Coco Peat Filter and Reuse Production, Kushtia, Bangladesh
Total Page:16
File Type:pdf, Size:1020Kb
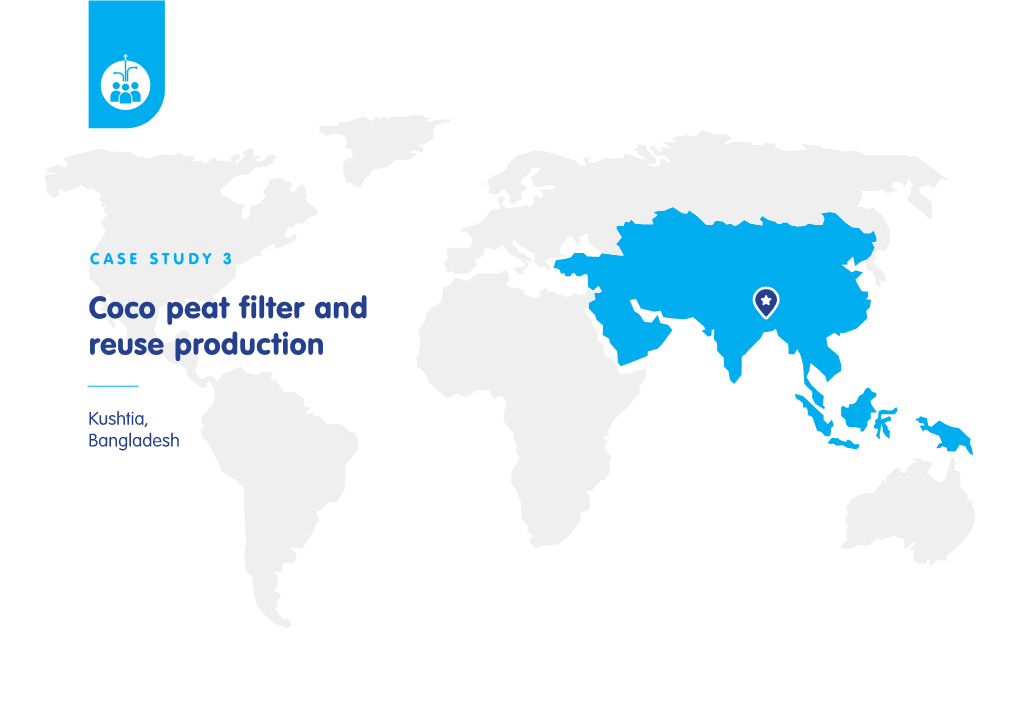
Load more
Recommended publications
-
Chapter-Vi : Socio-Economic Profile of the Study Area
Chapter-vi : Socio-economic Profile of the Study Area 189---198 Physical feature and socio-historical background Demography Literacy Administrative Unit Transport Communications Socio-economic Profile ofthe Study Area 189 For a proper understanding of the problem, it is essential to briefly refer to an ecological profile of Kushtia district as the values and characteristics of the masses very much depend upon, and are influenced by geographical, economic, social and political background of the area. Physical feature and socio-historical background Kushtia is not an ancient township but one of the eighteen oldest districts in independent Bangladesh. There is no much evidence to know the ancient history of Kushtia. The only tool to be informed about the district what was portrayed through description by different persons based on different regimes in the region governed. Hamilton's Gazetteer has mentioned of Kushtia town and of the fact that the local people called the town Kushtay (Kushte). In Tolemy's map, several little islands have been portrayed under the Ganges basin. These islands are considered as ancient Kushtia. 1 The district was under Natore Zemindar in 1725. Then it was under Rajshahi civil administration of Kanadarnagar Pargana. 2 Later East India Company transferred Kushtia under Jessore district in 1776. It was brought under Pabna district in 1828. Then Mahkuma Administration was established under Kushtia in 1861 and then brought under Nadia district.3 During the British rule, railway connection with Kolkata, capital of British India, established in 1860, made the town an alluring location for mills and factories, including the Jagneshwar Engineering Works (1896), Renwick and Company ( 1904 ), and the Mohini Mills (1919). -
Health Status and Modeling of Rural Aged Population of Kushtia District in Bangladesh
Journal of Neuroscience and Behavioural Health, Vol. 2(1) pp. 001-006, March 2010 Available online http://www.academicjournals.org/jnbh © 2010 Academic Journals Full Length Research Paper Health status and modeling of rural aged population of Kushtia District in Bangladesh Rafiqul Islam*, Mosharaf Hossain and Moshiur Rahman Department of Population Science and HRD, University of Rajshahi, Rajshahi-6205, Bangladesh. Accepted October 29, 2009 Aged population is an emerging issue in Bangladesh. It is a frightening problem of rural area in Bangladesh as well as a national problem. It has many socio-economic effects on national development. So, the aim of this study is to identify the determinants of health status of aged population in Kumarkhali Thana of Kushtia District in Bangladesh. Furthermore, an effort has been made here to fit mathematical model for aged population due to ages. For this, a total number of 250 rural aged populations have been interviewed through a structured questionnaire by purposive sampling technique. In this study, logistic regression model and polynomial model are applied. In logistic analysis, it is indicated that the respondent’s sex, type of family, occupation of the family head and suffering any diseases have significant effects for taking treatment on aged population. It is seen that age associated with aged population follow third degree polynomial model explaining more than 99% coefficient of determination. Key words: Aged population, socio-economic variables, logistic regression analysis, polynomial model, Bangladesh. INTRODUCTION Aged population is defined as the group of population aging is expected to accelerate in the coming decades, who belong to the age group of 60 years and more (BAG, mainly because the large cohorts born in 1950s and 2003). -
127 Branches
মেটলাইফ পলললির প্রিপ্রিয়াি ও অꇍযাꇍয মপমেন্ট বযা廬ক এপ্রিয়ার িকল শাখায় ꇍগদে প্রদান কমর তাৎক্ষপ্রিকভাদব বমু ে লনন ররপ্রভপ্রꇍউ স্ট্যাম্প ও সীলসহ রিটলাইদের প্ররপ্রসট এই িলু বধা পাওয়ার জনয গ্রাহকমক মকান অলিলরক্ত লফ অথবা স্ট্যাম্প চাজ জ প্রদান করমি হমব না Sl. No. Division District Name of Branches Address of Branch 1 Barisal Barisal Barishal Branch Fakir Complex 112 Birshrashtra Captain Mohiuddin Jahangir Sarak 2 Barisal Bhola Bhola Branch Nabaroon Center(1st Floor), Sadar Road, Bhola 3 Chittagong Chittagong Agrabad Branch 69, Agrabad C/ A, Chittagong 4 Chittagong Chittagong Anderkilla Branch 184, J.M Sen Avenue Anderkilla 5 Chittagong Chittagong Bahadderhat Branch Mamtaz Tower 4540, Bahadderhat 6 Chittagong Chittagong Bank Asia Bhaban Branch 39 Agrabad C/A Manoda Mansion (2nd Floor), Holding No.319, Ward No.3, College 7 Chittagong Comilla Barura Branch Road, Barura Bazar, Upazilla: Barura, District: Comilla. 8 Chittagong Chittagong Bhatiary Branch Bhatiary, Shitakunda 9 Chittagong Brahmanbaria Brahmanbaria Branch "Muktijoddha Complex Bhaban" 1061, Sadar Hospital Road 10 Chittagong Chittagong C.D.A. Avenue Branch 665 CDA Avenue, East Nasirabad 1676/G/1 River City Market (1st Floor), Shah Amant Bridge 11 Chittagong Chaktai Chaktai Branch connecting road 12 Chittagong Chandpur Chandpur Branch Appollo Pal Bazar Shopping, Mizanur Rahman Road 13 Chittagong Lakshmipur Chandragonj Branch 39 Sharif Plaza, Maddho Bazar, Chandragonj, Lakshimpur 14 Chittagong Noakhali Chatkhil Branch Holding No. 3147 Khilpara Road Chatkhil Bazar Chatkhil 15 Chittagong Comilla Comilla Branch Chowdhury Plaza 2, House- 465/401, Race Course 16 Chittagong Comilla Companigonj Branch Hazi Shamsul Hoque Market, Companygonj, Muradnagar J.N. -
Division Zila Upazila Name of Upazila/Thana 10 10 04 10 04
Geo Code list (upto upazila) of Bangladesh As On March, 2013 Division Zila Upazila Name of Upazila/Thana 10 BARISAL DIVISION 10 04 BARGUNA 10 04 09 AMTALI 10 04 19 BAMNA 10 04 28 BARGUNA SADAR 10 04 47 BETAGI 10 04 85 PATHARGHATA 10 04 92 TALTALI 10 06 BARISAL 10 06 02 AGAILJHARA 10 06 03 BABUGANJ 10 06 07 BAKERGANJ 10 06 10 BANARI PARA 10 06 32 GAURNADI 10 06 36 HIZLA 10 06 51 BARISAL SADAR (KOTWALI) 10 06 62 MHENDIGANJ 10 06 69 MULADI 10 06 94 WAZIRPUR 10 09 BHOLA 10 09 18 BHOLA SADAR 10 09 21 BURHANUDDIN 10 09 25 CHAR FASSON 10 09 29 DAULAT KHAN 10 09 54 LALMOHAN 10 09 65 MANPURA 10 09 91 TAZUMUDDIN 10 42 JHALOKATI 10 42 40 JHALOKATI SADAR 10 42 43 KANTHALIA 10 42 73 NALCHITY 10 42 84 RAJAPUR 10 78 PATUAKHALI 10 78 38 BAUPHAL 10 78 52 DASHMINA 10 78 55 DUMKI 10 78 57 GALACHIPA 10 78 66 KALAPARA 10 78 76 MIRZAGANJ 10 78 95 PATUAKHALI SADAR 10 78 97 RANGABALI Geo Code list (upto upazila) of Bangladesh As On March, 2013 Division Zila Upazila Name of Upazila/Thana 10 79 PIROJPUR 10 79 14 BHANDARIA 10 79 47 KAWKHALI 10 79 58 MATHBARIA 10 79 76 NAZIRPUR 10 79 80 PIROJPUR SADAR 10 79 87 NESARABAD (SWARUPKATI) 10 79 90 ZIANAGAR 20 CHITTAGONG DIVISION 20 03 BANDARBAN 20 03 04 ALIKADAM 20 03 14 BANDARBAN SADAR 20 03 51 LAMA 20 03 73 NAIKHONGCHHARI 20 03 89 ROWANGCHHARI 20 03 91 RUMA 20 03 95 THANCHI 20 12 BRAHMANBARIA 20 12 02 AKHAURA 20 12 04 BANCHHARAMPUR 20 12 07 BIJOYNAGAR 20 12 13 BRAHMANBARIA SADAR 20 12 33 ASHUGANJ 20 12 63 KASBA 20 12 85 NABINAGAR 20 12 90 NASIRNAGAR 20 12 94 SARAIL 20 13 CHANDPUR 20 13 22 CHANDPUR SADAR 20 13 45 FARIDGANJ -
Enhancing Quality Seed Supply Project (EQSSP)
Enhancing Quality Seed Supply Project (EQSSP) (Under Seed Wing, Ministry of Agriculture (MOA), Financed by IDB) Project Management Unit BADC, Shech Bhaban, 5th Floor, 22, Manik Mia Avenue, Sher-e-Bangla Nagar, Dhaka - 1207 Seed Dealer Status Report Search Criteria : District : Kushtia ; Registration No. Organization Name Organization Address Phone No Email Upazila District License Issue License Renewal Date Active/ Date Not Renewal From To 228 M/S. Gaji Seed House Kotpara, Kushtia 01720517073 Kushtia Sadar Kushtia 01/01/1998 01/07/2016 30/06/2022 Active 353 M/S. Krishi Kullen Seed Shamspur, Khoksa, Kushtia 01711311213 Khoksa Kushtia Not Renewal 421 M/S. Polash Beej Vander Khoksa Bazar, Kushtia 01716500740 Khoksa Kushtia 27/12/1998 01/07/2016 30/06/2022 Active 423 M/S. Beej Biponi Komarkhali Bazar, Kushtia 01917506601 Kumarkhali Kushtia 27/12/1998 01/07/2016 30/06/2022 Active 447 M/S. Polli Beej Vander Ar C Ar C Road kot Stason, 01708642299 Kushtia Sadar Kushtia 04/01/2000 01/07/2016 30/06/2022 Active Kushtia 795 M/S. Adorso Beej Vander Komarkhali Bazar, Kushtia 01729508371 Kumarkhali Kushtia 25/04/2004 01/07/2016 30/06/2022 Active 1305 M/S. Sheikh Traders Bittipara Bazar, Sadar, 01711572976 Kushtia Sadar Kushtia Not Renewal Kushtia 1308 M/S. Kushtia Seed Store Klajmor Kotpara, Sadar, 01711120922 Kushtia Sadar Kushtia 15/01/2006 01/07/2016 30/06/2022 Active Kushtia 1311 M/S. Frijue Mahabub Kamal Shamspur, Khoksa, Kushtia 01712257997 Khoksa Kushtia 15/01/2006 01/07/2016 30/06/2022 Active 1312 M/S Krishi Kallyan Seed Shomspur Bazar, Khoksha, Khoksa Kushtia 15/01/2006 01/07/2016 30/06/2022 Active Kushtia 1314 M/S. -
Municipal Waste Management of Kushtia Municipality: Challenges and Opportunities
Municipal Waste Management of Kushtia Municipality: Challenges and Opportunities Md. Abdul Kader1*, Sneha Paul2, Md. Sainur Rahman3, Md. Amanullah Parvez4 and Ranver Ahmed5 1Student, Department of Urban and Regional Planning, Chittagong University of Engineering and Technology, Email: [email protected] 2Student, Department of Urban and Regional Planning, Khulna University of Engineering and Technology, Email: [email protected] 3Student, Department of Urban and Regional Planning, Chittagong University of Engineering and Technology, Email: [email protected] 4Student, Department of Urban and Regional Planning, Chittagong University of Engineering and Technology, Email: [email protected] 5Town Planner, Kushtia Municipality, Kushtia. Email: [email protected] *Corresponding author ABSTRACT Municipal waste management is amongst of those most crucial issues of the world. Nowadays different international organizations i.e. WHO, ISWA etc. are working on introducing waste management system to ensure a better living atmosphere. The waste management system of Bangladesh is not up to the level. Recently, few municipalities have developed their municipal waste management system and Kushtia Municipality is one of them. The municipality owns composting plant where they compost municipal waste and sell into market as organic fertilizers. Though it is a revolutionary work and lot of opportunities are available in comparison with the current scenario of other municipalities in Bangladesh, there are some challenges faced by Kushtia municipal authority. This study aims also to identify the existing weakness and threats on the basis of SWOT analysis. And recommendations based on analysis of the existing scenario will go a long way to solve the problems faced by the authority. More importantly, to satisfy the increasing demand, a new landfill site and two transfer station are proposed. -
Btbrinjal Is Under ‘Life Support’
BTBRINJAL IS UNDER ‘LIFE SUPPORT’: EXPERIENCES OF FARMERS IN SECOND ROUND FIELD CULTIVATION CONTENTS Introduction ..................................................................................................................................................... 2 Background Information ................................................................................................................................. 2 Findings of the Second Round Field Cultivation ............................................................................................. 4 A. Sapling distribution of Btbrinjals in Field Cultivation ........................................................................... 4 B. Supervision by DAE and BARI ................................................................................................................ 6 C. Fertilizer use exceeds recommendation guide ........................................................................................ 7 D. Pesticide Use in Btbrinjal ........................................................................................................................ 7 E. Banned insecticide used: .......................................................................................................................... 8 Production Performance of Btbrinjal .............................................................................................................. 9 Marketing of Btbrinjal .................................................................................................................................... -
Marketing of Goat at Different Age and Weight by Different Categories of Farmers in Selected Areas of Bangladesh
Marketing of goat at different age and weight by different categories of farmers in selected areas of Bangladesh MA Khatun, MR Alam1, MR Amin* and MSI Khan Department of Animal Science, Bangladesh Agricultural University, Mymensingh 2202, Bangladesh 1School of Sustainable Agriculture, University of Malaysia, Sabah, Malaysia Abstract The factors influencing marketing of goats at different age and weight by different categories of farmers were investigated. The data were collected from village market (Hat) in selected places of Sirajgonj, Rajshahi, Kushtia, Mymensingh and Tangail districts. Goat owners belonged to one of the 4 categories of farmers at the Hat were interviewed through pre-tested questionnaire and the weight, body size and age of goats were determined. Landless and marginal farmers sold 58.81% of their goats at 6 months, 42.94% of small farmers at 10.5 months and 50% of medium farmers at 15.5 months of age. The average market weight and age of goats belonged to above categories of farmers were 8.39, 12.89, 17.10 and 17.20 kg and 6, 10.5, 15.5 and more than 18 months of age, respectively. The potential market weight of goats was found 17.10 kg at the age of 15.5 months. About 84% of farmers of all categories sold their goats for cash income, 15% for rearing problems and only 1% for disease prevalence. Key words: Goats, market, age, weight and farmers category Bangladesh Animal Husbandry Association. All rights reserved. Bang. J. Anim. Sci. 2012. 41 (1): 55-59 Introduction products. Subsistence level of goat farming is a combination of scavenging, free grazing in the Goats are reared in small holding system as a fallow land and depending on availability tree popular ruminant species for household income leaves and crop by-products are offered as due to its higher market value for meat. -
Global Map Around Northeast India and North Bangladesh (GLIDE: Global Unique Disaster Identifier)
GLIDE Number: ST-2010-000074-IND Global Map around northeast India and north Bangladesh (GLIDE: Global Unique Disaster Identifier) NALBARI DARJILING JALPAIGURI SHEOHAR SITAMARHI KOKRAJHAR KOKRAJHAR Legend DARRANG BONGAIGAON MADHUBANI KOCHBIHAR KOCHBIHAR BARPETA KOCHBIHAR Boundary SUPAUL KISHANGANJ KOCHBIHAR KOCHBIHAR BIHAR DHUBURI MARIGAON ARARIA PANCHAGARH KOCHBIHAR International MUZAFFARPUR DARBHANGA KAMRUP N " GOALPARA 0 ' 0 THAKURGAON NILPHAMARI LALMONIRHAT DHUBURI Primary/1st Order ° ASSAM 6 2 WEST DINAJPUR KOCHBIHAR CHHAPRA RIBOHI SAMASTIPUR SAHARSA MADHEPURA PURNIA KURIGRAM DHUBURI EAST GARO HILLS Transportation VAISHALI WEST GARO HILLS DINAJPUR Primary Route RANGPUR WEST GARO HILLS PATNA PATNA BEGUSARAI KHAGARIA KATIHAR WEST KHASI HILLS Secondary Route WEST GARO HILLS EAST KHASI HILLS DAKSHIN DINAJPUR Railroad BHAGALPUR SOUTH GARO HILLS JAINTIA HILLS NALANDA MUNGER DAKSHIN DINAJPUR LAKHISARAI MALDAH GAIBANDHA N SHEIKHPURA SAHIBGANJ SHERPUR Drainage " GODDA JOYPURHAT 0 ' JAMUI BANKA 0 GAYA NAWADA JAMUI ° MUNGER 5 LAKHISARAI River 2 SAHIBGANJ MALDAH JAMALPUR SUNAMGANJ SYLHET NAWADA BANKA GODDA NAOGAON BOGRA NETRAKONA Inland Water GAYA JAMUI NAWABGANJ MYMENSINGH PAKUR RAJSHAHI MAULBIBAZAR KODARMA SIRAJGANJ Land Use KISHORGANJ DUMKA NATORE TANGAIL HABIGANJ GIRIDIH DEVGHAR Forest NORTH TRIPURA NADIA N CHATRA " MURSHIDABAD PABNA GAZIPUR Mixture 0 ' 0 ° JAMTARA NARSINGDI BRAHMANBARIA 4 2 HAZARIBAG BIRBHUM Grassland/shrub DHANBAD KUSHTIA MANIKGANJ WEST TRIPURA DHALAI MEHERPUR RAJBARI DHAKA NARAYANGANJ Agricultural area BOKARO CHUADANGA -
4Th Convocation-2018 (Date: Jan 07, 2018) Islamic
4TH CONVOCATION-2018 (DATE: JAN 07, 2018) List of Registered Graduates Page 1 of 42 ISLAMIC UNIVERSITY, KUSHTIA-7003 Dept. of Public Administration Sl Session Name Present Address Degree(s) Cell_num 1 (1995-1996) MD. SHAIDUL ISLAM VILL.-MIRPUR, POST-HARINARAYANPUR , Hons 01731299082 UPAZILA-KUMARKHALI ,DIST.-KUSHTIA 2 (1995-1996)(1998-1999) Md.Sha Alam H s s Road.Jhenaidah Hons Masters 01713334949 3 (1995-1996)(1998-1999) MST. TAHAMINA C/O - Md. Liakat Ali, House - 76, Kabi Sukanta Hons Masters 01913291639 TAMANNA Sarak (A), Adarshapara, Jhenidah-7300 4 (1995-1996)(1998-1999) Mst.shirin sultana Vill.Birampur ,P/s.Harinakundu Dist.Jhenaidah Hons Masters 01784483822 5 (1995-1996)(1998-1999) MD. SHARIFUL ISLAM HABIBPUR, SHAILKUPA, JHENAIDAH Hons Masters 01712642101 6 (1995-1996)(1998-1999) Golam Mohammad Vip tower,Kazirmor Ukil para, Naogaon Hons Masters 01733272799 7 (1995-1996)(1998-1999) Most.Shamsunnahar House no-222/3,Road no-2,North Hons Masters 01716179631 Shaymoli,Mohammadpur,Dhaka. 8 (1995-1996)(1998-1999) MD.ZILLUR RAHAMAN 26Abul mohammad lane, courtpara,Kushtia. Hons Masters 01716936184 9 (1995-1996)(1998-1999) Md. Belayet Hossain 222/3, Road-2, North Shymoli, West Agargaon, Hons Masters 01712752864 Dhaka 10 (1995-1996)(1998-1999) MD. FULSAR ALI VILL: TOIL KUPI, POST: NALDANGA RAJBATI, Hons Masters 01715689029 UPAZILA: KALIGANJ, DIST: JHENAIDAH 11 (1995-1996)(1998-1999) Md Raihan Islam Hamdah Powerhouse Para, Jhenaidah Hons Masters 01721667584 12 (1995-1996)(1998-1999) MD. ALAUDDIN DHORMOTALA, JESSORE Hons Masters 01712130609 13 (1995-1996)(1998-1999) KAJAL DATTA DD ped sher e bangla, agriculture university, Hons Masters 01716263570 Doeal Bhavan house #c2, Dhaka 14 (1995-1996)(1998-1999) MOHAMMAD AMINUR CHAINABARI,WEST BANIA KHAMAR, Hons Masters 01972601173 RAHMAN SONADANGA,KHULNA 15 (1995-1996)(1998-1999) Jasmine Nahar 446, Munshibari Sorak, Ibrahimpur, Kafrul, Hons Masters 01917269676 Mirpur-14, Dhaka-1206 Professor Dr. -
Kushtia District
GEO Code based Unique Water Point ID Kushtia District Department of Public Health Engineering (DPHE) June, 2018 How to Use This Booklet to Assign Water Point Identification Code: Assuming that a contractor or a driller is to install a Shallow Tube Well with No. 6 Pump in SULTANPUR village BEMARTA union of BAGERHAT SADAR uapzila in BAGERHAR district. This water point will be installed in year 2010 by a GOB-Unicef project. The site of installation is a bazaar. The steps to assign water point code (Figure 1) are as follows: Y Y Y Y R O O W W Z Z T T U U U V V V N N N Figure 1: Format of Geocode Based Water Point Identification Code Step 1: Write water point year of installation as the first 4 digits indicated by YYYY. For this example, it is 2010. Step 2: Select land use type (R) code from Table R (page no. 4). For this example, a bazaar for rural commercial purpose, so it is 4. Step 3: Select water point type of ownership (OO) from Table OO (page no. 4) . For this example, it is 05. Step 4: Select water point type (WW) code from Table WW (page no. 5). For this example, water point type is Shallow Tube Well with No. 6 Pump. Therefore its code is 01. Step 5: Assign district (ZZ), upazila (TT) and union (UUU) GEO Code for water point. The GEO codes are as follows: for BAGERGAT district, ZZ is 01; for BAGERHAR SADAR upazila, TT is 08; and for BEMARTA union, UUU is 151. -
Identification of Aquifer Properties in the Eastern Part of Kushtia District, Bangladesh
Journal of Geoscience and Environment Protection, 2020, 8, 222-237 https://www.scirp.org/journal/gep ISSN Online: 2327-4344 ISSN Print: 2327-4336 Identification of Aquifer Properties in the Eastern Part of Kushtia District, Bangladesh Md. Shahinuzzaman1*, M. Nozibul Haque1, Khan M. Nasir Uddin1, M. Alibuddin2 1Department of Electrical and Electronic Engineering, Islamic University, Kushtia, Bangladesh 2Department of Physics, Meherpur Paura Degree College, Meherpur, Bangladesh How to cite this paper: Shahinuzzaman, Abstract M., Haque, M. N., Uddin, K. M. N., & Alibuddin, M. (2020). Identification of The present study has been undertaken to depict spatial distribution of dif- Aquifer Properties in the Eastern Part of ferent aquifer parameters in the eastern part of Kushtia district through a de- Kushtia District, Bangladesh. Journal of tailed hydrogeological survey. For this investigation, 119 lithologs and 92 Geoscience and Environment Protection, 8, pumping test data have been used. These data have been processed, analyzed, 222-237. https://doi.org/10.4236/gep.2020.811015 interpreted and krigged for the spatial assessment of the aquifer properties viz. transmissivity, hydraulic conductivity, hydraulic diffusivity, specific yield, Received: October 4, 2020 radius of influence, and specific drawdown. It is seen from the investigation Accepted: November 24, 2020 that the transmissivity and hydraulic conductivity values obtained from the Published: November 27, 2020 2 2 pumping tests of the wells are varying from 1811 m /day to 2568 m /day and Copyright © 2020 by author(s) and 32.5 m/day and 61.5 m/day respectively, the hydraulic diffusivity being rang- Scientific Research Publishing Inc. ing from 181,143 m2/day to 256,788 m2/day.