Experimental Clarification of the RWGS Reaction Effect in H2O/CO2
Total Page:16
File Type:pdf, Size:1020Kb
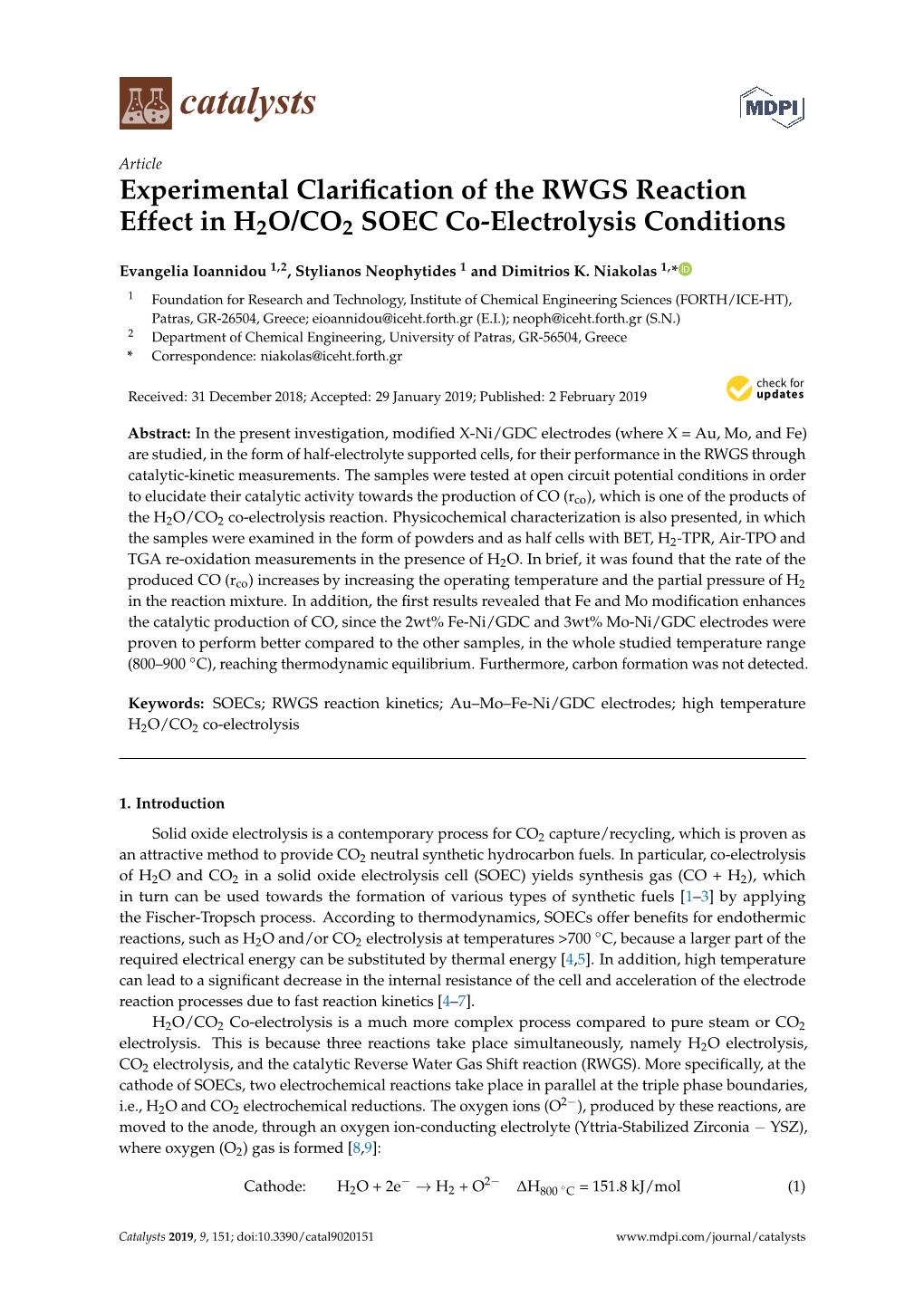
Load more
Recommended publications
-
Gas-Phase Boudouard Disproportionation Reaction Between Highly Vibrationally Excited CO Molecules
Chemical Physics 330 (2006) 506–514 www.elsevier.com/locate/chemphys Gas-phase Boudouard disproportionation reaction between highly vibrationally excited CO molecules Katherine A. Essenhigh, Yurii G. Utkin, Chad Bernard, Igor V. Adamovich *, J. William Rich Nonequilibrium Thermodynamics Laboratories, Department of Mechanical Engineering, The Ohio State University, Columbus, OH 43202, USA Received 3 September 2006; accepted 21 September 2006 Available online 30 September 2006 Abstract The gas-phase Boudouard disproportionation reaction between two highly vibrationally excited CO molecules in the ground elec- tronic state has been studied in optically pumped CO. The gas temperature and the CO vibrational level populations in the reaction region, as well as the CO2 concentration in the reaction products have been measured using FTIR emission and absorption spectroscopy. The results demonstrate that CO2 formation in the optically pumped reactor is controlled by the high CO vibrational level populations, rather than by CO partial pressure or by flow temperature. The disproportionation reaction rate constant has been determined from the measured CO2 and CO concentrations using the perfectly stirred reactor (PSR) approximation. The reaction activation energy, 11.6 ± 0.3 eV (close to the CO dissociation energy of 11.09 eV), was evaluated using the statistical transition state theory, by comparing the dependence of the measured CO2 concentration and of the calculated reaction rate constant on helium partial pressure. The dispro- À18 3 portionation reaction rate constant measured at the present conditions is kf =(9±4)· 10 cm /s. The reaction rate constants obtained from the experimental measurements and from the transition state theory are in good agreement. -
Reactions on Carbon Anodes in Aluminium Electrolysis
EI-NO--1052 09905089 Trygve Eidet .. -~,J: Reactions on carbon anodes in aluminium electrolysis of ntio M/W 2 4 S99 &STI universitet teknisk-naturvitenskapelige Norges DISCLAIMER Portions of this document may be illegible in electronic image products. Images are produced from the best available original document. Reactions On Carbon A nodes In A luminium Electrolysis . By Trygve Eidet Thesis submitted in partial fulfillment of the requirements for the degree Doktor Ingeni0r. The Norwegian University of Technology and Science Department of Electrochemistry October 1997 UST OF SYMBOLS -111- LIST OF SYMBOLS SYMBOL DESCRIPTION UNIT v Stoichiometric number aa Charge transfer coefficient (anodic) ac Charge transfer coefficient (cathodic) t] Overpotential [V] 0 Phase shift [°] cr Warburg coefficient [Q/slc] AG° Standard Gibbs energy change of reaction [kJ/mol] ARd Dust generation [wt%] ARt Total bumoff [wt%] Pa Symmetry factor (anodic) [0.5] Pc Symmetry factor (cathodic) [0.5] 6 Electrode coverage (fraction of 1) a> Angular frequency [2n Hz] a Activity a Regression coefficient a Tafel constant [V] A Apparent surface area [cm2] A Preexponential factor Ad apparent, geometric area [cm2] A, “True” electrode area [cm2] b Tafel slope [V/dec.] BAD Baked apparent density, anode [kg/m3] BC Baked carbon c Concentration [mol/dm 3] ca Surface concentration [mol/cm 2] C(O) Chemisorbed, fixed, oxygen atom C(G)„ Chemisorbed, mobile, oxygen atom C(OJ Chemisorbed, fixed, molecular oxygen C(OJ. Chemisorbed, mobile, molecular oxygen ^-"ads Capacitance due to adsorbed -
In Situ TEM Observation of the Boudouard Reaction: Multi-Layered Graphene Formation from CO on Cobalt Nanoparticles at Atmospheric Pressure
Faraday Discussions Cite this: Faraday Discuss.,2017,197,337 View Article Online PAPER View Journal | View Issue In situ TEM observation of the Boudouard reaction: multi-layered graphene formation from CO on cobalt nanoparticles at atmospheric pressure G. Marien Bremmer,a Eirini Zacharaki,b Anja O. Sjastad,˚ b Violeta Navarro,c Joost W. M. Frenkend and Patricia J. Kooyman*e Received 5th September 2016, Accepted 6th October 2016 DOI: 10.1039/c6fd00185h Creative Commons Attribution 3.0 Unported Licence. Using a MEMS nanoreactor in combination with a specially designed in situ Transmission Electron Microscope (TEM) holder and gas supply system, we imaged the formation of multiple layers of graphene encapsulating a cobalt nanoparticle, at 1 bar CO : N2 (1 : 1) and 500 C. The cobalt nanoparticle was imaged live in a TEM during the Boudouard reaction. The in situ/operando TEM studies give insight into the behaviour of the catalyst at the nanometer-scale, under industrially relevant conditions. When switching from Fischer–Tropsch syngas conditions (CO : H2 :N2 1 : 2 : 3 at 1 bar) to CO-rich conditions (CO : N2 1 : 1 at 1 bar), we observed the formation of multi-layered graphene on Co nanoparticles at 500 C. Due to the high temperature, the surface of the Co This article is licensed under a nanoparticles facilitated the Boudouard reaction, causing CO dissociation and the formation of layers of graphene. After the formation of the first patches of graphene at the surface of the nanoparticle, more and more layers grew over the course of about Open Access Article. Published on 06 October 2016. -
Chm415 Course Title
NATIONAL OPEN UNIVERSITY OF NIGERIA DEPARTMENT OF PURE AND APPLIED SCIENCE FACULTY OF SCIENCES COURSE CODE: CHM415 COURSE TITLE: INDUSTRIAL CHEMICAL TECHNOLOGY II CHEM 415 INDUSTRIAL CHEMICAL TECHNOLOGY 2 CHM415 INDUSTRIAL CHEMICAL TECHNOLOGY II COURSE TEAM: Prof. John Nduka :- Course writter Nnamdi Azikiwe University Akwa Prof.: Ojeyemi Matthew Olabemiwo- Course Editor Ladoke Akintola University of Technology (LAUTECH), Ogbomoso Dr. Emeka C. Ogoko Head of Department Pure and Applied Science, National Open University of Nigeria 2 National Open University of Nigeria Headquarters Plot 91, Cadastral Zone, Nnamdi Azikiwe Expressway, Jabi - Abuja National Open University of Nigeria Liaison Office 14/16 Ahmadu Bello Way Victoria Island, Lagos Email: [email protected] URL: www.nou.edu.ng Published by National Open University of Nigeria Printed 2018 ISBN: 3 CHEM 415 INDUSTRIAL CHEMICAL TECHNOLOGY 2 4 CONTENT PAGE Introduction - - - - - - - - - - 5 Course Description - - - - - - - - - 7 What you will Learn in this Course - - - - - - - 7 Course Objectives - - - - - - - - - 7 Working through this Course - - - - - - - - 8 Course Materials - - - - - - - - - 8 Study Units - - - - - - - - - - 8 Textbooks and References - - - - - - - - 10 Assessment - - - - - - - - - - 10 Summary - - - - - - - - - - 10 INTRODUCTION 5 CHEM 415 INDUSTRIAL CHEMICAL TECHNOLOGY 2 Industrial chemistry deals with the chemical unit operation and process in manufacturing industry. Chemical process technology has a variety of branches that tilted to development. Processes such as distillation, heat transfer, fluid flow, mass transfer etc, In the stage of product and process development several discipline were integrated including kinetics and catalysis, reactor technology, unit operation, process technology, process control etc. The chemical industry involves creation of wealth/value adding by converting raw materials like salt, oil and limestone to consumable products. -
The Boudouard–Bell Reaction Analysis Under High Pressure Conditions
J Therm Anal Calorim (2012) 110:93–102 DOI 10.1007/s10973-012-2334-2 The Boudouard–Bell reaction analysis under high pressure conditions Andrzej Mianowski • Zbigniew Robak • Martyna Tomaszewicz • Sławomir Stelmach CEEC-TAC1 Conference Special Issue Ó The Author(s) 2012. This article is published with open access at Springerlink.com Abstract A new method for the measurement of solid b1, b2, b3 Constants in L–H Eq. 8 related with kinetic fuel reactivity towards carbon dioxide has been developed. constants This new method takes into account high-pressure and B, B1, B2 Constants in Eqs. 12–13, 15, dimensionless -1 -1 temperature effects. Three devolatilized carbonaceous C0 Constant in Eqs. 24, 25,K s materials have been used in experiments: chars derived C, C1, C2 Constants from lignite, bituminous coal and blast furnace coke. Pro- [CO2], [CO] Molar fractions of CO2 and CO, respec- cesses were carried out at temperatures of 800, 850 and tively, 0 B [CO2] B 1, 0 B [CO] B 1, 900 °C and pressures of 1.52, 2.5 and 3.4 MPa. Analysis of [CO]m Maximum obtained molar fraction of CO, the product gas composition was carried out with the 0 \ [CO] B 1 maximum degree of conversion of CO2 (am) proposed as a DFE Distance from thermodynamic equilibrium, representative reactivity parameter. Arrhenius and Eyring dimensionless relationships have been analyzed, and values of the acti- E Activation energy, J mol-1 vation energy and activation volume have been calculated. k Rate coefficient, s-1, indexed constants corresponds with adequate equations Keywords Boudouard–Bell reaction Á CO2 Á Gasification kg Rate coefficient acc. -
Mechanism of Enhanced Performance on a Hybrid Direct Carbon Fuel Cell
Mechanism of enhanced performance on a hybrid direct carbon fuel cell using sawdust biofuels Shuangbin Li1, 2, Cairong Jiang3, Juan Liu1, Haoliang Tao1, Xie Meng1, Paul Connor2, Jianing Hui 2, Shaorong Wang4, *, Jianjun Ma3, and John T. S. Irvine2, * 1 CAS Key Laboratory of Materials for Energy Conversion, Shanghai Institute of Ceramics, Chinese Academy of Sciences (SICCAS), China 2 School of Chemistry, University of St Andrews, KY16 9ST, United Kingdom 3 Department of Materials Science and Engineering, Sichuan University of Science and Engineering, China 4 School of Chemical Engineering & Technology, China University of mining and Technology, China Abstract: Biomass is expected to play a significant role in power generation in the near future. With the uprising of carbon fuel cells, hybrid direct carbon fuel cells (HDCFCs) show its intrinsic and incomparable advantages in the generation of clean energy with higher efficiency. In this study, two types of biomass treated by physical sieve and pyrolysis from raw sawdust are investigated on an anode-supported HDCFC. The structure and thermal analysis indicate that raw sawdust has well-formed cellulose I phase with very low ash. Electrochemical performance behaviors for sieved and pyrolyzed sawdust combined with various weight ratios of carbonate are compared in N2 and CO2 purge gas. The results show that the power output of sieved sawdust with -2 789 mWcm is superior to that of pyrolyzed sawdust in CO2 flowing, as well as in N2 flowing. The anode reaction mechanism for the discrepancy of two fuels is explained and the emphasis is also placed on the modified oxygen-reduction cycle mechanism of catalytic effects of Li2CO3 and K2CO3 salts in promoting cell performance. -
Study of Promoters to Reverse Boudouard Reaction Under Regeneration Step Conditions of FCC Process
Study of promoters to Reverse Boudouard reaction under regeneration step conditions of FCC process Sérgio Pereira1*, Filipa Ribeiro1, Marcelo Maciel Pereira2 1*[email protected] 1Instituto Superior Técnico, Universidade de Lisboa, Av. Rovisco Pais, 1049-001 Lisboa, Portugal 2Instituto de Química, Universidade Federal do Rio de Janeiro, Av. Athos da Silveira Ramos, Rio de Janeiro, RJ, Brasil ABSTRACT The fluid cracking catalytic process (FCC) contributes with about 30% of the total CO2 emissions in a refinery. The possibility to react CO2 and coke (Reverse Boudouard reaction) during the spent catalyst regeneration using a rich atmosphere in CO2 and O2, instead of air, can mitigate CO2 emissions and, simultaneously, produce CO for sequential uses. In this work, alumina catalysts modified by both alkali and alkaline earth metals in presence or not of vanadium were prepared, with the purpose of finding promoters for this reaction. Therefore, it was shown that this goal was achieved by an alumina catalyst modified with lithium and vanadium under normal regeneration temperatures, i.e. in the range of 690 to 720ºC, with the best efficiency among all catalysts, verifying a great synergy between lithium and vanadium. This synergy is noticed by comparing the values of average conversion during the first five minutes of reaction in 13 CO2/O2/He atmosphere of Li-V/Al2O3 and Li/Al2O3. At 720ºC, the first catalyst attained a value of 39% while the second attained only 6%. The first formed product was 13CO, followed by 12CO and then 12 12 by CO2. The CO was formed by both RB reaction and by burning the coke with O2. -
Cobalt-Based Fischer–Tropsch Synthesis: a Kinetic Evaluation of Metal–Support Interactions Using an Inverse Model System
catalysts Article Cobalt-Based Fischer–Tropsch Synthesis: A Kinetic Evaluation of Metal–Support Interactions Using an Inverse Model System Anna P. Petersen, Michael Claeys, Patricia J. Kooyman and Eric van Steen * DST-NRF Centre of excellence in catalysis: c*change, Catalysis Institute, Department of Chemical Engineering, University of Cape Town, Private Bag X3, Rondebosch 7701, South Africa; [email protected] (A.P.P.); [email protected] (M.C.); [email protected] (P.J.K.) * Correspondence: [email protected] Received: 30 August 2019; Accepted: 21 September 2019; Published: 24 September 2019 Abstract: Metal–support interactions in the cobalt–alumina system are evaluated using an inverse model system generated by impregnating Co3O4 with a solution of aluminum sec-butoxide in n-hexane. This results in the formation of nano-sized alumina islands on the surface of cobalt oxide. The activated model systems were kinetically evaluated for their activity and selectivity in the Fischer–Tropsch synthesis under industrially relevant conditions (220 ◦C, 20 bar). The kinetic measurements were complemented by H2-chemisorption, CO-TPR, and pyridine TPD. It is shown that the introduction of aluminum in the model system results in the formation of strong acid sites and enhanced CO dissociation, as evidenced in the CO-TPR. The incorporation of aluminum in the model systems led to a strong increase in the activity factor per surface atom of cobalt in the rate expression proposed by Botes et al. (2009). However, the addition of aluminum also resulted in a strong increase in the kinetic inhibition factor. -
TECHNICAL NOTE on BEST AVAILABLE TECHNOLOGIES NOT ENTAILING EXCESSIVE COSTS for HEAVY METAL EMISSIONS from NON-FERROUS INDUSTRIAL PLANTS Final Report - May 1991
I - 2~637t.Pf TECHNICAL NOTE ON BEST AVAILABLE TECHNOLOGIES NOT ENTAILING EXCESSIVE COSTS FOR HEAVY METAL EMISSIONS FROM NON-FERROUS INDUSTRIAL PLANTS Final report - May 1991 *** EUROPEAN This document has been prepared for use within the Commission. It does not necessarily represent the Commission's official position. Cataloguing data can be found at the end of this publication. Luxembourg: Office for Official Publications of the European Communities, 1994 ISBN 92-826-5097-9 0 ECSC-EC-EAEC, Brussels Luxembourg, 1994 Reproduction is authorized, except for commercial purposes, provided the Cn,,.C" ir ...-l,..",..,-A,.-A European Commission Technical Note on Best Available Technologies Not Entailing Excessive Costs for Heavy Metal Emissions from Non-Ferrous Industrial Plants FINAL REPORT May 1991 Document This document has been prepared for use within the Commission. It does not necessarily represent the Coomission's official position. Copyright ECSC-EC-EAEC. Erussel - Luxembourg. 1994 Reproduction is authorized, except for commercial purposes, provided the source is acknowledged. Environmental Consultancy -~ ~ Technical Note on Best Avaliable Technologies Not entailing Excessive Costs €or Heavy Metal Emissions from Non-Ferrous Industrial Plants Editor: K.-H. Zierock FINAL REPORT May 1991 Final Report to etudy contract B 6611-90-6693 CONTENTS PAGE PREFACE 1 PART Ax GENERAL ASPECTS 3 AI Introduction 3 AI1 Legal Provisions of Member States Relevant for Plant Authorisation 3 AI11 Processes and Installations Included in this Technical Note 4 -
To Download Program Book for This Topic in Adobe Acrobat Format
Monday Morning, October 22, 2018 conditions; inappropriate handling and preparation of samples; damage to samples during analysis leading to faulty conclusions; incorrect or Applied Surface Science Division inconsistent quantification and/or spectral interpretation; lack of Room 204 - Session AS-MoM calibration and/or incorrect instrument set up; chemically meaningless fitting of data; inadequate reporting of methods, processes and results. Quantitative Surface Analysis This talk highlights examples of where XPS has been a tool for addressing Moderators: Kateryna Artyushkova, University of New Mexico, Tim reproducibility challenges, show a few examples of problem areas and Nunney, Thermo Fisher Scientific, UK summarize actions that the AVS is undertaking to help address reproducibility issues. 8:20am AS-MoM1 A Fistful of Data: The Good, the Bad and the Ugly of Quantitative Surface Analysis, Alexander Shard, National Physical 9:20am AS-MoM4 Rapid Calculation Method of the Voigt Function for Use Laboratory, UK INVITED in the Analysis of Photoelectron Spectroscopic Data, Peter Sherwood, The properties of surfaces and interfaces govern the performance of most University of Washington manufactured items, from advanced electronic devices, medical devices to The basic shape of a photoelectron peak is Lorentzian, which is modified by packaging materials. The chemical analysis of such surfaces underpins the instrumental and other factors, such as phonon broadening, to give a development of new products with better performance, ensures Gaussian contribution resulting in a peak shape that is a convolution of a consistency in production and identifies the causes of failure. Commonly Gaussian and a Lorentzian peak shape. The use of the correct peak shape is used methods, such as XPS and SIMS, can detect elements and chemical important in the analysis of photoelectron spectroscopic data. -
Boudouard Carbon Deposition on Nickel Cermet Electrodes, Kinetics Of
CHEMICAL ENGINEERING SCIENCE 64(10):2291-2300 15 May 2009 The effect of current density and temperature on the degradation of nickel cermet electrodes by carbon monoxide in solid oxide fuel cells Offer, G. J.*, Brandon, N. P. Department of Earth Science Engineering, Imperial College London, SW7 2BP, UK * corresponding author: [email protected]; tel: +44 (0)20 7594 5018; fax: +44 (0)20 7594 7444 Keywords Accelerated Degradation, Catalysis, Catalyst deactivation, Electrochemistry, Energy, Fuel Cell, Kinetics, Solid Oxide, Thermodynamics 1 Abstract The oxidation of dry Carbon Monoxide (CO) in Intermediate Temperature Solid Oxide Fuel Cells (IT-SOFCs) has been studied using a three electrode assembly. Ni/CGO:CGO:LSCF/CGO three electrode pellet cells at 500, 550 and 600C were exposed to dry carbon monoxide for fixed periods of time, at open circuit and under load at 50 and 100 mA cm-2, in an aggressive test designed to accelerate electrode degradation. It is shown that if the anode is kept under load during exposure to dry CO, degradation in anode performance can be minimised, and that under most conditions the anode showed significant irreversible degradation in performance after -2 subsequent load cycling on dry H2. Only at 500C and at 100 mA cm was the degradation in performance after operation on dry CO and subsequent load cycling on dry H2 within the background degradation rates measured. Where anode performance was compromised, this appeared to be caused by a reduction in the exchange current density for hydrogen oxidation, and the relatively large degradation after load cycling on dry H2 was primarily caused by an increase in the series resistance of the anode. -
Mathematical Model of the Sl/Rn Direct Reduction
MATHEMATICAL MODEL OF THE SL/RN DIRECT REDUCTION PROCESS by V. VENKATESWARAN B.E., Indian Institute of Science, 1972 A THESIS SUBMITTED IN PARTIAL FULFILMENT OF THE REQUIREMENTS FOR THE DEGREE OF MASTER OF APPLIED SCIENCE In the Department of METALLURGY We accept this thesis as conforming to the required standard THE UNIVERSITY OF BRITISH COLUMBIA April 1976 (c) V. Venkateswaran, 1976 In presenting this thesis in partial fulfilment of the requirements for an advanced degree at the University of British Columbia, I agree that the Library shall make it freely available for reference and study. I further agree that permission for extensive copying of this thesis for scholarly purposes may be granted by the Head of my Department or by his representatives. It is understood that copying or publication of this thesis for financial gain shall not be allowed without my written permission. Department of METALLURGY The University of British Columbia 20 75 Wesbrook Place Vancouver, Canada V6T 1W5 ABSTRACT A mathematical model has been developed to predict the operating behaviour of an SL/RN direct reduction kiln from a knowledge of the main process variables. The model is based on steady state principles and is capable of quantita• tively describing the complex chemical reactions in the kiln such as reduction, Boudouard reaction, coal volatilization and combustion in the freeboard together with the mass and heat flows. Output from the model is in the form of axial profiles of gas, solids and wall temperatures, and concentra• tions in both the gas and the solid phases. Results from the model are in good agreement with measurements made on the 100 ton per day pilot kiln at the Steel Company of Canada.