"Polycyanoacrylates". In: Encyclopedia of Polymer Science
Total Page:16
File Type:pdf, Size:1020Kb
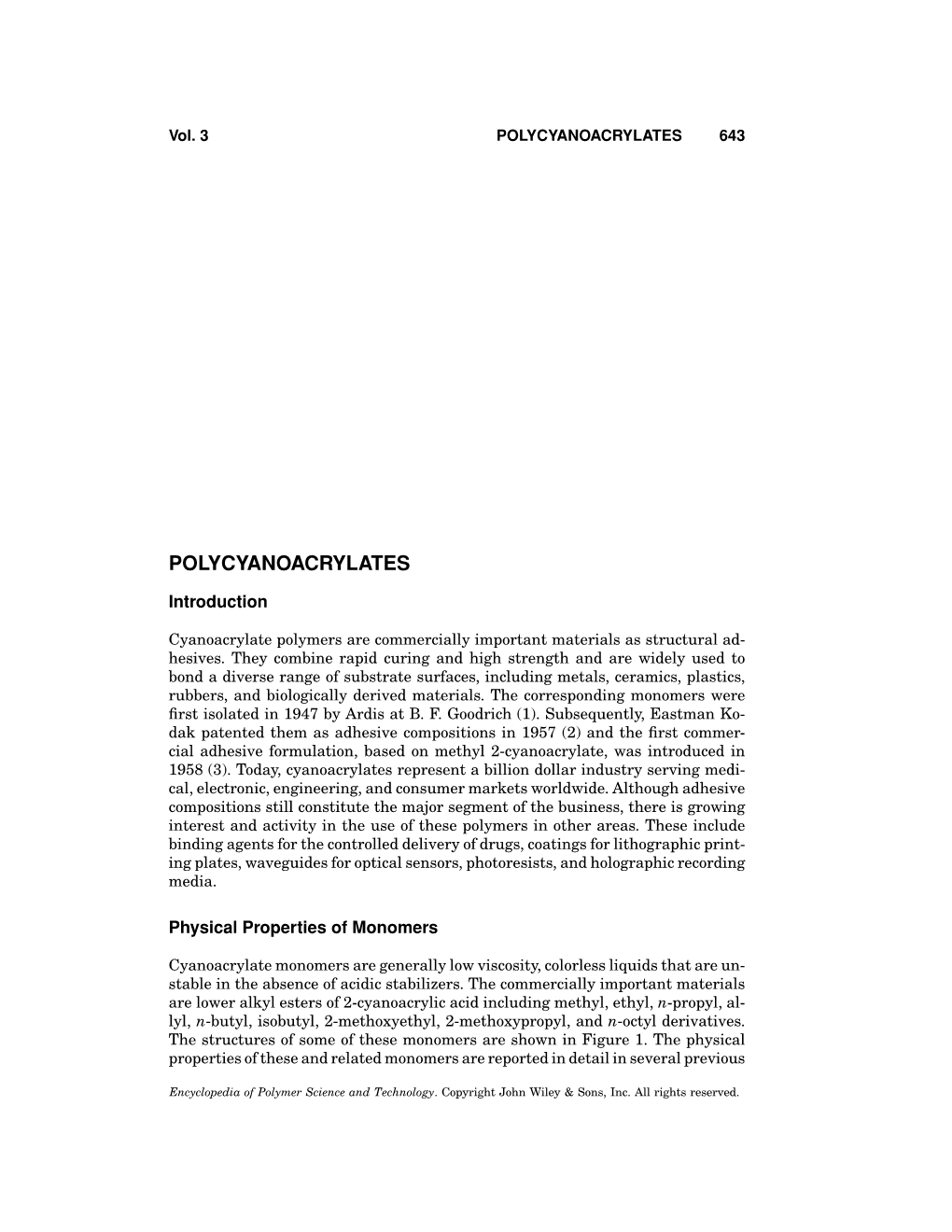
Load more
Recommended publications
-
Optrel-Filter-Guide.Pdf
Guide to optrel filters This information is intended to provide an overview of the relevant factors that will help in the selection of a suitable fil- ter. If you lack the necessary information and/or are not sure about your choice, consult a professional first. Only with the right choice you can protect yourself from the health risks caused by pollutants in the ambient air. 1. information you need for a correct choose: • Pollutants in the ambient air • Concentration(s) of the pollutant(s) • Aggregate state(s) of the pollutant(s) (gaseous, solid, as a mixture) • Can the pollutants be detected without aids? (e.g. odor or taste) • The valid limit values e.g. AGW, OEL, ... • Oxygen content of the ambient air. There are locally different minimum concentrations apply (Germany at least 17 vol. %) • Should respiratory protection be combined with other be combined? (head, eye or hearing protection) 3. selection of the suitable filter device With the information from chapter 2, the necessary protection factor can be determined. The following chart shows the protection factor of the optrel respiratory protection equipment is listed: 2 optrel Filter Guide Device Marking Nominal protection factor Particle filtering devices e3000X in combination with TH3P 500 PAPR helmet panoramaxx se- ries, sphere series, clearmaxx series swiss air TH3P 500 e3000X in combination with TH2P 50 PAPR clearmaxx und industri- al hard hat e3000X in combination with TH1P 10 PAPR panoramaxx series and industrial hard hat Chart 1 with protection factors of optrel equipment (Germany) The NPF is derived from the maximum permissible leakage of the respective equipment. -
(12) United States Patent (10) Patent No.: US 6,699,940 B2 Shalaby (45) Date of Patent: Mar
USOO66.9994OB2 (12) United States Patent (10) Patent No.: US 6,699,940 B2 Shalaby (45) Date of Patent: Mar. 2, 2004 (54) CYANOACRYLATE-CAPPED (56) References Cited HETEROCHAIN POLYMERS AND TISSUE ADHESIVES AND SEALANTS THEREFROM U.S. PATENT DOCUMENTS 4,260,719 A * 4/1981 Ching ........................ 528/196 (75) Inventor: Shalaby W. Shalaby, Anderson, SC 4,377,490 A * 3/1983 Shiraishi et al. ...... 252/188.3 R (US) 5,340,873 A * 8/1994 Mitry .......................... 525/10 5,350,798 A 9/1994 Linden et al. ................ 525/41 (73) Assignee: Poly Med, Inc., Anderson, SC (US) 5,373,035 A * 12/1994 Uemura et al. ............. 523/212 5,422,068 A 6/1995 Shalaby et al. ............... 422/22 (*) Notice: Subject to any disclaimer, the term of this 5,653,992 A 8/1997 Bezwada et al. ............ 264/4.3 5,714,159 A 2/1998 Shalaby ...................... 424/426 patent is extended or adjusted under 35 U.S.C. 154(b) by 0 days. 6,299,631 B1 10/2001 Shalaby ...................... 606/214 6,462,169 B1 10/2002 Shalaby ...................... 528/354 (21) Appl. No.: 10/300,079 6,467,169 B1 10/2002 Wieres ........................ 29/890 (22) Filed: Nov. 20, 2002 * cited by examiner (65) Prior Publication Data Primary Examiner Helen L. Pezzuto US 2003/0105256 A1 Jun. 5, 2003 (74) Attorney, Agent, or Firm-Leigh P. Gregory Related U.S. Application Data (57) ABSTRACT (60) Provisional application No. 60/335,439, filed on Dec. 4, The present invention is directed toward cyanoacrylate 2001. based tissue adhesive or Sealant compositions comprising (51) Int. -
Proposed 15-Day Modifications
INFORMAL PRELIMINARY REVIEW DRAFT Proposed 15-Day Modifications ATTACHMENT A PROPOSED 15-DAY MODIFICATIONS California Code of Regulations, Title 17, Division 3, Chapter 1, Subchapter 7.7, Article 1 Note: This document shows proposed modifications to the originally proposed amendments to the Regulation for the Reporting of Criteria Air Pollutants and Toxic Air Contaminants, as presented during the November 19, 2020, meeting of the California Air Resources Board. At that meeting, the Board directed staff to make modifications to the proposed amendments based on public comments received, and to provide these updates for public comment for a period of at least 15 days. The pre-existing regulation text is set forth below in normal type. The original proposed amendments are shown in underline formatting to indicate additions and strikeout to indicate deletions. The additional proposed modifications made available with the notice of public availability of modified text dated March XY, 2021, are shown in double- underline to indicate additions and double-strikeout to indicate deletions. The symbol “***” means that intervening text not proposed for amendment is not shown. PROPOSED AMENDMENTS TO THE REGULATION FOR THE REPORTING OF CRITERIA AIR POLLUTANTS AND TOXIC AIR CONTAMINANTS California Code of Regulations, Title 17, Division 3, Chapter 1, Subchapter 7.7, Articles 1 and 2 Amend Subchapter 7.7, Article 1, and sections 93400, 93401, 93402, 93403, 93404, 93405, 93406, 93407, 93408, 93409, 93410, title 17, California Code of Regulations, and adopt new Subchapter 7.7, Article 2, sections 93420, 93421, and new Subchapter 7.7, Article 2, Appendices A and B to title 17, California Code of Regulations, to read as follows: CARB / AQPSD 1 2/11/2021 INFORMAL PRELIMINARY REVIEW DRAFT Proposed 15-Day Modifications Subchapter 7.7: Regulation for the Reporting of Criteria Air Pollutants and Toxic Air Contaminants Article 1. -
Born2bond Structural Cyanoacrylate Adhesive
Born2Bond Structural Cyanoacrylate Adhesive Description Born2Bond™ Structural Cyanoacrylate Adhesive is a high-strength, high-temperature (120°C) hybrid cyanoacrylate adhesive that provides a fast fixture time at room temperature while maintaining good processability and the capability to bond gaps up to 5mm. This product offers excellent bonding characteristics to a large variety of substrates, including aluminium, plastics and elastomers, but also porous substrates, such as woods, chipboard and leather. Born2Bond Structural is the toughest structural, fast cure two part (2K) cyanoacrylate adhesive on the market, with the longest open time. Born2Bond Structural offers “on demand” structural bonding. Once mixed and applied, the exposed dot or bead has an open time of up to 30 minutes – but a fixture time of only seconds once the parts are assembled. This fixture and ultimate cure time compares favourably with other structural adhesive chemistries. Formulated using MECA (methoxyethyl cyanoacrylate) chemistry, Born2Bond Structural is able to withstand temperatures up to 120°C, far exceeding the capabilities of standard cyanoacrylate adhesives. It offers a balance between bonding speed, long open time, bond strength (>6 MPa), and impact and environmental resistance. Born2Bond Structural is supplied in a syringe cartridge, available in 10g and 50g sizes. Both cartridges come with static mixing nozzles. The 10g size is suitable for manual application and comes with a plunger. The 50g size is used with a dispensing gun for manual application, -
Dispensing Solutions for Cyanoacrylate Adhesives White
Dispensing Solutions for Cyanoacrylate Adhesives Contents How Cyanoacrylates Work .......................................................................3 Advantages of CAs ...................................................................................4 CA Dispensing Challenges .......................................................................4 Best Practices for Dispensing CAs .....................................................5-12 Best Systems for Dispensing CAs ....................................................13-14 Useful Resources ...................................................................................15 Introduction Cyanoacrylate adhesives, also known as CAs or cyanos, are highly effective at bonding many types of materials together in assembly processes. Often referred to as super glues, they exhibit high bond strength and fast cure times that help manufacturers speed production processes for higher throughput yields. This makes them an ideal choice for assembling products in a variety of industries, including automotive, electronics, life sciences, defense, and consumer goods. Though beneficial, these moisture-cure adhesives can be a challenge, especially when your assembly process requires precise, repeatable dispensing. This paper outlines proper handling methods and dispensing solutions for successful CA dispensing. Find out how to minimize material waste by more than 60% while also minimizing operator exposure to the adhesive. Speed your production processes while producing higher quality parts with -
Technical Procedure for Cyanoacrylate Ester Fingerprint
Technical Procedure for Cyanoacrylate Ester Fingerprint Development Kits Version 5 Latent Evidence Section Effective Date: 02/01/2019 Issued by Latent Technical Leader Technical Procedure for Cyanoacrylate Ester Fingerprint Development Kits 1.0 Purpose – This procedure is a non-porous development procedure. 2.0 Scope – This procedure is a step in the processing of non-porous evidence that may contain impressions that require developing/enhancing. 2.1 The Cyanoacrylate Ester Fingerprint Development Kit is a commercially prepared product that polymerizes the latent impression using cyanoacrylate. Numerous materials, including plastic bags, weapons, metals, and various other substrates, may be processed using the Cyanoacrylate Ester Fingerprint Development Kit. Cyanoacrylate shall be used as a preliminary process for subsequent processing techniques. Fluorescent dye staining, in conjunction with laser examinations, is dependent on the proper use of cyanoacrylate fuming techniques. 3.0 Definitions Alternate light source: Any of the multiple forensic light sources readily available in the Latent Evidence Section including, but not limited to, the CrimeScope (CS), Mini-CrimeScope (MCS), and TracER Laser. Ambient light: Light that is readily available in the office environment (i.e., natural light or light that emanates from an office lighting source). CE: Cyanoacrylate ester, also known as super glue. Cyanoacrylate Ester Fingerprint Development Kit: A commercially prepared cyanoacrylate ester fuming kit that assists in the processing of non-porous items of evidence with the assistance of cyanoacrylate ester. Commercial products currently used include Hot-Shot by Lynn Peavey and Cyano- Shot by Sirchie. 4.0 Equipment, Materials and Reagents 4.1 Equipment and Materials Cyanoacrylate Ester Fingerprint Development Kit 4.2 Reagents – N/A 5.0 Procedure 5.1 Hot-Shot (Lynn Peavey Product): 5.1.1 Items to be processed with the Hot-Shot shall first be examined visually in ambient lighting conditions and then with the use of an alternate light source (CS, MCS). -
The Pennsylvania State University the Graduate School College Of
The Pennsylvania State University The Graduate School College of Engineering NOVEL TEMPLATE-LESS SYNTHESIS OF POLYCYANOACRYLATE NANOFIBERS A Thesis in Chemical Engineering by Pratik Mankidy 2007 Pratik Mankidy Submitted in Partial Fulfillment of the Requirements for the Degree of Doctor of Philosophy December 2007 The thesis of Pratik Mankidy was reviewed and approved* by the following: Henry C. Foley Professor of Chemical Engineering Thesis Advisor Chair of Committee Carlo G. Pantano Distinguished Professor of Materials Science and Engineering Janna K. Maranas Associate Professor of Chemical Engineering Andrew L. Zydney Walter L. Robb Chair Professor of Chemical Engineering Head of the Department of Chemical Engineering *Signatures are on file in the Graduate School iii ABSTRACT Polymer nanofibers are 1D nanostructures that are gathering significant interest because of their potential applications in a wide variety of fields such as biomedicine, separation, electronics and sensor materials. They are also fascinating structures because in some cases they posses unique properties arising from the preferential arrangement of the polymer chains parallel to the fibers axes. Challenges that synthesis techniques for polymer nanofibers face are scalability and control during fabrication. An alternate to current common approaches such as electrospinning and templated-synthesis of polymer nanofibers, is template-less synthesis of polymer nanofibers during polymerization. This approach offers the advantage of bottom-up fabrication and the potential for large scale synthesis. Herein results from an investigation using this approach for poly (ethyl 2- cyanoacrylate) [PECA] nanofiber formation are reported. The template-less growth of PECA nanofibers is first demonstrated using the initiators present in human fingerprint residue via vapor phase polymerization of the monomer under conditions of high humidity. -
Technical Data Sheet Permatex® Plastic & Rubber Cyanoacrylate
Unit 3 Shipton Way Technical Data Sheet Express Business Park Permatex® Plastic & Rubber Northampton Road Rushden, NN10 6GL Cyanoacrylate Adhesive. Tel: 0870 458 9686 PRODUCT DESCRIPTION PROPERTIES OF UNCURED MATERIAL Permatex Plastic & Rubber Cyanoacrylate Adhesive is a Typical Value low viscosity Ethyl Cyanoacrylate adhesive. Permatex Chemical Type Ethyl Plastic & Rubber Cyanoacrylate Adhesive is formulated for Appearance Clear high strength, high speed bonding of plastics and rubbers. Specific Gravity 1.06 Viscosity cPs¹ PRODUCT BENEFITS - range 17-22 • Fast cure speed - typical value 20 • Bonds most plastic and rubbers Tensile Strength², typical (N/mm²) 20 • Can be post applied to pre assembled parts Fixture Time (seconds) 2-20 Full Cure (hours) 24 DIRECTIONS FOR USE Flash point (ºC) >85 1. Both surfaces must be smooth, clean, dry and free of Shelf Life @ 5 ºC (months) 12 oil, grease, etc. Max Gap Fill (mm) 0.10 2. USE EXTREME CARE WHEN OPENING. Hold bottle Operating Temperature Range (ºC) -50 to +80 upright, pointing away from face. Remove nozzle. 3. Apply adhesive to one surface, about one drop per ¹ISO 3104/3105 square inch. Spread evenly. ²ISO 6922 4. Immediately place the second surface in contact with the first surface and press together. TYPICAL CURING PERFORMANCE 5. Keep light pressure on surfaces for 15 seconds or until Substrate Cure time, seconds. bond sets. DO NOT REPOSITION THE PARTS. Steel/Steel <20 6. Allow to completely harden, for best results, overnight. ABS/ABS <10 NOTE: Not suitable for untreated polyethylene or Rubber/Rubber <5 polypropylene products. Cure speed vs. substrate FOR CLEANUP The cure speed of cyanoacrylates vary according to the 1. -
PERMABOND® 260 Cyanoacrylate Ref
PERMABOND ® 260 Cyanoacrylate Ref. #: 041509PB260 FEATURES & BENEFITS TYPICAL APPLICATION ¨ Instant Setting Rubber bonding ¨ Improved Gap Filling Bonding of passivated metals ¨ Faster Strength Development ¨ Improved Bonding to Difficult Surfaces ¨ High Shear Strength ¨ Easy to Apply ¨ One Part System GENERAL DESCRIPTION PERMABOND 260 is a low viscosity cyanoacrylate ideal fro wicking type application. PERMABOND 260 provides faster set times and improved gapfilling capability compared to conventional cyanoacrylates. The adhesive bonds to a wide range of substrates including metals, ceramics, plastics and elastomers. It is excellent for bonding difficulttobond plastics such as polyacetals. PHYSICAL PROPERTIES OF THE UNCURED ADHESIVE Chemical Type Ethyl Color Colorless Viscosity, cP @ 25°C 2 Specific Gravity 1.05 Flash point, °C (°F) 83 (181) Shelf Life stored at 2°C – 7°C (35°F – 45°F), months 12 Maximum gap fill; in (mm) .002 (0.05) NonWarranty: The information given and the recommendations made herein are based on our research and are believed to be accurate but no guarantee of their accuracy is made. In every case we urge and recommend that purchasers before using any product in fullscale production make their own tests to determine to their own satisfaction whether the product is of acceptable quality and is suitable for their particular purpose under their own operating conditions. THE PRODUCTS DISCLOSED HEREIN ARE SOLD WITHOUT ANY WARRANTY AS TO MERCHANTABILITY OR FITNESS FOR A PARTICULAR PURPOSE OR ANY OTHER WARRANTY, EXPRESS OR IMPLIED. No representative of ours has any authority to waive or change the foregoing provisions but, subject to such provisions, our engineers are available to assist purchasers in adapting our products to their needs and to the circumstances prevailing in their business. -
Ergo.® Instant Adhesives Fast-Bonding All-Rounders Fast, Secure, Universal
ergo.® instant adhesives Fast-bonding all-rounders Fast, secure, universal Joining what belongs together, and essentially doing it independently of the substrate material: ergo.® instance adhesives achieve excellent bonding results in practically every industry, as well as for repairs and maintenance. They are even used on difficult-to-bond materials, forming high-strength bonds that are resistant to aging. ergo.® instant adhesives ensure an effortless bonding Instructions for using performance on metals, plastics, elastomers, wood, ergo.® instant adhesives plaster, stone, ceramics and many other substrates. These solvent-free, extremely fast-curing one- Cleaning – For optimum bond strength, bonded surfaces component products can be used in a wide range must be free of oil, grease and other contami- of applications, even under difficult conditions. nants. We recommend ergo.® 9195 Cleaner to prepare plastics and ergo.® 9190 Cleaner to The former instant adhesives – which were first prepare metals. developed in the 1950s – cannot be compared – Where feasible, prepare surfaces by with the products made today. These have been mechanical abrasion (sanding, grinding, systematically improved and designed to meet sandblasting, etc.). – Clean prior to mechanical treatment and new requirements. after again. In short, ergo.® fast-curing adhesives are impact- – With elastomers, freshly cut surfaces must be bonded. Remove any plasticizers or traces resistant, flexible, temperature resistant, unaffected of talc. by variations in temperature or moisture, depending Dispensing on your requirements. – Apply the adhesive to one side of the substrate (drops or continuous bead). – This can be done by applying the product Advantages directly from the original packaging or using dosage dispensers, such as dispensing tips + one-component, easy to use or dosing systems. -
Nomination Background: Ethyl Cyanoacrylate (CASRN: 7085-85-0)
i' ETHYL CYANOACRYLATE CAS Number: 7085-85-0 NTP Nomination History and Review NCI summary of·oata for Chemical Selection Ethyl cyanoacrylate 7085-85-0 NTP NOMINATION HISTORY AND REVIEW A. Nomination History 1. Source: National Cancer Institute 2. Reco~endation: -Carcinogenicity (Inhalation) -Neurotoxicity -Reproductive and developmental effects 3. Rationale/Remarks: -Widespread use as a consumer instant adhesive -Lack of toxicity data -Potential biological activity 4. Priority: High 5. Date of Nomination: 5/91 B. Chemical Evaluation Committee Review 1. Date of Review: 2. Recommendations: 3. Priority: 4. NTP Chemical Selection Principles: 5. Rationale/Remarks: c. Board of Scientific Counselors Review 1. Date of Review: 2. Recommendations: 3. Priority: 4. Rationale/Remarks: D. Executive Committee Review 1. Date of Review: 2. Decision: . \ ,. 7085-85-0 Ethyl cyanoacrylate SUMMARY OF DATA FOR CHEMICAL SELECTION CHEMICAL IDENTIFICATION CAS Registry Number: 7085-85-0 Chern. Abstr. Name: 2-Cyano-2-propenoic acid, ethyl ester Synonyms & Trade Names: 910EM; ACE-EE; ACE-E SO; acrylic acid, 2-cyano-, ethyl ester; adhesive 502; Aron Alpha D; Black Max; CA 3; CA 3 (adhesive); CA 8-3A; CN 2; CN 4; Cemedine 3000RP; Cemedine 3000RP Type-II; Cemedine 3000RS; Cemedine 3000RS Type-11; Cyanobond W 100; Cyanobond W 300; Cyanolite 20 1; Cyan on 5MSP; DA 737S; ethyl Q-cyanoacrylate; ethyl 2-cyanoacrylate; Krazy Glue; N 135; Permabond 105; Permabond 200; Permabond 268; Pro Grip 4000; PTR-E 3; PTR-E 40; Super 3-1000; Superbonder 420; Super Glue; TK. 200; TK 201 Structure. Molecular Formula and Molecular Weight Mol. wt.: 125.13 Chemical and Physical Properties [From Coover eta/. -
Determination of the Kinetics of Curing of Cyanoacrylate-Based Adhesives with Fourier Transform Infrared Spectroscopy
CPGAN #001 Kinetics of Curing of Adhesives ©Cambridge Polymer Group, Inc.(2004). All rights reserved. Determination of the Kinetics of Curing of Cyanoacrylate-based Adhesives with Fourier Transform Infrared Spectroscopy Background Cyanoacrylate-based adhesives are low-viscosity, rapid curing adhesives that are commonly used for quick fix applications. They cure within a few minutes, and provide a brittle, non-space filling bond between two subtrates. The adhesives rely on moisture to initiate the curing reaction. Chemistry Cyanoacrylate cements contain a monomer group possessing an unsaturated carbon-carbon bond. The monomer is stabilized with a weak acid to prevent curing in the container. To initiate the reaction, the acid stabilizer must be neutralized with a weak base. Airborne or surface adsorbed water is usually sufficient to neutralize the weak base, although an alkaline surface will also suffice. The amino acid content in skin, in addition to the water content, initiates the polymerization reaction very well. Once the stabilizer is neutralized by the water, the monomer polymerizes via an anionic reaction. Only a small amount of water is necessary to catalyze the initiation reaction. As the monomer polymerizes, the carbon-carbon double bond is consumed, as shown in Figure 1. Figure 1: Initiation and propagation reactions for cyanoacrylate-based adhesives when exposed to a weak base. Reaction Kinetics In order to monitor the polymerization kinetics of cyanoacrylate adhesives, we often employ Fourier Transform Infrared Spectroscopy (FTIR). FTIR is used to identify and quantify chemical groups, such as C-H bonds or C=C bonds, which absorb infrared light at specific wavelengths. By identifying a specific chemical group that is consumed in a chemical reaction, FTIR can be used to monitor the kinetics and extent of reaction.