DACUM Research Chart for Pipefitter
Total Page:16
File Type:pdf, Size:1020Kb
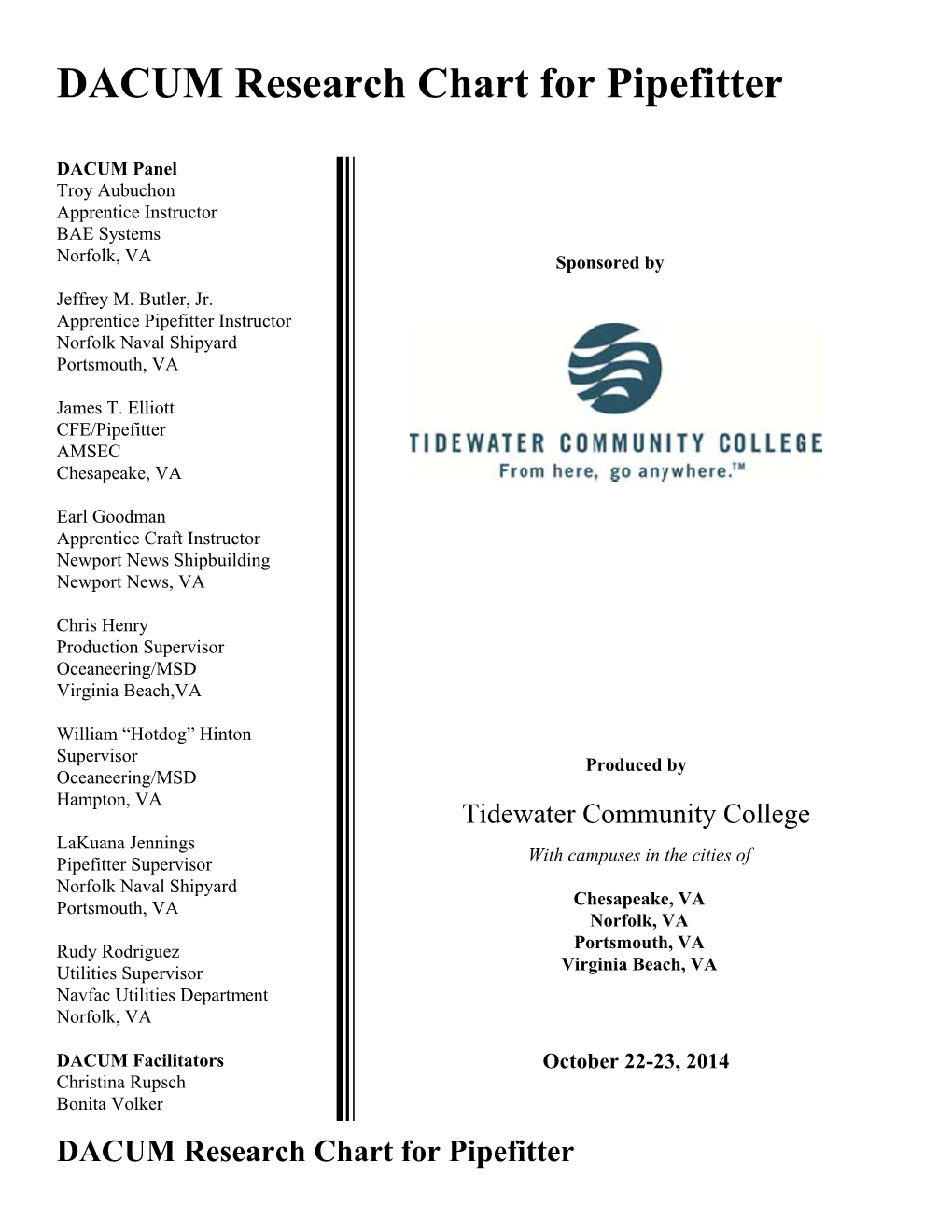
Load more
Recommended publications
-
0074 Steamfitter-Pipefitter Course Outline
Apprenticeship and Industry Training Steamfitter-Pipefitter Apprenticeship Course Outline 0708.1 (2008) ALBERTA ADVANCED EDUCATION AND TECHNOLOGY CATALOGUING IN PUBLICATION DATA Alberta. Alberta Advanced Education and Technology. Apprenticeship and Industry Training. Steamfitter-pipefitter : apprenticeship course outline. ISBN 978-0-7785-6473-7 1. Pipe fitters – Study and teaching – Alberta. 2. Steam-pipes – Study and teaching – Alberta. 3. Apprenticeship programs – Alberta. 4. Apprentices – Alberta. 5. Occupational training – Alberta. I. Title. HD4885.C2.S73.A333 2008 373.27 ALL RIGHTS RESERVED: © 2008, Her Majesty the Queen in right of the Province of Alberta, as represented by the Minister of Alberta Advanced Education and Technology, 10th floor, Commerce Place, Edmonton, Alberta, Canada, T5J 4L5. All rights reserved. No part of this material may be reproduced in any form or by any means, without the prior written consent of the Minister of Advanced Education and Technology Province of Alberta, Canada. Revised 2011. Steamfitter-Pipefitter Table of Contents Apprenticeship ........................................................................................................................................................................... 2 Apprenticeship and Industry Training System ........................................................................................................................ 2 Apprenticeship Safety .................................................................................................................. -
Program Outline
PROGRAM OUTLINE Steamfitter/Pipefitter The latest version of this document is available in PDF format on the ITA website www.itabc.ca To order printed copies of Program Outlines or learning resources (where available) for BC trades contact: Crown Publications, Queen’s Printer Web: www.crownpub.bc.ca Email: [email protected] Toll Free 1 800 663-6105 Copyright © 2014 Industry Training Authority This publication may not be modified in any way without permission of the Industry Training Authority Steamfitter/Pipefitter Industry Training Authority 1 02/16 STEAMFITTER/PIPEFITTER PROGRAM OUTLINE APPROVED BY INDUSTRY NOVEMBER 2011 BASED ON NOA 2010 Developed by Industry Training Authority Province of British Columbia Steamfitter/Pipefitter Industry Training Authority 2 02/16 Introduction TABLE OF CONTENTS Section 1 INTRODUCTION ................................................................................................................ 4 Foreword ........................................................................................................................... 5 Acknowledgements ........................................................................................................... 6 How to Use this Document ................................................................................................ 7 Section 2 PROGRAM OVERVIEW .................................................................................................... 9 Program Credentialing Model ........................................................................................ -
Steamfitter-Pipefitter On-The-Job Training Guide
Steamfitter-Pipefitter On-the-Job Training Guide 2019 Online: www.saskapprenticeship.ca Recognition: To promote transparency and consistency, this document has been adapted from the 2015 Steamfitter- Pipefitter Red Seal Occupational Standard (Employment and Social Development Canada). A complete version of the Occupational Standard can be found at www.red-seal.ca 1 On-the-Job Training Guide – Steamfitter-Pipefitter - 2019 STRUCTURE OF THE ON THE JOB TRAINING GUIDE CONTENT To facilitate understanding of the occupation, this on-the-job training guide contains the following sections: Description of the Steamfitter-Pipefitter trade: an overview of the trade’s duties and training requirements. Essential Skills Summary: an overview of how each of the nine essential skills is applied in this trade. Harmonization: a brief description on the pan-Canadian Harmonization Initiative for the Steamfitter- Pipefitter trade. Task Matrix: a chart which outlines graphically the major work activities, tasks and sub-tasks of this standard detailing the essential skills and the level of training where the content is covered. Major Work Activity (MWA): the largest division within the standard that is comprised of a distinct set of trade activities. Task: distinct actions that describe the activities within a major work activity. Sub-task: distinct actions that describe the activities within a task. On-the-Job and In-school Training Content for the Steamfitter-Pipefitter Trade: a chart which outlines on-the-job examples for apprentices to achieve relevant work experience to prepare for topics of technical training. 2 On-the-Job Training Guide – Steamfitter-Pipefitter - 2019 DESCRIPTION OF THE STEAMFITTER-PIPEFITTER TRADE Steamfitter/Pipefitters install and repair low and high pressure piping systems and their components, including heating and processing applications. -
Steamfitter, Pipefitter, Industrial Pipefitter Industry Training Criteria
- ---~-- ---- - ----~--------------- Steamfitter, Pipefitter, Industrial Pipefitter Industry Training Criteria 0-Net code 47-2152.0lS Sep 2010 Steamfitter/Pipefitter/lndustrial Pipefitter Industry Standards Criteria 0-Net code 47-2152.0lS 1. Length of Training Program sponsors shall establish a minimum of a five (5) year program of not less than 7,200 hours of on-the-job training. 2. Related Supplemental Instruction The required prescribed courses of related and supplemental instruction shall be no less than 216 hours per year. This instruction must include at a minimum the related and supplemental training processes listed in Exhibit "A". 3. On-the-lob Training Skills to be learned. See Exhibit "B". 4. Competency Testing All apprentices must pass a competency test prior to the time of their classification advancement to the next higher period. The tests shall be based on all Related and Supplemental Instruction and manipulative skills tests based. on laboratory assignments. 5. Completion Percentages Program sponsors must have a 45% graduation rate of all apprentices that satisfactorily complete the program's probationary period. 6. Revisions The schedule for revisions to the Plumbing Industry training criteria shall be in accordance with Labor Code-section 212:01. Sep2010 ,--------- EXHIBIT "A" Related and Supplemental Instruction Topics For Steamfitter, Pipe Fitter, and Industrial Pipe Fitter Industry Criteria 0-Net code 47-2152.0lS RELATED AND SUPPLEMENTAL INSTRUCTION 1. Orientation and safety to include OSHA 10 2. Piping mathematics and formulas 3. Copper soldering and brazing 4. Acetylene welding and burning 5. Pipe and equipment rigging 6. Drawing, isometrics, spool sheets and construction drawing interpretation. 7. Steam, hydronics, geo-thermal, and solar systems 8. -
Catalog Download
WELDER / PIPEFITTER TOOLS A. & B. TACK-IT From A-LINE • Step 1: Select pipe size. • Step 2: Insert pins in required pipe size holes & hand tighten. A • Step 3: Position tool against pipe with upward pressure to engage “Hi-Lo” pins. • Step 4: Align fitting on opposite side of tool, shutting it to the spacer and resting it on the “Hi-Lo” pins. • Step 5: Tack It. • Step 6: Slide tool out, opposite to the tack and finish as usual. • View Demo Video Online at www.thegangbox.com Item # Desc. Price 344332 Small 3/32” gap $59.25 34418 Small 1/8” gap $59.25 348332 Large 3/32” gap $60.95 34818 Large 1/8” gap $60.95 B C C. ERGO SMALL BORE SPACE-IT WEDGE #34102 . .$19.95 • 3/4" wide x 8" long , .212" thick • 1 ½" grip & striking surface • Double taper tip • Bright orange & high visibility D D. ERGO BIG BORE SPACE-IT WEDGE #34101 . .$19.95 • 1½" wide x 8" & .212" thick • Double taper tip E • Bright orange & high visibility ON E. SPACE-IT HOLSTER #34103 SALE PRICE SALE! Was $22.00...........................On Sale for $19.95 • Safest way to carry your Space-It wedges • 'No drop' safety flap belt loop fits up to 3" wide belts • Exceptional quality Top grain tanned leather • Holds 2 Space-It wedges (any combination) • Available Colors: Natural, Tan, Walnut 1 Call The Gangbox Toll Free 1-800-849-4821 • Order Online at: www.thegangbox.com JACKETS • SLEEVES • HOODS Prices subject to change without notice A. SATEEN JACKET • Five insulated snaps with spatter guard front closure. -
Pipe Cutting & Beveling Equipment | Pipe Alignment & Reforming Clamps
| Pipe Cutting & Beveling Equipment | Pipe Alignment & Reforming Clamps | Pipefitter’s Tools Call us: 800.725.7311 | 918.447.1288 | mathey.com 1 Where there’s pipe, there’s Mathey. For over seventy years, one company has set the standard for cutting, beveling, clamping and align- ing pipe: Mathey Dearman. Customers worldwide look to Mathey Dearman for innovative solutions, unparalleled technology and real world experience. In the field or in the shop, Mathey Dearman tools can be found working on pipelines, refineries, in shipyards, steel mills, power plants, tank farms, paper mills, food processing plants, and chemical plants, as well as military and utilities installations. When you need to cut, bevel, clamp or align pipe, you need Mathey Dearman. Mathey.com email us: [email protected] 2 email us: [email protected] Call us: 800.725.7311 | 918.447.1288 | mathey.com 3 Table of Contents Mathey Dearman Master Catalog Table of Contents CUTTING AND BEVELING | SADDLE MACHINES .............................5 CUTTING AND BEVELING | CHAIN MACHINES .............................. 17 CUTTING AND BEVELING | BAND CRAWLER ............................... 25 CUTTING & BEVELING | MAGNACUT XM & MINIMAG XM ............ 29 TORCHES AND ACCESSORIES ......................................................37 CGM COLD CUTTING & BEVELING MACHINE ............................... 41 ALIGNING AND REFORMING CLAMPS ......................................... 49 ALIGNING-ONLY CLAMPS ............................................................. 71 PIPEFITTER’S TOOLS .....................................................................79 Notes: Due to our ongoing efforts to offer the finest pipe cutting, beveling, clamping and alignment products available, product improvements may cause changes in specifications without notice. Some photos include optional equipment or accessories. Please read the Parts and Operating Manual thoroughly before attempting to use your Mathey Dearman machine or tool. Pictures are for illustration only. Actual product appearance may differ for some equipment. -
Steamfitter/Pipefitter Program Content
PIP-0100 Tools & Equipment NOA Reference: The material covered satisfies in whole or in part, the requirements for National Occupational Analysis: - Plumber tasks 1, 5 & 6 - Steamfitter-Pipefitter tasks 2 & 3 Description: This course is designed to provide apprentices with the knowledge and skills necessary to use and care for the tools of the trade in a safe, efficient and responsible manner. Course material includes: - hand and power tools, shop and job-site equipment, tools and facilities - safety practices in the use and care of equipment and tools used in the piping industry - operation and maintenance of hand and power tools Prerequisites: None Course Outcomes: Upon completion of this course, the apprentice will be able to: - develop safety practices in the use and care of tools and equipment used in the piping industry - select, operate and maintain hand and power tools, equipment and facilities without damage to equipment, operator or to others - demonstrate understanding of the responsibilities for the care and proper use of tools Required Knowledge and Skills: 1. Describe general safety requirements for using tools. - guarding, shielding when using tools - body positioning - pinch points 4 2. Describe the properties of metals used in hand and power tools. - tool steels for wrenches - tool steels for saws and blades 3. Describe the terminology associated with metals used in hand and power tools. - oxidation - corrosion - tensile strength - shear strength 4. Describe measuring tools, their purpose, applications, safe use and care. - tapes, rules, scale rules, calipers, micrometers, gauges, straight edges, plumb bobs, squares and levels - torque wrench - scribers, markers, dividers and compasses 5. -
Steamfitter/Pipefitter (BTJ) Mechanical Equipment Serviceman (MESS)
What is a Steam Fitter? What is an MESS Serviceman? What is the Term of the Apprenticeship? How long of a commitment? What does earn as you learn Mean? What is our Training Center Mission? Our Vision? What happens after I graduate from the Apprenticeship? How can I get in? What do I have to do? When can I start? Steamfitter/Pipefitter (BTJ) The scope of work of the Steamfitter/Pipefitter encompasses installation and servicing of systems requiring piping. This includes steam and hot water heating systems, air conditioning/refrigeration systems, chemical & petrochemical plants and complete environmental systems in hospitals, schools, churches, high rise office, and apartment buildings. The trade includes joining pipe mechanically and metallurgically by soldering, brazing, or welding. It also includes erecting and working on scaffolding, interpreting blueprints, and writing technical reports. Measuring, cutting, and fabricating piping or tubing using mechanical equipment is also the work of the Steamfitter Mechanical Equipment Serviceman (MESS) - HVAC & R The scope of the MESS encompasses service and maintenance of commercial air conditioning, refrigeration, ventilation and heating equipment and similar systems. Electric, gas & oil fired hydronic and forced air equipment, associated combustion controls, and temperature/humidity controls are included. Building automation equipment service is also included. Terms of Apprenticeship Apprentices serve a five (5) year working apprenticeship with each year divided into two (2) periods (semesters) for a total of ten (10) periods. Apprentices attend a full day of class at least once every two weeks for 11 days per period and must meet the minimum requirements pertaining to grades, attendance, appearance & conduct in the classroom and on the job. -
Pipefitter I & II
APPRENTICESHIP STANDARDS DEVELOPED BY FOR THE OCCUPATIONS OF Pipefitter I SOC: 47-2152.01 RAPIDS CODE: 414 Pipefitter II (PFJ Limited License) SOC: 47-2152.01 RAPIDS CODE: 90087 APPROVED AND CERTIFIED BY THE The Rhode Island Department of Labor & Training APPRENTICESHIP OFFICE Sherri Scalzo, SUPERVISOR OF APPRENTICESHIP REGISTERED AS PART OF THE NATIONAL APPRENTICESHIP PROGRAM IN ACCORDANCE WITH THE BASIC STANDARDS OF APPRENTICESHIP ESTABLISHED BY THE SECRETARY OF LABOR REGISTRATION DATE: DATE OF MOST RECENT UPDATE: RAPIDS REGISTRATION NUMBER: The legal requirements for registered apprenticeship are contained in 29 USC 50 and 29 CFR § 29 and 30 and Rhode Island General Laws Chapter 28 Section 45. RI DLT requires that standards be typed Appendix A TERM OF APPRENTICESHIP, ON THE JOB LEARNING OUTCOMES, & RELATED INSTRUCTION OUTLINE Pipefitter I SOC: 47-2152.01 RAPIDS CODE: 414 This schedule is attached to and a part of these Standards for the above identified occupation. 1. TERM OF APPRENTICESHIP. The term of the occupation is Time Based, 10000 hours of on-the-job learning (OJL), supplemented by 720 hours (5 levels) of related instruction. To become a licensed Pipefitter I, apprentices are required to pass the license exam. Credit for prior learning (work hours or instruction) granted by the sponsor requires the approval of the Mechanical Board to be applicable toward eligibility to test for the license. The probationary period shall be defined as hours on the job. Apprentices become eligible to test for the limited license (Pipefitter II) after 4000 OJL hours, 288 hours (2 levels) of instruction. Apprentices will will not be paid for hours spent attending classes. -
Material Handling Equipment Pipe Jacks and Stands Mega Jacks and Rollers Pipe Flame Cutting and Bevelling Pipe Rigging Equipment
PIPE FLAME CUTTING AND BEVELLING PIPE ALIGNMENT CLAMPS PIPE RIGGING EQUIPMENT PIPE JACKS AND STANDS MEGA JACKS AND ROLLERS MATERIAL HANDLING EQUIPMENT PIPE PURGING SYSTEMS PURGE OXYGEN MONITORS PIPE STOPPERS Introduction to S.F.E. Group Mathey Dearman Inc, B&B Pipe and Industrial Tools LLC and TAG Pipe Equipment Specialist Ltd; are proud to announce their merging and the formation of Specialized Fabrication Equipment Group, or The S.F.E. Group. The synergies of these three global brands enable S.F.E. Group to not only offer a more robust product range to our distribution partners, but also a proactive sales and marketing approach and increased infrastructure and customer support. With the backing of Gladstone Companies, a publicly listed private equity group; The S.F.E. Group will proactively be looking to further invest in the Welding and Industrial Equipment channels through add on acquisitions of other leading Brands, while continuing to grow our existing brands and product portfolio. Mathey Dearman based in Tulsa, Oklahoma is an 80-year-old company with 45 employees. Mathey Dearman is known as the pioneer of Mathey saddle type pipe cutters and bevelers, as well as Dearman type alignment and reforming clamps. PIPE FLAME CUTTING AND BEVELLING Mathey manufactures multiple flame and plasma Pipe Cutters and Bevelers and are recognized as the leader in this product category. These machines are used across multiple fabrication projects, most commonly found in the energy construction markets. PIPE ALIGNMENT CLAMPS With the invention of the Dearman clamp taking lead, additional Pipe Alignment and Reforming Clamps are now offered exhibiting the most complete line in the industry. -
Steamfitter-Pipefitter Level 2
Steamfitter-Pipefitter Level 2 Rev. April, 2019 Steamfitter-Pipefitter UNIT B1 TOOLS AND EQUIPMENT II Unit: B1a Tools and Equipment II Level: Two Duration: 7 hours Theory: 7 hours Practical: 0 hours Overview: This unit introduces Steamfitter-Pipefitter apprentices to additional procedures for selecting, using, and maintaining tools and equipment in a variety of steamfitting-project settings. The principles and practical methods introduced here are pursued in greater depth and complexity throughout technical training. Percent of Objectives and Content: Unit Mark (%) 1. Describe the selection, use, and maintenance of fabrication (power tools) and 25% equipment. 2. Describe intermediate level techniques for selection, use, and maintenance of 25% fabrication (power tools) and equipment. 3. Describe the selection, use, and maintenance of additional steel welding tools 25% and equipment. 4. Describe intermediate level techniques for selection, use, and maintenance of 25% steel welding. *** Rev. April 2019 1 Steamfitter-Pipefitter Unit: B1b Advanced Hoisting, Lifting, and Rigging Level: Two Duration: 7 hours Theory: 7 hours Practical: 0 hours Overview: This unit is designed to provide the Steamfitter-Pipefitter apprentice with the knowledge and understanding of advanced hoisting, lifting, and rigging. Percent of Objectives and Content: Unit Mark (%) 1. Identify hazards and describe safe work practices pertaining to advanced hoisting, 25% lifting and rigging operations. a. Energized power lines b. Critical lifts c. Weather conditions d. Ground conditions e. Multi-tag lines 2. Identify documentation required for engineered lifts. 25% 3. Describe how to do calculations pertaining to hoisting, lifting and rigging. 25% a. Sling angle b. Load/weight c. Centre of gravity d. -
Optional Requirements for Interim Credentials for Pipefitter/Steamfitter
To ensure that all United Association (UA) apprentices and journeyworkers receive the appropriate skills and knowledge from any of the 330 UA authorized training centers (covering 284 registered apprenticeship programs and over 40,000 registered apprentices), the International Pipe Trades Joint Committee Training (IPTJTC) has committed tremendous resources to the development of curriculum, standards and certifications (including 3rd party groups1). The IPTJTC works in partnership with government, education, and industry groups (private and nonprofit) in the development and validation of this material to assist in preparing these individuals for a successful career in the piping industry. Optional Requirements for Interim Credentials for Pipefitter/Steamfitter Level 1 1,700 – 2000 Hours OJL and 1st Year RI Completion of Brazing Certification UA‐51 – The completed braze test assembly shall be visually examined for cleanliness and the presence of brazing filler metal all around the joint at the interface between the socket and the pipe. Outside surfaces shall be free of excessive braze metal and oxidation. Sectioning tests shall be in accordance with ASME Code Section IX. OSHA 10/30‐Hour Course – Smart Mark is an OSHA approved safety and health training program. It is a standardized and intensive program that was developed in 1998 by the Construction Industry Partnership (CIP) that prepares construction industry workers to identify hazards and prevent on‐the‐job accidents. Soldering Certification – The Copper Development Association Inc. (CDA) regularly receives inquiries regarding the methods and procedures required to qualify installers for the installation of soldered‐joint copper piping systems. Currently, there are no known qualifications requirements developed and certified by any consensus code‐writing body.