Process Capability Process Capability
Total Page:16
File Type:pdf, Size:1020Kb
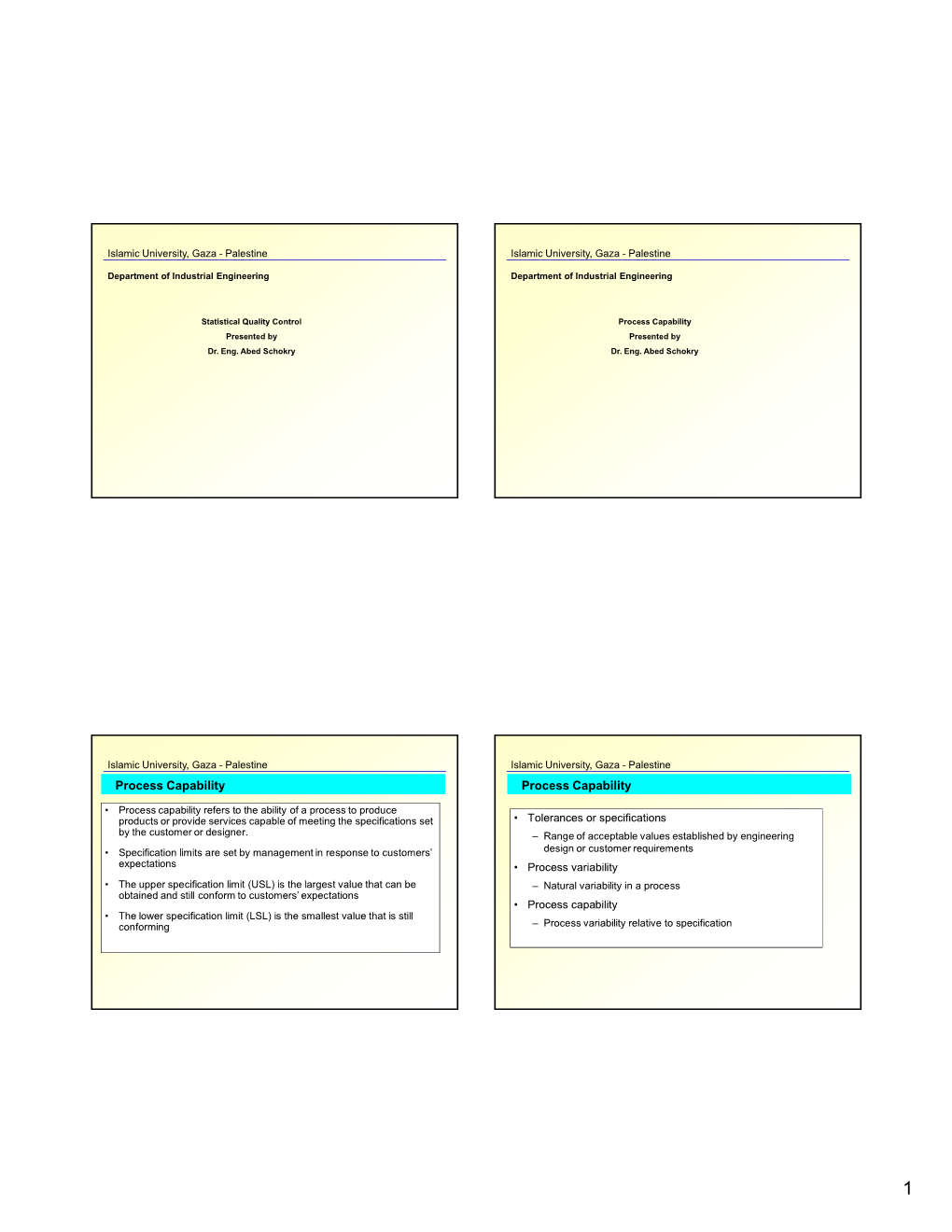
Load more
Recommended publications
-
Implementing SPC for Non-Normal Processes with the I-MR Chart: a Case Study
Implementing SPC for non-normal processes with the I-MR chart: A case study Axl Elisson Master of Science Thesis TPRMM 2017 KTH Industrial Engineering and Management Production Engineering and Management SE-100 44 STOCKHOLM Acknowledgements This master thesis was performed at the brake manufacturer Haldex as my master of science degree project in Industrial Engineering and Management at the Royal Institute of Technology (KTH) in Stockholm, Sweden. It was conducted during the spring semester of 2017. I would first like to thank my supervisor at Haldex, Roman Berg, and Annika Carlius for their daily support and guidance which made this project possible. I would also like to thank the quality department, production engineers and operators at Haldex for all insight in different subjects. Finally, I would like to thank my supervisor at KTH, Jerzy Mikler, for his support during my thesis. All of your combined expertise have been very valuable. Stockholm, July 2017 Axl Elisson Abstract The application of statistical process control (SPC) requires normal distributed data that is in statistical control in order to determine valid process capability indices and to set control limits that reflects the process’ true variation. This study examines a case of several non-normal processes and evaluates methods to estimate the process capability and set control limits that is in relation to the processes’ distributions. Box-Cox transformation, Johnson transformation, Clements method and process performance indices were compared to estimate the process capability and the Anderson-Darling goodness-of-fit test was used to identify process distribution. Control limits were compared using Clements method, the sample standard deviation and from machine tool variation. -
Process Capability Analysis
6 Process capability analysis In general, process capability indices have been quite controversial. (Ryan, 2000, p. 186) Overview Capability indices are widely used in assessing how well processes perform in relation to customer requirements. The most widely used indices will be defined and links with the concept of sigma quality level established. Minitab facilities for capability analysis of both measurement and attribute data will be introduced. 6.1 Process capability 6.1.1 Process capability analysis with measurement data Imagine that four processes produce bottles of the same type for a customer who specifies that weight should lie between 485 and 495 g, with a target of 490 g. Imagine, too, that all four processes are behaving in a stable and predictable manner as indicated by control charting of data from regular samples of bottles from the processes. Let us suppose that the distribution of weight is normal in all four cases, with the parameters in Table 6.1. The four distributions of weight are displayed in Figure 6.1, together with reference lines showing lower specification limit (LSL), upper specification limit (USL) and Target (T). How well are these processes performing in relation to the customer requirements? In the long term the fall-out, in terms of nonconforming bottles, would be as shown in the penultimate column of Table 6.1. The fall-out is given as number of parts bottles) per million (ppm) that would fail to meet the customer specifications. The table in Appendix 1 indicates that these fall-outs correspond to sigma quality levels of 4.64, 3.50, 2.81 and 3.72 respectively for lines 1–4. -
A New Non-Parametric Process Capability Index
A New Non-parametric Process Capability Index Deovrat Kakde Arin Chaudhuri Diana Shaw SAS Institute Inc. SAS Institute Inc. SAS Institute Inc. SAS Campus Dr., SAS Campus Dr., SAS Campus Dr., Cary, NC 27513, USA Cary, NC 27513, USA Cary, NC 27513, USA Email: [email protected] Email: [email protected] Email: [email protected] Abstract—Process capability index (PCI) is a commonly used Often manufacturing processes are not centered at the mid- statistic to measure ability of a process to operate within the given point of tolerance band. For such processes, PCI Cpk is specifications or to produce products which meet the required recommended. For a process centered at tolerance midpoint quality specifications. PCI can be univariate or multivariate depending upon the number of process specifications or qual- value, Cp and Cpk are identical. ity characteristics of interest. Most PCIs make distributional Many manufacturing processes have two or more corre- assumptions which are often unrealistic in practice. lated parameters of interest, which need to be monitored and This paper proposes a new multivariate non-parametric pro- controlled. For such processes, multivariate PCI are used. An cess capability index. This index can be used when distribution of excellent overview of various multivariate process capability the process or quality parameters is either unknown or does not follow commonly used distributions such as multivariate normal. indexes is provided in [19]. One of the popular parametric multivariate PCI is the multivariate capability vector (abbrevi- I. INTRODUCTION ated as MPCI) [12], [15]. This vector has three components. The first two components are computed with an assumption A process capability index (PCI) is an objective measure that the process data follows a multivariate normal distribution. -
Application of Monte Carlo Technique for Analysis of Tolerance & Allocation of Reciprocating Compressor Assembly 1Somvir Arya, 2Sachin Kumar, 3Viney Jain 1Dept
ISSN : 2249-5762 (Online) | ISSN : 2249-5770 (Print) IJRMET VOL . 2, ISSU E 1, AP ri L 2012 Application of Monte Carlo Technique for Analysis of Tolerance & Allocation of Reciprocating Compressor Assembly 1Somvir Arya, 2Sachin Kumar, 3Viney Jain 1Dept. of IIET, Mech. Engg., Kinana, Jind, Haryana, India ²Dept. of IIET, Electrical. Engg., Kinana, JInd, Haryana, India 3ACE & AR, Mithapur, Ambala, Haryana, India Abstract In order for mating feature (faces) of parts to fit together and The variation in part dimensions is one of the main causes of operate properly, each part must be manufactured within these variation in product quality. The allowable range in which the limits. The key, gears on the shaft, and other similar members dimension can vary is called tolerance. Tolerance can be expressed mounted by press or shrink-fit are toleranced so that the desired in either of two ways, 1). Bilatera 2). Unilateral tolerance. In interference is maintained without being so large as to make the bilateral tolerance, it is specified as plus or minus deviation from assembly impossible or the resulting stress too high. Tolerancing the basic size. In unilateral tolerance, variation is permitted only in is essential element of mass production and interchangeable one side direction from the basic size. If a part size and shape are not manufacturing, by which parts can be made in widely separated within tolerance limit, the part is not acceptable. The assignment location and then brought together for assembly. Tolerancing of actual values to the tolerance limits has major influence on makes it also possible for spare parts to replace broken or worn the overall cost and quality of an assembly or product. -
System Performance and Process Capability in Additive Manufacturing: Quality Control for Polymer Jetting
polymers Article System Performance and Process Capability in Additive Manufacturing: Quality Control for Polymer Jetting Razvan Udroiu * and Ion Cristian Braga Department of Manufacturing Engineering, Transilvania University of Brasov, 29 Eroilor Boulevard, 500036 Brasov, Romania; [email protected] * Correspondence: [email protected]; Tel.: +40-268-421-318 Received: 19 May 2020; Accepted: 3 June 2020; Published: 4 June 2020 Abstract: Polymer-based additive manufacturing (AM) gathers a great deal of interest with regard to standardization and implementation in mass production. A new methodology for the system and process capabilities analysis in additive manufacturing, using statistical quality tools for production management, is proposed. A large sample of small specimens of circular shape was manufactured of photopolymer resins using polymer jetting (PolyJet) technology. Two critical geometrical features of the specimen were investigated. The variability of the measurement system was determined by Gage repeatability and reproducibility (Gage R&R) methodology. Machine and process capabilities were performed in relation to the defined tolerance limits and the results were analyzed based on the requirements from the statistical process control. The results showed that the EDEN 350 system capability and PolyJet process capability enables obtaining capability indices over 1.67 within the capable tolerance interval of 0.22 mm. Furthermore, PolyJet technology depositing thin layers of resins droplets of 0.016 mm allows for manufacturing in a short time of a high volume of parts for mass production with a tolerance matching the ISO 286 IT9 grade for radial dimension and IT10 grade for linear dimensions on the Z-axis, respectively. Using microscopy analysis some results were explained and validated from the capability study. -
The Effects of Autocorrelation in the Estimation of Process Capability Indices." (1998)
Louisiana State University LSU Digital Commons LSU Historical Dissertations and Theses Graduate School 1998 The ffecE ts of Autocorrelation in the Estimation of Process Capability Indices. Lawrence Lee Magee Louisiana State University and Agricultural & Mechanical College Follow this and additional works at: https://digitalcommons.lsu.edu/gradschool_disstheses Recommended Citation Magee, Lawrence Lee, "The Effects of Autocorrelation in the Estimation of Process Capability Indices." (1998). LSU Historical Dissertations and Theses. 6847. https://digitalcommons.lsu.edu/gradschool_disstheses/6847 This Dissertation is brought to you for free and open access by the Graduate School at LSU Digital Commons. It has been accepted for inclusion in LSU Historical Dissertations and Theses by an authorized administrator of LSU Digital Commons. For more information, please contact [email protected]. INFORMATION TO USERS This manuscript has been reproduced from the microfilm master. U M I films the text directly from die original or copy submitted. Thus, some thesis and dissertation copies are in typewriter face, while others may be from any type o f computer printer. The quality o f this reproduction is dependent upon the quality o f the copy submitted. Broken or indistinct print, colored or poor quality illustrations and photographs, print bleedthrough, substandard margins, and improper alignment can adversely affect reproduction. hi the unlikely event that the author did not send UMI a complete manuscript and there are missing pages, these will be noted. Also, if unauthorized copyright material had to be removed, a note w ill indicate the deletion. Oversize materials (e.g., maps, drawings, charts) are reproduced by sectioning the original, beginning at the upper left-hand corner and continuing from left to right in equal sections with small overlaps. -
Improving Process Capability Database Usage for Robust Design Engineering by Generalising Measurement Data
Downloaded from orbit.dtu.dk on: Sep 25, 2021 Improving process capability database usage for robust design engineering by generalising measurement data Okholm, A.B.; Rask, M.; Ebro, Martin ; Eifler, Tobias; Holmberg, M.; Howard, Thomas J. Published in: 13th International Design Conference - Design 2014 Publication date: 2014 Document Version Publisher's PDF, also known as Version of record Link back to DTU Orbit Citation (APA): Okholm, A. B., Rask, M., Ebro, M., Eifler, T., Holmberg, M., & Howard, T. J. (2014). Improving process capability database usage for robust design engineering by generalising measurement data. In 13th International Design Conference - Design 2014 (pp. 1133-1144). Design Society. General rights Copyright and moral rights for the publications made accessible in the public portal are retained by the authors and/or other copyright owners and it is a condition of accessing publications that users recognise and abide by the legal requirements associated with these rights. Users may download and print one copy of any publication from the public portal for the purpose of private study or research. You may not further distribute the material or use it for any profit-making activity or commercial gain You may freely distribute the URL identifying the publication in the public portal If you believe that this document breaches copyright please contact us providing details, and we will remove access to the work immediately and investigate your claim. INTERNATIONAL DESIGN CONFERENCE - DESIGN 2014 Dubrovnik - Croatia, May 19 - 22, 2014. IMPROVING PROCESS CAPABILITY DATABASE USAGE FOR ROBUST DESIGN ENGINEERING BY GENERALISING MEASUREMENT DATA A. B. Okholm, M. Rask, M. -
Assignment 9 Control Charts, Process Capability and QFD
Assignment 9 Control Charts, Process capability and QFD Instructions: 1. Total No. of Questions: 25. Each question carries one point. 2. All questions are objective type. Only one answer is correct per numbered item. 1. How do you find the process capability? a) By Process Capability Ratio = Cp = − b) By USL and LSL only 6 c) By normal distribution curve d) By spread and mean shift of the process 2. In a certain process it is given that USL is 14, LSL is zero. The process has a mean of 10 and standard deviation 2. What will be the Process Capability Ratio? a) 0.83 b) 1.17 c) 1.33 d) 1.5 3. In a process the inverse of process capability ratio is 0.65. Which statement is correct? a) The process is capable. b) The process is incapable. c) The process is capable with tight control. d) None of the above 4. A process having mean 8.80 and process standard deviation 0.12 has spread of specification limit: 9.0±0.4. What will be the process capability index? a) 0.55 b) 1.67 c) 1.33 d) 0.83 5. How is different than ? a) Looks at the centrality of the process. b) Looks at the overall variability of the process. c) Both look at the overall variability of the process. d) Looks at the centrality of the process. 6. A QC scheme is in operation for a process producing ball-bearings. A sample of 6 bearings is taken every hour and diameters is measured. -
Use Process Capability to Ensure Product Quality
Use Process Capability to Ensure Product Quality Lawrence X. Yu, Ph.D. Director (acting) Office of Pharmaceutical Science, CDER, FDA FDA/ PQRI Conference on Evolving Product Quality September 16-17, 2104, Bethesda, MD 1 2 Quality by Testing vs. Quality by Design Quality by Testing – Specification acceptance criteria are based on one or more batch data (process capability) – Testing must be made to release batches Quality by Design – Specification acceptance criteria are based on performance – Testing may not be necessary to release batches L. X. Yu. Pharm. Res. 25:781-791 (2008) 3 ICH Q6A: Test Procedures and Acceptance Criteria… 4 5 Pharmaceutical QbD Objectives Achieve meaningful product quality specifications that are based on assuring clinical performance Increase process capability and reduce product variability and defects by enhancing product and process design, understanding, and control Increase product development and manufacturing efficiencies Enhance root cause analysis and post-approval change management 6 Concept of Process Capability First introduced in Statistical Quality Control Handbook by the Western Electric Company (1956). – “process capability” is defined as “the natural or undisturbed performance after extraneous influences are eliminated. This is determined by plotting data on a control chart.” ISO, AIAG, ASQ, ASTM ….. published their guideline or manual on process capability index calculation 7 Nomenclature Four indices: – Cp: process capability index – Cpk: minimum process capability index – Pp: process -
Design Approach for Quality Improvement and Cost Reduction: a Case Study of Cable Manufacturing
Design Approach for Quality Improvement and Cost Reduction: A Case Study of Cable Manufacturing Chukwuebuka. M. U-Dominic1*, Harold C. Godwin1 and Nkemakonam Igbokwe1 1Department of Industrial and Production Engineering, Nnamdi Azikiwe University, Awka, Nigeria. Authors’ contributions This work was carried out in collaboration among all authors. All authors read and approved the final manuscript. Case Study ABSTRACT In this study, an extrusion process was studied in a cable manufacturing company located in Southeastern Nigeria. The critical-to-quality (CTQ) characteristic considered in the study was the cable diameter and the design effort was to reduce the possibilities of having cables with inconsistent dimensions. Taguchi Orthogonal Array Design L16 (4˄2) was used to achieve the optimum parameter settings after statistically investigating the assumed correlations between the process parameters in relation to cable dimension. Thereafter, an appropriate engineering tolerance interval for the improved process was designed to tighten the existing tolerance of the process from T±0.185 to T±0.032, thus reducing the engineering tolerance by 82.7% from the initial tolerance limit. After the process improvement, the Taguchi loss function approach was used to estimate cost attributed to deviations. The loss function estimation result has shown that the cost attributed to cable diameter deviations from the nominal value reduced from the initial value of ₦7.34/coil to a reduced cost of ₦2.08/coil. The sigma level increased from 0.6 to 5.2 at the project termination stage and the estimated annual loss decreased by 72% from the baseline value. Keywords: Cable manufacturing; engineering tolerance; loss function; sigma level; Taguchi design. -
Mistakeproofing the Design of Construction Processes Using Inventive Problem Solving (TRIZ)
www.cpwr.com • www.elcosh.org Mistakeproofing The Design of Construction Processes Using Inventive Problem Solving (TRIZ) Iris D. Tommelein Sevilay Demirkesen University of California, Berkeley February 2018 8484 Georgia Avenue Suite 1000 Silver Spring, MD 20910 phone: 301.578.8500 fax: 301.578.8572 ©2018, CPWR-The Center for Construction Research and Training. All rights reserved. CPWR is the research and training arm of NABTU. Production of this document was supported by cooperative agreement OH 009762 from the National Institute for Occupational Safety and Health (NIOSH). The contents are solely the responsibility of the authors and do not necessarily represent the official views of NIOSH. MISTAKEPROOFING THE DESIGN OF CONSTRUCTION PROCESSES USING INVENTIVE PROBLEM SOLVING (TRIZ) Iris D. Tommelein and Sevilay Demirkesen University of California, Berkeley February 2018 CPWR Small Study Final Report 8484 Georgia Avenue, Suite 1000 Silver Spring, MD 20910 www. cpwr.com • www.elcosh.org TEL: 301.578.8500 © 2018, CPWR – The Center for Construction Research and Training. CPWR, the research and training arm of the Building and Construction Trades Department, AFL-CIO, is uniquely situated to serve construction workers, contractors, practitioners, and the scientific community. This report was prepared by the authors noted. Funding for this research study was made possible by a cooperative agreement (U60 OH009762, CFDA #93.262) with the National Institute for Occupational Safety and Health (NIOSH). The contents are solely the responsibility of the authors and do not necessarily represent the official views of NIOSH or CPWR. i ABOUT THE PROJECT PRODUCTION SYSTEMS LABORATORY (P2SL) AT UC BERKELEY The Project Production Systems Laboratory (P2SL) at UC Berkeley is a research institute dedicated to developing and deploying knowledge and tools for project management. -
Chapter 6: Process Capability Analysis for Six Sigma
Six Sigma Quality: Concepts & Cases‐ Volume I STATISTICAL TOOLS IN SIX SIGMA DMAIC PROCESS WITH MINITAB® APPLICATIONS Chapter 6 PROCESS CAPABILITY ANALYSIS FOR SIX SIGMA © Amar Sahay, Ph.D. Master Black Belt 1 Chapter 6: Process Capability Analysis for Six Sigma CHAPTER HIGHLIGHTS This chapter deals with the concepts and applications of process capability analysis in Six Sigma. Process Capability Analysis is an important part of an overall quality improvement program. Here we discuss the following topics relating to process capability and Six Sigma: 1. Process capability concepts and fundamentals 2. Connection between the process capability and Six Sigma 3. Specification limits and process capability indices 4. Short‐term and long‐term variability in the process and how they relate to process capability 5. Calculating the short‐term or long‐term process capability 6. Using the process capability analysis to: assess the process variability establish specification limits (or, setting up realistic tolerances) determine how well the process will hold the tolerances (the difference between specifications) determine the process variability relative to the specifications reduce or eliminate the variability to a great extent 7. Use the process capability to answer the following questions: Is the process meeting customer specifications? How will the process perform in the future? Are improvements needed in the process? Have we sustained these improvements, or has the process regressed to its previous unimproved state? 8. Calculating process