TCRP Report 57: Track Design Handbook for Light Rail Transit
Total Page:16
File Type:pdf, Size:1020Kb
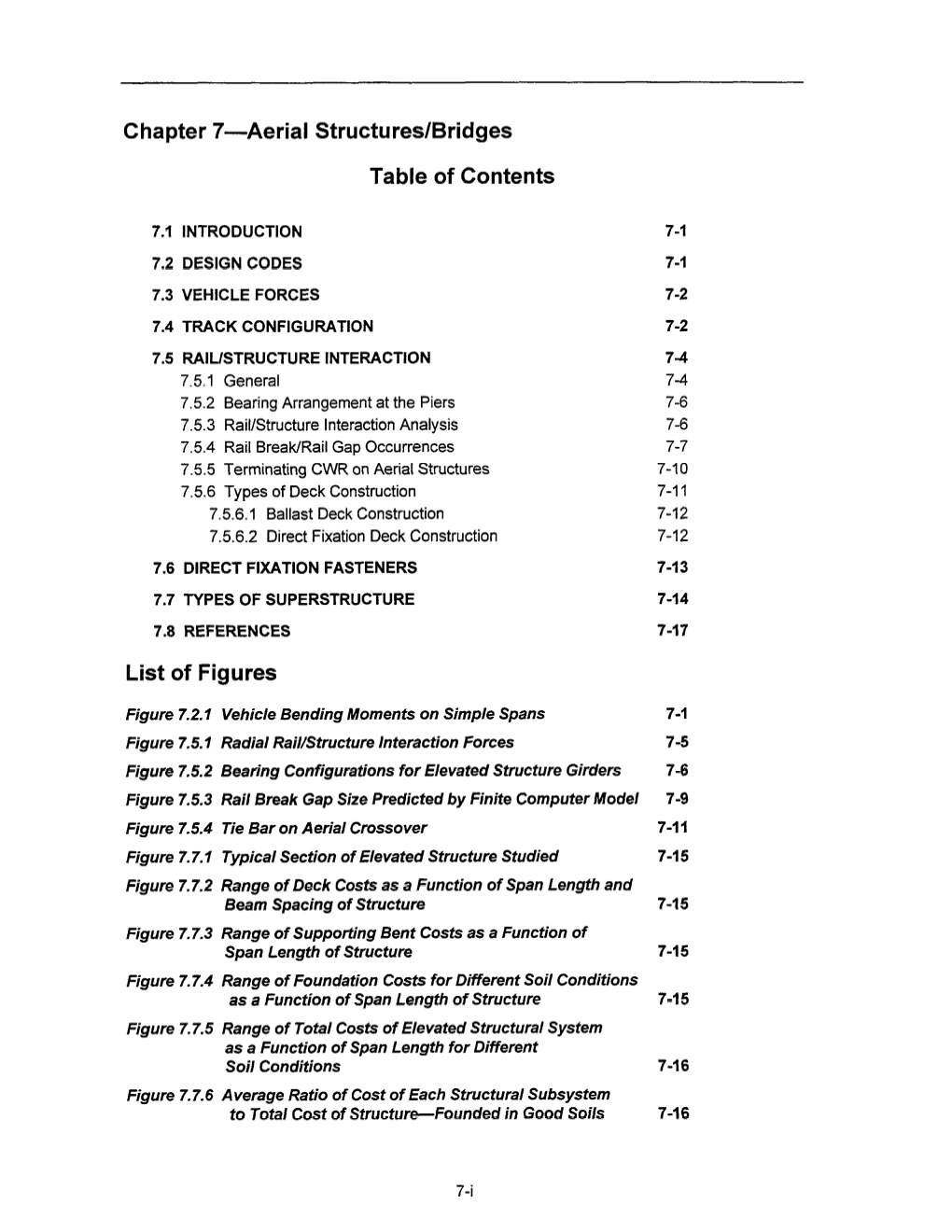
Load more
Recommended publications
-
Use of Ballast Inspection Technology for the Prioritization, Planning and Management of Ballast Delivery and Placement Dr
Use of Ballast Inspection Technology for the Prioritization, Planning and Management of Ballast Delivery and Placement Dr. Allan M. Zarembski, PE, Hon. Mbr. AREMA, FASME Research Professor University of Delaware Mr. Gregory T. Grissom, PE Vice President Engineering, Georgetown Rail Equipment Company Mr. Todd L. Euston, PE Senior Engineer Inspection Technologies Georgetown Rail Equipment Company Abstract This paper presents the results of a study on the optimization of ballast placement planning, prioritization and management for railway ballast distribution. Specifically, this paper presents the requirements for and inputs necessary to more effectively manage the ballast placement process and take advantage of the new track inspection technologies that provide more accurate and reliable data about ballast condition and track profile. This is to include addressing such key issues as: Where and how much ballast should be placed; to include ballast at end of ties (shoulders), under ties, and in cribs. How much ballast should be placed; to include reference or required ballast profile based on vertical, lateral and longitudinal performance requirements A key portion of this study was the introduction of new inspection technologies now available to more accurately define the ballast requirements. This includes such newly introduced inspection technologies as LIDAR for measurement of the ballast profile, Ground Penetrating Radar inspection for ballast depth deficiency, and other related inspection technologies. This in turn allows for more accurate ballast deficit analysis and calculation to include the reference or “ideal” profile used to determine the ballast deficit and the calculation of the difference between the current profile and this reference profile, which includes vertical load distribution and lateral and longitudinal restraint requirements. -
NORTH WEST Freight Transport Strategy
NORTH WEST Freight Transport Strategy Department of Infrastructure NORTH WEST FREIGHT TRANSPORT STRATEGY Final Report May 2002 This report has been prepared by the Department of Infrastructure, VicRoads, Mildura Rural City Council, Swan Hill Rural City Council and the North West Municipalities Association to guide planning and development of the freight transport network in the north-west of Victoria. The State Government acknowledges the participation and support of the Councils of the north-west in preparing the strategy and the many stakeholders and individuals who contributed comments and ideas. Department of Infrastructure Strategic Planning Division Level 23, 80 Collins St Melbourne VIC 3000 www.doi.vic.gov.au Final Report North West Freight Transport Strategy Table of Contents Executive Summary ......................................................................................................................... i 1. Strategy Outline. ...........................................................................................................................1 1.1 Background .............................................................................................................................1 1.2 Strategy Outcomes.................................................................................................................1 1.3 Planning Horizon.....................................................................................................................1 1.4 Other Investigations ................................................................................................................1 -
Improving the Performance of Rail Fastening System Evaluation
PAPER Improving the Performance of Rail Fastening System Evaluation Tadashi DESHIMARU,Improving Track the StructurePerfo randm aComponentsnce of R Laboratory,ail Fast Trackenin Structureg Syst Divisionem Ev aluation Shingo TAMAGAWA, Track Structures and Components Laboratory, Track Technology Division Masato NOGUCHI, Track Structures and ComponentsTadashi Laboratory, DESHIMA TrackRU Technology Division Track Structure and Components Laboratory, Track Structure Division Hiroo KATAOKA, Track Structures and Components Laboratory, Track Technology Division Shingo TAMAGAWA Masato NOGUCHI Hiroo KATAOKA RegardingTrack St rJapaneseuctures a ntestd C methodsompone nforts Lrailabo fasteningratory, Tr systems,ack Tech itn owaslogy confirmedDivision that the rail tilting angle obtained in a biaxial loading test did not agree with the angle calculatedRegarding using Japanese a conventional test methods rail tiltingfor rail analysis fastening model. systems, To address it was confirmedthis problem, that a the rail tilting angle obtained in a biaxial loading test did not agree with the, angle calculated us- ing calculationa conventional method rail fortilting biaxia analysisl loading model. using To an address FEM analysisthis problem, model a calculationwhere various method for stiffnessbiaxial loadingproperties using regarding an FEM the analysisrail fastening model, systems where can various be expressed stiffness as properties non-linearity regard, - ing wasthe railproposed fastening and systemsits validity can was be expressedconfirmed. as non-linearitIn -
Ballastless Track on High-Speed Lines a Guarantee for Travel Savety And
Ballastless track on high-speed lines A guarantee for travel savety and comfort Prologue High–speed rail travel, as a fast connection between high-density population areas and as an alternative to frequently-overloaded air connections with an uncertain future, is gaining increasingly in significance all over the world. In the face of growing traffic density, critical views of life-cycle costs and significantly increa- sed requirements of the availability of railway tracks, there is an increasing demand for track systems which have a long lifetime, low service and maintenance costs and which also guarantee tra- vel safety and comfort. Ballastless tracks (BLT) have numerous advantages over the tradi- tional ballasted track, because of markedly reduced maintenance costs, longer duration of use, improved precision of the running track and the resultant quiet vehicle running. High speed and ballast The nature of the route requirements is changing, as a result of an increase in travel speed or axle loads. The load transported creates inertial forces and the particular more-frequent faults ari- sing from the rolling process are increasing dramatically. Altered deformation mechanisms with dynamic stimulation can result in major grain shifts during piling-up of ballast, which result in con- siderable impairment of the ballasted track and are responsible for uneven creeping and track displacement in the ballast bed. In addition, the track ballast stones are sucked up by vehicles at very high speeds (flying ballast) and may damage them. De- spite the choice of harder types of stone for ballast in high-speed traffic, maintenance costs are considerably higher. -
2005 • Modern Steel Construction November 2005 • Modern Steel Construction • 36 Diation of the Existing Steel Stringers Was Minimal
NATIONAL STEEL BRIDGE ALLIANCE PRIZE BRIDGE COMPETITION NATIONAL AWARD RECONSTRUCTED Red Cliff Arch Rehabilitation Project Red Cliff, CO Gregg Gargan ocated near Red Cliff, CO, southwest of Vail railroad. Any falling material would have been haz- existing connections. A bare concrete deck was used on U.S. Highway 24, the Red Cliff Arch Bridge ardous not only to the public, but also to the envi- to minimize the dead loads. Because of the widening, Lwas originally completed in 1941. Sixty-three ronment. A hard platform scaffolding system was the overhang became larger. To minimize the effects years later, the bridge was in dire need of help. Due required and provided several safety and schedule of the large overhang, a mandatory construction to age, as well as loads and traffic that were not envi- benefits. joint was placed beyond the exterior stringer. The sioned in the 1940s, the bridge needed an extensive Since Highway 24 is the main access to this core of the deck was placed first and allowed to gain rehabilitation. popular ski destination, closure of the highway was strength. The curb and remaining deck was then The newly rehabilitated Red Cliff Arch Bridge a concern. In order to achieve a superior concrete placed with their loads distributed to the newly com- was dedicated in November 2004. Preserving the product for the deck, a complete closure for the posite bridge core. To increase strength of the reha- structure’s historical integrity, while updating it to bridge was deemed necessary. To minimize the bilitated bridge, shear studs were added to stringers current safety standards and strength requirements, impact on the town, the contract required the bridge to create a composite deck. -
Longitudinal Track-Ballast Resistance of Railroad Tracks Considering Four Different Types of Sleepers
Longitudinal Track-Ballast Resistance of Railroad Tracks Considering Four Different Types of Sleepers Rudney C. Queiroz São Paulo State University, Bauru (SP), Brazil Abstract This paper aims at studying the behavior of a railroad track concerning the action of longitudinal forces, targeting the determination of the track-ballast resistance, in a real scale standard track model. This research, was developed at the São Paulo State University, and consisted of a comparative study of track- ballast resistance for railroad tracks built with four different types of sleepers. The first set of sleepers was made of steel, the second one was made of wood, the third one of prestressed-concrete and the fourth one of two-block concrete. In order to carry out this research, four 1600 mm gauge models were built with two TR-68 rails, fastened to seven sleepers by means of elastic fasteners and base plates. The sleepers, all of the same type for each model, were embedded in 0.35 m thick ballast, which was supported by a layer of 30 cm thick compacted soil. The computerized data acquisition system allowed displacement and force values to be obtained in real time. By convention, the maximum longitudinal track-ballast resistance corresponds to a displacement of 15 mm. The prestressed-concrete sleeper setup showed the greatest longitudinal track-ballast resistance per sleeper. The second best performance was obtained by the two- block concrete sleeper setup, followed by the wooden and the steel sleeper setups. The force- displacement curves showed an exponential rise to a maximum shape. The displacement corresponding to the maximum track-ballast resistances were different for each kind of sleeper setup. -
the Swindon and Cricklade Railway
The Swindon and Cricklade Railway Construction of the Permanent Way Document No: S&CR S PW001 Issue 2 Format: Microsoft Office 2010 August 2016 SCR S PW001 Issue 2 Copy 001 Page 1 of 33 Registered charity No: 1067447 Registered in England: Company No. 3479479 Registered office: Blunsdon Station Registered Office: 29, Bath Road, Swindon SN1 4AS 1 Document Status Record Status Date Issue Prepared by Reviewed by Document owner Issue 17 June 2010 1 D.J.Randall D.Herbert Joint PW Manager Issue 01 Aug 2016 2 D.J.Randall D.Herbert / D Grigsby / S Hudson PW Manager 2 Document Distribution List Position Organisation Copy Issued To: Copy No. (yes/no) P-Way Manager S&CR Yes 1 Deputy PW Manager S&CR Yes 2 Chairman S&CR (Trust) Yes 3 H&S Manager S&CR Yes 4 Office Files S&CR Yes 5 3 Change History Version Change Details 1 to 2 Updates throughout since last release SCR S PW001 Issue 2 Copy 001 Page 2 of 33 Registered charity No: 1067447 Registered in England: Company No. 3479479 Registered office: Blunsdon Station Registered Office: 29, Bath Road, Swindon SN1 4AS Table of Contents 1 Document Status Record ....................................................................................................................................... 2 2 Document Distribution List ................................................................................................................................... 2 3 Change History ..................................................................................................................................................... -
Sustainable Trail Bridge Design
U.S. Department of Transportation United States Department of Agriculture Federal Highway Administration Sustainable Trail Bridge Design Forest National Technology & 2023–2805P–NTDP March 2020 Service Development Program 2300–Recreation Sustainable Trail Bridge Design Notice Ordering Information This document was produced in cooperation with You can order a copy of this document using the the Recreational Trails Program of the U.S. Depart- order form on FHWA’s Recreational Trails Program ment of Transportation’s Federal Highway Adminis- website <http://www.fhwa.dot.gov/environment/rec- tration in the interest of information exchange. The reational_trails/publications/trailpub.cfm> U.S. Government assumes no liability for the use of Fill out the order form and submit it electronically. information contained in this document. Or you may email your request to: [email protected] The U.S. Government does not endorse products or manufacturers. Trademarks or manufacturers’ names Or you may mail your request to: appear in this report only because they are consid- Szanca Solutions/FHWA PDC ered essential to the objective of this document. 700 North 3rd Avenue The contents of this report reflect the views of the Altoona, PA 16601 authors, who are responsible for the facts and Fax: 814–239–2156 accuracy of the data presented herein. The con- tents do not necessarily reflect the official policy of Produced by the U.S. Department of Transportation. This report USDA Forest Service does not constitute a standard, specification, or National Technology and Development Program regulation. 5785 Hwy. 10 West Missoula, MT 59808–9361 Phone: 406–329–3978 Fax: 406–329–3719 Email: [email protected] U.S. -
Notes on Curves for Railways
NOTES ON CURVES FOR RAILWAYS BY V B SOOD PROFESSOR BRIDGES INDIAN RAILWAYS INSTITUTE OF CIVIL ENGINEERING PUNE- 411001 Notes on —Curves“ Dated 040809 1 COMMONLY USED TERMS IN THE BOOK BG Broad Gauge track, 1676 mm gauge MG Meter Gauge track, 1000 mm gauge NG Narrow Gauge track, 762 mm or 610 mm gauge G Dynamic Gauge or center to center of the running rails, 1750 mm for BG and 1080 mm for MG g Acceleration due to gravity, 9.81 m/sec2 KMPH Speed in Kilometers Per Hour m/sec Speed in metres per second m/sec2 Acceleration in metre per second square m Length or distance in metres cm Length or distance in centimetres mm Length or distance in millimetres D Degree of curve R Radius of curve Ca Actual Cant or superelevation provided Cd Cant Deficiency Cex Cant Excess Camax Maximum actual Cant or superelevation permissible Cdmax Maximum Cant Deficiency permissible Cexmax Maximum Cant Excess permissible Veq Equilibrium Speed Vg Booked speed of goods trains Vmax Maximum speed permissible on the curve BG SOD Indian Railways Schedule of Dimensions 1676 mm Gauge, Revised 2004 IR Indian Railways IRPWM Indian Railways Permanent Way Manual second reprint 2004 IRTMM Indian railways Track Machines Manual , March 2000 LWR Manual Manual of Instructions on Long Welded Rails, 1996 Notes on —Curves“ Dated 040809 2 PWI Permanent Way Inspector, Refers to Senior Section Engineer, Section Engineer or Junior Engineer looking after the Permanent Way or Track on Indian railways. The term may also include the Permanent Way Supervisor/ Gang Mate etc who might look after the maintenance work in the track. -
University of Southampton Research Repository Eprints Soton
University of Southampton Research Repository ePrints Soton Copyright © and Moral Rights for this thesis are retained by the author and/or other copyright owners. A copy can be downloaded for personal non-commercial research or study, without prior permission or charge. This thesis cannot be reproduced or quoted extensively from without first obtaining permission in writing from the copyright holder/s. The content must not be changed in any way or sold commercially in any format or medium without the formal permission of the copyright holders. When referring to this work, full bibliographic details including the author, title, awarding institution and date of the thesis must be given e.g. AUTHOR (year of submission) "Full thesis title", University of Southampton, name of the University School or Department, PhD Thesis, pagination http://eprints.soton.ac.uk UNIVERSITY OF SOUTHAMPTON FACULTY OF ENGINEERING, SCIENCE AND MATHEMATICS SCHOOL OF CIVIL ENGINEERING AND THE ENVIRONMENT TRACK BEHAVIOUR: THE IMPORTANCE OF THE SLEEPER TO BALLAST INTERFACE BY LOUIS LE PEN THESIS FOR THE DEGREE OF DOCTOR OF PHILOSOPHY 2008 ACKNOWLEDGMENTS I would like to sincerely thank Professor William Powrie and Dr Daren Bowness for the opportunity given to me to carry out this research. I'd also like to thank the Engineering and Physical Sciences Research Council for the funding which made this research possible. Dr Daren Bowness worked very closely with me in the first year of my research and helped me begin to develop some of the skills required in the academic research community. Daren also provided me with some of the key references in this report, he is sadly missed. -
WMATA's Automated Track Analysis Technology & Data Leveraging For
WMATA’S Automated Track Analysis Technology & Data Leveraging for Maintenance Decisions 1 WMATA System • 6 Lines: 5 radial and 1 spur • 234 mainline track miles and 91 stations • Crew of 54 Track Inspectors and 8 Supervisors walk and inspect each line twice a week. • WMATA’s TGV and 7000 Series revenue vehicles, provide different approaches to automatic track inspection abilities. 2 Track Geometry Vehicle (TGV) • Provides services previously contracted out. • Equipped with high resolution cameras inspecting ROW and tunnels, infrared camera monitoring surrounding temperatures, and ultrasonic inspection system. • Measures track geometry parameters, and produces reports where track parameters do not meet WMATA’s maintenance and safety standards. 3 TGV Measured Parameters . Track gage, rail profile, cross level, alignment, twists, and warps. Platform height and gap, . 3rd rail: height, gage, missing cover board, and temperature. • Inspects track circuits transmitting speed commands and signals for train occupancy detection with different carrier frequencies and code rates. 4 TGV Technology • Parameters such as rail profile, gage distances, 3rd rail and platform gap distances are measured via laser beam shot across running rails, and platforms. • High-speed/high-resolution cameras take high resolution images of the surface where lasers makes contact with the rail. 5 TGV Technology • Track profile is measured via vertical accelerometers, and an algorithm converting acceleration into displacement. • Track alignment is measured with a lateral accelerometer in combination with image analysis. • Warps, twists, and cross levels are measured via gyros and inclinometers, along with distance measurements. 6 Kawasaki 7000 Series Cars • Cars are assembled into 4-Pack sets for operation. • 7K cars are equipped with a system of accelerometers that are mounted on 15% of the B cars. -
Innovations in Railway Track
INNOVATIONS IN RAILWAY TRACK Coenraad Esveld Professor of Railway Engineering, TU Delft This paper describes innovations in railway track structures. Special attention is devoted to alterna- tives for ballasted track, with emphasis on low-maintenance solutions, together with versatile high- speed track and heavy haul track for the 21st century. P.O. Box 5048 NL-2600 GA Delft The Netherlands Tel: +31 418 516369 Fax: +31 418 516372 Email: [email protected] Faculty of Civil Engineering, Section of Roads & Railways TABLE OF CONTENTS 1. Introduction........................................................................................................................................1 2. ballasted track ...................................................................................................................................1 3. reinforcing layers...............................................................................................................................2 4. ballastless track.................................................................................................................................2 5. use of ballastless track......................................................................................................................3 6. track resilience ..................................................................................................................................6 7. Critical train speeds...........................................................................................................................6