Abrasive Lessons For
Total Page:16
File Type:pdf, Size:1020Kb
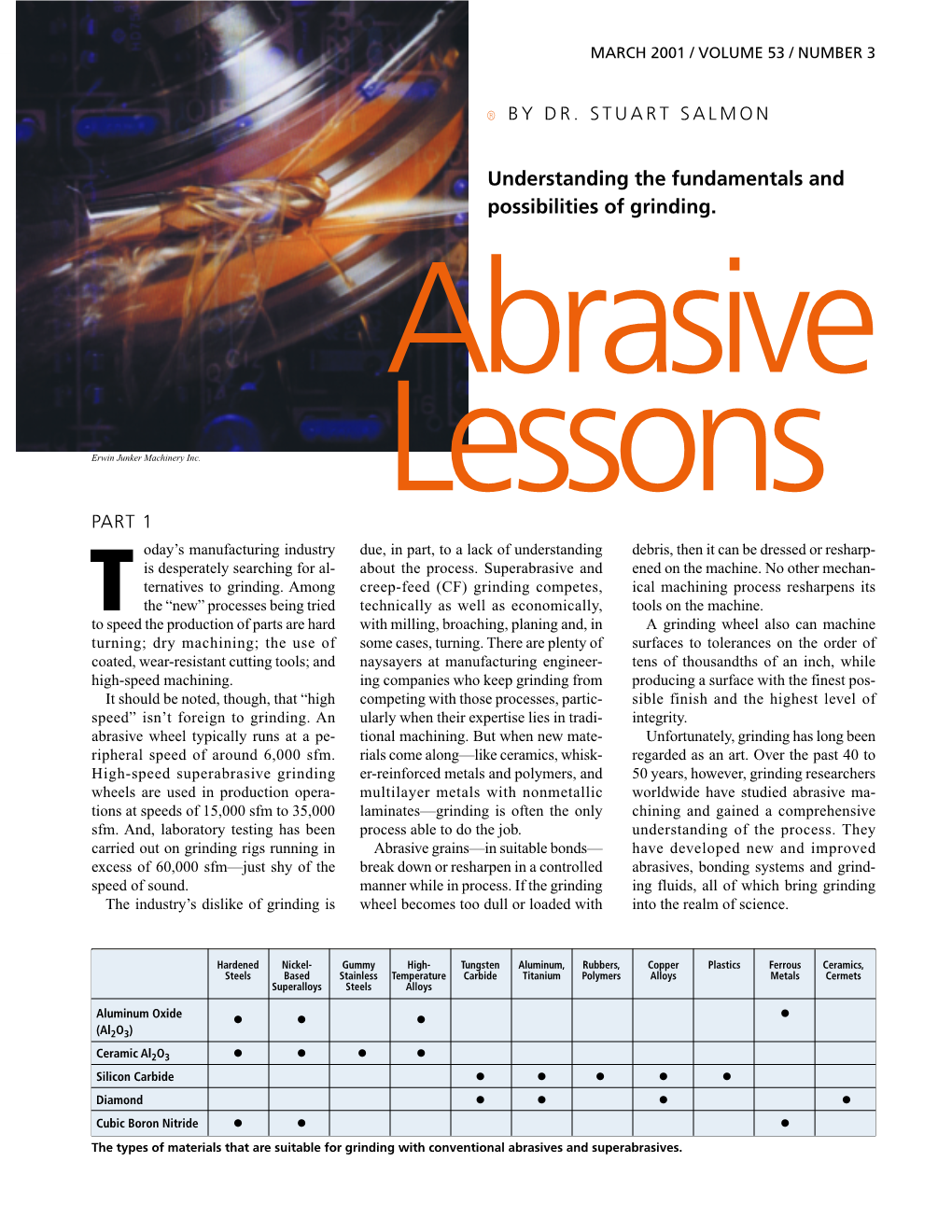
Load more
Recommended publications
-
NIMS CNC Milling Programming & Set-Up
SC ACCELERATE MTT 255 Open Text Module 5 3 NIMS CNC Milling 5 Programming & Set-Up Objectives Students will be able to: • Write and Format CNC milling programs • Diagram CNC Fanuc Control Programs • Analyze and edit CNC G-code based programs • Program and Operate a CNC Mill by earning Level I NIMS CNC Milling Credential Orienting Questions ü How do cutter offsets effect CNC programming? ü What is the difference between cutter compensation left and right? ü What is the difference between contour machining and point machining? ü Is “NIMS” a National or State Accredited Program? ü Why is NIMS important to Industry? **The bolded/underlined words are key terms…click on the blue underlined terms for more information. **Closed Captions and transcripts are available for all videos in this module. Click the button at the bottom right of the play menu to turn on closed captioning in the language of your choice. You may also read a full transcript of this video by clicking on the bottom below the play menu.** Except where otherwise noted, this work was created by Mark Cramer and is licensed under the Creative Commons Attribution 4.0 International License. SC ACCELERATE Page | 1 Version │ Course ID │ Rev 1 2012 SC ACCELERATE MTT 255 Open Text Module 5 To view a copy of this license, visit http://creativecommons.org/licenses/by/4.0/ or send a letter to Creative Commons, 444 Castro Street, Suite 900, Mountain View, California, 94041, USA. INTRODUCTION CNC Milling Programs can be divided into two basic divisions; the “Preparation Codes” and the actual “Machining Codes”. -
Knives 2019 Amoureux—Armour
custom knifemakers ABEGG—AMOS Uses stainless, salvage wrought iron, brass and copper for fi ttings. Handle materials A include stabilized and natural domestic and exotic fi gured woods, durable synthetics, ABEGG, ARNIE stacked leather. Makes own sheaths. Prices: $300 and up. Remarks: Part-time maker. 5992 Kenwick Cr, Huntington Beach, CA 92648, Phone: 714-848-5697 First knife sold in 2013. Doing business as Aldrich Knife & Tool. Emphasis put on clean ABERNATHY, LANCE lines, fi t and fi nish and performance. Mark: An arched ALDRICH. Sniper Bladeworks, 1924 Linn Ave., North Kansas City, MO 64116, Phone: 816-585- ALEXANDER, EUGENE 1595, [email protected]; Web: www.sniperbladeworks.com Box 540, Ganado, TX 77962-0540, Phone: 512-771-3727 Specialties: Tactical frame-lock and locking-liner folding knives. Alexander,, Oleg, and Cossack Blades ACCAWI, FUAD 15460 Stapleton Way, Wellington, FL 33414, Phone: 443-676-6111, Web: www. 130 Timbercrest Dr., Oak Ridge, TN 37830, Phone: 865-414-4836, gaccawi@ cossackblades.com comcast.net; Web: www.acremetalworks.com Technical: All knives are made from hand-forged Damascus (3-4 types of steel are used to Specialties: I create one of a kind pieces from small working knives to performance create the Damascus) and have a HRC of 60-62. Handle materials are all natural, including blades and swords. Patterns: Styles include, and not limited to hunters, Bowies, daggers, various types of wood, horn, bone and leather. Embellishments include the use of precious swords, folders and camp knives. Technical: I forge primarily 5160, produces own metals and stones, including gold, silver, diamonds, rubies, sapphires and other unique Damascus and does own heat treating. -
Grinding Grinding Is the Most Common Form of Abrasive Machining. It Is Acutting Process Which Engages an Abrasive Tool Whose
Grinding Grinding is the most common form of abrasive machining. It is acutting process which engages an abrasive tool whose cutting elements are grains of abrasive material known as grit. The grits are held together by a suitable bonding material to give shape of an abrasive tool. Advantages of grinding • dimensional accuracy • good surface finish • good form and locational accuracy • applicable to both hardened and unhardened material. Applications of grinding •surface finishing • slitting and parting • descaling, deburring • stock removal (abrasive milling) • finishing of flat as well as cylindrical surface • grinding of tools and cutters and resharpening of the same . Conventional grinding machines are classified as: (a) Surface grinding machine (b) Cylindrical grinding machine (c) Internal grinding machine (d) Tool and cutter grinding machine a)Surface grinding machine: This machine may be similar to a milling machine used mainly to grind flat surface. However, some types of surface grinders are also capable of producing contour surface with formed grinding wheel. Basically there are four different types of surface grinding machines characterised by the movement of their tables and the orientation of grinding wheel spindles as follows: • Horizontal spindle and reciprocating table • Vertical spindle and reciprocating table • Horizontal spindle and rotary table • Vertical spindle and rotary table B)Cylindrical grinding machine This machine is used to produce external cylindrical surface. The surfaces may be straight, tapered, steps or profiled. Broadly there are three different types of cylindrical grinding machine as follows: 1. Plain centre type cylindrical grinder 2. Universal cylindrical surface grinder 3. Centreless cylindrical surface grinder Plain centre type cylindrical grinder Universal cylindrical surface grinder Centreless grinder C)Internal grinding machine This machine is used to produce internal cylindrical surface. -
FANUC Series 0I-MODEL F for Lathe System OPERATOR's MANUAL
FANUC Series 0+-MODEL F For Lathe System OPERATOR'S MANUAL B-64604EN-1/01 • No part of this manual may be reproduced in any form. • All specifications and designs are subject to change without notice. The products in this manual are controlled based on Japan’s “Foreign Exchange and Foreign Trade Law”. The export of from Japan subject to an export license by the government of Japan. Other models in this manual may also be subject to export controls. Further, re-export to another country may be subject to the license of the government of the country from where the product is re-exported. Furthermore, the product may also be controlled by re-export regulations of the United States government. Should you wish to export or re-export these products, please contact FANUC for advice. The products in this manual are manufactured under strict quality control. However, when a serious accident or loss is predicted due to a failure of the product, pay careful attention to safety. In this manual we have tried as much as possible to describe all the various matters. However, we cannot describe all the matters which must not be done, or which cannot be done, because there are so many possibilities. Therefore, matters which are not especially described as possible in this manual should be regarded as “impossible”. B-64604EN-1/01 SAFETY PRECAUTIONS SAFETY PRECAUTIONS This section describes the safety precautions related to the use of CNC units. It is essential that these precautions be observed by users to ensure the safe operation of machines equipped with a CNC unit (all descriptions in this section assume this configuration). -
TIVAR Fabrication & Machining
TIVAR Fabrication & Machining TIVAR can be efficiently machined using conventional Turning (cont.) machine tools and woodworking machinery. It is often necessary to run at reduced RPMs to enable the operator to keep chips clear of the machine. Care must Cutting tools should have high rake angles and sufficient be taken: it is easy to get hands caught in the machinery chip clearance to prevent clogging. If the above criteria are and debris. met, cutting speeds of up to 5,000 surface feet per minute are practical. Feed rates should be high, so that minimum Milling time is allowed for the cutting tool to heat the material by Carbide cutters designed for machining aluminum give friction. the best results. Conventional high-speed steel end mills and Very high surface finishes can be obtained by using cutters designed for machining steel can be used, but they proper cutting tools. Attempts to improve poor finishes by do not have sufficient rake angle or chip clearance for filling or sanding usually result in worsening the appearance. efficient stock removal. Cutting fluids should not be necessary, but a blast of Router bits work well for slotting and light milling. For compressed air will sometimes aid in chip removal. cutting deep slots and T-slots, it is essential that compressed air be used to blow chips away from the cutter. Sawing For circular sawing, course tooth carbide-tipped blades Planing give the best results. An 8 diameter blade should have Wood planers will readily reduce the thickness and approximately 12 teeth with lots of clearance. A number of true up the surface of TIVAR. -
Super Abrasive Machining for PM
case study Super abrasive machining for PM Cost-effective secondary finish process offers upstream cost savings for manufacturers of aerospace, automotive, and industrial components. n today’s fast-paced world, how often ny’s stock removal processes has been • Wheel feed rate do you hear the phrase, “We wel- proven to save its users money by replac- • Coolant make-up, flow and applica- come interruptions?” Super abrasive ing traditional grinding or single-point tion (presentation) machining (SAM) does just that. machining applications. • Machine action, platform and capa- IThe impact of this secondary proc- It’s important to distinguish the dif- bility. ess is having a dramatic effect on the ferences between grinding and SAM. reliability and cost associated with dif- Although both are performed with ficult interrupted and other heavy and a wheel and not a single point tool, The correct complex cuts. These types of component grinding is typically used to remove applications geometries, whose numbers are ever a small amount of stock material to increasing with the growth and increas- achieve a final size and finish. SAM, by Because of the higher capital, wheel ing complexity of VVT (variable valve tim- comparison, is used to machine parts and fixturing costs associated with SAM ing) chain and gear drives (see Figure 5), from differing geometries and features when applied to net shape processes, besides the expanding demand of PM to extremely high degrees of accuracy users of the technology look for rapid to combine multiple components into and surface finish. Another distinction: paybacks of this initial investment. In single pressings, once threatened the SAM equipment more closely resembles order to improve this rate of payback, it economics of PM to satisfy these needs. -
Ch. 26 – Abrasive Machining and Finishing Operations
Abrasive Machining and Finishing Operations MAE 250 L Abrasive Machining and Finishing Operations • There are many situations where Mill & Lathe processes about cannot produce the required dimensional accuracy and/or surface finish. – Fine finishes on ball/roller bearings, pistons, valves, gears, cams, etc. – The best methods for producing such accuracy and finishes involve abrasive machining. Abrasives and Bonded Abrasives • An abrasive is a small, hard particle having sharp edges and an irregular shape. (grit) • Abrasives are capable of removing small amounts of material through a cutting process that produces tiny chips. Abrasive Processes • 1. Grinding • 2. Related Abrasive Processes – (Honing, Lapping, Super-finishing and Polishing & Buffing, Sanding/emory cloth) Grinding is the most important abrasive machining – Similar to slab milling: Cutting occurs at either the periphery or the face of the grinding wheel. – Different than milling: Cutting occurs by the abrasive grains that are much smaller, numerous and random. – Cutting speeds are higher, generating more heat – Higher negative rake angles on grit cutting edges – Self-sharpening as abrasive falls off Abrasive Grinding • Can be viewed as multiple very small cutting edges • Can result in a very fine finish • Can leave residual stresses on part • Slow, small material removal rates • Sparking out to finish Grinding Operations and Machines • Surface Grinding • Cylindrical Grinding • Internal Grinding • Centerless Grinding • Creep-feed Grinding – Heavy Stock Removal by Grinding • -
Machining Precise Material Removal to Bring a Part to Specified Size
Machining Precise material removal to bring a part to specified size • Automotive machining examples Boring cylinders Honing cylinders Grinding cranks and cams Grinding or milling heads and blocks Grinding flywheels Drilling and reaming for valve guides Copyright 2003 Gary Lewis – Dave Capitolo Machining Drilling • End cutting • Used for roughing holes to size • Reamers finish holes to size and surface finish Machining Turning & boring • Turning – outside diameter with single pointed tools on a lathe • Boring – inside diameter with single pointed tools on a lathe Machining Milling • Vertical spindle • Used to remove material from a flat surface Machining Milling • Typical milling cutters HSS & carbide Machining Grinding • Abrasive machining using millions abrasive grains • Minimal stock removal • High surface finish quality Vertical spindle surfacing • Used to grind flywheels, blocks, and cylinder heads Machining Horizontal spindle grinders • Used for valve grinders, crankshaft grinders, and camshaft grinders Machining Broaching • Chip removal is done with progressively larger cutting teeth • Keyways in sprockets and gears • Not done in auto machine shops Machining Tool materials HSS (High speed steel) • Drills, reamers, and milling cutters • Tungsten, vanadium, and cobalt added for hardness Tungsten carbide • Boring bars and cutter of a face mill • Attached to a tool holder • Heat resistant and operate at high speeds (up to 3 times HSS) • Cobalt increased for shock resistance Machining Tool materials Tungsten Carbide (cont.) • As cobalt -
NIMS CNC Lathe Programming & Set-Up
SC ACCELERATE MTT 255 Open Text Module 4 4 NIMS CNC Lathe Programming & Set-Up Objectives Students will be able to: • Describe the purpose and identify various canned cycles • Summarize and modify CNC turning programs • Analyze and edit CNC G-code based programs • Operate a CNC Lathe by earning Level I NIMS CNC Turning Credential Orienting Questions ü Why are canned cycles beneficial for CNC Programming? ü What is the difference between roughing and finishing? ü Why is tool-nose radius important to geometry? ü Why is NIMS important to Industry? ü Is “NIMS” a National or State Accredited Program? Except where otherwise noted, this work was created by Mark Cramer and is licensed under the Creative Commons Attribution 4.0 International License. To view a copy of this license, visit http://creativecommons.org/licenses/by/4.0/ or send a letter to Creative Commons, 444 Castro Street, Suite 900, Mountain View, California, 94041, USA. SC ACCELERATE Page | 1 Version │ Course ID │ Rev 1 2012 SC ACCELERATE MTT 255 Open Text Module 4 INTRODUCTION “CNC Turning Programs” are an arrangement of “Preparation Codes” and “Machining Codes”. These codes are known as G and M codes; they will control the movement of the machine tool to manufacture the parts. All CNC programs start and end with specific commands so the controller will recognize the stage of the process. This section will give detailed program guide lines that must be followed to complete the operation of the CNC lathe. The programs that will be used to generate the parts during this section will include “Roughing” and “Finishing” operations. -
Machining Nickel Alloys
NiDl Nickel Development Institute Machining nickel alloys A Nickel Development Institute Reference Book, Series No 11 008 Table of Contents Acknowledgments ............................................................................................ i Abbreviation key ............................................................................................... i Introduction ...................................................................................................... ii Nickel alloys and machinability ......................................................................1 Basic principles applicable to all machining operations .............................3 Work hardening .....................................................................................3 Choice of cutting tools ...........................................................................3 Lubricants and coolants ........................................................................4 Recommendations for machining ..................................................................5 Turning, boring and grooving ................................................................5 High speed steel tooling ....................................................................5 Carbide tooling ...................................................................................6 Ceramic tooling ..................................................................................7 Insert selection and method of use ....................................................9 Taking -
Saw Blades, Mill Supplies and Services PIPER’S Table of Contents Saw Shop Saw Hammering
PIPER’S Saw Shop 2017-2018 CATALOG Saw Blades, Mill Supplies and Services PIPER’S Table Of Contents Saw Shop saw hammeRing Circular Saw Blades 3 & RepaiR • Simonds ITW Saws • Carbide Saws • Piper Inserted Tooth Saws • Small Diameter IT Saws Saw Bits & Shanks 6 • Steel Saw Bits • Shanks • Chrome Saw Bits • Files • Carbide Saw Bits Saw Grinders 9 • Andrus Grinder • Jockey Grinder • Jones Grinder Bandsaw Blades 10 • Wood-Mizer SilverTip • Lenox Woodmaster C Bandsaw • Simonds Red Streak ReshaRpening Safety Supplies 13 • Ear Plugs • Gloves • Safety Glasses • Aprons Tally & Marking 14 • Tally Sheets, Pencils & Books • Crayon Holders & Marking Sticks • Lumber Crayons • Marking Paint • Paint Sticks • Railroad Chalk RecRown Log & Lumber Rules 15 Bandsaw Cant Hooks, S-irons & Anchorseal 16 wheels • Logrite Tools • S-irons, Log & Flitch Savers • Dixie Industries Tools • Anchorseal Chipper Knives & Parts 18 • Chipper Knives • Chipper Parts • Counter Knives caRBide saw RepaiR Strapping & Strapping Tools 20 & shaRpening • Steel Strapping • Polypropylene Strapping • Polyester Strapping • Strapping Tools Abrasives 24 • Filing Room • Jockey, Andrus & Arsaw Wheels • Knife Grinding Wheels • Diamond Wheels knife shaRpening Piper Equipment 26 • Piper Blower • Piper Log Turner • Piper Chopper • Piper Knife Grinder 2 800.845.6075 7:00a.m. to 3:30p.m. Monday Through Friday Circular Head Saws PIPER’S PIPER’S Saw Shop Saw Shop We have a long history of making inserted tooth saw blades and have been manufacturing them since 1991. More recently, we expanded on this by offering large diameter inserted tooth blades and now have hundreds of customers using these blades everyday. Our blades are custom made to order, with the type of teeth & shanks you order and hammered for your Piper Inserted Tooth Saw mill. -
Examination of Material Removal Process in Honing
ACTA TEHNICA CORVINIENSIS – Bulletin of Engineering Tome VII [2014] Fascicule 3 [July – September] ISSN: 2067 – 3809 1. Ottó SZABÓ EXAMINATION OF MATERIAL REMOVAL PROCESS IN HONING 1. University of Miskolc, Institute of Manufacturing Science, HUNGARY Abstract: The paper examines the possibilities of increasing of material removal rate of honing in case of use of superhard tools. Tool having superhard grains significantly increases performance of chip removal, technological process becomes more stable and the increase of tool life is meaningful. The author experimentally examined the effects of increase of grain size, cutting speed, tool pressure on changing of cutting time. The result of this is a two stage honing, in which the first stage assures removing of increased allowance, and the second stage is the final or fine stage which assures the realization of the prescribed accuracy and surface roughness. Keywords: superhard tools, chip removal, honing, grain size, cutting speed, tool pressure, cutting time INTRODUCTION Rmax.e is the maximum value of surface roughness Precision or finish machining procedures of high made by careful cutting operation before honing. accuracy and good surface quality are used in The obtainable average roughness is Ra = 0,09- automative industry (e.g. bores of cylinder and 0,02 µm. winch), bearing industry and in mass production Pre-honing, executed in between the finish or fine of hidraulic elements. honing and the previous machining operation, of The most frequent finish machining procedures of course, applies that type of tool and technological bores are: fine turning, fine drilling, broaching, parameter, by which larger volume of material, and reaming, fine grinding, honing (superfinishing), allowance can be removed.