Electropolishing of Surfaces in Metallic Parts Obtained by Additive Manufacturing
Total Page:16
File Type:pdf, Size:1020Kb
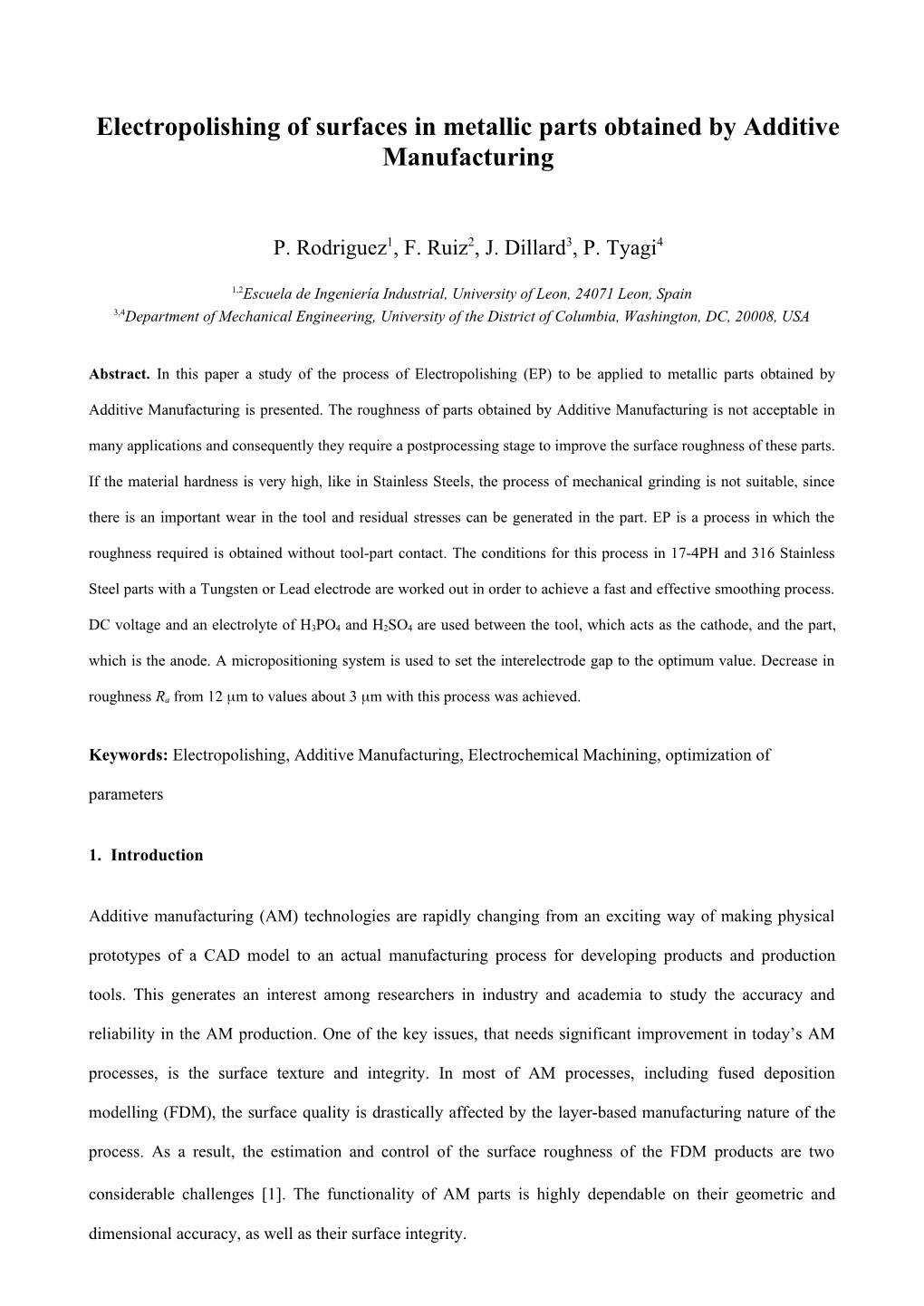
Load more
Recommended publications
-
Electrochemical Surface Finishing Is a Highly Scalable
Electrochemical Surface Finishing by E. J. Taylor and M. Inman lectrochemical surface finishing is a highly scalable to enable uniform polishing. For example, hydrofluoric acid and/ manufacturing process that traditionally uses viscous, or fluoride salts are added to traditional electrolytes to depassivate non-aqueous and/or highly acidic electrolytes to achieve the surface for strongly passive metals such as niobium and Nitinol E 5 the desired surface profiles on metallic parts, with the addition of alloys. In addition to the electrolyte handling and safety issues aggressive, hazardous chemical species to remove the oxide film on associated with concentrated hydrofluoric acid, conventional DC strongly passive materials. An emerging approach applies pulse and electropolishing of these materials presents process control issues, pulse reverse electric fields to control current distribution, mitigate and reject rates can be as high as 40 to 50%.6 oxide film formation and achieve the desired surface finish, in the This reliance on chemical mediation can be traced back 150 presence of environmentally benign and simple chemistries. This years when the understanding of electrochemical principles was approach lowers the cost of the manufacturing process, and improves nascent. The history of electrochemical processing is full of stories process robustness. After a brief discussion of electrochemical regarding the serendipitous “discovery” of chemical components of surface finishing processes, case studies that describe deburring of electrolytes leading to the desired surface properties and profiles. automotive gears and electropolishing of semiconductor valves and These discoveries ultimately became the paradigm for development superconducting radio frequency cavities are presented in this article. of new electrolyte chemistries, which led to the proprietary chemical additives of today’s chemical suppliers. -
Electropolishing Electrolytic Brightening, Smoothing and Deburring of Stainless Steel, Steel, Brass, Copper, Aluminium, Titanium and Magnesium
Electropolishing Electrolytic brightening, smoothing and deburring of stainless steel, steel, brass, copper, aluminium, titanium and magnesium Dr.-Ing. Dr. rer. nat. Magnus Buhlert 1st edition with 111 pictures and 3 tables Specialist publishing house for • Surface Technology - Plating • Printed Circuit Boards and Electronic Assembly Industries Said in one sentence, the chemical equilibrium seams to be an expression for the end of any chemical reaction. after van’t Hoff Foreword After dealing with many questions on electropolishing I was ask to write a book on this subject by Eugen G. Leuze Verlag KG. In 2009 the German version of this book was published [BUHL, 2009a]. It found its readers in the electrochemical community. Since I wrote my theses and many articles on electropolishing and the dynamics of the electro- chemical metal removal there was the wish to publish a book on the subject to give a wide overview on this manufacturing technique. This book was only possible, because I had the chance to work in the group of Prof. Dr. Andreas Visser at the University of Bremen. Subject of my research in his lab was the electrochemical removal of metals by etching and electropolishing. The same impor- tance for this work had my stay in the group of Prof. Dr. Peter Jörg Plath at the chemical department of the university. There I dealt with questions of the non-linear dynamics of the electrochemical removal of metals. The one and the other were necessary to get the know- ledge which is the basis for this book. I deeply thank both for their teaching and inspiration. -
Characterisation, Quantification and Modelling the EDC/NHS Activation
IMPEDANCE-BASED ANALYSIS AND MATHEMATICAL MODELLING OF IMMUNOSENSOR BIOLAYERS ANDREW PETER HENDERSON Doctor of Philosophy (PhD) Teesside University October 2010 This research project was carried out as part of an Engineering and Physical Sciences Research Council (EPSRC) CASE studentship and was done in collaboration with Immunodiagnostic Systems (IDS) Ltd. This copy of the thesis has been supplied on condition that anyone who consults it is understood to recognise that its copyright rests with its author and that no quotation from the thesis and no information derived from it may be published without proper acknowledgement. 1 Teesside University in Middlesbrough Impedance-based Analysis and Mathematical Modelling of Immunosensor Biolayers ANDREW PETER HENDERSON Doctor of Philosophy October 2010 Abstract A study to optimise an IgG based immunosensor is presented, that has been carried out by absorbing monolayers to a gold transducer surface at varying immersion times and temperatures. The theory and kinetics of monolayer adsorption are analysed and discussed. Existing mathematical models are reviewed and experimentally researched, to highlight gaps in knowledge that would facilitate high quality, cost effective immunosensor production. The creation of two mathematical models to predict monolayer adsorption kinetics and optimal immersion times are discussed. Details are provided of how the new mathematical models may be advanced, and how the production of immunosensors may be further improved. The first novel mathematical model (PTCS) has been created to model the presence of two sequentially forming structures on the surface of a substrate. It gives an insight into the percentages of each structure on the surface, along with the actual adsorption process. -
Electron Metallography of Alloy 718
Electron Metallography of Alloy 718 John F. Radavich Emeritus Professor Purdue University West Lafayette, IN 47907 Abstract Alloy 718 is unique in that it forms the greatest number of phases due to its composition and the large variety of imposed heat treatments. The microstructures produced can vary in size, distribution, and location. Some of the large structures can be resolved optically but for resolution of y”/y’ phases, the SEM and/or TEM is required. The normal metallographic preparation for Alloy 718 is a mechanical polish plus an immersion etch in a suitable acid solution. However, it has been found that the use of an electrolytic polish plus electrolytic etch yields more consistent results. In addition, the use of the electrolytic preparation reveals more consistently the phases and helps define the thermal behavior of the alloy. The electrolytic preparation will be described and examples of microstructures representing various thermal conditions will be presented. Introduction The prime objective of metallography is to understand the relationship of composition, processing, and mechanical behavior to the microstructure. Much of superalloy metallography can be considered as an “art,” but with the current analytical tools and our understanding of phase behavior, metallography of alloy 7 18 has become closer to being a “science.” While alloy 718 is the most widely used super alloy in cast, wrought, and powder applications, it is also one of the most segregation prone alloys. Depending on ingot size, Nb segregation, and thermal treatments, a whole range of phases can form during extended times in service at elevated temperatures. The most important of these phases are the y’ precipitates which are the order of 100-200 A in size. -
Comparison of Electropolishing of Aluminum in a Deep Eutectic Medium and Acidic Electrolyte
molecules Article Comparison of Electropolishing of Aluminum in a Deep Eutectic Medium and Acidic Electrolyte Tarek M. Abdel-Fattah 1,* and J. Derek Loftis 1,2 1 Applied Research Center at Thomas Jefferson National Accelerator Facility and Department of Molecular Biology and Chemistry at Christopher Newport University, Newport News, VA 23606, USA; [email protected] 2 Department of Physical Sciences, Virginia Institute of Marine Science, College of William & Mary, Williamsburg, VA 23187, USA * Correspondence: [email protected]; Tel.: +1-(757)-594-7606; Fax: +1-(757)-594-7356 Academic Editor: Paul Nancarrow Received: 20 October 2020; Accepted: 24 November 2020; Published: 3 December 2020 Abstract: Research advances in electropolishing, with respect to the field of metalworking, have afforded significant improvements in the surface roughness and conductivity properties of aluminum polished surfaces in ways that machine polishing and simple chemical polishing cannot. The effects of a deep eutectic medium as an acid-free electrolyte were tested to determine the potential energy thresholds during electropolishing treatments based upon temperature, experiment duration, current, and voltage. Using voltammetry and chronoamperometry tests during electropolishing to supplement representative recordings via atomic force microscopy (AFM), surface morphology comparisons were performed regarding the electropolishing efficiency of phosphoric acid and acid-free ionic liquid treatments for aluminum. This eco-friendly solution produced polished surfaces superior -
Electro-Polishing Information
ATLANTIS RAIL Contact Information: Atlantis Rail Systems 70 Armstrong Road 3900 Civic Center Drive Plymouth, MA 02360 North Las Vegas, NV 89030 (800) 541-6829 or (508) 732-9191 (508) 732-9798 www.atlantisrail.com Table of Contents Note The Benefits of Electropolishing Services 1 Why Electropolish? 2 What is Electropolishing? Rectifier or Electropolishing removes metal from a workpiece by passing DC Power Supply an electric current while the workpiece is submerged in an + electrolyte of a specific composition. The process is - Anode essentially the reverse of “electroplating”. Cathode (Workpiece) Rack IN A PLATING SYSTEM, METAL IONS ARE DEPOSITED FROM THE SOLUTION ONTO THE Tank WORK-PIECE. IN AN ELECTROPOLISHING SYSTEM, THE WORKPIECE ITSELF IS ERODED, ADDING METAL IONS TO THE SOLUTION. Electrolyte Heater Cathode Solution A typical electropolishing system consists of a power supply, cathodes, anode, heater housed in a tank suspended in an Figure A. A typical ectropolishing system. electrolyte solution. (See Figure A). The Benefits of Electropolishing Services Electropolishing removes elemental Iron from the surface of Before stainless steel alloys, enhancing the Chromium/Nickel content resulting in dramatically improved resistance to corrosion. Electropolishing improves the near surface chemistry of stainless steel. Not only does it remove embedded particles and inclusions, it also improves the atomic ratios of the material’s alloying elements. Electropolishing preferentially dissolves Iron from the material and leaves the surface with a higher relative concentration of Chromium. Upon exposure to Oxygen, this improved surface will form a thicker and more uniform oxide layer with enhanced corrosion resistance properties. Electropolished stainless steels are better suited After to resist the onset of pitting corrosion, crevice corrosion, stress corrosion cracking, and microbiologically influenced corrosion. -
Understanding the Mechanism for Electropolishing of Niobium And
On the Mechanism of Niobium Electropolishing THESIS Presented in Partial Fulfillment of the Requirements for the Degree Master of Science in the Graduate School of The Ohio State University By Ashwini Chandra Graduate Program in Materials Science and Engineering The Ohio State University 2012 Master's Examination Committee: Dr Gerald Frankel, Advisor Dr Michael Sumption, Co-Advisor Dr Rudolph Buchheit Copyright by Ashwini Chandra 2012 Abstract Pure Niobium is the material used to make Superconducting Radio Frequency (SRF) cavities. These cavities need to be free from surface defects like pits, bumps and protrusions to achieve the best performance. Electropolishing is commonly used as a final process to give a good surface finish to the niobium surface. The standard electrolyte used for electropolishing niobium is a 1:9 ratio of HF (48%) and H2SO4 (96%) respectively. The mechanism of electropolishing is not fully understood and also the best electropolishing parameters need to be determined. Acid concentration, stirring, temperature and amount of material removed are the parameters expected to affect the surface finish. Their effect is studied using electrochemical polarization measurement, galvanostatic and potentiostatic techniques. The electro-dissolution occurring needs to be under mass transport control for the phenomenon of electropolishing to occur. This is characterized by the presence of a current density plateau in the niobium polarization curves. However Galvanostatic experimental result analysis points to other interfering transport processes as well. Results based on microscopy, surface profile measurement and current transient measurements for different electrode configurations indicate the presence of natural convection as one of the reason which could be causing deviation from a perfect semi infinite linear diffusion model. -
Electropolishing* Written by Walter Schwartz Updated by Dr
Shop Talk Electropolishing* Written by Walter Schwartz Updated by Dr. James H. Lindsay, AESF Fellow Practical applications, equipment, electrolytes and troubleshooting are examined for the elec- tropolishing process. Since the early investigations by Jacquet and Elmore nearly 50 years ago, electropolishing has become a useful tool for a variety of metal finishing applications and has achieved a reasonable degree of commercial development and utility. Essentially, electropolishing is the improvement in the surface finish of a metal by making it anodic Fig. 2—Carbon steel pin (a) before and (b) after electropolishing. in a suitable solution. With the proper selection of current density, temperature and other conditions, the sur- phoric-acid-based electrolyte for 5 min. The leveling and face is smoothed and brightened while metal is removed. brightening of the beryllium-copper surface is dramatic, Figure 1 depicts a fundamental setup for the electropolish- and close inspection of the photomicrograph reveals that ing operation. substantial deburring of the part has also taken place. Figures 2 and 3 are photomicrographs illustrating the The photographs point out some of the outstanding effects of electropolishing on two types of substrates. features of electropolishing. Where the metal or alloy is Figure 2a shows a machined and tapered carbon-steel pin suitable, electropolishing will produce a chemically clean, before electropolishing. Figure 2b shows the same pin lustrous to mirror-bright surface. In contrast to mechani- after electropolishing for 7 min in an electrolyte based cal polishing, electropolishing does not incorporate for- on chromic, sulfuric and phosphoric acids. Almost com- eign inclusions into the surface layer. -
The Electrolytic Polishing of Metals: Application to Copper and Niobium
Proceedings of the 11th Workshop on RF Superconductivity, Lübeck/Travemünder, Germany )81'$0(17$/6 2) (/(&752&+(0,675< 7+( (/(&752/<7,& 32/,6+,1* 2) 0(7$/6 $33/,&$7,21 72 &233(5 $1' 1,2%,80 V. Palmieri ,67,78721$=,21$/(',),6,&$18&/($5( /DERUDWRUL1D]LRQDOLGL/HJQDUR $EVWUDFW moreover, that the severity of plastic deformation at the In the surface polishing system electropolishing is a surface decreases progressively with increasing of fineness of mandatory stem for the preparation of superconducting polish. cavities both bulk niobium made and Niobium sputtered In this context, even if the state of surface vary with the copper. Since the aim of this tutorial is to facilitate the type of mechanical finish, it is instructive looking at approach of newcomers to the field, or to give an hint to experimental results already existing in literature about experts in order to promote further investigation, the mechanically polished Copper surfaces. Turley and Samuels history of the electrolytic polishing is resumed from the [3] for instance report the following microstructure for an beginning. Several explanation attempts are reported, OFHC Copper surface abraded by P1200 grade silicon and a few new techniques are recalled. Nevertheless it carbide abrasive paper (fig. 1). does not exist yet one extensive theory that applies to any polishing system, both metal and electrolyte. Ac- Impedance spectroscopy offers unique insight into such a complex phenomena that, although it is usually considered a simple classical problems, it can be intimately understood only by means of quantum- mechanics. ,1752'8&7,21 The development of new forming techniques for the fabrication of seamless TESLA-type cavities requires good control of the Electro-Polishing process (EP). -
Electropolishing Stainless Steels
Electropolishing Stainless Steels Materials and Applications Series, Volume 11 E l ect r o P o l is h ing stain l ess stee l S Euro Inox Euro Inox is the European market development asso- Full members ciation for stainless steel. Acerinox Members of Euro Inox include: www.acerinox.es • European stainless steel producers ArcelorMittal Stainless Belgium • national stainless steel development associations ArcelorMittal Stainless France • development associations of the alloying element www.arcelormittal.com industries Outokumpu The prime objectives of Euro Inox are to create aware- www.outokumpu.com ness of the unique properties of stainless steel and to further its use in existing applications and in new mar- ThyssenKrupp Acciai Speciali Terni kets. To achieve these objectives, Euro Inox organises www.acciaiterni.it conferences and seminars, issues guidance in printed ThyssenKrupp Nirosta and electronic form to enable architects, designers, www.nirosta.de specifiers, fabricators and end users to become more familiar with the material. Euro Inox also supports Associate members technical and market research. Acroni www.acroni.si British Stainless Steel Association (BSSA) www.bssa.org.uk Cedinox www.cedinox.es Centro Inox www.centroinox.it Informationsstelle Edelstahl Rostfrei www.edelstahl-rostfrei.de International Chromium Development Association (ICDA) www.icdachromium.com ISBN 978-2-87997-310-4 International Molybdenum Association (IMOA) 978-2-87997-311-1 German version www.imoa.info 978-2-87997-312-8 Finnish version Nickel Institute 978-2-87997-313-5 French version www.nickelinstitute.org 978-2-87997-314-2 Italian version 978-2-87997-315-9 Dutch version Paslanmaz Çelik Derneği (PASDER) www.turkpasder.com 978-2-87997-316-6 Polish version 978-2-87997-317-3 Spanish version Polska Unia Dystrybutorów Stali (PUDS) 978-2-87997-318-0 Swedish version www.puds.pl 978-2-87997-319-7 Czech version SWISS INOX 978-2-87997-320-3 Turkish version www.swissinox.ch E l ect r o P o l is h ing stain l ess stee l S Contents Electropolishing Stainless Steels 1. -
Electropolishing of Re-Melted SLM Stainless Steel 316L Parts Using Deep Eutectic Solvents: 3X3 Full Factorial Design
View metadata, citation and similar papers at core.ac.uk brought to you by CORE provided by De Montfort University Open Research Archive Electropolishing of re-melted SLM stainless steel 316L parts using deep eutectic solvents: 3x3 full factorial design K. Alrbaey1, D.I. Wimpenny2, A. A. Al-Barzinj3,4, and A. Moroz1 1School of Engineering and Sustainable Development, De Montfort University, the Gateway, Leicester, LE1 9BH UK. T: +44 (0)116 250 66 49 E-mail: [email protected] 2Manufacturing Technology Centre, Coventry, UK 3Chemistry Department, University of Leicester, Leicester, UK LE1 7RH. E-mail: [email protected] 4Physics Department, University of Salahaddin, Arbil, Iraq Summary This three levels three factors full factorial study describes the effects of electropolishing using deep eutectic solvents on the surface roughness of re-melted 316L stainless steel samples produced by the Selective Laser Melting (SLM) powder bed fusion additive manufacturing method. An improvement in the surface finish of re-melted stainless steel 316L parts was achieved by optimizing the processing parameters for a relatively environmentally friendly (‘green’) electropolishing process using a Choline Chloride ionic electrolyte. The results show that further improvement of the response value- average surface roughness (Ra) can be obtained by electropolishing after re-melting to yield a 75% improvement compared to the as-built Ra. The best Ra value was less than 0.5μm, obtained with a potential of 4 volts, maintained for 30mins at 40C°. Electropolishing has been shown to be effective at removing the residual oxide film formed during the re-melting process. The material dissolution during the process is not homogenous and is directed preferentially towards the iron and nickel, leaving the surface rich in chromium with potentially enhanced properties. -
Electrolytic Polishing of Non-Ferrous Metals
ELECTROLYTIC POLISHING OP NON-FERROUS METALS fey LEOPOLDO MARTI-BALAGUER B, S., Kansas State College of Agriculture and Applied Science, 1951 A THESIS submitted in partial fulfillment of the requirements for the degree MASTER OP SCIENCE Department of Shop Practice KANSAS STATE COLLEGE OP AGRICULTURE AND APPLIED SCIENCE 1951 . mercVs 11 ^ Oq TABLE OP CONTENTS INTRODUCTION 1 The ory , 1 Advantages of Electrolytic Over Mechanical Polishing 2 SURVEY OP LITERATURE 3 PURPOSE 7 EXPERIMENTAL PROCEDURE 8 Equipment , 8 Solutions , .,, 9 Specimens , 9 Proc edure , , 9 RESULTS AND CONCLUSIONS 17 ACKNOWLEDGMENTS 27 REFERENCES , , , 28 INTRODUCTION Electrolytic polishing is in essence the reverse process of electroplating. In the electroplating process the object to "be plated is made the cathode (negative electrode) of a source of direct current in an electrolytic solution which is made of a salt of the metal to be deposited. The anode (positive elec- trode) is made of the metal to be deposited or of an inert mate- rial. In the electropolishing process, on the other hand, the object to be polished is made the positive electrode of a direct current source in a proper solution. The negative electrode may be of any other conductive material which is not attacked by the electrolyte being used. When the direct current is applied, the protruding ridges or high points are dissolved and the surface of the object becomes smooth and bright. Theory i At present there are two theories concerning the mechanism of electrolytic polishing. According to one of the theories the polishing action is caused by the formation of a viscous film which adheres to the surface of the metal.