Methods and Materials Used for Patination at the Fonderia Chiurazzi Luisa Fucito
Total Page:16
File Type:pdf, Size:1020Kb
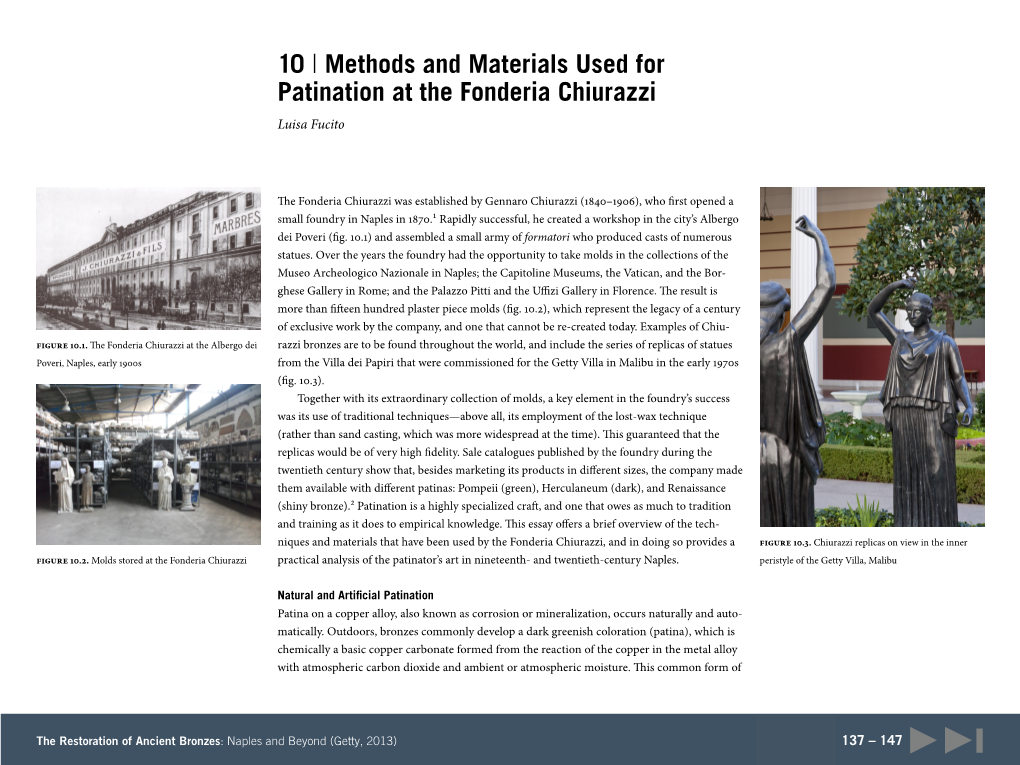
Load more
Recommended publications
-
Treatise on Combined Metalworking Techniques: Forged Elements and Chased Raised Shapes Bonnie Gallagher
Rochester Institute of Technology RIT Scholar Works Theses Thesis/Dissertation Collections 1972 Treatise on combined metalworking techniques: forged elements and chased raised shapes Bonnie Gallagher Follow this and additional works at: http://scholarworks.rit.edu/theses Recommended Citation Gallagher, Bonnie, "Treatise on combined metalworking techniques: forged elements and chased raised shapes" (1972). Thesis. Rochester Institute of Technology. Accessed from This Thesis is brought to you for free and open access by the Thesis/Dissertation Collections at RIT Scholar Works. It has been accepted for inclusion in Theses by an authorized administrator of RIT Scholar Works. For more information, please contact [email protected]. TREATISE ON COMBINED METALWORKING TECHNIQUES i FORGED ELEMENTS AND CHASED RAISED SHAPES TREATISE ON. COMBINED METALWORKING TECHNIQUES t FORGED ELEMENTS AND CHASED RAISED SHAPES BONNIE JEANNE GALLAGHER CANDIDATE FOR THE MASTER OF FINE ARTS IN THE COLLEGE OF FINE AND APPLIED ARTS OF THE ROCHESTER INSTITUTE OF TECHNOLOGY AUGUST ( 1972 ADVISOR: HANS CHRISTENSEN t " ^ <bV DEDICATION FORM MUST GIVE FORTH THE SPIRIT FORM IS THE MANNER IN WHICH THE SPIRIT IS EXPRESSED ELIEL SAARINAN IN MEMORY OF MY FATHER, WHO LONGED FOR HIS CHILDREN TO HAVE THE OPPORTUNITY TO HAVE THE EDUCATION HE NEVER HAD THE FORTUNE TO OBTAIN. vi PREFACE Although the processes of raising, forging, and chasing of metal have been covered in most technical books, to date there is no major source which deals with the functional and aesthetic requirements -
How to Apply Statuary and Patina Finishes
Working With Copper Soldering / Welding / Brazing How to Apply Statuary and Patina Finishes Copper and copper alloys are widely used in architectural applications to take ad- vantage of their inherent range of colors. While these metals may be used in their natural color, as fabricated, it is sometimes desirable to chemically color pure copper (C11000*), commercial bronze (C22000), architectural bronze (C38500) or other alloys referred to as “bronze” in architectural parlance. The most common colors to be produced are referred to as brown or statu- ary fi nishes for bronze and green or patina fi nishes for copper. This data sheet outlines procedures and formulations for producing both. While the chemical solu- tions described are those generally accepted in the metal fi nishing trade, many variations exist. The wide range of colors and shades which may be achieved are largely a matter of craftsmanship and experience. Chemical coloring techniques depend upon time, temperature, surface, preparation, mineral content of the water, humidity and other variables which infl uence the ultimate result. This data sheet presents the technology which underlies the craftsmanship and art involved in producing these colored fi nishes. Brown Statuary Finishes Statuary fi nishes are conversion coatings. In conversion coatings, the metal surface is either converted into a protective fi lm, usually an oxide or sulfi de of the metal involved, or a compound is precipitated which forms a surface fi lm. The use of chemical solutions is generally termed “oxidizing,” although the oldest method and the one which produces the widest range of brown to black stages on copper alloys actually produces not an oxide but a metal sulfi de fi nish by the use of alkaline sulfi de solutions. -
Simple Chemical Experiments Simple Chemical Experiments
SIMPLE CHEMICAL EXPERIMENTS SIMPLE CHEMICAL EXPERIMENTS By ALFRED MORGAN Illustrated by THE AUTHOR APPLETON-CENTURY-CROFTS, INC. NEW YORK COPYRIGHT, 1941, BY D. APPLETON-CENTURY COMPANY, INC All rights reserved. This book, or parts thereof, must not be reproduced in any form without permission of the publisher. PRINTED IN THE UNITED STATES OF AMERICA CONTENTS CHAPTER PAGE I. YOUR LABORATORY i II. EXPERIMENTS WITH PRECIPITATES .... 26 III. EXPERIMENTS WITH SULFUR AND SOME OF ITS COMPOUNDS 54 IV. EXPERIMENTS WITH OXYGEN AND OXYGEN COM POUNDS 73 V. EXPERIMENTS WITH GASES AND SOME OF THEIR COMPOUNDS 103 VI. CHEMICAL TESTS 123 VII. SAFE "FIREWORKS" 144 VIII. EXPERIMENTS WITH A FEW ORGANIC COMPOUNDS 156 IX. CHEMICAL TRICKS AND MAGIC 170 X. MISCELLANEOUS EXPERIMENTS 186 XI. PRACTICAL USES FOR YOUR CHEMICAL KNOWL EDGE 214 XII. THE CHEMICALS YOU WILL NEED . .231 INDEX OF CHEMICALS 259 GENERAL INDEX 263 V SIMPLE CHEMICAL EXPERIMENTS *> CHAPTER I I YOUR LABORATORY I OST of the experiments described in this book can be M performed without elaborate equipment or apparatus. | For them you will need only a few bottles, test-tubes, meas- i uring-spoons, and an alcohol lamp. Jelly glasses, mayonnaise f jars, small enameled saucepans, and thin glass tumblers can | often be substituted for the beakers, flasks, and glassware of I the professional chemist. t A few of the experiments require beakers, flasks, tubing, | funnels, filter paper, crucibles, mortar and pestle, and Bunsen I burner. The small sizes of these are not expensive. Frequently the cost of apparatus and chemicals can be shared by estab lishing a "community" laboratory which is used by two or more experimenters. -
1 Abietic Acid R Abrasive Silica for Polishing DR Acenaphthene M (LC
1 abietic acid R abrasive silica for polishing DR acenaphthene M (LC) acenaphthene quinone R acenaphthylene R acetal (see 1,1-diethoxyethane) acetaldehyde M (FC) acetaldehyde-d (CH3CDO) R acetaldehyde dimethyl acetal CH acetaldoxime R acetamide M (LC) acetamidinium chloride R acetamidoacrylic acid 2- NB acetamidobenzaldehyde p- R acetamidobenzenesulfonyl chloride 4- R acetamidodeoxythioglucopyranose triacetate 2- -2- -1- -β-D- 3,4,6- AB acetamidomethylthiazole 2- -4- PB acetanilide M (LC) acetazolamide R acetdimethylamide see dimethylacetamide, N,N- acethydrazide R acetic acid M (solv) acetic anhydride M (FC) acetmethylamide see methylacetamide, N- acetoacetamide R acetoacetanilide R acetoacetic acid, lithium salt R acetobromoglucose -α-D- NB acetohydroxamic acid R acetoin R acetol (hydroxyacetone) R acetonaphthalide (α)R acetone M (solv) acetone ,A.R. M (solv) acetone-d6 RM acetone cyanohydrin R acetonedicarboxylic acid ,dimethyl ester R acetonedicarboxylic acid -1,3- R acetone dimethyl acetal see dimethoxypropane 2,2- acetonitrile M (solv) acetonitrile-d3 RM acetonylacetone see hexanedione 2,5- acetonylbenzylhydroxycoumarin (3-(α- -4- R acetophenone M (LC) acetophenone oxime R acetophenone trimethylsilyl enol ether see phenyltrimethylsilyl... acetoxyacetone (oxopropyl acetate 2-) R acetoxybenzoic acid 4- DS acetoxynaphthoic acid 6- -2- R 2 acetylacetaldehyde dimethylacetal R acetylacetone (pentanedione -2,4-) M (C) acetylbenzonitrile p- R acetylbiphenyl 4- see phenylacetophenone, p- acetyl bromide M (FC) acetylbromothiophene 2- -5- -
Patination with Non-Toxic Solutions
Area Research Paper PATINATION WITH NON-TOXIC SOLUTIONS Submitted by: Julie Jerman-Melka Department of Visual Art Colorado State University Fort Collins, Colorado Fall 1996 Presented to: Professor Nilda Getty In partial fulfillment of the requirements for the degree of Master of Fine Arts. PATINATION WITH NON-TOXIC SOLUTIONS A Patina is a thin layer of corrosion, usually brown or green, that appears on copper or copper alloys as a result of natural or artificial oxidation. The purpose of coloring metal is to produce a change in its appearance in a short time. This could take place naturally but would take much longer and would require controlled conditions. The natural discoloration of metal surfaces after exposure to air, moisture, and gases is actually a combination of corrosion and oxidation which alters the composition of the metal's surface. Coloring is the final process, after all soldering and polishing have been completed. Coloring will not conceal any surface defects. In some cases, the defects will actually be more exposed. Good ventilation is important for any chemical coloring process. The coloring should be done near an exhaust fan, or even outside. Many of the solutions and chemicals used for patinas are extremely toxic and corrosive and are difficult to dispose of after they are used. Some of the chemicals are difficult to find and the solutions have complicated procedures. In this paper I researched simple, fairly non-toxic solutions for use on copper, brass, and sterling silver. Each piece of metal has been slightly formed with a hammered texture, a high polish, and sandblasted finish to show the different effects that a patina can have on various surfaces. -
Care of Outdoor Bronze Sculptures
CARE OF OUTDOOR BRONZE SCULPTURES Bronze sculpture is meant to be used and enjoyed in the outdoor environment and can maintain the original appearance as long as it is periodically cared for. The maintenance of bronze is easy and basic. This set of care instructions is meant to make the owner of fine bronze more knowledgeable and thus better able to enjoy their bronze to their full satisfaction. A brief introduction on the nature of patinas will start our discussion on the care of fine outdoor bronze. Nature of Patina Patination is the name for the process of coloring metals. These colors arise from chemical interaction between elements in the metals and various chemicals. A patina on bronze is the equivalent to rust on iron, only bronze is much more interesting than iron because the copper in the bronze reacts with different colors. The important thing to note is that the patina is not a paint but a very thin conversion coat on the surface of the bronze. Accordingly, as different chemicals are brought into contact with the surface of the metal, the color is liable to change. When leaving the foundry, the sculptures have a coating of paste wax. This paste wax helps prevent oxygen from getting to the bronze and oxidizing the surface. Over time, this barrier is worn off and water and oxygen work together to oxidize the surface, aging the patina. The best method for caring for patinas always includes regular cleaning and waxing, which is important to both the appearance and longevity of the bronze. -
Electrochemical Evaluation of the Patina of the Weathering Steel Sculpture Once Módulo
Ge-conservación Conservação | Conservation Electrochemical evaluation of the patina of the weathering steel sculpture Once Módulo A. Crespo, B. Ramírez-Barat, I. Díaz, E. Cano Abstract: Weathering steels (WS) have been widely used due to the protective rust formed on the surface of the bare metal exposed to the atmosphere. They have been studied attending to specifications and characteristics in engineering, but in cultural heritage the use of this material does not follow the same criteria and has different needs which must be addressed. Among them, the design and the location of the sculpture may have an impact on the rust formed and may not be as protective as it was supposed to be. This work presents the study of the weathering steel sculpture Once Módulo which shows areas with different exposure to rainwater and different surface heterogeneities. The results obtained by Electrochemical Impedance Spectroscopy (EIS) have shown that the protective ability of the rust depends on the previous differences and that design and location of the artwork play an important role for its conservation. Keywords: weathering Steel, sculpture, electrochemical impedance spectroscopy, atmospheric corrosion, conservation, contemporary art. Evaluación electroquímica de la pátina de la escultura en acero patinable Once Módulo Resumen: Los aceros patinables han sido ampliamente utilizados debido a la habilidad protectora de la herrumbre que se forma en la superficie del metal al exponerlo a la atmosfera. Su estudio se ha enfocado en las especificaciones y características desde un punto de vista ingenieril, sin embargo, en patrimonio cultural el uso de este material no sigue los mismos criterios y tiene distintas necesidades que han de atenderse. -
Copper Reactivity: Patination
CHEMISTRY Copper Reactivity: 16 - 18 YEARS Patination Reactivity Metals can be listed according to their reactivity. Some, like sodium, are so reactive that they explode on contact with water. Some, like gold, are so unreactive that they appear to be unchanged after being buried for thousands of years. Copper is low on this scale. It will react, but slowly. This low reactivity, combined with its malleability makes it ideal for use in architecture. It can be cut and hammered into ornate shapes The restored domes show new copper that and it will protect itself with a pale green coating of copper salts will take many decades to develop the called a patina. Note this is not to be confused with verdigris, patina of the original copper. the name given to the green finish obtained by treatment with (Courtesy of Royal Observatory acetic acid to form copper acetate. Verdigris is soluble and not Edinburgh.) as durable as natural patinas. This view inside the dome shows how thin These are the two telescope domes of the Royal Observatory the structure is. (Courtesy of Eric Begbie.) Edinburgh. The picture was taken before the restoration in 2010. The copper cladding has a layer of green “patina”, that has built up since the domes were built in 1894. The patina is 1 a combination of copper salts that are unreactive and protect the copper from further corrosion. The domes are quite lightweight structures that rotate on a circular rail to allow the telescopes to point in any direction through a panel that slides open. They are also exposed to high winds. -
TECU® Patina Pre-Patinated Copper for Roofing and Façade Cladding
TECU® Patina Pre-patinated copper for Roofing and Façade Cladding [GB] Patina ® TECU KME Germany AG & Co. KG AG KME Germany Member of the KME Group Quality 2 The Surface 4 Processing and Installation 6 Copper and Sustainability 8 TECU® System Products 10 TECU® Sizes and Availability 14 TECU® Project Consulting 16 TECU® References 18 TECU_Patina_f5.indd 2 28.12.2006 14:20:43 Uhr Green copper for immediate creative application – all natural, no limits. Often the shortest path takes you directly to your goal. When the design demands the power and expressiveness of the patina green typical for copper, then it should be implemented just as required – without waiting for the gradual changes caused by natural weathering. The solution is TECU ® Patina – patinated copper for immediate use to satisfy the highest aesthetic demands in building design. Using a specially developed industrial process, TECU ® copper sheets are patinated green on one side. This process causes an oxidised layer to form on the surface of the copper – a process similar to the natural patination that occurs over a long period of time when copper is exposed to atmospheric conditions. TECU ® Patina is always extremely varied, just as you would expect from a natural surface. The many different colour tones and shades eventually blend together, but only gradually. The unique developments occurring in TECU ® Patina are exciting – just as modern architecture should be. TECU_Patina_f5.indd 3 28.12.2006 14:20:50 Uhr TECU® Patina sheets are manufactured in state-of-the-art production facilities according to DIN EN 1172 and KME’s own strict guidelines. -
Essays on Colour
Essays on Colour ESSAYS ON COLOUR A collection of columns from Cabinet Magazine Eleanor Maclure Introduction For every issue the editors of Cabinet Magazine, an American quarterly arts and culture journal, ask one of their regular contributors to write about a specific colour. The essays are printed as Cabinet’s regular Colours Column. To date, forty-two different colours have been the subject of discussion, beginning with Bice in their first ever issue. I first encountered Cabinet magazine when I stumbled upon Darren Wershler-Henry’s piece about Ruby, on the internet. I have since been able to collect all of the published columns and they have provided a wealth of knowledge, information and invaluable research about colour and colour names. Collectively, the writings represent a varied and engaging body of work, with approaches ranging from the highly factual to the deeply personal. From the birth of his niece in Matthew Klam’s Purple, to a timeline of the history of Lapis Lazuli mining in Ultramarine by Matthew Buckingham, the essays have provided fascinating insights into a whole range of colours, from basic terms such as black and red, to the more obscure: porphyry and puce. While some focus very much on the colour in question, others diverge into intricate tales of history, chemistry or geopolitics. There are personal anecdotes, legends and conspiracies, but more than that, the essays demonstrate the sheer diversity of ways we can talk about colour. The essays gathered here have become far more than just the background reading they began as. The aim of this book is to bring together the works, as a unique representation of the different ways we relate to, experience and interpret colours. -
Artificial Patination of Copper and Copper Alloys in Wet Atmosphere
coatings Article Artificial Patination of Copper and Copper Alloys in Wet Atmosphere with Increased Content of SO2 Richard Bureš 1, Martin Klajmon 2, Jaroslav Fojt 1, Pavol Rak 1, Kristýna Jílková 3 and Jan Stoulil 1,* 1 Department of Metals and Corrosion Engineering, University of Chemistry and Technology, 166 28 Prague, Czech Republic; [email protected] (R.B.); [email protected] (J.F.); [email protected] (P.R.) 2 Department of Physical Chemistry, University of Chemistry and Technology, 166 28 Prague, Czech Republic; [email protected] 3 Department of Glass and Ceramics, University of Chemistry and Technology, 166 28 Prague, Czech Republic; [email protected] * Correspondence: [email protected]; Tel.: +420-220-443-750 Received: 3 October 2019; Accepted: 6 December 2019; Published: 8 December 2019 Abstract: Natural copper patina is usually formed over several decades. This work investigates the possibility of obtaining a stable artificial patina based on brochantite in a more reasonable time. The patination process was based on patina formation from a humid atmosphere containing sulphur dioxide. The studied parameters were humidity (condensation and condensation/drying), sulphur dioxide concentration (4.4–44.3 g m 3) and surface pre-treatments (grinding, pre-oxidation and · − pre-patination) prior to the patination process. Samples were evaluated by mass change, digital image analysis, spectrophotometry, scanning electron microscopy (SEM), X-ray photoelectron spectroscopy (XPS) and X-ray diffraction (XRD). A resistometric method was employed in order to observe the patina formation continuously during the exposure. Conditions inside the chamber were monitored during the exposure (pH of water and concentration of SO2 in gaseous phase). -
Prestige Metal Patina Finishes
PRESTIGE METAL PATINA FINISHES + Architectural Cladding & Facades + Showroom: 6 Kambouris Court, Corio, Victoria 3214 www.apsaus.com.au + SERVICES Architectural Panel Systems offers a range of custom patina finishes, as part of our Prestige range of metals. Metals such as Brass, Copper, Bronze, Stainless Steel, Aluminium and Mild Steel are able to be chemically treated, patinated and sealed as part of our colouring process to achieve a high end, unique, custom finish unmatched by any other form of topical treatment. Precious metal coating is a liquid application process that involves high end surface technology. We deliver a range of one of a kind metal finish solutions, dealing closely with Architects, Designers, Builders, Developers, Corporate Business and direct to public. Our range of finishes can be used for both modern and traditional requirements. The patina process can be customised to form different patterns and create an instant aged or antique finish. Metal patination is unique and services a niche, specialty market. To complement our range of patination finishes, we also offer a complete manufacturing service, in house at our production facility in Geelong. Our product and services extend nationally, with both supply only and supply & installation options available. The Architectural Panel Systems office team can also assist in the design and engineering of all products where required, whether it be for architectural, heritage, sculptural, simple shelving for a shop fit out or lift doors in a grand hotel. Architectural Panel