Romulo Parte 1.Pdf
Total Page:16
File Type:pdf, Size:1020Kb
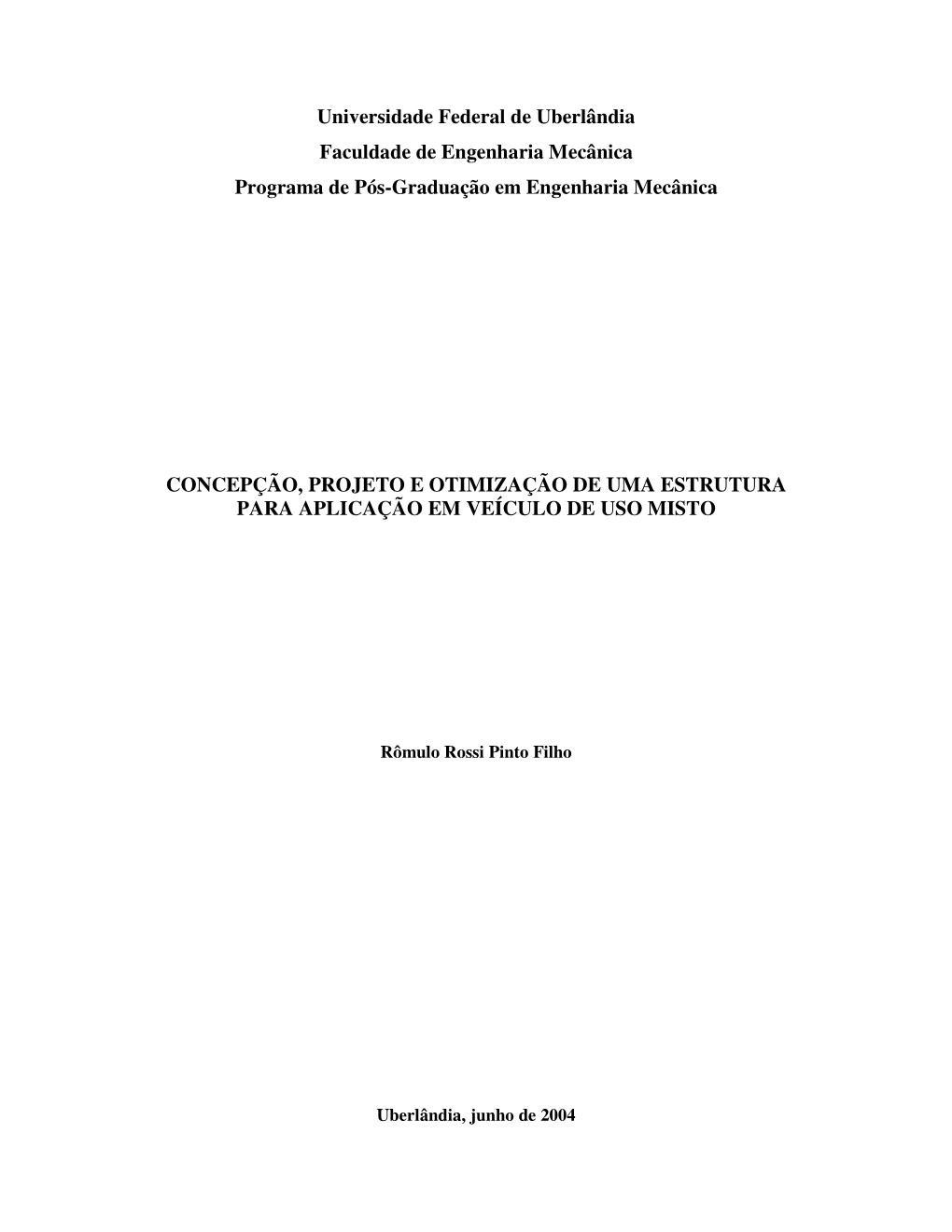
Load more
Recommended publications
-
Jeep City - New Location Grand Opening
ACT JeepTrAction Newsletter Edition 14 — June 2015 Jeep City - New Location Grand Opening plus Camp Coffs Mag Pics & Part 1 of “ Jeep Through the Years” arti- cle & Rolfe Jeep Social nite, plus more… Presidents note… As I flick through the current edition of Jeep Action Magazine it was great to see so many photos of club members who attended Camp Coffs 2015 earlier this year. Starting with Marek on the front cover, pictures of the Bartell’s, Paul Hannelly, the Little’s, the Slattery’s & a few shots of our campsites & our club letter thanking Michael, Robyn & Coffs Coast Jee- pers in the editors notes section & Troy featuring in a half page Camp Coffs repairs section. Further to the exposure we received in the magazine we also had a lot of club members feature throughout the Camp Coffs DVD that was put to- gether & released recently. Earlier in the month we were all invited as a club to attend the official launch of Jeep City’s new location at Fyshwick. The night was well sup- ported by club members & Brett had certainly done a lot of work in getting his new shop up & running. The opening also saw other trade stalls from Total Tools, Uneek 4x4, Cal Offroad, Mickey Thompson Tires & Rinse Kit. On Tuesday the 12th of May we had another Club Social & Sponsors trade night at Rolfe Jeep. Along with providing a free BBQ & some liquid refreshments, Rolfe Jeep also organised a short presentation. The night also gave us an opportunity to show our thanks & our appreciation for their long term support of our club, with a presentation of 2 sponsors awards, one recognising their support from 2010 to 2014 & another for the current year, of 2015. -
1940 Ford Pygmy
1940 FORD PYGMY Willys Model MD (M38A1), 1952-71 Podle denníku the New York Times z 21června 2002, the Museum of Modern Art (MOMA) in New York nedávno koupilo Willys M38A1 z r.1952,pro svou stálou sbírku významných vozidel s popisem,že je to nejlepší Jeep,co kdy Willys postavil. Ještě před rokem 2002 mělo MOMA vystaveno mnoho kusů vozidel různých značek na.př. Bentley,Mercedes,MG, Cisitalia, Talbot Lincoln Continental a Jeep M38. Brzy poté,byl vedoucí MOMA přizván k posouzení designu nově restaurovaného M38A1 a jeho citace z pohledu výtvarné formy byla:: "A typical case of styling -- and ugly styling at that -- ruining a good, clear example of machine art. It is the usual case of bloating used to make cars look bigger by adding unnecessary curves."./Opravdu svérázný přístup k stylingu zvenku a ještě svéráznější uvnitř. Toto ničící dobro má mnoho zatáček a vypouklin".Nyní se mu podařilo tento vůz dostat do sbírky a také jeho pohled na věc se změnila.Již mluví o významném stylu od konce války. Významný stal byl ale ve skutečnosti výsledek Willysovo snažení o požadavek armády o silnější jeep. Kapotáž musela býti zvýšena ,aby se do ní vešel motor s F hlavou.Willysův model MD byl nástupcem k jeho vojenské verzi CJ3A,přezdívaný mariňáky na M38 a považovali ho za naprosto stejný s MD a tak se stalo,že byl přejmenován na M38A1 That new Jeep no longer appears bloated in 2002. Obviously even MOMA has accepted it now. But as the first significant styling change to the Jeep since World War II, it raised a few eyebrows fifty years ago. -
Bibliographie Articles De Revue
BIBLIOGRAPHIE ARTICLES DE REVUE Mise à jour au 14 juillet 2021 Classement par ordre chronologique Merci à Eric BESSON qui a contribué à enrichir cette bibliographie en me communiquant les références des articles de la revue Army Motors (M.P.V.A.) et les références de la défunte revue française V.M.I.. EN ANGLAIS The Military Jeep in Action, photographies compilées par Mark ASKEW . Vol 1 issue 1 : Bantam Number One (with over 16 photos), the Ford GPA (Seep) (with over 50 photos) and Machine Guns & Mounts on WW2 Jeeps (with over 66 photos). Vol 1 issue 2 : 2 Bantam Number MK II (with over 30 photos), the Ford GPA (Seep) Part 2 (with over 50 photos) and Machine Guns & Mounts on WW2 Jeeps Part 2 (with over 70 photos). Vol 1 issue 3 : Bantam Number BRC 40 Part One (with over 60 photos), Mini Jeeps Part One (with over 25 photos) and WW2 Jeeps and Trailers Part One (with over 66 photos). Vol 1 issue 4 : Bantam Number BRC 40 Part Two (with over 40 photos), Mini Jeeps Part Two (with over 60 photos) and WW2 Jeeps and Trailers Part Two (with over 40 photos). Vol 1 Issue 5 : Ford Pygmy/Budd Jeeps (with over 30 photos), the Ford GP Pre-production model (with over 50 photos) Rail Jeeps during WW2 (with over 40 photos) and the 1/2 Ton Jeep (MLW) (with over 17 photos). Vol 1 Issue 6 : the Willys Quad and Willys MA (with over 56 photos). WW2 Jeeps and Wire Cutters (with over 40 photos). -
Digital Magazine
DIGITAL MAGAZINE 6 Jeep, the Jeep grille and related logos, vehicle model names and trade dress are trademarks of FCA US LLC and used under license by Premium & Collectibles Trading Co ltd. ©2021 FCA US LLC. CONTENTS THE JEEP STORY ® 1 THE TESTS THE JEEP BRAND ® 6 CJ-3B © 2021 YOUR COLLECTION Editorial Manager: Phil Hunt Eaglemoss Inc. Build the WIllys MB Jeep® Design Manager: Caroline Grimshaw 315 West 36th Street, is available by monthly subscription. New York, NY 10018 www.build-willysjeep.com Packaged by: Milanoedit srl, www.milanoedit.com Eaglemoss Ltd., US CUSTOMER SERVICE Premier Place, For questions about the collection, Researcher/writer: Roberto Bruciamonti 2 & A Half Devonshire Square, replacements and substitutions, London, EC2M 4UJ, UK or to cancel, pause or modify Photography credits: © NARA (pp.1, 2, 3, 4, 5), your subscription, please call © Bruciamonti (pp.6, 7), 144 Avenue Charles de Gaulle, our US Customer Service team © FCA (p.8), 92200 NEUILLY-SUR-SEINE, at 800-261-6898, or email us at © MMC (p.10) France [email protected] Die-Cast Club® 2021 All rights reserved Jeep, the Jeep grille and related logos, vehicle model names and trade dress are trademarks of FCA US LLC and used under license by Premium & Collectibles Trading Co ltd. ©2021 FCA US LLC. THE JEEP® STORY THE TESTS THE TESTS ▲ The tests conducted on the pre- The Camp Holabird trials really put the series models called for teamwork prototypes through their paces. and effort from everyone involved. o paraphrase an old adage, prior to ton vehicle could have on the battlefield. -
Spring 2016 No
Arkansas Military History Journal A Publication of the Arkansas National Guard Museum, Inc. Vol. 10 Spring 2016 No. 2 Black History Trail Blazing a Path for the Future of Black Soldiers BOARD OF DIRECTORS Chairman Brigadier General Keith A. Klemmer Ex-Officio Vice Chairman Major General (Ret) Kendall Penn Ex-Officio Secretary Dr. Raymond D. Screws (Non-Voting) Ex-Officio Treasurer Colonel Damon N. Cluck Board Members Ex-Officio. Major James Holifield Ex-Officio. Captain Barry Owens Historian – Major Anthony Rushing At Large – Lieutenant Colonel Clement J. Papineau, Jr. At Large – Chief Master Sergeant Melvin E. McElyea Major Matthew Anderson (Non-Voting Consultant) Deanna Holdcraft (Non-Voting Consultant) Museum Staff Dr. Raymond D. Screws, Director/Journal Editor Erica McGraw, Museum Assistant, Journal Layout & Design Incorporated 27 June 1989 Arkansas Non-profit Corporation Cover Photograph: Copyright is held by National Archives. Brig. General B.O. Davis and Buffalo Soldiers at Camp Robinson, 15 March 1943. Message from the Editor We begin our second edition of the resurrected Arkansas Military History Journal covering the Arkansas National Guard Museum’s Black History Month panel discussion that was facilitated by COL (ret) Joe Davis in February. This was a lively discussion and if you were unable to attend, this article is the next best thing. The ARNG Museum has a temporary exhibit that runs through June 24, 2016, covering the 153rd and 206 regiments that were stationed in the Aleutians during WWII. To help commemorate their sacrifices, we include an article on these units compiled by COL Damon Cluck. In addition, we provide a piece by Arkansas National Guard Command Historian Anthony Rushing on lineage and honors. -
'Thundering Herd'
‘Thundering Herd’ Newsletter of the 8th Armored Division Association Ardennes, Rhineland, Central Europe Winter/Spring –2017 – 2018 Vol. VI No. 2 th Dear Veterans of the 8 Armored Division, Members of the Association, Descendants, Family and Friends, Merry Christmas -Happy Holidays- Happy New Year! Welcome to the ‘Winter’/Spring 2017-2018 edition of the Association Newsletter – ‘The Thundering Herd’. We hope to continue to use this newsletter as a means to communicate with the membership, share information, tell the stories of the veterans, and preserve the memory of this gallant fighting unit. A number of original veterans, descendants and those committed to commemorating the th service of the veterans of the 8 Armored Division are maintaining the Association and are planning events, ceremonies and dissemination of articles on the history of the Division. May sincere thanks to them! th We invite all living veterans of the 8 Armored Division to join the Association as honorary members, no dues required, although donations are welcomed. We are also seeking members who share our mission and goals. Please take a look at the th outstanding Division web site created by Okey Taylor, C-58 AIB and maintained by webmaster – Scott Thorpe. There you can obtain membership applications to fill out and mail to the Association address: http://www.8th-armored.org/ th 8 Armored Division Association 2345 E. Dauphin St Philadelphia, PA 19125 Use the E-Mail address: [email protected] To communicate further, we also feature a ‘Facebook’ account and ask all interested to enroll in order to stay in contact and share comments and information: New Association ‘Facebook’ page http://www.facebook.com/groups/269231523148647/ We are in need of volunteers to assist with the following: * Reunions - a volunteer committee to work on the details of a potential annual reunion/Association meeting where yearly business and elections and planning can be conducted. -
Digital Magazine
DIGITAL MAGAZINE 5 Jeep, the Jeep grille and related logos, vehicle model names and trade dress are trademarks of FCA US LLC and used under license by Premium & Collectibles Trading Co ltd. ©2021 FCA US LLC. CONTENTS THE JEEP STORY ® 1 THE ANCESTORS THE JEEP Brand ® 6 M38 AND M170 © 2021 US CUSTOMER SERVICE Editorial Manager: Phil Hunt Eaglemoss Inc. For questions about the collection, Design Manager: Caroline Grimshaw 315 West 36th Street replacements and substitutions, New York, NY 10018 or to cancel, pause or modify Packaged by: Milanoedit srl, your subscription, please call www.milanoedit.com Die-Cast Club® 2021 our US Customer Service team at 800-261-6898, or email us at Researcher/writer: Roberto Bruciamonti All rights reserved [email protected] Photography credits: © NARA (pp.1, 2, 3, YOUR COLLECTION 4, 5, 8, 10), Build the WIllys MB Jeep® © Bruciamonti (pp.6, 7) is available by monthly subscription. www.build-willysjeep.com Jeep, the Jeep grille and related logos, vehicle model names and trade dress are trademarks of FCA US LLC and used under license by Premium & Collectibles Trading Co ltd. ©2021 FCA US LLC. THE JEEP® STORY THE ANCESTORS THE ANCESTORS ▲ A Ford Pygmy being tested The tests that would eventually lead to the by two members of the US Army at Camp Holabird. birth of the Jeep® started in the fall of 1940. ith the arrival of the Bantam Major Herbert J. Lawes, the officer prototype at the US Army test center in charge of testing, took delivery of the in Camp Holabird, Maryland, the Jeep . -
Livres.Doc - 1/13 - TM 10-1100 : Parts Price List for Special Model GP 1/4 Ton, 80" Wheelbase, 4 Wheel Drive (4X4), for U.S
ELÉMENTS DE BIBLIOGRAPHIE (WILLYS MB, FORD GPW, HOTCHKISS M201, REMORQUES) La plupart des ouvrages cités ci-dessous comportent eux-mêmes des indications bibliographiques dont certaines, trop imprécises, ne sont pas reprises ici. Une étoile (*) placée à la fin d'une référence indique une référence vérifiée. Mise à jour au 15 août 2021 ◄ dessin : Edward D'ANCONA Ouvrages généraux sur les véhicules militaires (références en français) e - U.S. (2 guerre mondiale) BECKER Emile, MILMEISTER Jean, Marquages et organisation U.S. Army (ETO 1944-45), Luxembourg, 1988, 2e édition 1995, 415p. * BERTIN François, Les véhicules américains de la Libération, Ed. Ouest-France, 1989, 127p. * BONIFACE J.-M., JEUDY J.-G., Les véhicules du Débarquement, E.P.A., 1994, 189p. * BONIFACE J.-M., JEUDY J.-G., Les véhicules militaires américains de 1939 à 1945, E.P.A., 1995, 189p. * - Français BONIFACE J.-M., JEUDY J.-G., Les véhicules militaires français de 1945 à nos jours, E.P.A., 1995, 227p. * BONIFACE J.-M., 50 ans de véhicules militaires en France de 1945 à nos jours, 3 volumes, E.T.A.I., Boulogne-Billancourt . volume 1 (cosigné par JEUDY J.G.), 1999, 191p. * . volume 2 (avec la collaboration de JEUDY J.G.), 2001, 191p. * . volume 3, armée de l’air, marine nationale, 2002, 191p. * ____________________ 1) Manuels techniques : Armée américaine : Les références ci-dessous concernent les modèles Willys-Overland MB et Ford GPW. Pour mémoire, figurent aussi ci-dessous les références des manuels et listes de pièces détachées des ancêtres (Willys MA, Bantam BRC, Ford GP) ainsi que des remorques traditionnelles (Willys MB-T et Bantam T3). -
Wheels & Tracks Index
INDEX ISSUES 1-75 Compiled by Peter B. Gunn Wheels & Tracks Index Issues 1-75 compiled by Peter B. Gunn Note: Issues and pages are represented by issue no. followed by page no. Thus 12-34 indicates issue no. 12, page 34. Australia — continued Austria — continued ABU DHABI MV accidents, 47-53 MV Events, 7-7, 13-6, 25-5, 28-4, 36-5 IDEX ‘95, 53-10 MV Events, 6-5, 10-4, 13-8, 16-5, 17-6, 21-5, ÖAF, 11-39, 19-46, 25-5 IDEX ‘97, 60-7 29-4, 32-4, 36-4, 39-4, 40-4, 41-4, 56-9 Saurer, 16-1, 19-46 MV reminiscences, 51-36 Steyr (-Daimler-Puch), 1-43, 2-23, 4-37, 6- ALBANIA MVs various, 34-9, 35-44, 39-47, 42-25, 44- 18, 9-22, 9-51, 16-2, 17-3, 17-42, 18-45, 19- MVs various, 68-14 10, 74-41 6, 19-18, 19-26, 19-46, 23-14, 24-10, 24-40, UNRRA trucks for, 38-13 Pontiac, 6-5 27-20, 27-53, 29-20, 39-47, 40-51, 42-11, Studebaker, 4-11, 6-5, 11-2, 16-38, 20-45, 51-30, 59-10, 60-7, 67-14, 68-16, 70-51, 71- ALGERIA , Sonacome, 6-39 20-51, 21-5 11, 72-11 Trailers , 16-5, 20-10 Collections (inc. Museums) ARGENTINA Transfield Systems, 61-11 Ardagger, 24-40, 25-2, 31-51, 41-48 AFVs , 63-11, 71-10 Unimog, 56-14, 57-9 Bad Ischl, 41-48 MVs various, 72-38 Yeramba, 16-40 Gill, Robert, 6-13 Panhard, 12-46 Collections (inc. -
Willys Overland Ww2 Essay
WILLYS OVERLAND WW2 ESSAY In , the Willys Overland company was nearing bankruptcy, but things , from oberonlife.com The only way to tell the difference is to locate the name plates on the vehicles. Only 27 units are still known to exist. There were nearly 13, of these produced. Even though the Gallipoli Campaign was deemed a disaster in terms of the loss of life suffered there… Words - Pages 4 Essay on Arthurian Legends Arthurian Legends The Arthurian legends have been around for years. World War II Jeeps had a three-speed transmission. Army started looking for a small vehicle suited for reconnaissance and messaging, while at the same time searching for a light cross-country weapons carrier. Jeeps became so ubiquitous in the European battle theater that some German troops believed that each American soldier was issued their own jeep. The names are all affectionate, for the jeep has made good. Recognizing the need to create standard specifications, the Army formalized its requirements on July 11, , and submitted them to U. Also referred to as 'any small plane, helicopter, or gadget'". Convergence from mixed origins and media coverage[ edit ] External images Part of Hillyer's February article. Continues on Page 2 Many body detail differences remained for as long as January , when a composite body, fabricated by American Central, was adopted by both Ford and Willys. To be sure, the jeep would be a lucky thing to have in time of trouble. Although, this myth has been speculated to have been traced back to the early first part of the century. -
The Brass Lamp the Brass Lamp
January 2016 The Brass Lamp CADILLAC and its RISE to FAME Article & photo by Gerald Perschbacher (LL.D.); all rights reserved In the home stretch on the numbers of acclaimed classic cars that were ever made, the name-brand of Cadillac is among the best known. Little wonder! Cadillac went from its modest lower-priced status of selling for under $1,000 in 1903 to tower atop the luxury car market in America by the 1950s. That was hardly a small feat when considering the early success of Winton, Stevens-Duryea, and a Traditional Cadillac designs were massaged to greater perfection in the eyes of rafter full of luxury car the wealthy who had the cash and willpower to back it up. Thus, custom classics were cultivated and added luster to the growing popularity of the Cadillac sur- makers. Among them name. Shown: a 1939 model. were Pierce-Arrow and Packard, two brands des- The first achievement of various twists and turns with tined for legendary status monumental fame and impact the luxury level as its target. which was realized while was the winning of the Dew- Becoming part of General they were very much in ar Trophy for successful in- Motors in 1908 gave it production. terchangeability of parts. enough momentum to gain The award originated in the the top rung on society’s up- Yet, Cadillac watched. United Kingdom but, inter- wardly mobile ladder of ac- Cadillac learned. Cadillac estingly, was not restricted. clamation which car buyers tried to increase and gain The first Americans to be hoped to climb.