Linear and Non Linear Analysis of Central Crack Propagation in Polyurethane Material - a Comparison
Total Page:16
File Type:pdf, Size:1020Kb
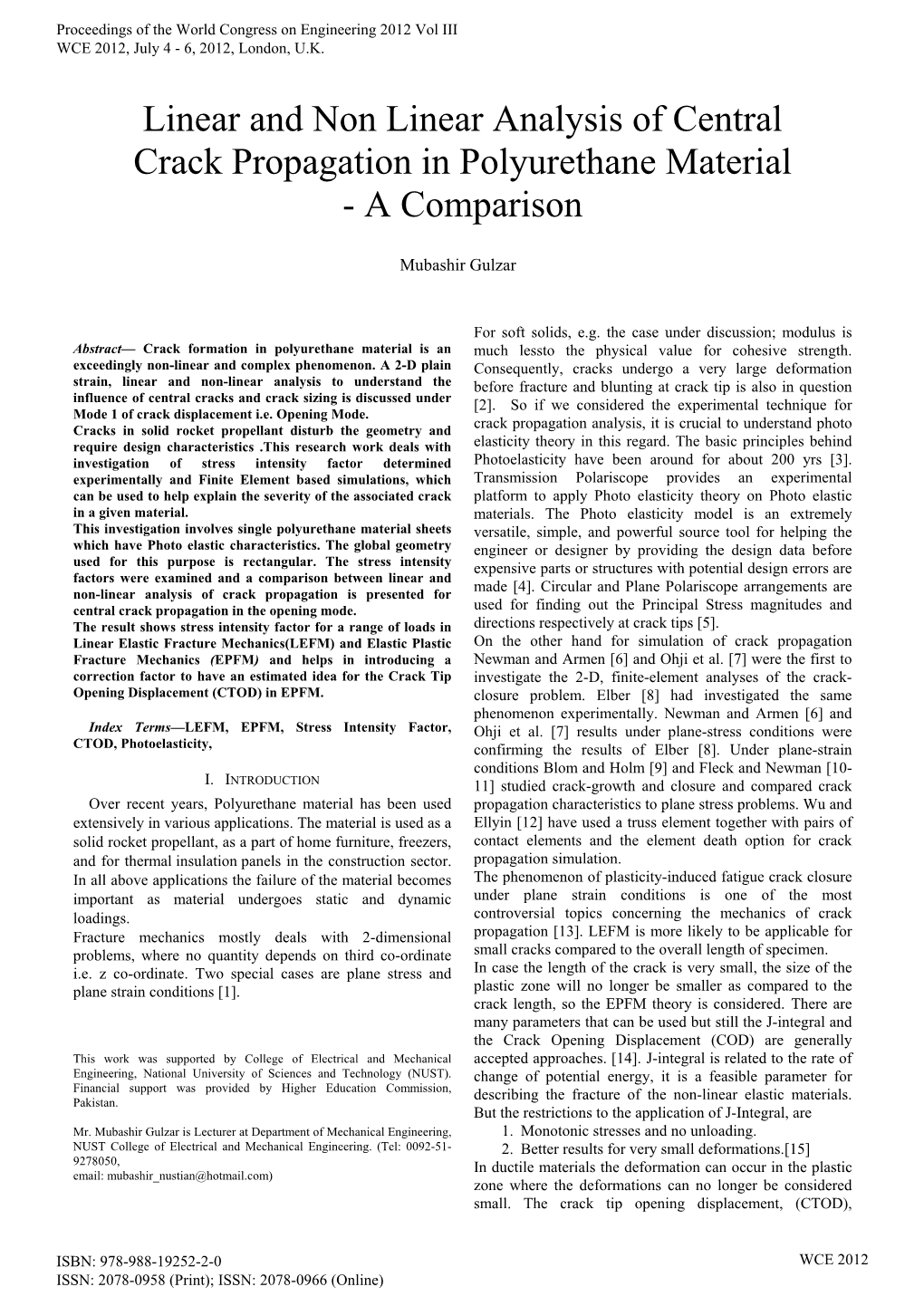
Load more
Recommended publications
-
1 Useful Definitions Or Concepts
ETH Zurich Institute for Mechanical Systems Department of Mechanical and Process Engineering Center of Mechanics Winter 06/07 Nonlinear Continuum Mechanics Exercise 9 Prof. Dr. Sanjay Govindjee 1 Useful Definitions or Concepts 1.1 Elastic constitutive laws One general type of elastic material model is the one called Cauchy elastic material, which depend on only the current local deformation of the material and has no dependence on past history. This type is often to general and a slightly more restrictive model called Green elastic materials which are derivable from a scalar function (strain energy density function) are often used in mechanics. • Cauchy elastic S = Sˆ(deformation measure) ∂Ψ • Green elastic S = ∂deformation measure) The definition of Green elastic materials coincide with that of hyperelasticity. From hyperelasticity and thermody- namic consistency, one obtains, ∂Ψ P = (1) ∂F or ∂Ψ S = 2 . (2) ∂C Objectivity requires that Ψˆ depend only the stretches or for example on the Right Cauchy deformation tensor, Ψ(ˆ C) . (3) If the material is isotropic, then the Ψ can also be a function of the Left Cauchy deformation tensor, Ψ(ˆ b) (4) or equivalently, Ψ(ˆ I1(b),I2(b),I3(b)) (5) Ψ(ˆ I1(C),I2(C),I3(C)) . (6) 1 ETH Zurich Institute for Mechanical Systems Department of Mechanical and Process Engineering Center of Mechanics Winter 06/07 Nonlinear Continuum Mechanics Exercise 9 Prof. Dr. Sanjay Govindjee 2 Applications Problem: Consider the Neo-Hookean model, 2 Ψ = c1(I1 − 3) + c2(J − 1) + c3lnJ. (7) What should c1, c2, c3 be such that this model is consistent with linear elasticity? Express ci (i = 1, 2, 3) in terms of the Lame constants. -
Supplementary Notes For: Nonlinear Elasticity with Applications to the Arterial Wall Short Course in the EU-Regional School in C
A. M. Robertson, Nonlinear elasticity, Spring 2009 1 Supplementary Notes for: Nonlinear elasticity with applications to the arterial wall Short Course in the EU-Regional School in Computational Engineering Science RWTH Aachen University Part I- March 27, 2009 Part II- April 3, 2009 Associate Professor A. M. Robertson Department of Mechanical Engineering and Materials Science McGowan Institute for Regenerative Medicine Center for Vascular Remodeling and Regeneration (CVRR) University of Pittsburgh 2 A. M. Robertson, Supplementary Notes Contents 1 Kinematics 7 1.1ContinuumIdealization............................. 7 1.2Descriptionofmotionofmaterialpointsinabody.............. 7 1.3Referentialandspatialdescriptions....................... 9 1.4 Displacement, Velocity, and Acceleration . 10 1.4.1 Displacement............................... 10 1.4.2 Velocity and Acceleration . 10 1.5DeformationGradientoftheMotion...................... 11 1.6 Transformations of infinitesimal areas and volumes during the deformation 13 1.6.1 Transformationofinfinitesimalareas . 13 1.6.2 Transformation of infinitesimal volumes . 13 1.7MeasuresofStretchandStrain......................... 14 1.7.1 Material stretch and strain tensors, C and E ............. 14 1.7.2 Spatial Stretch and Strain Tensors, b,e................. 16 1.8 Polar Decomposition of the Deformation Gradient Tensor . 17 1.9OtherStrainMeasures.............................. 19 1.10VelocityGradient................................. 19 1.10.1 Vorticity Vector and Vorticity Tensor . 22 1.11SpecialMotions................................. -
Absolute Temperature, 210, 243, 362 Acceleration, 6, 152, 267, 361
Cambridge University Press 978-1-107-02543-1 - An Introduction to Continuum Mechanics, Second Edition J. N. Reddy Index More information Index Absolute temperature, 210, 243, 362 orthonormal, 21{23, 26, 74, 78, 82, Acceleration, 6, 152, 267, 361 158, gravitational, 371 reciprocal, 19, 20, 43 vector, 182 unitary, 21, 42, 43 Adiabatic, 210 Beam, 2, 7, 278{284, 303{306 Adjoint, 38 bending, 278 Adjunct, 38 theory, 124, 278, 280, 305, 328, 351 Airy stress function, 301{309 Beltrami{Michell equations, 270, 271, 352 Algebraic Beltrami's equations, 271 equations, 328 Bending moment, 217, 280, 288, 305, multiplicity, 70 321{325, 346 Almansi{Hamel strain tensor, 104 Bernoulli's equations, 385 Alternating symbol, 25 Betti's reciprocity theorem, 288 Ampere's law, 254 Bianchi formulas, 147 Analytical solution, 272, 369, 379 Biaxial state of strain, 146 Angle of twist, 308 Biharmonic Angular equation, 301 momentum, 4, 169, 193{206 operator, 301 velocity, 14 Bilinear form, 326 Anisotropic, 222, 238, 258 Bingham model, 247 Antisymmetric tensor, see skew symmet- Body couple, 5, 169, 173, 205 ric Body force, 152, 197 Applied mechanics, 255 Boundary Approximate solution, 272 conditions, 364 Approximation functions, 328 curve, 18 Area change, 97 value problem, 265 Associative, 35 Bulk viscosity, 244 Asymmetry, 292 Axial vector, 119 Axisymmetric Cable supported beam, 282 body, 148 Caloric equation of state, 357 boundary condition, 292 Cantilever beam, 123, 217, 287, 290, 303, flow, 364 344 geometry, 296 Carreau model, 247 heat conduction, 376 Cartesian, 21, -
Mechanical Constitutive Models for Engineering Materials
MECHANICAL CONSTITUTIVE MODELS FOR ENGINEERING MATERIALS by Behzad Rohani Soils and Pavements Laboratory U. S. Army Engineer Waterways Experiment Station P. O. Box 631, Vicksburg, Miss. 39180 September 1977 Final Report Approved For Public Release; Distribution Unlimited TA Prepared for Assistant Secretary of the Army (R&-D) 7 Department of the Army ,W34m Washington, D. C. 203I0 S-77-19 1977 Under Project 4 A I6 II0 IA 9 ID LIBRARY JAN 2 1970 Bureau of Reclamation Pnnvo*' f*- »^ ¡-~ J Destroy this report when no longer needed. Do not return it to the originator. V BUREAU OF RECLAMATION DENVER LIBRARY 92051290 V Unclassified ß ‘[ SECURITY CLASSIFICATION OF THIS PAGE (When Data Entered) READ INSTRUCTIONS REPORT DOCUMENTATION PAGE BEFORE COMPLETING FORM 1 .^REPORT NUMBER 2. GOVT ACCESSION NO. 3. RECIPIENT'S CATALOG NUMBER vb Miscellaneous^Paper S-77-19 A 4. T IT L E (and Subtitle) ' 5. TYPE OF REPORT & PERIOD COVERED 3 MECHANICAL CONSTITUTIVE MODELS FOR ENGINEERING £ Final Report) MATERIALS'-— .--------------------- ------ $ 6. PERFORMING ORG. REPORT NUMBER 7. A U T H O R S 8. CONTRACT OR GRANT NUMBER^) ( Behzad Rohani /" 4 9. PERFORMING ORGANIZATION NAME AND ADDRESS 10. PROGRAM ELEMENT, PROJECT, TASK AREA & WORK UNIT NUMBERS U. S.^Army Engineer Waterways Experiment Station Soils and Pavements Laboratory ^ ^ Project UA161101A91B P. 0. Box 631, Vicksburg, Miss. 39180 11. CONTROLLING OFFICE NAME AND ADDRESS / 12. REPORT DATE Assistant Secretary of the Army (R&D) ’ September 1977 t/ Department of the Army, Washington, D. C. 20310 13. NUMBER OF PAGES ' l8l 14. MONITORING AGENCY NAME & ADDRESSf/f different from Controlling Office) 15. -
Finite Strain Elastoplasticity: Consistent Eulerian and Lagrangian Approaches
Finite Strain Elastoplasticity: Consistent Eulerian and Lagrangian Approaches by Mohammad Amin Eshraghi A thesis presented to the University of Waterloo in fulfillment of the thesis requirement for the degree of Doctor of Philosophy in Mechanical Engineering Waterloo, Ontario, Canada, 2009 © Mohammad Amin Eshraghi 2009 Author’s Declaration I hereby declare that I am the sole author of this thesis. This is a true copy of the thesis, including any required final revisions, as accepted by my examiners. I understand that my thesis may be made electronically available to the public. Mohammad Amin Eshraghi ii Abstract Infinitesimal strain approximation and its additive decomposition into elastic and plastic parts used in phenomenological plasticity models are incapable of predicting the hardening behavior of materials for large strain loading paths. Experimentally observed second-order effect in finite torsional loading of cylindrical bars, known as the Swift effect, as well as deformations involving significant amount of rotations are examples for which infinitesimal models fail to predict the material response accurately. Several different Eulerian and Lagrangian formulations for finite strain elastoplasticity have been proposed based on different decompositions of deformation and their corresponding flow rules. However, issues such as spurious shear oscillation in finite simple shear and elastic dissipation in closed-path loadings as well as elastic ratchetting under cyclic loading have been identified with the classical formulations for finite strain analysis. A unified framework of Eulerian rate-type constitutive models for large strain elastoplasticity is developed here which assigns no preference to the choice of objective corotational rates. A general additive decomposition of arbitrary corotational rate of the Eulerian strain tensor is proposed. -
Nmmo401 Continuum Mechanics, Winter Semester 2020/2021 Syllabus
NMMO401 CONTINUUM MECHANICS, WINTER SEMESTER 2020/2021 SYLLABUS V´IT PRU˚SAˇ Topics/notions printed in italics are not a part of the exam. All other topics/notions are expected to mastered at the level of a reflex action. • Preliminaries. { Linear algebra. ∗ Scalar product, vector product, mixed product, tensor product. Transposed matrix. ∗ Tensors. Inertia tensor as an example of a tensorial quantity in mechanics. ∗ Cofactor matrix cof A and determinant det A. Geometrical interpretation. ∗ Cayley{Hamilton theorem, characteristic polynomial, eigenvectors, eigenvalues. ∗ Trace of a matrix. ∗ Invariants of a matrix and their relation to the eigenvalues and the mixed product. ∗ Properties of proper orthogonal matrices, angular velocity. ∗ Polar decomposition. Geometrical interpretation. { Elementary calculus. ∗ Matrix functions. Exponential of a matrix. ∗ Representation theorem for scalar valued isotropic tensorial functions and tensor valued isotropic tensorial functions. ∗ G^ateauxderivative, Fr´echet derivative. Derivatives of the invariants of a matrix. ∗ Operators r, div and rot for scalar and vector fields. Operators div and rot for tensor fields. Abstract definitions and formulae in Cartesian coordinate system. Identities in tensor calculus. { Line, surface and volume integrals. R R ∗ Line integral of a scalar valued function γ ' dX, line integral of a vector valued function γ v • dX. R R ∗ Surface integral of a scalar valued function S ' dS, surface integral of a vector valued function S v • dS, surface Jacobian. ∗ Volume integral, Jacobian matrix. { Stokes theorem and its consequences. ∗ Potential vector field, path independent integrals, curl free vector fields. Characterisation of potential vector fields. { Elementary concepts in classical physics. ∗ Newton laws. ∗ Galilean invariance, principle of relativity, non-inertial reference frame. -
Neoclassical Navier–Stokes Equations Considering the Gyftopoulos–Beretta Exposition of Thermodynamics
energies Article Neoclassical Navier–Stokes Equations Considering the Gyftopoulos–Beretta Exposition of Thermodynamics Janusz Badur 1, Michel Feidt 2 and Paweł Ziółkowski 3,* 1 Energy Conversion Department, Institute of Fluid Flow Machinery, Polish Academy of Science, Fiszera 14, 80-952 Gda´nsk,Poland; [email protected] 2 Laboratory of Energetics & Theoretical & Applied Mechanics (LEMTA), University of Lorraine, 2 Avenue de la Forêt de Haye, 54518 Vandœuvre-lès-Nancy, France; [email protected] 3 Faculty of Mechanical Engineering, Department of Energy and Industrial Apparatus, Gda´nskUniversity of Technology, Narutowicza 11/12, 80-233 Gda´nsk,Poland * Correspondence: [email protected]; Tel.: +48-58-347-2073 Received: 14 February 2020; Accepted: 25 March 2020; Published: 2 April 2020 Abstract: The seminal Navier–Stokes equations were stated even before the creation of the foundations of thermodynamics and its first and second laws. There is a widespread opinion in the literature on thermodynamic cycles that the Navier–Stokes equations cannot be taken as a thermodynamically correct model of a local “working fluid”, which would be able to describe the conversion of “heating” into “working” (Carnot’s type cycles) and vice versa (Afanasjeva’s type cycles). Also, it is overall doubtful that “cycle work is converted into cycle heat” or vice versa. The underlying reason for this situation is that the Navier–Stokes equations come from a time when thermodynamic concepts such as “internal energy” were still poorly understood. Therefore, this paper presents a new exposition of thermodynamically consistent Navier–Stokes equations. Following that line of reasoning—and following Gyftopoulos and Beretta’s exposition of thermodynamics—we introduce the basic concepts of thermodynamics such as “heating” and “working” fluxes. -
Zhu, Yunfei (2010) Nonlinear Deformations of a Thick-Walled Hyperelastic Tube Under External Pressure
Zhu, Yunfei (2010) Nonlinear deformations of a thick-walled hyperelastic tube under external pressure. PhD thesis. http://theses.gla.ac.uk/1627/ Copyright and moral rights for this thesis are retained by the author A copy can be downloaded for personal non-commercial research or study, without prior permission or charge This thesis cannot be reproduced or quoted extensively from without first obtaining permission in writing from the Author The content must not be changed in any way or sold commercially in any format or medium without the formal permission of the Author When referring to this work, full bibliographic details including the author, title, awarding institution and date of the thesis must be given. Glasgow Theses Service http://theses.gla.ac.uk/ [email protected] Nonlinear deformations of a thick-walled hyperelastic tube under external pressure by Yunfei Zhu A thesis submitted to the Faculty of Information and Mathematical Sciences at the University of Glasgow for the degree of Doctor of Philosophy December 2009 °c Yunfei Zhu 2009 Abstract This research deals with several novel aspects of the nonlinear behaviour of thick-walled cylindrical hyperelastic tubes under external pressure. Initially, we consider bifurcation from a circular cylindrical deformed con¯guration of a thick-walled circular cylindrical tube of incompressible isotropic elastic material subject to combined axial loading and external pressure. In particular, we examine both axisymmet- ric and asymmetric modes of bifurcation. The analysis is based on the three-dimensional incremental equilibrium equations, which are derived and then solved numerically for a speci¯c material model using the Adams-Moulton method. -
Finite Strain Elasticity
Part 2 THEORY OF ELASTICITY CHAPTER 5 FINITE STRAIN ELASTICITY 5.1. Green-Elasticity Elastic deformation does not cause irreversible rearrangement of internal structure, and the corresponding Helmholtz free energy is a function of stress and temperature only. Restricting consideration to isothermal elastic defor- mation (θ˙ = 0), Eqs. (4.3.7) and (4.3.9) give ˙ ∂ψ ˙ 1 ˙ ψ = : E(n) = 0 T(n) : E(n), (5.1.1) ∂E(n) ρ i.e., ∂Ψ 0 T(n) = , Ψ=ρ ψ E(n) . (5.1.2) ∂E(n) Alternatively, Eq. (5.1.2) can be deduced by adopting an experimentally observed property that there is no net work left in a body upon any closed cycle of elastic strain, i.e., T(n) :dE(n) =0. (5.1.3) This implies that T(n) :dE(n) = dΨ (5.1.4) is a total differential, which leads to Eq. (5.1.2). The function Ψ = Ψ E(n) is the strain energy function per unit initial volume. It represents the work done to isothermally deform a unit of initial volume to the state of strain E(n). The explicit representation of the function Ψ E(n) depends on the selected strain measure E(n) and the material properties. Since the material and spatial strain tensors (see Section 2.3) are related by ˆ T E(n) = E (n) = R ·EE (n) · R, (5.1.5) the strain energy per unit mass can be written as ˆ ψ = ψ E(n) = ψ E (n) . (5.1.6) It can be easily verified that • ∂ψ ∂ψ T ˆ˙ T = R · · R , E (n) = R · E (n) · R, (5.1.7) ∂E (n) ∂E(n) and the rate of ψ becomes • ˙ ∂ψ ˙ ∂ψ ψ = : E(n) = : E (n). -
Soil Constitutive Models and Their Application in Geotechnical Engineering: a Review
Published by : International Journal of Engineering Research & Technology (IJERT) http://www.ijert.org ISSN: 2278-0181 Vol. 7 Issue 04, April-2018 Soil Constitutive Models and Their Application in Geotechnical Engineering: A Review Kh Mohd Najmu Saquib Wani1 Rakshanda Showkat 2 Post Graduate Student, Post Graduate Student, Dept. of Civil Engineering Dept. of Civil Engineering NIT Srinagar, Kashmir, India 190006 NIT Srinagar,Kashmir,India 190006 Abstract: Various constitutive models have been developed Moreover, the failure of soil under three dimensional state for modeling the stress strain behavior of soils and apply such of stress is extremely complicated. Various criteria have models in finite element modeling for application in been proposed to explain failure condition under this state. geotechnical engineering and also for analysis of soil structure With the advancement in numerical methods like problems under different loading conditions. Simple as well as development of finite element method, it has been possible complex models have been formulated based upon the mechanical principle (hooks law of linear elasticity and to analyze and predict the complex behavior of soils and columbs law of perfect plasticity).However soils are not soil-structure interaction problems. Such analysis depends entirely linearly elastic and perfectly plastic for the entire on relation between stress and strain of various materials. range of loading. In fact, actual behavior of soils is very In numerical methods, this relation of stress and strain of a complicated to understand and it shows range of behaviors given material is represented by constitutive Model which under different conditions. Hence, different models have been models the behavior of soil in a single element. -
Elastic Solids
Section 4.1 4.1 Elastic Solids In this section is given an overview of the common elasticity models. 4.1.1 The Linear Elastic Solid The classical Linear Elastic model, or Hookean model, has the following linear relationship between stress and strain: σ = C⋅ :ε, σ ij = Cijmnε mn (4.1.1) where ε is the small strain tensor, §2.7. Strain Energy In this purely mechanical theory of elastic materials, there is no dissipation of energy – all the energy of the loads is stored as elastic strain energy in the material as it deforms, and can be recovered. For the linear elastic material, the rate of deformation is equivalent to the rate of small- strain, d = ε& , so the strain-energy function can be written as dW =σ : dε (4.1.2) and the total energy stored per unit volume over the complete history of straining is W = ∫ σ :dε (4.1.3) nnd the stress can be written as ∂W σ = (4.1.4) ∂ε Reduction in the number of Independent Elastic Constants Since the stress and strain are symmetric, σ ij = σ ji and ε mn = ε nm , the fourth-order elasticity tensor of stiffness coefficients contains the minor symmetries 1.9.65, Cijkl = C jikl = Cijlk (4.1.5) and so the 81 coefficients reduce to 36 independent coefficients. Further, since C is independent of the strains, 1 W = σ : dε = C⋅ :εdε = e : C : e (4.1.6) ∫ ∫ 2 Solid Mechanics Part III 353 Kelly Section 4.1 and so ∂W C = (4.1.7) ∂e∂e Now ∂W ∂W = (4.1.8) ∂ε ij ∂ε mn ∂ε mn∂ε ij and it follows that C possesses the major symmetries: Cijmn = Cmnij (4.1.9) This reduces the number of independent elastic constants from 36 to 21. -
Stress Channelling in Extreme Couple-Stress Materials Part II: Localized Folding Vs Faulting of a Continuum in Single and Cross Geometries
Stress channelling in extreme couple-stress materials Part II: Localized folding vs faulting of a continuum in single and cross geometries Panos A. Gourgiotis, Davide Bigoni1 email: [email protected], [email protected] University of Trento, via Mesiano 77, I-38123 Trento, Italy Abstract. The antiplane strain Green’s functions for an applied concentrated force and moment are obtained for Cosserat elastic solids with extreme anisotropy, which can be tailored to bring the material in a state close to an instability threshold such as failure of ellipticity. It is shown that the wave propagation condition (and not ellipticity) governs the behavior of the antiplane strain Green’s functions. These Green’s functions are used as perturbing agents to demonstrate in an extreme material the emergence of localized (single and cross) stress channelling and the emergence of antiplane localized folding (or creasing, or weak elastostatic shock) and faulting (or elastostatic shock) of a Cosserat continuum, phenomena which remain excluded for a Cauchy elastic material. During folding some components of the displacement gradient suffer a finite jump, whereas during faulting the displacement itself displays a finite discontinuity. Keywords: Cosserat elasticity; strain localization; Green’s functions; wave propagation; anisotropy 1. Introduction The mechanical conditions leading to the formation of a periodic pattern of creases in an elastic solid under load have attracted great interest (see for instance Onuki, 1989; Roccabianca et al., 2010; Hutchinson, 2013; Jin and Suo, 2015), particularly with reference to soft matter in biological applications, for altering wettability, and for flexible electronics. It is 1 Corresponding author. Email: [email protected] 1 not difficult to explain periodic creasing in terms of bifurcation theory for elastic solids, but the formation of an isolated crease, or fold (to be distinguished from bend2), is hard to obtain and perhaps even impossible for a Cauchy elastic continuum.