Appendix C Noise and Vibration Technical Report
Total Page:16
File Type:pdf, Size:1020Kb
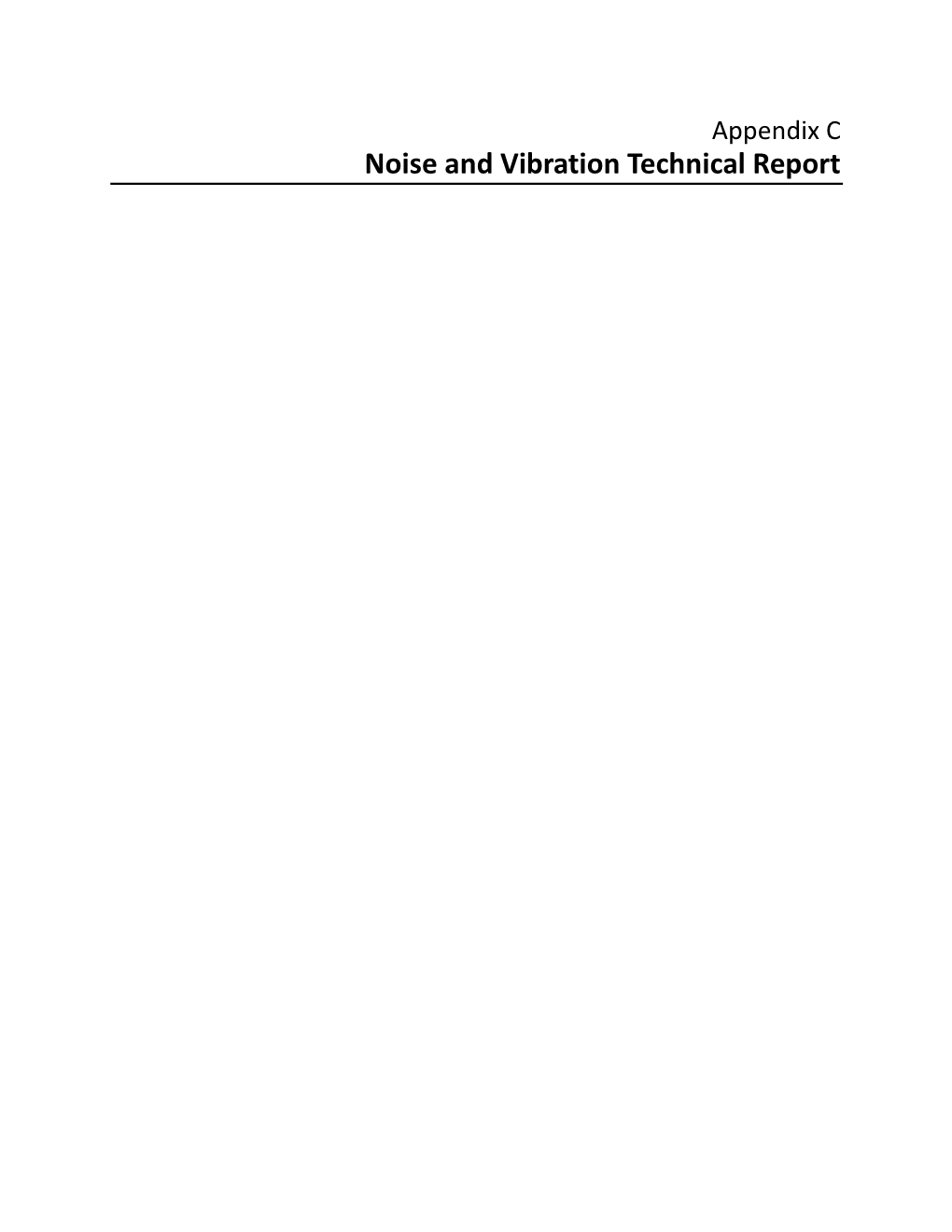
Load more
Recommended publications
-
Wayside Noise of Elevated Rail Transit Structures: Analysis of Published Data and Supplementary Measurements
HE )8# 5 ORT NO. UMTA-MA-06-0099-80-6 . A3 7 no. DOT- TSC- UMTA- 3n-4i WAYSIDE NOISE OF ELEVATED RAIL TRANSIT STRUCTURES: ANALYSIS OF PUBLISHED DATA AND SUPPLEMENTARY MEASUREMENTS Eric E. Unger Larry E. Wittig TRJ < of A , DECEMBER 1980 INTERIM REPORT DOCUMENT IS AVAILABLE TO THE PUBLIC THROUGH THE NATIONAL TECHNICAL INFORMATION SERVICE, SPRINGFIELD, VIRGINIA 22161 Prepared for U,S, DEPARTMENT OF TRANSPORTATION RESFARCH AND SPECIAL PROGRAMS ADMINISTRATION Transportation Systems Center Cambridge MA 02142 x . NOTICE This document is disseminated under the sponsorship of the Department of Transportation in the interest of information exchange. The United States Govern- ment assumes no liability for its contents or use thereof NOTICE The United States Government does not endorse pro- ducts or manufacturers. Trade or manufacturers' names appear herein solely because they are con- sidered essential to the object of this report. i Technical Report Documentation Page 1 . Report No. 2. Government Accession No. 3. Recipient's Catalog No. UMTA-MA- 0 6-0099-80-6 4.^Jitle and Subtitle 5. Report Date WAYSIDE NOISE OF ELEVATED RAIL TRANSIT December 1980 STRUCTURES: ANALYSIS OF PUBLISHED DATA 6. Performing Organization Code AND SUPPLEMENTARY MEASUREMENTS DTS-331 8. Performing Organization Report No. 7. Author's) DOT-TSC-UMTA-80- 41 linger, Eric E.; Wittig, Larry E. 9. Performing Organization Name and Address 10. Work Unit No. (TRAIS) UM049/R0701 Bolt Beranek and Newman Inc.* Moulton Street 11. Contract or Grant No. 50 DOT-TSC Cambridge MA 02238 -1531 13. Type of Report and Period Covered 12 U.S. Department of Transportation Interim Report Urban Mass Transportation Administration July 1978-Oct. -
Interior Noise Reduction Approach for Monorail System
View metadata, citation and similar papers at core.ac.uk brought to you by CORE provided by UTHM Institutional Repository INTERIOR NOISE REDUCTION APPROACH FOR MONORAIL SYSTEM DJAMAL HISSEIN DIDANE A thesis submitted in fulfillment of the requirement for the award of the Degree of Master of Science in Railway Engineering Center For Graduate Studies Universiti Tun Hussein Onn Malaysia JANUARY 2014 v ABSTRACT This study presents an overview on the possibilities of interior noise reduction for monorail system using passive means. Nine samples out of three materials were subjected for noise test and the performance of each sample was observed. It is found that all of these samples have proved to reduce a significant amount noise at low and high frequencies even though the amount reduced differ from one sample to another. It is also been noticed that this reductions were denominated by means of absorption for some samples such as those from rubber material, and it was dominated by means of reflection for some others such as those from aluminum composite and paper composite. Moreover, from these different acoustic properties of each material, the whereabouts to install every material is different as well. It was suggested that, the rubber material should be installed on the upper floor of the monorail while, the paper composite should be installed under floor, and the aluminum composite should be installed at the outer parts from the monorail such as the apron door, ceiling, etc. However, despite their promising potential to reduce noise, there were few uncertainties with some samples at certain frequency, for example samples from aluminum composite could not reduce noise at 1250 Hz which denotes that it is not a good practice to use this material at that frequency. -
Real-Time Train Wheel Condition Monitoring by Fiber Bragg Grating Sensors
Hindawi Publishing Corporation International Journal of Distributed Sensor Networks Volume 2012, Article ID 409048, 7 pages doi:10.1155/2012/409048 Research Article Real-Time Train Wheel Condition Monitoring by Fiber Bragg Grating Sensors Chuliang Wei,1 Qin Xin,2 W. H. Chung, 3 Shun-yee Liu,3 Hwa-yaw Tam,3 andS.L.Ho3 1 Department of Electronic Engineering, Shantou University, Guangdong 515063, China 2 Department of Applied Mathematics, Universit´e catholique de Louvain 1348, Louvain-la-Neuve, Belgium 3 Department of Electrical Engineering, The Hong Kong Polytechnic University, Kowloon, Hong Kong Correspondence should be addressed to Qin Xin, [email protected] Received 25 July 2011; Accepted 8 August 2011 Academic Editor: Tai Hoon Kim Copyright © 2012 Chuliang Wei et al. This is an open access article distributed under the Creative Commons Attribution License, which permits unrestricted use, distribution, and reproduction in any medium, provided the original work is properly cited. Wheel defects on trains, such as flat wheels and out-of-roundness, inevitably jeopardize the safety of railway operations. Regular visual inspection and checking by experienced workers are the commonly adopted practice to identify wheel defects. However, the defects may not be spotted in time. Therefore, an automatic, remote-sensing, reliable, and accurate monitoring system for wheel condition is always desirable. The paper describes a real-time system to monitor wheel defects based on fiber Bragg grating sensors. Track strain response upon wheel-rail interaction is measured and processed to generate a condition index which directly reflects the wheel condition. This approach is verified by extensive field test, and the preliminary results show that this electromagnetic- immune system provides an effective alternative for wheel defects detection. -
Applicable Directivity Description of Railway Noise Sources
THESIS FOR THE DEGREE OF DOCTOR OF PHILOSOPHY Applicable Directivity Description of Railway Noise Sources XUETAO ZHANG Department of Civil and Environmental Engineering Division of Applied Acoustics, Vibroacoustic Group CHALMERS UNIVERSITY OF TECHNOLOGY Göteborg, Sweden 2010 Applicable Directivity Description of Railway Noise Sources XUETAO ZHANG ISBN 978-91-7385-416-0 © Xuetao Zhang, 2010 Doktorsavhandlingar vid Chalmers tekniska högskola Ny serie nr 3097 ISSN 0346-718X Department of Civil and Environmental Engineering Division of Applied Acoustics Chalmers University of Technology SE – 412 96 Göteborg Sweden Tel: +46 (0) 31-772 2200 Fax: +46 (0) 31-772 2212 Cover: 3D directivity pattern of a perpendicular dipole pair, viewed along the axis of the red dipole component which is 4 dB weaker than the blue one. Printed by Chalmers Reproservice Göteborg, Sweden, 2010 ii Applicable Directivity Description of Railway Noise Sources XUETAO ZHANG Department of Civil and Environmental Engineering Division of Applied Acoustics Chalmers University of Technology Abstract For a sound source, directivity is an important parameter to specify. This parameter also reflects the physical feature of the sound generation mechanism. For example, turbulence sound is of quadrupole directivity while fluid-structure interaction often produces a sound of dipole characteristic. Therefore, to reach a proper directivity description is in fact a process of understanding the sound source in a better way. However, in practice, this is often not a simple procedure. As for railway noise engineering, several noise types of different directivity characters are often mixed together, such as wheel and rail radiation, engine and cooling fan noise, scattered fluid sound around bogies and turbulent boundary layer noise along train side surfaces. -
Low Adhesion and Sanders
Low adhesion and sanders AUTHORS INTRODUCTION WHY IS LOW ADHESION IMPORTANT TO THE RAILWAY? Andrew Lightoller is a This paper will introduce the concept of low Chartered Mechanical adhesion between train wheel and rail, including Low adhesion can cause safety incidents (such Engineer, working for why it is so important to the railway, and will as Signals Passed At Danger, or SPADs) and DB ESG, a rolling stock show how sand is used to improve low adhesion significant performance issues (such as station consultancy. Andrew braking performance. Using sand is not a new overruns or delays). In low adhesion, train drivers started his career in concept, indeed steam trains were using sand for will naturally drive more cautiously; perhaps the rail industry as a traction purposes over 100 years ago. However, resulting in a lower maximum speed between graduate engineer at by increasing sand delivery it is possible to deliver stations and braking early and gently. There are Bombardier where consistent train braking performance regardless also issues with traction, particularly affecting he took over as Brakes engineer on the of the underlying adhesion conditions. Solving freight trains with limited motored axles. Classic project. After various experience the braking issue builds driver confidence in poor Each year, approximately 350,000 delay minutes including a six month placement at Chiltern adhesion conditions and opens the door to using are attributed to low adhesion. The direct impact depot commissioning 168s and EU testing sand in traction to achieve higher performance. of low adhesion is estimated to cost the GB of aluminium foam, Andrew moved to Atkins railway industry and wider society £345m per as a Brakes & Pneumatics Engineer in 2001. -
BLUE LINE Light Rail Time Schedule & Line Route
BLUE LINE light rail time schedule & line map Baypointe View In Website Mode The BLUE LINE light rail line (Baypointe) has 2 routes. For regular weekdays, their operation hours are: (1) Baypointe: 12:29 AM - 11:46 PM (2) Virginia: 12:16 AM - 11:33 PM Use the Moovit App to ƒnd the closest BLUE LINE light rail station near you and ƒnd out when is the next BLUE LINE light rail arriving. Direction: Baypointe BLUE LINE light rail Time Schedule 17 stops Baypointe Route Timetable: VIEW LINE SCHEDULE Sunday 12:30 AM - 10:20 PM Monday Not Operational Virginia Station West Virginia Street, San Jose Tuesday Not Operational Children's Discovery Museum Station Wednesday 12:29 AM - 11:46 PM Convention Center Station Thursday 12:29 AM - 11:46 PM 300 Almaden Bl, San Jose Friday 12:29 AM - 11:46 PM San Antonio Station Saturday 12:29 AM - 11:47 PM 200 S 1st St, San Jose Santa Clara Station Fountain Alley, San Jose BLUE LINE light rail Info Saint James Station Direction: Baypointe Stops: 17 Japantown/Ayer Station Trip Duration: 33 min 15 Hawthorne Way, San Jose Line Summary: Virginia Station, Children's Discovery Museum Station, Convention Center Station, San Civic Center Station Antonio Station, Santa Clara Station, Saint James 800 North 1st Street, San Jose Station, Japantown/Ayer Station, Civic Center Station, Gish Station, Metro/Airport Station, Karina Gish Station Court Station, Component Station, Bonaventura North 1st Street, San Jose Station, Orchard Station, River Oaks Station, Tasman Station, Baypointe Station Metro/Airport Station 1740 North First -
Online Condition Monitoring of Railway Wheelsets”
ONLINE CONDITION MONITORING OF RAILWAY WHEELSETS by Arash Amini A thesis submitted to The University of Birmingham For the degree of DOCTOR OF PHILISOPHY School of Electronic, Electrical and Systems Engineering College of Engineering and Physical Sciences University of Birmingham May 2016 University of Birmingham Research Archive e-theses repository This unpublished thesis/dissertation is copyright of the author and/or third parties. The intellectual property rights of the author or third parties in respect of this work are as defined by The Copyright Designs and Patents Act 1988 or as modified by any successor legislation. Any use made of information contained in this thesis/dissertation must be in accordance with that legislation and must be properly acknowledged. Further distribution or reproduction in any format is prohibited without the permission of the copyright holder. Synopsis Wheelset failures can occur unexpectedly resulting in very serious derailments. The rail industry has focused on the improvement of maintenance through the effective use of online condition monitoring of rolling stock and rail infrastructure in order to reduce the occurrence of unexpected catastrophic failures and disruption that arise from them. The basic components comprising a railway wheelset are the wheels, axle and axle bearings. Defective bearings due to their position within the wheelset configuration can be very difficult to detect. Existing wayside technologies based predominantly on Hot Axle Box Detectors (HABDs) are only able to detect a faulty axle bearing only after it has practically failed. Trackside Acoustic Array Detectors (TAADs) on the other hand have not yet proven their effectiveness as an alternative technique for the early detection of faulty axle bearings. -
Increasing the Maintenance Work Rate of Lhb and Icf Wheel Using Cnc Machine
International Research Journal of Engineering and Technology (IRJET) e-ISSN: 2395-0056 Volume: 07 Issue: 03 | Mar 2020 www.irjet.net p-ISSN: 2395-0072 INCREASING THE MAINTENANCE WORK RATE OF LHB AND ICF WHEEL USING CNC MACHINE T.S.RUCKMANI1, T.RAJESH BILLEE 2,S.SARAVANAN3,M.THIRUKUMARAN4 1,2,3Department of Mechanical and Automation Engineering, PSN College of Engineering and Technology, Tirunelveli 4Ass.Professor. Department of Mechanical and Automation Engineering, PSN College of Engineering and Technology, Tirunelveli ---------------------------------------------------------------------***---------------------------------------------------------------------- Abstract :- The aim of this paper is to reduce the manufacturing cost and to reduce the time of remanufacturing work on the rail wheels. There are two types of surface machining or reprofiling a rail wheel. They are lathe machining process and cnc machining process. In this paper, for our research and development of reprofiling a rail wheel, we are using the cnc machining process for the better result and the major need as reducing the time of reprofiling the surface of the wheels. In the paper the defective wheels are taken and are to be reprofiled to extend their service in the railways. The process done on the surface of the wheel is termed as turning operation. The defective wheels are set into the cnc lathe machine for the turning process. The input parameter of the cnc machine is feeded. The parameters are i)depth of cut ii)speed rate iii)feed rate. The time reducing and increasing the remanufacturing work rate of the defective wheels is the major role in this paper. Key Words: Reprofiling, turning operation, remanufacturing work, CNC machining 1. -
Steam Simulator Operating Manual
Highball Sim **** STEAM LOCOMOTIVE SIMULATOR Based on the Santa Fe & Disneyland Railroad 5/8th Narrow Gauge Railroad OPERATING MANUAL **** by Preston Nirattisai Los Angeles, CA based on simulator version 1.0.0.2017-12 **** ckhollidayplans.com Contents Contents iv Foreword vii Acknowledgements xi Introduction xiii 1 Installing, Updates, and Support 1 1.1 Installing and Running . 1 1.2 Updates . 1 1.3 Uninstalling . 2 1.4 Support . 2 1.5 License . 2 2 The Simulator 3 2.1 Quick Start . 4 2.2 Navigating the Simulator . 9 2.3 Controls . 11 2.4 Home Menu . 15 2.5 Main Menu . 17 2.6 Tracks and Scenery Configuration . 35 2.7 Quick Engine Setup . 36 2.8 Pause Menu . 38 2.9 Failure Dialogue . 38 3 The Locomotives 41 3.1 History . 41 3.2 Engine Components . 42 3.3 Cab Controls . 56 4 Firing Up a Cold Engine 63 5 Water Management (Fireman) 69 5.1 Water quantity . 69 5.2 Water Contents . 76 iv 6 Steam and Pressure Management 79 6.1 Steam Loss . 80 6.2 Boiler Pressure Safety . 85 7 Firing and Fire Management 87 7.1 Creating, Building, and Maintaining a Fire . 89 7.2 Fire Indications . 95 7.3 Refilling the Water and Fuel . 96 7.4 Firing on Compressed Air . 97 8 Running a Steam Locomotive (Engineer) 99 8.1 Locomotive Construction . 99 8.2 Physics of a Steam Locomotive . 102 8.3 Stephenson Valve Gear . 104 8.4 Throttle and Johnson Bar . 105 8.5 Engine and Train Lubrication . 112 8.6 Air Compressor . -
Determination of Tramway Wheel and Rail Profiles to Minimise Derailment
Rail Te~h~~l~~~ l~l~~t at Manchester Metropolitan University Determination of Tramway Wheel and Rail Profiles to Minimise Derailment Date: 12th February 2008 RTU Ref: 90/3/A Client: ORR Authors: Dr Paul Allen Dr Adam Bevan Senior Research Engineer Senior Research Engineer Tel: 0161 247 6251 Tel: 0161 247 6514 E-mail: [email protected] E-mail: [email protected] ,; oFFacE o~ aa~~ a~cu~arioN Determination of Tramway Wheel and Rail Profiles to Minimise Derailment Final Report Project Title Determination of Tramway Wheel and Rail Profiles to Minimise Derailment(ORR/CT /338/DTR) Project Manager Dr. Paul Allen Client ORR Date 12/02/2008 Project Duration 6 Months Issue 1 Distribution Dudley Hoddinott (ORR) David Keay (ORR) PDA/AB/SDI/JMS (RTU) Project file Report No. 90/3/A Reviewed bv: Prof. Simon Iwnicki Contact: Dr Paul Allen Senior Research Engineer Tel: 0161 247 6251 E-mail: [email protected] si !Yw. 2n'.-^y..yy.:m'~ ~ 4'~:~~ .!fit'•.. ~' .y,.l.: CONFIDENTIAL Determination of Tramway Wheel and Rail Profiles to Minimise Derailment Final Report Summary As the first phase of a three stage project, the Office of Rail Regulation (ORR) commissioned a wide ranging study to review current tramway systems and their wheel and rail profiles within the UK. Completed by the Health and Safety Executive (HSE) Labs, the work was reported under the Phase 1 ORR study document, entitled `A survey of UK tram and light railway systems relating to the wheel/rail interface' ~'~. Phase 2 of the work, presented within this report, analyses this initial study and extends the work through the application of wheel-rail contact analysis techniques and railway vehicle dynamics modelling to determine optimised wheel and rail profile combinations which minimise derailment risk and wear. -
2017 Triennial On-Site Safety Review of Santa Clara Valley Transportation Authority (Vta)
2017 TRIENNIAL ON-SITE SAFETY REVIEW OF SANTA CLARA VALLEY TRANSPORTATION AUTHORITY (VTA) RAIL TRANSIT SAFETY BRANCH SAFETY AND ENFORCEMENT DIVISION CALIFORNIA PUBLIC UTILITIES COMMISSION 505 VAN NESS AVENUE SAN FRANCISCO, CA 94102 September 19, 2018 Final Report Daren Gilbert, Manager Rail Transit Safety Branch Safety and Enforcement Division 287047411 2017 TRIENNIAL ON-SITE SAFETY REVIEW OF SANTA CLARA VALLEY TRANSPORTATION AUTHORITY ACKNOWLEDGEMENT The California Public Utilities Commission’s Rail Transit Safety Branch (RTSB) conducted this system safety program review. Staff members directly responsible for conducting safety review and inspection activities include: Daren Gilbert, Rail Transit Safety Branch Program Manager Stephen Artus, Program and Project Supervisor Steven Espinal, Senior Utilities Engineer Rupa Shitole, CPUC Representative to VTA, Utilities Engineer Michael Borer, Rail Transit Operations Safety Section Supervisor Debbie Dziadzio, Senior Transportation Operations Supervisor Matthew Ames, Senior Transportation Operations Supervisor John Madriaga, Track Inspector Salvador Herrera, Track Inspector Michael Rose, Operating Practices Inspector Richard Fernandez, Operating Practices Inspector Adam Freeman, Equipment Inspector (Mechanical) James Matus, Equipment Inspector (Mechanical) Shane Roberson, Signal and Train Control Inspector Claudia Lam, Senior Utilities Engineer Specialist – Risk Assessment Jamie Lau, Utilities Engineer Arun Mehta, Utilities Engineer Howard Huie, Utilities Engineer Joey Bigornia, Utilities Engineer -
Grading California's Rail Transit Sta on Areas Appendix LEGEND
! Grading California's Rail Transit Sta3on Areas Appendix LEGEND: CONTENTS: Group 1 - Residen<al • BART Final Scores • LA Metro Final Scores Group 2 - Mixed • Sacramento RT Final Scores • San Diego MTS Final Scores • San Francisco MUNI Final Scores Group 3 - Employment • Santa Clara VTA Final Scores A+ 95% A 80% A- 75% B+ 70% B 55% B- 50% C+ 45% C 30% C- 25% D+ 20% D 5% D- 2% F below 2% Appendix | www.next10.org/transit-scorecard Next 10 ! BART FINAL SCORES AVERAGE: C Final City Line Sta3on Raw Score Grade San SFO-MILLBRAE Civic Center/UN Plaza BART 90.60 A Francisco San SFO-MILLBRAE Montgomery St. BART 88.20 A Francisco San SFO-MILLBRAE 24th St. Mission BART 87.30 A Francisco San SFO-MILLBRAE 16th St. Mission BART 84.30 A Francisco San SFO-MILLBRAE Powell St. BART 84.10 A Francisco San SFO-MILLBRAE Embarcadero BART 83.80 A Francisco Oakland FREMONT Lake Merri] BART 77.60 A DUBLIN/PLEASANTON Berkeley Downtown Berkeley BART 74.50 A TO DALY CITY Berkeley RICHMOND Ashby BART 75.30 A- Berkeley RICHMOND North Berkeley BART 74.30 A- San SFO-MILLBRAE Glen Park BART 74.10 A- Francisco Oakland FREMONT Fruitvale BART 73.50 A- Oakland SFO-MILLBRAE 19th St. Oakland BART 72.90 B+ San SFO-MILLBRAE Balboa Park BART 69.80 B+ Francisco 12th St. Oakland City Center Oakland SFO-MILLBRAE 71.70 B BART Contra Pleasant Hill/Contra Costa Costa SFO-MILLBRAE 66.20 B Centre BART Centre Appendix | www.next10.org/transit-scorecard Next 10 ! Oakland PITTSBURG/BAY POINT MacArthur BART 65.70 B Fremont FREMONT Fremont BART 64.20 B El Cerrito RICHMOND El Cerrito Plaza