Operation and Maintenance Manual
Total Page:16
File Type:pdf, Size:1020Kb
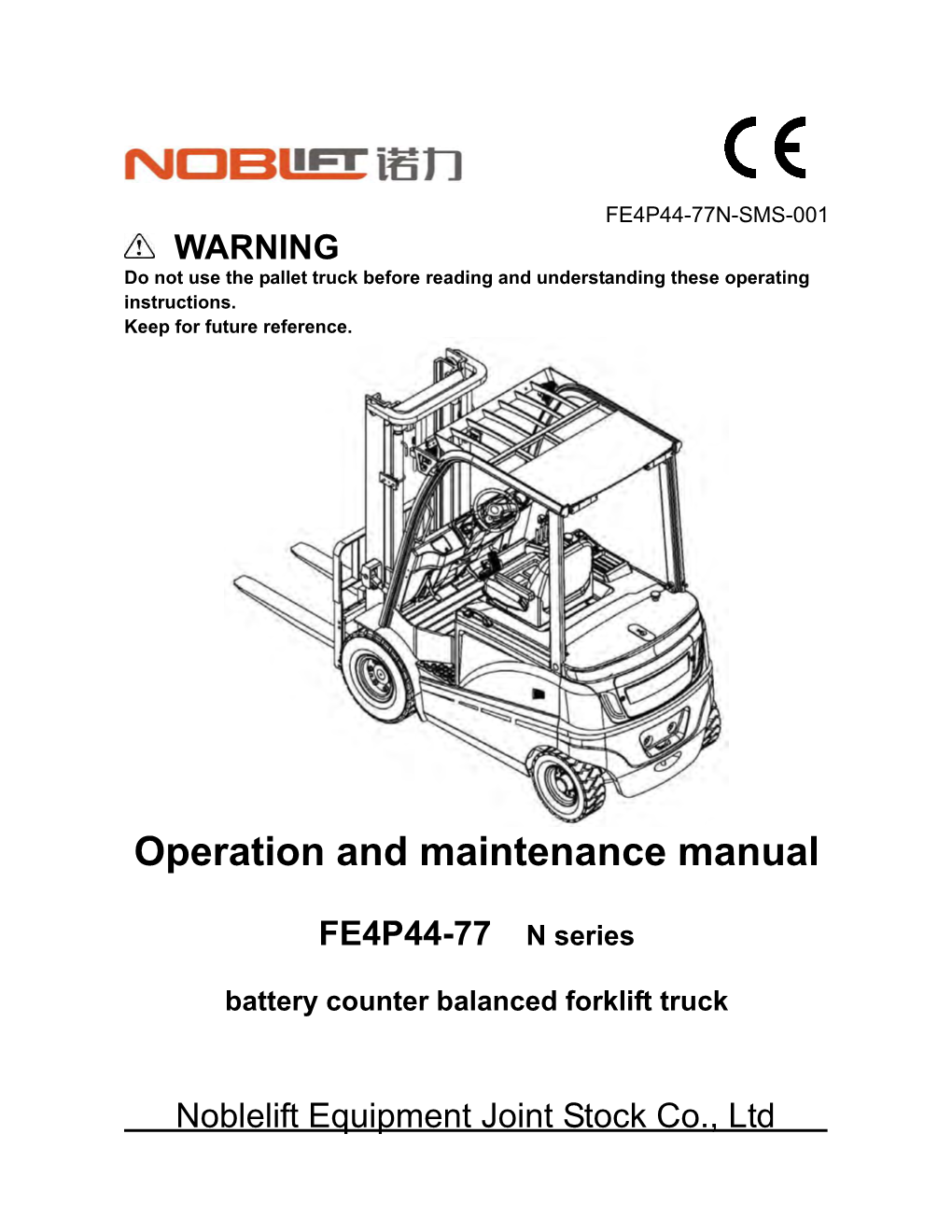
Load more
Recommended publications
-
UC-NRLF GIFT of No
U F UC-NRLF GIFT OF No. 1773 HANDBOOK OF THE 8-INCH GUN MATERIEL (ELEVEN PLATES) JANUARY 19, 1917 WASHINGTON GOVERNMENT PRINTING OFFICE 1917 No. 1773 HANDBOOK OF THE i 3.8-INCH GUN MATERIEL (ELEVEN PLATES) JANUARY 19, 1917 WASHINGTON GOVERNMENT PRINTING OFFICE 1917 111 WAR DEPARTMENT, OFFICE OF THE CHIEF OF ORDNANCE. Washington, January 19, 1917. This manual is published for the information and government of the Regular Army and National Guard of the United States. By order of the Secretary of War: WILLIAM CROZIER, Brigadier General, Chief of Ordnance. (3) 362104 CONTENTS. Page. List of 6 plates. , List of equipment 7 Gun . description 9 Gun, weights, dimensions, etc 9 Range table, service table for shell and shrapnel 10 Ammunition 12 ( 'art ridge case 12 Propelling charge 12 Projectiles 12 ( Common steel shell 12 ( 'ommon shrapnel 13 Fuxes 13 F. A. combination 13 A llowance of ammunition .". 13 Blank ammunition 14 The charge 14 Preparation of blank metallic ammunition 14 Flash targets 14 Drill cartridge 14 Fuze setter, hand, model of 1913 14 Operation 15 Fuze hand old model 15 setter, , Adjustment 16 " Adaptability to other guns 16 Carriage 17 Weights, dimensions, etc 17 Nomenclature of parts 17 Description 23 Adjustment of sights 26 Verification of parallelism of lines of sight and axis of bore 26 Limber. .- 26 Weights, dimensions, etc 26 Nomenclature of parts 27 Description 29 Caisson 30 Weights, dimensions, etc 30 Nomenclature of parts 30 Description 33 Forge limber 33 Battery wagon 33 Store limber 33 Store wagon 33 Repairs for Field Artillery materiel issued to the United States Army and the National Guard 34 Method of loading one 3.8-inch gun battery for transportation by rail 34 Total equipment of a field battery, together with expendable supplies 36 Index 51 (5) LIST OF PLATES. -
Iwaki Walchem Magnetic Drive Pump Mdh-(F) Series Instruction Manual
Thank you for selecting an Iwaki Walchem MDH-(F) Series magnetic drive pump. This instruction manual explains the correct handling, maintenance, inspection and troubleshooting procedures for your pump. Please read through it carefully to ensure the optimum performance, safety and long service of your pump. 1 Unpacking and Inspection IWAKI WALCHEM MODEL MDH-F HEAD (FT.) CAPACITY (GPM) HP 60 Hz. RPM SERIAL NO. HOLLISTON, MA 01746 Fig. 1 Open the package and check that the product conforms to your order. Also, check each of the following points. For any problem or inconsistency, contact your distributor at once. 1. Check that the model number and the HP indicated on the nameplate conform to the specifications of your order. 2. Check that all the accessories you ordered are included. 3. Check that the pump body and parts have not been accidentally damaged or that any bolts or nuts have not been loosened in transit. 1 n IWAKI WALCHEM MAGNETIC DRIVE PUMP MDH-(F) SERIES INSTRUCTION MANUAL IWAKI WALCHEM Corporation Table of Contents 1 Unpacking and Inspection.............................................................................................................. 1 2 Model Identification Guide ............................................................................................................ 2 3 Specifications ................................................................................................................................. 3 4 Handling ....................................................................................................................................... -
The Suprising Adventures of Bampfylde-Moore Carew
THE SUPRISING ADVENTURES OF BAMPFYLDE-MOORE CAREW King of the Beggars Published by the Ex-classics Project, 2016 http://www.exclassics.com King of the Beggars Public Domain -2- Frontispiece Portrait of Carew -3- King of the Beggars CONTENTS Frontispiece....................................................................................................................3 Title Page .......................................................................................................................5 PREFACE......................................................................................................................6 Chapter I His Early Life; Joining the Gypsies ...............................................................7 Chapter II His First Ventures as an Imposter..............................................................12 Chapter III His Trip to Newfoundland; Impersonating a Shipwrecked Fisherman.....16 Chapter IV He Falls Victim to the Tender Passion .....................................................19 Chapter V He Impersonates a Clergyman...................................................................22 Chapter VI Further impostures....................................................................................24 Chapter VII. He is Crowned King of the Beggars .......................................................30 Chapter VIII Not resting on His Authority, He Continues his Career.........................37 Chapter IX He is Imprisoned and Transported to Maryland, but Escapes .................40 Chapter X He -
11 12 Tools Sets
WWW.ENDURATOOLS.COM WWW.ENDURATOOLS.COM 75PC.MACHINE REPAIR SET 48PC.AUTO REPAIR TOOL SET 49PC.TELE-COMMUNICATION TOOL SET 13PC.AUTO REPAIR TOOL SET 50PC.TELE-COMMUNICATION TOOL SET 3 1-Plastic-coated Handled Adjustable Wrench 8" 7-Comb. Wrench 11,12,13,14,15,17,19mm 1-Heavy Duty Adjustable Wrench 6" 12-1/4" Dr. Socket 4,4.5,5,5.5,6,7,8,9,10,11,12,13mm 1-Digital Detecting Screwdriver TOOLS SETS 1-1/4" Dr. Quick-Release Ratchet 2-Screwdriver Slotted 6x38,5x100mm 1 - 1/2" Dr. Quick-Release Ratchet 1-Adjustable Wrench 6" - 1 1/4" Dr. Bit Adapter 2- Screwdriver Phillips 5x100,6x100mm 2-1/4" Dr. Bit Adapter, Spinner Handle - 9 1/2" Dr. Socket 10,12,13,14,15,16,17,19,22mm 3-Long Nose Plier6", Diagonal Nose Plier6", 12-1/4" Dr. Socket 4,4.5,5,5.5,6,7,8,9,10,11,12,13mm 1-1/2" Dr. Extension Bar 5" 8-Comb. Wrench10,11,12,13,14,15,17,19mm 2-Long Nose Plier 6",Diagonal Plier 6" 1-1/2" Dr. Spark Plug Socket 16mm German-type Lineman's Plier6" - - 2-Screwdriver Slotted 6x38,6x100mm - 8 1/2" Dr. Socket 10,11,12,13,14,15,17,19mm 1-Claw Hammer 8oz 2 Screwdriver Slotted 6x38,6x100mm 2 Long Nose Plier 6",Lineman's Plier 7" 2-Screwdriver Phillips #2x38,#2x100mm - 8-1/2" Dr. Socket 20,21,22,23,24,27,30,32mm 2-Screwdriver Phillips #2x38,#2x100 1 Straight Jaw Locking Plier 10" 1-Mini Nylon Handled Hacksaw 6" 2-Digital Detecting Screwdriver, Digital Multi-meter - 1 Groove Joint Plier 10" 1-1/2" Dr. -
Stark Munro Letters,The
THE STARK MUNRO LETTERS BEING A SERIES OF TWELVE LETTERS WRITTEN BY J. STARK MUNRO, M.B., TO HIS FRIEND AND FORMER FELLOW-STUDENT, HERBERT SWANBOROUGH, OF LOWELL, MASSACHUSETTS, DURING THE YEARS 1881-1884 EDITED AND ARRANGED BY A. CONAN DOYLE The letters of my friend Mr. Stark Munro appear to me to form so connected a whole, and to give so plain an account of some of the troubles which a young man may be called upon to face right away at the outset of his career, that I have handed them over to the gentleman who is about to edit them. There are two of them, the fifth and the ninth, from which some excisions are necessary; but in the main I hope that they may be reproduced as they stand. I am sure that there is no privilege which my friend would value more highly than the thought that some other young man, harassed by the needs of this world and doubts of the next, should have gotten strength by reading how a brother had passed down the valley of shadow before him. HERBERT SWANBOROUGH. LOWELL, MASS. THE STARK MUNRO LETTERS. HOME. 30th March, 1881. I have missed you very much since your return to America, my dear Bertie, for you are the one man upon this earth to whom I have ever been able to unreservedly open my whole mind. I don't know why it is; for, now that I come to think of it, I have never enjoyed very much of your confidence in return. -
Tm 55-1015-228-14 Transportability Guidance Howitzer, Light, Towed, 105-Mm, M119
TM 55-1015-228-14 TECHNICAL MANUAL TRANSPORTABILITY GUIDANCE HOWITZER, LIGHT, TOWED, 105-MM, M119 H E A D Q U A R T E R S , D E P A R T M E N T O F T H E A R M Y JANUARY 1990 TM 55-1015-228-14 TECHNICAL M ANUAL HEADQUARTERS DEPARTMENT OF THE ARMY No. 55-1015-228-14 WASHINGTON, DC ,25 January 1990 TECHNICAL MANUAL TRANSPORTABILITY GUIDANCE HOWITZER, LIGHT, TOWED, 105-MM, M119 Paragraph Page CHAPTER 1. INTRODUCTION Purpose and scope . 1-1 1-1 Safety . 1-2 1-1 Definitions of warnings, cautions, and notes . 1-3 1-1 Reporting of recommendations and comments. 1-4 1-1 2. TRANSPORTABILITY DATA Scope . 2-1 2-1 Description . 2-2 2-1 Hazardous and dangerous characteristics . 2-3 2-1 3. SAFETY General . 3-1 3-1 Specific safety requirements. 3-2 3-1 4. AIR TRANSPORTABILITY GUIDANCE Scope . 4-1 4-1 Maximum utilization of aircraft . 4-2 4-1 Applicability. 4-3 4-1 Safety . 4-4 4-1 Preparation of equipment . 4-5 4-1 Transport by US Air Force aircraft . 4-6 4-1 External transport by US Army aircraft. 4-7 4-2 Internal transport by CH–47 helicopter . 4-8 4-7 5. HIGHWAY TRANSPORTABILITY GUIDANCE Section I. GENERAL Scope . 5-1 5-1 Safety . 5-2 5-1 II. TOW AWAY MOVEMENT US highways . 5-3 5-1 European and other country highways . 5-4 5-1 III. TRANSPORT BY SEMITRAILER General . 5-5 5-1 Preparation, loading, and tiedown on semitrailer . -
155-MM HOWITZER MATERIEL MODEL of 1918 (Schneider)
No. 2017 HANDBOOK OF THE 155-MM HOWITZER MATERIEL MODEL OF 1918 (Schneider) MOTORIZED WITH INSTRUCTIONS FOR ITS CARE (FIFTY-FIVE ILLUSTRATIONS) ...•••••••••...••••• DECEMBER 14, 1918 WASHINGTON GOVERNMENT PRINTING OFFICE 1919 ( No. 2017 HANDBOOK OF THE 155-MM HOWITZER MATERIEL MODEL OF 1918 (Schneider) MOTORIZED WITH INSTRUCTIONS FOR ITS CARE (FIFTY-FIVE ILLUSTRATIONS) DECEMBER 14, 1918 WASHINGTON GOVERNMENT PRINTING OFFICE 1919 (Form No., 2017.) The Commanding Officer or the Post or Coast Defense Ordnance Officer to whom this copy is issued will be held personally responsible for its safe-keeping. When another officer relieves him a' receipt for it will be taken, which should be mailed to the CHIEF OF ORDNANCE, U. S. Army, Wash- ington, D. C. NOTE.—This pamphlet should be destroyed when superseded by one of later date. (2) WAR DEPARTMENT, OFFICE OF THE CHIEF OF ORDNANCE, Washington, December 14, 1918. This manual is published for the information and government of the Army of the 'United States. By order of the Secretary of War: C. C. WILLIAMS,. Major General,.Major Chief of Ordnance. (3) PLATE I B 155-mm. Howitzer Carriage, Model of 1918 (Schneider). Traveling Position. CONTENTS. Page. List of plates 10 Table of equivalents 12 PART I.-DESCRIPTION OF MATERIEL. General description of the 155-mm. howitzer materiel 13 155-mm. howitzer 14-20 Table of weights, principal dimensions, etc. Nomenclature of the howitzer. Description of the howitzer. The howitzer. .--,5he breech mechanism. The firing mechanism. The percussion mechanism. Operation of the breech mechanism. To open the breech. To close the breech. Misfirings. Missing of the primer. -
Performance Under Pressure V01/14 V01/14
ER-0404/1995 Since 1940 V01/14 Head Office and Factory LARZEP, S.A. Avenida Urtiaga, 6 48269 MALLABIA, SPAIN Tel. +34 943 171200 Fax. +34 943 174166 e‐mail: [email protected] www.larzep.com LARZEP AUSTRALIA PTY LTD 104 Wedgewood Road Hallam, Victoria, 3803 AUSTRALIA Tel: 03 9796 3744 Fax: 03 9796 5964 e-mail: [email protected] www.larzep.com.au LARZEP AUSTRALIA PTY LTD 49A Sustainable Avenue Bibra Lake, Western Australia, 6163 AUSTRALIA Performance under Pressure Tel: 08 9418 4988 Fax: 08 9418 2644 e-mail: [email protected] www.larzep.com.au V01/14 LARZEP® is an internationally registered trade mark. Any kind of reproduction, even partially, of this catalogue requires a previous written authorization from LARZEP, S.A. LARZEP, S.A. reserves all rights of total or partial modification of its models and features without prior notice. www.larzep.com Performance under PPerformance under PPerformance under Pressurressureessurere Since 1940SinceSince 1940 1940 GENERAL CATALOGUE MODEL INDEX Introduction A ___________________________ 148 D _____________________________56 J _____________________________76 Larzep Since 1940 ____________________________________________________ 1 Petrol Hydraulic Pumps HAG __________________________ 91 AA __________________________ 134 DAH __________________________66 LAS _________________________ 135 Quality and ISO 9001 certificate _________________________________________ 2 Accessories for Powerpacks B-C-H-P-R-T ______________ 92 AB __________________________ 148 DDA __________________________60 LAX _________________________ -
Frederick Douglass
NARRATIVE OF THE LIFE OF FREDERICK DOUGLASS, AN AMERICAN SLAVE BY FREDERICK DOUGLASS 7^WYS`f7Taa]e NARRATIVE OF THE LIFE OF FREDERICK DOUGLASS, AN AMERICAN SLAVE. WRITTEN BY HIMSELF. BOSTON PUBLISHED AT THE ANTI-SLAVERY OFFICE, NO. 25 CORNHILL 1845 Entered, according to Act of Congress, in the year 1845, BY FREDERICK DOUGLASS, in the Clerk’s Office of the District Court of Massachusetts. COPYRIGHT INFORMATION Book: Narrative of the Life of Frederick Douglass Author: Frederick Douglass, 1817?–95 First published: 1845 The original book is in the public domain in the United States and in most, if not all, other countries as well. Readers outside the United States should check their own countries’ copyright laws to be certain they can legally download this ebook. The Online Books Page has an FAQ which gives a summary of copyright durations for many other countries, as well as links to more official sources. This PDF ebook was created by José Menéndez. PREFACE. IN the month of August, 1841, I attended an anti-slavery convention in Nantucket, at which it was my happiness to become acquainted with FREDERICK DOUGLASS, the writer of the following Narrative. He was a stranger to nearly every member of that body; but, having recently made his escape from the southern prison-house of bondage, and feeling his curiosity excited to ascertain the principles and measures of the abolitionists,—of whom he had heard a somewhat vague description while he was a slave,—he was induced to give his attendance, on the occasion alluded to, though at that time a resident in New Bedford. -
Ordnance Instructions for the United States Navy. 1866
1 PART I. PART II. PART III. PART I. CHAPTER I. Part III.), and first expended. Part III.) as nearly as practicable, and after action or exercise, Part II.) Part III.) Part III.) Two boats' Part III.) Part III. for further CHAPTER II. CHAPTER III. CHAPTER IV. CHAPTER V. Part III.), and all the CHAPTER VI. CHAPTER VII. CHAPTER VIII. Ordnance Instructions for the United States by Bureau of Ordnance, USN 2 PART II. PART III. PART III. CHAPTER I. CHAPTER II. Part I.), and to Arrangements for Delivering Part I.). Ledges on the shelves, or CHAPTER III. Part I., Page 10, Art. 42.) Part III.) Part I., to arm | Part I., to arm crew. | Part I., | | | | | | Ordnance Instructions for the United States by Bureau of Ordnance, USN The Project Gutenberg EBook of Ordnance Instructions for the United States Navy., by Bureau of Ordnance, USN This eBook is for the use of anyone anywhere at no cost and with almost no restrictions whatsoever. You may copy it, give it away or re-use it under the terms of the Project Gutenberg License included with this eBook or online at www.gutenberg.org Title: Ordnance Instructions for the United States Navy. 1866. Fourth edition. Author: Bureau of Ordnance, USN Release Date: August 16, 2006 [EBook #19058] Language: English Ordnance Instructions for the United States by Bureau of Ordnance, USN 3 Character set encoding: ISO-8859-1 *** START OF THIS PROJECT GUTENBERG EBOOK ORDNANCE INSTRUCTIONS *** Produced by Jeannie Howse, Curtis Weyant and the Online Distributed Proofreading Team at http://www.pgdp.net (This file was produced from images generously made available by The University of Michigan Making of America collection) ORDNANCE INSTRUCTIONS FOR THE UNITED STATES NAVY. -
Gunnery Instructions, Simplified for The
i\bxM% af §ovi$xw. UNITED STATES OF AMERICA. GUNNERY INSTRUCTIONS SIMPLIFIED FOR THE flolttttte dfors of % St.ft. Dta&|; WITH HINTS TO EXECUTIVE AID OTHER OFFICERS. BT LIEUT. EDWARD BARRETT, IT. S. K, INSTRUCTOR IX GUNNERY, BROOKLYN NAVY YARD. NEW YORK: D. VAN NOSTRAND, 192 BROADWAY. 1862. *" „ Entered, according to Act of Congress, in the Tear 1862, BY D. TAN NOSTEAND, In the Clerk's Office of the District Court of the United States for the Southern District of New York. liy t> *t C. A. ALYORD, STEREOTYPES AND PRINTER. THIS WOEK RESPECTFULLY DEDICATED ACTING MASTERS AND THE ACTING MASTERS' MATES UNITED STATES NAVY. PREFACE. Executive Officers and Officers of Divisions, will find this work particularly valuable as a book of ref- erence and advice to them in the performance of the duties of their respective positions. The disposition of the crew of a man-of-war in every contingency of battle is dictated and the duties of each man defined. Guns, their calibre and weight, the number of men they are entitled to, the stations and duties of each, are all concisely explained. Wherever there is a departure from the " Ordnance Manual," the change has been suggested by experience Edward Barrett, Lieutenant U. S. Nl, Instructor in Gunnery, U. S. Naval Station, New York. GUNNERY INSTRUCTIONS. NOMENCLATIVE OF CANNON. See Figs. 1, 2, 3, 4, 5, 6 and 1. The cascabel, A Z, is that part of the gun behind the base-ring, and in general terms, includes the knob, the neck, and the base of the breech ; but as the forms, and consequently the nomenclature of the subdivisions of the cascabel, as well as the other parts of the gun, vary in guns of different construction, these minor details are given in the diagrams, and the explanation. -
American Lightships, 1820-1983: History, Construction, and Archaeology with the Maritime Cultural Landscape
Abstract American Lightships, 1820-1983: History, Construction, and Archaeology within the Maritime Cultural Landscape by Morgan MacKenzie April, 2011 Director: Dr. Lawrence Babits DEPARTMENT OF HISTORY, PROGRAM IN MARITIME STUDIES In 1820, the United States Government began funding construction and conversion of watercraft for use as lightships. Floating beacons utilized to mark dangerous shoals, reefs, and shifting channels in inland as well as open waters, lightships served where lighthouse construction was unfeasible. This study intends to examine the general history of U.S. lightships, improvements to construction design, technological modifications in illumination and signaling, venue of employment, as well as use, re-use, and the maritime cultural landscape associated with these craft. American Lightships, 1820-1983: History, Construction, and Archaeology within the Maritime Cultural Landscape A Thesis Presented To The Faculty of the Department of History, Program in Maritime Studies East Carolina University In Partial Fulfillment of the Requirements for the Degree Master of Arts By Morgan MacKenzie April 2011 © Copyright 2011 Morgan MacKenzie American Lightships, 1820-1983: History, Construction, and Archaeology within the Maritime Cultural Landscape by Morgan MacKenzie APPROVED BY: DIRECTOR OF THESIS:___________________________________________________ Dr. Lawrence Babits, PhD COMMITTEE MEMBER:__________________________________________________ Dr. Wade Dudley, PhD COMMITTEE MEMBER:__________________________________________________