Simulation of Motion Interactions of a 2-DOF Linear Piezoelectric Impact Drive Mechanism with a Single Friction Interface
Total Page:16
File Type:pdf, Size:1020Kb
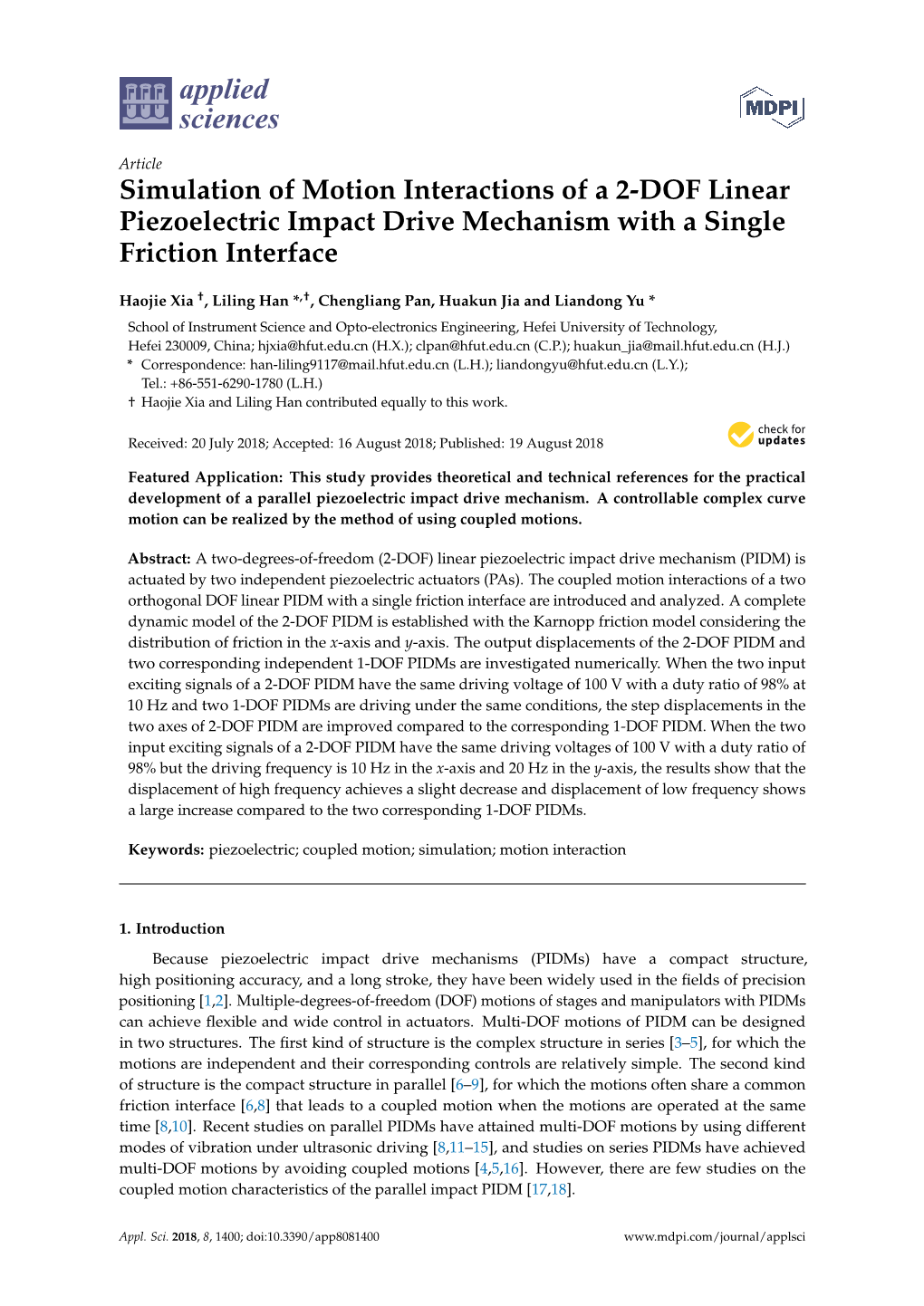
Load more
Recommended publications
-
Student Chapter Annual Report Cover Page
SOCIETY OF ECONOMIC GEOLOGISTS, INC. 7811 Shaffer Parkway • Littleton, CO 80127-3732 USA • Tel: +1.720.981.7882 • Fax: +1.720.981.7874 • E-mail: [email protected] Student Chapter Annual Report Cover Page Submission Deadline: September 30th Submit to: [email protected] Month/Year Reported:From ___________________________(mm/yyyy)09/2019 – To _______________________________09/2020 (mm/yyyy) Check if update STUDENT CHAPTER: needed at segweb.org Name: _________________________________________________________________________________Heifei University of Technology Student Chapter □ University Affiliation: _____________________________________________________________________Heifei University of Technology □ Mailing Address: ________________________________________________________________________No.193, Tunxi road, Baohe district, Hefei, Anhui province □ Dedicated E-mail: _______________________________________________________________________295659970@qq.com □ Website: ________________________________________________________________________________ □ Logo: __________________________________________________________________________________ □ Facebook: ______________________________________________________________________________ □ Twitter: ________________________________________________________________________________ □ Instagram: ______________________________________________________________________________ □ LinkedIn: _______________________________________________________________________________ □ YouTube: _______________________________________________________________________________ -
2 2 Hefei Analysis
NATURE INDEX CHINA Hefei Hefei has kept a low profile for many years. However, as the ARTICLE COUNT (AC): 530 University of Science and Technology of China continues to FRACTIONAL COUNT (FC): 226 break new ground in the physical sciences, the city is moving WEIGHTED FRACTIONAL COUNT into the global spotlight. (WFC): 212 efei, the capital city of the eastern researcher in this field, with 17 articles (WFC articles (WFC = 5.73) — including one in Nature Anhui province, is the smallest of the =13.2) in the index, mostly on graphene-like — about molecular and surface imaging. cities profiled in this supplement. But materials.“Graphene comprises carbon atoms USTC also hosts the CAS Key Laboratory Hit is growing rapidly in population, disposable only, so its structure and chemical properties for Research in Galaxies and Cosmology in its income levels and gross domestic product are rather simple,” she says. “We are develop- department of physics. Tinggui Wang is the (GDP) — and when it comes to the pursuit ing graphene-like inorganic materials with biggest contributor in astrophysics, with seven of basic science, it holds its own among much unusual properties that may find applications articles on quasars and active galactic nuclei. larger cities. in photocatalysis and biomedicine.” Another However, owing to the down-weighting of astro- Hefei is home to the University of Science successful chemistry researcher from the same physics journals in the index, these papers only and Technology of China (USTC), one of division, Shuhong Yu co-authored 12 articles add a WFC of 1 to the institution (see ‘A guide to three universities affiliated with the Chinese (WFC = 11.4) in 2013 on aerogels. -
February 2014
winter issue february 2014 News from the Ohio Articulation & Transfer Network IN THIS ISSUE Special Features Special Features. 1-4 Board of Regents welcomes delegates from Anhui, China Policy & Compliance In October, Chancellor John Carey hosted several university delegates from Anhui, Reports. 4 China for a visit to the Ohio Board of Regents (OBR) offices. Anhui, China has been a sister city to Columbus since 1988 when a group from Columbus traveled Meetings of the Minds. 5 to China to negotiate obtaining a panda bear for the Columbus Zoo. Transfer Technology. 6-7 Delegates were present from Anhui University, Bengbu Medical College, (CT)2 Corner. 7-8 Chuzhou University, Fuyang University, Hefei University, Huaibei Normal College, Staff Happenings. 9 Huangshan College, and Wannan College. Delegates were provided a brief overview of Ohio’s public higher education system by Ohio Board of Regents (OBR) staff members Paula Compton, Charles See, A Note from Paula Jeff Robinson, David Cannon, and Shane DeGarmo. Chancellor Carey responded Even though it has been a long, to questions from the delgates on cold winter, the OATN staff are topics such as supporting STEM faculty keeping warm with the constant and initiatives in Ohio public institutions of higher transfer activities happening education, the Choose Ohio First scholarship, and funding Ohio public higher around the state. We continue education. to be so grateful for our many colleagues around the state The event was arranged by Paula Compton and Lin Ba, with help from the OATN (and beyond with some of staff. Lin Ba is a professor of economics at The Ohio State University’s Newark our long-reaching initiatives) campus. -
Nutraceuticals and Nutrition Supplements July 18-19, 2016 Bangkok, Thailand
Zhao-Jun Wei, J Nutr Food Sci 2016, 6:4 (Suppl) conferenceseries.com http://dx.doi.org/10.4172/2155-9600.C1.023 2nd International Conference on Nutraceuticals and Nutrition Supplements July 18-19, 2016 Bangkok, Thailand The nutraceutical properties of polysaccharides sequential extracted from peony seed dreg Zhao-Jun Wei Hefei University of Technology, China eony seed dreg, a byproduct of oil processing, is rich in many nutrients. However, this is always used as animal fodder and fertilizer. PMy laboratory has explored the possible use of nutrient-rich peony seed dreg as a functional food. To this end, Peony seed dreg polysaccharides (PSDP) were sequentially extracted using hot buffer (HBSS), chelating agent (CHSS) and dilute alkaline (DASS) followed by concentrated alkaline (CASS). The nutraceutical properties of the various polysaccharides fractions were investigated. The four PSDPs possessed simple composition and showed the characteristic absorptions for polysaccharides at 3600-3200 cm-1 and 3000-2800 cm-1. The functional group of four PSDPs displayed some slight differences. The results of melting point and enthalpy of four samples confirmed a good thermal stability. The emulsifying activity and emulsifying stability of four PSDPs exhibited dose- dependent response, HBSS with the highest emulsifying activity and CHSS with the longest emulsifying stability. Comparison among the antioxidant activities of four PSDPs, CASS showed highest abilities in the DPPH radical scavenging activity, reducing power and ABTS radical scavenging activity, HBSS exhibited the highest hydroxyl radical scavenging activity and CHSS displayed the higher chelating ability on ferrous ions than others. At a liquid-solid ratio less than 2.5% w/w in aqueous solution, the polysaccharides extracted from peony seed presented non-Newtonian shear thinning behavior and could be well described by the Cross model. -
A Complete Collection of Chinese Institutes and Universities For
Study in China——All China Universities All China Universities 2019.12 Please download WeChat app and follow our official account (scan QR code below or add WeChat ID: A15810086985), to start your application journey. Study in China——All China Universities Anhui 安徽 【www.studyinanhui.com】 1. Anhui University 安徽大学 http://ahu.admissions.cn 2. University of Science and Technology of China 中国科学技术大学 http://ustc.admissions.cn 3. Hefei University of Technology 合肥工业大学 http://hfut.admissions.cn 4. Anhui University of Technology 安徽工业大学 http://ahut.admissions.cn 5. Anhui University of Science and Technology 安徽理工大学 http://aust.admissions.cn 6. Anhui Engineering University 安徽工程大学 http://ahpu.admissions.cn 7. Anhui Agricultural University 安徽农业大学 http://ahau.admissions.cn 8. Anhui Medical University 安徽医科大学 http://ahmu.admissions.cn 9. Bengbu Medical College 蚌埠医学院 http://bbmc.admissions.cn 10. Wannan Medical College 皖南医学院 http://wnmc.admissions.cn 11. Anhui University of Chinese Medicine 安徽中医药大学 http://ahtcm.admissions.cn 12. Anhui Normal University 安徽师范大学 http://ahnu.admissions.cn 13. Fuyang Normal University 阜阳师范大学 http://fynu.admissions.cn 14. Anqing Teachers College 安庆师范大学 http://aqtc.admissions.cn 15. Huaibei Normal University 淮北师范大学 http://chnu.admissions.cn Please download WeChat app and follow our official account (scan QR code below or add WeChat ID: A15810086985), to start your application journey. Study in China——All China Universities 16. Huangshan University 黄山学院 http://hsu.admissions.cn 17. Western Anhui University 皖西学院 http://wxc.admissions.cn 18. Chuzhou University 滁州学院 http://chzu.admissions.cn 19. Anhui University of Finance & Economics 安徽财经大学 http://aufe.admissions.cn 20. Suzhou University 宿州学院 http://ahszu.admissions.cn 21. -
University of Leeds Chinese Accepted Institution List 2021
University of Leeds Chinese accepted Institution List 2021 This list applies to courses in: All Engineering and Computing courses School of Mathematics School of Education School of Politics and International Studies School of Sociology and Social Policy GPA Requirements 2:1 = 75-85% 2:2 = 70-80% Please visit https://courses.leeds.ac.uk to find out which courses require a 2:1 and a 2:2. Please note: This document is to be used as a guide only. Final decisions will be made by the University of Leeds admissions teams. -
Preparation of Monoethyl Fumarate-Based Molecularly Imprinted Polymers and Their Application As SPE Sorbent for Enrichment of Scopolamine from Tropane Alkaloids
Electronic Supplementary Material (ESI) for RSC Advances. This journal is © The Royal Society of Chemistry 2019 Preparation of monoethyl fumarate-based molecularly imprinted polymers and their application as SPE sorbent for enrichment of scopolamine from tropane alkaloids Jie Zuo a, Xingyuan Zhang a*, Xinyu Li a, Zhiwei Li a, Zongren Li a, Honghong Li b, Wencheng Zhang b*. a CAS Key Laboratory of Soft Matter Chemistry, Department of Polymer Science and Engineering, University of Science and Technology of China, Hefei 230026, PR China. E-mail: [email protected]. b Engineering Research Center of Bio-Process of Ministry of Education, School of Food and Biological Engineering, Hefei University of Technology, Hefei, P. R. China. E-mail: [email protected]. 1. 1H NMR spectra The structure of synthetic functional monomer was identified using 1H NMR 1 spectra. As seen from Fig. S1, H NMR (400 MHz, DMSO-d6) δ: 1.21 (t, J=8 Hz, 3H), 4.14 (dd, J1=4 Hz, J2=8 Hz, 2H), 6.36 (q, J=12Hz, 2H), 12.97 (s, 1H), which proved mmaa-a-26 38000 HDO DMSO DMSO DMSO DMSO DMSO 36000 12.97 6.39 6.36 6.36 6.33 4.16 4.14 4.13 4.11 3.36 2.51 2.51 2.50 2.50 2.50 1.23 1.21 1.19 -0.00 34000 e 32000 30000 a O 6 28000 HO 4 b&c 26000 7 c 1 2 24000 b 22000 3 O 8 d 20000 O 9 d 18000 5 16000 H3C 10 DMSO 14000 e 12000 H2 O 10000 8000 6000 4000 a 2000 0 -2000 0.95 2.00 2.06 3.06 13.0 12.0 11.0 10.0 9.0 8.0 7.0 6.0 5.0 4.0 3.0 2.0 1.0 0.0 f1 (ppm) that MFMA had been successfully synthesized. -
Full Name Affiliation Research ID98001 Weikang Qian(Professor)
Number(ID) Full Name Affiliation Research Weikang Shanghai University Of Electrical engineering&Intelligent ID98001 Qian(Professor) Technology control Ling ID98002 Guangxi University Computer science Song(Professor) Danyang International ID98003 Zhao(Associate economy&Multinational culture professor) Chunxue Shanghai University Of ID98004 Computer science Wu(Professor) Technology Naval Aviation ID98005 Yunan Hu Network control Engineering Institute Computer Department of ID98006 Xingfu Wang University of Science & Embedded system Technology China Computer and Xiao Information College of ID98007 Sun(Associate Artificial intelligence HeFei University of professor) Technology Bingru Beijing University Of ID98008 Yang(Academici Intelligent system Science and Technology an) Software College of ID98009 Kunhong Liu Database technology Xiamen University Mingfen Fuzzy set theory&Rough set ID98010 WuYi University Wu(Professor) theory College of computer Nanfeng science and engineering ID98011 Intelligent robot Xiao(Professor) of South China University of Technology Bo Computer Department of ID98012 Information security Zhao(Professor) Wuhan University Zhang HeFei University of ID98013 Zhang(Associate IC design Technology researcher) Computer Department of ID98014 Yu Dong South China Normal Computer control technology University College of mathematics Xiaofu and computer science of ID98015 Li(Associate Software engineering SUN YAT-SEN professor) University Liang Civil Aviation University Image processing and pattern ID98016 Zhang(Professor of China -
Page 1 of 38 YUCHENG LIU Associate Professor and Graduate
Yucheng Liu Curriculum Vita YUCHENG LIU Associate Professor and Graduate Coordinator, Ph.D., P.E. Jack Hatcher Chair in Engineering Entrepreneurship ASME Fellow Department of Mechanical Engineering Mail Stop 9552, 222 Carpenter Hall James Worth Bagley College of Engineering Mississippi State University Mississippi State, MS 39762 (662) 325-1536 (O) (662) 325-7223 (F) Email: [email protected] Nationality: People’s Republic of China Immigration Status: Permanent Resident in USA, Alien of Extraordinary Ability BIOGRAPHICAL DATA EDUCATION 2002-2005 Doctor of Philosophy degree in Mechanical Engineering granted August 2005 University of Louisville, Louisville, Kentucky Research area: advanced product design and development/finite element methods 2000-2002 Master of Science degree in Mechanical Engineering granted August 2003 University of Louisville, Louisville, Kentucky Research area: computer aided design/finite element methods 1993-1997 Bachelor of Science degree in Mechanical Engineering granted July 1997 Hefei University of Technology, Hefei, Anhui, China Major: mechanical and computational design EMPLOYMENT 2018-Present Jack Hatcher Chair in Engineering Entrepreneurship, The James Worth Bagley College of Engineering, Mississippi State University, Mississippi State, Mississippi 2016-Present Graduate Coordinator, Department of Mechanical Engineering, The James Worth Bagley College of Engineering, Mississippi State University, Mississippi State, Mississippi 2014-Present Associate Professor, Department of Mechanical Engineering, The James -
Invitation and Call for Papers To
Invitation and Call for Papers to The 13th International Conference on Multi-functional Materials and Applications (ICMMA 2019) November 21-24, 2019 Bengbu University, Bengbu, China Dear Colleagues, We are going to organize “The 13th International Conference on Multi-functional Materials and Application” on 21-24 November 2019 in Bengbu University,Bengbu, China. The detail information of the conference is shown in our official webpage: http://www.ijpcs.org. In view of your reputation in the field of Chemistry, Physics, Materials Science and Engineering, Construction and Environmental Materials, I would like to invite you to participate in the conference, present and share your valuable research achievements to our participants. Conference Chairman: Prof. Ming Ding (President, Bengbu University, China) Conference Vice Chairman: 1 Prof. Jin Liu (Anhui Jianzhu University, China) Prof. Won-Chun Oh (Hanseo University, Korea) Advisory Chairman: Prof. Mingxu Zhang (Anhui University of Science & Technology, China) Prof. Zhigang Chen (Suzhou University of Science and Technology, China) Prof. Saksit Chanthai (Khon Kaen University, Thailand) Conference Local Chairman: Prof. Won-Chun Oh (Hanseo University, Korea) Prof. Jin Liu (Anhui Jianzhu University, China) Prof. Ding Ming (Bengbu University, China) Prof. Chuyang Xu (Anhui University of Science & Technology, China) Prof. Shin Mukai (Hokkaido University, Japan) Dr. Chong-Hun Jung (Korea Atomic Energy Research Institute, Korea) Prof. Cheol Gyu Kim (Hanbat National University, Korea) Prof. Heon-Chang Kim (Hoseo University, Korea) Prof. Masahiro Toyoda (Oita University, Japan) Prof. Chan-Kyung Kim, (Inha University, Korea) Prof. Daosung Sun (Hefei Normal University, China) Prof. Zhaoqi Sun (Anhui University, China) Prof. Chen-Hao Wang (National Taiwan University of Science and Technology, Taiwan) Prof. -
Huizhou's Roots in Trade Still Echo Today
Xxxxx April 1X,11, 2017 | PAGE S1-4 CHINA DAILY chinadaily.COM.CN Hefei science center to pursue technological specialization Anhui in the eyes of foreigners China Daily reporter Zhuan Ti interviewed international scholars and students at By LI YOU universities in Anhui. They expressed their feelings toward the province. [email protected] Hefei, the capital city of Anhui province, Why Anhui? I tell I am currently launched a major project on Feb 27 to con- my friends “if studying in the struct a comprehensive national science cen- Urumqi Beijing you want to see Hefei University ter by the year 2020. the real China, of Technology It will be the second comprehensive nation- come to visit and this is my al science center in China, following Shang- me in Hefei”! seventh year hai’s Zhangjiang Comprehensive National Delingha Ji'nan While Shanghai in China. In the Science Center, and also the first national is glamorous past couple of Xiuning, once one of the major bases for merchants of Huizhou, is now seeing a revival of commercial innovation platform in the central and west- and Beijing is years, I have prosperity with better transport links. ern regions of China. Ngari stately, Anhui witnessed the The signature Welcoming-Guests Pine in the Huangshan Mountains. PHOTOS PROVIDED TO CHINA DaILY The science center will focus on research Lijiang Hefei is authentic — real people living real, quick growth and development of Hefei. AN OPEN CHINA: SPLENDID ANHUI of information technology, energy, health and Shanghai hard-working lives in an environment of I feel very comfortable and at home the environment, and will seek breakthroughs enthusiasm for change and innovation. -
1 Please Read These Instructions Carefully
PLEASE READ THESE INSTRUCTIONS CAREFULLY. MISTAKES IN YOUR CSC APPLICATION COULD LEAD TO YOUR APPLICATION BEING REJECTED. Visit http://studyinchina.csc.edu.cn/#/login to CREATE AN ACCOUNT. • The online application works best with Firefox or Internet Explorer (11.0). Menu selection functions may not work with other browsers. • The online application is only available in Chinese and English. 1 • Please read this page carefully before clicking on the “Application online” tab to start your application. 2 • The Program Category is Type B. • The Agency No. matches the university you will be attending. See Appendix A for a list of the Chinese university agency numbers. • Use the + by each section to expand on that section of the form. 3 • Fill out your personal information accurately. o Make sure to have a valid passport at the time of your application. o Use the name and date of birth that are on your passport. Use the name on your passport for all correspondences with the CLIC office or Chinese institutions. o List Canadian as your Nationality, even if you have dual citizenship. Only Canadian citizens are eligible for CLIC support. o Enter the mailing address for where you want your admission documents to be sent under Permanent Address. Leave Current Address blank. Contact your home or host university coordinator to find out when you will receive your admission documents. Contact information for you home university CLIC liaison can be found here: http://clicstudyinchina.com/contact-us/ 4 • Fill out your Education and Employment History accurately. o For Highest Education enter your current degree studies.