A Metallic Fuel Performance Benchmark Problem Based on the IFR-1 Experiment
Total Page:16
File Type:pdf, Size:1020Kb
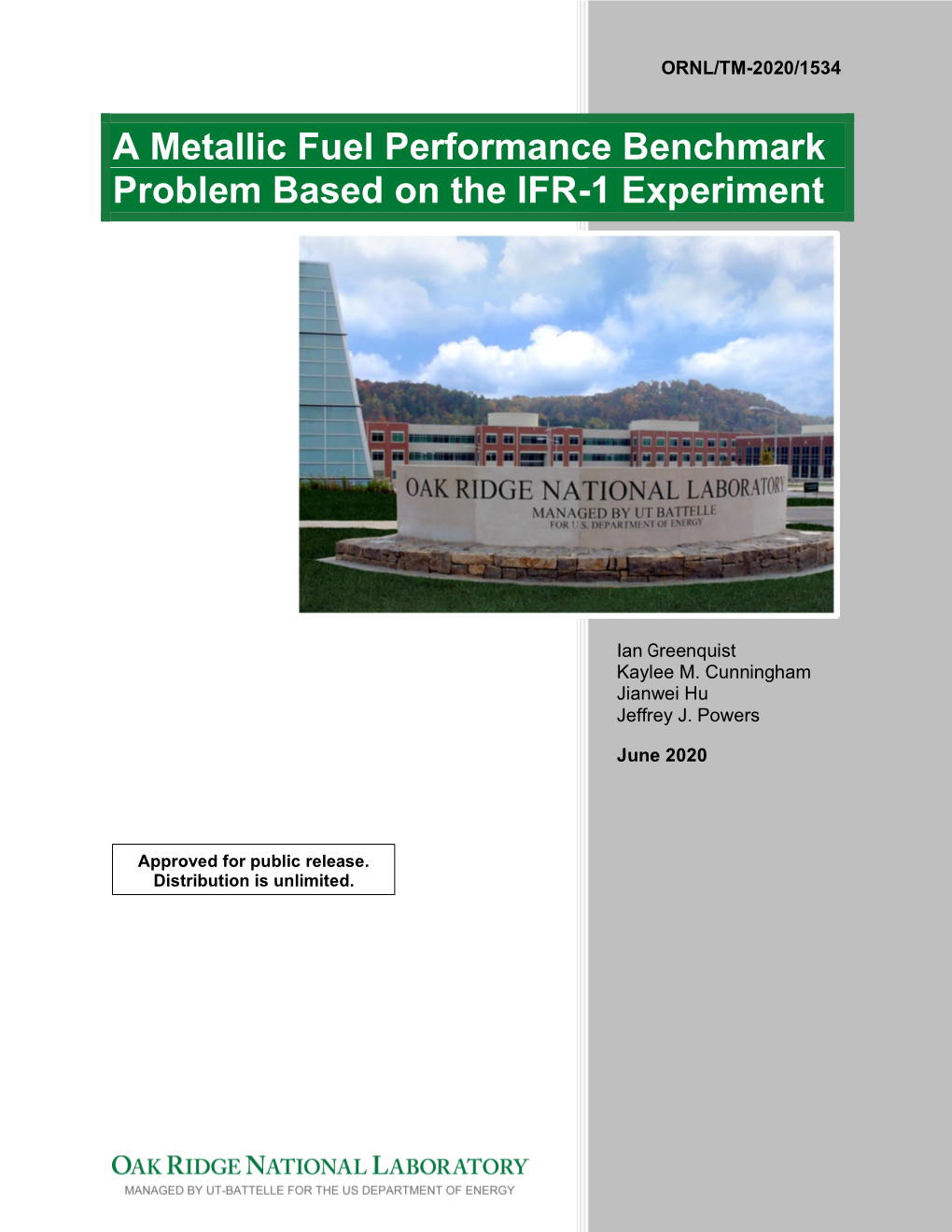
Load more
Recommended publications
-
Mission Need Statement for the VERSATILE TEST REACTOR (VTR) PROJECT
Mission Need Statement for the VERSATILE TEST REACTOR (VTR) PROJECT A Major Acquisition Project Office of Nuclear Technology Research and Development Office of Nuclear Energy U.S. Department of Energy Date Approved: December 2018 1 Table of Contents 1 Statement of Mission Need .................................................................................................. 4 2 Alignment .............................................................................................................................. 4 3 Capabilities Gap ................................................................................................................... 5 3.1 Capability Gap ............................................................................................................. 5 3.2 Strategic Risk ............................................................................................................... 8 3.3 Capability Requirements ............................................................................................ 8 3.4 High-Level Interdependencies .................................................................................... 9 3.5 Status of Existing Capabilities ................................................................................... 10 4 Potential Approach ............................................................................................................. 11 5 Resource and Schedule Forecast ....................................................................................... 12 5.1 Cost Forecast -
“Advanced” Isn't Always Better
SERIES TITLE OPTIONAL “Advanced” Isn’t Always Better Assessing the Safety, Security, and Environmental Impacts of Non-Light-Water Nuclear Reactors “Advanced” Isn’t Always Better Assessing the Safety, Security, and Environmental Impacts of Non-Light-Water Nuclear Reactors Edwin Lyman March 2021 © 2021 Union of Concerned Scientists All Rights Reserved Edwin Lyman is the director of nuclear power safety in the UCS Climate and Energy Program. The Union of Concerned Scientists puts rigorous, independent science to work to solve our planet’s most pressing problems. Joining with people across the country, we combine technical analysis and effective advocacy to create innovative, practical solutions for a healthy, safe, and sustainable future. This report is available online (in PDF format) at www.ucsusa.org/resources/ advanced-isnt-always-better and https:// doi.org/10.47923/2021.14000 Designed by: David Gerratt, Acton, MA www.NonprofitDesign.com Cover photo: Argonne National Laboratory/Creative Commons (Flickr) Printed on recycled paper. ii union of concerned scientists [ contents ] vi Figures, Tables, and Boxes vii Acknowledgments executive summary 2 Key Questions for Assessing NLWR Technologies 2 Non-Light Water Reactor Technologies 4 Evaluation Criteria 5 Assessments of NLWR Types 8 Safely Commercializing NLWRs: Timelines and Costs 9 The Future of the LWR 9 Conclusions of the Assessment 11 Recommendations 12 Endnotes chapter 1 13 Nuclear Power: Present and Future 13 Slower Growth, Cost and Safety Concerns 14 Can Non-Light-Water Reactors -
VTR EIS) (DOE/EIS-0542) Comment Submittal by Tami Thatcher, February 11, 2021
Public Comment Submittal on the U.S. Department of Energy’s Versatile Test Reactor Draft Environmental Impact Statement (VTR EIS) (DOE/EIS-0542) Comment submittal by Tami Thatcher, February 11, 2021. Comments Due: February 16, 2021. Sent by email to [email protected] BACKGROUND The draft Environmental Impact Statement for the Versatile Test Reactor (VTR) considers the potential environmental impacts for the construction and operation a new Department of Energy regulated test reactor, and associated facilities for post-irradiation evaluation of fuels and other materials, VTR driver fuel production (fuel feedstock and fuel fabrication), and the managing of its spent nuclear fuel. The VTR would be a 300 megawatt (thermal) fast neutron reactor that does not generate electricity and is only used for high neutron bombardment of fuels and other materials. The VTR is a pool-type, sodium-cooled reactor with a fast-neutron spectrum and will use a uranium-plutonium-zirconium metal fuel. GE Hitachi Nuclear Energy is working with the Idaho National Laboratory on the VTR conceptual design based on its PRISM reactor, which was based on the Experimental Breeder II reactor. 1 The EBR II which was operated by Argonne National Laboratory – West at the Idaho site which is now the Materials and Fuels Complex (MFC) at the INL, although the EBR II has been dismantled. The 60-year-old pyroprocessing facility at MFC, the Fuel Conditioning Facility (FCF) remains at the former EBR II complex. SUMMARY OF VTR EIS INADEQUACY I disapprove of the DOE’s preferred alternative, to construct the VTR at either proposed location, the Idaho National Laboratory or the Oak Ridge National Laboratory because of cost, accident risk and nuclear weapons proliferation concerns. -
UCS Technical Rebuttal to the Idaho National Laboratory's Opinions on the Versatile (Fast) Test Reactor Edwin Lyman Senior Sc
UCS technical rebuttal to the Idaho National Laboratory’s opinions on the Versatile (Fast) Test Reactor Edwin Lyman Senior Scientist, Global Security Program, Union of Concerned Scientists June 11, 2018 On February 15, I published a blog post entitled “The Versatile Fast Neutron Source: A Misguided Nuclear Reactor Project.” The post was critical of the recent Congressional efforts to compel the Department of Energy (DOE) to build a multibillion-dollar fast-neutron nuclear reactor without thorough evaluation of the need for such a project and its cost and benefits. In response, on March 13, the Idaho National Laboratory (INL) released an unsigned “technical rebuttal” responding to what it characterized as “personal opinions that are inaccurate or misleading.” It starts by arguing that such a reactor is needed, and then comments on seven statements from my blog post. Given that INL would likely be the site for such a reactor and therefore has a vested interest in the project, the lab’s favorable opinions on its merits come as no surprise. However, INL’s response contains numerous inaccurate or misleading statements. Below, I list the seven quotes from my blog post, and respond to INL’s rebuttal. 1. “What may not be clear from the name is that this facility itself would be an experimental fast reactor, likely fueled with weapon-usable plutonium.” a) “Experimental fast reactor” versus “test reactor” INL takes issue with my description of the reactor under question as an “experimental fast reactor” and insists it should be called a “test reactor.” In fact, other than a legal distinction, calling it a “test reactor” would make no meaningful difference. -
How DOE and Industry Collaborations Are Paving the Way for Advanced Nuclear Reactors
As seen in the April 2021 issue of NuclearNews Copyright © 2021 by the American Nuclear Society April 2021 Road to Advanced Nuclear How DOE and industry collaborations are paving the way for advanced nuclear reactors 24 Nuclear News April 2021 By Cory Hatch s electric utilities rush to reduce carbon emissions by investing in intermittent renew- ables such as wind and solar, they often rely heavily on fossil fuels to provide steady A baseload power. More than 60 percent of the nation’s electricity is still generated with fossil fuels, especially coal- fired and gas- fired power plants that have the ability to quickly ramp up or ramp down power to follow loads on the electric grid. Most experts agree that even with a radical advancement in energy storage technology, relying exclusively on wind and solar to replace fossil fuels won’t be enough to maintain a stable electric grid and avoid the major impacts of climate change. To complete the transition to a carbon- free energy future, one key piece of the puzzle remains: nuclear power. Conventional light water reactors already account for roughly 55 percent of all carbon- free electric- ity produced in the United States. A crucial distinction between nuclear and other clean sources like wind and solar is that nuclear remains one of the few ways to generate reliable, carbon- free power 24 hours a day, 365 days a year. But conventional LWRs have three major limitations. First and foremost is cost. U.S. utilities that have attempted new reactor construction in the past decade or so have faced major cost overruns and construction delays. -
VERSATILE TEST REACTOR Experimental Capabilities: Driving Nuclear Innovation
VERSATILE TEST REACTOR Experimental Capabilities: Driving Nuclear Innovation WHAT ARE THE VTR test vehicles will have large VTR TEST VEHICLES? irradiation test volumes—more than VTR SYNERGY 7 liters per vehicle—that will be he United States has long been There will be four test vehicle available to all users. The VTR will categories for inserting a leader in the development be able to accommodate up to five T experiments into the VTR: of nuclear technologies. However, NTA’s, four ELTA’s, and one RTA the U.S. lacks a fast neutron testing • Dismountable Test Assembly described above. Many more test (DTA): A modified driver fuel capability to support advanced positions will be available for DTA’s. assembly that will have an insert nuclear technology, thereby placing that replaces the middle 7-19 HOW DOES THE VTR WORK the U.S. industry in a position to rely on pins of the driver fuel, which can WITH PARTNERS TO ADVANCE foreign services to support advanced contain fuel or material tests. The EXPERIMENT CAPABILITIES? reactor research and development. DTA insert can remain for one The Versatile Test Reactor (VTR) is cycle, or for as many cycles as Eighteen universities, nine private the material limits of the insert entities/industry partners and intended to fill this long-standing gap, allow. The DTA insert will be six national laboratories are leveraging previous and existing U.S. removable and a new insert can collaborating within each of the test government and industry investments be loaded (during any outage). vehicle categories and key areas. in nuclear reactors to accelerate the design and construction process, using • Normal Test Assembly (NTA): The objective is to cover the wide These are the standard range of potential experiment proven nuclear reactor technology to non-instrumented open test designs that meet the needs of create a world-class test facility. -
Us Nuclear Industry Council (Usnic)
U.S. NUCLEAR INDUSTRY COUNCIL (USNIC) Advanced Nuclear Reactor Development Benefits from Versatile Test Reactor U.S. Nuclear Industry Council Policy Brief 24 January 2020 Findings To maintain U.S. global advanced nuclear leadership, it is important to have a versatile, high- energy neutron source. The U.S. Versatile Test Reactor (VTR) can provide that capability to accelerate research and test nuclear materials, fuel, and other components. The VTR can assist in developing innovative nuclear energy technologies that have inherent safety features, lower waste yields, the capability to consume waste materials, the ability to support both electric and non-electric applications, and other improvements over the current generation of reactors. Furthermore, the success of the VTR will advance the U.S. industry by not having domestic nuclear developers relying upon Russian or Chinese test facilities and allowing the U.S. to be a competitive international resource for irradiation and testing services. In addition, constructing the VTR will enable the U.S. government to demonstrate advanced reactor technologies. The U.S. Nuclear Industry Council (USNIC), supports fully funding the U.S. Department of Energy’s (DOE) appropriations requests to ultimately construct and operate the VTR. Inconsistent or inadequate funding will only increase the uncertainty of the schedule, resulting in cost increases and potentially project failure. DOE should continue developing the conceptual design, preparing the Environmental Impact Statement (EIS), establishing processes and procedures to construct the facility on-time and within budget, and pursuing creative domestic and international co-financing opportunities. Background The demand for next-generation nuclear power is expected to grow as the world expands energy production from clean, zero emitting sources. -
VERSATILE TEST REACTOR Experimental Capabilities: Driving Nuclear Innovation
VERSATILE TEST REACTOR Experimental Capabilities: Driving Nuclear Innovation WHAT ARE THE VTR TEST HOW DOES THE VTR WORK VTR SYNERGY VEHICLES? WITH PARTNERS TO ADVANCE There will be four test vehicle EXPERIMENT CAPABILITIES? he VTR is already helping to types, or methods, of inserting Twenty universities, ten private address challenges faced by experiments into the VTR: entities/industry partners and T six national laboratories are reactor innovators today through • Un-instrumented test assemblies: include fuels and/or materials collaborating within the eight development of innovative tests embedded in VTR fuel key areas. Each area is led by a national laboratory technical expert sensors and monitoring systems, assemblies. Also ideal for “drop-in” type tests and can and is supported by other national digital engineering approaches, accommodate materials, fuels, laboratory personnel, university partners and industry partners. enhanced modeling, and new etc. Open to the reactor/primary sodium coolant. measurement techniques. The objective is to cover the wide • Fully instrumented test range of potential experiment assemblies: contain various designs that meet the needs of sensors and instruments and relevant stakeholders and potential capable of manipulating the test users. WHAT EXPERIMENTAL environment (temperature, flow, CAPABILITIES WILL THE VTR etc.) during the test. Open to the PROVIDE? reactor/primary sodium coolant. Thermocouple The VTR provides a platform to • Fully instrumented cartridge accelerate nuclear technology loops: contains a coolant system development for today’s light water segregated from the reactor/ Gas Line reactors and tomorrow’s advanced primary sodium coolant. The reactors by conducting research in loop coolants and/or fuel can eight key areas: be molten salt, gas, lead/lead bismuth, sodium, or others. -
Advanced Nuclear Reactors: Technology Overview and Current Issues
Advanced Nuclear Reactors: Technology Overview and Current Issues April 18, 2019 Congressional Research Service https://crsreports.congress.gov R45706 SUMMARY R45706 Advanced Nuclear Reactors: Technology April 18, 2019 Overview and Current Issues Danielle A. Arostegui All nuclear power in the United States is generated by light water reactors (LWRs), which were Research Assistant commercialized in the 1950s and early 1960s and are now used throughout most of the world. LWRs are cooled by ordinary (“light”) water, which also slows (“moderates”) the neutrons that Mark Holt maintain the nuclear fission chain reaction. High construction costs of large conventional LWRs, Specialist in Energy Policy concerns about safety raised by the 2011 Fukushima nuclear disaster in Japan, and other issues have led to increased interest in unconventional, or “advanced,” nuclear technologies that could be less expensive and safer than existing LWRs. An “advanced nuclear reactor” is defined in legislation enacted in 2018 as “a nuclear fission reactor with significant improvements over the most recent generation of nuclear fission reactors” or a reactor using nuclear fusion (P.L. 115-248). Such reactors include LWR designs that are far smaller than existing reactors, as well as concepts that would use different moderators, coolants, and types of fuel. Many of these advanced designs are considered to be small modular reactors (SMRs), which the Department of Energy (DOE) defines as reactors with electric generating capacity of 300 megawatts and below, in contrast -
Advanced Nuclear Reactor Plant Parameter Envelope and Guidance
Advanced Nuclear Reactor Plant Parameter Envelope and Guidance BK McDowell D Goodman NRIC-21-ENG-0001; PNNL-30992 | 2.18.2021 Advanced Nuclear Reactor Plant Parameter Envelope and Guidance Summary Pacific Northwest National Laboratory (PNNL) is supporting the National Reactor Innovation Center (NRIC) at Idaho National Laboratory (INL) by developing advanced nuclear reactor plant parameter envelopes (PPEs) to facilitate environmental reviews of potential future advanced reactor demonstration projects at INL and elsewhere in the United States. Two PPEs are developed in this report for two size ranges: (1) microreactors, which are defined for this PPE as single units with outputs of 60 MWt or less, and (2) small- to medium-sized advanced reactors with outputs above 60 MWt up to 1,000 MWt. This report describes the methodology for developing the PPEs, including reactor vendor responses to NRIC questionnaires, input from INL staff, independent assessments by subject matter experts, and a review of regulatory requirements a vendor would have to meet during construction and operation. This report presents the compiled PPEs for surrogate plants derived from these inputs, lists documentation supporting the PPE, and provides recommendations for its use when developing an environmental impact assessment. McDowell, Goodman NRIC-21-ENG-0001; PNNL-30992 2/18/2021 iii Advanced Nuclear Reactor Plant Parameter Envelope and Guidance Acronyms and Abbreviations AC alternating current ALARA as low as reasonably achievable ANR advanced nuclear reactor BWR boiling-water reactor BWXT BWX Technologies CFR Code of Federal Regulations CITRC Critical Infrastructure Test Range Complex CT combustion turbine dBA A-weighted decibel DOE U.S. Department of Energy DoD U.S. -
Draft Versatile Test Reactor Environmental Impact Statement
DOE/EIS-0542 December 2020 Draft Versatile Test Reactor Environmental Impact Statement Summary U.S. Department of Energy Office of Nuclear Energy COVER SHEET Lead Agency: U.S. Department of Energy (DOE) Cooperating Agencies: None Title: Draft Versatile Test Reactor Environmental Impact Statement (VTR EIS) (DOE/EIS-0542) Location: Idaho, South Carolina, Tennessee For further information or for copies of this For general information on the DOE National Draft VTR EIS, contact: Environmental Policy Act (NEPA) process, contact: Mr. James Lovejoy Mr. Jason Sturm VTR EIS Document Manager NEPA Compliance Officer U.S. Department of Energy U.S. Department of Energy Idaho Operations Office Idaho Operations Office 1955 Fremont Avenue, MS 1235 1955 Fremont Avenue, MS 1235 Idaho Falls, ID 83415 Idaho Falls, ID 83415 Telephone: 208-526-6805 Telephone: 208-526-6805 Email: [email protected] Email: [email protected] This document is available on the DOE NEPA website (http://energy.gov/nepa/nepa-documents) for viewing and downloading. Abstract: This Versatile Test Reactor Environmental Impact Statement (VTR EIS) evaluates the potential environmental impacts of proposed alternatives for the construction and operation of a new test reactor, as well as associated facilities that are needed for performing post-irradiation evaluation of test articles and managing spent nuclear fuel (SNF). In accordance with the Nuclear Energy Innovation Capabilities Act of 2017 (NEICA) (Pub. L. 115–248), DOE assessed the mission need for a versatile reactor-based fast- neutron source (or Versatile Test Reactor) to serve as a national user facility. DOE determined that there is a need for a fast-neutron spectrum VTR to enable testing and evaluating nuclear fuels, materials, sensors, and instrumentation for use in advanced reactors and other purposes. -
VERSATILE TEST REACTOR Experimental Capabilities: Driving Nuclear Innovation
VERSATILE TEST REACTOR Experimental Capabilities: Driving Nuclear Innovation WHAT ARE THE VTR TEST HOW DOES THE VTR WORK VTR SYNERGY VEHICLES? WITH PARTNERS TO ADVANCE There will be four test vehicle EXPERIMENT CAPABILITIES? he VTR is already helping to types, or methods, of inserting Twenty universities, ten private address challenges faced by experiments into the VTR: entities/industry partners and T six national laboratories are reactor innovators today through • Un-instrumented test assemblies: include fuels and/or materials collaborating within the eight development of innovative tests embedded in VTR fuel key areas. Each area is led by a national laboratory technical expert sensors and monitoring systems, assemblies. Also ideal for “drop-in” type tests and can and is supported by other national digital engineering approaches, accommodate materials, fuels, laboratory personnel, university partners and industry partners. enhanced modeling, and new etc. Open to the reactor/primary sodium coolant. measurement techniques. The objective is to cover the wide • Fully instrumented test range of potential experiment assemblies: contain various designs that meet the needs of sensors and instruments and relevant stakeholders and potential capable of manipulating the test users. WHAT EXPERIMENTAL environment (temperature, flow, CAPABILITIES WILL THE VTR etc.) during the test. Open to the PROVIDE? reactor/primary sodium coolant. Thermocouple The VTR provides a platform to • Fully instrumented cartridge accelerate nuclear technology loops: contains a coolant system development for today’s light water segregated from the reactor/ Gas Line reactors and tomorrow’s advanced primary sodium coolant. The reactors by conducting research in loop coolants and/or fuel can eight key areas: be molten salt, gas, lead/lead bismuth, sodium, or others.