Stellite Wear Solutions Components Alloy Characteristics
Total Page:16
File Type:pdf, Size:1020Kb
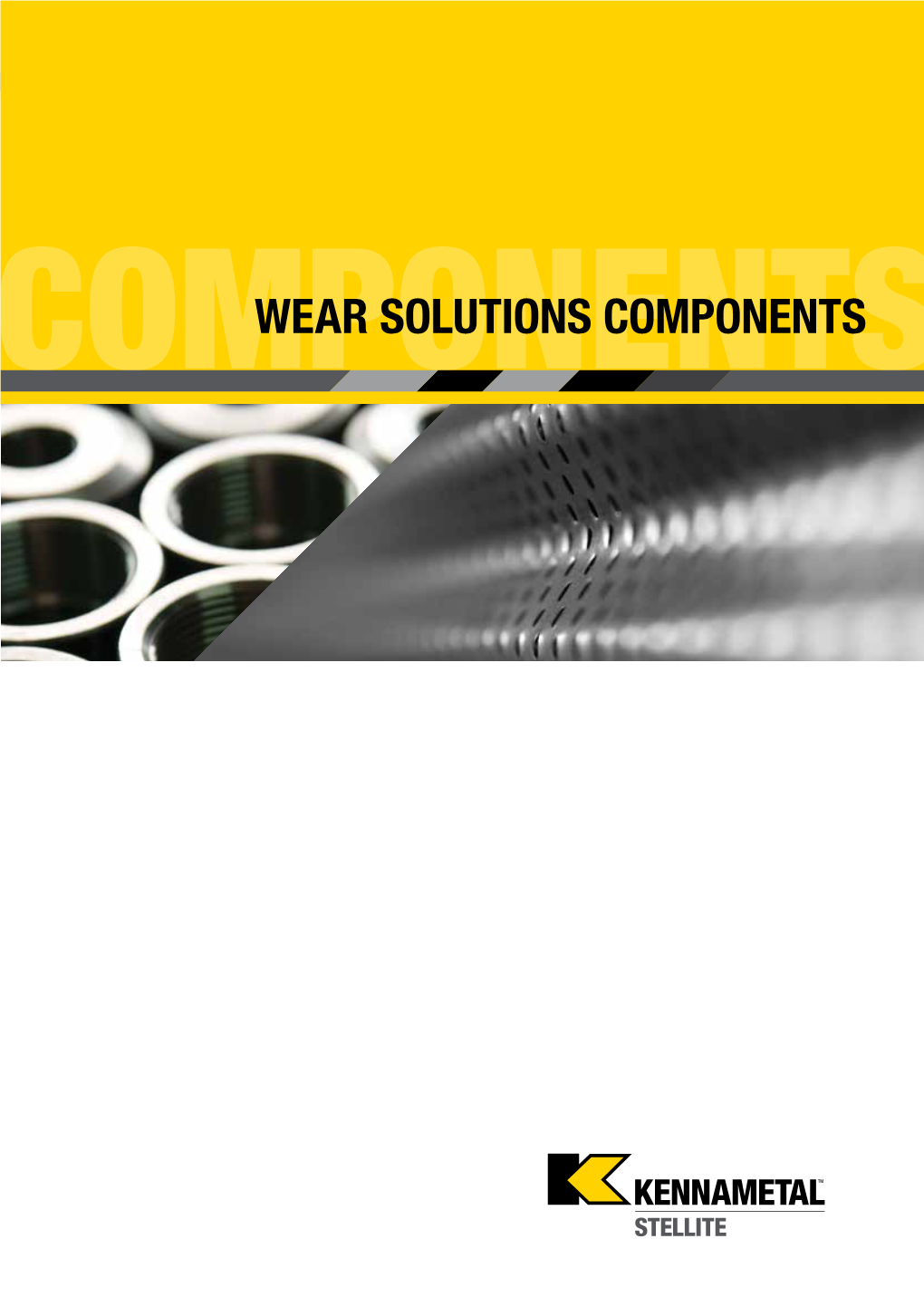
Load more
Recommended publications
-
Development of Sleeve Parts for Continuous Hot Zinc Plating Roll Applied to Wear-Resistant Alloy Cast Steel
Journal of the Korean Society of Manufacturing Technology Engineers 26:4 (2017) 357~364 https://doi.org/10.7735/ksmte.2017.26.4.357 J. Korean Soc. Manuf. Technol. Eng. ISSN 2508-5107(Online) / ISSN 2508-5093(Print) Development of Sleeve Parts for Continuous Hot Zinc Plating Roll Applied to Wear-Resistant Alloy Cast Steel Dong-Hwan Parka, Jin-Tae Hongb, Hyuk-Hong Kwonc* a Gyeongbuk Hybrid Technology Institute, 24-24, Goeyeon 1-gil, Yeongcheon, Gyeongbuk-do, 38899, Korea b Bugang Special Co., Ltd., 42, Bonchongongdan-gil, Yeongcheon, Gyeongbuk-do, 38899, Korea c Department of Computer Aided Mechanical Engineering, Daejin University, 1007, Hoguk-ro, Pocheon, Gyeonggi-do, 11159, Korea ARTICLE INFO ABSTRACT Article history: Metal casting is a process in which molten metal or liquid metal is poured into a Received 8 June 2017 mold made of sand, metal, or ceramic. The mold contains a cavity of the desired Revised 23 July 2017 shape to form geometrically complex parts. The casting process is used to create Accepted 2 August 2017 complex shapes that are difficult to make using conventional manufacturing practices. For the optimal casting process design of sleeve parts, various analyses Keywords: were performed in this study using commercial finite element analysis software. Metal casting The simulation was focused on the behaviors of molten metal during the mold Sleeve parts filling and solidification stages for the precision and sand casting products. This Stellite study developed high-life sleeve parts for the sink roll of continuous hot-dip Wear-resistant alloy galvanizing equipment by applying a wear-resistant alloy casting process. -
Corrosive Wear Behaviour of Various Stainless Steel Alloys and a Stellite 6 Weld Cladding
Corrosive wear behaviour of various stainless steel alloys and a Stellite 6 weld cladding F.Brownlie1*, T.Hodgkiess2, A.Pearson3, A.M.Galloway1 1Department of Mechanical & Aerospace Engineering, University of Strathclyde, Glasgow, UK. 2Porthan Ltd, Lochgilphead, UK. 3Weir Engineering Services, East Kilbride, UK Abstract This study has comprised an investigation the corrosive wear behaviour of UNS S31600, a low hardness (280Hv) UNS S42000, a high hardness (480Hv) UNS S42000 and a single layer Stellite 6 (UNS R30006) weld cladding on a low alloy carbon steel (UNS G43400). Erosion-corrosion testing was conducted using a submerged jet of 3.5% NaCl aqueous solution with spherical silica sand particles. The sand concentration was 2.4g/l, the velocity of the jet was 18m/s and the testing temperature range was 16°C-27°C. Both normal incidence (90°) and low angle (20°) tests were performed. Mass losses, wear scar depths and a volumetric analysis technique were used to assess the damage in the direct impinged zone (DIZ) and the outer area (OA) of the specimens. For all materials, it was found that mass loss was higher at 20° tests than that of 90°. However, when comparing wear scar depths the opposite trend was found. The results are discussed in terms of comparative material behaviour, the influence of material hardness and the corrosive wear mechanisms in different regions formed during slurry jet impingement. Keywords: Erosion-corrosion, impingement, volumetric analysis *Corresponding author: Frazer Brownlie ([email protected]). 1. INTRODUCTION Erosion-corrosion is an intricate material degradation process which involves mechanical wear, electrochemical processes and the combined effect of both, termed synergy. -
Mechanical Properties of the Stellite 6 Cobalt Alloy Implanted with Nitrogen Ions P
Vol. 132 (2017) ACTA PHYSICA POLONICA A No. 2 Proc. of the XI Int. Conf. — Ion Implantation and other Applications of Ions and Electrons, Kazimierz Dolny 2016 Mechanical Properties of the Stellite 6 Cobalt Alloy Implanted with Nitrogen Ions P. Budzyńskia;∗, M. Kamińskia, M. Wiertelb, K. Pyszniakb and A. Droździelb aFaculty of Mechanical Engineering, Lublin University of Technology, Nadbystrzycka 36, 20-618 Lublin, Poland bInstitute of Physics, M. Curie-Skłodowska University, pl. M. Curie-Skłodowskiej 1, 20-031 Lublin, Poland The effect of nitrogen ion implantation on Stellite 6 cobalt alloy was investigated. In this research, cobalt alloy was implanted with 65 keV nitrogen ions at the fluence of (1 ÷ 10) × 1016 N+/cm2. The distribution of implanted nitrogen ions and vacancies produced by them was calculated using the SRIM program. The surface morphology was examined and the elemental analysis was performed using scanning electron microscopy, energy dispersive X-ray spectroscopy and grazing incidence X-ray diffraction. The wear tests were conducted with the use of the pin-on-disc method. The results demonstrate that implantation with nitrogen ions significantly reduces the friction factor and wear. The friction coefficient of the implanted sample at the fluence of 1 × 1017 N+/cm2 increased to the values characteristic of an unimplanted sample after 5000 measurement cycles. The depth of the worn trace was about 2:0 µm. This implies that the thickness of the layer modified by the implantation process is ≈ 2:0 µm and exceeds the initial range of the implanted ions by an order of magnitude. This is referred to as a long-range implantation effect. -
1. Introduction a Non-Conventional Metal Alloys Processing in the Semi
Arch. Metall. Mater., Vol. 61 (2016), No 4, p. 1901–1908 DOI: 10.1515/amm-2016-0306 K.SołeK*,#, P. KaPranoS** RHEOLOGY OF STELLITETM 21 ALLOY IN SEMI-SOLID STATE The main objective of this study was to conduct an analysis of the rheological properties of StelliteTM 21 alloy in the semi-solid state, as the results could be used for identifying the appropriate temperature range for thixoforming of this alloy, and a secondary objective of the experimental work was the development of mathematical model of the alloy’s apparent viscosity. Such viscosity models are necessary for numerical simulations of the thixoforming processes. The StelliteTM 21 alloy exhibits high hardness and thus shaping in the semi-solid state is promising route of production of parts from this alloy. Within the confines of experimental work the measurement methods of the rheological properties at high temperatures was developed. They are based on the use of specially designed viscometer equipped with high temperature furnace. Keywords: thixoforming, rheological properties, viscosity, thixotropy, StelliteTM alloys 1. Introduction The basic difficulty within the confines of experimental work was the very high temperatures involved to obtain the A non-conventional metal alloys processing in the semi-solid state in StelliteTM 21 alloy. Such high melting semi-solid state, also known as thixoforming are hybrid points alloys require using of specialized equipment. The manufacturing methodologies based on modified methods second difficulty is necessity of maintenance of the constant normally used in forging or casting processes. Thixoforming shear rate over long time intervals in the case of analysis of processing is successfully used by a number of industries thixotropic properties. -
Wrought Products (Stellite™ Alloy 6B/6K)
WROUGHTWROUGHT WEAR-RESISTANT ALLOYS Wrought Wear-Resistant Alloys Plate, Sheet, and Bar Kennametal Stellite is a global provider of solutions for wear, heat, and corrosion problems, and is a world-class manufacturer of cobalt- and nickel-based materials and components. Industries Served Wrought Stellite™ 6B materials and components, and Stellite™ 6K knife and scraper components are found in many industries, including: • Aerospace • Oil & Gas • Power Generation • Food • Pulp & Paper • Glass • Other Processing Industries Wrought Wear-Resistant Alloys StelliteTM 6B and 6K StelliteTM 6B and 6K Stellite™ alloys are available in many different grades (chemical compositions) and several different processes or methods of manufacture. These different processes include casting, powder metal, hardfaced deposit, and wrought. For wrought grades Stellite™ 6B and Stellite™ 6K, the wrought or hot forging method of production leads to improvements of the resulting material in regards to: • Mechanical Properties • Toughness • Wear Resistance • Corrosion Resistance StelliteTM 6B StelliteTM 6K When it comes to tough, wear-resistant materials with Stellite™ 6K has similar properties to Stellite™ 6B, but is “guaranteed” mechanical properties, Stellite™ 6B is slightly harder and less ductile. Stellite™ 6K is excellent in a class by itself. Unlike many other materials that for cutting or scraping applications, such as knives or sacrifice toughness for wear resistance, Stellite™ 6B scraper blades. Stellite™ 6K is a custom-rolled material offers both. The key is the extensive hot working and can be produced to a gauge and sheet size uniquely processing of the material which transforms a brittle, suited to your application. wear-resistant ingot into tough, wear-resistant Stellite™ 6B. -
Corrosion Behaviour of High-Carbon High-Molybdenum Stellite Alloys in Amine Environment
Corrosion Behaviour of High-Carbon High-Molybdenum Stellite Alloys in Amine Environment by Kafeel Kamal A thesis submitted to the Faculty of Graduate and Postdoctoral Affairs in partial fulfillment of the requirements for the degree of Master of Applied Science in Materials Engineering Carleton University Ottawa, Ontario © 2018, Kafeel Kamal Abstract Stellite alloys are cobalt-based alloys which display exceptional mechanical properties, wear and corrosion resistance owing to its unique chemical compositions. Stellite 6 is the most popular Stellite alloy employed in various applications, one of which is the hardfacing of valve trim components within control valves in boiler feedwater treatment systems where hydrazine and/or amine derivatives are used. Erosion-corrosion caused failure of Stellite 6 hardfacing has been reported from industry in such applications. To find a better replacement of Stellite 6 for improved corrosion resistance in amine environment, 700 series Stellite alloys, including Stellite 706, Stellite 712 and Stellite 720, are proposed, which are high-carbon high-molybdenum Stellite alloys. The corrosion performance of these alloys in morpholine solution with pH 9.5, which simulates the corrosive environment of boiler feedwater service, is evaluated using a series of electrochemical tests such as electrochemical impedance spectroscopy (EIS), potentiodynamic polarization and potentiostatic polarization. Both regular polarization tests (potential up to 1.2 V) and failure polarization tests (potential up to 12 V) are conducted on the alloys. The former identifies general and localized corrosion behaviour, while the latter intends to fail the alloy surface to analyze their limitations. Two different surface conditions (intact and damaged) and two different temperature variables (25°C and 50°C) are also studied to simulate erosion-corrosion behaviour. -
Erosion Resistance of Tungsten-Carbide Coatings for Steel Pipes in Fluid Catalytic Cracking Units
Erosion Resistance of Tungsten-Carbide Coatings for Steel Pipes in Fluid Catalytic Cracking Units Group Members: Jennifer Hulfachor Davis Vannasing Advisor: Dr. Trevor Harding Sponsor: Chevron ETC – Richmond California Jessica Williams Maricela Johnson June 11th, 2019 1. Abstract 3 2. Introduction 4 2.1 Stakeholders 4 2.2 Broader Impacts 5 2.2.A - Benefits 5 2.2.B - Risks 5 2.2. C - Ethics 5 3. Background 6 3.1 Petroleum Processing 6 3.1.A - Chevron Corporation 6 3.1.B - Petroleum Properties 6 3.1.C - Fluid Catalytic Cracking (FCC) 7 3.1.D - Catalyst Characteristics 8 3.1.E - Erosion due to Flow of Catalyst 9 3.2 Evaluation of Erosion in FCC Units 9 3.2.A - Solid Particle Erosion 9 3.2.B - Factors Influencing Erosion 10 3.2.C - Erosion Control 10 3.3 Desirable Properties of Internal Erosion-Resistant Coatings 12 3.3.A - Hardness and Fracture Toughness 12 3.3.B - Adhesion 14 3.3.C - Ease of Application 14 3.4 Characteristics and Properties of Stellite 14 3.4.A - Coating Composition 14 3.4.B - Application Method 15 3.4.C - Adhesion to Carbon Steel Pipes and Intricate Parts 16 3.4.D - Erosion Resistance 16 3.5 Selection of Potential Alternative Coatings to Stellite 17 3.5.A - Conforma Clad 17 3.5.B - Hardide Coating 19 3.6 Problem statement 20 4. Experimental Procedure 21 4.1 Methodology for Project Designs 21 4.1.A – Design Criteria 21 4.1.B – Variables 21 4.1.C - Others 21 4.2 Methodology for Experiments and Testing 22 4.2.A – Inputs 22 4.2.B – Outputs 22 1 4.2.C – Experimentation 23 5. -
Electro-Spark Deposited Coatings for Replacement of Chrome Plating
AD AD-E403 050 Contractor Report ARAET-CR-05002 ELECTRO-SPARK DEPOSITED COATINGS FOR REPLACEMENT OF CHROME PLATING R. N. Johnson J. A. Bailey Pacific Northwest National Laboratory 902 Battelle Boulevard P.O. Box 999 Richland, WA 99352 Joseph A. Goetz Project Engineer ARDEC June 2005 ARMAMENT RESEARCH, DEVELOPMENT AND ENGINEERING CENTER Armaments Engineering & Technology Center Picatinny, New Jersey Approved for public release; distribution is unlimited. The views, opinions, and/or findings contained in this report are those of the author(s) and should not be construed as an official Department of the Army posi- tion, policy, or decision, unless so designated by other documentation. The citation in this report of the names of commercial firms or commercially available products or services does not constitute official endorsement by or approval of the U.S. Government. Destroy this report when no longer needed by any method that will prevent disclosure of its contents or reconstruction of the document. Do not return to the originator. REPORT DOCUMENTATION PAGE Form Approved OMB No. 0704-01-0188 The public reporting burden for this collection of information is estimated to average 1 hour per response, including the time for reviewing instructions, searching existing data sources, gathering and maintaining the data needed, and completing and reviewing the collection of information. Send comments regarding this burden estimate or any other aspect of this collection of information, including suggestions for reducing the burden to Department of Defense, Washington Headquarters Services Directorate for Information Operations and Reports (0704-0188), 1215 Jefferson Davis Highway, Suite 1204, Arlington, VA 22202-4302. -
Erosion Resistance of Stellite Alloys Under Solid-Particle Impact
Journal of Materials Science and Engineering B 3 (9) (2013) 555-566 D DAVID PUBLISHING Erosion Resistance of Stellite Alloys under Solid-Particle Impact Sydney Nsoesie 1, Rong Liu 1, Kuiying Chen 2 and Matthew Yao3 1. Department of Mechanical and Aerospace Engineering, Carleton University, 1125 Colonel By Drive, Ottawa, Ontario, K1S 5B6 Canada 2. Institute for Aerospace Research, National Research Council of Canada, 1200 Montreal Road, Ottawa, Ontario, K1A 0R6 Canada 3. Kennametal Stellite Inc., P.O. Box 5300, Belleville, Ontario, K8N 5C4 Canada Received: September 18, 2013 / Accepted: September 21, 2013 / Published: September 25, 2013 Abstract: Selected Stellite alloys, which are currently or potentially employed in an environment involving erosion, are studied under solid-particle erosion test. These alloys include high-carbon Co-Cr-W system and low-carbon Co-Cr-Mo system. Two particle impact velocities (84 m/s and 98 m/s) and two impingement angles (30° and 90°) are used in the test. It is shown that Stellite alloys are more resistant to erosion at 90° impingement angle than at 30° impingement angle and the weight losses of Stellite alloys increase with the particle impact velocity. The erosion resistance of Stellite alloys is controlled mainly by their carbon content, but tungsten and molybdenum contents also play an important role in the erosion resistance of these alloys, because these elements determine the volume fractions of carbides and intermetallic compounds in the alloys. The eroded surfaces are analyzed using SEM to further understand the erosion test results. Key words: Solid-particle erosion, Stellite alloy, hardness, particle impingement angle, particle impact velocity. -
Refinery & FCCU Applications
REFINERYREFINERY AND FCCU APPLICATIONS Refinery And FCCU Applications Kennametal Stellite is a global provider of solutions to wear, heat, and corrosion problems and is a world-class manufacturer of Cobalt and Nickel based materials and components. Kennametal Stellite offers proven heat, wear and corrosion solutions in solid cast or coated form to the refinery and FCCU market segments. Typical applications include: • Nozzles • Thermowells • Valve Trim & Bodies • Pump Components • Return Bends Refinery and FCCU Applications StelliteTM Solutions Kennametal Stellite Refinery and FCCU Applications Kennametal Stellite manufactures solutions that extend component life, reduce unplanned down time, and decrease maintenance expenditures. Typical applications in the refinery industry include nozzles, thermowells, valves, and pump components. To meet customer needs, Kennametal Stellite rapidly develops and supplies a finish machined component utilizing one, or more, of the following processes: • Investment Casting • Powder Metallurgy • Vacuum Casting • Wrought Material and Processing • Sand Casting • Coatings/Claddings • Centrifugal Casting • Finish Machining High-Temperature Erosion Resistance Stellite™ alloys are noted for their high-temperature erosion resistance in a multitude of industries. In petroleum refining, the reactor and regenerator sections of the FCCU’s pose severe erosion problems. During an accelerated wear test at regenerator temperatures (700ºC), using an FCCU catalyst as the erosive media, Cobalt-based alloys such as Tribaloy™ T-800™ and Molybdenum-containing alloy Stellite™ 720, showed a significant engineering advantage over 304, 410, and boron diffused 410. These Cobalt and Molybdenum alloys provide an exceptional blend of high-temperature sulfidation, oxidation, and erosion resistance. In even more demanding situations, alloy matrix composites such as Stellite™ TiC20 are candidate materials. -
Ultraflex Cladding Technology
SURFACEULTRAFLEX™ CLADDING ULTRAFLEX™ CLADDING Kennametal is a global provider of solutions for wear, heat, and corrosion problems, a world-class manufacturer of components, and a service provider to a wide range of industries. Kennametal is your trusted source for the most innovative solutions that deliver productivity, reliability, and extended service life in the most demanding environments. Drawing on expertise from Kennametal with tungsten carbide-based materials, and incorporating super alloy-based technologies from the Kennametal Stellite™ organization, UltraFlex™ provides an extensive portfolio of surface treatments for your application. Designed to accommodate even the most complex geometries, including non-line-of-sight surfaces, UltraFlex covers a variety of industries and applications, including: • Oil & Gas Drilling & Production • Chemical & Petrochemical Processing • Power Generation • General Conveyance • Mechanical Equipment Language Version_KMT_Ultraflex_Broc_EN UltraFlexUltraFlex™™ Cladding Cladding Solution Solution Surface Wear Applications & Benefits UltraFlex™ Cladding UltraFlex, a wear-resistant surface treatment from Kennametal, brings industry-leading performance to components with complex geometries for power generation, oil and gas, and many other industries. UltraFlex is a proven product for extending component life and increasing productivity. The Kennametal UltraFlex treatment is available in a broad array of materials, ensuring the optimum solution for your application’s wear environment. Surface Wear Applications Benefits • Abrasion • Increased component life • Erosion • Reduced downtime • Corrosion • Reduction in failures • Metal on metal wear • Reduced maintenance costs • Galling • Reliable performance between • Fretting scheduled maintenance • High-temperature environments • Consistent product quality • Maintain system efficiency The UltraFlex Process Using the Kennametal patented process, UltraFlex material is first applied in a slurry form to the substrate using proprietary flow-coating methods. -
Machinability of Stellite 6 Hardfacing
EPJ Web of Conferences 6,6 02001 (2010) DOI:10.1051/epjconf/20100602001 © Owned by the authors, published by EDP Sciences, 2010 Machinability of Stellite 6 hardfacing M. Benghersallah1, L. Boulanouar 1, G. Le Coz2, A. Devillez2, D. Dudzinski2 1Mechanical laboratory of Materials and Plant Maintenance (LR3MI), Mechanical Department of Engineering, University Badji Mokhtar BP12, Annaba 23000. E – mail: [email protected] 2 Laboratoire de Physique et Mécanique des Matériaux UMR CNRS 7554 ISCMP – Bâtiment C Ile du Saulcy57045 METZ Cedex 01 France Abstract. This paper reports some experimental findings concerning the machinability at high cutting speed of nickel-base weld-deposited hardfacings for the manufacture of hot tooling. The forging work involves extreme impacts, forces, stresses and temperatures. Thus, mould dies must be extremely resistant. The aim of the project is to create a rapid prototyping process answering to forging conditions integrating a Stellite 6 hardfacing deposed PTA process. This study talks about the dry machining of the hardfacing, using a two tips machining tool and a high speed milling machine equipped by a power consumption recorder Wattpilote. The aim is to show the machinability of the hardfacing, measuring the power and the tip wear by optical microscope and white light interferometer, using different strategies and cutting conditions. Key words: Weld hardfacing/ base-cobalt/ Machinability/ High speed milling/ Wattpilote 1. Introduction Prototyping is the realisation of models, before the industrial manufacturing start of a new mechanical part, to test different aspects and particularly it feasibility, it functionality and more generally, it design. In the context of the world competition, the necessity to develop a new product and to manufacture it in a minimum of time has driven firms to the expansion of rapid prototyping and rapid tooling concept [1, 2].