LSUG 2011 Revised CR 2
Total Page:16
File Type:pdf, Size:1020Kb
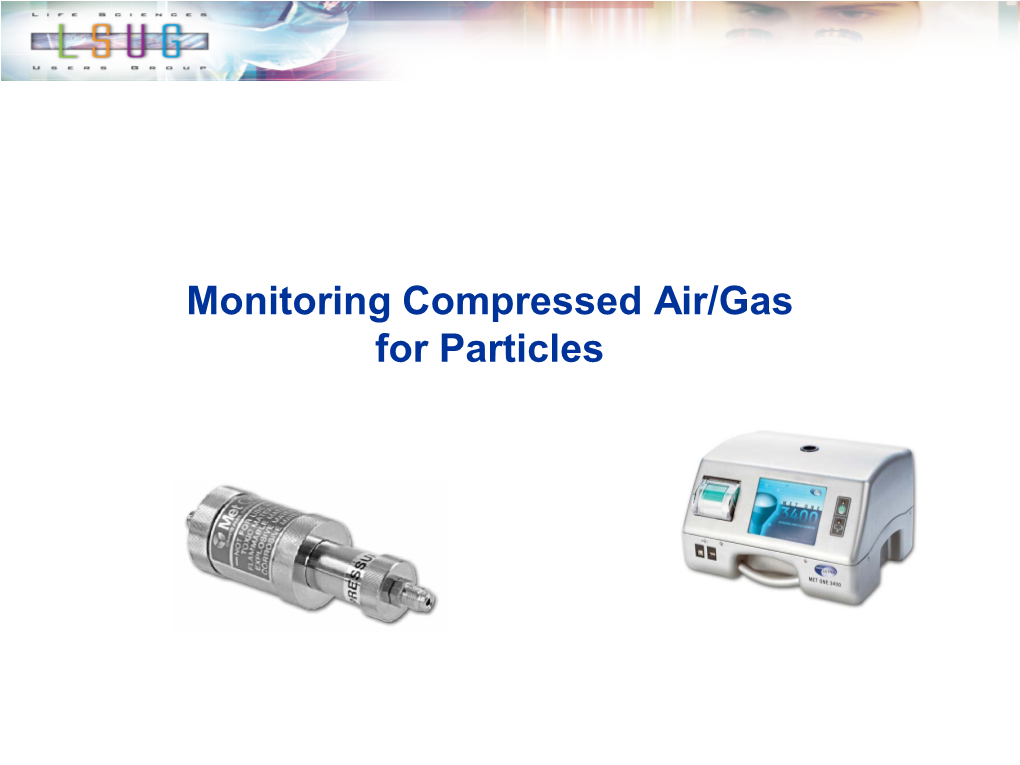
Load more
Recommended publications
-
Iso 14644-4:2001(E)
INTERNATIONAL ISO STANDARD 14644-4 First edition 2001-04-01 Cleanrooms and associated controlled environments — Part 4: Design, construction and start-up Salles propres et environnements maîtrisés apparentés — Partie 4: Conception, construction et mise en fonctionnement Reference number ISO 14644-4:2001(E) © ISO 2001 Dit document mag slechts op een stand-alone PC worden geïnstalleerd. Gebruik netwerk is alleen toegestaan als een aanvullende licentieovereenkomst voor netwerkgebruik met NEN is afgesloten. This document may only be used on a stand-alone PC. Use in network is permitted when supplementary license agreement for use in a network with NEN has been concluded. Dit document is door NEN onder licentie verstrekt aan: / This document has been supplied under license by NEN to: GTI N.V. M.R. Janmohamed 2004/10/15 ISO 14644-4:2001(E) PDF disclaimer This PDF file may contain embedded typefaces. In accordance with Adobe's licensing policy, this file may be printed or viewed but shall not be edited unless the typefaces which are embedded are licensed to and installed on the computer performing the editing. In downloading this file, parties accept therein the responsibility of not infringing Adobe's licensing policy. The ISO Central Secretariat accepts no liability in this area. Adobe is a trademark of Adobe Systems Incorporated. Details of the software products used to create this PDF file can be found in the General Info relative to the file; the PDF-creation parameters were optimized for printing. Every care has been taken to ensure that the file is suitable for use by ISO member bodies. -
2009-03-21 - Prague, Czech Republic Copyright © Crane Softwrights Ltd
Introduction to Code Lists in XML (Using Controlled Vocabularies in XML Documents) Crane Softwrights Ltd. http://www.CraneSoftwrights.com +//ISBN 1-894049::CSL::Presentation::UBL//DOCUMENT Introduction to Code Lists in XML 2009-02-07 17:00UTC//EN XML Prague 2009 http://www.CraneSoftwrights.com 2009-03-21 - Prague, Czech Republic Copyright © Crane Softwrights Ltd. Introduction to Code Lists in XML Introduction to Code Lists in XML (Using Controlled Vocabularies in XML Documents) Crane Softwrights Ltd. http://www.CraneSoftwrights.com Copyrights - Other original material herein is copyright (C) 1998-2009 Crane Softwrights Ltd. This is commercial material and may not be copied or distributed by any means whatsoever without the expressed permission of Crane Softwrights Ltd. Disclaimer - By purchasing and/or using any product from Crane Softwrights Ltd. ("Crane"), the product user ("reader") understands that this product may contain errors and/or other inaccuracies that may result in a failure to use the product itself or other software claiming to utilize any proposed or finalized standards or recommendations referenced therein. Consequently, it is provided "AS IS" and Crane disclaims any warranty, conditions, or liability obligations to the reader of any kind. The reader understands and agrees that Crane does not make any express, implied, or statutory warranty or condition of any kind for the product including, but not limited to, any warranty or condition with regard to satisfactory quality, merchantable quality, merchantability or fitness for any particular purpose, or such arising by law, statute, usage of trade, course of dealing or otherwise. In no event will Crane be liable for (a) punitive or aggravated damages; (b) any direct or indirect damages, including any lost profits, lost savings, damaged data or other commercial or economic loss, or any other incidental or consequential damages even if Crane or any of its representatives have been advised of the possibility of such damages or they are foreseeable; or (c) for any claim of any kind by any other party. -
Appendix No. 1 Specifications
Government of Canada Existing Building Renovation Issued for Tender 144202775.200 St. Paul, Alberta Appendix No. 1 Specifications June 8, 2016 GOVERNMENT OF CANADA Existing Building Renovation Section 00 01 01 St. Paul, Alberta, Canada SPECIFICATION INDEX Project No.: 144202775.200 Page 1 of 4 DIVISION 02 EXISTING CONDITIONS Section 02 41 16 Selective Demolition ................................................................... 5 Section 02 83 33 Lead Abatement and Removal ..................................................... 9 Section 02 83 33.01 Initial Lead Surface Contamination Assessment ....................... 10 DIVISION 03 CONCRETE Section 03 10 00 Concrete Forming and Accessories ........................................... 10 Section 03 20 00 Concrete Reinforcing ................................................................... 7 Section 03 30 00 Cast-in Place Concrete ............................................................... 15 DIVISION 04 MASONRY Section 04 05 00 Common Work Results for Masonry ........................................... 8 Section 04 05 12 Masonry Mortar ........................................................................... 5 Section 04 05 19 Masonry Anchorage and Reinforcing .......................................... 5 Section 04 22 00 Concrete Unit Masonry ................................................................ 6 DIVISION 05 METALS Section 05 50 00 Metal Fabrications ....................................................................... 9 Section 05 72 00 Stainless Steel Fabrications -
Clean Rooms – Environmental Monitoring
PhEn-602 Notes # 4 J. Manfredi Pharmaceutical Facility Design Spring 2009 1 Clean Rooms and Controlled Environments Basic definitions Clean Room: A room in which the concentration of airborne particles is controlled and contains one or more clean zones Clean Zone: A defined space in which the concentration of airborne particles is controlled to meet a specified airborne particulate class. Pharmaceutical Facility Design Spring 2009 2 Clean Rooms and Controlled Environments Federal Standard 209E (FS-209E) provides Clean Room Classes Rooms classified based on number of particles > 0.5 micron per cubic foot Class descriptions still in use today. FS 209E is concerned about the following particle sizes, in microns: 0.1, 0.2, 0.3, 0.5, 5.0 Pharmaceutical Facility Design Spring 2009 3 Clean Rooms and Controlled Environments Types of Contaminants Viable Particulates Non-Viable Particulates Pharmaceutical Facility Design Spring 2009 4 Controlled Environments - Types of Contaminants Non-viable Particulates Metal specks, fiber from clothing Obtained from: Equipment, people, tools Viable (micro-organisms) Bacteria Yeast, molds Obtained from: People, outside air, water, equipment, tools, excipients, active ingredients Pharmaceutical Facility Design Spring 2009 5 Clean Rooms and Controlled Environments Sources of particulate generation Internal: Personnel Normally the highest source of contamination Process Air conditioning system Introduction of raw materials Introduction of equipment and materials External Outside air Pharmaceutical Facility Design Spring 2009 6 Clean Rooms and Controlled Environments Some interesting facts: Visible indoor air particles constitute only about 10% of particles present in indoor air. It may be possible to see particles as small as 10 microns It may be possible to see particles as small as 10 microns under favorable conditions. -
Dell EMC Poweredge R640 Technical Guide
Dell EMC PowerEdge R640 Technical Guide Regulatory Model: E39S Series Regulatory Type: E39S001 June 2021 Rev. A08 Notes, cautions, and warnings NOTE: A NOTE indicates important information that helps you make better use of your product. CAUTION: A CAUTION indicates either potential damage to hardware or loss of data and tells you how to avoid the problem. WARNING: A WARNING indicates a potential for property damage, personal injury, or death. © 2017 - 2021 Dell Inc. or its subsidiaries. All rights reserved. Dell, EMC, and other trademarks are trademarks of Dell Inc. or its subsidiaries. Other trademarks may be trademarks of their respective owners. Contents Chapter 1: Product overview......................................................................................................... 5 Introduction...........................................................................................................................................................................5 New technologies................................................................................................................................................................ 5 Chapter 2: System features...........................................................................................................7 Product comparison............................................................................................................................................................ 7 Technical specifications.................................................................................................................................................... -
ISO Types 1-6: Construction Code Descriptions
ISO Types 1-6: Construction Code Descriptions ISO 1 – Frame (combustible walls and/or roof) Typically RMS Class 1 Wood frame walls, floors, and roof deck Brick Veneer, wood/hardiplank siding, stucco cladding Wood frame roof with wood decking and typical roof covers below: *Shingles *Clay/concrete tiles *BUR (built up roof with gravel or modified bitumen) *Single-ply membrane *Less Likely metal sheathing covering *May be gable, hip, flat or combination of geometries Roof anchorage *Toe nailed *Clips *Single Wraps *Double Wraps Examples: Primarily Habitational, max 3-4 stories ISO 2 – Joisted Masonry (JM) (noncombustible masonry walls with wood frame roof) Typically RMS Class 2 Concrete block, masonry, or reinforced masonry load bearing exterior walls *if reported as CB walls only, verify if wood frame (ISO 2) or steel/noncombustible frame roof (ISO 4) *verify if wood frame walls (Frame ISO 1) or wood framing in roof only (JM ISO 2) Stucco, brick veneer, painted CB, or EIFS exterior cladding Floors in multi-story buildings are wood framed/wood deck or can be concrete on wood or steel deck. Wood frame roof with wood decking and typical roof covers below: *Shingles *Clay/concrete tiles *BUR (built up roof with gravel or modified bitumen) *Single-ply membrane *Less Likely metal sheathing covering *May be gable, hip, flat or combination of geometries Roof anchorage *Toe nailed *Clips *Single Wraps *Double Wraps Examples: Primarily Habitational, small office/retail, max 3-4 stories If “tunnel form” construction meaning there is a concrete deck above the top floor ceiling with wood frame roof over the top concrete deck, this will react to wind forces much the same way as typical JM construction. -
BRIEFING 〈797〉 Pharmaceutical Compounding—Sterile
BRIEFING 797 Pharmaceutical Compounding—Sterile Preparations, USP 41 page 6554 and PF 41(6) [Nov.–Dec. 2015]. 〈 〉 Based on the number and significance of public comments received in response to the revision proposal published in PF 41(6), the USP Compounding Expert Committee is proposing to revise this chapter. The current proposed chapter in PF 44(5) [Sept.–Oct. 2018] is posted online at http://www.uspnf.com/notices/general-chapter-797-proposed-revisions with line numbers. Submit comments using the form available at https://usp.az1.qualtrics.com/jfe/form/SV_3dDhnN2ZVCYh5yJ. The Expert Committee seeks stakeholder feedback on the proposed revisions to the chapter, including the following major changes: 1. Reorganization of the chapter to include section and subsection numbers. Placement of procedural information in boxes. 2. Definition of the scope of the chapter to include sterile compounding activities and exclude administration of medication (e.g., withdrawing doses for administration). 3. Simplified compounded sterile preparation (CSP) microbial risk levels from three (low, medium, and high) to two—Category 1 CSPs and Category 2 CSPs. Category 1 and 2 CSPs are distinguished primarily by the facility in which they are made and the time period within which they must be used, i.e., the beyond-use date (BUD). • Category 1 CSPs have a shorter BUD and may be prepared in an unclassified segregated compounding area (SCA). • Category 2 CSPs have a longer BUD and must be prepared in a cleanroom suite (buffer room with ante-room). 4. Addition of guidance on use and storage of opened or needle- punctured conventionally manufactured products and CSPs. -
Federal Standard 209E for Cleanroom - an Obsolete Document!
FEDERAL STANDARD 209E FOR CLEANROOM - AN OBSOLETE DOCUMENT! By Ir Liew Huey Chyan, P.Eng, APEC Eng, ASEAN Eng, M.IEM, M.IEAust, SM.IEST, M.ASHRAE ABSTRACT The United States (U.S.) Federal Standard 209 (FS 209) was published by the Institute of Environmental Sciences and Technology (IEST), FS 209 was approved for use by the U.S. General Services Administration (GSA) in 1963, making it obligatory for organizations doing work for the United States government. FS 209 has been used widely as the de facto clean room standard in and around the world including in Malaysia, some countries completely adopted FS 209, while others made their own national version, similar to FS 209. Some made minor changes of the classes to comply with the metric system. Australia (AS 1386), France (AFNOR X44101), Germany (VDI 2083:3), Holland (VCCN 1), Japan (JIS-B-9920), Russia (Gost-R 50766), United Kingdom (BS 5295) are among the major national standards that referenced to FS 209. The activities of the ISO Technical Committee ISO/TC209 "Clean rooms and other associated controlled environments" which started in 1993, has effectively and in reality made obsolete what is in FS 209. In addition ISO/TC209 offers broader domestic and international appeal. The ISO clean room standards will be known by their identifying number series, ISO 14644 and ISO 14698. ISO 14644-1 "Classification of Air Cleanliness" standard had became mandatory in the Europe Union (E.U.) since November 1999. In January 2000, the IEST submitted a formal request to the U.S. General Services Administration (GSA) to retire the standard, and the GSA officially did so on November 2001. -
Isoenum Documentation Release 0.4.1
isoenum Documentation Release 0.4.1 Andrey Smelter, Hunter N.B. Moseley Aug 14, 2019 Contents: 1 isoenum 1 1.1 Links...................................................1 1.2 Installation................................................2 1.3 Docker..................................................2 1.4 Development version installation....................................3 1.5 License..................................................3 2 Documentation index: 5 2.1 The isoenum Tutorial...........................................5 2.2 The isoenum Docker Tutorial...................................... 25 2.3 The isoenum API Reference....................................... 46 2.4 Release History.............................................. 54 2.5 License.................................................. 56 3 Indices and tables 59 Python Module Index 61 Index 63 i ii CHAPTER 1 isoenum Isotopic (iso) enumerator (enum) - enumerates isotopically resolved InChI (International Chemical Identifier) for metabolites. The isoenum Python package provides command-line interface that allows you to enumerate the possible isotopically-resolved InChI from one of the Chemical Table file( CTfile) formats (i.e. molfile, SDfile) used to describe chemical molecules and reactions as well as from InChI itself. See Tutorial documentation for usage examples of isoenum Python package as well as isoenum docker container. 1.1 Links • isoenum @ GitHub • isoenum @ PyPI 1 isoenum Documentation, Release 0.4.1 • isoenum @ DockerHub • isoenum @ ReadTheDocs 1.2 Installation The isoenum package runs under Python 2.7 and Python 3.4+. Use pip to install. 1.2.1 Install on Linux, Mac OS X python3-m pip install isoenum 1.2.2 Install on Windows py-3-m pip install isoenum 1.2.3 Dependencies The isoenum Python package requires a non-pip-installable dependency: the Open Babel chemistry library version 2.3.90 or later, which relies on InChI library version 1.0.4 or later to perform InChI conversions. -
FFTA FIRST 5.0 Design Guide (Pdf)
Complimentary Design Guide 5.0 Flexographic Image Reproduction Specifications & Tolerances Complimentary Design Guide An FTA Strategic Planning Initiative Project The Flexographic Technical Association has made this FIRST 5.0 supplement of the design guide available to you, and your design partners, as an enhancement to your creative process. To purchase the book in it’s entirety visit: www.flexography.org/first Copyright, © 1997, ©1999, ©2003, ©2009, ©2013, ©2014 by the Flexographic Technical Association, Inc. All rights reserved, including the right to reproduce this book or portions thereof in any form. Library of Congress Control Number: 2014953462 Edition 5.0 Published by the Flexographic Technical Association, Inc. Printed in the United States of America Inquires should be addressed to: FTA 3920 Veterans Memorial Hwy Ste 9 Bohemia NY 11716-1074 www.flexography.org International Standard Book Number ISBN-13: 978-0-9894374-4-8 Content Notes: 1. This reference guide is designed and formatted to facilitate ease of use. As such, pertinent information (including text, charts, and graphics) are repeated in the Communication and Implementation, Design, Prepress and Print sections. 2. Registered trademark products are identified for information purposes only. All products mentioned in this book are trademarks of their respective owner. The author and publisher assume no responsibility for the efficacy or performance. While every attempt has been made to ensure the details described in this book are accurate, the author and publisher assume no responsibility for any errors that may exist, or for any loss of data which may occur as a result of such errors. .1 ii Flexographic Image Reproduction Specifications & Tolerances 5.0 INTRODUCTION The Mission of FIRST FIRST seeks to understand customers’ graphic requirements for reproduction and translate those aesthetic requirements into specifications for each phase of the flexographic printing process including: customers, designers, prepress providers, raw material & equipment suppliers, and printers. -
[Pdf] ISO Cleanroom Standards and Federal Standard
FS209E and ISO Cleanroom Standards Terra Universal is the leading expert in the design and fabrication of critical-environment applications. We offer a complete range of equipment, furnishing and supplies for cleanroooms and laboratories. Following are the rigorous standards to which Terra Universal adheres. Before global cleanroom classifications and standards were adopted by the International Standards Organization (ISO), the U.S. General Service Administration’s standards (known as FS209E) were applied virtually worldwide. However, as the need for international standards grew, the ISO established a technical committee and several working groups to delineate its own set of standards. FS209E contains six classes, while the ISO 14644-1 classification system adds two cleaner standards and one dirtier standard (see chart below). The “cleanest” cleanroom in FS209E is referred to as Class 1; the “dirtiest” cleanroom is a class 100,000. ISO cleanroom classifications are rated according to how much particulate of specific sizes exist per cubic meter (see second chart). The “cleanest” cleanroom is a class 1 and the “dirtiest” a class 9. ISO class 3 is approximately equal to FS209E class 1, while ISO class 8 approximately equals FS209E class 100,000. By law, Federal Standard 209E can be superseded by new international standards. It is expected that 209E will be used in some industries over the next five years, but that eventually it will be replaced internationally by ISO 14644-1. Before global cleanroom classifications and standards were adopted by the International Standards Organization (ISO), the U.S. General Service Administration’s standards (known as FS209E) were applied virtually worldwide. -
International Standard Iso 14644-1:2015(E)
INTERNATIONAL ISO STANDARD 14644-1 Second edition 2015-12-15 Cleanrooms and associated controlled environments — Part 1: Classification of air cleanliness by particle concentration Salles propres et environnements maîtrisés apparentés — Partie 1: Classification de la propreté particulaire de l’air Reference number ISO 14644-1:2015(E) Este documento ha sido adquirido por CVTEC el 3 de Febrero de 2016. © ISO 2015 Para poder utilizarlo en un sistema de red interno, deberá disponer de la correspondiente licencia de AENOR ISO 14644-1:2015(E) COPYRIGHT PROTECTED DOCUMENT © ISO 2015, Published in Switzerland All rights reserved. Unless otherwise specified, no part of this publication may be reproduced or utilized otherwise in any form orthe by requester. any means, electronic or mechanical, including photocopying, or posting on the internet or an intranet, without prior written permission. Permission can be requested from either ISO at the address below or ISO’s member body in the country of Ch. de Blandonnet 8 • CP 401 ISOCH-1214 copyright Vernier, office Geneva, Switzerland Tel. +41 22 749 01 11 Fax +41 22 749 09 47 www.iso.org [email protected] ii Este documento ha sido adquirido por CVTEC el 3 de Febrero de 2016.© ISO 2015 – All rights reserved Para poder utilizarlo en un sistema de red interno, deberá disponer de la correspondiente licencia de AENOR ISO 14644-1:2015(E) Contents Page Foreword ........................................................................................................................................................................................................................................iv