A Study of High-Chroma Inks for Expanding CMYK Color Gamut
Total Page:16
File Type:pdf, Size:1020Kb
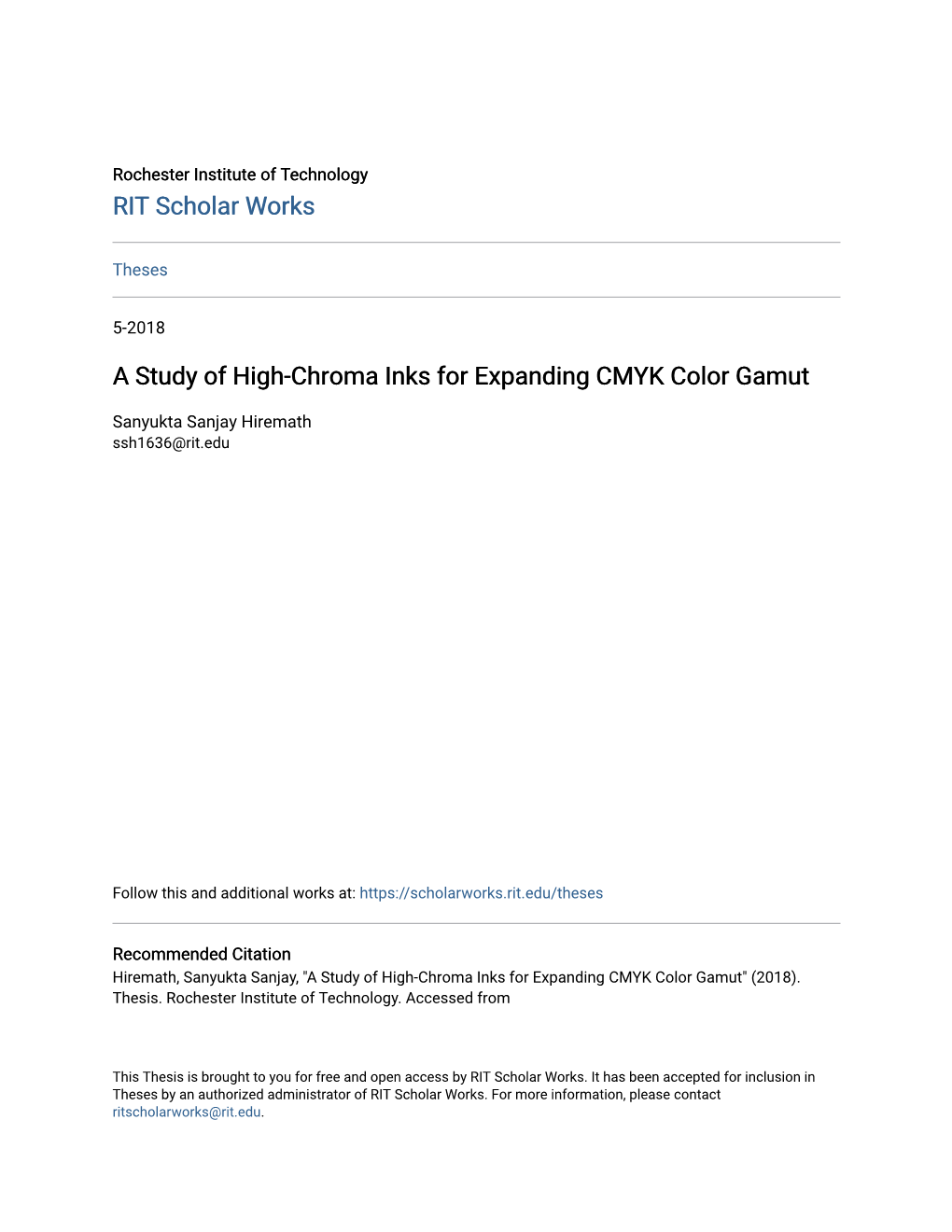
Load more
Recommended publications
-
Color Management
Color Management hotoshop 5.0 was justifiably praised as a ground- breaking upgrade when it was released in the summer of 1998, although the changes made to the color P management setup were less well received in some quarters. This was because the revised system was perceived to be complex and unnecessary. Bruce Fraser once said of the Photoshop 5.0 color management system ‘it’s push-button simple, as long as you know which of the 60 or so buttons to push!’ Attitudes have changed since then (as has the interface) and it is fair to say that most people working today in the pre-press industry are now using ICC color profile managed workflows. The aim of this chapter is to introduce the basic concepts of color management before looking at the color management interface in Photoshop and the various color management settings. 1 Color management Adobe Photoshop CS6 for Photographers: www.photoshopforphotographers.com The need for color management An advertising agency art buyer was once invited to address a meeting of photographers. The chair, Mike Laye, suggested we could ask him anything we wanted, except ‘Would you like to see my book?’ And if he had already seen your book, we couldn’t ask him why he hadn’t called it back in again. And if he had called it in again we were not allowed to ask why we didn’t get the job. And finally, if we did get the job we were absolutely forbidden to ask why the color in the printed ad looked nothing like the original photograph! That in a nutshell is a problem which has bugged many of us throughout our working lives, and it is one which will be familiar to anyone who has ever experienced the difficulty of matching colors on a computer display with the original or a printed output. -
Expanded Gamut Shoot-Out: Real Systems, Real Results
Expanded Gamut Shoot-Out: Real Systems, Real Results Abhay Sharma Click toRyerson edit Master University, subtitle Toronto style Advisors Roger Breton, Marc Levine, John Seymour, Bill Pope Comprehensive Report – 450+ downloads tinyurl.com/ExpandedGamut Agenda – Expanded Gamut § Why do we need Expanded Gamut? § What is Expanded Gamut? (CMYK-OGV) § Use cases – Spot Colors vs Images PANTONE 109 C § Printing Spot Colors with Kodak Spotless (KSS) § Increased Accuracy § Using only 3 inks § Print all spot colors, without spot color inks § How do I implement EG? § Issues with Adobe and Pantone § Flexo testing in 2020 Vendors and Participants Software Solutions 1. Alwan – Toolbox, ColorHub 2. CGS ORIS – X GAMUT 3. ColorLogic – ColorAnt, CoPrA, ZePrA 4. GMG Color – OpenColor, ColorServer 5. Heidelberg – Prinect ColorToolbox 6. Kodak – Kodak Spotless Software, Prinergy PDF Editor § Hybrid Software - PACKZ (pronounced “packs”) RIP/DFE § efi Fiery XF (Command WorkStation) – Epson P9000 § SmartStream Production Pro – HP Indigo 7900 Color Management Solutions § X-Rite i1Profiler Expanded Gamut Tools § PANTONE Color Manager, Adobe Acrobat Pro, Adobe Photoshop Why do we need Expanded Gamut? - because imaging systems are imperfect Printing inks and dyes CMYK color gamut is small Color negative film What are the Use Cases for Expanded Gamut? ✓ 1. Spot Colors 2. Images PANTONE 301 C PANTONE 109 C Expanded gamut is most urgently needed in spot color reproduction for labels and package printing. Orange, Green, Violet - expands the colorspace Y G O C+Y M+Y -
Harlequin RIP OEM Manual
0RIPMate for Windows operating systems Harlequin PLUS Server RIP v9.0 June 2011 AG12325 Rev. 13 Copyright and Trademarks Harlequin PLUS Server RIP June 2011 Part number: HK‚9.0‚ÄìOEM‚ÄìWIN Document issue: 106 Copyright ¬© 2011 Global Graphics Software Ltd. All rights reserved. Certificate of Computer Registration of Computer Software. Registration No. 2006SR05517 No part of this publication may be reproduced, stored in a retrieval system, or transmitted, in any form or by any means, elec- tronic, mechanical, photocopying, recording, or otherwise, without the prior written permission of Global Graphics Software Ltd. The information in this publication is provided for information only and is subject to change without notice. Global Graphics Software Ltd and its affiliates assume no responsibility or liability for any loss or damage that may arise from the use of any information in this publication. The software described in this book is furnished under license and may only be used or cop- ied in accordance with the terms of that license. Harlequin is a registered trademark of Global Graphics Software Ltd. The Global Graphics Software logo, the Harlequin at Heart Logo, Cortex, Harlequin RIP, Harlequin ColorPro, EasyTrap, FireWorks, FlatOut, Harlequin Color Management System (HCMS), Harlequin Color Production Solutions (HCPS), Harlequin Color Proofing (HCP), Harlequin Error Diffusion Screening Plugin 1-bit (HEDS1), Harlequin Error Diffusion Screening Plugin 2-bit (HEDS2), Harlequin Full Color System (HFCS), Harlequin ICC Profile Processor (HIPP), Harlequin Standard Color System (HSCS), Harlequin Chain Screening (HCS), Harlequin Display List Technology (HDLT), Harlequin Dispersed Screening (HDS), Harlequin Micro Screening (HMS), Harlequin Precision Screening (HPS), HQcrypt, Harlequin Screening Library (HSL), ProofReady, Scalable Open Architecture (SOAR), SetGold, SetGoldPro, TrapMaster, TrapWorks, TrapPro, TrapProLite, Harlequin RIP Eclipse Release and Harlequin RIP Genesis Release are all trademarks of Global Graphics Software Ltd. -
Organic Pigments for Digital Color Printing
Organic Pigments For Digital Color Printing Ruediger Baur and Hans-Tobias Macholdt R&D Pigments, Hoechst AG, Frankfurt/Main, Germany Abstract ency (decreasing transparency automatically means in- creasing hiding power). Also, aspects like lightfastness, Digital color printing (DCP) is becoming more important thermostability and eco/toxicology have to be covered by a versus traditional printing technologies. For electro-graphic- suitable organic pigment for toner use. These aspects are based printers, colored tribo (friction) toner creates the full influenced by both chemical constitution and solid state color image. Typically organic color pigments provide the parameters7 (particle size distribution, particle shape, crys- required color. They have to fulfil both coloristic and tallinity etc.) . electrostatic properties. These properties are the result of To attain the needed coloristic properties the dispersion the chemical constitution and solid-state characteristics of behaviour is of special relevance. In general, solid pigment the pigment. Low electrostatic influence together with high particles are classified in three groups7: tinctorial strength and appropriate transparency is useful. A new yellow pigment type of the benzimidazolone class 1. pigment agglomerates (particle size approx. 0.2-10µm) combines these aspects. The final electrostatic charge of the 2. pigment aggregates (particle size approx. < 1µm) toner is achieved by adding suitable charge control agents 3. primary pigment particles (particle size approx.<<1µm) (CCAs) to control toner charge both in magnitude and sign. Organic color pigments are typically provided in pow- Introduction der form. The single powder particles usually consist of agglomerates. Agglomerates are groups of small crystals In general terms, digital printing means a direct connection and/or smaller aggregates, joined at their corner and edges. -
Predictability of Spot Color Overprints
Predictability of Spot Color Overprints Robert Chung, Michael Riordan, and Sri Prakhya Rochester Institute of Technology School of Print Media 69 Lomb Memorial Drive, Rochester, NY 14623, USA emails: [email protected], [email protected], [email protected] Keywords spot color, overprint, color management, portability, predictability Abstract Pre-media software packages, e.g., Adobe Illustrator, do amazing things. They give designers endless choices of how line, area, color, and transparency can interact with one another while providing the display that simulates printed results. Most prepress practitioners are thrilled with pre-media software when working with process colors. This research encountered a color management gap in pre-media software’s ability to predict spot color overprint accurately between display and print. In order to understand the problem, this paper (1) describes the concepts of color portability and color predictability in the context of color management, (2) describes an experimental set-up whereby display and print are viewed under bright viewing surround, (3) conducts display-to-print comparison of process color patches, (4) conducts display-to-print comparison of spot color solids, and, finally, (5) conducts display-to-print comparison of spot color overprints. In doing so, this research points out why the display-to-print match works for process colors, and fails for spot color overprints. Like Genie out of the bottle, there is no turning back nor quick fix to reconcile the problem with predictability of spot color overprints in pre-media software for some time to come. 1. Introduction Color portability is a key concept in ICC color management. -
The Printer's Guide to Expanded Gamut
DISTRIBUTED BY TECHKON USA February 2017 THE PRINTER’S GUIDE TO EXPANDED GAMUT Understanding the technology landscape and implementation approach By Ron Ellis Printer’s Guide to Expanded Gamut Page | 1 Printer’s Guide to Expanded Gamut Whitepaper By Ron Ellis Table of Contents What is Expanded Gamut ............................................................................................................... 4 ......................................................................................................................................................... 5 Why Expanded Gamut .................................................................................................................... 6 The Current Expanded Gamut Landscape ...................................................................................... 9 Standardization and Expanded Gamut ......................................................................................... 10 Methods of Producing Expanded Gamut...................................................................................... 11 Techkon and Expanded Gamut ..................................................................................................... 11 CMYK expanded gamut ................................................................................................................. 12 The CMYK Expanded Gamut Workflow ........................................................................................ 16 Conversion from source to CMYK Expanded gamut .................................................................... -
Color Printing Techniques
4-H Photography Skill Guide Color Printing Techniques Enlarging Color Negatives Making your own color prints from Color Relations color negatives provides a whole new area of Before going ahead into this fascinating photography for you to enjoy. You can make subject of color printing, let’s make sure we prints nearly any size you want, from small ones understand some basic photographic color and to big enlargements. You can crop pictures for the visual relationships. composition that’s most pleasing to you. You can 1. White light (sunlight or the light from an control the lightness or darkness of the print, as enlarger lamp) is made up of three primary well as the color balance, and you can experiment colors: red, green, and blue. These colors are with control techniques to achieve just the effect known as additive primary colors. When you’re looking for. The possibilities for creating added together in approximately equal beautiful color prints are as great as your own amounts, they produce white light. imagination. You can print color negatives on conventional 2. Color‑negative film has a separate light‑ color printing paper. It’s the kind of paper your sensitive layer to correspond with each photofinisher uses. It requires precise processing of these three additive primary colors. in two or three chemical solutions and several Images recorded on these layers appear as washes in water. It can be processed in trays or a complementary (opposite) colors. drum processor. • A red subject records on the red‑sensitive layer as cyan (blue‑green). • A green subject records on the green‑ sensitive layer as magenta (blue‑red). -
Designing Your Best Ad For
WOW File Requirements and Design Services WOW has an entirely electronic workflow. See below for specific print design requirements. All WOW products are perfect bound and printed in CMYK process color. Please remove all spot colors from ads. All ad materials are due by the 5th of each month. On larger ads, relevant information must be positioned inside of the safe zone (page 3). REQUIRED FILE FORMATS PREFERRED: Adobe® Acrobat PDF files set for press quality, CMYK output (300 DPI) and embedded fonts. PC-based, EPS or TIF, CMYK Adobe® InDesign, Photoshop or Illustrator for layout with fonts outlined. Files should not exceed 10 MB. WOW is not responsible for unconverted file problems. Unsupported program files include PageMaker, Corel Draw, QuarkXPress, and Freehand. Files must be converted to press quality, CMYK PDFs before submission. WOW is not responsible for final quality when faxes, scans and materials from Publisher, PowerPoint and Microsoft Word are provided; nor when RGB files are converted to CMYK. Type should not be smaller than 6 pt. to ensure readability. AD MATERIALS As a courtesy to advertisers, WOW provides professional design services. All materials for WOW design must be received by the 5th of each month. All ad graphics and photos must be set at a resolution of 300 DPI and CMYK. Files submitted as RGB may incur an additional fee. Logos should be submitted as CMYK, vector EPS files. Simple set-up or reconstruction of ads is free of charge up to 10 minutes of design time. After 10 minutes, advertisers will be billed $57 per hour. -
Print Options
Fiery® EXP8000 Color Server SERVER & CONTROLLER SOLUTIONS Print Options © 2005 Electronics for Imaging, Inc. The information in this publication is covered under Legal Notices for this product. 45049630 13 July 2005 CONTENTS 3 CONTENTS INTRODUCTION 5 Terminology and conventions 5 About this document 5 PRINT OPTIONS OVERVIEW 6 About printer drivers and printer description files 6 Setting print options 7 Print option override hierarchy 8 PRINT OPTIONS 9 Print options and settings 9 Additional information 20 Booklet Maker 20 Centering Adjustment 22 Collation 22 Creep Adjustment 22 Duplex 23 Image Shift 24 Paper Source 24 Scale 24 INDEX 25 INTRODUCTION 5 INTRODUCTION This document provides a description of the Fiery EXP8000 print options. This document also explains each print option and provides information on any constraints or requirements. Terminology and conventions This document uses the following terminology and conventions. Term or convention Refers to Aero Fiery EXP8000 (in illustrations and examples) Digital press DocuColor 8000/7000 digital press Fiery EXP8000 Fiery EXP8000 Color Server Windows Microsoft Windows 2000, Windows XP, Windows Server 2003 Mac OS Apple Mac OS 9, Mac OS X Titles in italics Other documents in this set Topics for which additional information is available by starting Help in the software Tips and information Important information Important information about issues that can result in physical harm to you or others About this document This document covers the following topics: •Information about printer drivers, PPD (PostScript Printer Description) files, and setting Fiery EXP8000 print options. •Descriptions of each print option including default settings and any constraints or requirements. PRINT OPTIONS OVERVIEW 6 PRINT OPTIONS OVERVIEW This chapter describes printer drivers and PPD files, Fiery EXP8000 print options, and where to set print options. -
Restricting Color Printing Using Department Codes
Restricting Color Printing Using Department Codes This document applies to the following OKI models that utilize TopAccess MB7x0 Series MPS 5502 MC7x0 Series MPS 3537 MPS 4242 CX3535 / CX4545 ES94x5 Series Go to the TopAccess interface of the printer and select Login. Enter the user name and password. Default user name: admin Default password: 1,2,3,4,5,6. Enter user name and password Select the [User Management] tab. 1. Select [Department Management] tab. 2. Select [New]. 1 2 For this example the following Department Codes have been used. No Color Printing = 1111 Restricted Color Printing = 2222 Open Color Printing = 3333 For “No Color Printing” 1. Create a Department Name. 2. Enter a Department Code. 3. Select [Color Quota Setting] ON. 4. Ensure [color quota setting] is 0. 5. Select [Save]. 5 1 1111 2 3 4 For “Restricted Color Printing” 1. Create a Department name. 2. Enter a Department Code. 3. Select [Color Quota Setting] ON. 4. Set [color quota setting] to desired number of color prints allowed. 5. Select [Save]. 5 1 2222 2 3 4 For “Open Color Printing” 1. Create a Department name. 2. Enter a Department Code. 3. Select [Color Quota Setting] OFF. 4. Select [Save]. 4 1 3333 2 3 The new departments and department codes will appear in the Department Management tab. No Color Printing = 1111 Restricted Color = 2222 Open Color Printing = 3333 1. Select the [Administration] tab. 2. Select [Security] tab. 3. Under [Department Setting] “Enable” (Department Code) and (Require Department Code in User Registration [See NOTE]) 1 2 3 NOTE: The highlighted option may or may not appear depending on the OKI model. -
HIFI Color Printing Within a Color Management System
HIFI Color Printing within a Color Management System Marc Mahy and Dirk De Baer Agfa-Gevaert N.V., Mortsel, Belgium Introduction This transformation to device color values should be colo- rimetrically correct e.g. neutrals should remain neutral, pre- About five years ago the concept of high fidelity color1-4 serve detail both in the low lights as in the high lights, was introduced in the graphic arts community as a reaction reproduce powerful images, and no artifacts or banding to digital color reproduction systems such as video and the should be present. internet. Graphic arts manufacturers, suppliers and provid- In general the best image quality is obtained with de- ers unified their forces to develop new technologies for vices with a high resolution and a large dynamic range, making print more vivid, more convenient and economi- both in gray values as in color saturation. This range, also cal. However, each provider has its own interpretation to referred to as the gamut of the device, should be large reach this goal and as a result there is no clear difference enough so that images from any source can be reproduced between conventional offset and Hifi color printing. Be- exactly. In general however, the gamut of color reproduc- cause also with conventional offset techniques very pleas- tion devices is too small to reproduce all the colors of the ing images can be obtained, the main criterion for Hifi color most common input devices. One of the tasks of a CMS is printing is related to the quality of the printing process and to map the out of gamut colors onto printable colors in such hence we assume that Hifi color printing corresponds to a way that the visual difference between the out of gamut high quality printing. -
Tips for Better Dual Color Printing
TIPS FOR BETTER DUAL COLOR PRINTING 047-36019 CHAPTER1 Dual-Color Printing from Computer …… 2 Contents Printer driver setting …………………………… 3 Important points for preparing originals (Dual-Color printing) …………………………… 4 CHAPTER2 Using "Manual" Effectively / Color Separation …… 6 Setting of color separation conditions …… 6 Important points for selecting parameters … 8 What is the Preview and Edit application? (Preview and Edit) ……………………………… 9 CHAPTER3 Dual-Color printing from paper original About Easy 2Color …………………………… 10 What is "Easy 2Color ?" ……………………… 10 Easy 2color Types …………………………… 12 Red color …………………………………………… 12 Hand Writing1/Hand Writing2 ……………… 13 Color editor ………………………………………… 14 Specified Area …………………………………… 15 Separation Sheet ……………………………… 15 Tips for Making Originals ………………… 16 CHAPTER4 Easy 2Color Operation Flow ……………… 18 When using "Color editor" ……………………… 19 Combine "Easy 2color" and "Combination Print" …………………………… 20 CHAPTER5 General Information of MZ Series ……… 22 Printing Area and Paper ……………………… 22 Parameter list for "Manual" …………………… 24 Caution Please be sure to read "Safety Guide" sections of the RISO Printer's User's Guide before operating the machine. About the contents of this manual Notice (1) This manual may not be reproduced, wholly or in part, in any manner without express authorization. (2) As we are constantly improving our products, this product may vary in some respects from the illustrations used in this manual without notice. (3) Riso shall not be liable for any damage or expenses resulting from the use of this product or included manual. This document is described in American English and, therefore, some words and expressions are different from British English. Ex.) colour: color cylinder: drum is a registered trademark of RISO KAGAKU CORPORATION in Japan and other countries.