Providing Unique Fracture Mechanics Capabilities
Total Page:16
File Type:pdf, Size:1020Kb
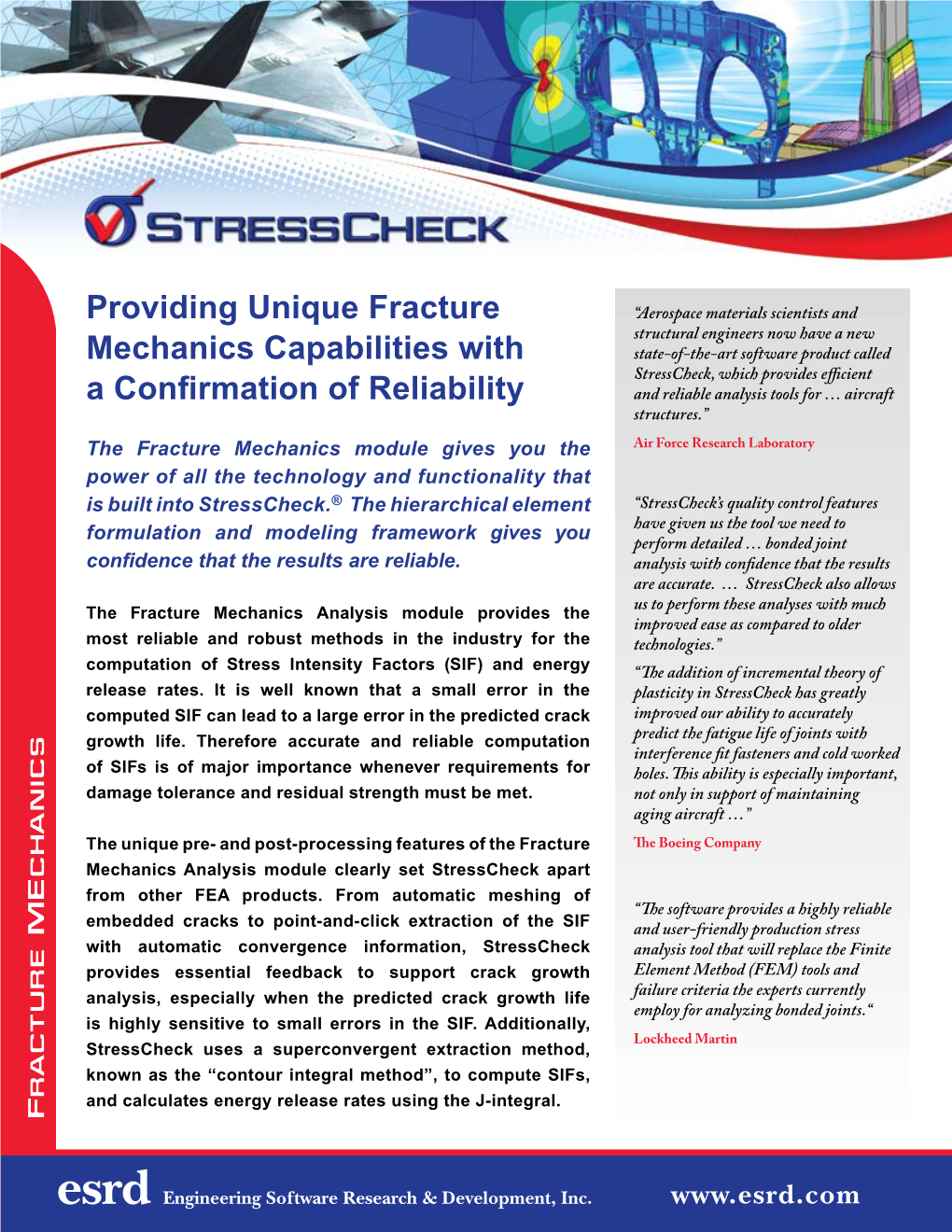
Load more
Recommended publications
-
How Similitude Can Improve Our Understanding of Fatigue Delamination Growth
Misinterpreting the Results: How Similitude can Improve our Understanding of Fatigue Delamination Growth *Submitted for publishing in Composites Science and Technology on March 25 2010 Calvin Rans, René Alderliesten, Rinze Benedictus Structural Integrity Group, Faculty of Aerospace Engineering, Delft University of Technology, P.O. Box 5058, 2600 GB Delft, The Netherlands Abstract: Use of the strain energy release rate for characterizing delamination growth in composite and bonded structures is now commonplace. Although its use is common, a consensus on the best formulation of strain energy release rate has not been reached for describing fatigue delamination growth. Most commonly selected formulations are the maximum strain energy release rate and the strain energy release rate range. This paper examines the use strain energy release rate range and how a misconception of its definition is misleading our understanding of fatigue delamination growth. Keywords: Delamination, fatigue, strain energy release rate, similitude 1. INTRODUCTION The study and characterization of delamination growth behaviour has gained significant attention in the research community due to the growing use of composite structures in a wide range of structural applications. A widely utilized approach is to apply a linear elastic fracture mechanics (LEFM) description using the strain energy release rate (G) in a manner analogous to metal crack growth in terms of the stress intensity factor (K). The primary reason for the use of G rather than K is that the local crack-tip stresses used to determine K are difficult to obtain in inhomogeneous composite laminates [1, 2]. Use of G avoids the need to determine crack-tip stresses. -
Fastran an Advanced Non-Linear Crack-Closure Based Life-Prediction Code
FASTRAN AN ADVANCED NON-LINEAR CRACK-CLOSURE BASED LIFE-PREDICTION CODE J. C. Newman, Jr. Department of Aerospace Engineering Mississippi State University AFGROW WORKSHOP Layton, Utah September 15, 2015 ffa OUTLINE OF PRESENTATION • Brief History on Fatigue-Crack Growth • Plasticity-Induced Crack-Closure Model • Crack Initiation and Small-Crack Behavior • Fatigue-Crack Growth and Fracture • Concluding Remarks fastran # 2 Stress Concentration Factor for an Elliptical Hole in an Infinite Plate Inglis (1913) c se = S KT 2c c fastran # 3 Notch Strength Analysis – Fracture Mechanics c c Paul Kuhn George Irwin Notch Strength Analysis Fracture Mechanics (Neuber ) (Griffith) fastran # 4 Father of “Modern” Fracture Mechanics Irwin, 1957 George Rankin Irwin (1907-1998) + T fastran # 5 5 25 Notch-Strength Analyses: McEvily and Illg (LaRC), NACA TN-4394, 1958 7075-T6 KNSnet against da/dN fastran # 6 Fracture Mechanics: Paris, Gomez, and Anderson, Trends in Engineering, Seattle, WA, 1961 LEFM: K against d(2a)/dN Paris (1970): KNSnet ~ Kmax fastran # 7 Plasticity-Induced Fatigue-Crack Closure: Elber, 1968 fastran # 8 DOMINANT MECHANISMS OF FATIGUE-CRACK CLOSURE Plastic wake Oxide debris Elber, 1968 Beevers, 1979 Paris et al., 1972 Newman, 1976 Suresh & Ritchie, 1982 Suresh & Ritchie, 1981 (a)(FASTRAN) Plasticity-induced (b) Roughness-induced (c) Oxide/corrosion product- closure closure fastran induced # 9 closure OUTLINE OF PRESENTATION • Brief History on Fatigue-Crack Growth • Plasticity-Induced Crack-Closure Model • Crack Initiation and Small-Crack -
4.2 Failure Criteria
4.2 Failure Criteria The determination of residual strength for uncracked structures is straightforward because the ultimate strength of the material is the residual strength. A crack in a structure causes a high stress concentration resulting in a reduced residual strength. When the load on the structure exceeds a certain limit, the crack will extend. The crack extension may become immediately unstable and the crack may propagate in a fast uncontrollable manner causing complete fracture of the component. Figure 4.2.1 illustrates the results obtained from a series of tests conducted on a lug geometry containing a crack. The lug geometry shown in Figure 4.2.1a is a single-load-path structure. Figure 4.2.1b indicates that the cracks in each of the three tests extended abruptly at a critical level of load, which is noted to be a function of a crack length. The crack length-critical load level data shown in Figure 4.2.1b provide the basis for establishing the residual strength capability curve. The locus of critical load levels as a function of crack length is shown in Figure 4.2.1c, where the residual strength capability of the lug structure is shown to decrease with increasing crack length. Figure 4.2.1. Description of Crack Geometry and Residual Strength Results Considering the preceding in terms of applied stress (σ) rather than load gives the σ versus a and σc versus ac plots as shown in Figure 4.2.2 a and b. Schematically, the plots exhibit the same abrupt fracture behavior as the curves presented in Figure 4.2.1. -
A Review on Stress Intensity Factor B.D Bhalekar1, R
International Research Journal of Engineering and Technology (IRJET) e-ISSN: 2395 -0056 Volume: 03 Issue: 03 | March-2016 www.irjet.net p-ISSN: 2395-0072 A Review on Stress Intensity Factor B.D Bhalekar1, R. B. Patil2 1 Post Graduate student, Mechanical Engineering department, JNEC, Maharashtra, India 2 Associate Professor., Mechanical Engineering department, JNEC, Maharashtra, India ---------------------------------------------------------------------***--------------------------------------------------------------------- Abstract - In this paper effort are taken to review on predictions with real life failures fractography is widely the Stress Analysis of cracked plate for the used with fracture mechanics. The prediction of crack growth is very important in damage tolerance discipline. determination of stress intensity factor near the crack The objective of fracture mechanics is to determine what tip. Cracks in plates with different configurations often conditions will create and drive a crack. Engineers can observed in both modern and classical aerospace, expertly design against this particular mode of failure by mechanical engineering structure. To understand effect understanding the phenomena of fracture. of loading mode and crack configuration on load bearing capacity of such plate is very significant in 2. FRACTURE FAILURE designing of structure. There are number of Analytical, Consider a cracked plate on which a force is applied which Numerical, and experimental technique available for might enable the crack to propagate. Irwin projected a stress analysis to determine the stress intensity factor classification matching to the three situations represented near crack tip under different loading modes in an in Fig .1. Thus, three distinct modes are considered: mode infinite and finite cracked plate made up of different I, mode II and mode III. -
Residual Stress Effects on Fatigue Life Via the Stress Intensity Parameter, K
University of Tennessee, Knoxville TRACE: Tennessee Research and Creative Exchange Doctoral Dissertations Graduate School 12-2002 Residual Stress Effects on Fatigue Life via the Stress Intensity Parameter, K Jeffrey Lynn Roberts University of Tennessee - Knoxville Follow this and additional works at: https://trace.tennessee.edu/utk_graddiss Part of the Engineering Science and Materials Commons Recommended Citation Roberts, Jeffrey Lynn, "Residual Stress Effects on Fatigue Life via the Stress Intensity Parameter, K. " PhD diss., University of Tennessee, 2002. https://trace.tennessee.edu/utk_graddiss/2196 This Dissertation is brought to you for free and open access by the Graduate School at TRACE: Tennessee Research and Creative Exchange. It has been accepted for inclusion in Doctoral Dissertations by an authorized administrator of TRACE: Tennessee Research and Creative Exchange. For more information, please contact [email protected]. To the Graduate Council: I am submitting herewith a dissertation written by Jeffrey Lynn Roberts entitled "Residual Stress Effects on Fatigue Life via the Stress Intensity Parameter, K." I have examined the final electronic copy of this dissertation for form and content and recommend that it be accepted in partial fulfillment of the equirr ements for the degree of Doctor of Philosophy, with a major in Engineering Science. John D. Landes, Major Professor We have read this dissertation and recommend its acceptance: J. A. M. Boulet, Charlie R. Brooks, Niann-i (Allen) Yu Accepted for the Council: Carolyn R. Hodges Vice Provost and Dean of the Graduate School (Original signatures are on file with official studentecor r ds.) To the Graduate Council: I am submitting herewith a dissertation written by Jeffrey Lynn Roberts entitled “Residual Stress Effects on Fatigue Life via the Stress Intensity Parameter, K.” I have examined the final electronic copy of this dissertation for form and content and recommend that it be accepted in partial fulfillment of the requirements for the degree of Doctor of Philosophy, with a major in Engineering Science. -
Calculation 32-9222042-000, "ASME Section XI End of Life Analysis
Enclosure Relief Request 52 Proposed Alternative in Accordance with 10 CFR 50.55a(a)(3)(i) ATTACHMENT 1 ASME Section Xl End of Life Analysis of PVNGS Unit 3 RV BMI Nozzle Repair 0402-01-FOl (Rev. 018, 01/30/2014) A CALCULATION SUMMARY SHEET (CSS) AREVA Document No. 32 - 9222042 - 000 Safety Related: MYes El No Title ASME Section Xl End of Life Analysis of PVNGS3 RV BMI Nozzle Repair (Non-Proprietary) PURPOSE AND SUMMARY OF RESULTS: AREVA Inc. proprietary information in the document is indicated by pairs of braces "[I". PURPOSE: Visual inspection of the reactor vessel Bottom Mounted Instrument (BMI) nozzles at Palo Verde Nuclear Generation Station, Unit 3 (PVNGS3), in October of 2013 revealed the presence of boric acid crystals on the outside of the lower head at BMI nozzle #3. Boric acid deposits at the gap between the nozzle and head indicate leakage of primary water through cracks in the J-groove weld and the nozzle wall. AREVA performed a half nozzle repair of nozzle #3 that maintained the full incore instrumentation functionality of the nozzle. This repair, described in References [1] and [2], moves the primary pressure boundary nozzle weld from the inside of the vessel to a weld pad on the outside surface. This calculation evaluates fatigue crack growth of postulated radial-axial flaws in the existing J-Groove weld and buttering of PVNGS BMI nozzle #3 until the plant license expiration in 2047 (Reference [15]). Acceptance of each postulated flaw is determined based on available fracture toughness or ductile tearing resistance using the safety factors outlined in Table 1-1. -
Stress Intensity of Delamination in a Sintered-Silver Interconnection Preprint D
Stress Intensity of Delamination in a Sintered-Silver Interconnection Preprint D. J. DeVoto and P. P. Paret National Renewable Energy Laboratory A. A. Wereszczak Oak Ridge National Laboratory Presented at IMAPS/HiTEC Albuquerque, New Mexico May 13–15, 2014 NREL is a national laboratory of the U.S. Department of Energy Office of Energy Efficiency & Renewable Energy Operated by the Alliance for Sustainable Energy, LLC This report is available at no cost from the National Renewable Energy Laboratory (NREL) at www.nrel.gov/publications. Conference Paper NREL/CP-5400-61598 August 2014 Contract No. DE-AC36-08GO28308 NOTICE The submitted manuscript has been offered by an employee of the Alliance for Sustainable Energy, LLC (Alliance), a contractor of the US Government under Contract No. DE-AC36-08GO28308. Accordingly, the US Government and Alliance retain a nonexclusive royalty-free license to publish or reproduce the published form of this contribution, or allow others to do so, for US Government purposes. This report was prepared as an account of work sponsored by an agency of the United States government. Neither the United States government nor any agency thereof, nor any of their employees, makes any warranty, express or implied, or assumes any legal liability or responsibility for the accuracy, completeness, or usefulness of any information, apparatus, product, or process disclosed, or represents that its use would not infringe privately owned rights. Reference herein to any specific commercial product, process, or service by trade name, trademark, manufacturer, or otherwise does not necessarily constitute or imply its endorsement, recommendation, or favoring by the United States government or any agency thereof. -
Fracture Mechanics Me312
FRACTURE MECHANICS ME312 Hamrock Section 6.3 through 6.5 Just as studying Column Buckling lets us avoid rapid failure of structures by unstable bending, Fracture Mechanics (FM) lets us avoid rapid failure of structures by unstable cracking. Examples of unstable cracking are a balloon contacted by a sharp object, and the Aloha Airlines 737 shown on page 265 of Hamrock. The “wrong” combination of materials, loads, and initiating crack can result in rapid “unzipping” of a structure. In section 6.2, we saw that holes and notches in plates and bars caused stress concentrations above the average stress due to tension, torsion, or bending loading. For a general, ellipse-shaped hole of width = 2a and height = 2b, in a very wide plate, the stress concentration factor is: a K = 1+ 2 Eqn. 6.2 c b This is more commonly called “Kt” for b “theoretical.” If the hole is circular, a = b and K = 3. This agrees with Hamrock’s Fig. 6.2a c a for a wide plate with a central hole. For cracks, however, “b” is very, very small compared to “a”, and Kc calculated by this equation gets huge. Right at the crack tip, the stress is high enough to actually cause a small volume of the material to yield and redistribute the stress in ductile materials, or cause local microfractures in brittle materials. )If stresses are high enough at the tip of a crack of sufficient length, even a ductile material will “unzip” – have a sudden “brittle-like” fracture. Rather than deal with giant stress concentrations, Fracture Mechanics uses a stress intensity factor, K. -
Development and Validation of Crack Growth Models and Life
DOT/FAA/AR-07/50 Development and Validation of Air Traffic Organization Operations Planning Crack Growth Models and Life Office of Aviation Research and Development Enhancement Methods for Washington, DC 20591 Rotorcraft Damage Tolerance November 2007 Final Report This document is available to the U.S. public through the National Technical Information Service (NTIS), Springfield, Virginia 22161. U.S. Department of Transportation Federal Aviation Administration NOTICE This document is disseminated under the sponsorship of the U.S. Department of Transportation in the interest of information exchange. The United States Government assumes no liability for the contents or use thereof. The United States Government does not endorse products or manufacturers. Trade or manufacturer's names appear herein solely because they are considered essential to the objective of this report. This document does not constitute FAA certification policy. Consult your local FAA aircraft certification office as to its use. This report is available at the Federal Aviation Administration William J. Hughes Technical Center’s Full-Text Technical Reports page: actlibrary.tc.faa.gov in Adobe Acrobat portable document format (PDF). Technical Report Documentation Page 1. Report No. 2. Government Accession No. 3. Recipient's Catalog No. DOT/FAA/AR-07/50 4. Title and Subtitle 5. Report Date DEVELOPMENT AND VALIDATION OF CRACK GROWTH MODELS AND November 2007 LIFE ENHANCEMENT METHODS FOR ROTORCRAFT DAMAGE TOLERANCE 6. Performing Organization Code 7. Author(s) 8. Performing Organization Report No. S. R. Daniewicz and J. C. Newman 9. Performing Organization Name and Address 10. Work Unit No. (TRAIS) Mississippi State University P.O. Box 6156 Mississippi State, MS 39762 11. -
Stress Intensity and Fracture Toughness
Issue No. 68 – August 2014 New Publication Stress Intensity and Fracture Toughness (This issue of Technical Tidbits continues the materials science refresher series on basic concepts of How intense is your material properties.) In prior editions, we have demonstrated how to estimate the fatigue life of a component through characterization of test specimens using cyclically applied stresses or strain, followed stress level – An introduction to fracture by analysis of the data. The fracture mechanics method is fundamentally different, since it is the study of mechanics . how fatigue cracks grow through a given material, and is more concerned with what is happening at the tips of growing cracks than with macro-scale loading. A quick introduction to fracture mechanics is required before any discussion of how to apply it to fatigue analysis can begin. A quick overview of the method starts with the test specimens used to generate the data. Each specimen starts with a pre-existing crack of a given length "a". Stress intensity is categorized according to mode, as , shown in Figure 1. Mode I is a spreading apart of the two halves of the crack interface, recognizable as the most severe case. (When people split logs with a wedge, they are using Mode I fracture mechanics, although they are most likely unaware that they are doing so.) Failures due to Mode I crack propagation . Stress Intensity are by far the most common, while Mode III is mainly of academic interest. Stress Intensity Undeformed Mode I Factors (KI, KII, KIII) . Critical Stress Intensity Factors (KIC, KIIC, KIIIC) . Plane Strain Fracture Toughness . -
Study of Mixed Mode Stress Intensity Factor Using the Experimental Method of Transmitted Caustics Nasser Soltani Iowa State University
Iowa State University Capstones, Theses and Retrospective Theses and Dissertations Dissertations 1989 Study of mixed mode stress intensity factor using the experimental method of transmitted caustics Nasser Soltani Iowa State University Follow this and additional works at: https://lib.dr.iastate.edu/rtd Part of the Applied Mechanics Commons Recommended Citation Soltani, Nasser, "Study of mixed mode stress intensity factor using the experimental method of transmitted caustics " (1989). Retrospective Theses and Dissertations. 9182. https://lib.dr.iastate.edu/rtd/9182 This Dissertation is brought to you for free and open access by the Iowa State University Capstones, Theses and Dissertations at Iowa State University Digital Repository. It has been accepted for inclusion in Retrospective Theses and Dissertations by an authorized administrator of Iowa State University Digital Repository. For more information, please contact [email protected]. INFORMATION TO USERS The most advanced technology has been used to photo graph and reproduce this manuscript from the microfilm master. UMI films the text directly from the original or copy submitted. Thus, some thesis and dissertation copies are in typewriter face, while others may be from any type of computer printer. The quality of this reproduction is dependent upon the quality of the copy submitted. Broken or indistinct print, colored or poor quality illustrations and photographs, print bleedthrough, substandard margins, and improper alignment can adversely affect reproduction. In the unlikely event that the author did not send UMI a complete manuscript and there are missing pages, these will be noted. Also, if unauthorized copyright material had to be removed, a note will indicate the deletion. -
Finite Element Method to Determine Stress Intensity Factor Using J Integral Approach
International J. of Math. Sci. & Engg. Appls. (IJMSEA) ISSN 0973-9424, Vol. 9 No. III (September, 2015), pp. 211-221 FINITE ELEMENT METHOD TO DETERMINE STRESS INTENSITY FACTOR USING J INTEGRAL APPROACH S. SUNDARESAN1, SIVA VIJAY2, A. P. BEENA3, C. K. KRISHNADASAN4 AND B. NAGESWARA RAO5 1−4 Structural Analysis and Testing Group, Vikram Sarabhai Space Centre, Trivandrum, India 5 Department of Mechanical Engineering, School of Mechanical and Civil Sciences, KL University, Vaddeswaram, India Abstract Finite element methods (FEM) are widely employed in Damage Tolerance (DT) assessment of structural components. It has become very important concept in pre- dicting strength and life of cracked structures. For assessing the strength of flawed structures, the evaluation of the stress intensity factor is essential. This paper de- scribes the finite element procedure to determine the stress intensity factor using J integral approach. A comparative study is made on the stress intensity factor of cracked configurations utilizing a plane82 element of ANSYS. The computed values of strain energy release rate (GI ), J-integral (JI ) and stress intensity factor (KI ) for tensile cracked configurations are found to be in good agreement with those of handbook solutions. A plane 82 element is proved to be well suited to model curved boundaries. Finite element formulation and fracture analysis procedures are explained briefly. 1. Introduction Fracture mechanics has developed into a useful discipline for predicting strength and −−−−−−−−−−−−−−−−−−−−−−−−−−−− c http: //www.ascent-journals.com 211 212 S. SUNDARESAN, SIVA VIJAY, A.P. BEENA, C.K. KRISHNADASAN & B. NAGESWARA RAO life of cracked structures. The important aspect of linear elastic fracture mechanics is the \Damage Tolerance"' (DT) assessment.