Characterisation of Recycled Aluminium Swarf Into Fine Powder for MIM Applications Via Ball Milling
Total Page:16
File Type:pdf, Size:1020Kb
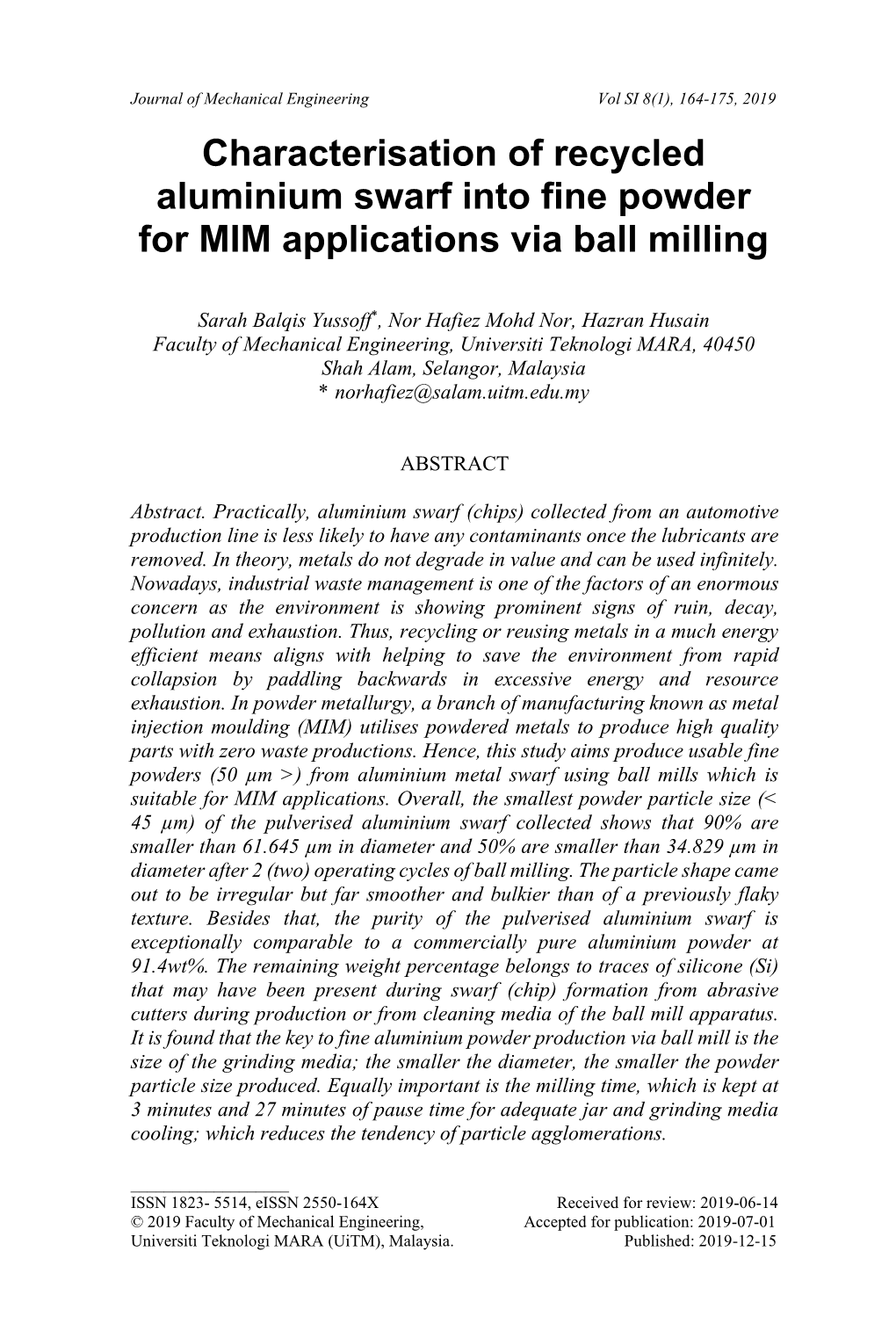
Load more
Recommended publications
-
Extrinsic Allergic
Chest clinic Thorax: first published as 10.1136/thoraxjnl-2014-205251 on 8 July 2014. Downloaded from CASE BASED DISCUSSION Lesson of the month: extrinsic allergic (bronchiolo) alveolitis and metal working fluids Paul Cullinan,1 Eva D’Souza,2 Rachel Tennant,3 Chris Barber4 1Department of Occupational INTRODUCTION since he had never kept them, a probable attribu- and Environmental Medicine, One of us was asked to consider a diagnosis of tion to ‘birds’ had been made. He had been Imperial College (NHLI) and Royal Brompton Hospital, occupational asthma for a man who had worked treated, intermittently, with high doses of prednis- London, UK for 20 years as a metal turner in a large, modern olone with no evidence of lasting benefit. The 2Health Management Limited, factory producing specialised machine parts. He survey of other employees and subsequent specialist London, UK 3 described a 2 year history of severe breathlessness investigation established a further two cases of Department of Respiratory that improved when he was not at work. His spir- occupational bronchioloalveolitis with probable Medicine, Northwick Park – Hospital, London, UK ometry was restrictive with a FEV1 of 1.35 L (40% onset in 2010 2011. 4Centre for Workplace Health, predicted) and FVC of 1.8 L (45% predicted), a Northern General Hospital, ratio of 75%. Other lung function measurements DISCUSSION Brearley Outpatient, Herries indicated gas trapping; his TLC was 5.01 L (79% These five men had a diagnosis and an occupation in Road, Sheffield, UK predicted) and RV/TLC 170% predicted. A high common; all were metal machinists in a single Correspondence to resolution CT scan of his lungs revealed a wide- factory, a job that entails exposure to mists of metal Dr Paul Cullinan, Department spread ‘mosaic’ pattern of attenuation indicative of working fluids (MWFs). -
Extrinsic Allergic
Thorax Online First, published on August 18, 2014 as 10.1136/thoraxjnl-2014-205251 Chest clinic CASE BASED DISCUSSION Thorax: first published as 10.1136/thoraxjnl-2014-205251 on 8 July 2014. Downloaded from Lesson of the month: extrinsic allergic (bronchiolo) alveolitis and metal working fluids Paul Cullinan,1 Eva D’Souza,2 Rachel Tennant,3 Chris Barber4 1Department of Occupational INTRODUCTION since he had never kept them, a probable attribu- and Environmental Medicine, One of us was asked to consider a diagnosis of tion to ‘birds’ had been made. He had been Imperial College (NHLI) and Royal Brompton Hospital, occupational asthma for a man who had worked treated, intermittently, with high doses of prednis- London, UK for 20 years as a metal turner in a large, modern olone with no evidence of lasting benefit. The 2Health Management Limited, factory producing specialised machine parts. He survey of other employees and subsequent specialist London, UK 3 described a 2 year history of severe breathlessness investigation established a further two cases of Department of Respiratory that improved when he was not at work. His spir- occupational bronchioloalveolitis with probable Medicine, Northwick Park – Hospital, London, UK ometry was restrictive with a FEV1 of 1.35 L (40% onset in 2010 2011. 4Centre for Workplace Health, predicted) and FVC of 1.8 L (45% predicted), a Northern General Hospital, ratio of 75%. Other lung function measurements DISCUSSION Brearley Outpatient, Herries indicated gas trapping; his TLC was 5.01 L (79% These five men had a diagnosis and an occupation in Road, Sheffield, UK predicted) and RV/TLC 170% predicted. -
UKLA HSE Good Practice Guide for Safe Handling and Disposal of Metalworking Fluids
Good Practice Guide for Safe Handling and Disposal of Metalworking Fluids Version 2.2 Table of Amendments Page Section Amendment 7 Right hand column, paragraph 2 removed 0.4mm in brackets 30 Right hand column, paragraph 1 removed 0.4mm in brackets 42 Left hand column, 5th section in Table 4th row headed ‘Clear’ has been changed labelled ‘Tramp Oil’ to ‘None’ Disclaimer: This guide has been developed by the United Kingdom Lubricants Association (UKLA) Metalworking Fluid Product Stewardship Group (MWFPSG) with support from the Health and Safety Executive (HSE) and other industry experts. The contents of the guide represent UKLA members’ current knowledge about good practice with advice from the HSE. This guide contains advice which should be considered together with your knowledge and the advice of your lubricant supplier. No warranty either expressed or implied is provided to users of this guide by either both UKLA and/or HSE. This guide provides advice to dutyholders who ultimately have responsibility for protecting the health and safety of their employees. Future changes to this guide may be required to address changes to technology and working practices. (www.ukla.org.uk) The Health and Safety Executive (HSE) was involved with the UKLA MWFPSG in producing this guidance. HSE endorses the guidance, as it follows a sensible and proportionate approach to managing health and safety. Version 2.2, January 2021 UNITED KINGDOM LUBRICANTS ASSOCIATION Good Practice Guide for Safe Handling and Disposal of Metalworking Fluids I am pleased to introduce the revised guide on managing MWF and also provides advice for the good practice for safe handling and disposal operators. -
Aluminium SWARF Handling Ofgrinding Sludge Metal Swarf
stEEl SWARF GuidelineS foralloy swarf eco-friendlyBRASS Swarf aluminium SWARF handling ofgrinding sludge metal swarf An Initiative of associations representing Bundesvereinigung Deutscher producers of industrial waste, Stahlrecycling- und Fachverband Metallwaren- Entsorgungsunternehmen e.V. und verwandte Industrien e.V. hauliers and freight forwarders, the metal-recycling sector and recyclers vsi-schmierstoffe.de stEEl SWARF alloy swarf BRASS Swarf aluminium SWARF grinding sludge IMPRINT: These guidelines are an initiative of associations representing producers of industrial waste, hauliers and freight forwarders, the metal-recycling sector and recyclers. Status: November 2014 Editors: Birgit Guschall-Jaik [email protected] Beate Kölling [email protected] Nadine Zocher [email protected] Responsible for Dipl.-Ing. Eric Rehbock content: Hohe Straße 73 · 53119 Bonn Translated by: GDA, German Aluminium Association Photos on inside pages: Initiative’s own photos Cover photo: www.fotolia.de © steven Graphic implementation: www.bn-mediendesign.de 1 INTRODUCTION stEEl SWARF These guidelines provide advice on the eco-friendly handling of metal swarf fromalloy the time it is produced swarf through to its professional processing by a recycling company. It has been prepared by the participants shown in the appendix in order to offer a guide for handling swarf in a responsible manner. The main issues dealt with in the guidelines are the diverse types of swarf and the consideration that has to be givenBRASS to the respective characteristics to ensure Swarf safe recycling. The related topics metalworking fluids and the leak-tightness of the units used for collection and transport are also dealt with extensively. The present translation refers to best practicesaluminium recommendations and the current situation in certain SWARF German states. -
NIMS Machining Level I Preparation Guide Grinding
NIMS Machining Level I Preparation Guide Grinding Table of Contents Overview pages 2 - 6 · Introduction page 2 · Who Wrote the Questions page 2 · How to Prepare for the Credentialing Exam page 3 · Areas of Knowledge Measured by the Credentialing Exam pages 3 - 5 · Before the Credentialing Exam page 5 · At the Testing Site page 6 Machining Exam – Grinding pages 7 - 28 · Credentialing Exam Content, Sample Question Overview page 7 · Credentialing Exam Specifications page 8 · Task List pages 9 - 25 · Sample Exam pages 9 - 25 · Answer Key pages 26 - 28 © 2003 National Institute for Metalworking Skills, Inc. Page 1 of 28 Overview Introduction This preparation guide or test advisor is intended to help machinists study and prepare for the National Institute for Metalworking Skills (NIMS) written credentialing exam. The sample exam will prepare machinists to take the actual credentialing exam. None of the questions are duplicates from the actual credentialing exam. However, this preparation guide is a useful tool for reviewing technical knowledge and identifying areas of strength and deficiency for adequate credentialing exam preparation. Achieving a NIMS credential is a means through which machinists can prove their abilities to themselves, to their instructors or employers and to the customer. By passing the NIMS credentialing exam, you will earn a valuable and portable credential. Because the credentialing exam is challenging, you will have the satisfaction of proving to yourself and others that you have reached a level of competency that is accepted nationally. Who Wrote the Questions A panel of technical experts, from all areas of the metalworking industry, wrote the questions used on the actual credentialing exam. -
PART IA MACHINE TOOLS Andrew Gee, Andy Last and Richard Roebuck
FIRST YEAR DYSON CENTRE PART IA MACHINE TOOLS Andrew Gee, Andy Last and Richard Roebuck A day or two before your timetabled session: • Read all of this handout and the accompanying risk assessment. • Sign and date the risk assessment. • Watch the two short videos referred to in this handout. On the day of your timetabled session: • Bring along the signed risk assessments, which will be collected in. • Do not bring the rest of the handout, you will be guided by a demonstrator throughout. • Come to the student machine tools area (below) at the south end of the Dyson Centre. • Be prepared to answer some basic questions about the exercise and the risk assessment. • If it is clear that you have not read this handout and the risk assessment, you will not be allowed to continue and it may not be possible to reschedule your participation for another time. May 11, 2017 1 Introduction Manufacturing engineering is concerned with the processes by which raw materials are transformed into fin- ished products. Thousands of years of technical innovation have made possible a dazzling array of products manufactured from a wide variety of raw materials (metals, plastics, ceramics, composites, textiles) using an ever expanding range of processes. For example, solid objects may be cast in metal or moulded in plastic. Or they might be formed by extrusion, rolling, forging, pressing, bending or shearing. Parts might be joined by weld- ing, brazing, soldering, adhesive bonding or fastening. The recent development of additive manufacturing (3D printing) has made possible the construction of solid objects through the controlled deposition of material. -
Cutting Fluids & Cleaners
CUTTING FLUIDS & CLEANERS CYCLO COOL® CYCLO COOL Metal Machining Fluids & Cleaners CYCLO COOL® metal machining fluids and cleaners help you lower cost and achieve higher productivity in order to be competitive in today’s market. Our high-performance metal machining fluids bundled with our applications experience and CYCLO CUT® tooling product line deliver a Total Process Improvement solution – giving the competitive edge you are looking for. From coolants to lubricants, forming fluids to process cleaners and corrosion inhibitors, our fluid line supports all your metal machining needs. Our fluid packages come in all shapes and sizes, so you only get what you need – and that’s important when it comes to your bottom line. Many of our products are transparent, containing chemical lubricants, and are ideal for light to heavy-duty operations. They are also able to handle many applications and plant environments… and while they are perfect for individual machines, they work just as well in central system applications thanks to their wide ranging operating capabilities. Count on our Comprehensive Line of CYCLO COOL Metal Machining Fluids and Cleaners for All Your Manufacturing Needs , Synthetic and Semi-Synthetic Cutting Fluids for a Wide Range of Applications , Soluble Oil Cutting Fluids for Enhanced Machining and Grinding Performance , Tooling Specialty Products Including Water-Soluble Tapping Paste and Liquid , A Full Line of Production Cleaners, Corrosion Inhibitors, and Parts for your Equipment With our Range of Fluids, your Machining Operations will Improve Productivity and your Bottom Line! 02 | 03 CYCLO COOL 5ME Advanced Technology Series CYCLO COOL 5ME Advanced Technology Series of metal machining fluids are a new line of resilient and flexible industrial manufacturing fluids created to meet present day and future manufacturing challenges. -
A Novel Turning-Induced-Deformation Based Technique to Process Magnesium Alloys
metals Article A Novel Turning-Induced-Deformation Based Technique to Process Magnesium Alloys Sravya Tekumalla 1, Manasa Ajjarapu 2 and Manoj Gupta 1,* 1 Department of Mechanical Engineering, National University of Singapore, Singapore 117575, Singapore 2 Department of Mechanical Engineering, Sastra Deemed University, Tamilnadu 613401, India * Correspondence: [email protected]; Tel.: +65-6516-6358 Received: 9 July 2019; Accepted: 26 July 2019; Published: 29 July 2019 Abstract: A magnesium alloy was fabricated through the consolidation of chips accumulated during the turning process, followed by cold compaction and hot extrusion. A variation in the depths of cut was done during turning to understand the effect of deformation imparted during primary processing on the mechanical properties of an AZ91 alloy (Mg–9 wt.% Al–1 wt.% Zn–0.3 wt.% Mn). The results revealed a significant improvement in compressive strengths (up to 75%) with increased depth of cut, without compromising ductility through the development of fine-grained structures and prior plastic strain induction. This approach resulted in superior materials vis-a-vis conventional deformation techniques and promotes cost and energy efficiency through recycling industrial metal swarf, which is a significant environmental and economic concern. Keywords: magnesium; turning; deformation; processing; strength 1. Introduction For magnesium to replace the relatively heavier aluminum, titanium, and steels in structural applications, there are still several challenges that are persistent such as the inferior strength, ductility, corrosion resistance, etc. of magnesium [1]. Among the magnesium alloys, the most widely used commercial alloy AZ91 exhibits an excellent combination of mechanical properties, corrosion resistance, and cast ability [2]. However, improved strength is still needed to extend its applications. -
Rapport Eng NSBU, 2010-10-14
Westinghouse Proprietary Class 2 Report SEW 13-123, rev 0 Page 2 of 54 CONTENTS 0 SUMMARY 4 1 INTRODUCTION AND METHOD 4 1.1 Purpose 4 1.2 Method 5 1.3 Scope and Assumptions 5 2 BACKGROUND 5 2.1 Present Situation in Norway 5 2.2 International Experience 5 3 CONCLUSIONS AND RECOMMENDATIONS 6 4 DISMANTLING TECHNIQUES 7 4.1 In-Situ Decontamination 7 4.2 Reactor Internals Segmentation 9 4.2.1 Thermal / Hydraulic Internals Segmentation Techniques 10 4.2.1.1 Plasma Arc Cutting System (PAC) 10 4.2.1.2 Abrasive Water Jet Cutting System (AWJC) 11 4.2.1.3 Metal Disintegration Machining (MDM) 11 4.2.2 Thermal / Hydraulic Internals Segmentation Equipment 12 4.2.2.1 Control Systems 12 4.2.2.2 Manipulator Bridge 12 4.2.2.3 Abrasive Water Jet Cutting System 14 4.2.2.4 Plasma Arc Cutting (PAC) System 15 4.2.2.5 Metal Disintegration Machining (MDM) Equipment 16 4.2.2.6 Hydraulic Shears 17 4.2.2.7 Specialised Rigging, Material Handling Equipment and Storage Stands 17 4.2.2.8 Contamination Control Confinements 18 4.2.2.9 Video Monitoring System and Lighting 18 4.2.2.10 Water Filtration System 19 4.2.2.11 Off-gas Collection/Filtration System 19 4.2.3 Mechanical Techniques 20 4.2.4 Mechanical Internals Segmentation Techniques 21 4.2.5 Mechanical Internals Segmentation Equipment 21 4.2.5.1 Shear Tools 21 4.2.5.2 Saws 23 4.3 Reactor Pressure Vessel 28 4.3.1 One-Piece Removal of the RPV 28 4.3.2 Reactor Pressure Vessel Segmentation 29 4.3.2.1 Thermal Cutting 29 4.3.2.2 Mechanical Cutting 31 4.4 Large Diameter Pipe Work 32 This document contains proprietary information and is subject to the restrictions on the title page. -
Swarf Spinner
The Marketplace for Surface Technology. New and Used Process Equipment & Machinery. Home > Surface Treatment Process Plant & Equipment > Associated Process Plant & Equipment > Swarf Spinner The centrifugal separator is designed to drain fluid from solid mass by spinning off the fluids whilst retaining the mass parts in the perforated drum. After separation the drum can be removed and tipped to reclaim the mass parts ready for disposal / reuse. Although cutting fluids are relatively inexpensive, their disposal and problems from contamination can be costly. A recycling system such as this helps cut these costs and more. Batch deoiling centrifuges, also known as chip spinners or swarf spinners, are specifically designed for applications in the machine tool and surface treatment industries, and are used for services such as metal swarf recovery, brass swarf, stainless steel swarf, aluminum swarf, copper swarf, bronze swarf, metal chips, brass and bronze chips, precious metal chips, metal recycling and metal recovery, oil recovery, and coolant recovery. Metal working centrifuges have the following design features: - De-oiling of swarf and components after turning, machining, and cold stamping - De-watering of metal components after surface treatment - Impregnation or coating of components and spin drying of components - Spinning after hot galvanizing, tinning, or other surface treatments Typical applications: Swarf chips [bronze, brass, mild or stainless steel, aluminum, copper, silver, and gold...] Metal or plastic components and components and other materials De-watering after impregnation or coating of components Riley Industries Ltd A subsidiary of Barry Riley & Sons Ltd. Directors: R T Barry Riley, M P A Riley, Secretary: J C Riley Registered in England no. -
Valcool®- a Cutting Fluid System with Synergy
® ValCOOL® General Catalog Metalworking fluids _INNOVATIONS ValCOOL®- a cutting fluid system with synergy VALCOOL® SELECTIONS Selection Guide 3 Semi-Synthetic 4 Soluble Oil 6 Synthetic 7 Cutting Oil 8 Specialty Fluids 9 Cleaners 10 Additives 11 GENERAL INFORMATION Troubleshooting 12 Fluid maintenance tips & techniques 14 Clean-out procedure 16 Packaging 17 Glossary 18 SERVICE EASY TO ORDER If it’s just about the tool, Material #/Order Numbers you can turn to anyone - If you want more, turn to ValCOOL, LLC. Our Sales Engineers are widely regarded as Makes ordering products quick, easy and accurate. the most competent and responsive in the business: An Material #/Order Number is assigned to every they know the material, the workpiece, the tools and ValCOOL® fluid, cleaner and accessory. the fluids that you need to make it right. Together To place an order, simply provide the desired with our Field Application Engineers, they’re available quantity and the Material #/Order Number. with on-site assistance and technical support when you need it. 2 Selection Guide ® High Low High Refractive Cast Nickel Brass & Application Recommended Product Chlorinated Steel Carbon Silicon Silicon Titanium Index Iron Alloys Copper Severity Concentration Steel Aluminum Aluminum Range VP 700 P u u u u u u u u Low 5 – 10% 2.5 – 6.0 VP 800 P u u u u u u u u 5 – 10% 2.5 – 6.0 VPTECH P u u u u u u u u 5 – 10% 3.0 – 6.5 VP 850 u u u u u u u u 5 – 10% 3.0 – 6.5 VP 690 u u u u u u u u 5 – 10% 5.0 – 9.0 SEMI-SYNTHETIC VP 855 P u u u u u u u u 5 – 10% 3.0 – 6.5 Aerotech -
Identifying the Human Factors Associated with the Defeating of Interlocks on Computer Numerical Control (CNC) Machines
Health and Safety Executive Identifying the human factors associated with the defeating of interlocks on Computer Numerical Control (CNC) machines Prepared by the Health and Safety Laboratory for the Health and Safety Executive 2013 RR974 Research Report Health and Safety Executive Identifying the human factors associated with the defeating of interlocks on Computer Numerical Control (CNC) machines Jane Hopkinson and Chrysanthi Lekka Health and Safety Laboratory Harpur Hill Buxton Derbyshire SK17 9JN HSL were commissioned by HSE to carry out research which sought to identify reasons why operatives defeat interlocks on Computer Numerical Control (CNC) machines, and to obtain an understanding of the extent of this behaviour across the UK engineering industry. The findings from this research provided a number of valuable insights about the frequency of defeating interlocks and the influences upon this behaviour. With regard to frequency of defeating, semi-CNC machines were identified as being commonly defeated in the sample* used in this research. Common activities associated with defeating were setting, proving, swarf removal and deburring. Managers, and operatives / supervisors felt defeating was commonplace (the ‘norm’). With regard to influences, three sets of influences on operative behaviour (Predisposing, Enabling and Reinforcing) were identified as influencing behaviour in relation to defeating interlocks. Interventions that take into account these influences could be developed to promote behaviour change. Suggestions for such interventions are provided within this report. This report and the work it describes were funded by the Health and Safety Executive (HSE). Its contents, including any opinions and/or conclusions expressed, are those of the authors alone and do not necessarily reflect HSE policy.