Base Project: Report on the Status of Russian Hot Spots
Total Page:16
File Type:pdf, Size:1020Kb
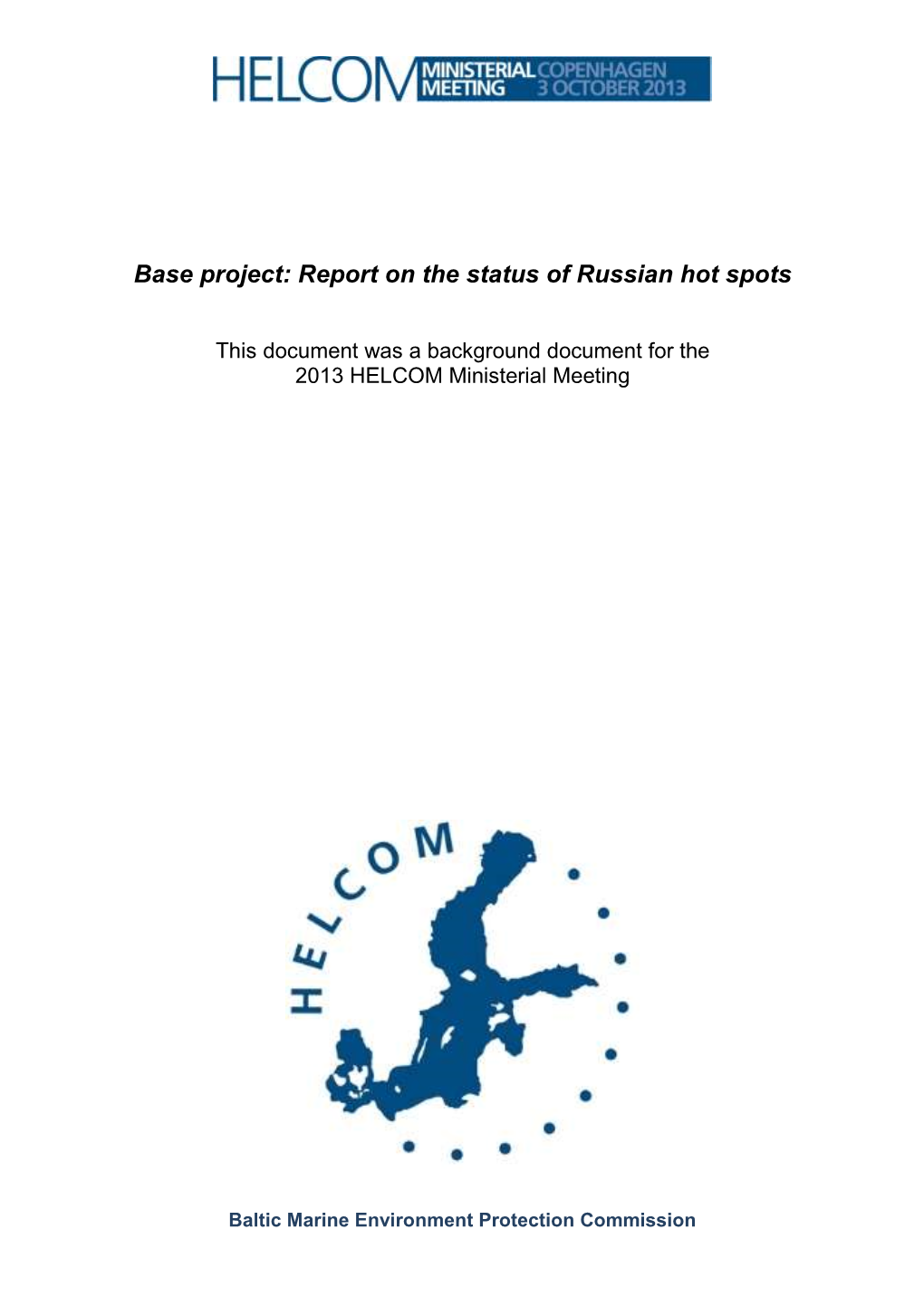
Load more
Recommended publications
-
Passport of St. Petersburg Industrial Zones
The Committee for industrial policy and innovation of St. Petersburg Passport of St. Petersburg industrial zones 3-d edition 2015 Contents 1. Preamble..................................................................................................................................................................2 2. Industrial zones of St. Petersburg............................................................................................................................8 2.1. Area of industrial zones...................................................................................................................................9 2.2. Branch specialization of industrial zones according to town-planning regulations of industrial zones..............9 2.3. The Master plan of Saint-Petersburg (a scheme of a functional zoning of St. Petersburg)..............................................................................................10 2.4. The Rules of land use and building of St. Petersburg (a scheme of a territorial zoning of St. Petersburg).............................................................................................12 2.5. Extent of development of territories of industrial zones and the carried-out projects of engineering training of territories of industrial zones............................................................................................................................13 2.6. Documentation of planning areas of the industrial zones........................................................................13 -
BR IFIC N° 2654 Index/Indice
BR IFIC N° 2654 Index/Indice International Frequency Information Circular (Terrestrial Services) ITU - Radiocommunication Bureau Circular Internacional de Información sobre Frecuencias (Servicios Terrenales) UIT - Oficina de Radiocomunicaciones Circulaire Internationale d'Information sur les Fréquences (Services de Terre) UIT - Bureau des Radiocommunications Part 1 / Partie 1 / Parte 1 Date/Fecha 06.10.2009 Description of Columns Description des colonnes Descripción de columnas No. Sequential number Numéro séquenciel Número sequencial BR Id. BR identification number Numéro d'identification du BR Número de identificación de la BR Adm Notifying Administration Administration notificatrice Administración notificante 1A [MHz] Assigned frequency [MHz] Fréquence assignée [MHz] Frecuencia asignada [MHz] Name of the location of Nom de l'emplacement de Nombre del emplazamiento de 4A/5A transmitting / receiving station la station d'émission / réception estación transmisora / receptora 4B/5B Geographical area Zone géographique Zona geográfica 4C/5C Geographical coordinates Coordonnées géographiques Coordenadas geográficas 6A Class of station Classe de station Clase de estación Purpose of the notification: Objet de la notification: Propósito de la notificación: Intent ADD-addition MOD-modify ADD-ajouter MOD-modifier ADD-añadir MOD-modificar SUP-suppress W/D-withdraw SUP-supprimer W/D-retirer SUP-suprimir W/D-retirar No. BR Id Adm 1A [MHz] 4A/5A 4B/5B 4C/5C 6A Part Intent 1 109078651 ARG 7233.0000 PICHANAL ARG 64W13'34'' 23S19'09'' FX 1 ADD 2 109078654 -
Russia's Akademik Lomonosov – the First Modern Floating Nuclear
Russia’s Akademik Lomonosov – The First Modern Floating Nuclear Power Plant (FNPP) Peter Lobner, 15 May 2021 1. Introduction Designated Project 20870, construction of Akademik Lomonosov started on 15 April 2007, when the keel was laid at the Sevmash shipyard in Severodvinsk, which also is Russia’s premier submarine building shipyard. Originally, Akademik Lomonosov was expected to supply power to the Sevmash shipyard itself and the town of Severodvinsk, in Northwest Russia. Cutaway drawing showing the general arrangement of the Akademik Lomonosov. Source: Rosatom In August 2008, the hull of Akademik Lomonosov was transferred to the Baltic Shipyard in St. Petersburg, where a second “keel laying” was held in May 2009. Plans for deploying the FNPP were reconsidered, leading to the final selection of Pevek, a remote Arctic coastal city in Russia’s Far East. The FNPP was launched on 30 June 2010 and outfitting continued with the vessel secured dockside at the Baltic Shipyard. Two un-fueled OKBM Afrikantov KLT-40S modular pressurized water reactors (PWRs) were installed in October 2013. 1 After work on the vessel and reactor systems was completed in April 2018, Akademik Lomonosov was towed 4,000 km (2,485 miles) around Norway to Murmansk, where the reactors were fuelled and tested at Rosatomflot facilities, which also support their nuclear- powered icebreaker fleet. In June 2019, the Russian nuclear regulatory agency Rostekhnadzor issued a 10-year license to Rosenergoatom to operate Akademik Lomonosov until 2029. After successfully completing testing, Akademik Lomonosov departed Murmansk on 23 August 2019 and was towed 4,770 km (2,964 miles) along the Northern Sea Route, arriving at its final destination on 9 September 2019 at a new protected pier at Pevek, which is about 980 km (609 miles) west of the Bering Strait. -
Õdagumeresoomõ Kodo / Võro Instituudi
Õdagumeresoomõ kodo Läänemeresoome kodu VÕRO INSTITUUDI TOIMÕNDUSÕQ PUBLICATIONS OF VÕRO INSTITUTE 20 Õdagumeresoomõ kodo Läänemeresoome kodu Toimõndanuq Helen Koks ja Jan Rahman Konvõrents Võrol, 19.–21. rehekuul 2006 Võro 2007 Võro kiil: Helen Koks, Jüvä Sullõv Inglüse kiil: Mari Mets Makett: Jan Rahman Kaasõpilt: Aapo Ilves Nõvvomiis: Karl Pajusalu ISBN: 978-9985-9640-2-6 ISSN: 1406-2534 ALOSTUSÕS Võro instituudi ja Tarto ülikooli eesti ja soomõ-ugri keeletiide osakunna kõrraldõdul riikevaihõlidsõl konvõrendsil Võrol 2006. aastaga 19.–21. re- hekuu pääväl püüti löüdäq vastussit küsümiisele, kon ja määne om olluq õdagumeresoomõ rahvidõ kodo ja määne om katõkeeline kodo. Arotõldi ka tuud, kuimuudu umma kiilt, kultuuri ni ilmanägemist alalõ hoitaq. Seon kogomikun ommaq konvõrendsi ettekandidõ perrä kirotõduq artik- liq ja esseeq. Edimädsen jaon “Õdagumeresoomõ kodo” om artikliid mitmõ ala päält. Saarõ Evar kõnõlõs Lõuna-Eesti kotussõnimmist. Autor tuu Võromaa eri nukkõ kotussõnimmi põâal vällä näütäjäq, miä mõotasõq kotussõnimesüs- teemi kujonõmist. Péter Pomozi tutvustas “Agenda Parva” lõunaeestikeelid- se jao kiräviit. Marjatta Normani artiklist tulõvaq vällä katõkeelidse kodo hääq ja halvaq küleq. Pia poolõq artikliist pututasõq väiküide õdagumeresoomõ kiili ja kul- tuurõ saisu. Enn Ernits kõnõlõs isuriist, näide elopaigust ni algkodost. Hei- nike Heinsoo seletäs uma kogomiskäüke põâal, ku häste vaèalasõq viil taimõnimetüisi mälehtäseq. Muusiän võrdõlõs tä ummi illatsit kogomistulõ- muisi Gustav Vilbaste kogot keelematõrjaaliga. A Anitta Viinikka-Kallinen näütäs, kuimuudu om kveene kunstkirändüsen kujutõt ni kõnõlõs artiklin edimädsest kveeni keelidsest romaanist. Helen Kõmmusõ artikli tutvustas Hiiumaal elävä, a Võromaalt peri olõva lauligu Mäe Laine käest kogotuid rahvalaulõ. Kogomigu tõsõn jaon “Kodo kullanõ…” ommaq essesitlikuq kirotusõq. Madis Arukask ja Õie Sarv kaesõq, määne om rahvalaulõ kodo. -
Western Sanctions Will Affect Russian Shipbuilding
WESTERN SANCTIONS WILL AFFECT RUSSIAN SHIPBUILDING Western sanctions will not hamper construction of nuclear icebreakers, but can have negative consequences for other Russian civilian shipbuilding. Western sanctions could curb Russian Arctic oil Statoil, Rosneft delay Siberian drilling, while CEO Sechin added to international sanction list This week the U.S. and EU hardened its sanctions against Russia designed to punish its continuing backing of separatists in Eastern Ukraine. The sanctions include the EU banning any trade in arms and the US prohibiting transactions with Russia’s United Shipbuilding Corporation, which it classified as a defense company. According to the United Shipbuilding Corporation the sanctions will probably have no impact on state orders that already are under construction, but can seriously hamper future orders. The Baltic Shipyard outside St. Petersburg has orders to construct Russia’s three next, much-needed nuclear-powered icebreakers. The prototype was laid down in November 2013 and is planned to be ready for service in December 2017. The two next icebreakers should be ready for delivery in 2019 and 2020. “We don’t see any problems in the construction of the nuclear icebreakers, since no part of the equipment - down to the last bolt and screw – has anything to do with the U.S.” a spokesperson from United Shipbuilding Corporation says to Arctic Info. Others are not so optimistic about the future of civilian Russian shipbuilding after the last sanctions were imposed. Head of St. Petersburg’s Committee for Industrial Policy and Innovation Maksim Meyksin says to website Baltpp that the sanctions can have serious impacts on the large shipyards in the region. -
Report-On-The-Status-Of-HELCOM-Hot-Spots-In-Russia.Pdf
BASE Project - Implementation of the Baltic Sea Action Plan in Russia Baltic Marine Environment Protection Commission Report on the Status of HELCOM hot spots in Russia Pilot Activity Preparation of hot spots report including hot spot ques- tionnaire - Report on the status of HELCOM hot spots in Russia. Annex to the HELCOM Final Report on Implementation of the Baltic Sea Joint Comprehensive En- vironmental Action Programme (JCP) 1992-2013 (Hot Spots Component) Implemented by (Main Consultant) LTD «Ecological Monitoring, Management, Audit and Con- sulting» (EcoMMAK) Report compilation and general conclusions by Sergey Kondratenko, Yulija Ruigite, Andrey Aldushin For bibliographic purposes this document HELCOM 2014, BASE project 2012-2014: Pilot activity on should be cited as preparation of hot spots report including hot spot ques- tionnaire - Report on the status of HELCOM hot spots in Russia. English editing by Howard McKee, Key Image Ltd Design and layout HELCOM Secretariat Cover photo ‘Krasny Bor landfill’ EcoMMAK Ltd Back cover Johanna Laurila Implemented in the framework of: Project Implementation of the Baltic Sea Action Plan in Russia (BASE) Funded by European Union Implemented by HELCOM Secretariat and St. Petersburg Public Organisation ‘Ecology and Business’ Following the decision of the HELCOM Moscow Ministerial Meeting (2010), the report on current status of the Russian hot spots was presented to the HELCOM Copenhagen Ministerial Meeting in 2013. This report does not necessarily represent the views of HELCOM. HELCOM does not assume responsibility for the content of the report. Information included in this publication or extracts thereof are free for citation on the condition that the complete reference of the publication is given as stated above. -
List of Hot Spots
List of JCP Hot Spots in the Baltic Sea catchment area (the shadowed lines indicate the Hot Spots deleted from the list as per December 2009) Key Priority Location Country Site name Site type Hot Spots Bothnian Bay 1 Bothnian Bay Sweden Rönnskärsverken Industry (Metal Smelter) 2 Bothnian Bay Finland Metsä-Botnia Oy Kemi Industry (Pulp & Paper) Bothnian Sea 3 Bothnian Sea Sweden Husum Kraft Mill (1) Industry (Pulp & Paper) 4 Bothnian Sea Sweden Östrand (1) Industry (Pulp & Paper) 5 Bothnian Sea Sweden Vallvik (1) Industry (Pulp & Paper) 6 Dalälven River Sweden Dalälven Mining Waste 7 Bothnian Sea Finland Outokumpu Group Industry (Metal Smelter) Harjavalta 8 Bothnian Sea Finland Kemira Oy Vuorikemia Industry (Titanium oxide) Archipelago and Åland Seas 9 Arch & Åland Finland Fish Farming Fish Farming Seas 10 Archipelago Sea Finland Agriculture (2) Agricultural Runoff Neva River Basin / Lake Ladoga 11 Lake Saimaa Finland YPT Joutseno Industry (Pulp & Paper) 12 Lake Saimaa Finland Kaukas Lappeenranta Industry (Pulp & Paper) 13 Lake Saimaa Finland E-G Kaukopää Industry (Pulp & Paper) 14 Lake Ladoga Russia Syasstroi Industry (Pulp & Paper) 15 Lake Ladoga Russia Volkhov Industry (Aluminum) Gulf of Finland 16 Gulf of Finland Finland Sunila Oy – Kotka Industry (Pulp & Paper) 17 Gulf of Finland Finland Helsinki Region Municipal 18.1 X Gulf of Finland Russia St. Petersburg Connection Sewers 18.2 Prior Gulf of Finland Russia St. Petersburg – Central Municipal & Industrial 19+21 Aeration Station 18.3 Prior Gulf of Finland Russia St. Petersburg – Northern Municipal & Industrial 19+21 Aeration Station 18.4 Prior Gulf of Finland Russia St. Petersburg – South Municipal & Industrial 19+21 West Treatment Pland 18.5 X Gulf of Finland Russia St. -
Marine Nuclear Power: 1939 – 2018
Marine Nuclear Power: 1939 – 2018 Part 3B: Russia - Surface Ships & Non-propulsion Marine Nuclear Applications Peter Lobner July 2018 1 Foreword In 2015, I compiled the first edition of this resource document to support a presentation I made in August 2015 to The Lyncean Group of San Diego (www.lynceans.org) commemorating the 60th anniversary of the world’s first “underway on nuclear power” by USS Nautilus on 17 January 1955. That presentation to the Lyncean Group, “60 years of Marine Nuclear Power: 1955 – 2015,” was my attempt to tell a complex story, starting from the early origins of the US Navy’s interest in marine nuclear propulsion in 1939, resetting the clock on 17 January 1955 with USS Nautilus’ historic first voyage, and then tracing the development and exploitation of marine nuclear power over the next 60 years in a remarkable variety of military and civilian vessels created by eight nations. In July 2018, I finished a complete update of the resource document and changed the title to, “Marine Nuclear Power: 1939 – 2018.” What you have here is Part 3B: Russia - Surface Ships & Non-propulsion Marine Nuclear Applications. The other parts are: Part 1: Introduction Part 2A: United States - Submarines Part 2B: United States - Surface Ships Part 3A: Russia - Submarines Part 4: Europe & Canada Part 5: China, India, Japan and Other Nations Part 6: Arctic Operations 2 Foreword This resource document was compiled from unclassified, open sources in the public domain. I acknowledge the great amount of work done by others who have published material in print or posted information on the internet pertaining to international marine nuclear propulsion programs, naval and civilian nuclear powered vessels, naval weapons systems, and other marine nuclear applications. -
Circumpolar Military Facilities of the Arctic Five
CIRCUMPOLAR MILITARY FACILITIES OF THE ARCTIC FIVE Ernie Regehr, O.C. Senior Fellow in Arctic Security and Defence The Simons Foundation and Michelle Jackett, M.A. ---------------------------------------------------------------------------------------------------------------------------------------------------------------------------------------- Circumpolar Military Facilities of the Arctic Five – last updated: September 2017 Ernie Regehr, O.C., and Michelle Jackett, M.A. Circumpolar Military Facilities of the Arctic Five Introduction This compilation of current military facilities in the circumpolar region1 continues to be offered as an aid to addressing a key question posed by the Canadian Senate more than five years ago: “Is the [Arctic] region again becoming militarized?”2 If anything, that question has become more interesting and relevant in the intervening years, with commentators divided on the meaning of the demonstrably accelerated military developments in the Arctic – some arguing that they are primarily a reflection of increasing military responsibilities in aiding civil authorities in surveillance and search and rescue, some noting that Russia’s increasing military presence is consistent with its need to respond to increased risks of things like illegal resource extraction, terrorism, and disasters along its frontier and the northern sea route, and others warning that the Arctic could indeed be headed once again for direct strategic confrontation.3 While a simple listing of military bases, facilities, and equipment, either -
Doing Business in St. Petersburg St
Doing business in St. Petersburg St. Petersburg Foundation for SME Development – member of Enterprise Europe Network | www.doingbusiness.ru 1 Doing business in St. Petersburg Guide for exporters, investors and start-ups The current publication was developed by and under supervision of Enterprise Europe Network - Russia, Gate2Rubin Consortium, Regional Center - St. Petersburg operated by St. Petersburg Foundation for SME Development with the assistance of the relevant legal, human resources, certification, research and real estate firms. © 2014 Enterprise Europe Network - Russia, Gate2Rubin Consortium, Regional Center – St. Petersburg operated by St. Petersburg Foundation for SME Development. All rights reserved. International copyright. Any use of materials of this publication is possible only after written agreement of St. Petersburg Foundation for SME Development and relevant contributing firms. Doing business in St. Petersburg. – Spb.: Politekhnika-servis, 2014. – 167 p. ISBN 978-5-906555-22-9 Online version available at www.doingbusiness.ru. Doing business in St. Petersburg 2 St. Petersburg Foundation for SME Development – member of Enterprise Europe Network | www.doingbusiness.ru Table of contents 1. The city ....................................................................................................................... 6 1.1. Geography ............................................................................................................................. 6 1.2. Public holidays and business hours ...................................................................................... -
Reform, Foreign Technology, and Leadership in the Russian Imperial and Soviet Navies, 1881–1941
REFORM, FOREIGN TECHNOLOGY, AND LEADERSHIP IN THE RUSSIAN IMPERIAL AND SOVIET NAVIES, 1881–1941 by TONY EUGENE DEMCHAK B.A., University of Dayton, 2005 M.A., University of Illinois, 2007 AN ABSTRACT OF A DISSERTATION submitted in partial fulfillment of the requirements for the degree DOCTOR OF PHILOSOPHY Department of History College of Arts and Sciences KANSAS STATE UNIVERSITY Manhattan, Kansas 2016 Abstract This dissertation examines the shifting patterns of naval reform and the implementation of foreign technology in the Russian Empire and Soviet Union from Alexander III’s ascension to the Imperial throne in 1881 up to the outset of Operation Barbarossa in 1941. During this period, neither the Russian Imperial Fleet nor the Red Navy had a coherent, overall strategic plan. Instead, the expansion and modernization of the fleet was left largely to the whims of the ruler or his chosen representative. The Russian Imperial period, prior to the Russo-Japanese War, was characterized by the overbearing influence of General Admiral Grand Duke Alexei Alexandrovich, who haphazardly directed acquisition efforts and systematically opposed efforts to deal with the potential threat that Japan posed. The Russo-Japanese War and subsequent downfall of the Grand Duke forced Emperor Nicholas II to assert his own opinions, which vacillated between a coastal defense navy and a powerful battleship-centered navy superior to the one at the bottom of the Pacific Ocean. In the Soviet era, the dominant trend was benign neglect, as the Red Navy enjoyed relative autonomy for most of the 1920s, even as the Kronstadt Rebellion of 1921 ended the Red Navy’s independence from the Red Army. -
NKS-138, Russian Nuclear Power Plants for Marine Applications
Nordisk kernesikkerhedsforskning Norrænar kjarnöryggisrannsóknir Pohjoismainen ydinturvallisuustutkimus Nordisk kjernesikkerhetsforskning Nordisk kärnsäkerhetsforskning Nordic nuclear safety research NKS-138 ISBN 87-7893-200-9 Russian Nuclear Power Plants for Marine Applications Ole Reistad Norwegian Radiation Protection Authority, Norway Povl L. Ølgaard Risø National Laboratory, Denmark April 2006 Abstract In order to establish a systematic approach for future proliferation and environ- mental analyses of Russia’s marine nuclear reactor systems, this paper summa- rizes and analyzes the available open-source information on the design proper- ties of reactor systems and nuclear fuels. The most distinctive features of Rus- sian marine reactor development are pointed out, and similarities and differences between Russian military and civilian reactor systems and fuel are discussed. Relevant updated information on all Russian vessels using nuclear propulsion is presented in Annex I. The basic analytic division in this paper follows vessel gen- erations – first to third generation; and reactor types – PWR and LMC technol- ogy. Most of the available information is related to nuclear icebreakers. This in- formation is systematically analyzed in order to identify stages in the develop- ment of Russia’s civilian naval nuclear reactors. Three different reactor models are discussed: OK-150, OK-900 and KLT-40, together with several versions of these. Concerning military reactors, it is not possible to identify characteristics for the individual reactor models, so the basic division follows vessel generations – first to third generation. From the information available, however, it is possible to identify the main lines along which the design of submarines of especially the first and the second generation has been made.