Reviewing Iso 14649 Through Iso10303
Total Page:16
File Type:pdf, Size:1020Kb
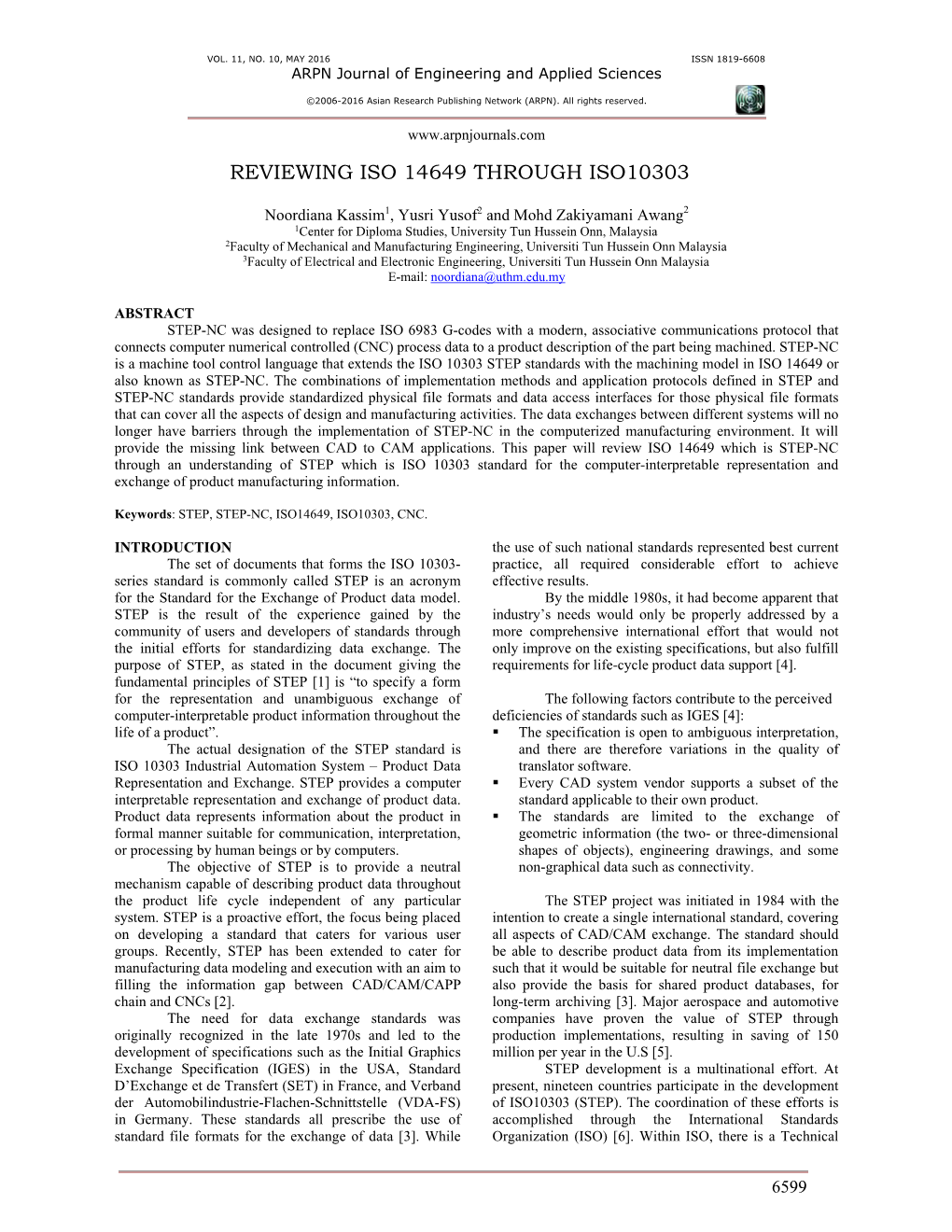
Load more
Recommended publications
-
Recommended Practices for AP242 BO Model XML Assembly Structure
Recommended Practices for STEP AP242 TC Business Object Model XML Product & Assembly Structure Release 2.0 October 30, 2018 Contacts: Organizational Jochen Boy Phil Rosché Frédéric Darré PROSTEP AG ACCR, LLC. Cimpa Dolivostraße 11 125 King Charles Circle 4 Avenue Didier Daurat 64293 Darmstadt Summerville 31700 Blagnac Germany SC 29485 / USA France [email protected] [email protected] [email protected] Technical Guillaume Hirel Jochen Haenisch T-Systems Jotne EPM [email protected] [email protected] © PDM / CAx / JT Implementor Forum PDM-IF/CAx-IF/JT-IF Recommended Practices AP242 BO Model XML Product & Assembly Structure Version 2.0; October 30, 2018 Table of Contents 1 Introduction ........................................................................................................ 11 1.1 Document Overview ................................................................................................ 11 1.1.1 Goal and Objectives ........................................................................................................ 11 1.1.2 Scope ............................................................................................................................... 11 1.1.3 Intended Audience ........................................................................................................... 12 1.1.4 Intended Use.................................................................................................................... 12 1.1.5 Document Style............................................................................................................... -
TP-1996-789.Pdf (141.1Kb)
Nationaal Lucht- en Ruimtevaartlaboratorium National Aerospace Laboratory NLR NLR TP 96789 Overview and discussion of electronic exchange standards for technical information H. Kuiper and J.C. Donker DOCUMENT CONTROL SHEET ORIGINATOR'S REF. SECURITY CLASS. NLR TP 96789 U Unclassified ORIGINATOR National Aerospace Laboratory NLR, Amsterdam, The Netherlands TITLE Overview and discussion of electronic exchange standards for technical information PRESENTED AT the CALS Europe'96 conference, Paris, May 29-31, under the title "SGML, HTML, the paperless office... what about the forests and the trees", upon invitation of the NL MOD Representative in the conference committee. AUTHORS DATE pp ref H. Kuiper and J.C. Donker 960725 36 8 DESCRIPTORS Computer graphics Multimedia Document storage Software tools Document markup languages Standards Format Texts Hypertext Word processing Information dissemination ABSTRACT Nowadays more and more information is being exchanged electronically. Reasons for this include a higher degree of cooperation between information suppliers and users, an increasing demand for speed (of production and modification, and reduction of time to market), and cost reduction. On the technology side, the advent of the electronic highway enables effective and efficient electronic information exchange. For reasons of timeliness and life cycle costs, standards and specifications are becoming more important. The aim of this paper is to provide an overview of standards and specifications for electronic exchange of (technical document) information and to discuss the most common ones currently available for text, images, and document exchange. Emerging standards and specifications, such as for audio, video and virtual environments are also briefly discussed. Finally, a brief description is given of a standard for enterprise integration and product data exchange. -
ISO/IEC JTC 1 N13604 ISO/IEC JTC 1 Information Technology
ISO/IEC JTC 1 N13604 2017-09-17 Replaces: ISO/IEC JTC 1 Information Technology Document Type: other (defined) Document Title: Study Group Report on 3D Printing and Scanning Document Source: SG Convenor Project Number: Document Status: This document is circulated for review and consideration at the October 2017 JTC 1 meeting in Russia. Action ID: ACT Due Date: 2017-10-02 Pages: Secretariat, ISO/IEC JTC 1, American National Standards Institute, 25 West 43rd Street, New York, NY 10036; Telephone: 1 212 642 4932; Facsimile: 1 212 840 2298; Email: [email protected] Study Group Report on 3D Printing and Scanning September 11, 2017 ISO/IEC JTC 1 Plenary (October 2017, Vladivostok, Russia) Prepared by the ISO/IEC JTC 1 Study Group on 3D Printing and Scanning Executive Summary The purpose of this report is to assess the possible contributions of JTC 1 to the global market enabled by 3D Printing and Scanning. 3D printing, also known as additive manufacturing, is considered by many sources as a truly disruptive technology. 3D printers range presently from small table units to room size and can handle simple plastics, metals, biomaterials, concrete or a mix of materials. They can be used in making simple toys, airplane engine components, custom pills, large buildings components or human organs. Depending on process, materials and precision, 3D printer costs range from hundreds to millions of dollars. 3D printing makes possible the manufacturing of devices and components that cannot be constructed cost-effectively with other manufacturing techniques (injection molding, computerized milling, etc.). It also makes possible the fabrications of customized devices, or individual (instead of identical mass-manufactured) units. -
Iso 10303-511:2001(E)
This preview is downloaded from www.sis.se. Buy the entire standard via https://www.sis.se/std-617578 INTERNATIONAL ISO STANDARD 10303-511 First edition 2001-04-15 Industrial automation systems and integration — Product data representation and exchange — Part 511: Application interpreted construct: Topologically bounded surface Systèmes d'automatisation industrielle et intégration — Représentation et échange de données de produits — Partie 511: Construction interprétée: Surface délimitée topologiquement Reference number ISO 10303-511:2001(E) © ISO 2001 This preview is downloaded from www.sis.se. Buy the entire standard via https://www.sis.se/std-617578 ISO 10303-511:2001(E) PDF disclaimer This PDF file may contain embedded typefaces. In accordance with Adobe's licensing policy, this file may be printed or viewed but shall not be edited unless the typefaces which are embedded are licensed to and installed on the computer performing the editing. In downloading this file, parties accept therein the responsibility of not infringing Adobe's licensing policy. The ISO Central Secretariat accepts no liability in this area. Adobe is a trademark of Adobe Systems Incorporated. Details of the software products used to create this PDF file can be found in the General Info relative to the file; the PDF-creation parameters were optimized for printing. Every care has been taken to ensure that the file is suitable for use by ISO member bodies. In the unlikely event that a problem relating to it is found, please inform the Central Secretariat at the address given below. © ISO 2001 All rights reserved. Unless otherwise specified, no part of this publication may be reproduced or utilized in any form or by any means, electronic or mechanical, including photocopying and microfilm, without permission in writing from either ISO at the address below or ISO's member body in the country of the requester. -
Forcepoint DLP Supported File Formats and Size Limits
Forcepoint DLP Supported File Formats and Size Limits Supported File Formats and Size Limits | Forcepoint DLP | v8.8.1 This article provides a list of the file formats that can be analyzed by Forcepoint DLP, file formats from which content and meta data can be extracted, and the file size limits for network, endpoint, and discovery functions. See: ● Supported File Formats ● File Size Limits © 2021 Forcepoint LLC Supported File Formats Supported File Formats and Size Limits | Forcepoint DLP | v8.8.1 The following tables lists the file formats supported by Forcepoint DLP. File formats are in alphabetical order by format group. ● Archive For mats, page 3 ● Backup Formats, page 7 ● Business Intelligence (BI) and Analysis Formats, page 8 ● Computer-Aided Design Formats, page 9 ● Cryptography Formats, page 12 ● Database Formats, page 14 ● Desktop publishing formats, page 16 ● eBook/Audio book formats, page 17 ● Executable formats, page 18 ● Font formats, page 20 ● Graphics formats - general, page 21 ● Graphics formats - vector graphics, page 26 ● Library formats, page 29 ● Log formats, page 30 ● Mail formats, page 31 ● Multimedia formats, page 32 ● Object formats, page 37 ● Presentation formats, page 38 ● Project management formats, page 40 ● Spreadsheet formats, page 41 ● Text and markup formats, page 43 ● Word processing formats, page 45 ● Miscellaneous formats, page 53 Supported file formats are added and updated frequently. Key to support tables Symbol Description Y The format is supported N The format is not supported P Partial metadata -
IDOL Keyview Viewing SDK 12.7 Programming Guide
KeyView Software Version 12.7 Viewing SDK Programming Guide Document Release Date: October 2020 Software Release Date: October 2020 Viewing SDK Programming Guide Legal notices Copyright notice © Copyright 2016-2020 Micro Focus or one of its affiliates. The only warranties for products and services of Micro Focus and its affiliates and licensors (“Micro Focus”) are set forth in the express warranty statements accompanying such products and services. Nothing herein should be construed as constituting an additional warranty. Micro Focus shall not be liable for technical or editorial errors or omissions contained herein. The information contained herein is subject to change without notice. Documentation updates The title page of this document contains the following identifying information: l Software Version number, which indicates the software version. l Document Release Date, which changes each time the document is updated. l Software Release Date, which indicates the release date of this version of the software. To check for updated documentation, visit https://www.microfocus.com/support-and-services/documentation/. Support Visit the MySupport portal to access contact information and details about the products, services, and support that Micro Focus offers. This portal also provides customer self-solve capabilities. It gives you a fast and efficient way to access interactive technical support tools needed to manage your business. As a valued support customer, you can benefit by using the MySupport portal to: l Search for knowledge documents of interest l Access product documentation l View software vulnerability alerts l Enter into discussions with other software customers l Download software patches l Manage software licenses, downloads, and support contracts l Submit and track service requests l Contact customer support l View information about all services that Support offers Many areas of the portal require you to sign in. -
IGOSS-Industry/Government Open Systems Specification
NIST Special Publication 500-217 Computer Systems IGOSS-Industry/Government Technology Open Systems Specification U.S. DEPARTMENT OF COMMERCE Technology Administration National Institute of Gerard Mulvenna, Editor Standards and Technology NIST RESEARCH INFORMATION NAT-L INST. OF STAND & TECH R.I.C. MAR 2 6 1996 "'^ NIST PUBLICATIONS CENTER QC 100 .U57 iO. 500-217 994 7he National Institute of Standards and Technology was established in 1988 by Congress to "assist industry in the development of technology . needed to improve product quality, to modernize manufacturing processes, to ensure product reliability . and to facilitate rapid commercialization ... of products based on new scientific discoveries." NIST, originally founded as the National Bureau of Standards in 1901, works to strengthen U.S. industry's competitiveness; advance science and engineering; and improve public health, safety, and the environment. One of the agency's basic functions is to develop, maintain, and retain custody of the national standards of measurement, and provide the means and methods for comparing standards used in science, engineering, manufacturing, commerce, industry, and education with the standards adopted or recognized by the Federal Government. As an agency of the U.S. Commerce Department's Technology Administration, NIST conducts basic and applied research in the physical sciences and engineering and performs related services. The Institute does generic and precompetitive work on new and advanced technologies. NIST's research facilities are located -
ISO 10303-Part303.Pdf
Note to reviewers: 1. This document closely reflects the changes recommended by Q&E at the ISO meeting in Kobe, Japan, June 1996 and editorial changes recommended by ISO staff review at the ISO meeting in Toronto, Canada, Oct 1996. 2. This document reflects the latest version of the ATS Guidelines methods document (N434 plus ballot comment resolutions). 3. This document will be submitted for TR ballot in the near future. ISO/TR 10303-303(E) Contents Page 1 Scope ........................................................................... 1 2 Normative references ............................................................... 1 3 Definitions ....................................................................... 2 3.1 Terms defined in ISO 10303-1 ................................................ 2 3.2 Terms defined in ISO 10303-22 ............................................... 3 3.4 Terms defined in ISO 10303-203 .............................................. 3 3.5 Other definitions ........................................................... 3 3.6 Abbreviations ............................................................. 4 4 Test purposes ..................................................................... 4 4.1 Application element test purposes ............................................. 5 4.2 AIM test purposes ........................................................ 15 4.3 Implementation method test purposes ......................................... 52 4.4 Domain test purposes ..................................................... -
ASTM Standards
PUBLISHED BIWEEKLY BY THE AMERICAN NATIONAL STANDARDS INSTITUTE 25 West 43rd Street, NY, NY 10036 VOL. 32, #23 November 16, 2001 Contents American National Standards Call for Comment on Standards Proposals ............................................................. 2 Call for Comment Contact Information .................................................................... 12 Final Actions............................................................................................................... 14 Project Initiation Notification System (PINS)........................................................... 18 ISO and IEC Standards ISO Draft Standards ................................................................................................... 20 ISO and IEC Newly Published Standards................................................................. 22 CEN/CENELEC Standards Activity ............................................................................ 25 Registration of Organization Names in the U.S. ....................................................... 27 Proposed Foreign Government Regulations............................................................. 27 International Organization of Legal Metrology.......................................................... 28 Information Concerning .............................................................................................. 31 Standards Action is now available via the World Wide Web For your convenience Standards Action can now be downloaded from the following web address: -
Introduction to ISO 10303 - the STEP Standard for Product Data Exchange
TECHNICAL NOTE Introduction to ISO 10303 - the STEP Standard for Product Data Exchange Michael J. Pratt* National Institute of Standards and Technology Manufacturing Systems Integration Division Gaithersburg, MD 20899-8261, USA. [email protected] Background Since 1984 the International Organization for Standardization (ISO) has been working on the development of a comprehensive standard for the electronic exchange of product data between computer-based product life-cycle systems. Initial concentration has been on design and manufacturing applications. This standard, ISO 10303 [1,2,3], is informally known as STEP (STandard for the Exchange of Product model data). Its scope is much broader than that of other existing CAD data exchange formats, notably the Initial Graphics Exchange Specification (IGES), a US standard that has been in use for nearly twenty years. Whereas IGES was developed primarily for the exchange of pure geometric data between computer aided design (CAD) systems, STEP is intended to handle a much wider range of product-related data covering the entire life-cycle of a product. The development of STEP has been one of the largest efforts ever undertaken by ISO. Several hundred people from many different countries have been involved in the work for the past sixteen years, and development is as active now as it ever has been in the past. STEP is increasingly recognized by industry as an effective means of exchanging product-related data between different CAD systems or between CAD and downstream application systems [4]. The first parts of the standard were published in 1994 [1,2] after some ten years of work by members of the relevant standards subcommittee, ISO TC184/SC4, whose responsibility is `Industrial Data'. -
WG-16 Presentation VM.Pdf
Web3D Design Printing and Scanning WG formerly CAD Working Group Activities in support of 3D Visualization for CAX activities For presentation to SC 4 WG 16 Nov 2018 3D Visualization always involves a dynamic interactive scenegraph with elements of • 3D Geometry • Material Appearance (colors, visual properties) • Navigation and Perspective • Interactivity Our 3D visualizations: • Always refer to external objects, visual appearance is not their primary or sole purpose • Exist in the world of copyright, licenses, proprietary and intellectual rights, security and authorization needs, version control, traceability,…. Metadata and Annotation There is a need to clarify terminology and usage. DPS WG recognizes 3 distinct but related concepts. 2 are called metadata! 1. Metadata about the “document” , author, owner, version 2. Metadata about the elements of the scenegraph … and 1 is called, at least by a CoChair 3. Annotation : A visual feature presenting extended information about some element of the scenegraph. Examples are labels, dimensions, callouts. Related to term “helpers” from definitions prepared by STEP Geometry Services Existing STEP or ISO definition Add presentation Wikipedia source Definitions Defined by 23301 constructive solid geometry (CSG) 10303, they are defined here to make an important distinction between two helpers type of geometric modelling in which a solid is defined as the result of a fundamentally different modelling approaches. The present resource is Supplemental geometry used to construct or document the geometric -
Development Architecture for Industrial Data Management
Development architecture for industrial data management Yujiang Li Licentiate Thesis Royal Institute of Technology School of Industrial Engineering and Management Department of Production Engineering Stockholm, Sweden 2013 Abstract Standardized information modeling is important for interoperability of CAx systems. Existing information standards such as ISO 10303 STEP have been proposed and developed for decades for this purpose. Comprehensive data structure and various implementation methodologies make such standards strong in support of different industry domains, information types, and technical requirements. However, this fact also leads to increased implementation complexity and workloads for CAx system developers. This licentiate proposes the development architecture, STEP Toolbox, to help users implement standards with a simplified development process and minimal knowledge requirements on standards. Implementation difficulties for individuals are identified with analysis on implementation of the information standards in three aspects: tasks, users, and technology. Then the toolbox is introduced with an illustration of design of behavior and structure. Case studies are performed to validate the toolbox with prototypes. Internal and external observation has shown the around two-month learning process skipped and a great amount of workload reduction in implementation with the utilization of this architecture. Keywords: Information modeling, ISO 10303 STEP, CAx, API I Contents Abstract ........................................................................................................................