Formation of Ettringite in Pastes Containing Calcium Aluminoferrites and Gypsum P
Total Page:16
File Type:pdf, Size:1020Kb
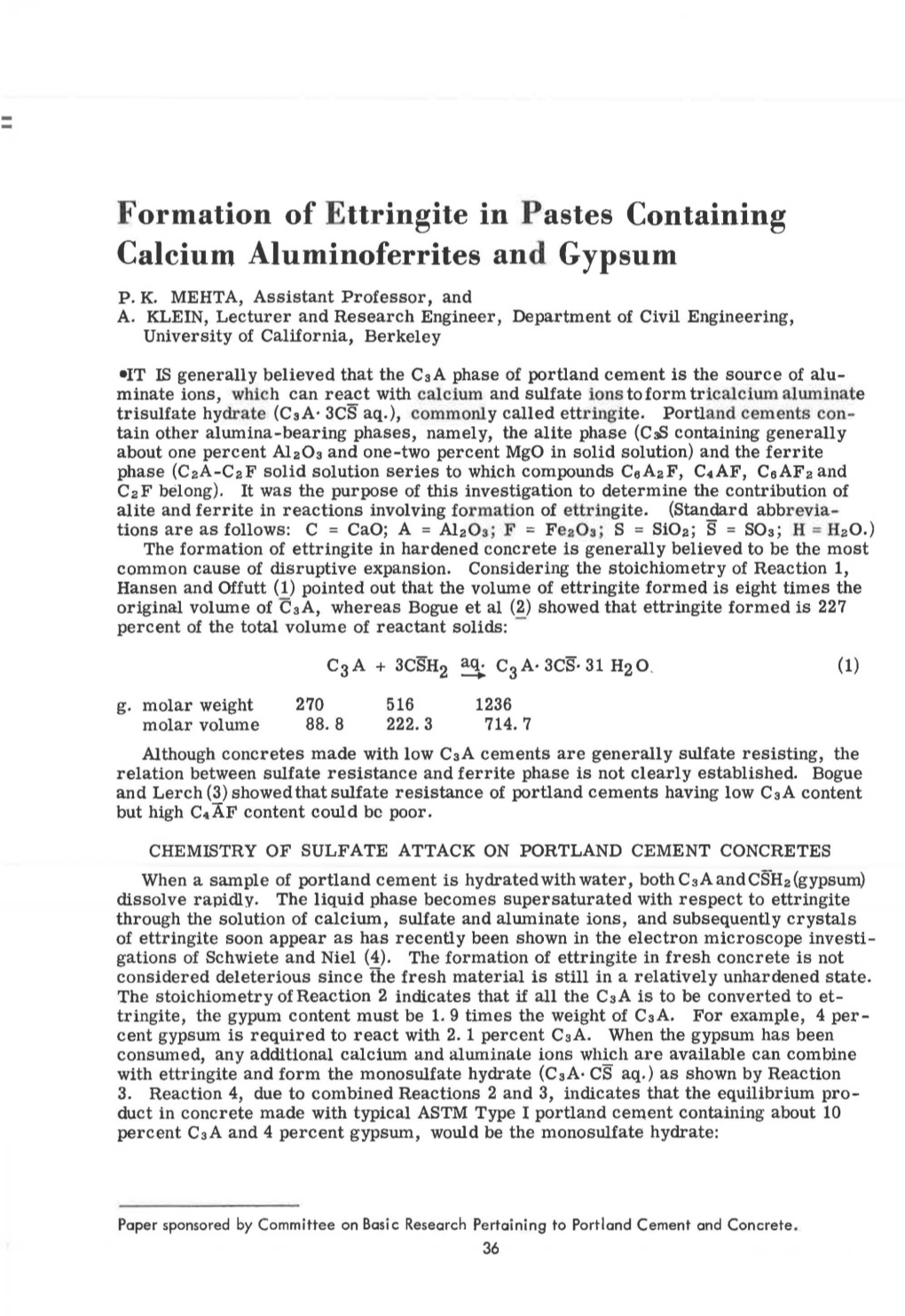
Load more
Recommended publications
-
The Sulphoaluminates of Calcium
RPS4 THE SULPHOALUMINATES OF CALCIUM By William Lerch, F. W. Ashton, and R. H. Bogue ABSTRACT Two calcium sulphoaluminates have been prepared and their compositions and optical characteristics determined. One of these, having the composition 3CaO.Al2 3 .3CaS04 .31H 2 0, is relatively stable in aqueous solutions but is decom- posed by solutions of magnesium salts and of carbonates. The other, having the composition 3CaO.Al2 3 .CaS04.12H 2 0, is relatively unstable except in high concentration of hydroxyl ion. It is readily converted to the high sulphate form in aqueous solutions but is decomposed by magnesium salts and carbonates. In sulphate solutions the high sulphate form may be produced, but in the presence of a slight excess of magnesium salts or carbonates neither of the sulphoaluminates can continue to exist. In these cases the less soluble magnesium hydroxide and calcium carbonate, respectively, are formed. CONTENTS Page I. Introduction 715 II. Review of the literature 716 III. Experimental procedure 718 1. The high sulphate calcium sulphoaluminate 718 2. The low sulphate calcium sulphoaluminate 722 3. Calcium sulphosilicoaluminate 724 IV. Conditions of stability in salt solutions 725 V. Relative stability with calcium chloraluminate 729 VI. Summary 729 L INTRODUCTION Among the products formed by the action of sulphate waters on Portland cement there has been observed, under some conditions, a calcium sulphoaluminate. This has been ascribed by some inves- tigators to be responsible for certain expansion effects observed at times in concrete which is exposed to sea water and to alkali soil waters. The exact nature of this compound and its conditions of formation and stability have not been adequately treated, however. -
Cement Heat of Hydration and Thermal Control Ahmadreza Sedaghat
University of South Florida Scholar Commons Graduate Theses and Dissertations Graduate School 3-22-2016 Cement Heat of Hydration and Thermal Control Ahmadreza Sedaghat Follow this and additional works at: http://scholarcommons.usf.edu/etd Part of the Civil Engineering Commons, and the Materials Science and Engineering Commons Scholar Commons Citation Sedaghat, Ahmadreza, "Cement Heat of Hydration and Thermal Control" (2016). Graduate Theses and Dissertations. http://scholarcommons.usf.edu/etd/6142 This Dissertation is brought to you for free and open access by the Graduate School at Scholar Commons. It has been accepted for inclusion in Graduate Theses and Dissertations by an authorized administrator of Scholar Commons. For more information, please contact [email protected]. Cement Heat of Hydration and Thermal Control by Ahmadreza Sedaghat A dissertation submitted in partial fulfillment of the requirements for the degree of Doctor of Philosophy Department of Civil and Environmental Engineering College of Engineering University of South Florida Major Professor: A. Zayed, Ph.D. Manoj K. Ram, Ph.D. Mahmoood H. Nachabe, Ph.D. Ajit Mujumdar, Ph.D. Abdul Malik, Ph.D. Date of Approval: January 29, 2016 Keywords: Portland Cement, Isothermal Calorimetry, Graphene Nanoplatelet, Statistical Analysis, Thermal Cracking Copyright © 2016, Ahmadreza Sedaghat DEDICATION I would like to dedicate my dissertation to my parents (Aliasghar Sedaghat, Golnar J. Javidan), my beloved wife Rana, my brother Arsalan and my grandmother Ms. Koukab Sanakhan. A special feeling of gratitude to my parents whose words of encouragement and push for tenacity ring in my ears. My brother Arsalan who supported me emotionally and was a strong pier for my parents to lean on while I was far away from home pursuing my education. -
Delayed Ettringite Formation
Ettringite Formation and the Performance of Concrete In the mid-1990’s, several cases of premature deterioration of concrete pavements and precast members gained notoriety because of uncertainty over the cause of their distress. Because of the unexplained and complex nature of several of these cases, considerable debate and controversy have arisen in the research and consulting community. To a great extent, this has led to a misperception that the problems are more prevalent than actual case studies would indicate. However, irrespective of the fact that cases of premature deterioration are limited, it is essential to address those that have occurred and provide practical, technically sound solutions so that users can confidently specify concrete in their structures. Central to the debate has been the effect of a compound known as ettringite. The objectives of this paper are: Fig. 1. Portland cements are manufactured by a process that combines sources of lime (such as limestone), silica and • to define ettringite and its form and presence in concrete, alumina (such as clay), and iron oxide (such as iron ore). Appropriately proportioned mixtures of these raw materials • to respond to questions about the observed problems and the are finely ground and then heated in a rotary kiln at high various deterioration mechanisms that have been proposed, and temperatures, about 1450 °C (2640 °F), to form cement compounds. The product of this process is called clinker • to provide some recommendations on designing for durable (nodules at right in above photo). After cooling, the clinker is concrete. interground with about 5% of one or more of the forms of Because many of the questions raised relate to cement character- calcium sulfate (gypsum shown at left in photo) to form portland cement. -
The Influence Mechanism of Ettringite Crystals and Microstructure
materials Article The Influence Mechanism of Ettringite Crystals and Microstructure Characteristics on the Strength of Calcium-Based Stabilized Soil Youmin Han 1,2,3 , Junwu Xia 1,3,* , Hongfei Chang 1 and Jun Xu 4,5 1 State Key Laboratory for Geomechanics and Deep Underground Engineering, China University of Mining and Technology, Daxue Road, Xuzhou 221116, China; [email protected] (Y.H.); [email protected] (H.C.) 2 School of Architecture and Civil Engineering, Anhui Polytechnic University, Beijing Road, Wuhu 241000, China 3 Jiangsu Collaborative Innovation Center for Building Energy Saving and Construction Technology, Xueyuan Road, Xuzhou 221116, China 4 School of Civil Engineering and Architecture, Jiangsu University of Science and Technology, Changhui Road, Zhenjiang 212100, China; [email protected] 5 School of Materials Science and Engineering, Southeast University, Southeast University Road, Nanjing 211189, China * Correspondence: [email protected] or [email protected] Abstract: To reveal the influence mechanism of ettringite (AFt) crystals and microstructure character- istics on the strength of calcium-based stabilized soil, the strengths and microscopic properties of seven groups of stabilized soil samples were studied systematically through unconfined compressive strength, scanning electron microscope (SEM), X-ray diffraction (XRD), thermogravimetry (TG), and Fourier transform infrared spectroscopy (FTIR) testing methods. The results indicate that the strength of the cement-stabilized soil is relatively high because abundant calcium silicate hydrate (CSH) gels Citation: Han, Y.; Xia, J.; Chang, H.; coat the outer surface of soil particles to cement together. For the cement–gypsum-stabilized soil, Xu, J. The Influence Mechanism of Ettringite Crystals and superabundant thick and long AFt crystals make the pores in soil particles larger, and the sample Microstructure Characteristics on the becomes looser, resulting in lower strength than that of the cement-stabilized soil. -
Brownmillerite Ca2(Al, Fe )2O5 C 2001-2005 Mineral Data Publishing, Version 1
3+ Brownmillerite Ca2(Al, Fe )2O5 c 2001-2005 Mineral Data Publishing, version 1 Crystal Data: Orthorhombic. Point Group: mm2. As square platelets, to about 60 µm; massive. Physical Properties: Hardness = n.d. D(meas.) = 3.76 D(calc.) = 3.68–3.73 Optical Properties: Semitransparent. Color: Reddish brown. Optical Class: Biaxial (–). Pleochroism: Distinct; X = Y = yellow-brown; Z = dark brown. Orientation: Y and Z lie in the plane of the platelets; extinction in that plane is diagonal. α = < 2.02 β = > 2.02 γ = > 2.02 2V(meas.) = n.d. Cell Data: Space Group: Ibm2. a = 5.584(5) b = 14.60(1) c = 5.374(5) Z = 2 X-ray Powder Pattern: Near Mayen, Germany. 2.65 (vs), 7.19 (s), 2.78 (s), 1.93 (s), 2.05 (ms), 3.65 (m), 1.82 (m) Chemistry: (1) (2) (3) TiO2 1.5 1.9 Al2O3 17.2 22.3 13.1 Fe2O3 30.5 27.6 41.9 Cr2O3 0.1 n.d. MgO n.d. n.d. CaO 46.2 44.8 43.7 insol. 4.0 LOI 0.5 Total 94.4 100.3 100.6 (1) Near Mayen, Germany; by semiquantitative spectroscopy. (2) Hatrurim Formation, Israel; corresponds to Ca1.99(Al1.09Fe0.86Ti0.05)Σ=2.00O5. (3) Do.; corresponds to Ca1.95(Fe1.31Al0.64 Ti0.06)Σ=2.01O5. Occurrence: In thermally metamorphosed limestone blocks included in volcanic rocks (near Mayen, Germany); in high-temperature, thermally metamorphosed, impure limestones (Hatrurim Formation, Israel). Association: Calcite, ettringite, wollastonite, larnite, mayenite, gehlenite, diopside, pyrrhotite, grossular, spinel, afwillite, jennite, portlandite, jasmundite (near Mayen, Germany); melilite, mayenite, wollastonite, kalsilite, corundum (Kl¨och, Austria); spurrite, larnite, mayenite (Hatrurim Formation, Israel). -
How to Make Concrete More Sustainable Harald Justnes1
Journal of Advanced Concrete Technology Vol. 13, 147-154, March 2015 / Copyright © 2015 Japan Concrete Institute 147 Scientific paper How to Make Concrete More Sustainable Harald Justnes1 A selected paper of ICCS13, Tokyo 2013. Received 12 November 2013, accepted 16 February 2015 doi:10.3151/jact.13.147 Abstract Production of cement is ranking 3rd in causes of man-made carbon dioxide emissions world-wide. Thus, in order to make concrete more sustainable one may work along one or more of the following routes; 1) Replacing cement in con- crete with larger amounts of supplementary cementing materials (SCMs) than usual, 2) Replacing cement in concrete with combinations of SCMs leading to synergic reactions enhancing strength, 3) Producing leaner concrete with less cement per cubic meter utilizing plasticizers and 4) Making concrete with local aggregate susceptible to alkali silica reaction (ASR) by using cement replacements, thus avoiding long transport of non-reactive aggregate. 1 Introduction SCMs, also uncommon ones like calcined marl 2. Replacing cement in concrete with combinations of The cement industry world-wide is calculated to bring SCMs leading to synergic reactions enhancing about 5-8% of the total global anthropogenic carbon strength dioxide (CO2) emissions. The general estimate is about 3. Producing leaner concrete with less cement per cubic 1 tonne of CO2 emission per tonne clinker produced, if meter utilizing plasticizers. fossil fuel is used and no measures are taken to reduce it. 4. Making concrete with local aggregate susceptible to The 3rd rank is not because cement is such a bad mate- alkali silica reaction (ASR) by using cement re- rial with respect to CO2 emissions, but owing to the fact placements, thus avoiding long transport of non- that it is so widely used to construct the infrastructure reactive aggregate and buildings of modern society as we know it. -
Investigation of the Incompatibilities of Cement and Superplasticizers and Their Influence on the Rheological Behavior
materials Article Investigation of the Incompatibilities of Cement and Superplasticizers and Their Influence on the Rheological Behavior Ursula Pott 1, Cordula Jakob 2, Daniel Jansen 2, Jürgen Neubauer 2 and Dietmar Stephan 1,* 1 Department of Civil Engineering, Building Materials and Construction Chemistry, Technische Universität Berlin, 13355 Berlin, Germany; [email protected] 2 Department of Geography and Geosciences, GeoZentrum Nordbayern, Friedrich-Alexander-University, 91054 Erlangen, Germany; [email protected] (C.J.); [email protected] (D.J.); [email protected] (J.N.) * Correspondence: [email protected] Received: 2 December 2019; Accepted: 18 February 2020; Published: 21 February 2020 Abstract: The rheological behavior of cement paste and the improvement of its flowability takes center stage in many research projects. An improved flowability can be achieved by the addition of superplasticizers (SP), such as polycarboxylate ethers (PCE). In order to be able to use these PCEs effectively and in a variety of ways and to make them resistant to changes in the environment, it is crucial to understand the influence of SPs on cement hydration. For that reason, the topic of this paper was the incompatibility of a specific SP and an ordinary Portland cement (OPC). The incompatible behavior was analyzed using rheological tests, such as the spread flow test and penetration test, and the behavior was compared by means of an ultrasound technique and explained by the phase content measured by in-situ X-ray diffraction (XRD) the heat evolution measured by calorimetry, and scanning electron microscope (SEM) images. We showed that the addition of the SP in a high dosage led to a prevention of the passivation of the most reactive and aluminum-containing clinker phases, aluminate and brownmillerite. -
Raman Spectroscopy and Single-Crystal High-Temperature Investigations of Bentorite, Ca6cr2(SO4)3(OH)12·26H2O
minerals Article Raman Spectroscopy and Single-Crystal High-Temperature Investigations of Bentorite, Ca6Cr2(SO4)3(OH)12·26H2O Rafał Juroszek 1,* , Biljana Krüger 2 , Irina Galuskina 1 , Hannes Krüger 2 , Martina Tribus 2 and Christian Kürsten 2 1 Institute of Earth Sciences, Faculty of Natural Sciences, University of Silesia, B˛edzi´nska60, 41-205 Sosnowiec, Poland; [email protected] 2 Institute of Mineralogy and Petrography, University of Innsbruck, Innrain 52, 6020 Innsbruck, Austria; [email protected] (B.K.); [email protected] (H.K.); [email protected] (M.T.); [email protected] (C.K.) * Correspondence: [email protected]; Tel.: +48-516-491-438 Received: 28 November 2019; Accepted: 27 December 2019; Published: 30 December 2019 Abstract: The crystal structure of bentorite, ideally Ca Cr (SO ) (OH) 26H O, a Cr3+ analogue of 6 2 4 3 12· 2 ettringite, is for the first time investigated using X-ray single crystal diffraction. Bentorite crystals of suitable quality were found in the Arad Stone Quarry within the pyrometamorphic rock of the Hatrurim Complex (Mottled Zone). The preliminary semi-quantitative data on the bentorite composition obtained by SEM-EDS show that the average Cr/(Cr + Al) ratio of this sample is >0.8. Bentorite crystallizes in space group P31c, with a = b = 11.1927(5) Å, c =21.7121(10) Å, V = 2355.60(18) Å3, and Z = 2. The crystal structure is refined, including the hydrogen atom positions, to an agreement index R1 = 3.88%. The bentorite crystal chemical formula is Ca (Cr Al ) [(SO ) (CO ) ] (OH) ~25.75H O. -
Effects of Storage Temperature and Time on False Setting Behavior of CPI-S Portland Cement
321 Cerâmica 66 (2020) 321-329 http://dx.doi.org/10.1590/0366-69132020663792842 Effects of storage temperature and time on false setting behavior of CPI-S Portland cement (Efeitos da temperatura e do tempo de armazenamento no comportamento de falsa pega do cimento Portland CPI-S) R. M. Mota1, A. S. Silva2, V. H. S. Ramos1, J. C. T. Rezende1, E. de Jesus1* 1Federal University of Sergipe, Department of Chemical Engineering, Av. Marechal Rondon, s/n, São Cristóvão, SE, Brazil 2Federal University of Sergipe, Department of Mathematics, São Cristóvão, SE, Brazil Abstract The false setting is when cement stiffens prematurely in a few minutes after adding water. Some variables could cause false setting in CPI-S-32 Portland cement, for example, alkali concentration in the cement, the formation of alite (C3S) with low reactivity, and cement storage temperature and time in silos. Temperature increases cause calcium sulfate dihydrate to dehydrate, forming hemihydrate (CaSO4.0.5H2O) or anhydrite (CaSO4), which causes the false setting. In this study, the influence of cement storage temperature (100, 105, 110, 120, and 130 °C) combined with the cement storage time (30, 60, and 120 min) in a silo was studied regarding the CPI-S-32 false setting behavior. It was verified that temperatures above 110 °C and storage time above 60 min are conditions that favor the false setting of CPI-S-32 cement. Physicochemical analysis, TG/DTG, XRF, and XRD were applied as complementary analyzes for the false setting assays of CPI-S-32. Keywords: false setting, CPI-S-32 Portland cement, cement storage temperature, cement storage time. -
Cement Safety Data Sheet
Product Name: Portland Cement Revision Date: July 2018 Page 1 of 12 MITSUBISHI CEMENT CORPORATION Safety Data Sheet Portland Cement Section 1 Identification GHS product identifier: Portland Cement Chemical name: Calcium compounds, calcium silicate compounds, and other calcium compounds containing iron and aluminum make up the majority of this product. Major Compounds: 3CaO•SiO2 Tricalcium silicate 2CaO•SiO2 Dicalcium silicate 3CaO•Al2O3 Tricalcium aluminate 4CaO•Al2O3•Fe2O3 Tetracalcium aluminoferrite CaSO4•2H2O Calcium sulfate dihydrate or Gypsum Other means of identification: Cement, hydraulic cement, Portland cement silicate. Relevant identified uses: Building materials, construction, a basic ingredient in concrete. MANUFACTURER: TELEPHONE NUMBERS: Mitsubishi Cement Corporation Phone: . (760) 248-5184 Cushenbury Plant Fax: . (760) 248-5139 5808 State Highway 18 Lucerne Valley, CA 92356 Contact Person: David Rib EMERGENCY TELEPHONE NUMBER: Call 911 for local emergency services. Section 2 Hazards Identification Portland cement is a gray or white powder. A single short-term exposure to the dry powder is not likely to cause serious harm. DANGER! Overexposure to Portland cement can cause serious, potentially irreversible skin or eye damage in the form of chemical (caustic) burns, including third degree burns. The same serious injury can occur if wet or moist skin has prolonged contact exposure to dry Portland cement. Carcinogenicity. Portland cement is not classifiable as a human carcinogen by the Occupational Health and Safety Administration (OSHA), the National Toxicity Program (NTP), or the International Agency for Research on Cancer (IARC). However, Portland cement may contain trace amounts of substances listed as carcinogens by NCP, OHSA, or IARC: crystalline silica, chromium VI compounds, nickel compounds, lead compounds. -
Novel Approach for Suppression of Ettringite Formation in Sulfate
applied sciences Article Novel Approach for Suppression of Ettringite Formation in Sulfate-Bearing Soil Using Blends of Nano-Magnesium Oxide, Ground Granulated Blast-Furnace Slag and Rice Husk Ash Khaled Ibrahim Azarroug Ehwailat, Mohd Ashraf Mohamad Ismail * and Ali Muftah Abdussalam Ezreig School of Civil Engineering, Universiti Sains Malaysia, Engineering Campus, Nibong Tebal 14300, Seberang Prai Selatan, Pulau Pinang, Malaysia; [email protected] (K.I.A.E.); [email protected] (A.M.A.E.) * Correspondence: [email protected] Abstract: The treatment of sulfate-bearing soil with calcium-based stabilizers such as cement or lime often results in ettringite formation, consequently leading to swelling and strength deterioration. Ettringite formation has negative environmental and economic effects on various civil engineering structures. This study was conducted to investigate the use of different materials (nano–magnesium oxide (M), ground granulated blast-furnace slag (GGBS), and rice husk ash (RHA)) for gypseous soil stabilization to prevent ettringite formation. Various tests were performed, including flexural strength, unconfined compression strength, linear expansion, and microstructure analysis (SEM/EDX), on lime (L)-, (M)-, (M-RHA)-, (M-GGBS)-, and (M-GGBS-RHA)-stabilized gypseous soil samples to determine Citation: Ehwailat, K.I.A.; Ismail, their properties. The results indicated that the swelling rates of the soil samples mixed with 20% M.A.M.; Ezreig, A.M.A. Novel M-RHA, M-GGBS, and M-GGBS-RHA binders were much lower (less than 0.01% of volume change) Approach for Suppression of than those of the soil samples mixed with 10% and 20% lime-stabilized binders after a curing period Ettringite Formation in of 90 days. -
Secondary Ettringite Formation in Concrete Subjected to Different Curing Conditions
CORE Metadata, citation and similar papers at core.ac.uk Provided by Centro de Servicios en Gestión de Información Cement and Concrete Research 30 (2000) 1407±1412 Secondary ettringite formation in concrete subjected to different curing conditions Oscar R. Batica,*, Carlos A. Milanesia, Pedro J. Maizab, Silvina A. Marfilb aLaboratorio de Entrenamiento Multidisciplinario para la InvestigacioÂn TecnoloÂgica, (LEMIT-CIC), Calle 52 entre 121 y 122, La Plata 1900, Argentina b Departamento de GeologÂa, Universidad Nacional del Sur, San Juan 670, BahÂa Blanca 8000, Argentina Received 20 September 1999; accepted 16 June 2000 Abstract The large amount of ettringite detected in concrete affected by different failure mechanisms (alkali-silica reaction [ASR], freezing and thawing [FT], and wetting and drying [WD]) in sulfate-free environments has been a matter of concern for many researchers over the past years. Two major lines to approach this issue have been defined. One of them considers ettringite as the main cause of damage and the other assumes that it appears after concrete distress. In order to contribute to the clarification of this phenomenon, research was conducted to cover the above issues. This paper reports on the conclusions arrived at up to date, from studies conducted on concrete affected by different damaging mechanisms: FT, WD, and precracking induced by loading and ASR. Changes in length and mechanical strength of test concrete are reported, as well as the evaluations made by optical microscopy (OM), scanning electron microscopy (SEM) and energy dispersive X-ray analysis (EDAX). Secondary ettringite formation (SEF) is closely linked to pore fluid transport in the mass of concrete.