Connections for Architectural Precast Concrete
Total Page:16
File Type:pdf, Size:1020Kb
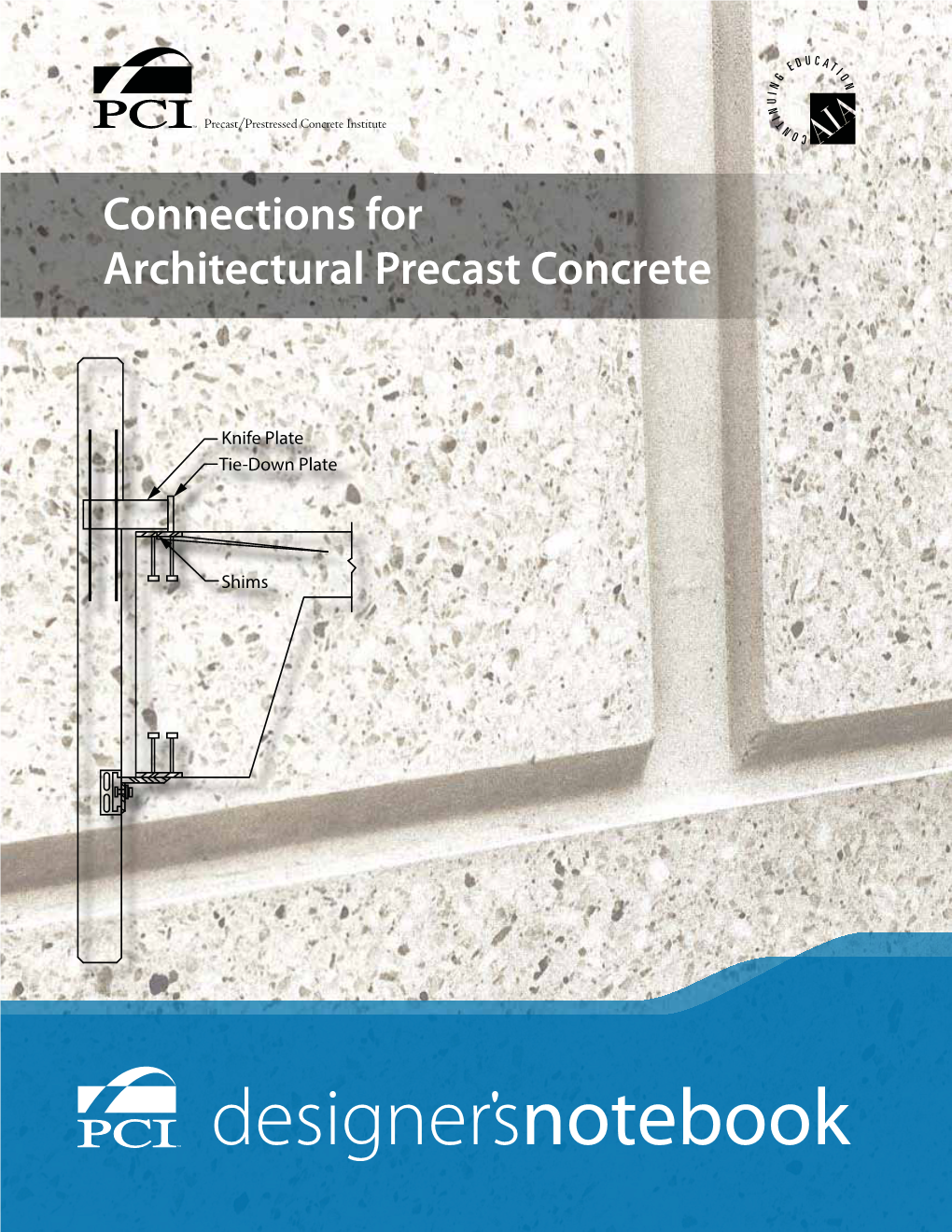
Load more
Recommended publications
-
Anchor Bolts
[ PREVIOUS ] [ NEXT ] ANCHOR BOLTS MASCO.NET POUR IN PLACE Anchor Bolt Holder Fits ½" to ¾" diameter anchor bolts. Anchor bolt locks into e-z bolt sleeve with locking ring and is then placed into the base. Unique design allows for vertical height adjustment of anchor bolts. Assures proper placement of anchor bolts on elevated slabs. Base Plate holder attaches to the decking by nail or staple. No. Qty/Ctn Wt/Ctn (lbs) AZ ABH 100 16.0 Anchor Bolts Anchor bolts are fabricated from low carbon steel for use in the limited load requirements of a foundation bolt. Available in 1/2" Washers ,5/8" and 3/4" diameters with national course thread. All sizes are Washers are used with all sizes of bolts and rod. The furnished with N.C. nut only. washers are fabricated from carbon steel. No. Size Wt (lbs) Qty/Bag No. Size Wt (lbs) CT 126BOLT 1/2"x 6" 0.35 100 pcs CT 12WASH 1/2" 0.04 CT 128BOLT 1/2"x 8" 0.45 100 pcs CT 58WASH 5/8" 0.08 CT 1210BOLT 1/2"x 10" 0.51 100 pcs CT 34WASH 3/4" 0.11 CT 1212BOLT 1/2"x 12" 0.61 100 pcs CT 1WASH 1" 0.17 CT 588BOLT 5/8"x 8" 0.70 50 pcs CT 114WASH 1-1/4" 0.21 CT 5810BOLT 5/8"x 10" 0.82 50 pcs CT 5812BOLT 5/8"x 12" 1.0 50 pcs CT 348BOLT 3/4"x 8" 1.1 50 pcs CT 3410BOLT 3/4"x 10" 1.3 50pcs CT 3412BOLT 3/4"x 12" 1.5 50 pcs Nuts - N/C Hot Dipped Galvanized Nuts are used with all sizes N/C bolts and rod, the nust are fabricated from carbon steel. -
Precast Handbook Concrete Construction Products
BUILDING STRENGTH™ PRECAST HANDBOOK CONCRETE CONSTRUCTION PRODUCTS Safety Information Improper Use of Concrete Accessories Can Cause Severe Injury or Death Read, understand and follow the information and instructions in this publication before using any of the Dayton Superior concrete accessories displayed herein. When in doubt about the proper use or installation of any Dayton Superior concrete accessory, immedi- ately contact the nearest Dayton Superior Service Center or Technical Service Department for clarification. See back cover for your nearest location. Dayton Superior products are intended for use by trained, qualified and experienced workers only. Misuse or lack of supervision and/or inspection can contrib- ute to serious accidents or deaths. Any application other than those shown in this publication should be carefully tested before use. The user of Dayton Superior products must evaluate the product application, determine the safe working load and control all field conditions to prevent applications of loads in excess of a product’s safe working load. Safety factors shown in this publication are approximate minimum values. The data used to develop safe working loads for products displayed in this publication are a combination of actual testing and/or other industry sources. Recommended safe working loads given for the products in this publication must never be exceeded. Worn Working Parts For safety, concrete accessories must be properly used and maintained. Concrete accessories shown in this publication may be subject to wear, overloading, corrosion, deformation, intentional alteration and other factors that may affect the device’s performance. All reusable accessories must be inspected regularly by the user to determine if they may be used at the rated safe working load or should be removed from service. -
A Review of Structural Failures in Ireland
A Review of Structural Failures in Ireland Trinity College Dublin Department of Civil, Structural and Environmental Engineering A Thesis submitted for the degree of Master of Science by Ian James Duckenfield June 2016 Declaration I declare that this thesis has not been submitted as an exercise for a degree at this or any other University and that it is entirely my own work. I agree to deposit this thesis in the University’s open access institutional repository or allow the Library to do so on my behalf, subject to Irish Copyright Legislation and Trinity College Library conditions of use and acknowledgement. Signed i Abstract A Review of Structural Failures in Ireland Ian James Duckenfield Many technical papers have been written and presented to the structural engineering community in Ireland giving details of major projects successfully completed. These projects are on time and under budget. Far more interesting to practising engineers are the cases where things go wrong, and in some cases very badly wrong. Unfortunately the lessons learnt in such cases are hidden from view. No engineer wants to admit that he made an error which now, with the benefit of hindsight, is obvious. The risks of structural failures are extremely low, especially when compared to activities such as car driving and smoking. Nevertheless lives have been lost and life-altering injuries sustained by structural collapses in Ireland. The author has over 40 years of structural design experience and has been collecting examples of failures and near misses. This includes cases where the author acted as an expert witness relating to failures. -
Pull-Out Behavior of Headed Anchors Used in a Totally Prefabricated Counterfort Retaining Wall System
Pull-out behavior of headed anchors used in a totally prefabricated counterfort retaining wall system Maen Farhat, Mohsen Issa, and Bruno F. J. Prado totally prefabricated counterfort retaining wall sys- tem was developed as a method for fast-track con- ■■ This paper studies the pull-out behavior of headed A struction. It is composed of a precast concrete base anchors used in a totally prefabricated counterfort slab and a precast concrete face panel with three counterforts retaining wall system through an experimental test- that are connected on-site with headed anchors. In this study, ing program as well as finite element analysis. an experimental testing program was conducted to examine the pull-out behavior of the headed anchors. The study took ■■ The testing program included various anchor bar into account different bar sizes, ranging from 19M to 29M sizes and embedment lengths and studied the mode (no. 6 to 9), that can be used in the design process, as well as of failure when subjected to tensile loading. two different commercially available grout types and headed anchors. The anchors were studied with different embedded ■■ Results of the test program were compared with lengths to examine the change in the mode of failure asso- results from various design methods, including those ciated with changing the embedment depth of the headed from the American Concrete Institute, the American anchors. In addition, a detailed three-dimensional finite Institute of Steel Construction, and the American element analysis was performed to further investigate the Society of Civil Engineers. damage development in the anchors and shear pocket under axial loading conditions. -
Prediction Models for the Breakout Strength Design Of
Concrete breakout capacity of cast-in-place concrete anchors in early-age concrete James B. Winters and Charles W. Dolan rediction models for the breakout strength design of inserts were developed using mature concrete with a Pminimum concrete compressive strength of 2500 psi (17 MPa). Inserts used in stripping precast and prestressed concrete and tilt-up construction may see loads applied as early as 18 hours after casting, and architectural elements may have stripping and handling loads applied even earlier. There are anecdotal reports of failure of stripping inserts at these early ages. There are multiple potential reasons for these failures. First, the failure can occur due to the intricacies of the individual lifting device. Second, if the tensile capacity of the concrete develops more slowly than the compressive strength and decisions are based on com- ■ Precast concrete elements are often stripped at strengths lower pressive strength, a premature failure may occur. Third, if than the minimum 2500 psi (17 MPa) required by ACI 318-08 the insert is designed for the specified concrete strength appendix D, raising a concern as to whether the ACI equations rather than the stripping strength, there may be insufficient are applicable for early-age concrete. embedment. Fourth, stripping requirements may not have incorporated suction or dynamic loads due to stripping and ■ Seventy-eight pullout tests were conducted on headed stud handling. Increases in loads from stripping and handling assemblies in concrete as young as 12 hours. are not -
Precast Concrete Segments
Precast Forming and Accessories Table of Contents Coil Inserts .................................................................................................................................................... 3 Ferrule Inserts ........................................................................................................................................... 17 Ring-Lift System ........................................................................................................................................ 25 Uni-Lift System .......................................................................................................................................... 61 Easy-Lift System ....................................................................................................................................... 71 Accessories ............................................................................................................................................... 79 Anchor Rail ............................................................................................................................................. 80 C-Connector ........................................................................................................................................... 89 Chord Connector .................................................................................................................................... 82 Column Base Connector ....................................................................................................................... -
Foundation Design and Narrative
79-811B Country Club Drive Indio, CA 92203 (760) 345-1588 (800) 924-7015 FAX (760) 345-7315 ENGINEERING DESIGN AND ANALYSIS OF THE PATRICK AND HENDERSON ROCK ANCHOR FOUNDATION Stetson Mountain Wind Project, Danforth, Maine 38 – GE Wind 1.5sle 1.5MW on 80-m Hub Height Towers 14 – 40 to 50-foot Rock Anchors on 20-foot Ring with 24-foot Diameter Cap using Williams 2-1/2-in diameter Grade 150 ksi Anchors or Equal September 16, 2007 © 2007 Earth Systems Southwest Unauthorized use or copying of this document is strictly prohibited without the express written consent of Earth Systems Southwest. ESSW Job No: 09824-55 P&H Job No. 07-036 September 17, 2007 -ii- Engineering Design and Analysis of the P&H Rock Anchor Foundation TABLE OF CONTENTS Page ENGINEERING DESIGN AND ANALYSIS OF THE .......................................................1 PATRICK AND HENDERSON ROCK ANCHOR FOUNDATION.................................1 Description................................................................................................................................3 Design Criteria and Assumptions...........................................................................................4 Referenced Code, Standards, and Industry Recommended Practices ...........................4 Design Criteria...............................................................................................................5 Geotechnical Parameters ........................................................................................................6 Load Cases................................................................................................................................6 -
Pre-Set Anchors Railings High Mast Overhead Signs
Concrete Forming Systems Bridge Deck Forming and Hanging Systems Reinforcing Bar Supports Precast Concrete Products Rock Anchoring and Bolt Systems CONCRETE PRE-SET ANCHORS RAILINGS ANCHORING HIGH MAST SYSTEMS OVERHEAD SIGNS 1 TABLE OF CONTENTS Table of Contents M V PRE-SET ANCHORS FOR LIGHT & FLAG POLES Foundation Design.................................................32 B.C.D. Pre-Set Anchor System............................................4 Test Results...........................................................34 N.A. FIGURE 2 ANCHOR CONFIGURATION Pre-Set Anchor - Light Poles...................................6 CRANE & ANCHOR BOLTS 5000 mm (16'-4 3/4") Typical Light Poles Installation..................................7 Crane Bolts............................................................37 2 ROUND WASHERS AND 2 HEX NUTS PER STUD HI-TENSILE BOLT OR AND ROUND WASHER FERRULE OR COIL 11000 mm (36'-1") C Light Pole Anchor Ordering Information.....................8 Anchor Bolts..........................................................38 Pre-Set Anchor Design............................................9 Crimped Anchor.....................................................39 4 - A325 BOLTS (MIN.) MOMENT SHEAR 120 (88.8) Anchor Type: DGR-1TM Strut Material: C-1030 C Bored Concrete Pile Diameter: 600 mm (24") 110 Min. Bolt Size: 20 mm (3/4") (81.4) AllowableForces Lateral From Specified Load.....................................10 Hook Anchor Bolt...................................................39 Soil Pressure: 67 kPa (1400 psf) 100 (74.0)