Synthetic Methods and Applications of Silicon Nanowire: a Review
Total Page:16
File Type:pdf, Size:1020Kb
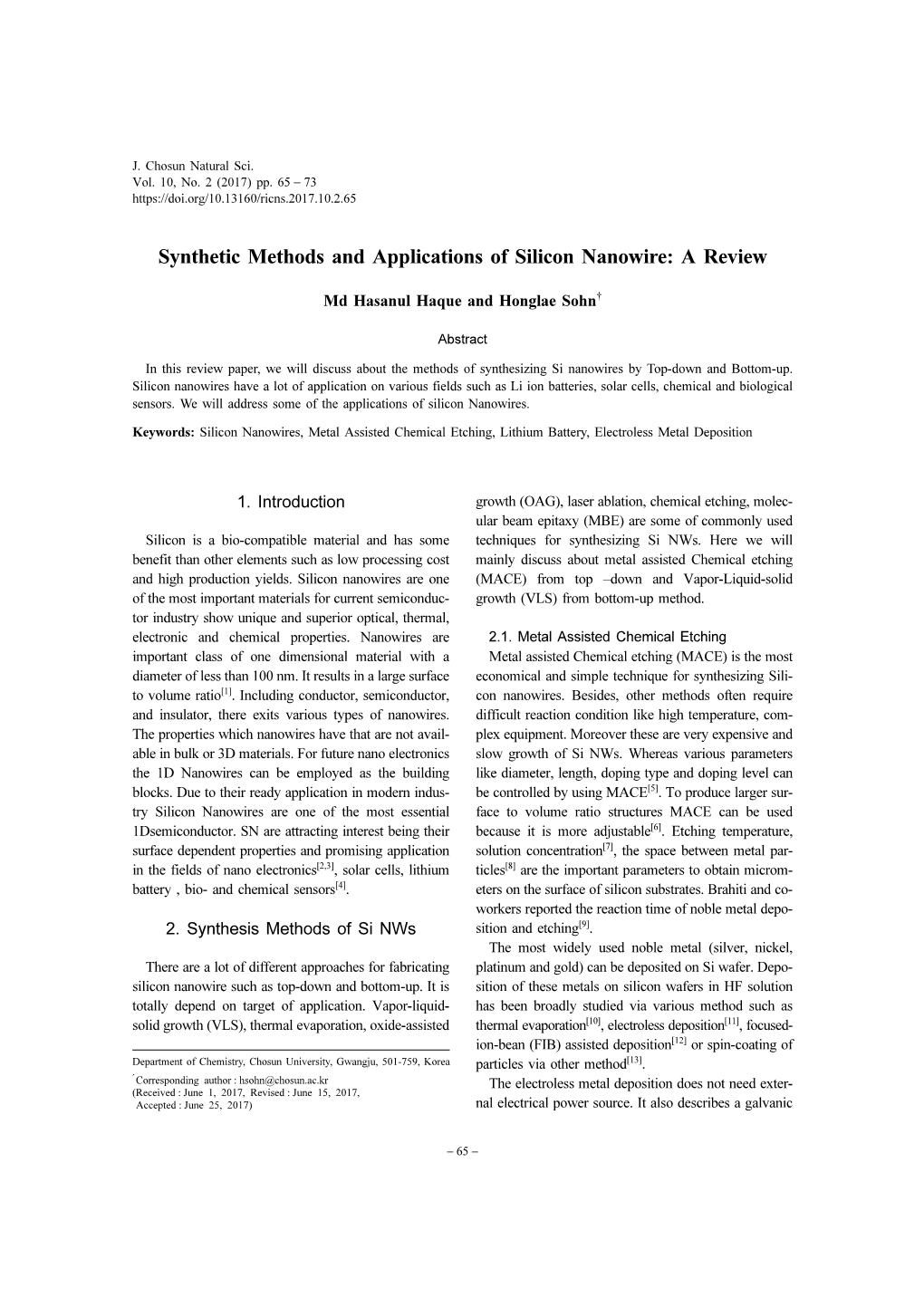
Load more
Recommended publications
-
Cu&Si Core–Shell Nanowire Thin Film As High-Performance Anode
applied sciences Article Cu&Si Core–Shell Nanowire Thin Film as High-Performance Anode Materials for Lithium Ion Batteries Lifeng Zhang 1, Linchao Zhang 1,*, Zhuoming Xie 1 and Junfeng Yang 1,2,* 1 Key Laboratory of Materials Physics, Institute of Solid State Physics, Hefei Institute of Physical Science, Chinese Academy of Sciences, Hefei 230032, China; [email protected] (L.Z.); [email protected] (Z.X.) 2 Lu’an Branch, Anhui Institute of Innovation for Industrial Technology, Lu’an 237100, China * Correspondence: [email protected] (L.Z.); [email protected] (J.Y.) Abstract: Cu@Si core–shell nanowire thin films with a Cu3Si interface between the Cu and Si were synthesized by slurry casting and subsequent magnetron sputtering and investigated as anode materials for lithium ion batteries. In this constructed core–shell architecture, the Cu nanowires were connected to each other or to the Cu foil, forming a three-dimensional electron-conductive network and as mechanical support for the Si during cycling. Meanwhile, the Cu3Si layer can enhance the interface adhesion strength of the Cu core and Si shell; a large amount of void spaces between the Cu@Si nanowires could accommodate the lithiation-induced volume expansion and facilitate electrolyte impregnation. As a consequence, this electrode exhibits impressive electrochemical properties: the initial discharge capacity and initial coulombic efficiency is 3193 mAh/g and 87%, respectively. After 500 cycles, the discharge capacity is about 948 mAh/g, three times that of graphite, corresponding to an average capacity fading rate of 0.2% per cycle. Keywords: lithium ion battery; anode; silicon; core–shell structure; magnetron sputtering Citation: Zhang, L.; Zhang, L.; Xie, Z.; Yang, J. -
Recent Advances in Vertically Aligned Nanowires for Photonics Applications
micromachines Review Recent Advances in Vertically Aligned Nanowires for Photonics Applications Sehui Chang, Gil Ju Lee and Young Min Song * School of Electrical Engineering and Computer Science, Gwangju Institute of Science and Technology (GIST), 123 Cheomdangwagi-ro, Buk-gu, Gwangju 61005, Korea; [email protected] (S.C.); [email protected] (G.J.L.) * Correspondence: [email protected]; Tel.: +82-62-715-2655 Received: 29 June 2020; Accepted: 25 July 2020; Published: 26 July 2020 Abstract: Over the past few decades, nanowires have arisen as a centerpiece in various fields of application from electronics to photonics, and, recently, even in bio-devices. Vertically aligned nanowires are a particularly decent example of commercially manufacturable nanostructures with regard to its packing fraction and matured fabrication techniques, which is promising for mass-production and low fabrication cost. Here, we track recent advances in vertically aligned nanowires focused in the area of photonics applications. Begin with the core optical properties in nanowires, this review mainly highlights the photonics applications such as light-emitting diodes, lasers, spectral filters, structural coloration and artificial retina using vertically aligned nanowires with the essential fabrication methods based on top-down and bottom-up approaches. Finally, the remaining challenges will be briefly discussed to provide future directions. Keywords: nanowires; photonics; LED; nanowire laser; spectral filter; coloration; artificial retina 1. Introduction In recent years, nanowires originated from a wide variety of materials have arisen as a centerpiece for optoelectronic applications such as sensors, solar cells, optical filters, displays, light-emitting diodes and photodetectors [1–12]. Tractable but outstanding, optical features of nanowire arrays achieved by modulating its physical properties (e.g., diameter, height and pitch) allow to confine and absorb the incident light considerably, albeit its compact configuration. -
Designing a Nanoelectronic Circuit to Control a Millimeter-Scale Walking Robot
Designing a Nanoelectronic Circuit to Control a Millimeter-scale Walking Robot Alexander J. Gates November 2004 MP 04W0000312 McLean, Virginia Designing a Nanoelectronic Circuit to Control a Millimeter-scale Walking Robot Alexander J. Gates November 2004 MP 04W0000312 MITRE Nanosystems Group e-mail: [email protected] WWW: http://www.mitre.org/tech/nanotech Sponsor MITRE MSR Program Project No. 51MSR89G Dept. W809 Approved for public release; distribution unlimited. Copyright © 2004 by The MITRE Corporation. All rights reserved. Gates, Alexander Abstract A novel nanoelectronic digital logic circuit was designed to control a millimeter-scale walking robot using a nanowire circuit architecture. This nanoelectronic circuit has a number of benefits, including extremely small size and relatively low power consumption. These make it ideal for controlling microelectromechnical systems (MEMS), such as a millirobot. Simulations were performed using a SPICE circuit simulator, and unique device models were constructed in this research to assess the function and integrity of the nanoelectronic circuit’s output. It was determined that the output signals predicted for the nanocircuit by these simulations meet the requirements of the design, although there was a minor signal stability issue. A proposal is made to ameliorate this potential problem. Based on this proposal and the results of the simulations, the nanoelectronic circuit designed in this research could be used to begin to address the broader issue of further miniaturizing circuit-micromachine systems. i Gates, Alexander I. Introduction The purpose of this paper is to describe the novel nanoelectronic digital logic circuit shown in Figure 1, which has been designed by this author to control a millimeter-scale walking robot. -
Formation of Silicon Nanowires by Chemical Vapour Deposition Technique Using Indium Catalyst
View metadata, citation and similar papers at core.ac.uk brought to you by CORE provided by University of Malaya Students Repository FORMATION OF SILICON NANOWIRES BY CHEMICAL VAPOUR DEPOSITION TECHNIQUE USING INDIUM CATALYST CHONG SU KONG DISSERTATION SUBMITTED IN FULFILMENT OF THE REQUIREMENTS FOR THE DEGREE OF MASTER OF SCIENCE DEPARTMENT OF PHYSICS FACULTY OF SCIENCE UNIVERSITY OF MALAYA KUALA LUMPUR 2012 UNIVERSITI MALAYA ORIGINAL LITERARY WORK DECLARATION Name of Candidate: CHONG SU KONG (I.C/Passport No: 850515-01-6097) Registration/Matric No: SGR090004 Name of Degree: MASTER OF SCIENCE (DISSERTATION) Title of Project Paper/Research Report/Dissertation/Thesis (“this Work”): FORMATION OF SILICON NANOWIRES BY CHEMICAL VAPOUR DEPOSITION TECHNIQUE USING INDIUM CATALYST Field of Study: NANOTECHNOLOGY I do solemnly and sincerely declare that: (1) I am the sole author/writer of this Work; (2) This Work is original; (3) Any use of any work in which copyright exists was done by way of fair dealing and for permitted purposes and any excerpt or extract from, or reference to or reproduction of any copyright work has been disclosed expressly and sufficiently and the title of the Work and its authorship have been acknowledged in this Work; (4) I do not have any actual knowledge nor do I ought reasonably to know that the making of this work constitutes an infringement of any copyright work; (5) I hereby assign all and every rights in the copyright to this Work to the University of Malaya (“UM”), who henceforth shall be owner of the copyright in this Work and that any reproduction or use in any form or by any means whatsoever is prohibited without the written consent of UM having been first had and obtained; (6) I am fully aware that if in the course of making this Work I have infringed any copyright whether intentionally or otherwise, I may be subject to legal action or any other action as may be determined by UM. -
A Simulation Study of a Gate-All-Around Nanowire Transistor with a Core–Insulator
micromachines Article A Simulation Study of a Gate-All-Around Nanowire Transistor with a Core–Insulator Yannan Zhang † , Ke Han † and and Jiawei Li * School of Electronic Engineering, Beijing University of Posts and Telecommunications, Haidian district, Beijing 100876, China; [email protected] (Y.Z.); [email protected] (K.H.) * Correspondence: [email protected] † These authors contributed equally to this work. Received: 27 December 2019; Accepted: 18 February 2020; Published: 21 February 2020 Abstract: Ultra-low power and high-performance logical devices have been the driving force for the continued scaling of complementary metal oxide semiconductor field effect transistors which greatly enable electronic devices such as smart phones to be energy-efficient and portable. In the pursuit of smaller and faster devices, researchers and scientists have worked out a number of ways to further lower the leaking current of MOSFETs (Metal oxide semiconductor field effect transistor). Nanowire structure is now regarded as a promising candidate of future generation of logical devices due to its ultra-low off-state leaking current compares to FinFET. However, the potential of nanowire in terms of off-state current has not been fully discovered. In this article, a novel Core–Insulator Gate-All-Around (CIGAA) nanowire has been proposed, investigated, and simulated comprehensively and systematically based on 3D numerical simulation. Comparisons are carried out between GAA and CIGAA. The new CIGAA structure exhibits low off-state current compares to that of GAA, making it a suitable candidate of future low-power and energy-efficient devices. Keywords: CMOS; core-insulator; gate-all-around; field effect transistor; GAA; nanowire 1. -
Effect of Size and Shape on Electrochemical Performance of Nano-Silicon-Based Lithium Battery
nanomaterials Article Effect of Size and Shape on Electrochemical Performance of Nano-Silicon-Based Lithium Battery Caroline Keller 1,2, Antoine Desrues 3, Saravanan Karuppiah 1,2, Eléa Martin 1, John P. Alper 2,3, Florent Boismain 3, Claire Villevieille 1 , Nathalie Herlin-Boime 3,Cédric Haon 2 and Pascale Chenevier 1,* 1 CEA, CNRS, IRIG, SYMMES, STEP, University Grenoble Alpes, 38000 Grenoble, France; [email protected] (C.K.); [email protected] (S.K.); [email protected] (E.M.); [email protected] (C.V.) 2 CEA, LITEN, DEHT, University Grenoble Alpes, 38000 Grenoble, France; [email protected] (J.P.A.); [email protected] (C.H.) 3 CEA, CNRS, IRAMIS, NIMBE, LEDNA, University Paris Saclay, 91191 Gif-sur-Yvette, France; [email protected] (A.D.); fl[email protected] (F.B.); [email protected] (N.H.-B.) * Correspondence: [email protected] Abstract: Silicon is a promising material for high-energy anode materials for the next generation of lithium-ion batteries. The gain in specific capacity depends highly on the quality of the Si dispersion and on the size and shape of the nano-silicon. The aim of this study is to investigate the impact of the size/shape of Si on the electrochemical performance of conventional Li-ion batteries. The scalable synthesis processes of both nanoparticles and nanowires in the 10–100 nm size range are discussed. In cycling lithium batteries, the initial specific capacity is significantly higher for nanoparticles than for nanowires. We demonstrate a linear correlation of the first Coulombic efficiency with the specific area of the Si materials. -
Two-Dimensional Modeling of the Self-Limiting Oxidation in Silicon and Tungsten Nanowires
Theoretical & Applied Mechanics Letters 6 (2016) 195–199 Contents lists available at ScienceDirect Theoretical & Applied Mechanics Letters journal homepage: www.elsevier.com/locate/taml Letter Two-dimensional modeling of the self-limiting oxidation in silicon and tungsten nanowires Mingchao Liu a,b, Peng Jin a, Zhiping Xu a, Dorian A.H. Hanaor b, Yixiang Gan b, Changqing Chen a,∗ a Department of Engineering Mechanics, CNMM & AML, Tsinghua University, Beijing 100084, China b School of Civil Engineering, The University of Sydney, Sydney, NSW 2006, Australia h i g h l i g h t s • A new diffusion-controlled kinetic model for nanowire oxidation is developed. • A finite reactive region is included to account for oxidation stress and suboxide formation. • Self-limiting nanowire oxidation and its curvature/temperature dependence are predicted. • Results are consistent with observed oxidation behavior of silicon (Si) and tungsten (W) nanowires. article info a b s t r a c t Article history: Self-limiting oxidation of nanowires has been previously described as a reaction- or diffusion-controlled Received 18 July 2016 process. In this letter, the concept of finite reactive region is introduced into a diffusion-controlled model, Received in revised form based upon which a two-dimensional cylindrical kinetics model is developed for the oxidation of silicon 1 August 2016 nanowires and is extended for tungsten. In the model, diffusivity is affected by the expansive oxidation Accepted 2 August 2016 reaction induced stress. The dependency of the oxidation upon curvature and temperature is modeled. Available online 16 August 2016 *This article belongs to the Solid Mechanics Good agreement between the model predictions and available experimental data is obtained. -
Silicon Nanowire Anode for Lithium-Ion Batteries
Louisiana State University LSU Digital Commons LSU Doctoral Dissertations Graduate School 2011 Silicon nanowire anode for lithium-ion batteries: fabrication, characterization and solid electrolyte interphase Wanli Xu Louisiana State University and Agricultural and Mechanical College Follow this and additional works at: https://digitalcommons.lsu.edu/gradschool_dissertations Part of the Chemical Engineering Commons Recommended Citation Xu, Wanli, "Silicon nanowire anode for lithium-ion batteries: fabrication, characterization and solid electrolyte interphase" (2011). LSU Doctoral Dissertations. 219. https://digitalcommons.lsu.edu/gradschool_dissertations/219 This Dissertation is brought to you for free and open access by the Graduate School at LSU Digital Commons. It has been accepted for inclusion in LSU Doctoral Dissertations by an authorized graduate school editor of LSU Digital Commons. For more information, please [email protected]. SILICON NANOWIRE ANODE FOR LITHIUM-ION BATTERIES: FABRICATION, CHARACTERIZATION AND SOLID ELECTROLYTE INTERPHASE A Dissertation Submitted to the Graduate Faculty of the Louisiana State University and Agriculture and Mechanical College in partial fulfillment of the requirements for the degree of Doctor of Philosophy in The Gordon A. and Mary Cain Department of Chemical Engineering by Wanli Xu B.S., Dalian University of Technology August 2011 DEDICATION To My Loving Parents, Grandparents, And Husband Zhe Nan 谨以此文 献给 我挚爱的父亲母亲 爷爷奶奶 和丈夫南哲 ii ACKNOWLEDGEMENTS First of all, my heartfelt gratitude goes out to my supervisor, Professor John C. Flake, for successful completion of my dissertation. I am so honored to join in his research group as the first graduate student, and worked with him to set up the lab and equipment from scratch. His untiring effort, encouragement, guidance and support helped me greatly in my graduate studies as well as successful completion of this dissertation. -
Robustness Analysis of Controllable-Polarity Silicon Nanowire Devices and Circuits
Robustness Analysis of Controllable-Polarity Silicon Nanowire Devices and Circuits THÈSE NO 6924 (2016) PRÉSENTÉE LE 8 AVRIL 2016 À LA FACULTÉ INFORMATIQUE ET COMMUNICATIONS LABORATOIRE DES SYSTÈMES INTÉGRÉS (IC/STI) PROGRAMME DOCTORAL EN INFORMATIQUE ET COMMUNICATIONS ÉCOLE POLYTECHNIQUE FÉDÉRALE DE LAUSANNE POUR L'OBTENTION DU GRADE DE DOCTEUR ÈS SCIENCES PAR Hassan GHASEMZADEH MOHAMMADI acceptée sur proposition du jury: Prof. B. Falsafi, président du jury Prof. G. De Micheli, directeur de thèse Prof. M. Sonza Reorda, rapporteur Prof. M. Nicolaidis, rapporteur Prof. D. Atienza Alonso, rapporteur Suisse 2016 To Maryam for her endless love, and to the memory of my father, Ahmad Acknowledgements This thesis was a unique adventure during my study at EPFL. This work could not be done without the help and support of many people. Collaborating, discussing, and working with such great colleagues were invaluable experience during the last 4 years. I would particularly like to thank my supervisor Prof. Giovanni De Micheli for all of his supports, guides and time for constructive discussions. He was a constant source of support and encouragement during the challenges of my research. Working with a knowledgeable person like Prof. Pierre-Emmanuel Gaillardon is always a remarkable experience. I would like to thank him for his tremendous guides and supports. I would also appreciate my examiners, Prof. Babak Falsafi, Prof. David Atienza Alonso, Prof. Matteo Sonza Reorda, and Prof. Michael Nicolaidis, who provided encouraging and beneficial feedbacks. My colleagues at EPFL have a significant role in my project. I wish to thank Dr. Majid Yazdani and Dr. Sara S. Ghoreishizadeh. -
Two-Dimensional Modeling of the Self-Limiting Oxidation in Silicon and Tungsten Nanowires
Theoretical & Applied Mechanics Letters 6 (2016) 195–199 Contents lists available at ScienceDirect Theoretical & Applied Mechanics Letters journal homepage: www.elsevier.com/locate/taml Letter Two-dimensional modeling of the self-limiting oxidation in silicon and tungsten nanowires Mingchao Liu a,b, Peng Jin a, Zhiping Xu a, Dorian A.H. Hanaor b, Yixiang Gan b, Changqing Chen a,∗ a Department of Engineering Mechanics, CNMM & AML, Tsinghua University, Beijing 100084, China b School of Civil Engineering, The University of Sydney, Sydney, NSW 2006, Australia h i g h l i g h t s • A new diffusion-controlled kinetic model for nanowire oxidation is developed. • A finite reactive region is included to account for oxidation stress and suboxide formation. • Self-limiting nanowire oxidation and its curvature/temperature dependence are predicted. • Results are consistent with observed oxidation behavior of silicon (Si) and tungsten (W) nanowires. article info a b s t r a c t Article history: Self-limiting oxidation of nanowires has been previously described as a reaction- or diffusion-controlled Received 18 July 2016 process. In this letter, the concept of finite reactive region is introduced into a diffusion-controlled model, Received in revised form based upon which a two-dimensional cylindrical kinetics model is developed for the oxidation of silicon 1 August 2016 nanowires and is extended for tungsten. In the model, diffusivity is affected by the expansive oxidation Accepted 2 August 2016 reaction induced stress. The dependency of the oxidation upon curvature and temperature is modeled. Available online 16 August 2016 *This article belongs to the Solid Mechanics Good agreement between the model predictions and available experimental data is obtained. -
Synthesis, Characterization, and Integration of Silicon Nanowires for Nanosystems Technology
Synthesis, Characterization, and Integration of Silicon Nanowires for Nanosystems Technology by Gregory Stephen Doerk A dissertation submitted in partial satisfaction of the requirements for the degree of Doctor of Philosophy in Chemical Engineering in the Graduate Division of the University of California, Berkeley Committee in charge: Professor Roya Maboudian, Chair Professor Jeffrey Reimer Professor Liwei Lin Fall 2010 Synthesis, Characterization, and Integration of Silicon Nanowires for Nanosystems Technology Copyright 2010 by Gregory Stephen Doerk 1 Abstract Synthesis, Characterization, and Integration of Silicon Nanowires for Nanosystems Technology by Gregory Stephen Doerk Doctor of Philosophy in Chemical Engineering University of California, Berkeley Professor Roya Maboudian, Chair Silicon’s chemical stability, high natural abundance (as the second most common element in the earth’s crust), mechanical stiffness, and semiconducting behavior have made it the subject of extensive scientific investigation and the material of choice for both the micro- electronics and microelectromechanical device industries. The success of Moore’s Law that demands continual size reduction has directed it to a central place in emerging nanoscience and nanotechnology as well. Crystalline nanowires (NWs) are one nanostructured form that silicon may take that has sparked significant interest as they can exhibit considerable con- finement effects and high surface-to-volume ratios, but may be interfaced simply along one direction for the determination of material properties and implementation into new technolo- gies. The expense and difficulty involved in the creation of semiconductor nanowires using the “top down” fabrication techniques of the microelectronics industry has promoted an explosion of chemical synthetic “bottom up” techniques to produce high quality crystalline nanowires in large quanitities. -
Piezoresistivity Characterization of Synthetic Silicon Nanowires Using
JOURNAL OF MICROELECTROMECHANICAL SYSTEMS, VOL. 20, NO. 4, AUGUST 2011 959 Piezoresistivity Characterization of Synthetic Silicon Nanowires Using a MEMS Device Yong Zhang, Student Member, IEEE, Xinyu Liu, Member, IEEE, Changhai Ru, Member, IEEE, Yan Liang Zhang, Member, IEEE, Lixin Dong, Senior Member, IEEE, and Yu Sun, Senior Member, IEEE Abstract—This paper presents a microelectromechanical sys- for nanoelectronic applications. For instance, individual single- tems (MEMS) device for simultaneous electrical and mechanical walled carbon nanotubes were used as active transducer ele- characterization of individual nanowires. The device consists of ments in a pressure sensor [1] and a displacement sensor [2]. an electrostatic actuator and two capacitive sensors, capable of acquiring all measurement data (force and displacement) elec- To quantify the piezoresistivity of individual nanomaterials, a tronically without relying on electron microscopy imaging. This number of experimental techniques have been reported. The ex- capability avoids the effect of electron beam (e-beam) irradiation periments in common require simultaneous mechanical loading during nanomaterial testing. The bulk-microfabricated devices and electrical measurement of a nanomaterial. For example, the perform electrical characterization at different mechanical strain cantilever tip of an atomic force microscope (AFM) was used to levels. To integrate individual nanowires to the MEMS device for testing, a nanomanipulation procedure is developed to transfer laterally push a single-walled carbon nanotube suspended over individual nanowires from their growth substrate to the device a trench between two solid electrodes [3], which results in large inside a scanning electron microscope. Silicon nanowires are char- local deformation of the nanotube at the tube–tip contact point.