Active Filter Techniques for Reducing EMI Filter Capacitance
Total Page:16
File Type:pdf, Size:1020Kb
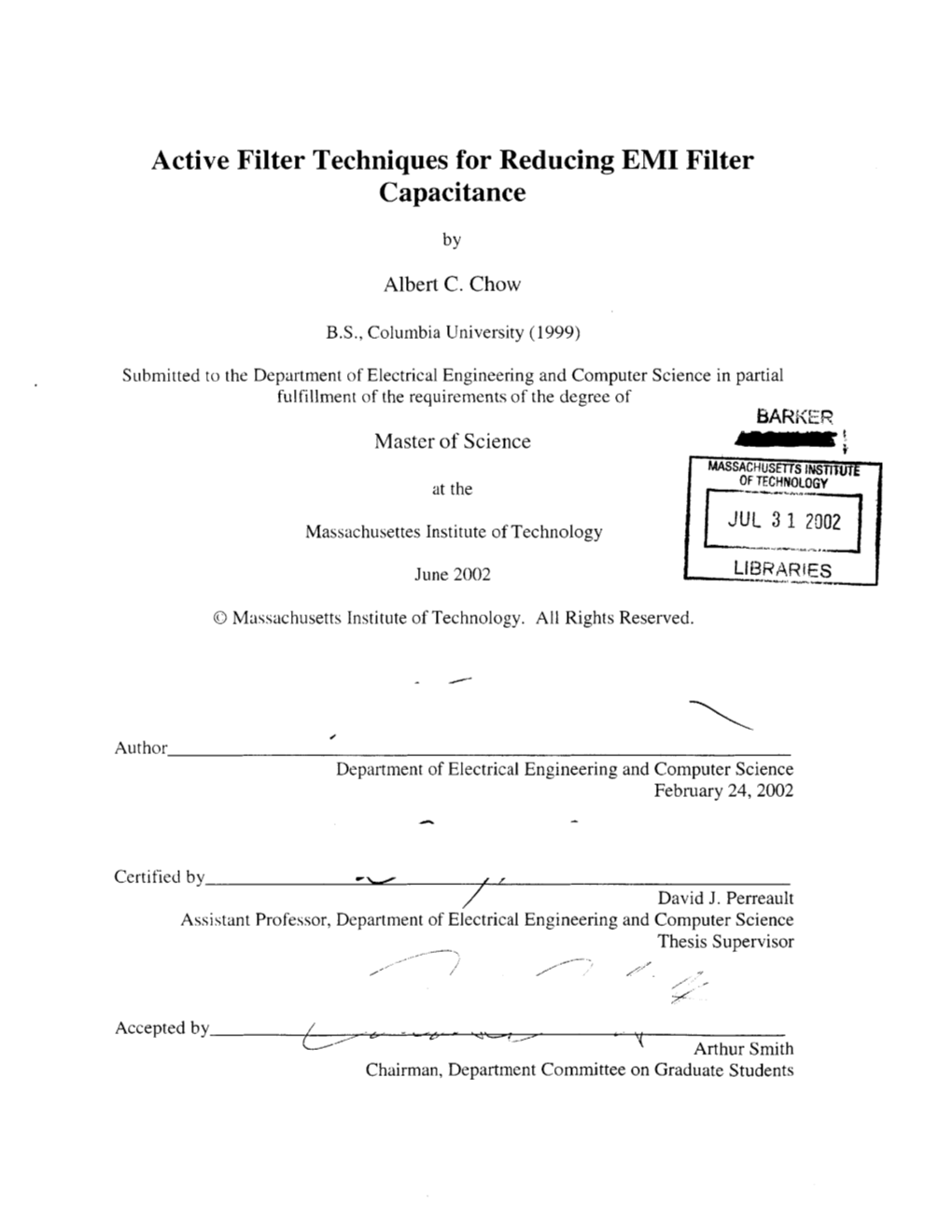
Load more
Recommended publications
-
Last.Fm Wants to Become the Web's MTV 10 May 2007
Last.fm Wants to Become the Web's MTV 10 May 2007 Online social music site Last.fm is moving into the video realm, adding music videos with a goal of providing every video ever made. The site, which provides music recommendations based on user preferences, will be leveraging its music label relationships to bring artist video content to members. Users who currently sign up at Last.fm site provide it with the names of their favorite artists and the site then generates streaming music recommendations based on those entries. A plug- in also lets the site determine which music users actually play. Listeners then vote on whether they love or hate those recommendations, so that Last.fm has a better idea of what that user might enjoy. Last.fm intends to use the same model for music video content in order to create personalized video channels. The site promises higher quality than that of YouTube, with audio encoded at 128 Kbits/s on Last.fm compared to YouTube's 64 Kbits/s. Last.fm boasts partnerships with major labels like The EMI Group and Warner Music Group in addition to approximately 20,000 independent labels like Ninja Tune, Nettwerk Music Group, Domino, Warp, Atlantic and Mute. The intent is to have every music video ever made available on the site, "from the latest hits to underground obscurities to classics from the past," according to Last.fm. In November of last year, Last.fm launched a system that provides suggestions on upcoming performances based on user location and taste in music. -
Experiment 5 Resonant Circuits and Active Filters
Introductory Electronics Laboratory Experiment 5 Resonant circuits and active filters Now we return to the realm of linear analog circuit design to consider the final op-amp circuit topic of the term: resonant circuits and active filters. Two-port networks in this category have transfer functions which are described by linear, second-order differential equations. First we investigate how a bit of positive feedback may be added to our repertory of linear op-amp circuit design techniques. We consider a negative impedance circuit which employs positive feedback in conjunction with negative feedback. This sort of circuit is found in a wide variety of linear op-amp applications including amplifiers, gyrators (inductance emulators), current sources, and, in particular, resonant circuits and sinusoidal oscillators. Next we switch topics to consider the archetypal resonant circuit: the LC resonator (inductor + capacitor). We use this circuit to define the resonant frequency and quality factor for a second-order system, and we investigate the frequency and transient responses of a high-Q, tuned circuit. We then introduce the general topic of second-order filters: resonant circuits with quality factors of around 1. We describe the behavior of second-order low-pass, high- pass, and band-pass filters. Finally, we implement such filters using linear op-amp circuits containing only RC combinations in their feedback networks, eliminating the need for costly and hard-to-find inductors. The filters’ circuitry will employ positive as well as negative feedback to accomplish this feat. We discuss some of the tradeoffs when selecting the Q to use in a second-order filter, and look at Bessel and Butterworth designs in particular. -
John Lennon from ‘Imagine’ to Martyrdom Paul Mccartney Wings – Band on the Run George Harrison All Things Must Pass Ringo Starr the Boogaloo Beatle
THE YEARS 1970 -19 8 0 John Lennon From ‘Imagine’ to martyrdom Paul McCartney Wings – band on the run George Harrison All things must pass Ringo Starr The boogaloo Beatle The genuine article VOLUME 2 ISSUE 3 UK £5.99 Packed with classic interviews, reviews and photos from the archives of NME and Melody Maker www.jackdaniels.com ©2005 Jack Daniel’s. All Rights Reserved. JACK DANIEL’S and OLD NO. 7 are registered trademarks. A fine sippin’ whiskey is best enjoyed responsibly. by Billy Preston t’s hard to believe it’s been over sent word for me to come by, we got to – all I remember was we had a groove going and 40 years since I fi rst met The jamming and one thing led to another and someone said “take a solo”, then when the album Beatles in Hamburg in 1962. I ended up recording in the studio with came out my name was there on the song. Plenty I arrived to do a two-week them. The press called me the Fifth Beatle of other musicians worked with them at that time, residency at the Star Club with but I was just really happy to be there. people like Eric Clapton, but they chose to give me Little Richard. He was a hero of theirs Things were hard for them then, Brian a credit for which I’m very grateful. so they were in awe and I think they had died and there was a lot of politics I ended up signing to Apple and making were impressed with me too because and money hassles with Apple, but we a couple of albums with them and in turn had I was only 16 and holding down a job got on personality-wise and they grew to the opportunity to work on their solo albums. -
Investor Group Including Sony Corporation of America Completes Acquisition of Emi Music Publishing
June 29, 2012 Sony Corporation INVESTOR GROUP INCLUDING SONY CORPORATION OF AMERICA COMPLETES ACQUISITION OF EMI MUSIC PUBLISHING New York, June 29, 2012 -- Sony Corporation of America, a subsidiary of Sony Corporation, made the announcement noted above. For further detail, please refer to the attached English press release. Upon the closing of this transaction, Sony Corporation of America, in conjunction with the Estate of Michael Jackson, acquired approximately 40 percent of the equity interest in the newly-formed entity that now owns EMI Music Publishing from Citigroup, and paid an aggregate cash consideration of 320 million U.S. dollars. The impact of this acquisition has already been included in Sony’s consolidated results forecast for the fiscal year ending March 31, 2013 that was announced on May 10, 2012. No impact from this acquisition is anticipated on such forecasts. For Immediate Release INVESTOR GROUP INCLUDING SONY CORPORATION OF AMERICA COMPLETES ACQUISITION OF EMI MUSIC PUBLISHING (New York, June 29, 2012) -- An investor group comprised of Sony Corporation of America, the Estate of Michael Jackson, Mubadala Development Company PJSC, Jynwel Capital Limited, the Blackstone Group’s GSO Capital Partners LP and David Geffen today announced the closing of its acquisition of EMI Music Publishing from Citigroup. Sony/ATV Music Publishing, a joint venture between Sony and the Estate of Michael Jackson, will administer EMI Music Publishing on behalf of the investor group. The acquisition brings together two of the leading music publishers, each with comprehensive and diverse catalogs of music copyrights covering all genres, periods and territories around the world. EMI Music Publishing owns over 1.3 million copyrights, including the greatest hits of Motown, classic film and television scores and timeless standards, and Sony/ATV Music Publishing owns more than 750,000 copyrights, featuring the Beatles, contemporary superstars and the Leiber Stoller catalog. -
Backgrounder.Pdf
Backgrounder March 31, 2016 Universal Music Canada donates archive of music label EMI Music Canada to University of Calgary Partnership with National Music Centre offers public access for education and celebration of music On March 31, 2016, the University of Calgary announced a gift from Universal Music Canada of the complete archive of EMI Music Canada. Universal Music Canada acquired the archive when Universal Music Group purchased EMI Music in 2012. The University of Calgary has partnered with the National Music Centre (NMC) to collaborate on opportunities for the public to celebrate music in Canada through educational programming and exhibitions that highlight the archive at NMC’s new facility, Studio Bell. This partnership began with NMC’s critical role in connecting the university with Universal Music Canada. The EMI Music Canada Archive will be accessible to students, researchers and music fans in Calgary and around the world. The University of Calgary has also partnered with the National Music Centre to collaborate on opportunities for the public to celebrate music in Canada through educational programming and exhibitions that highlight the archive. About the EMI Music Canada Archive The EMI Music Canada Archive documents 63 years of the music industry in Canada, from 1949 to 2012. The collection consists of 5,500 boxes containing more than 18,000 video recordings, 21,000 audio recordings and more than two million documents and photographs. More than 40 different recording formats are represented: quarter‐inch, half‐inch, one‐inch and two‐inch reel‐to‐reel tapes, U‐matic tapes, film, DATs, vinyl, Betacam, VHS, cassette tapes, compact discs and DVDs. -
6 Ghz RF CMOS Active Inductor Band Pass Filter Design and Process Variation Detection
Wright State University CORE Scholar Browse all Theses and Dissertations Theses and Dissertations 2014 6 GHz RF CMOS Active Inductor Band Pass Filter Design and Process Variation Detection Shuo Li Wright State University Follow this and additional works at: https://corescholar.libraries.wright.edu/etd_all Part of the Electrical and Computer Engineering Commons Repository Citation Li, Shuo, "6 GHz RF CMOS Active Inductor Band Pass Filter Design and Process Variation Detection" (2014). Browse all Theses and Dissertations. 1386. https://corescholar.libraries.wright.edu/etd_all/1386 This Thesis is brought to you for free and open access by the Theses and Dissertations at CORE Scholar. It has been accepted for inclusion in Browse all Theses and Dissertations by an authorized administrator of CORE Scholar. For more information, please contact [email protected]. 6 GHz RF CMOS Active Inductor Band Pass Filter Design and Process Variation Detection A thesis submitted in partial fulfillment of the requirements for the degree of Master of Science in Engineering By SHUO LI B.S., Dalian Jiaotong University, China, 2012 2014 WRIGHT STATE UNIVERSITY WRIGHT STATE UNIVERSITY GRADUATE SCHOOL July 1, 2013 I HEREBY RECOMMEND THAT THE THESIS PREPARED UNDER MY SUPERVISION BY Shuo Li ENTITLED “6 GHz RF CMOS Active Inductor Band Pass Filter Design and Process Variation Detection” BE ACCEPTED IN PARTIAL FULFILLMENT OF THE REQUIREMENTS FOR THE DEGREE OF Master of Science in Engineering ___________________________ Saiyu Ren, Ph.D. Thesis Director ___________________________ Brian D. Rigling, Ph.D. Chair, Department of Electrical Engineering Committee on Final Examination ___________________________ Saiyu Ren, Ph.D. ___________________________ Raymond Siferd, Ph.D. -
UNITED STATES SECURITIES and EXCHANGE COMMISSION Washington, D.C
Table of Contents UNITED STATES SECURITIES AND EXCHANGE COMMISSION Washington, D.C. 20549 FORM 10-Q (Mark One) x QUARTERLY REPORT PURSUANT TO SECTION 13 OR 15(d) OF THE SECURITIES EXCHANGE ACT OF 1934 For the quarterly period ended June 30, 2013 OR ¨ TRANSITION REPORT PURSUANT TO SECTION 13 OR 15(d) OF THE SECURITIES EXCHANGE ACT OF 1934 Commission File Number 001-32502 Warner Music Group Corp. (Exact name of Registrant as specified in its charter) Delaware 13-4271875 (State or other jurisdiction of (I.R.S. Employer incorporation or organization) Identification No.) 75 Rockefeller Plaza New York, NY 10019 (Address of principal executive offices) (212) 275-2000 (Registrant’s telephone number, including area code) Indicate by check mark whether the Registrant (1) has filed all reports required to be filed by Section 13 or 15(d) of the Securities Exchange Act of 1934 during the preceding 12 months (or for such shorter period that the Registrant was required to file such reports), and (2) has been subject to such filing requirements for the past 90 days. Yes ¨ No x Indicate by check mark whether the registrant has submitted electronically and posted on its corporate Web site, if any, every Interactive Data File required to be submitted and posted pursuant to Rule 405 of Regulation S-T (§232.405 of this chapter) during the preceding 12 months (or for such shorter period that the registrant was required to submit and post such files). Yes x No ¨ Indicate by check mark whether the Registrant is a large accelerated filer, an accelerated filer, a non-accelerated filer or a smaller reporting company. -
“A Powerful and Thrilling Blend of Punk, Rock, Indie and Hardcore That’Ll Get the Teeth in Your Skull Rattling.” - NME
“a powerful and thrilling blend of punk, rock, indie and hardcore that’ll get the teeth in your skull rattling.” - NME "they're in a field of their own... this is one of the albums of the year" - KERRANG! (5/5) “A debut as savage and unrelenting as their name suggests… the trio are kicking up dust and throwing it in the eyes of all that is inane and boring” - Upset (5/5) "post-punks making the brutal beautiful" - Total Guitar “A distinctive shot at post-hardcore… Brutus contribute an intriguing new voice to underground music” Rocksound “exciting, expansive and full of surprises” - Louder Than War (9/10) “‘Burst’ is a truly stunning record allowing two hostile genres (Punkrock and Postrock) to become real friends with apparent ease” - VISIONS (9/12) "Brutus prove they know exactly what they are doing. With this amazing debut, they deserve to get attention!" - FUZE “..if they were British or American, Brutus would’ve already qualified to grace the covers of Rock Sound and Kerrang!” - Record Collector (4/5) “Short sharp burst of genre-jumping heavy rock” - CMU “With Burst, Brutus claims their unique spot in the Belgian rock-scene. There is no other band that sounds like this trio.” - Damusic “They better start packing for a tour along the world’s biggest metropolises.”- Focus Knack (4/5) “‘Explosive' is the most fitting label for Brutus' debut album - 'Burst' carries masses of energy, catchy hooks and emotional melodies alike.” - Eclipsed (8.5/10) "The trio from Belgium releases an extraordinarily good album on Hassle Records. -
Vinyl Theory
Vinyl Theory Jeffrey R. Di Leo Copyright © 2020 by Jefrey R. Di Leo Lever Press (leverpress.org) is a publisher of pathbreaking scholarship. Supported by a consortium of liberal arts institutions focused on, and renowned for, excellence in both research and teaching, our press is grounded on three essential commitments: to publish rich media digital books simultaneously available in print, to be a peer-reviewed, open access press that charges no fees to either authors or their institutions, and to be a press aligned with the ethos and mission of liberal arts colleges. This work is licensed under the Creative Commons Attribution- NonCommercial 4.0 International License. To view a copy of this license, visit http://creativecommons.org/licenses/by-nc/4.0/ or send a letter to Creative Commons, PO Box 1866, Mountain View, CA 94042, USA. The complete manuscript of this work was subjected to a partly closed (“single blind”) review process. For more information, please see our Peer Review Commitments and Guidelines at https://www.leverpress.org/peerreview DOI: https://doi.org/10.3998/mpub.11676127 Print ISBN: 978-1-64315-015-4 Open access ISBN: 978-1-64315-016-1 Library of Congress Control Number: 2019954611 Published in the United States of America by Lever Press, in partnership with Amherst College Press and Michigan Publishing Without music, life would be an error. —Friedrich Nietzsche The preservation of music in records reminds one of canned food. —Theodor W. Adorno Contents Member Institution Acknowledgments vii Preface 1 1. Late Capitalism on Vinyl 11 2. The Curve of the Needle 37 3. -
1 "Disco Madness: Walter Gibbons and the Legacy of Turntablism and Remixology" Tim Lawrence Journal of Popular Music S
"Disco Madness: Walter Gibbons and the Legacy of Turntablism and Remixology" Tim Lawrence Journal of Popular Music Studies, 20, 3, 2008, 276-329 This story begins with a skinny white DJ mixing between the breaks of obscure Motown records with the ambidextrous intensity of an octopus on speed. It closes with the same man, debilitated and virtually blind, fumbling for gospel records as he spins up eternal hope in a fading dusk. In between Walter Gibbons worked as a cutting-edge discotheque DJ and remixer who, thanks to his pioneering reel-to-reel edits and contribution to the development of the twelve-inch single, revealed the immanent synergy that ran between the dance floor, the DJ booth and the recording studio. Gibbons started to mix between the breaks of disco and funk records around the same time DJ Kool Herc began to test the technique in the Bronx, and the disco spinner was as technically precise as Grandmaster Flash, even if the spinners directed their deft handiwork to differing ends. It would make sense, then, for Gibbons to be considered alongside these and other towering figures in the pantheon of turntablism, but he died in virtual anonymity in 1994, and his groundbreaking contribution to the intersecting arts of DJing and remixology has yet to register beyond disco aficionados.1 There is nothing mysterious about Gibbons's low profile. First, he operated in a culture that has been ridiculed and reviled since the "disco sucks" backlash peaked with the symbolic detonation of 40,000 disco records in the summer of 1979. -
NETC Welcome Package, a Refrigerator and Microwave Are Available in Each Dormitory Room
National Emergency Training Center Welcome Package National Fire Academy/Emergency Management Institute August 2021 Welcome Package for the National Fire Academy and Emergency Management Institute Welcome to the National Emergency Training Center (NETC), home of the National Fire Academy (NFA) and Emergency Management Institute (EMI). Your decision to continue your education is a positive step toward increasing your skills and knowledge, gaining recognition in the industry, and enhancing your career. This package contains important campus information, including points of contact and links to additional information. Whether this is your first time or you previously attended courses, we encourage you to review the information as our policies and procedures update periodically. The Federal Emergency Management Agency (FEMA) Educational and Training Participant Standards of Conduct (FEMA Policy 123-0-2) can be accessed via the following link (https:// www.usfa.fema.gov/training/nfa/admissions/student_policies.html). In addition, FEMA Directive: Personnel Standards of Conduct (Directive 123-0-2-1) can be accessed via the following link (https://www.usfa.fema.gov/training/nfa/admissions/student_policies.html). Please review these important documents. If you have any questions regarding your visit to NETC, please contact our Admissions Office and the staff will be glad to assist you. Our Admissions Office may be reached at 301-447-1035 or at [email protected], Monday to Friday between 8 a.m. and 4 p.m. ET. We commend you for your commitment to enhancing your education and wish you great success in your professional endeavors. NETC regulations (44 C.F.R. Part 15 and Policy 119-22, VII.A.8 and VII.A.10) prohibit personal possession of alcohol or firearms on campus. -
Manual De Procedimentos
Manual de Procedimentos Volume 8 – Área de Comunicação e Imagem Área de Comunicação e Imagem Volume: 8 - ACI MANUAL DE PROCEDIMENTOS Revisão n.º 01-14 Data: set.2014 Índice Princípios Gerais ................................................................................................................. 4 Abreviaturas e Acrónimos .................................................................................................... 6 Legislação Aplicável ............................................................................................................ 7 Mapa de Atualização do Documento ................................................................................... 8 Capítulo 1 – Gabinete de Comunicação e Relações Públicas ............................................. 9 Processo 1 - Marketing e Comunicação ...................................................................................... 9 Subprocesso 1.1 – Gestão da divulgação de notícias e eventos ............................................................. 9 Subprocesso 1.2 - E-mails enviados à comunidade Técnico ................................................................. 10 Subprocesso 1.3 – Gestão de pedidos inclusão de Banners no Website .............................................. 11 Subprocesso 1.4 – Plano de Meios ........................................................................................................ 11 Subprocesso 1.5. - Produção de Conteúdos .......................................................................................... 12