Design and Analysis of Micro-Channel Heat
Total Page:16
File Type:pdf, Size:1020Kb
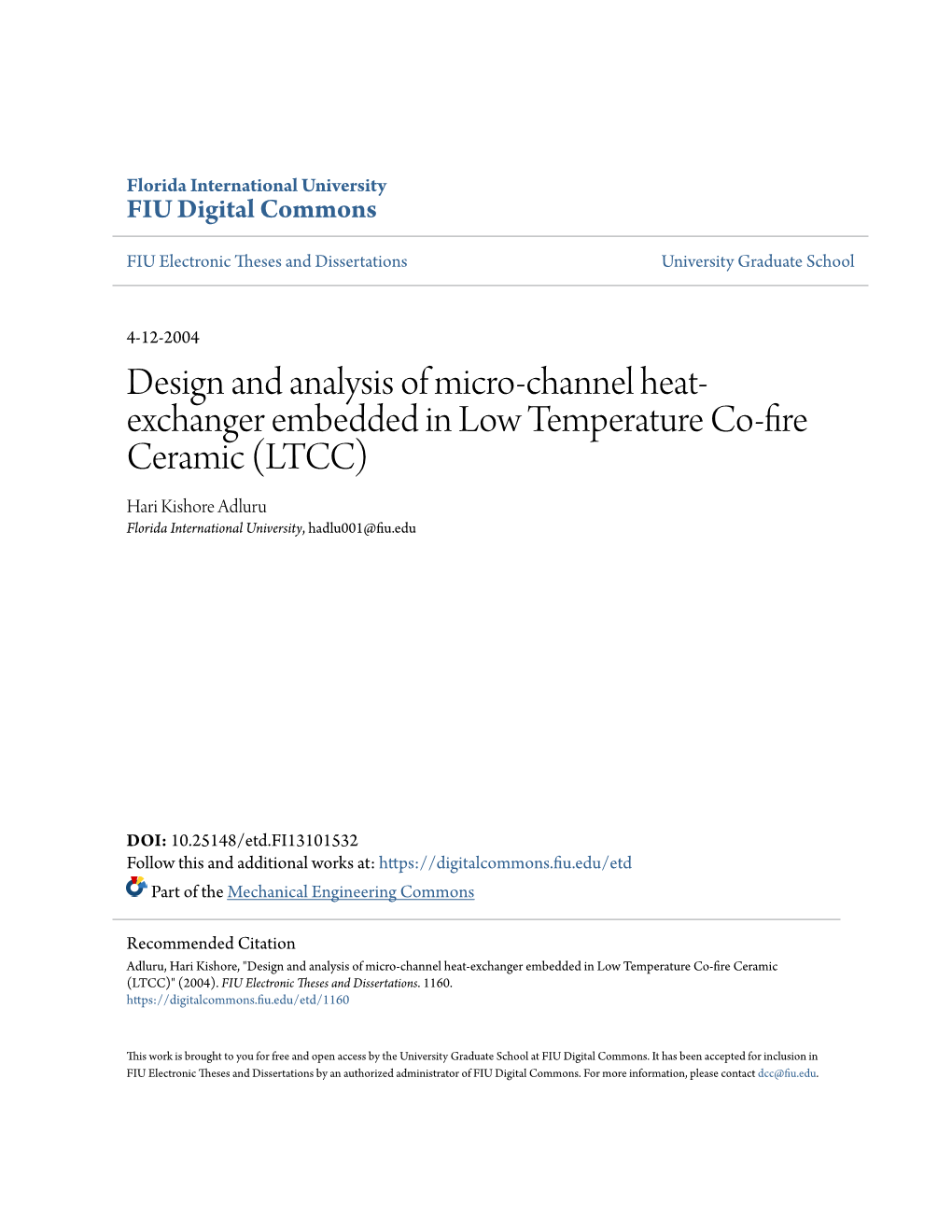
Load more
Recommended publications
-
Design for Manufacturability of Macro and Micro Products: a Case Study of Heat Exchanger Design
Downloaded from orbit.dtu.dk on: Oct 01, 2021 Design for manufacturability of macro and micro products: a case study of heat exchanger design Omidvarnia, F.; Weng Feng, L.; Hansen, H. N.; Sarhadi, A.; Lenau, T. A.; Mortensen, N. H. Published in: International Journal on Interactive Design and Manufacturing Link to article, DOI: 10.1007/s12008-018-0457-9 Publication date: 2018 Document Version Peer reviewed version Link back to DTU Orbit Citation (APA): Omidvarnia, F., Weng Feng, L., Hansen, H. N., Sarhadi, A., Lenau, T. A., & Mortensen, N. H. (2018). Design for manufacturability of macro and micro products: a case study of heat exchanger design. International Journal on Interactive Design and Manufacturing, 12(3), 995–1006. https://doi.org/10.1007/s12008-018-0457-9 General rights Copyright and moral rights for the publications made accessible in the public portal are retained by the authors and/or other copyright owners and it is a condition of accessing publications that users recognise and abide by the legal requirements associated with these rights. Users may download and print one copy of any publication from the public portal for the purpose of private study or research. You may not further distribute the material or use it for any profit-making activity or commercial gain You may freely distribute the URL identifying the publication in the public portal If you believe that this document breaches copyright please contact us providing details, and we will remove access to the work immediately and investigate your claim. International -
Metallic Micro Heat Exchangers: Properties, Applications and Long Term Stability
ECI Symposium Series, Volume RP5: Proceedings of 7th International Conference on Heat Exchanger Fouling and Cleaning - Challenges and Opportunities, Editors Hans Müller-Steinhagen, M. Reza Malayeri, and A. Paul Watkinson, Engineering Conferences International, Tomar, Portugal, July 1 - 6, 2007 METALLIC MICRO HEAT EXCHANGERS: PROPERTIES, APPLICATIONS AND LONG TERM STABILITY J.J. Brandner1), W. Benzinger, U. Schygulla, S. Zimmermann and K. Schubert Forschungszentrum Karlsruhe, Institute for Micro Process Engineering (IMVT), P.O.Box 3640, DE-76021 Karlsruhe, Germany 1) corresponding author: Phone +49 7247 82 3963, Fax +49 7247 82 3186, e-mail: [email protected] ABSTRACT showed that CFD calculations may be advantageous to use for the primary design and to obtain a first idea of the heat Micro heat exchangers, which until recently have been transfer performance of such microstructure devices. implemented only at laboratory scale, are now being Nevertheless, the manufacturing process is determined by available for industrial applications. They are well known the possibilities to obtain micro channels or microstructures, for their superior heat transfer properties due to the large the bonding methods and of course by the needs of the surface-to-volume ratio. But there are little data available on processes the devices are meant for. Moreover, the process the long term stability of these devices. itself is limited by the long term stability of the In this paper application several application examples microstructure devices against corrosion, blocking and for micro heat exchangers made of stainless steel are fouling. presented. The devices consist of stainless steel foils In this paper, the design and manufacturing technique providing numerous micro channels generated by of microstructure heat exchangers is described. -
Optimization of a Residential Air Source Heat Pump Using Heat
Purdue University Purdue e-Pubs International Refrigeration and Air Conditioning School of Mechanical Engineering Conference 2016 Optimization of a Residential Air Source Heat Pump using Heat Exchangers with Small Diameter Tubes Mohamed Beshr University of Maryland, United States of America, [email protected] Vikrant Aute University of Maryland, United States of America, [email protected] Reinhard Radermacher University of Maryland, United States of America, [email protected] Follow this and additional works at: http://docs.lib.purdue.edu/iracc Beshr, Mohamed; Aute, Vikrant; and Radermacher, Reinhard, "Optimization of a Residential Air Source Heat Pump using Heat Exchangers with Small Diameter Tubes" (2016). International Refrigeration and Air Conditioning Conference. Paper 1587. http://docs.lib.purdue.edu/iracc/1587 This document has been made available through Purdue e-Pubs, a service of the Purdue University Libraries. Please contact [email protected] for additional information. Complete proceedings may be acquired in print and on CD-ROM directly from the Ray W. Herrick Laboratories at https://engineering.purdue.edu/ Herrick/Events/orderlit.html 2066, Page 1 Optimization of a Residential Air Source Heat Pump using Heat Exchangers with Small Diameter Tubes Mohamed BESHR1, Vikrant AUTE2*, Reinhard RADERMACHER3 1,2,3Department of Mechanical Engineering, University of Maryland, College Park, MD 20742 USA Phone: 1301-405-7314, 2301-405-8726, 3301-405-5286 Email: [email protected], [email protected], [email protected] * Corresponding Author ABSTRACT Heat exchangers play significant role in refrigeration and air conditioning systems. Ongoing research aims to improve, or at least maintain, the system performance while reducing the size, weight and cost of the heat exchangers. -
Heat Exchanger/Reactors (HEX Reactors): Concepts, Technologies: State-Of-The-Art
Review Heat exchanger/reactors (HEX reactors): Concepts, technologies: State-of-the-art Z. Anxionnaz a,b, M. Cabassud a,∗, C. Gourdon a, P. Tochon b a Laboratoire de Génie Chimique, UMR 5503 CNRS/INPT/UPS, 5 rue P. Talabot, BP 1301, 31106 Toulouse Cedex 1, France b Atomic Energy Commission-GRETh, 17 avenue des Martyrs, F-38054 Grenoble Cedex 9, France abstract Process intensification is a chemical engineering field which has truly emerged in the past few years and is currently rapidly growing. It consists in looking for safer operating conditions, lower waste in terms of costs and energy and higher productivity; and a way to reach such objectives is to develop multifunctional devices such as heat exchanger/reactors for instance. This review is focused on the latter and makes a point on heat exchanger/reactors. After a brief presentation of requirements due to transposition from batch to continuous apparatuses, Keywords: heat exchangers/reactors at industrial or pilot scales and their applications are described. Process intensification Heat exchanger reactor State-of-the-art Technology Continuous reactor Contents 1. Introduction........................................................................................................................................ 2030 2. Transposition from batch to continuous heat-exchanger/reactor ................................................................................ 2030 2.1. Thermal intensification.................................................................................................................... -
Testing and Design of a Microchannel Heat Exchanger with Multiple Plates
Ind. Eng. Chem. Res. 2009, 48, 4535–4541 4535 Testing and Design of a Microchannel Heat Exchanger with Multiple Plates Haishan Cao,†,‡ Guangwen Chen,*,† and Quan Yuan† Dalian National Laboratory for Clean Energy, Dalian Institute of Chemical Physics, Chinese Academy of Sciences, Dalian 116023, China, and Graduate UniVersity, Chinese Academy of Sciences, Beijing 100049, China The microheating system is one of the hard cores of a microchemical system. In this paper, the performance of microchannel heat exchangers (MCHEs) with two plates made of stainless steel was investigated experimentally. The maximum volumetric heat transfer coefficient was up to 5.2 MW/m3 · K with a corresponding pressure drop of less than 20 kPa under a Reynolds number of around 65. The correlations of average Nusselt number and pressure drop to Reynolds number in microchannels were presented for designing MCHEs with multiple plates with the same geometric structure being researched, and the validity of correlations was verified through MCHEs with two plates and ten plates. Moreover, experimental results verified that MCHEs can be applied to recover energy in integrated microstructure systems of thermal and chemical processes via a system of ethanol dehydration to ethylene. 1. Introduction number (Re) for fully developed flow can not be effectively applied to the design of MCHEs, especially counterflow Since the emergence of silicon integrated circuit technology, MCHEs. the integrated circuit density has increased by several orders of Among earlier research work related to the overall perfor- magnitude. Accordingly, the heat dissipation problem has mance of two-fluid MCHEs, Alm et al.4 experimentally become a serious limitation on development in the semiconduc- investigated and simulated the performance of counterflow tor industry. -
Design, Fabrication, and Testing of Cross Flow Micro Heat Exchangers. Chad Randall Harris Louisiana State University and Agricultural & Mechanical College
Louisiana State University LSU Digital Commons LSU Historical Dissertations and Theses Graduate School 2001 Design, Fabrication, and Testing of Cross Flow Micro Heat Exchangers. Chad Randall Harris Louisiana State University and Agricultural & Mechanical College Follow this and additional works at: https://digitalcommons.lsu.edu/gradschool_disstheses Recommended Citation Harris, Chad Randall, "Design, Fabrication, and Testing of Cross Flow Micro Heat Exchangers." (2001). LSU Historical Dissertations and Theses. 290. https://digitalcommons.lsu.edu/gradschool_disstheses/290 This Dissertation is brought to you for free and open access by the Graduate School at LSU Digital Commons. It has been accepted for inclusion in LSU Historical Dissertations and Theses by an authorized administrator of LSU Digital Commons. For more information, please contact [email protected]. INFORMATION TO USERS This manuscript has been reproduced from the microfilm master. UMI films the text directly from the original or copy submitted. Thus, some thesis and dissertation copies are in typewriter face, while others may be from any type of computer printer. The quality of this reproduction is dependent upon the quality of the copy submitted. Broken or indistinct print, colored or poor quality illustrations and photographs, print bleedthrough, substandard margins, and improper alignment can adversely affect reproduction. In the unlikely event that the author did not send UMI a complete manuscript and there are missing pages, these will be noted. Also, if unauthorized copyright material had to be removed, a note will indicate the deletion. Oversize materials (e.g., maps, drawings, charts) are reproduced by sectioning the original, beginning at the upper left-hand comer and continuing from left to right in equal sections with small overlaps. -
Heat Spreader Heat Sink Heat Spreader Heat Sink Heat Spreader Heat Sink Heat Spreader Heat Sink
Proceedings of Fifth International Conference on Enhanced, Compact and Ultra-Compact Heat Exchangers: Science, Engineering and Technology, Eds. R.K. Shah, M. Ishizuka, T.M. Rudy, and V.V. Wadekar, Engineering Conferences International, Hoboken, NJ, USA, September 2005. CHE2005 – 22 MICRO AND MESO SCALE COMPACT HEAT EXCHANGERS IN ELECTRONICS THERMAL MANAGEMENT-A REVIEW Yogendra Joshi and Xiaojin Wei G.W. Woodruff School of Mechanical Engineering Georgia Institute of Technology Atlanta, GA 30332 [email protected] ABSTRACT often required for both single phase and two phase devices. The current status of these technologies is discussed. Due to dramatic gains in functionality and speed, A number of new effects in the physics of transport microelectronic components are experiencing ever phenomena have been identified by various researchers in increasing heat fluxes. Microprocessor heat fluxes are meso-sized thermal management devices. These are approaching 100W/cm2 on a spatially averaged basis on the discussed over the range of feature sizes studied. chip of typical footprint area 1-5 cm2, with several times Remaining gaps in the understanding of these phenomena larger values locally in the logic regions. Power electronics are identified. devices are approaching heat fluxes in the 1 kW/cm2 range over footprint areas of 10 cm2 or higher. Proper operation of the semiconductor devices typically requires maximum 1 INTRODUCTION temperatures to be limited below 85-100oC for o o microprocessors and 125 C-150 C for silicon based power While the clock speed and capabilities of electronics components. microprocessors have increased dramatically over the past During the past two decades dramatic advances have decade in accordance with the Moores’s Law, the system been made in microfabrication techniques. -
Experimental Investigation of Fluid Flow and Heat Transfer in a Single-Phase
Experimental investigation of fluid flow and heat transfer in a single-phase liquid flow micro-heat exchanger N. García-Hernando a,*, A. Acosta-Iborra a, U. Ruiz-Rivas a, M. Izquierdo b a Energy Systems Engineering Research Group, Departamento de Ingeniería Térmica y de Fluidos, Universidad Carlos III de Madrid, Avda. de la Universidad 30, Leganés, 28911 Madrid, Spain b Instituto de Ciencias de la Construcción Eduardo Torroja (CSIC), C/Serrano Galvache 4, 28033 Madrid, Spain abstract This work presents an experimental analysis of the hydrodynamic and thermal performance of micro heat exchangers. Two micro heat exchangers, characterized by microchannels of 100 Â 100 and 200 Â 200 lm square cross sections, were designed for that purpose. The fluid used was deionized water and there was no phase change along the fluid circuit. The fluid pressure drop along the heat exchanger and the heat transfer were measured and corrections were made to isolate the contribution of the micro channels. The results were compared with the predictions of the classical viscous flow and heat transfer theory. The main conclusions show that the experimental results fit well with these theories. No effects of heat transfer enhancement or pressure drop increase were observed as a consequence of the small scale of the microchannels. 1. Introduction devices. The channels were 50 lm wide and 300 lm deep. They used deionized water and the results obtained showed good agree The heat transfer processes between two fluids are common in ment with the classical theory of laminar flow. The thermal resis many engineering systems, such as power plants, chemical reac tance was independent of the mass flow rate when the conditions tors or other power devices. -
Analysis of Effectiveness and Pressure Drop in Micro Cross-Flow Heat Exchanger
International Journal of Engineering Research & Technology (IJERT) ISSN: 2278-0181 Vol. 2 Issue 4, April - 2013 Analysis of Effectiveness and Pressure Drop in Micro Cross-flow Heat Exchanger Hiteshgiri Goswami Student, Mechanical Engineering Department, R. K. University, Gujarat, India Jiten Makadia Asst. Prof, Mechanical Engineering Department, R. K. University, Gujarat, India Abstract k thermal conductivity ɛ exchanger effectiveness Micro heat exchanger is an extremely high efficiency, cross flow, ṁ mass flow rate fluid-fluid, micro heat exchanger formed from high aspect ratio m fin efficiency parameter microstructures. Toconcurrently achieve the goals of high mass flow N total number of channels on one side rate, low pressure drop, and high heat transfer rates, one embodiment NuT constant wall temperature Nusselt number of the micro heat exchanger comprises numerous parallel, IJERTbut NTU number of transfer units relatively short microchannels. The performance of these heatIJERT P pressure exchangersis superior to the performance of previously available heat T temperature exchangers, as measured by the heat exchange rate per unit volume or Re Reynolds number per unit mass. Typical gas channel lengths in the micro heat not U overall heat transfer coefficient exchangers are from a few hundred micrometers to about age. t X,Y,Z principal dimensions of heat exchanger 2000micrometers, with typical channel widths from around 50 in micrometers to a few hundred micrometers, although the dimensions in particular applications could be greater or smaller. The novel micro 1. Introduction heat exchangers offer substantial advantages over conventional, larger l A heat exchanger is a thermal device that transports energy by heat exchangers in performance, weight, size, and cost. -
Experimentation and Simulation of a Sub-Millimeter Channel Heat Exchanger Julien Fontaine, J
Liquid Cooling of a Microprocessor: Experimentation and Simulation of a Sub-Millimeter Channel Heat Exchanger Julien Fontaine, J. Gonzales, Prashant Kumar, François Pigache, Pascal Lavieille, Frédéric Topin, Marc Miscevic To cite this version: Julien Fontaine, J. Gonzales, Prashant Kumar, François Pigache, Pascal Lavieille, et al.. Liquid Cooling of a Microprocessor: Experimentation and Simulation of a Sub-Millimeter Channel Heat Exchanger. Heat Transfer Engineering, Taylor & Francis, 2019, 41 (15-16), 10.1080/01457632.2019.1628485. hal-03189296 HAL Id: hal-03189296 https://hal-amu.archives-ouvertes.fr/hal-03189296 Submitted on 3 Apr 2021 HAL is a multi-disciplinary open access L’archive ouverte pluridisciplinaire HAL, est archive for the deposit and dissemination of sci- destinée au dépôt et à la diffusion de documents entific research documents, whether they are pub- scientifiques de niveau recherche, publiés ou non, lished or not. The documents may come from émanant des établissements d’enseignement et de teaching and research institutions in France or recherche français ou étrangers, des laboratoires abroad, or from public or private research centers. publics ou privés. Distributed under a Creative Commons Attribution - NonCommercial| 4.0 International License 1 Liquid Cooling of a Microprocessor: Experimentation and Simulation of a 2 Sub-Millimeter Channel Heat Exchanger 3 4 5 Fontaine J.1, Gonzalez C.1,2, Kumar P.2, Pigache F. 1, Lavieille P. 1, Topin F. 2, Miscevic M. 1 6 7 8 1University of Toulouse, LAPLACE (Laboratory on Plasma and Conversion of Energy), Toulouse, France 2 9 Aix Marseille Univ, CNRS, IUSTI, Marseille, France 10 11 12 13 14 15 16 17 18 19 20 21 22 23 24 25 26 27 28 29 30 31 32 33 34 Address correspondence to Dr. -
Numerical and Experimental Study of Microchannel Performance on Flow Maldistribution
micromachines Article Numerical and Experimental Study of Microchannel Performance on Flow Maldistribution Jojomon Joseph 1,2,*, Danish Rehman 3 , Michel Delanaye 1, Gian Luca Morini 3 , Rabia Nacereddine 1, Jan G. Korvink 2 and Juergen J. Brandner 2 1 MITIS SA, Rue del Rodje Cinse 98, 4102 Seraing, Belgium; [email protected] (M.D.); [email protected] (R.N.) 2 Institute of Microstructure Technology, Karlsruhe Institute for Technology, 76131 Karlsruhe, Germany; [email protected] (J.G.K.); [email protected] (J.J.B.) 3 Microfluidics Laboratory, Department of Industrial Engineering (DIN), University of Bologna, Via del Lazzaretto 15/5, 40131 Bologna BO, Italy; [email protected] (D.R.); [email protected] (G.L.M.) * Correspondence: [email protected] Received: 27 February 2020; Accepted: 19 March 2020; Published: 20 March 2020 Abstract: Miniaturized heat exchangers are well known for their superior heat transfer capabilities in comparison to macro-scale devices. While in standard microchannel systems the improved performance is provided by miniaturized distances and very small hydraulic diameters, another approach can also be followed, namely, the generation of local turbulences. Localized turbulence enhances the heat exchanger performance in any channel or tube, but also includes an increased pressure loss. Shifting the critical Reynolds number to a lower value by introducing perturbators controls pressure losses and improves thermal efficiency to a considerable extent. The objective of this paper is to investigate in detail collector performance based on reduced-order modelling and validate the numerical model based on experimental observations of flow maldistribution and pressure losses. -
Microstructured Reactors for a Portable Hydrogen Production Unit
Microstructured reactors for a portable hydrogen production unit Citation for published version (APA): Delsman, E. R. (2005). Microstructured reactors for a portable hydrogen production unit. Technische Universiteit Eindhoven. https://doi.org/10.6100/IR589892 DOI: 10.6100/IR589892 Document status and date: Published: 01/01/2005 Document Version: Publisher’s PDF, also known as Version of Record (includes final page, issue and volume numbers) Please check the document version of this publication: • A submitted manuscript is the version of the article upon submission and before peer-review. There can be important differences between the submitted version and the official published version of record. People interested in the research are advised to contact the author for the final version of the publication, or visit the DOI to the publisher's website. • The final author version and the galley proof are versions of the publication after peer review. • The final published version features the final layout of the paper including the volume, issue and page numbers. Link to publication General rights Copyright and moral rights for the publications made accessible in the public portal are retained by the authors and/or other copyright owners and it is a condition of accessing publications that users recognise and abide by the legal requirements associated with these rights. • Users may download and print one copy of any publication from the public portal for the purpose of private study or research. • You may not further distribute the material or use it for any profit-making activity or commercial gain • You may freely distribute the URL identifying the publication in the public portal.