that we do; on the capacity and capability of the contracting supply chain to deliver, within safety, quality, schedule, and still making a sustainable fair amount of profit. -
DNVGL-RP-E306 Dynamic Positioning Vessel Design
RECOMMENDED PRACTICE DNVGL-RP-E306 Edition July 2015 Dynamic positioning vessel design philosophy guidelines The electronic pdf version of this document found through http://www.dnvgl.com is the officially binding version. The documents are available free of charge in PDF format. DNV GL AS FOREWORD DNV GL recommended practices contain sound engineering practice and guidance. © DNV GL AS July 2015 Any comments may be sent by e-mail to [email protected] This service document has been prepared based on available knowledge, technology and/or information at the time of issuance of this document. The use of this document by others than DNV GL is at the user's sole risk. DNV GL does not accept any liability or responsibility for loss or damages resulting from any use of this document. CHANGES – CURRENT General This document supersedes DNV-RP-E306, September 2012. Text affected by the main changes in this edition is highlighted in red colour. However, if the changes involve a whole chapter, section or sub-section, normally only the title will be in red colour. Main changes July 2015 • General The revision of this document is part of the DNV GL merger, updating the previous DNV service document into a DNV GL format including updated nomenclature and document reference numbering. Changes – current Recommended practice, DNVGL-RP-E306 – Edition July 2015 Page 3 DNV GL AS CONTENTS CHANGES – CURRENT .................................................................................................. 3 Sec.1 Introduction...............................................................................................