Characterization of the Interfacial Toughness in a Novel “Gan-On-Diamond” Material for High-Power RF Devices
Total Page:16
File Type:pdf, Size:1020Kb
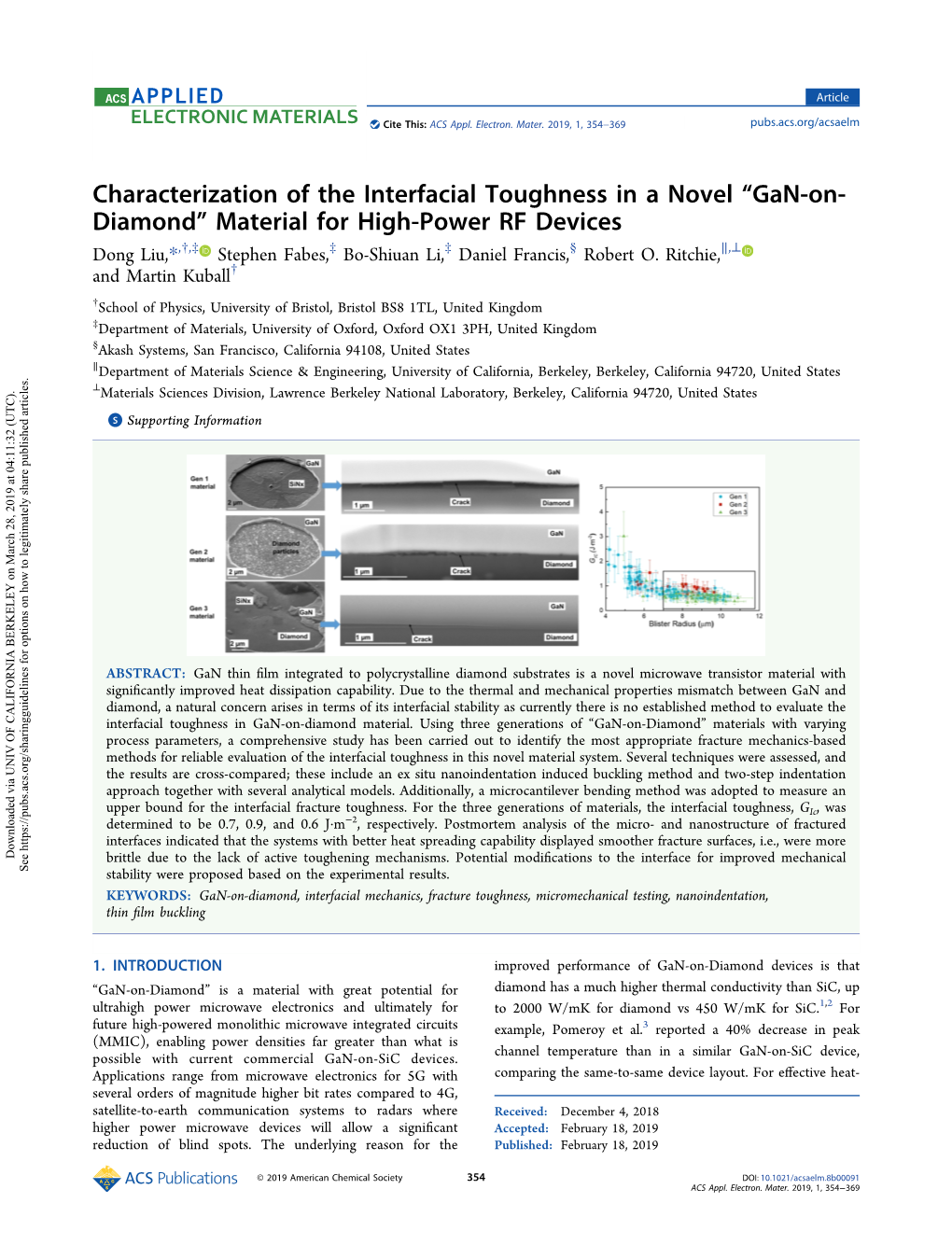
Load more
Recommended publications
-
Novel Nanoindentation-Based Techniques for MEMS and Microfluidics Applications Ke Du University of South Florida
University of South Florida Scholar Commons Graduate Theses and Dissertations Graduate School 11-7-2008 Novel Nanoindentation-Based Techniques for MEMS and Microfluidics Applications Ke Du University of South Florida Follow this and additional works at: https://scholarcommons.usf.edu/etd Part of the American Studies Commons Scholar Commons Citation Du, Ke, "Novel Nanoindentation-Based Techniques for MEMS and Microfluidics Applications" (2008). Graduate Theses and Dissertations. https://scholarcommons.usf.edu/etd/220 This Thesis is brought to you for free and open access by the Graduate School at Scholar Commons. It has been accepted for inclusion in Graduate Theses and Dissertations by an authorized administrator of Scholar Commons. For more information, please contact [email protected]. Novel Nanoindentation-Based Techniques for MEMS and Microfluidics Applications by Ke Du A thesis submitted in partial fulfillment of the requirements for the degree of Master of Science in Mechanical Engineering Department of Mechanical Engineering College of Engineering University of South Florida Major Professor: Alex. A. Volinsky, Ph.D. Craig Lusk, Ph.D. Nathan Crane, Ph.D. Date of Approval: November 7, 2008 Keywords: thin films, mechanical properties, compliant MEMS, electrowetting © Copyright 2008 , Ke Du Dedication I would like to dedicate this manuscript to my relatives, especially my parents. Thanks for their support and encouragement throughout the years. Acknowledgements I would like to thank for my advisor Dr. Volinsky. Without his guidance, -
Nanotechnology for the Forest Products Industry Vision and Technology Roadmap
Nanotechnology for the Forest Products Industry—Vision and Technology Roadmap iii Table of Contents Executive Summary .......................................................................................................... v 1—Overview of the Forest Products Industry ................................................................... 1 2—Vision for Nanotechnology in the Forest Products Industry ....................................... 7 3—R&D Strategy ............................................................................................................ 11 R&D Focus Area 1 Polymer Composites and Nano-Reinforced Materials .............................................. 17 R&D Focus Area 2 Self-Assembly and Biomimetics ................................................................................ 23 R&D Focus Area 3 Cell Wall Nanotechnology ....................................................................................... 27 R&D Focus Area 4 Nanotechnology in Sensors, Processing, and Process Control ................................. 33 R&D Focus Area 5 Analytical Methods for Nanostructure Characterization ......................................... 37 R&D Focus Area 6 Collaboration in Advancing Programs and Conducting Research ........................... 43 4—Implementation Plan: Next Steps and Recommendations ........................................ 45 Appendices .................................................................................................................... 49 A—Workshop Agenda........................................................................................ -
Pencil Hardness
Measuring Coating Mechanical Properties CTT 2019 Rahul Nair Fischer Technology, Inc. 2018 1 Coating Mechanical Properties Characterization Nanoindentation Progressive Load Scratch Fischer Technology, Inc. 2018 2 Characterizing Surfaces Treated surfaces Coatings and Thin Films Composites Fischer Technology, Inc. 2018 3 Coating Mechanical Properties Characterization Fischer Technology, Inc. 2018 4 Coating Mechanical Properties Characterization H a r d n e s s I C r e e p I E l a s t i c i t y I U n i a x i a l M e c h a n i c a l R e s p o n s e I Te n s i l e S t r e n g t h and Te n s i l e S t r e s s I S t i f f n e s s in Te n s i o n - Yo u n g ’ s M o d u l u s I T h e P o i s s o n E f f e c t I S h e a r i n g S t r e s s e s and S t r a i n s S t r e s s - S t r a i n C u r v e s Thermodynamics of M e c h a n i c a l R e s p o n s e I E n t h a l p i c R e s p o n s e I E n t r o p i c R e s p o n s e I Viscoelasticity I S t i f f n e s s I K i n e m a t i c s : the S t r a i n – Displacement R e l a t i o n s I Equilibrium : the S t r e s s R e l a t i o n s I Transformation of S t r e s s e s and S t r a i n s Constitutive I Y i e l d and P l a s t i c F l o w I M u l t i a x i a l S t r e s s S t a t e s I E f f e c t of Hydrostatic P r e s s u r e I E f f e c t of Rate and Temperature I C o n t i n u u m P l a s t i c i t y I T h e Dislocation B a s i s of Y i e l d and C r e e p K i n e t i c s of C r e e p in Crystalline M a t e r i a l s I F r a c t u r e I A t o m i s t i c s of C r e e p R u p t u r e I F r a c t u r e M e c h a n i c s - the E n e r g y - B a l a n c e A p p r o a c h I the S t r e s s I n t e n s i t y A p p r o a c h I F a t i g u e Fischer Technology, Inc. -
Experimental Correlation of Mechanical Properties of the Ti-6Al-4V Alloy at Different Length Scales
metals Article Experimental Correlation of Mechanical Properties of the Ti-6Al-4V Alloy at Different Length Scales Víctor Tuninetti 1,* , Andrés Felipe Jaramillo 1 , Guiomar Riu 2, Carlos Rojas-Ulloa 1 , Amna Znaidi 3, Carlos Medina 4 , Antonio Manuel Mateo 2 and Joan Josep Roa 2,* 1 Department of Mechanical Engineering, Universidad de La Frontera, 4780000 Temuco, Chile; [email protected] (A.F.J.); [email protected] (C.R.-U.) 2 Department of Materials Science and Engineering (CIEFMA), Barcelona School of Engineering (EEBE), Universitat Politècnica de Catalunya-BarcelonaTech, 08019 Barcelona, Spain; [email protected] (G.R.); [email protected] (A.M.M.) 3 Laboratory of Applied Mechanics and Engineering LR-MAI, University Tunis El Manar–ENIT BP37, Tunis 1068, Tunisia; [email protected] 4 Department of Mechanical Engineering, Universidad de Concepción, 4030000 Concepción, Chile; [email protected] * Correspondence: [email protected] (V.T.); [email protected] (J.J.R.); Tel.: +56-452325984 (V.T.); +34-93-413-41-39 (J.J.R.) Abstract: This article focuses on a systematic study of a Ti-6Al-4V alloy in order to extensively characterize the main mechanical properties at the macro-, micro- and submicrometric length scale under different stress fields. Hardness, elastic modulus, true stress–strain curves and strain-hardening exponent are correlated with the intrinsic properties of the a- and b-phases that constitute this alloy. A systematic characterization process followed, considering the -
Cobalt Composites As a Function of Tungsten Carbide Crystal Orientation
Article Nano-Indentation Properties of Tungsten Carbide- Cobalt Composites as a Function of Tungsten Carbide Crystal Orientation Renato Pero 1, Giovanni Maizza 2,*, Roberto Montanari 1 and Takahito Ohmura 3 1 Department of Industrial Engineering, University of Rome “Tor Vergata”, 00133 Rome, Italy; [email protected] (R.P.); [email protected] (R.M.) 2 Department of Applied Science and Technology, Politecnico di Torino, 10129 Torino, Italy 3 High Strength Materials Group, National Institute for Materials Science (NIMS), 1-2-1 Sengen, Ibaraki Tsukuba 305-0047, Japan; [email protected] * Corresponding author: [email protected] Received: 4 April 2020; Accepted: 28 April 2020; Published: 5 May 2020 Abstract: Tungsten carbide-cobalt (WC-Co) composites are a class of advanced materials that have unique properties, such as wear resistance, hardness, strength, fracture-toughness and both high temperature and chemical stability. It is well known that the local indentation properties (i.e., nano- and micro-hardness) of the single crystal WC particles dispersed in such composite materials are highly anisotropic. In this paper, the nanoindentation response of the WC grains of a compact, full- density, sintered WC-10Co composite material has been investigated as a function of the crystal orientation. Our nanoindentation survey has shown that the nanohardness was distributed according to a bimodal function. This function was post-processed using the unique features of the finite mixture modelling theory. The combination of electron backscattered diffraction (EBSD) and statistical analysis has made it possible to identify the orientation of the WC crystal and the distinct association of the inherent nanoindentation properties, even for a small set (67) of nanoindentations. -
Operando Nanoindentation
A3840 Journal of The Electrochemical Society, 164 (14) A3840-A3847 (2017) Operando Nanoindentation: A New Platform to Measure the Mechanical Properties of Electrodes during Electrochemical Reactions Luize Scalco de Vasconcelos, Rong Xu, and Kejie Zhao∗,z School of Mechanical Engineering, Purdue University, West Lafayette, Indiana 47907, USA We present an experimental platform of operando nanoindentation that probes the dynamic mechanical behaviors of electrodes during real-time electrochemical reactions. The setup consists of a nanoindenter, an electrochemical station, and a custom fluid cell integrated into an inert environment. We evaluate the influence of the argon atmosphere, electrolyte solution, structural degradation and volumetric change of electrodes upon Li reactions, as well as the surface layer and substrate effects by control experiments. Results inform on the system limitations and capabilities, and provide guidelines on the best experimental practices. Furthermore, we present a thorough investigation of the elastic-viscoplastic properties of amorphous Si electrodes, during cell operation at different C-rates and at open circuit. Pure Li metal is characterized separately. We measure the continuous evolution of the elastic modulus, hardness, and creep stress exponent of lithiated Si and compare the results with prior reports. operando indentation will provide a reliable platform to understand the fundamental coupling between mechanics and electrochemistry in energy materials. © The Author(s) 2017. Published by ECS. This is an open access article distributed under the terms of the Creative Commons Attribution 4.0 License (CC BY, http://creativecommons.org/licenses/by/4.0/), which permits unrestricted reuse of the work in any medium, provided the original work is properly cited. -
Indentation Hardness Measurements at Macro-, Micro-, and Nanoscale: a Critical Overview
Tribol Lett (2017) 65:23 DOI 10.1007/s11249-016-0805-5 REVIEW Indentation Hardness Measurements at Macro-, Micro-, and Nanoscale: A Critical Overview Esteban Broitman1 Received: 25 September 2016 / Accepted: 15 December 2016 / Published online: 28 December 2016 Ó The Author(s) 2016. This article is published with open access at Springerlink.com Abstract The Brinell, Vickers, Meyer, Rockwell, Shore, 1 Introduction IHRD, Knoop, Buchholz, and nanoindentation methods used to measure the indentation hardness of materials at The hardness of a solid material can be defined as a mea- different scales are compared, and main issues and mis- sure of its resistance to a permanent shape change when a conceptions in the understanding of these methods are constant compressive force is applied. The deformation can comprehensively reviewed and discussed. Basic equations be produced by different mechanisms, like indentation, and parameters employed to calculate hardness are clearly scratching, cutting, mechanical wear, or bending. In metals, explained, and the different international standards for each ceramics, and most of polymers, the hardness is related to method are summarized. The limits for each scale are the plastic deformation of the surface. Hardness has also a explored, and the different forms to calculate hardness in close relation to other mechanical properties like strength, each method are compared and established. The influence ductility, and fatigue resistance, and therefore, hardness of elasticity and plasticity of the material in each mea- testing can be used in the industry as a simple, fast, and surement method is reviewed, and the impact of the surface relatively cheap material quality control method. -
Nanoindentation and XPS Studies of Titanium TNZ Alloy After Electrochemical Polishing in a Magnetic Field
Materials 2015, 8, 205-215; doi:10.3390/ma8010205 OPEN ACCESS materials ISSN 1996-1944 www.mdpi.com/journal/materials Article Nanoindentation and XPS Studies of Titanium TNZ Alloy after Electrochemical Polishing in a Magnetic Field Tadeusz Hryniewicz 1,†,*, Krzysztof Rokosz 1,†, Ryszard Rokicki 2 and Frédéric Prima 3 1 Division of Surface Electrochemistry, Koszalin University of Technology, Racławicka 15-17, Koszalin 75-620, Poland; E-Mail: [email protected] 2 Electrobright, 142 W. Main St., Macungie, PA 18062, USA; E-Mail: [email protected] 3 Institut de Recherche de Chimie Paris, CNRS–Chimie ParisTech, 11 rue Pierre et Marie Curie, Paris 75005, France; E-Mail: [email protected] † These authors contributed equally to this work. * Author to whom correspondence should be addressed; E-Mail: [email protected]; Tel.: +48-94-3478244. Academic Editor: Daolun Chen Received: 19 September 2014 / Accepted: 25 December 2014 / Published: 8 January 2015 Abstract: This work presents the nanoindentation and XPS results of a newly-developed biomaterial of titanium TNZ alloy after different surface treatments. The investigations were performed on the samples AR (as received), EP (after a standard electropolishing) and MEP (after magnetoelectropolishing). The electropolishing processes, both EP and MEP, were conducted in the same proprietary electrolyte based on concentrated sulfuric acid. The mechanical properties of the titanium TNZ alloy biomaterial demonstrated an evident dependence on the surface treatment method, with MEP samples revealing extremely different behavior and mechanical properties. The reason for that different behavior appeared to be influenced by the surface film composition, as revealed by XPS study results displayed in this work. -
The Edge Effect in Nanoindentation Joseph E
Philosophical Magazine 2010, 1-13, iFirst The edge effect in nanoindentation Joseph E. Jakesab and Donald S. Stoneac* aMaterials Science Program, University of Wisconsin-Madison, Madison, Wisconsin, USA; bPerformance Enhanced Biopolymers, United States Forest Service, Forest Products Laboratory, Madison, Wisconsin, USA; ‘Department of Materials Science and Engineering, University of Wisconsin-Madison, Madison, Wisconsin, USA (Received 23 October 2009; final version received 19 May 2010) Until recently, obtaining unambiguous data from a nanoindentation measurement placed near a free edge has not been possible because the discontinuity associated with the edge introduces artifacts into the measurement. The primary consequence of a free edge is to introduce a structural compliance, Cs, into the measurement. Like the machine compliance, Cm, Cs is independent of the size of the indent and it adds to the measured unloading compliance; but unlike Cm, Cs is a function of position. Accounting for Cs in nanoindentation analyses removes the artifacts in nanoindentation measurements associated with the edge, allowing researchers to more accurately probe material properties near an edge. Expressions were obtained for the effect of the free edge on hardness and modulus measured using the Oliver-Pharr method. The theory was tested on specimens including fused silica, poly(methyl methacrylate), and alayered silicon-on-insulatorspecimen. Keywords: nanoindentation; edge effect 1. Introduction A key capability of nanoindentation is its ability to probe local mechanical properties in specimens that are highly non-uniform. Determining how properties change near an edge, such as the interface between phases or a free edge, is often of interest. The problem with making those kinds of measurements is that, above and beyond any effect associated with changes in properties near the edge, the presence of the elastic discontinuity will itself give rise to effects, i.e. -
Nanotechnology Applications in the Forest Products Industry by Robert J
Nanotechnology Applications in the Forest Products Industry By Robert J. Moon, Charles R. Frihart, and Theodore Wegner The National Nanotechnology Initiative (NNI) was has grown to 12 and 25, respectively.1 The vision of the NNI established in 2001 to coordinate the R&D of nanoscale sci is a future in which the ability to understand and control ence, engineering, and technology across the federal gov matter at the nanoscale level leads to a revolution in tech ernment. The Nanoscale Science, Engineering and nology and industry. The four goals of NNI are to 1) maintain Technology Subcommittee coordinates in the NNI and oper a world-class R&D program aimed at realizing the full poten ates under the auspices of the National Science and tial of nanotechnology; 2) facilitate transfer of new tech Technology Council. In its first year, NNI was composed of nologies into products for economic growth, jobs, and other six agencies investing in nanotechnology. Since that time, public benefits; 3) support responsible development of nan the annual federal investment has more than doubled in otechnology; and 4) develop educational resources, a nanotechnology R&D to approximately $1.3 billion, while skilled workforce, and the supporting infrastructure and the number of funding and participating federal agencies tools to advance nanotechnology. In addition, the NNI is 4 MAY 2006 developing a national infrastructure that will provide access products industry to include paper, composites, and solid to user centers that house expensive and sophisticated sawnlumber.Specifically,thealliancehasidentifiedsixmajor equipment that is necessary but not cost effective for any areas of technological needs: 1) advancing the forest biorefin one group or institution to purchase and maintain. -
Fabrication of Zinc–Tungsten Carbide Nanocomposite Using Cold
Fabrication of Zinc–Tungsten Carbide candidate for potential applications in biodegradable implants [4,10]. Due to a relatively weak mechanical strength, Zn is widely Nanocomposite Using Cold Compaction used as an alloy addition [11] and coating material in galvaniza- tion [12] but not much for load-bearing structures [13]. It has been Followed by Melting a long standing challenge to enhance the mechanical strength of zinc toward a prominent material with a combination of high Injoo Hwang strength, high corrosion resistivity and great biocompatibility. A great deal of studies have been conducted to improve the mechan- Department of Mechanical and Aerospace Engineering, ical properties of Zn for applications such as load-bearing stents University of California, Los Angeles, [4,14]. Los Angeles, CA 90095 Since conventional manufacturing processes (e.g., alloying) e-mail: [email protected] have already reached their limits to improve mechanical proper- ties of Zn [12], innovative methods have been applied to tackle Zeyi Guan this problem. For example, nanoparticles have been introduced to Downloaded from http://asmedigitalcollection.asme.org/manufacturingscience/article-pdf/140/8/084503/6406225/manu_140_08_084503.pdf by guest on 02 October 2021 Department of Mechanical and Aerospace Engineering, Zn to improve its properties [15]. According to the research on ceramic nanoparticle-reinforced metal matrix nanocomposites University of California, Los Angeles, recently [16–20], ceramic nanoparticles were able to improve the Los Angeles, CA 90095 mechanical strength, not only by the intrinsic high mechanical e-mail: [email protected] strength but also by the grain refinement, which introduces more grain boundaries to impede the movement of dislocations. -
Nanoindentation of Soft Biological Materials
micromachines Review Nanoindentation of Soft Biological Materials Long Qian and Hongwei Zhao * School of Mechanical and Aerospace Engineering, Jilin University, Changchun 130025, China; [email protected] * Correspondence: [email protected]; Tel.: +86-0431-85095757 Received: 29 October 2018; Accepted: 5 December 2018; Published: 11 December 2018 Abstract: Nanoindentation techniques, with high spatial resolution and force sensitivity, have recently been moved into the center of the spotlight for measuring the mechanical properties of biomaterials, especially bridging the scales from the molecular via the cellular and tissue all the way to the organ level, whereas characterizing soft biomaterials, especially down to biomolecules, is fraught with more pitfalls compared with the hard biomaterials. In this review we detail the constitutive behavior of soft biomaterials under nanoindentation (including AFM) and present the characteristics of experimental aspects in detail, such as the adaption of instrumentation and indentation response of soft biomaterials. We further show some applications, and discuss the challenges and perspectives related to nanoindentation of soft biomaterials, a technique that can pinpoint the mechanical properties of soft biomaterials for the scale-span is far-reaching for understanding biomechanics and mechanobiology. Keywords: nanoindentation; mechanical properties; soft biomaterials; viscoelasticity; atomic force microscopy (AFM) 1. Introduction Mechanical behavior of biological materials has come to the front stage recently, not only since its importance from the mechanical and load-bearing viewpoints, but also in the way that it influences other bio-functionalities [1]. Recent studies have directly linked major biological performances, mechanisms, and diseases to the mechanical response from the biomolecular up to the organ level [2–7].