Application of Membrane Bioreactor Technology to Wastewater Treatment and Reuse
Total Page:16
File Type:pdf, Size:1020Kb
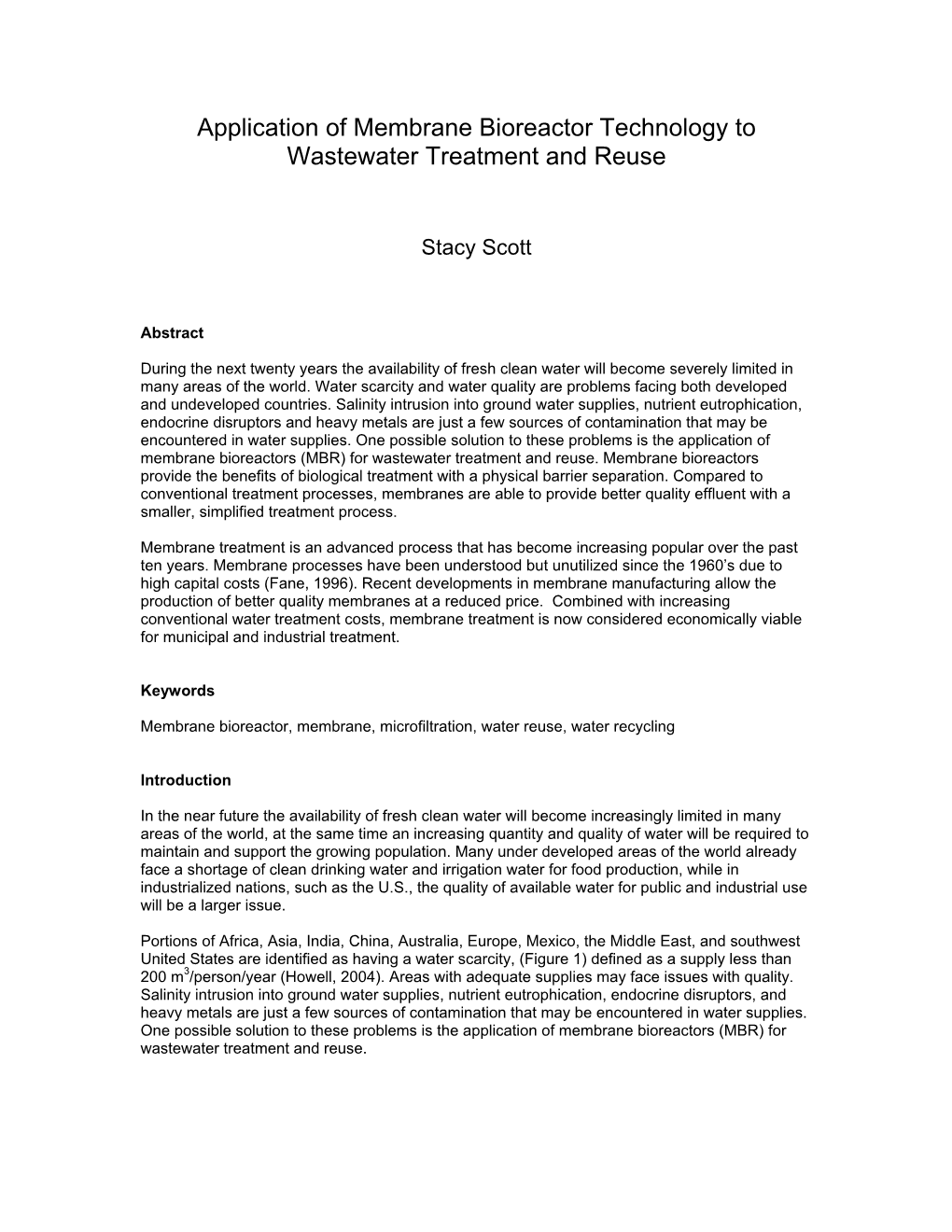
Load more
Recommended publications
-
(MBR) Technology for Wastewater Treatment and Reclamation: Membrane Fouling
membranes Review Membrane Bioreactor (MBR) Technology for Wastewater Treatment and Reclamation: Membrane Fouling Oliver Terna Iorhemen *, Rania Ahmed Hamza and Joo Hwa Tay Department of Civil Engineering, University of Calgary, Calgary, AB T2N 1N4, Canada; [email protected] (R.A.H.); [email protected] (J.H.T.) * Correspondence: [email protected]; Tel.: +1-403-714-7451 Academic Editor: Marco Stoller Received: 14 April 2016; Accepted: 12 June 2016; Published: 15 June 2016 Abstract: The membrane bioreactor (MBR) has emerged as an efficient compact technology for municipal and industrial wastewater treatment. The major drawback impeding wider application of MBRs is membrane fouling, which significantly reduces membrane performance and lifespan, resulting in a significant increase in maintenance and operating costs. Finding sustainable membrane fouling mitigation strategies in MBRs has been one of the main concerns over the last two decades. This paper provides an overview of membrane fouling and studies conducted to identify mitigating strategies for fouling in MBRs. Classes of foulants, including biofoulants, organic foulants and inorganic foulants, as well as factors influencing membrane fouling are outlined. Recent research attempts on fouling control, including addition of coagulants and adsorbents, combination of aerobic granulation with MBRs, introduction of granular materials with air scouring in the MBR tank, and quorum quenching are presented. The addition of coagulants and adsorbents shows a significant membrane fouling reduction, but further research is needed to establish optimum dosages of the various coagulants/adsorbents. Similarly, the integration of aerobic granulation with MBRs, which targets biofoulants and organic foulants, shows outstanding filtration performance and a significant reduction in fouling rate, as well as excellent nutrients removal. -
Biopharma PAT Quality Attributes, Critical Process Parameters & Key
Biopharma PAT Quality Attributes, Critical Process Parameters & Key Performance Indicators at the Bioreactor May 2018 White Paper: Biopharma PAT Quality Attributes, Critical Process Parameters & Key Performance Indicators at the Bioreactor Table of Contents PAT Building Blocks .................................................................................................... 3 PAT for Biopharma ...................................................................................................... 5 Culture & Fermentation Process Types ....................................................................... 6 Monitoring Methods .................................................................................................... 8 Critical Process Parameters ...................................................................................... 10 Critical Quality Attributes & Key Performance Indicators ........................................... 14 Recent Applications of In-situ VCD & TCD ................................................................ 17 Conclusions .............................................................................................................. 19 References ................................................................................................................ 20 Focus Spots Intelligent Arc Sensors for pH and DO in-situ Measurement...................................... 10 Dissolved Oxygen User’s Experiences ...................................................................... 11 In-situ Cell Density -
EPPH2009's Guide 2
Part I Conference Schedule June 14 ~ June 16, 2009 09:00-20:00 Registration Location: Lobby, Friendship Palace, Beijing Friendship Hotel, Beijing Note: You can register at any time during the conference Monday Morning, June 15 Time Activity Location: 2nd floor, Ju Ying Ting in Friendship Palace, Beijing Friendship Hotel 08:30-09:00 Opening Ceremony Plenary Speech 1: Combining Data and Numerical Modeling for Improving the Predictive Ability of Eco- 09:00-09:45 system and Water Quality Model of the Chesapeake Bay and Virginia Tributaries, USA , Prof. Jian Shen, College of William and Mary, USA Plenary Speech 2: Environment and Human Health: Integrating Scientific Developments into Practical En- 09:45-10:30 vironmental Applications for the Improvement of Human Health , Dr. Yue Ge , US Environmental Protection Agency, USA 10:30-10:50 Coffee Break 10:50-11:35 Plenary Speech 3: The 21st Century Water Quality, Safety and Monitoring Issues , Prof. George Zhaoguang Yang , Centre for Advanced Water Technology, Singapore Public Utilities Board, Singapore Monday Noon, June 15 12:00-13:30 Lunch Location: 1st floor, restaurant in Friendship Palace, Beijing Friendship Hotel Monday Afternoon, June 15 Location (1 st floor, Beijing Time Activity Friendship Hotel) Oral_1: Modeling and Measuring of Water Pollution Room 1 in Meeting Hall 14:00 - 15:30 Oral_2: New Wastewater Treatment Technologies Room 2 in Meeting Hall Coffee Break Oral_3: Treatment, Disposal and Discharge of Wastewater Room 3 in Meeting Hall Oral_4: Methods of Monitoring Water Quality Room -
Comparison Between Continuous and Intermittent Model on the Performance of a Pilot-Scale Anoxic/Oxic Membrane Bioreactor for Toilet Wastewater Reuse System
Research Article Adv Biotech & Micro Volume 4 Issue 3 - July 2017 Copyright © All rights are reserved by Lijie Zhou DOI: 10.19080/AIBM.2017.04.555639 Comparison between Continuous and Intermittent Model on the Performance of a Pilot-Scale Anoxic/Oxic Membrane Bioreactor for Toilet Wastewater Reuse System Lijie Zhou1,2*, Shufang Yang3 and Xiufang Shen2 1College of Chemistry and Environmental Engineering, Shenzhen University, China 2State Environmental Protection Key Laboratory of Drinking Water Source Management and Technology, Shenzhen Academy of Environmental Sciences, China 3Shenzhen Municipal Design & Research Institute Co. Ltd, China Submission: May 25, 2017; Published: July 25, 2017 *Corresponding author: Lijie Zhou, College of Chemistry and Environmental Engineering, Shenzhen University, Shenzhen 518060, Shenzhen, State Environmental Protection Key Laboratory of Drinking Water Source Management and Technology, Shenzhen Key Laboratory of Drinking Water Source Safety Control, Shenzhen Key Laboratory of Emerging Contaminants Detection & Control in Water Environment, Shenzhen Academy of Environmental Sciences, Guangdong Shenzhen 518001, China, Tel: ; Fax: ; Email: Abstract Membrane bioreactor (MBR) is a novel and effective technology, which is widely applied in wastewater treatment and water reuse. A generation, continuous and intermittent models were applied, respectively, for this reuse system. This study aimed to identify the comparison betweenpilot-scale continuous anoxic/oxic and MBR intermittent (A/O-MBR) model was on set the up performance to reuse toilet of A/O-MBRwastewater for for toilet a 5-floor wastewater lab building. reuse system. Because Due of tolow remaining volume wastewater sludge and high DO, both continuous and intermittent model showed a great performance on CODCr and NH4+-N removal. -
Stachytarpheta Cayennensis Aqueous Extract, a New Bioreactor Towards Silver Nanoparticles for Biomedical Applications
Journal of Biomaterials and Nanobiotechnology, 2019, 10, 102-119 http://www.scirp.org/journal/jbnb ISSN Online: 2158-7043 ISSN Print: 2158-7027 Stachytarpheta cayennensis Aqueous Extract, a New Bioreactor towards Silver Nanoparticles for Biomedical Applications Francois Eya’ane Meva1,2* , Joel Olivier Avom Mbeng1, Cecile Okalla Ebongue1,3, Carsten Schlüsener2, Ülkü Kökҫam-Demir2, Agnes Antoinette Ntoumba4, Phillipe Belle Ebanda Kedi4, Etienne Elanga1, Evrard-Rudy Njike Loudang1, Moise Henri Julien Nko’o1, Edmond Tchoumbi1, Vandi Deli1, Christian Chick Nanga1, Emmanuel Albert Mpondo Mpondo1, Christoph Janiak2 1Department of Pharmaceutical Sciences, Faculty of Medicine and Pharmaceutical Sciences, University of Douala, Douala, Cameroon 2Institute for Inorganic Chemistry and Structural Chemistry, Heinrich-Heine-University Düsseldorf, Düsseldorf, Germany 3Clinical Biology Laboratory, General Hospital of Douala, Douala, Cameroon 4Department of Animal Biology and Physiology, Faculty of Science, University of Douala, Douala, Cameroon How to cite this paper: Meva, F.E., Abstract Mbeng, J.O.A., Ebongue, C.O., Schlüsener, C., Kökҫam-Demir, Ü., Ntoumba, A.A., Kedi, This study reports the preparation and characterization of silver nanopar- P.B.E., Elanga, E., Loudang, E.-R.N., Nko’o, ticles synthesized by the mediation of the plant weed Stachytarpheta cayen- M.H.J., Tchoumbi, E., Deli, V., Nanga, C.C., nensis through solution method. Ultraviolet visible spectroscopy (UV-Vis) Mpondo, E.A.M. and Janiak, C. (2019) Sta- chytarpheta cayennensis Aqueous Extract, a determines the presence of nanoparticles in the solution. Infrared spectros- New Bioreactor towards Silver Nanopar- copy (IR) proves organic molecules at the particles interface. Powder X-ray ticles for Biomedical Applications. Journal diffraction (PXRD) provides phase composition and crystallinity. -
Bioreactor Studies of Heterologous Protein Production by Recombinant Yeast
BIOREACTOR STUDIES OF HETEROLOGOUS PROTEIN PRODUCTION BY RECOMBINANT YEAST by ZHIGEN ZWNG A thesis presented to the University of Waterloo in fulNlment of the thesis quinment for the degree of Doctor of Philosophy in Chernical Engineering Waterloo, Ontario, Canada, 1997 @ Zhigen Zhang 1997 National tibrary Bibliothi?que nationale l*l dm, du Canada Acquisitions and Acquisitions et Bibliographie Services seMces bubriographiques 395 wellaStreet 395, me wdtingtori OrtawaON KIAW ûtiawaOlJ K1AûN4 Canada Canada Va#& Voinciilline, avm Nom- The author has pteda non- L'auteur a accordé une licence non exclusive licence dowiug the exclwe permettant il Ia National Ijiiiof Canada to Bibliothèque nationale du Cadade reproduce, 10- disttibute or sell reprodnire, *, distn'buerou copies of bis/her thesis by any means vendre des copies de sa thése de and in any fonn or fomLaf making qyelqy manière et sous quelque this thesis avaiiable to interested forme que ce soit pour mettre des persofls- exemplaires de cette thèse à la disposition des persornes intéressées. The auîhor retains owndpof the L'auteur conserve la propriété du copyright m Merthesis. Neither droit d'auteur qui protège sa thèse. Ni the thesis nor substsmtial extracts la thèse ni &s extmits substantiels de fiom it may be printed or otherwiSe celleci ne doivent être imprimés ou reproduced with the author's autrement reproduits sans son permission. autorisalian, nie University of Waterloo requin% the signatures of ali pesons using or photocopying this thesis. Please sign below. and give address and dite. ABSTRACT Fundamend enginee~gstudies were carried out on heterologous protein production using a recombinant Saccharomyces cerevisiae sPain (C468fpGAC9) which expresses Aspergillus mamon glucoamylase gene and secretes glucoamylase into the extracellular medium, as a model system. -
Guide to Biotechnology 2008
guide to biotechnology 2008 research & development health bioethics innovate industrial & environmental food & agriculture biodefense Biotechnology Industry Organization 1201 Maryland Avenue, SW imagine Suite 900 Washington, DC 20024 intellectual property 202.962.9200 (phone) 202.488.6301 (fax) bio.org inform bio.org The Guide to Biotechnology is compiled by the Biotechnology Industry Organization (BIO) Editors Roxanna Guilford-Blake Debbie Strickland Contributors BIO Staff table of Contents Biotechnology: A Collection of Technologies 1 Regenerative Medicine ................................................. 36 What Is Biotechnology? .................................................. 1 Vaccines ....................................................................... 37 Cells and Biological Molecules ........................................ 1 Plant-Made Pharmaceuticals ........................................ 37 Therapeutic Development Overview .............................. 38 Biotechnology Industry Facts 2 Market Capitalization, 1994–2006 .................................. 3 Agricultural Production Applications 41 U.S. Biotech Industry Statistics: 1995–2006 ................... 3 Crop Biotechnology ...................................................... 41 U.S. Public Companies by Region, 2006 ........................ 4 Forest Biotechnology .................................................... 44 Total Financing, 1998–2007 (in billions of U.S. dollars) .... 4 Animal Biotechnology ................................................... 45 Biotech -
Pharmaceutical Review
Pharmaceutical Review Pharm. Bioprocess. (2013) 1(2), 167–177 Single-use bioreactors for microbial cultivation Single-use bioreactors are commonly used in the biopharmaceutical industry today, Nico MG Oosterhuis*1, Peter however, they are mostly limited to mammalian cell culture processes. For microbial Neubauer2 & Stefan Junne2 processes, concepts including the CELL-tainer® technology provide comparable 1CELLution Biotech BV, Dr AF oxygen mass transfer such as in stirred tank reactors. Data obtained with 15 and Philipsweg 15A, 9403AC Assen, The Netherlands 120 l working volumes indicate excellent performance with Escherichia coli and 2Chair of Bioprocess Engineering, Corynebacterium glutamicum cultures. Therefore, this type of single-use bioreactor is Institute of Biotechnologie, Technische applicable in biopharmaceutical processes, and also in a seed train for bulk chemicals Universität Berlin, Germany production such as amino acid production. It is expected that single-use technologies *Author for correspondence: will be applied ever more frequently in microbial-fed batch cultivation processes in E-mail: nico.oosterhuis@ cellutionbiotech.com combination with improved monitoring and control. Single-use bioreactors (SUBs, also often re- for cultivation of plant cells [1] . A step towards ferred to as disposable bioreactors) are nowa- innovation was achieved by the release of the days widely applied in the biopharmaceutical first single-use wave-mixed bioreactor for the industry. The scale is not restricted to labo- cultivation of shear-sensitive cells by Singh in ratory use, as reactors with working volumes 1999 [2]. The wide spread of the technology up to the m³-scale exist and can also be used has led to numerous optimiz ations and dif- for good manufactur practice processes. -
Study on Anaerobic Landfill Leachate Treatability by Membrane Bioreactor
2010 International Conference on Biology, Environment and Chemistry IPCBEE vol.1 (2011) © (2011) IACSIT Press, Singapore Study on Anaerobic Landfill Leachate Treatability by Membrane Bioreactor Rouhallah Mahmoudkhani, Amir Hessam Hassani, Ali Torabian Seyed Mahdi Borghei Faculty of Civil and Environmental Engineering Department of Environmental and Energy University of Tehran Science and Research Branch, Islamic Azad University Tehran, Iran Tehran, Iran E-mail: [email protected] E-mail: [email protected] Abstract— This study was undertaken to examine feasibility of of contaminants, it cannot be easily treated by conventional biological treating of landfill leachate that was collected from methods. Therefore, a number of scientists around the world Tehran municipal landfill with about 0.5 – 1 year old. Average have intensively focused on the combination of biological COD of the leachate in aerobic submerged membrane and physico-chemical treatment systems for effective bioreactor is 68000 mg/L. The reactor with a working volume leachate treatment [18, 1]. of 175 L, having membrane module (Hollow fiber) with pore Alternative treatments have been reviewed. Briefly, size of 0.1 µm was used in this study. The dissolved oxygen leachate can be recirculated to the same landfill or treated by concentration (DO) was maintained at 3.2 mg/L and solid different methods: biological, aerobic, anaerobic methods retention times (SRTs) and hydraulic retention times (HRT) and/or nitrification–denitrification to remove organic matter were controlled at 55 and 15 days respectively. Following that and ammonium nitrogen. Biological processes to remove the mixed liquor suspended solids (MLSS) was stabilized at 6.3 organic matter can be effective for young leachate with a g/l. -
Nanotechnology Applications for Food and Bioprocessing Industries
nd M y a ed g ic lo i o n i e B Trujillo et al., Biol Med (Aligarh) 2016, 8:3 DOI: 10.4172/0974-8369.1000289 ISSN: 0974-8369 Biology and Medicine Research Article Open Access Nanotechnology Applications for Food and Bioprocessing Industries Luis E Trujillo1*, Rodrigo Ávalos1, Silvana Granda1, Luis Santiago Guerra1 and José M País-Chanfrau2 1Industrial Biotechnology and Bioproducts Research Group, Universidad de las Fuerzas Armadas (ESPE), CENCINAT, Ecuador 2Universidad Técnica del Norte (UTN), Avenida 17 de julio, 5-21 y General José María Córdoba. CP 199, Ibarra, Imbabura, Ecuador *Corresponding author: Luis E. Trujillo, Industrial Biotechnology and Bioproducts Rearch Group, Universidad de las Fuerzas Armadas (ESPE), Ecuador, Tel: +81-3-5800-8653; Fax: +81-3-3811-6822; E-mail: [email protected] Received date: March 18, 2016; Accepted date: May 10, 2016; Published date: May 16, 2016 Copyright: © 2016 Trujillo LE, et al. This is an open-access article distributed under the terms of the Creative Commons Attribution License, which permits unrestricted use, distribution and reproduction in any medium, provided the original author and source are credited. Abstract Nanoscience is an emerging technology today with great application in different fields. Biocatalysts design, identification of different bacterial strains, monitoring the quality of food by different biosensors, food packaging with smart systems, active, intelligent and nano-encapsulation of bioactive food compounds are examples of some of these applications in the food industry. In this paper, some topics related to the potential of nanotechnology in the food industry are updated. In addition, some concerns about nanotechnology application in this popular industry are also discussed. -
Thermal Effects
Thermal Effects Ming Yan1,2,*, Panyue Zhang1,2, Guangming Zeng1,2 ABSTRACT: This review focuses on the research Biological Nitrogen and Phosphorus Removal literatures published in 2015 relating to topics of thermal The short-term effect of temperature on the effects in water pollution control. This review is divided maximum biomass specific activity of anaerobic into the following sections: biological nitrogen and ammonium oxidizing (anammox) bacteria was reported by phosphorus removal, wastewater treatment for organic Lotti et al. (2015). The results indicated that for the conversion, industrial wastewater treatment, anaerobic anammox conversion, the temperature dependency could digestion of sewage sludge and solid waste, sludge biochar not be accurately modeled by one single Arrhenius preparation and application, pyrolysis of sewage sludge, coefficient as typically applied for other biological reduction heavy metal in sewage sludge and soil, and other processes. The temperature effect increased at lower issues of wastewater and sludge treatment. temperatures. Adapted anammox sludge had a higher specific rate at lower temperature. Anammox sludge KEYWORDS: thermal effects, biological nitrogen and cultivated in an aerated partial nitritation/anammox process phosphorus removal, wastewater treatment for organic and/or in biofilm seemed to be less influenced be a conversion, industrial wastewater treatment, anaerobic decrease in temperature than anammox sludge grown under digestion of sewage sludge and solid waste, sludge biochar non-arated conditions and/or in suspension. preparation and application, pyrolysis of sewage sludge, Lackner et al. (2015) compared partial nitritation- reduction heavy metal in sewage sludge and soil. anammox in two laboratory-scale reactors, a sequencing batch reactor (SBR) and a moving bed biofilm reactor doi: 10.2175/106143016X14696400495730 (MBBR). -
Novel Membrane Bioreactors and Constructed Wetlands for Treatment of Pre Processed Animal Rendering Plant Waste
Novel membrane bioreactors and constructed wetlands for treatment of pre- processed animal rendering plant wastewater in Scotland Scholz, M Title Novel membrane bioreactors and constructed wetlands for treatment of pre-processed animal rendering plant wastewater in Scotland Authors Scholz, M Type Article URL This version is available at: http://usir.salford.ac.uk/id/eprint/16529/ Published Date 2006 USIR is a digital collection of the research output of the University of Salford. Where copyright permits, full text material held in the repository is made freely available online and can be read, downloaded and copied for non-commercial private study or research purposes. Please check the manuscript for any further copyright restrictions. For more information, including our policy and submission procedure, please contact the Repository Team at: [email protected]. E-WAter Official Publication of the European Water Association (EWA) © EWA 2006 M. Scholz 1 Comparison of novel membrane bioreactors and constructed wetlands for treatment of pre-processed animal rendering plant wastewater in Scotland The performance of a novel industrial membrane bioreactor (MBR) comprising denitrification, nitrification and ultrafiltration for the secondary treatment of primary treated animal rendering wastewater has been compared with an experimental, low-cost and novel vertical-flow constructed treatment wetland planted with Typha latifolia L. The process wastewater followed pre-treatment by dissolved air flotation (DAF). The DAF effluent gave highly variable chemical oxygen demand (COD) and ammonia of 5200 (± 2050) and 490 (± 270) mg/l, respectively. The MBR effluent for COD and ammonia was 45 and 63 mg/l, respectively. The treatment performance of the constructed wetland for COD, ammonia and suspended solids was 167, 63 and 15 mg/l, respectively.