Backflow Prevention Management Plan
Total Page:16
File Type:pdf, Size:1020Kb
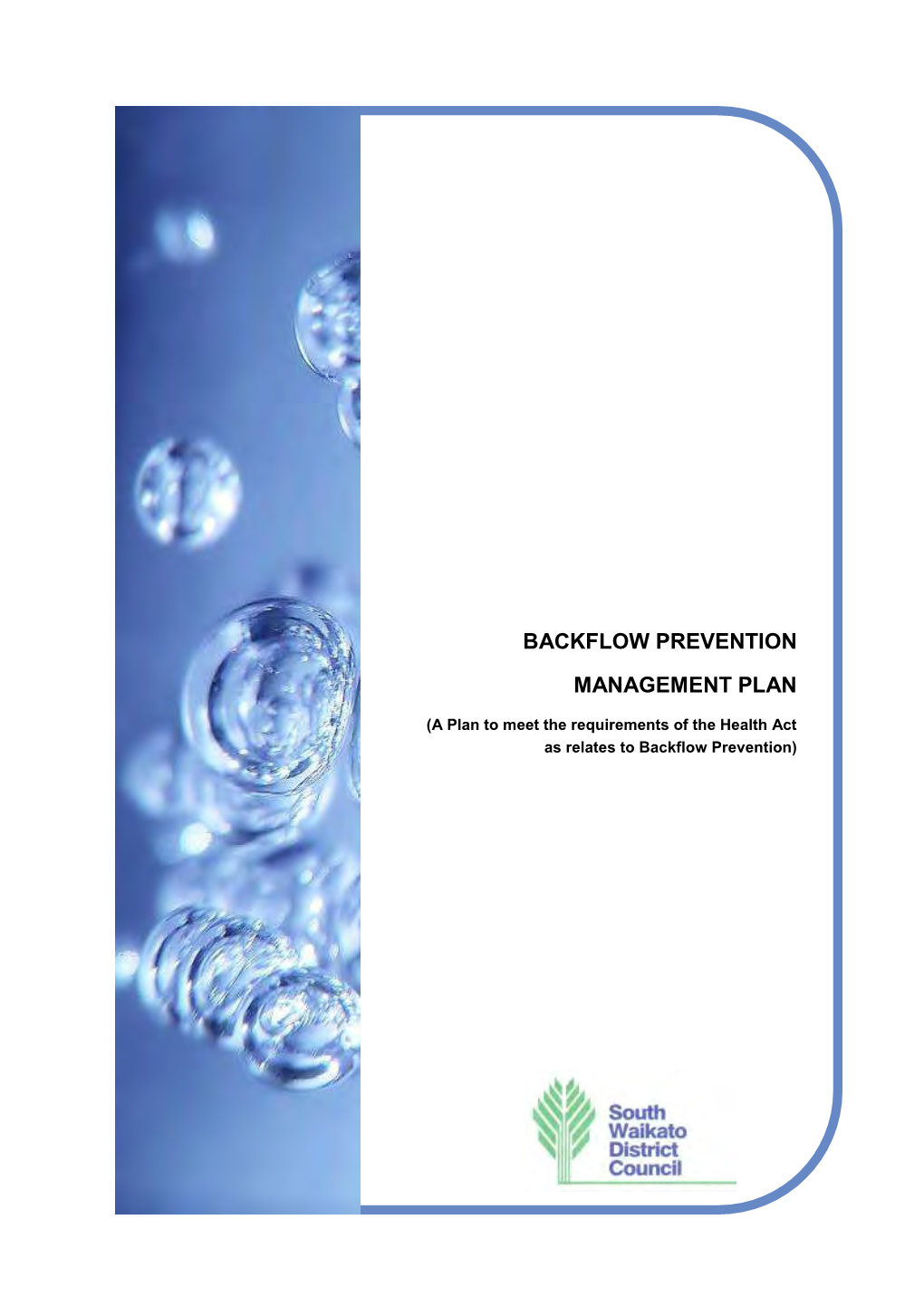
Load more
Recommended publications
-
2019 Drinking Water Quality Report
City of Leominster, Department of Public Works, Water Division Public Water Supply ID # 2153000 2019 DRINKING WATER QUALITY REPORT The City of Leominster is dedicated to preserving and improving the quality and reliability of its drinking water supplies. In addition to continued source protection efforts and significant upgrades to all the treatment facilities, the City has an aggressive flushing and water main replacement program. Further information about this report or any aspect of the public water supply can be obtained by contacting Mark Piermarini at 978-534-7590, ext. 3639, cell phone 978-660-0061, or e-mail: [email protected] YOUR DRINKING WATER SOURCES The City of Leominster lies entirely within the Nashua River basin. It encompasses about 30 square miles of land. Much of the western half of the city includes state forest, watershed lands, and other protected open space. The City obtains its drinking water from the Distributing Reservoir system, including Haynes and Morse Reservoirs; the Fallbrook Reservoir at Wachusett Street; the Notown Reservoir system, including Goodfellow Pond and Simonds Reservoirs; and the Southeast Corner Well Fields off Jungle Road. Leominster also has an emergency connection to the Wachusett Reservoir. SOURCE WATER ASSESSMENT AND PROTECTION In 2004 the Massachusetts Department of Environmental Protection (MassDEP) completed a Source Water Assessment and Protection (SWAP) report for the sources serving this water system. MassDEP assigned an overall susceptibility ranking of high to Leominster's water sources, based on the presence of at least one high threat land use within the water supply protection areas. The City of Leominster continues to actively promote source protection through aggressive land acquisition, installation of sanitary sewers, and continued public education efforts Where can I see the SWAP Report? The SWAP report and map are available at the Leominster Water Division. -
The Following Test Is Continuing Education For
The following test is Continuing Education for: Master Plumbers, Journeyman Plumbers, UDC Plumbing Inspectors, and Commercial Plumbing Inspectors. You can complete the test by printing a hard copy, or you can take it online. All answers are found in the Wisconsin Uniform Plumbing Code Book (Comm. 81 and 82). If you do not own a Plumbing codebook, you may follow this link to the State of Wisconsin website and download it to your computer. http://commerce.wi.gov/SB/SBDivCodesListing.tml. The answer sheet can be found at the end of the test. Take the following steps to complete the testing process: 1. Print the answer sheet and circle the correct answer. 2. Complete and Mail the: a) Answer sheet b) Educational Course Attendance Verification Form (found after the answer sheet) c) Correct fees. There is no reason to mail the whole test. Remember: All questions have been extracted from the codebook. Therefore, the one correct answer will be as worded in the codes. Begin test on the following page… 1 Plumbing Continuing Education Test 8 Comm 81.01: Definitions 1. _____ means an individual or agency recognized by the department to act on the department’s behalf relative to a specific activity or function. a. Manager b. Agent c. Inspector d. Representative 2. ______ means a pressure vessel fixture designed to use steam under pressure for sterilizing. a. Sterilizer, pressure b. Autoclave c. Sterilizer, pressure instrument washer d. Both a and b 3. ______ means a health care facility that accepts federal funding in accordance with 42 CFR 416 of the federal register for health care finance and where 4 or more individuals that undergo a surgical procedure for which federal reimbursement is based. -
Plumbing Continuing Education Test 13.Pdf
The following test is Continuing Education for: Master Plumbers, Journeyman Plumbers, UDC Plumbing Inspectors, and Commercial Plumbing Inspectors. You can complete the test by printing a hard copy, or you can take it online. All answers are found in the Wisconsin Uniform Plumbing Code Book (Comm. 81 and 82). If you do not own a Plumbing codebook, you may follow this link to the State of Wisconsin website and download it to your computer. http://commerce.wi.gov/SB/SBDivCodesListing.tml. The answer sheet can be found at the end of the test. Take the following steps to complete the testing process: 1. Print the answer sheet and circle the correct answer. 2. Complete and Mail the: a) Answer sheet b) Educational Course Attendance Verification Form (found after the answer sheet) c) Correct fees. There is no reason to mail the whole test. Remember: All questions have been extracted from the codebook. Therefore, the one correct answer will be as worded in the codes. Begin test on the following page… 1 Plumbing Continuing Education Test 13 Comm 81.01: Definitions 1. _______ means a plumbing appliance, the function of which is unique to health care activities. a. Hand held shower b. Assisted living bath fixtures c. Health care plumbing appliance d. Healthcare accessible 2. ______ means a device designed to prevent the reverse flow of wastewater in a drain system. a. Access box b. Diverter valve c. Backwater valve d. Access sleeve 3. ______ means a water supply valve opened or closed by means of a float or similar device used to supply water to a tank. -
2020 Drinking Water Quality Report
City of Leominster, Department of Public Works, Water Division Public Water Supply ID # 2153000 2020 DRINKING WATER QUALITY REPORT The City of Leominster is dedicated to preserving and improving the quality and reliability of its drinking water supplies. In addition to continued source protection efforts and significant upgrades to all the treatment facilities, the City has an aggressive flushing and water main replacement program. Further information about this report or any aspect of the public water supply can be obtained by contacting Mark Piermarini at 978-534-7590, ext. 3639, cell phone 978-660-0061, or e-mail: [email protected] YOUR DRINKING WATER SOURCES The City of Leominster lies entirely within the Nashua River basin. It encompasses about 30 square miles of land. Much of the western half of the city includes state forest, watershed lands, and other protected open space. The City obtains its drinking water from the Distributing Reservoir system, including Haynes and Morse Reservoirs; the Fallbrook Reservoir at Wachusett Street; the Notown Reservoir system, including Goodfellow Pond and Simonds Reservoirs; and the Southeast Corner Well Fields off Jungle Road. Leominster also has an emergency connection to the Wachusett Reservoir. SOURCE WATER ASSESSMENT AND PROTECTION In 2004 the Massachusetts Department of Environmental Protection (MassDEP) completed a Source Water Assessment and Protection (SWAP) report for the sources serving this water system. MassDEP assigned an overall susceptibility ranking of high to Leominster's water sources, based on the presence of at least one high threat land use within the water supply protection areas. The City of Leominster continues to actively promote source protection through aggressive land acquisition, installation of sanitary sewers, and continued public education efforts Where can I see the SWAP Report? The SWAP report and map are available at the Leominster Water Division. -
WISCONSIN HEALTHCARE ENGINEERING ASSOCIATION (WHEA) Cross Connection/Backflow Prevention
WISCONSIN HEALTHCARE ENGINEERING ASSOCIATION (WHEA) Cross Connection/Backflow Prevention Webinar: September 13, 2018 AFFILIATED ENGINEERS, INC. September 13, 2018 | Slide 1 Presenter - Bio • Affiliated Engineers • 25 years overall experience • 15 year healthcare • Market sectors served: healthcare, higher education, pharma/biotech, and research clients • Clients: University of Wisconsin Hospital & Clinics, Unity Point Healthcare-Meriter, Aurora Healthcare, Ascension Health Care, Ann & Robert H. Lurie Children’s Hospital of Chicago SCOTT LARGENT, PE PIPING Senior Project Engineer 608-236-1228 [email protected] AFFILIATED ENGINEERS, INC. September 13, 2018 | Slide 2 Wisconsin Healthcare Engineering Association (WHEA) • https://www.whea.com/ AFFILIATED ENGINEERS, INC. September 13, 2018 | Slide 3 Wisconsin Healthcare Engineering Association (WHEA) • https://www.whea.com/education/webinars/ AFFILIATED ENGINEERS, INC. September 13, 2018 | Slide 4 Wisconsin Healthcare Engineering Association (WHEA) AFFILIATED ENGINEERS, INC. September 13, 2018 | Slide 5 Backflow – Cross Connection • What is unique to Healthcare? • Why do we care about backflow prevention? • Patient and Personnel Safety • How do we ensure backflow prevention requirements are being met? • Identification of Hazard • Code Requirements AFFILIATED ENGINEERS, INC. September 13, 2018 | Slide 6 Backflow – Cross Connection • Code • Backflow Conditions • Cross Connection Devices • Design and Device Locations • Plan Review • Testing • Fixtures, Food Service, Equipment • Q & A / Wrap up