Indium Oxide and Indium-Tin Oxide ( ITO)
Total Page:16
File Type:pdf, Size:1020Kb
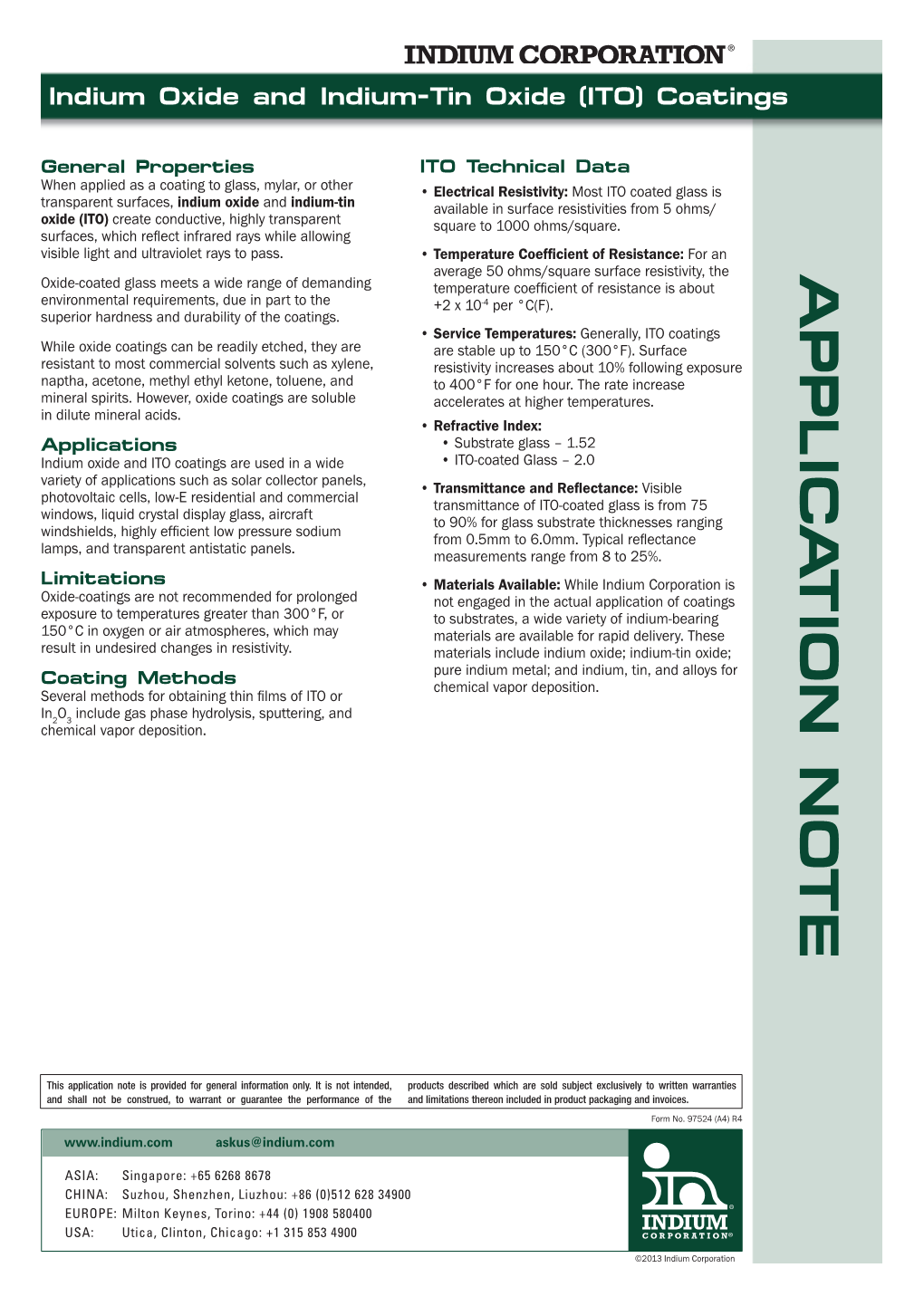
Load more
Recommended publications
-
Understanding of the Mechanism for Laser Ablation-Assisted Patterning of Graphene/ITO Double Layers: Role of Effective Thermal Energy Transfer
micromachines Article Understanding of the Mechanism for Laser Ablation-Assisted Patterning of Graphene/ITO Double Layers: Role of Effective Thermal Energy Transfer 1, 2, 3, 4 4 Hyung Seok Ryu y, Hong-Seok Kim y, Daeyoon Kim y, Sang Jun Lee , Wonjoon Choi , Sang Jik Kwon 1, Jae-Hee Han 2,* and Eou-Sik Cho 1,* 1 Department of Electronic Engineering, Gachon University, Gyeonggi-do 13120, Korea; [email protected] (H.S.R.); [email protected] (S.J.K.) 2 Department of Materials Science and Engineering, Gachon University, Gyeonggi-do 13120, Korea; [email protected] 3 Department of Energy IT, Gachon University, Gyeonggi-do 13120, Korea; [email protected] 4 School of Mechanical Engineering, Korea University, 145 Anam-ro, Seongbuk-gu, Seoul 02841, Korea; [email protected] (S.J.L.); [email protected] (W.C.) * Correspondence: [email protected] (J.-H.H.); [email protected] (E.-S.C.); Tel.: +82-31-750-8689 (J.-H.H.); +82-31-750-5297 (E.-S.C.) These authors contributed equally to this work. y Received: 3 August 2020; Accepted: 28 August 2020; Published: 29 August 2020 Abstract: Demand for the fabrication of high-performance, transparent electronic devices with improved electronic and mechanical properties is significantly increasing for various applications. In this context, it is essential to develop highly transparent and conductive electrodes for the realization of such devices. To this end, in this work, a chemical vapor deposition (CVD)-grown graphene was transferred to both glass and polyethylene terephthalate (PET) substrates that had been pre-coated with an indium tin oxide (ITO) layer and then subsequently patterned by using a laser-ablation method for a low-cost, simple, and high-throughput process. -
Synthesis and Characterization of Indium Tin Oxide Nanoparticles Via Reflux Method
Materials Science-Poland, 35(4), 2017, pp. 799-805 http://www.materialsscience.pwr.wroc.pl/ DOI: 10.1515/msp-2018-0008 Synthesis and characterization of indium tin oxide nanoparticles via reflux method SAHEBALI MANAFI˚,SIMIN TAZIKEH,SEDIGHEH JOUGHEHDOUST Department of Engineering, Shahrood Branch, Islamic Azad University, Shahrood, Iran Synthesis of indium tin oxide (ITO) nanoparticles by reflux method without chlorine contamination at different pHs, tem- peratures, solvents and concentrations has been studied. Indium chloride, tin chloride, water, ethanol and Triton X-100 were used as starting materials. Structure, size, surface morphology and transparency of indium tin oxide nanoparticles were stud- ied by X-ray diffraction (XRD), Fourier transform infrared spectroscopy (FT-IR), scanning electron microscopy (SEM) and UV-Vis spectrophotometry. XRD patterns showed that 400 °C is the lowest temperature for synthesis of ITO nanoparticles because metal hydroxide does not transform to metal oxide in lower temperature. FT-IR results showed the transformation of hydroxyl groups to oxide. SEM images showed that pH is the most important factor affecting the nanoparticles size. The smallest nanoparticles (40 nm) were obtained at pH “ 8.8. The size of crystallites was decreased by lowering of concentration (0.025 M). Keywords: reflux method; indium tin oxide; resistivity; transparency 1. Introduction containing hydrogen of 1 % demonstrated almost flat temperature dependent resistivity and the low- ´4 Transparent conductive oxides (TCO) have at- est resistivity of « 1.5 × 10 W¨cm at room tracted attention for the past few years [1–4]. TCOs temperature [16]. have been used widely in different industries, re- Delacy et al. [17] reported the synthesis of cently. -
Transparent Conducting Oxides for Electro-Optical Plasmonic Modulators
Nanophotonics 2015; 4:165–185 Review Article Open Access Viktoriia E. Babicheva*, Alexandra Boltasseva, and Andrei V. Lavrinenko Transparent conducting oxides for electro-optical plasmonic modulators DOI 10.1515/nanoph-2015-0004 1 Introduction Received January 21, 2015; accepted February 3, 2015 Abstract: The ongoing quest for ultra-compact optical The advent of broadband optical signals in telecommuni- devices has reached a bottleneck due to the diffraction cation systems led to unprecedented high bit rates that limit in conventional photonics. New approaches that pro- were unachievable in the electronic domain. Later on, vide subwavelength optical elements, and therefore lead photonics presented a new platform for high-speed data to miniaturization of the entire photonic circuit, are ur- transfer by implementing hybrid electronic-photonic cir- gently required. Plasmonics, which combines nanoscale cuits, where data transmission using light instead of elec- light confinement and optical-speed processing of signals, tric signals significantly boosted the data exchange rates has the potential to enable the next generation of hy- on such photonic/electronic chips [1–3]. Different silicon- brid information-processing devices, which are superior based photonic passive waveguides have recently been to the current photonic dielectric components in terms of proposed and realized as possible optical interconnects speed and compactness. New plasmonic materials (other for electronic chip communications [4]. Nevertheless, the than metals), or optical materials with metal-like behav- main building block in the next generation networks ar- ior, have recently attracted a lot of attention due to the chitecture is an effective electro-optical modulator. promise they hold to enable low-loss, tunable, CMOS- There are several different physical effects for light compatible devices for photonic technologies. -
Indium Tin Oxide (ITO) for Evaporation Indium Tin Oxide (ITO) for Evaporation
Indium Tin Oxide (ITO) for Evaporation Indium Tin Oxide (ITO) for Evaporation Umicore Thin Film Products Umicore Thin Film Products, a globally active business unit within the Umicore Group, is one of the leading producers of coating materials for physical vapour deposition, with more than 50 years of experience in this field. Its product portfolio covers a wide range of highly effective sputtering targets and evaporations materials. Indium Tin Oxide can be used in Evaporation Systems for depositing thin conductive transparent layers for a variety of applications such as LED, sensors, and antistatic coatings. The desired combination of electrical conductivity and optical properties is achieved by varying In/Sn mixing ratio and process conditions. Selection of ITO Products for Evaporation Indium Tin Oxide (ITO) for Evaporation Indium Tin Oxide (ITO) for Evaporation Production Process Material Properties Evaporation Characteristics Our ITO evaporation materials are produced from › Chemical formula: In-Sn-oxide ITO fully sublimes. ITO is deposited by reactive or engineered powders by state-of-the-art blending non-reactive electron beam (e-beam) evapora- › Relative density: low density grade: and consolidation techniques. This ensures well tion using Cu-crucibles with Mo-liners (e.g. fitting typical 55 – 70% defined physical properties and uniformity within the tablet size) as well as thermal evaporation the product. The products are designed to be high density grade: > 99% using Mo-boats with cover. applicable in E-beam and thermal evaporation. › Theoretical density: 7.14 g/cm³ (90/10 wt%) The refractory index of ITO films, the degree of transmittance in the visible spectral range, › Appearance: yellowish green the on-set of metallic-like reflectance in the IR Composition (low density) to bluish spectral range and the electrical conductivity can black (high density) Typical composition ratios In/Sn are 95/5, 90/10, be tuned using the composition of the starting 83/7 wt%; other compositions upon request. -
Indium Tin Oxide 97550
PRODUCT DATA SHEET Indium-Tin Oxide (ITO) In2O3: SnO2 Standard ITO Introduction • Primary particles are regularly shaped ranging in size from Indium-tin oxide (ITO, or tin-doped indium oxide) is a 0.4 to 1.0µm mixture of indium(III) oxide (In O ) and tin(IV) oxide (SnO ), 2 3 2 • Agglomerates in size up to approximately 31µm typically 90% In2O3, 10% SnO2 by weight. In powder form it is yellow-green in color, but it is transparent and colorless when deposited as a thin film at thicknesses of 50–300nm. When deposited as a thin film on glass or clear plastic, it functions as a transparent electrical conductor. ITO is normally deposited by a physical vapor deposition process such as D.C. magnetron sputtering or electron beam deposition. Less frequently, ITO can be incorporated in inks using an appropriate film-forming polymer resin and solvent system, and deposited by screen printing albeit with lower transparency and conductivity compared to a physical deposition process. Of the various transparent conductive oxides (TCOs), ITO is considered the premium TCO, having superior conductivity and transparency, stability, and ease of patterning to form transparent circuitry. ITO is used in both LCDs and OLED displays, as well as in plasma, electroluminescent, and electrochromatic displays. It is also utilized in touch panels, antistatic coatings, EMI Fine ITO shielding, aircraft windshields, freezer-case glass for • Primary particles are regularly shaped ranging in size from demisting, and photovoltaic solar cells. A further use is as 0.1 to 1.0µm an IR-coating to reflect heat energy, such as in low-E glass and in low-pressure sodium lamps. -
Organic Solar Cells on Indium Tin Oxide and Aluminum Doped Zinc
Organic solar cells on indium tin oxide and aluminum doped zinc oxide anodes Kerstin Schulze, Bert Maennig, Karl Leo, Yuto Tomita, Christian May, Jürgen Hüpkes, Eduard Brier, Egon Reinold, and Peter Bäuerle Citation: Appl. Phys. Lett. 91, 073521 (2007); View online: https://doi.org/10.1063/1.2771050 View Table of Contents: http://aip.scitation.org/toc/apl/91/7 Published by the American Institute of Physics Articles you may be interested in Aluminum-doped zinc oxide films as transparent conductive electrode for organic light-emitting devices Applied Physics Letters 83, 1875 (2003); 10.1063/1.1605805 Transparent conducting aluminum-doped zinc oxide thin films for organic light-emitting devices Applied Physics Letters 76, 259 (2000); 10.1063/1.125740 Tin doped indium oxide thin films: Electrical properties Journal of Applied Physics 83, 2631 (1998); 10.1063/1.367025 Efficient semitransparent inverted organic solar cells with indium tin oxide top electrode Applied Physics Letters 94, 243302 (2009); 10.1063/1.3154556 Aluminum doped zinc oxide for organic photovoltaics Applied Physics Letters 94, 213301 (2009); 10.1063/1.3142423 Electrical, optical, and structural properties of indium–tin–oxide thin films for organic light-emitting devices Journal of Applied Physics 86, 6451 (1999); 10.1063/1.371708 APPLIED PHYSICS LETTERS 91, 073521 ͑2007͒ Organic solar cells on indium tin oxide and aluminum doped zinc oxide anodes ͒ Kerstin Schulze,a Bert Maennig, and Karl Leo Institut für Angewandte Photophysik, Technische Universität Dresden, George-Bähr-Straße -
Ultra-Low Thermal Conductivity of Nanogranular Indium Tin Oxide Films Deposited by Spray Pyrolysis
Ultra-low Thermal Conductivity of Nanogranular Indium Tin Oxide Films Deposited by Spray Pyrolysis Vladimir I. Brinzari1, Alexandr I. Cocemasov1, Denis L. Nika1,*, Ghenadii S. Korotcenkov2 1E. Pokatilov Laboratory of Physics and Engineering of Nanomaterials, Department of Theoretical Physics, Moldova State University, Chisinau, MD-2009, Republic of Moldova 2Gwangju Institute of Science and Technology, Gwangju 500-712, Republic of Korea Abstract The authors have shown that nanogranular indium tin oxide (ITO) films, deposited by spray pyrolysis on silicon substrate, demonstrate ultralow thermal conductivity ~ 0.84±0.12 Wm- 1K-1 at room temperature. This value is approximately by one order of magnitude lower than that in bulk ITO. The strong drop of thermal conductivity is explained by nanogranular structure and porosity of ITO films, resulting in enhanced phonon scattering on grain boundaries. The experimental results were interpreted theoretically, employing Boltzmann transport equation approach for phonon transport and filtering model for electronic transport. The calculated values of thermal conductivity are in a reasonable agreement with the experimental findings. Our results show that ITO films with optimal nanogranular structure may be prospective for thermoelectric applications. _____________________________ Corresponding author: [email protected] (D.L. Nika) . 1. Introduction Thermoelectric materials are described by a figure of merit ZT, which reveals how well a material converts heat into electrical energy: S 2T ZT (1) where σ, S, κ, and T are the electrical conductivity, Seebeck coefficient or thermopower, thermal conductivity and absolute temperature, respectively. Electrical part of the heat conversion is usually characterized by a power factor PF S 2 . ZT is directly related to the efficiency of thermoelectric energy conversion - the higher ZT means the better efficiency. -
Analyzing the Influences of Work Function Anode on the Performance of OLED
IOSR Journal of Electrical and Electronics Engineering (IOSR-JEEE) e-ISSN: 2278-1676,p-ISSN: 2320-3331, Volume 10, Issue 5 Ver. II (Sep – Oct. 2015), PP 131-135 www.iosrjournals.org Analyzing the influences of work function Anode on the Performance of OLED 1 1 1 Iman Farjamtalab , Alireza Kashaniniya , Reza Sabbaghi-Nadooshan 1(Department of Electrical Engineering/ Central Tehran Branch, Islamic Azad University, Tehran, Iran) Abstract: In this work, we investigate the effect of increasing the work function of the anode on luminancepower and recombination rate. For this purpose, we choose a high-work function anode, and a low- work function anode. Then, we investigate their influences on luminance power and recombination rate. Therefore, two organic light-emitting diodes are designed by utilizing the indium tin oxide (ITO) anode and zinc oxide (ZnO) anode, and then we compare their performance. We utilize Langevin model and Poole-Frenkel model to analyze the OLEDs. The results indicate that increasing work function anode affects increasing luminance power, anode current and recombination rate. Keywords: OLED; work function anode; ITO; ZnO; work function I. Introduction By studying the different reports, we understand that there are various factors that influence on performance such as band gap, conductance, and work function. Transparent indium tin oxide (ITO) is commonly used as the anode in the organic electronic devices such as organic light-emitting diodes (OLEDs) and organic photovoltaic devices (OPVs) according to its high conductivity and excellent transmission of light [1–2]. However, ITO is toxic, expensive, and inflexible [3–4]. In addition, the graphene is suitable for the future portable electronics because it has high transparency in visible wavelength and better flexibility than the existing transparent conductive electrodes (TCEs) such as ITO, aluminum zinc oxide (AZO), and indium zinc oxide (IZO) [5]. -
Investigation of Indium Tin Oxide-Titanium Dioxide Interconnection Layers for Perovskite-Silicon Tandem Solar Cells
Alma Mater Studiorum · Università di Bologna Scuola di Scienze Dipartimento di Fisica e Astronomia Corso di Laurea Magistrale in Fisica Investigation of indium tin oxide-titanium dioxide interconnection layers for perovskite-silicon tandem solar cells Relatore: Presentata da: Prof. Daniela Cavalcoli Jacopo Gasparetto Correlatore: Dott. Jan Christoph Goldschmidt Dott. Armin Richter M.Sc. Alexander Bett Anno Accademico 2016/2017 Abstract In questo lavoro è stato studiato ed investigato in dettaglio una nuova tipologia di stack di layer per interconnettere una cella solare a perovskite (PSC) e una cella solare etero- giunzione al silicio (SHJ) con lo scopo di realizzare in futuro una cella tandem monolitica a due terminali, ove la PSC veste il ruolo di top-cell mentre la cella SHJ quello di bottom-cell. Lo stack consiste in un layer di 20 nm di indium tin oxide (ITO), depositato tramite sputtering, e un film sottile di titanium dioxide (TiO2) depositato tramite differenti tecniche. In una cella SHJ, il layer di ITO costituisce il contatto frontale (top contact) e nel caso di una cella tandem completa svolge la funzione di recombination layer per i portatori di carica generati dalla due singole celle. Il layer di TiO2 è invece il contatto posteriore della PSC e svolge la funzione di electron transport layer (ETL), andando a migliorare l’estrazione degli elettroni foto-generati e quindi l’efficienza della stessa. La presente tesi si focalizza sullo studio di un sandwich ITO/TiO2/ITO, dove il film di TiO2 è stato depositato tramite Thermal Atomic Layer Deposition (T–ALD), Pla- sma Enhanced Atomic Layer Deposition (PE–ALD) ed Electron Beam Physical Vapour Deposition (EBPVD). -
Effect of Silver Nanoparticles with Indium Tin Oxide Thin Layers on Silicon Solar Cells
Appl. Sci. Converg. Technol. 26(4): 91-94 (2017) http://dx.doi.org/10.5757/ASCT.2017.26.4.91 Research Paper Effect of Silver Nanoparticles with Indium Tin Oxide Thin Layers on Silicon Solar Cells Gyujin Oh and Eun Kyu Kim* Department of Physics and Research Institute for Convergence of Basic Sciences, Hanyang University, Seoul 04763, Korea Received June 16, 2017; revised July 29, 2017; accepted July 30, 2017 Abstract AThe effect of localized surface plasmon on silicon substrates was studied using silver nanoparticles. The nanoparticles were formed by self-arrangement through the surface energy using rapid thermal annealing (RTA) technique after the thin nanolayer of silver was deposited by thermal evaporation. By the theoretical calculation based on Mie scattering and dielectric function of air, indium tin oxide (ITO), and silver, the strong peak of scattering cross section of silver nanoparticles was found at 358 nm for air, and 460 nm for ITO, respectively. Accordingly, the strong suppression of reflectance under the condition of induced light of 30o occurred at the specific wavelength which is almost in accordance with peak of scattering cross section. When the external quantum efficiency was measured using silicon solar cells with silver nanoparticles, there was small enhancement peak near the 460 nm wavelength in which the light was resonated between silver nanoparticles and ITO. Keywords: Ag nanoparticle, Localized surface plasmon resonance, Application to solar cells I. Introduction In this paper, silver nanoparticles with ITO on the silicon substrates was examined. Indium tin oxides (ITO) has been The effect of localized surface plasmon is localized extensively used on various kinds of solar cells regardless effect of surface plasmon resonance in the tiny metal of organic and inorganic devices. -
Indium Tin Oxide
INDIUM TIN OXIDE 1. Exposure Data Melting point: volatilizes at 850 °C (In2O3) (Weast, 1970); 1630 °C (SnO2) (HSDB, 2017); 1.1 Identification volatilizes at 1910 °C (commercial formula) (Indium Corporation, 2008) Chem. Abstr. Serv. Reg. No.: 50926-11-9 Boiling point: volatilizes at 850 °C (In2O3) (Weast, 1970); sublimes at 1800–1900 °C Chem. Abstr. Serv. Name: indium tin oxide (SnO2) (HSDB, 2017); sublimes at 982 °C IUPAC systematic name: indium tin oxide (commercial formula) (Indium Corporation, Other common names: ITO, tin indium oxide, 2008) tin doped indium oxide Solubility in water: insoluble (In2O3; SnO2; Molecular formula: In2O3; SnO2 ITO) (HSDB, 2017) Indium tin oxide (ITO) is a yellow-green solid One manufacturer reported that ITO particle mixture of indium oxide (In2O3, CAS No. size varies over the range 0.1–1.0 µm depend- 1312-43-2) and stannic (or tin) oxide (SnO2, ing on grade, with agglomerates varying over CAS No. 18-282-10-5) (Indium Corporation, the range 7–31 µm (Indium Corporation, 2014). The proportion of indium oxide is typi- 2014). cally 90% (Hines et al., 2013), but can vary ITO may contain impurities in small quan- over the range 80–95% (NTP, 2009). As the tities. In the commercial product line of one physicochemical properties of ITO depend ITO fabricator, the total concentration of on the relative proportions of indium and tin impurities (aluminium, antimony, bismuth, oxides, they are presented below separately chromium, copper, iron, lead, magnesium, for both compounds. As an illustration, the nickel, potassium, sodium, titanium, zinc) properties for one commercial formula (exact does not exceed 100 ppm (UMICORE, 2013). -
Transparent Conductive Oxide Thin Films
TECHNICAL PAPER Transparent Conductive Oxide Thin Films ABSTRACT Transparent conductive oxides (TCO) have high optical transmission at visible wavelengths and electrical conductivity close to that of metals. They also reflect near infrared and infrared (i.e., heat) wavelengths, and are used in products ranging from energy efficient low-e windows to photovoltaics. One of their most important uses is for transparent electrical contacts. Virtually all applications involve thin films. TCO’s range from simple binary compounds to exotic ternary and quaternary compounds. Examples of TCO’s are indium tin oxide (ITO), zinc oxide (ZnO), tin oxide, aluminum doped zinc oxide (AZO), indium oxide and cadmium oxide. Cost savings using TCO’s is enormous because material usage is low, they are used in a wide range of energy efficiency products and they increase the efficiency of these products. TCO’s are generally n-type wide bandgap semiconductors (although p-type materials are now being developed) with a relatively high concentration of free electrons in the conduction band. The wide bandgap is responsible for high optical transmittance and free electrons increase electrical conductivity. This article will provide a basic understanding of TCO optical and electrical properties, survey TCO applications and types of TCO’s and deposition processes. INTRODUCTION Transparent conductive oxides (TCO) are used in a wide range of applications, including low-e windows, transparent contacts for solar cells, optoelectronic devices, flat panel displays, liquid crystal devices, touch screens, EMI shielding and automobile window deicing and defogging. These materials have been intensely developed since the late 1970’s but have actually been around for a century.