Petroleum Reservoir Simulation Using 3-D Finite Element Method with Parallel Implementation
Total Page:16
File Type:pdf, Size:1020Kb
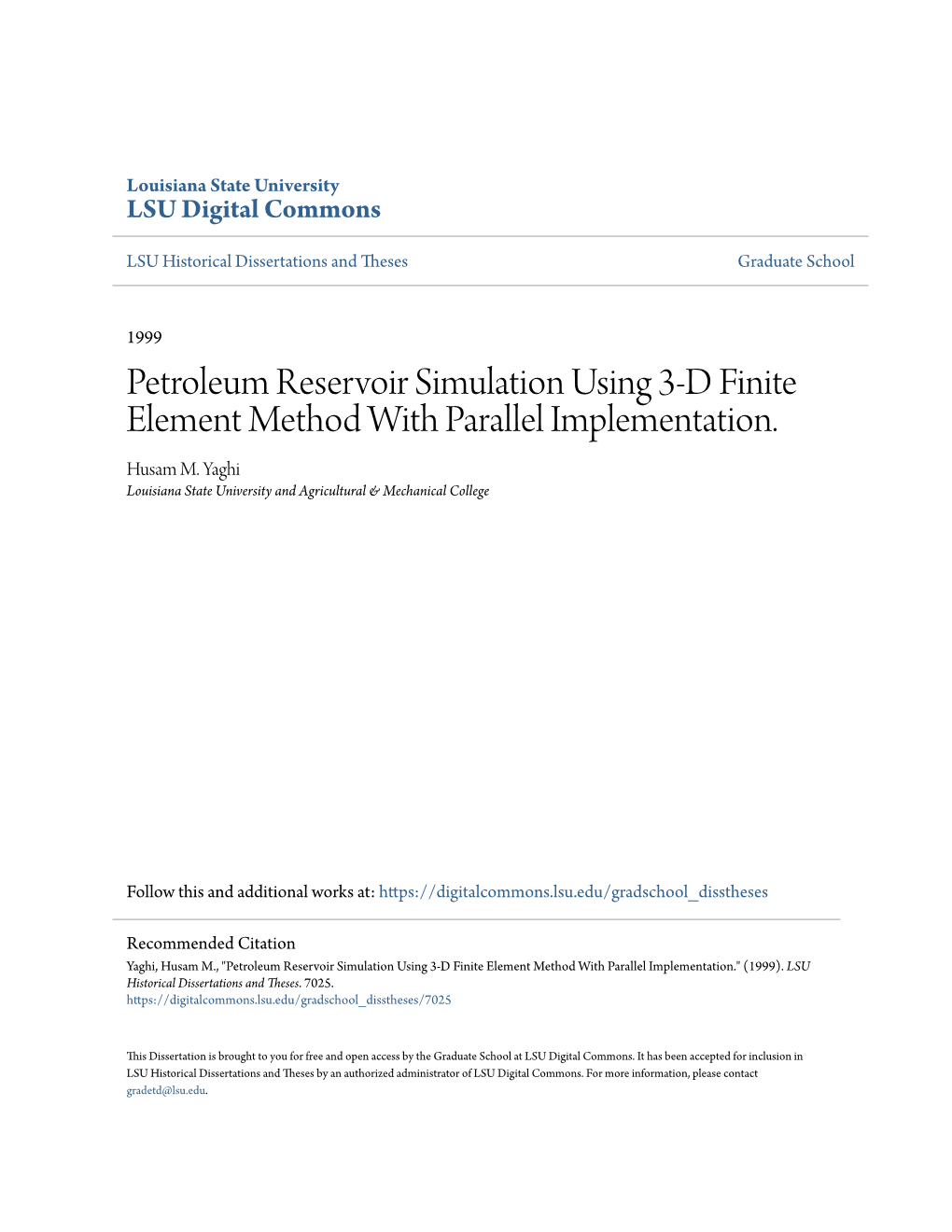
Load more
Recommended publications
-
The Open Petroleum Engineering Journal
1874-8341/19 Send Orders for Reprints to [email protected] 1 The Open Petroleum Engineering Journal Content list available at: https://openpetroleumengineeringjournal.com RESEARCH ARTICLE Analysis of Spatial Distribution Pattern of Reservoir Petrophysical Properties for Horizontal Well Performance Evaluation-A Case Study of Reservoir X Aidoo Borsah Abraham1,*, Annan Boah Evans1 and Brantson Eric Thompson2 1Oil and Gas Engineering Department, School of Engineering, All Nations University College, Koforidua, Ghana 2Petroleum Engineering Department, Faculty of Mineral Resources Technology, University of Mines and Technology, Tarkwa, Ghana Abstract: Introduction: Building a large number of static models to analyze reservoir performance is vital in reservoir development planning. For the purpose of maximizing oil recovery, reservoir behavior must be modelled properly to predict its performance. This requires the study of the variation of the reservoir petrophysical properties as a function of spatial location. Methods: In recent times, the method used to analyze reservoir behavior is the use of reservoir simulation. Hence, this study seeks to analyze the spatial distribution pattern of reservoir petrophysical properties such as porosity, permeability, thickness, saturation and ascertain its effect on cumulative oil production. Geostatistical techniques were used to distribute the petrophysical properties in building a 2D static model of the reservoir and construction of dynamic model to analyze reservoir performance. Vertical to horizontal permeability anisotropy ratio affects horizontal wells drilled in the 2D static reservoir. The performance of the horizontal wells appeared to be increasing steadily as kv/kh increases. At kv/kh value of 0.55, a higher cumulative oil production was observed compared to a kv/kh ratio of 0.4, 0.2, and 0.1. -
Reservoir Simulation
Reservoir Simulation NETHERLAND, SEWELL & ASSOCIATES, INC. One of the most respected names in global petroleum consulting Preferred by companies who need reliable results Quality at a competitive price Expertise in Reservoir Simulation Numerical reservoir simulation is a state-of-the- art evaluation tool that includes material balance, fluid flow, reservoir heterogeneity, well interference, wellbore hydraulics, and facility characteristics in its predictions of reservoir performance. Simulation can be a valuable tool to determine the best development plan for a new reservoir or to improve an existing field by understanding historical production behavior. Experience has taught us that in order for reservoir simulation to be a useful evaluation tool, it must be implemented by an experienced, multi-functional team of geoscientists and reservoir engineers. The Reservoir Simulation team at Netherland, Sewell & Associates, Inc. (NSAI) is comprised of experts who have been working with simulation tools for over 15 years and have been evaluating reservoirs around the world for over 20 years. Reservoir Simulation Experts Dave Adams - Reservoir/Simulation Engineer - Dallas Mike Begland - Reservoir/Simulation Engineer - Dallas Chris Tucker - Reservoir/Simulation Engineer - Dallas Derek Newton - Reservoir/Simulation Engineer - Houston Methodology We use black oil and compositional models in our studies, and our experts are proficient with a variety of simulation software applications including Schlumberger Eclipse® and Halliburton Landmark’s VIP®. No job is too large—our history match models have included fields with over 1,200 wells and 80 years of history. Be it a single-well evaluation, a mechanistic model, or a full-field history match, our experts are skilled in all aspects of reservoir simulation. -
ECLIPSE 2012 Reservoir Simulation Software Industry-Reference Simulator
ECLIPSE 2012 Reservoir Simulation Software Industry-reference simulator ECLIPSE* reservoir simulation software provides a complete and robust upscaling, history match analysis, uncertainty and sensitivity analysis, set of numerical solutions for fast and accurate prediction of dynamic well path and completion design, and design optimization of well behavior—for all types of reservoirs and degrees of complexity, including locations, completions, and reservoir recovery methods. structure, geology, fluids, and development schemes. Blackoil simulation The ECLIPSE industry-reference simulator covers the entire spectrum The ECLIPSE Blackoil simulator supports three-phase, 3D reservoir of reservoir simulation, including black-oil, compositional, and thermal simulation with extensive well controls, field operations planning, and finite-volume reservoir simulation, as well as ECLIPSE FrontSim comprehensive enhanced oil recovery (EOR) schemes. streamline reservoir simulation capabilities. With a wide range of add-on options—such as coal and shale gas, enhanced oil recovery, advanced Compositional simulation wells, and surface networks—you can tailor the simulator capabilities, When modeling multicomponent hydrocarbon flow, the ECLIPSE enhancing the scope of your reservoir simulation studies. Compositional simulator provides a detailed description of reservoir fluid phase behavior and compositional changes. With their depth and breadth of capabilities, innovative technologies, robustness, speed, parallel scalability, and platform coverage, ECLIPSE -
Reservoir Simulation for Strategic Decisions Simulation for Strategically Sound Economic Decisions
Reservoir Simulation for Strategic Decisions Simulation for Strategically Sound Economic Decisions E&P companies are increasingly making better investment decisions for costs can run into the millions of dollars, Ryder Scott reservoir models field development by using reservoir simulation. These built-for-purpose models pay for themselves again and again. help you devise development or operational strategies to maximize recovery and profit. Your objective may be to develop behind-pipe reserves, identify infill- Clients using Ryder Scott reservoir models avoid drilling opportunities, optimize a pressure maintenance program or determine over-development and over-drilling. They put efficient well spacing. Or you may have other goals, such as evaluating their projects on the fast track, capture changes to processing facilities or improving gas-storage operations. What- more reserves per well, increase ever the case, reviewing model runs leads to better decisions by helping predict field efficiency, boost ultimate complex reservoir behavior and field performance under various drilling and recoveries and improve operating scenarios. overall economics. Typically, a simulation study guides and, in some cases, limits development activities that cost far more than the simulation itself. Since drilling and completion Reviewing model runs leads to better decisions by helping predict complex reservoir behavior and field performance. The Utility of the Simulation Tool A reservoir simulation model is a tool that helps E&P companies make informed business decisions regarding oil and gas reserves estimates, reservoir management, reservoir performance, process design and strategic planning. Nearly every type of field-production scenario can be modeled. Ryder Scott constructs and executes models to predict the performance of straight, horizontal and directional wells, well patterns, sectors of fields, entire fields and wellbore tubulars linked to the surface. -
Techniques for Modeling Complex Reservoirs and Advanced Wells
TECHNIQUES FOR MODELING COMPLEX RESERVOIRS AND ADVANCED WELLS A DISSERTATION SUBMITTED TO THE DEPARTMENT OF ENERGY RESOURCES ENGINEERING AND THE COMMITTEE ON GRADUATE STUDIES OF STANFORD UNIVERSITY IN PARTIAL FULFILLMENT OF THE REQUIREMENTS FOR THE DEGREE OF DOCTOR OF PHILOSOPHY Yuanlin Jiang December 2007 °c Copyright by Yuanlin Jiang 2008 All Rights Reserved ii I certify that I have read this dissertation and that, in my opinion, it is fully adequate in scope and quality as a dissertation for the degree of Doctor of Philosophy. Dr. Hamdi Tchelepi Principal Advisor I certify that I have read this dissertation and that, in my opinion, it is fully adequate in scope and quality as a dissertation for the degree of Doctor of Philosophy. Dr. Khalid Aziz Advisor I certify that I have read this dissertation and that, in my opinion, it is fully adequate in scope and quality as a dissertation for the degree of Doctor of Philosophy. Dr. Roland Horne Approved for the University Committee on Graduate Studies. iii Abstract The development of a general-purpose reservoir simulation framework for coupled systems of unstructured reservoir models and advanced wells is the subject of this dissertation. Stanford's General Purpose Research Simulator (GPRS) serves as the base for the new framework. In this work, we made signi¯cant contributions to GPRS, in terms of architectural design, extensibility, computational e±ciency, and new advanced well modeling capabilities. We designed and implemented a new architectural framework, in which the fa- cilities (man-made) model is treated as a separate component and promoted to the same level as the reservoir (natural) component. -
Subsea Sampling Hardware
In-line Subsea Sampling: Non-disruptive Subsea Intervention Technology for Production Assurance Hua Guan, Principal Engineer, OneSubsea Phillip Rice, Sales&Commercial Manager, OneSubsea February 8, Subsea Expo 2018, Aberdeen Presentation Outline • Production assurance challenges along the fluid journey • Fluid PVT and importance of representative samples • Subsea sampling system • Subsea sampling demo • Project example – subsea sampling application for scale squeeze optimization 2 Complexity and Multi-disciplines in Subsea Production Topside Production Forecasting, Process Operations Risks, and Sim. & Opt. Sensitivities The Fluid Journey Riser & Fluid Steady Subsea SS MP Flow Processing Production Transient Flowline Interv. Analysis & State MP Archi- Surveill. Metering / Boosting chemicals MP Monitoring Modelling Flow Sim. Flow Sim. tecture Solids Prec. & Depos. Wellbore Sim. PVT Completion Sampling Inflow Performance 3 Production Assurance Challenges along the Fluid Journey Deposition management Liquid management Pressure management 4 Production Assurance Challenges along the Fluid Journey 5 Fluid PVT and Importance of Representative Samples Reservoir P&T Start Hydrate Curve Hydrate Pressure Reservoir P&T Long-Term Facility Look-a-head Temperature 6 Subsea Industry Trends Increasing production assurance challenges + high intervention costs 7 Drivers for Representative Sampling Almost all technical and economic reservoir studies require an accurate and reliable understanding of the reservoir fluids. 8 Drivers for Representative Sampling -
2013 Annual Report Schlumberger Limited Profile
2013 Annual Report Schlumberger Limited Profile Schlumberger is the world’s leading supplier of technology, Throughout this report you integrated project management, and information solutions to will see QR Codes similar to the international oil and gas exploration and production industry. the one to the left. Scan the The company employs 123,000 people of over 140 nationalities codes with your mobile working in approximately 85 countries. Schlumberger supplies device to view the multimedia a wide range of products and services, from seismic acquisition version of this report. and processing; drill bits and drilling fluids; directional drilling and drilling services; formation evaluation and well testing; to well cementing and stimulation; artificial lift, well completions and well intervention; and consulting, software, and information management. Financial Performance (Stated in millions, except per-share amounts) Year ended December 31 2013 2012 2011 Revenue $ 45,266 $ 41,731 $ 36,579 Income from continuing operations $ 6,801 $ 5,230 $ 4,516 Diluted earnings-per-share from continuing operations $ 5.10 $ 3.91 $ 3.32 Cash dividends per share $ 1.25 $ 1.10 $ 1.00 Net debt $ 4,443 $ 5,111 $ 4,850 Safety and Environmental Performance Combined Lost Time Injury Frequency (CLTIF)— Industry Recognized (OGP) † 1.2 1.3 1.4 Auto Accident Rate mile (AARm)—Industry Recognized † 0.24 0.36 0.39 Tonnes of CO 2 per employee per year 15 17 15 Total Scope 1 CO 2 emissions (million tons) 1.8 2.0 1.7 † Safety performance figures for 2011 do not include data from Smith International and Geoservices. In This Report Inside Front Cover Financial Performance Front Cover Safety and Environmental Performance Field Test Coordinator Jonathan Leonard and Senior Mechanical Technician Stacy Johnson handle a Saturn* Page 1 Letter to Shareholders 3D radial probe on a test rig in Sugar Land, Texas, USA. -
Dr. Talal D. Gamadi Texas Tech University (806) 4489495 [email protected]
Dr. Talal D. Gamadi Texas Tech University (806) 4489495 [email protected] Education and Post Graduate Training PhD, Texas Tech University, 2014. Major: Petroleum Engineering MS, University of Louisiana at Lafayette, 2011. Major: Master of Engineering Science, Petroleum Engineering Academic and Professional Experience Assistant Professor, Bob L. Herd Department of Petroleum Engineering( 2016- present) Instructor, Petroleum Dept., Texas Tech University. (August 2014 - 2016). Teaching Assistant, College of engineering, Texas Tech University. (Fall 2012 – spring 2014) Reservoir engineer, field engineer, Libyan National Oil Corporation (May 2006 – May 2008) TEACHING Courses Taught Undergraduate Courses ENGR 1106, Math Fundamentals for Engineers. ENGR1315, Introduction to Engineering PETR 1305, Engineering Analysis I, PETR 2322, Petroleum Methods, PETR 3302, reservoir fluids properties PETR 3306, Reservoir Engineering, PETR 4000, Special Studies in Petroleum Engineering, PETR 4121, Petroleum Design I, II, PETR 4319, Simulation Methods, PETR 4331, Special Problems in Petroleum Engineering, Graduate Courses PETR5329, Advanced Core Analysis PETR 5323, Advanced Phase Behavior, PETR 5383, Reservoir Engineering Fundamentals, PETR5328, Advanced Gas Production Engineering PETR5316, Advanced Production Engineering Teaching Awards and Honors Most Influential Professor, Students. (Spring 2015). Most Influential Professor, Students. (Spring 2016). Research Interests • Enhanced Oil Recovery EOR applications in conventional and unconventional reservoirs -
Identifying Reservoir Opportunities Using Automated Well Selection and Ranking
® Originally appeared in World Oil OCTOBER 2020 issue, pgs 37-41. Posted with permission. RESERVOIR MANAGEMENT Identifying reservoir opportunities using automated well selection and ranking Effective reservoir The technology automates steps, typical- components, including: management requires ly performed during the selection of field • Engineering analytics - combining multiple development candidates, by applying ad- Automatically performs decline engineering/geoscience vanced algorithms and AI/ML to multi- curve analysis, using AI-based disciplines to identify disciplinary datasets, enabling teams to event detection and type rapidly review alternatives by leveraging curve generation; allocates improvement opportunities. cloud computing.1-3 This cloud-native production per zone for each To optimize analysis, an platform enables all members of an asset well, using a series of data- AI-powered management team to collaboratively assess field devel- driven techniques, integrating platform was developed that opment possibilities. production, completion, rock and delivers faster, more accurate It also integrates disparate sources fluid properties, and PLT/ILT results to maximize asset of data, including well logs, 3D reser- information. voir models, production history, and • Remaining pay identification - value. completion data, breaking down existing Identifies uncontacted pay with silos and opening new cross-functional many distinguishing features, workflows. Many steps are involved in such as pay connectivity analysis, ŝ HAMED DARABI, WASSIM BENHALLAM, generating a field development catalog, automatic baffle identification, JOHANNA SMITH, AMIR SALEHI and DAVID including identification of bypassed pay, perforation strategy and standoff CASTINEIRA, Quantum Reservoir Impact; drainage analysis, mapping of geo-en- constraints. EMMANUEL GRINGARTEN, Emerson gineering attributes to assess geological • Drainage analysis - Estimates Automation Solutions risks, and estimation of initial produc- areas that have been drained by tion potential. -
Halliburton Word Document
WHITE PAPER Digital Twin Implementation for Integrated Production & Reservoir Management WHITE PAPER | Digital Twin Implementation for Integrated Production & Reservoir Management Table of Contents Introduction .................................................................................................................................................... 2 Leveraging a Digital Twin for Integrated Reservoir and Production Management .................................. 3 Digital Twin for Production............................................................................................................................. 4 Condition & Performance Monitoring ....................................................................................................... 5 Well Design and Performance Optimization ............................................................................................ 6 Surface Network Operational Optimization .............................................................................................. 7 Integrated Asset Model (IAM) ................................................................................................................... 8 Digital Twin for Reservoir .............................................................................................................................. 9 Collaboration Between Production Operations & Field Development ...................................................... 9 Elements of the Overall Solution ........................................................................................................... -
Fully Compositional Multi-Scale Reservoir Simulation of Various CO2 Sequestration Mechanisms
University of Rhode Island DigitalCommons@URI Chemical Engineering Faculty Publications Chemical Engineering 2017 Fully Compositional Multi-Scale Reservoir Simulation of Various CO2 Sequestration Mechanisms Denis V. Voskov Heath Henley University of Rhode Island Angelo Lucia University of Rhode Island, [email protected] Follow this and additional works at: https://digitalcommons.uri.edu/che_facpubs Part of the Chemical Engineering Commons The University of Rhode Island Faculty have made this article openly available. Please let us know how Open Access to this research benefits you. This is a pre-publication author manuscript of the final, published article. Terms of Use This article is made available under the terms and conditions applicable towards Open Access Policy Articles, as set forth in our Terms of Use. Citation/Publisher Attribution Voskov, D. V., Henley, H., & Lucia, L. (2017). Fully Compositional Multi-Scale Reservoir Simulation of Various CO2 Sequestration Mechanisms. Computers & Chemical Engineering, 96(4), 183-195. doi: 10.1016/j.compchemeng.2016.09.021 Available at: http://dx.doi.org/10.1016/j.compchemeng.2016.09.021 This Article is brought to you for free and open access by the Chemical Engineering at DigitalCommons@URI. It has been accepted for inclusion in Chemical Engineering Faculty Publications by an authorized administrator of DigitalCommons@URI. For more information, please contact [email protected]. Fully Compositional Multi-Scale Reservoir Simulation of Various CO2 Sequestration Mechanisms Denis V. Voskov Delft University of Technology Department of Geoscience & Engineering Stevinweg 1, 2628 CN Delft, NL Heath Henley & Angelo Lucia* Department of Chemical Engineering University of Rhode Island Kingston, RI 02882 USA * Corresponding author: Tel: +1 401 874-2814; Email: [email protected] 1 Abstract A multi-scale reservoir simulation framework for large-scale, multiphase flow with mineral precipitation in CO2-brine systems is proposed. -
Eos Modeling and Reservoir Simulation Study of Bakken Gas Injection Improved Oil Recovery in the Elm Coulee Field, Montana
EOS MODELING AND RESERVOIR SIMULATION STUDY OF BAKKEN GAS INJECTION IMPROVED OIL RECOVERY IN THE ELM COULEE FIELD, MONTANA by Wanli Pu © Copyright by Wanli Pu, 2013 All Rights Reserved A thesis submitted to the Faculty and the Board of Trustees of the Colorado School of Mines in partial fulfillment of the requirements for the degree of Master of Science (Petroleum Engineering). Golden, Colorado Date Signed: Wanli Pu Signed: Dr. B. Todd Hoffman Thesis Advisor Golden, Colorado Date Signed: Dr. William Fleckenstein Professor and Head Department of Petroleum Engineering ii ABSTRACT The Bakken Formation in the Williston Basin is one of the most productive liquid- rich unconventional plays. The Bakken Formation is divided into three members, and the Middle Bakken Member is the primary target for horizontal wellbore landing and hydraulic fracturing because of its better rock properties. Even with this new technology, the primary recovery factor is believed to be only around 10%. This study is to evaluate various gas injection EOR methods to try to improve on that low recovery factor of 10%. In this study, the Elm Coulee Oil Field in the Williston Basin was selected as the area of interest. Static reservoir models featuring the rock property heterogeneity of the Middle Bakken Member were built, and fluid property models were built based on Bakken reservoir fluid sample PVT data. By employing both compositional model simulation and Todd-Longstaff solvent model simulation methods, miscible gas injections were simulated and the simulations speculated that oil recovery increased by 10% to 20% of OOIP in 30 years. The compositional simulations yielded lower oil recovery compared to the solvent model simulations.