Analysis Techniques December 30, 2000
Total Page:16
File Type:pdf, Size:1020Kb
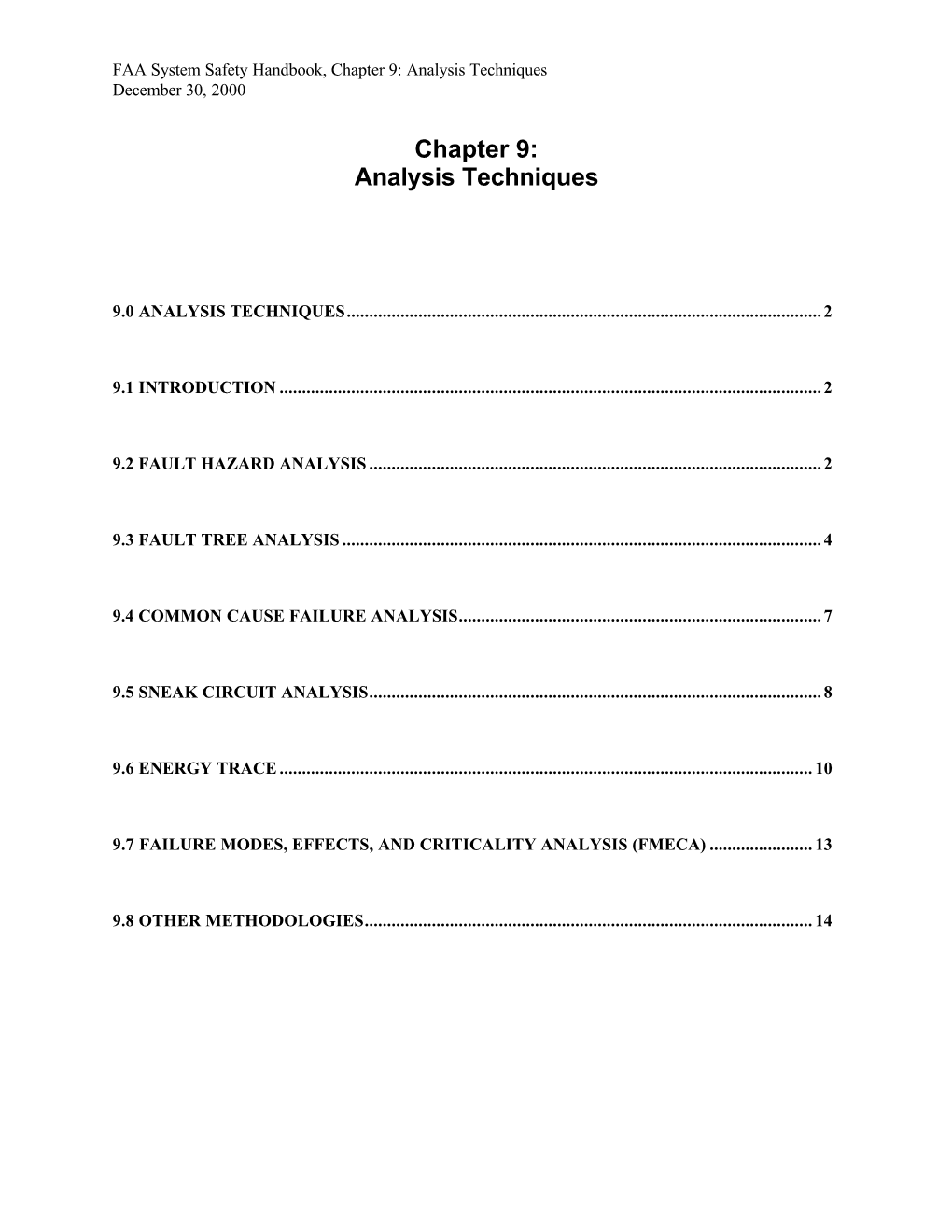
Load more
Recommended publications
-
OCCUPATIONAL MEDICINE PROGRAM HANDBOOK October 2005
U.S. DEPARTMENT OF THE INTERIOR OFFICE OF OCCUPATIONAL HEALTH AND SAFETY OCCUPATIONAL MEDICINE PROGRAM HANDBOOK October 2005 This Occupational Medicine Program Handbook was prepared by the U.S. Department of the Interior’s Office of Occupational Health and Safety, in consultation with the U.S. Office of Personnel Management and the U.S. Public Health Service’s Federal Occupational Health service. This edition of the Handbook represents the continuing efforts of the contributing agencies to improve occupational health services for DOI employees. It reflects the comments and suggestions offered by users over the years since it was first introduced, and addresses the findings, concerns, and recommendations summarized in the final report of a program review completed in 1994 by representatives of the Uniformed Services University of the Health Sciences. That report, entitled “A Review of the Occupational Health Program of the United States Department of the Interior,” was prepared by Margaret A.K. Ryan, M.D., M.P.H., Gail Gullickson, M.D., M.P.H., W. Garry Rudolph, M.D., M.P.H., and Elizabeth Odell. The report led to the establishment of the Department’s Occupational Health Reinvention Working Group, composed of representatives from the DOI bureaus and operating divisions. The recommendations from the Reinvention Working Group final report, published in May of 1996, were addressed and are reflected in what became this Handbook. First published in 1997, the Handbook underwent a major update in July, 2000. This 2005 version of the Handbook incorporates the updates and enhancements that have been made in DOI policies and occupational medicine practice since the last edition. -
A Model for Mandatory Job Safety Analysis Embedded in the Premit-To-Work System >
International Gas Union Research Conference 2011 <A MODEL FOR MANDATORY JOB SAFETY ANALYSIS EMBEDDED IN THE PREMIT-TO-WORK SYSTEM > Main author I. K. Yoon KOREA ABSTRACT Permit to Work (PTW) systems is defined as "a formal documented system used to control the certain types of work that are potentially hazardous". Generally, PTW system should be designed to specify the work to be done safely and the precaution to be taken as well as approval, responsibility, permissions of work. For this reason, PTW is regarded as one of the most important safety management system to control the risk of maintenance that causes 30% of the accident in chemical industries. In the early days, PTW was based on paper based system. But recently has continued to evolve into a computer based system. And these advanced systems has been applied to 80% of oil industry in North Sea and upgraded with providing the hazard information as well as supporting documentation. Usually, the hazard information is provided in the form of hazard checklist or attached risk assessment report such as JSA sheet. But when we consider the various types of work, place and environment, all the potential work related hazard cannot be reviewed in the form of prescribed checklist or certain attachment. To review the potential hazard perfectly, the work permit should be supported by Job Safety Analysis (JSA). But it has rarely been seen that company have a rule to require the mandatory JSA whenever permit to work is accomplished. Despite a relatively simple analysis structure, it is time-consuming and person-consuming methodology to complete all the procedure. -
Personal Protective Equipment Hazard Assessment
WORKER HEALTH AND SAFETY Personal Protective Equipment Hazard Assessment Oregon OSHA Personal Protective Equipment Hazard Assessment About this guide “Personal Protective Equipment Hazard Assessment” is an Oregon OSHA Standards and Technical Resources Section publication. Piracy notice Reprinting, excerpting, or plagiarizing this publication is fine with us as long as it’s not for profit! Please inform Oregon OSHA of your intention as a courtesy. Table of contents What is a PPE hazard assessment ............................................... 2 Why should you do a PPE hazard assessment? .................................. 2 What are Oregon OSHA’s requirements for PPE hazard assessments? ........... 3 Oregon OSHA’s hazard assessment rules ....................................... 3 When is PPE necessary? ........................................................ 4 What types of PPE may be necessary? .......................................... 5 Table 1: Types of PPE ........................................................... 5 How to do a PPE hazard assessment ............................................ 8 Do a baseline survey to identify workplace hazards. 8 Evaluate your employees’ exposures to each hazard identified in the baseline survey ...............................................9 Document your hazard assessment ...................................................10 Do regular workplace inspections ....................................................11 What is a PPE hazard assessment A personal protective equipment (PPE) hazard assessment -
Federal Register/Vol. 84, No. 97/Monday, May 20, 2019/Proposed Rules
22756 Federal Register / Vol. 84, No. 97 / Monday, May 20, 2019 / Proposed Rules rents, or royalties received or accrued (iii) Anti-abuse rule. Paragraphs § 1.958–2 Constructive ownership of from a foreign corporation as received or (f)(2)(iv)(B)(1) and (3) of this section stock. accrued from a controlled foreign apply to taxable years of controlled * * * * * corporation payor if a principal purpose foreign corporations ending on or after (d) * * * of the use of an option to acquire stock May 17, 2019, and to taxable years of (1) * * * Except as otherwise or an equity interest, or an interest United States shareholders in which or provided in paragraph (d)(2) of this similar to such an option, that causes with which such taxable years end, with section and § 1.954–1(f)— the foreign corporation to be a respect to amounts that are received or * * * * * controlled foreign corporation payor is accrued by a controlled foreign (e) * * * Except as otherwise to qualify dividends, interest, rents, or corporation on or after May 17, 2019 to provided in § 1.954–1(f), if any person royalties paid by the foreign corporation the extent the amounts are received or has an option to acquire stock, such for the section 954(c)(6) exception. For accrued in advance of the period to stock shall be considered as owned by purposes of this paragraph which such amounts are attributable such person. * * * (f)(2)(iv)(B)(2), an interest that is similar with a principal purpose of avoiding the * * * * * to an option to acquire stock or an application of paragraph (f)(2)(iv)(B)(1) (h) Applicability date. -
Hazards Analysis Report
PROJECT MANAGEMENT Doc. No. LUSI SUB-SYSTEM DOCUMENT PM-391-001-34 R0 1.1 Management Hazards Analysis Report Technical Contact: Nadine Kurita LUSI Chief Engineer Signature Date Approved by: Tom Fornek LUSI Project Manager Signature Date Approved by: John Galayda LCLS Project Director Signature Date Rev Description Date 0 Initial Release July 8, 2008 PM-391-001-34 R0 Verify that this is the latest revision. 1 of 34 Check for change orders or requests TABLE OF CONTENTS 1. Introduction............................................................................................................. 3 1.1 Purpose and Scope .............................................................................................. 3 1.2 Environment, Worker and Public Safety ............................................................ 3 2. Summary................................................................................................................. 4 2.1 Overview of Hazards .......................................................................................... 4 2.2 Comprehensiveness of the Safety Analysis ........................................................ 5 2.3 Appropriateness of the Accelerator Safety Envelope ......................................... 5 3. Project Description..................................................................................................5 3.1 X-Ray Pump/Probe Diffraction Instrument........................................................ 6 3.2 Coherent X-ray Imaging Instrument.................................................................. -
Personal Protective Equipment/Job Hazard Analysis Program
SALISBURY UNIVERSITY PPE/JOB HAZARD ANALYSIS STANDARD PRACTICE INSTRUCTION DATE: January 15, 2019 SUBJECT: Personal Protective Equipment/Job Hazard Analysis Program REGULATORY STANDARD: 29 CFR §1910.132-138. I. PURPOSE: The purpose of this program is to establish procedures for wearing Personal Protective Equipment (PPE) by all Salisbury University employees, contractors and visitors on campus. This program supports compliance with the Occupational Safety and Health Administration (OSHA) standards that cover PPE, specifically, 29 CFR 1910.132, .133, .135, .136 and .138. This program applies to all University employees, contractors and visitors who work in areas that contain hazards to the eyes, face, head, hands and feet. Respiratory and noise hazards are covered in the S0U Respiratory Protection Program and the SU Hearing Conservation Program. II. DEFINITIONS: ANSI (American National Standards Institute): A nonprofit organization that approves national safety standards. Ophthalmologist: A physician/surgeon who specializes in diagnosing and treating eye diseases and disorders. Optician: A skilled technician who, when given a medical prescription, is qualified to make, fit and dispense eyeglasses and contact lenses, either in an optical laboratory or for retail sale to the public; opticians do not examine patients or write prescriptions. Optometrist: A licensed primary eye-care provider who performs eye examinations, prescribes and dispenses eyeglasses and contact lenses and performs some diagnostic work, such as screening for glaucoma or cataracts. Plano: A common term for nonprescription safety glasses. PPE: Personal Protective Equipment III. RESPONSIBILITIES: A. The Program Administrator The SU PPE Program Administrator is the Director of Sustainability & Environmental Safety. Responsibilities include: Modify only under the supervision of the Safety Manager. -
A Zonal Safety Analysis Methodology for Preliminary Aircraft Systems and Structural Design
A Zonal Safety Analysis Methodology for Preliminary Aircraft Systems and Structural Design Chen, Z. and Fielding, J. P. School of Aerospace, Transport and Manufacturing, Cranfield University ABSTRACT Zonal Safety Analysis (ZSA) is a major part of the civil aircraft safety assessment process described in Aerospace Recommended Practice 4761 (ARP4761). It considers safety effects that systems/items installed in the same zone (i.e. a defined area within the aircraft body) may have on each other. Although the ZSA may be conducted at any design stage, it would be most cost-effective to do it during preliminary design, due to the greater opportunity for influence on system and structural designs and architecture. The existing ZSA methodology of ARP4761 was analysed but it was found to be more suitable for detail design rather than preliminary design. The authors therefore developed a methodology that would be more suitable for preliminary design and named it the Preliminary Zonal Safety Analysis (PZSA). This new methodology was verified by means of the use of a case-study, based on the NASA N3-X project. Several lessons were learnt from the case study, leading to refinement of the proposed method. These lessons included focusing on the positional layout of major components for the zonal safety inspection, and using the Functional Hazard Analysis (FHA)/Fault Tree Analysis (FTA) to identify system external failure modes. The resulting PZSA needs further refinement, but should prove to be a useful design tool for the preliminary design process. _____________________________________ INTRODUCTION This paper outlines the development of a methodology, hereafter referred to as the Preliminary Zonal Safety Historically, system safety analysis was primarily based Analysis (PZSA). -
Personal Protective Equipment (PPE) Guide
Personal Protective Equipment (PPE) Guide Volume 1: General PPE February 2003 F417-207-000 This guide is designed to be used by supervisors, lead workers, managers, employers, and anyone responsible for the safety and health of employees. Employees are also encouraged to use information in this guide to analyze their own jobs, be aware of work place hazards, and take active responsibility for their own safety. Photos and graphic illustrations contained within this document were provided courtesy of the Occupational Safety and Health Administration (OSHA), Oregon OSHA, United States Coast Guard, EnviroWin Safety, Microsoft Clip Gallery (Online), and the Washington State Department of Labor and Industries. TABLE OF CONTENTS (If viewing this pdf document on the computer, you can place the cursor over the section headings below until a hand appears and then click. You can also use the Adobe Acrobat Navigation Pane to jump directly to the sections.) How To Use This Guide.......................................................................................... 4 A. Introduction.........................................................................................6 B. What you are required to do ..............................................................8 1. Do a Hazard Assessment for PPE and document it ........................................... 8 2. Select and provide appropriate PPE to your employees................................... 10 3. Provide training to your employees and document it ........................................ 11 -
2010 Ca-1 Tutorial Textbook
Name:_______________________ 2010 CA-1 TUTORIAL TEXTBOOK 4th Edition STANFORD UNIVERSITY MEDICAL CENTER DEPARTMENT OF ANESTHESIOLOGY Aileen Adriano, M.D. KtKate EllbEllerbroc k, MDM.D. Becky Wong, M.D. TABLE OF CONTENTS Introduction…………………………………………………………………….ii Acknowledgements…………………………………………………………….iii Contributors…………………………………………………………………….iv Key Points and Expectations…………………………………………………...v Goals of the CA-1 Tutorial Month……………………………………………..vi Checklist for CA-1 Mentorship Intraoperative Didactics………………………vii CA-1 Mentorship Intraoperative Didactic Lectures Standard Monitors………………………………………………..1 Inhalational Agents…………………………………………….....4 MAC and Awareness……………………………………………..7 IV Induction Agents……………………………………………..10 Rational Opioid Use……………………………………………..13 Intraoperative Hypotension & Hypertension……………………16 Neuromuscular Blocking Agents………………………………..19 Difficult Airway Algorithm……………………………………..23 Fluid Management ……………………………………………...27 Transfusion Therapy…………………………………………….31 Hypoxemia…………………………………………………........35 Electrolyte Abnormalities……………………………………….39 Hypothermia & Shivering………………………………….……44 PONV……………………………………………………………47 Extubation Criteria & Delayed Emergence……………….….…50 Laryngospasm & Aspiration…………………………………….53 Oxygen Failure in the OR……………………………………….56 Anaphylaxis……………………………………………………..59 ACLS…………………………………………………….………62 Malignant Hyperthermia………………………………………...65 Perioperative Antibiotics………………………………………..69 Cognitive Aids Reference Slides………………………………..72 i INTRODUCTION TO THE CA-1 TUTORIAL MONTH We want to welcome you as the -
Risk Assesment: Fault Tree Analysis
RISK ASSESMENT: FAULT TREE ANALYSIS Afzal Ahmed+, Saghir Mehdi Rizvi*Zeshan Anwer Rana* Faheem Abbas* +COMSAT Institute of Information and Technology, Sahiwal, Pakistan *Navy Engineering College National University of Sciences and Technology, Islamabad drafzal@ciitsahiwal>edu.pk, 03452325972 ABSTRACT The failure of engineering equipment causes loss of capital as well as human loss, injuries, and stoppage of production line. The hazards can be classified as safe, minor, major, critical and catastrophic Risk analysis or hazard analysis pin points the potential failures of engineering systems and or components when being used.. Failure mode and effects analysis is used to identify hazard and to make system safer. A system is broken down up to level of components and using reliability data the safety or probability of failure of assemblies and the system can be calculated. The failure mode and effects analysis is used with fault tree analysis to point the areas of a complex system where failure mode effect analysis is required. Fault tree analysis (FTA) is a technique which pinpoints any failure or severe accidents. It tells how things fail rather than emphasize on the design performance. It is a logic diagram connecting inputs an outputs using Boolean algebra. This paper shows how FTA can be applied to car carburetor failure and car brake failure. Key words : Risk Management, Reliability, Fault tree, Failure mode INTRODUCTION The world is full risk. We are at risk of accident minor. A failure of an aircraft may cause death when crossing a road or driving. We are at risk to passengers, while a machine may cause living in an apartment not properly designed. -
Redundancy Unite Guide for Members Contents
Legal services Right by your side Redundancy Unite guide for members Contents Introduction 3 What is redundancy? 4 Lay-off and short term working Consultation 5 Re-structures and changes to terms and conditions When should consultation begin? Disclosure of information Scope of Consultation Requirement to complete the HR1 form Insolvency Failure to inform and consult Protective Award Representative’s role 8 Time off for representatives Facilities for representatives Statutory protection for representatives Selection for redundancy 9 Discrimination Automatically unfair selection criteria Notice 11 Time off to look for work Redundancy pay 12 Workers with no right to redundancy pay Calculating redundancy pay A ‘weeks’ pay Written statement Redundancy payments and tax State benefits Alternative employment 14 Maternity Leave Trial period Unfair dismissal Time limit COVID 19 16 Corona Virus Job Retention Scheme Section 188 consultation Selection for Redundancy Calculation of Statutory Redundancy Pay Calculation of Statutory Notice Pay Introduction Redundancy has become an all too depressing feature of the modern economic landscape. Globalisation, increased competition, technological change, government cuts have all contributed to the continuing tide of job losses. At least 109,000 workers lost their jobs in the UK through redundancy in 2019. Redundancy affects not only individuals, but their families and local communities as well. For this reason Unite seeks to use all means possible to safeguard jobs. Our aim is always to reach agreements which -
Complementarity in Public Health Systems: Using Redundancy As a Tool of Public Health Governance
Annals of Health Law Volume 22 Issue 2 Special Edition 2013 Article 4 2013 Complementarity in Public Health Systems: Using Redundancy as a Tool of Public Health Governance Lance Gable Benjamin Mason Meier Follow this and additional works at: https://lawecommons.luc.edu/annals Part of the Health Law and Policy Commons Recommended Citation Lance Gable & Benjamin M. Meier Complementarity in Public Health Systems: Using Redundancy as a Tool of Public Health Governance, 22 Annals Health L. 224 (2013). Available at: https://lawecommons.luc.edu/annals/vol22/iss2/4 This Article is brought to you for free and open access by LAW eCommons. It has been accepted for inclusion in Annals of Health Law by an authorized editor of LAW eCommons. For more information, please contact law- [email protected]. Gable and Meier: Complementarity in Public Health Systems: Using Redundancy as a T Complementarity in Public Health Systems: Using Redundancy as a Tool of Public Health Governance Lance Gable* & Benjamin Mason Meier** I. INTRODUCTION Modem notions of public health law embody an astounding complexity. Layers of authority arise from the accretion of legislative, regulatory, and common law developments over many years and across many subjects and jurisdictions.' As recognition of the variety and interconnectedness of public health threats has grown to encompass both proximal and distal determinants of health, the application and relevance of law has evolved to address these challenges.2 Traditional understandings of public health law focused primarily on alleviation