MLS300 Series User's Guide
Total Page:16
File Type:pdf, Size:1020Kb
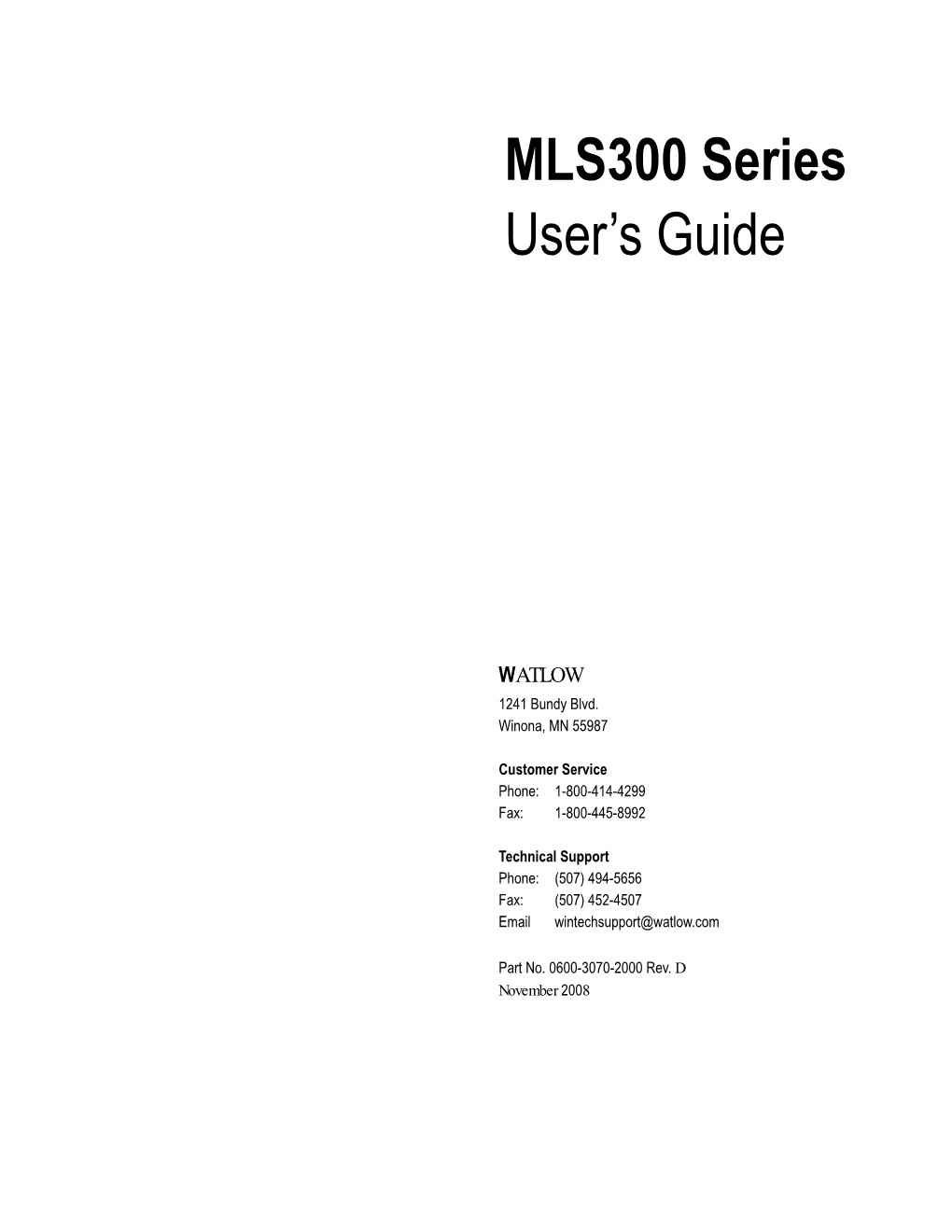
Load more
Recommended publications
-
Treatise on Combined Metalworking Techniques: Forged Elements and Chased Raised Shapes Bonnie Gallagher
Rochester Institute of Technology RIT Scholar Works Theses Thesis/Dissertation Collections 1972 Treatise on combined metalworking techniques: forged elements and chased raised shapes Bonnie Gallagher Follow this and additional works at: http://scholarworks.rit.edu/theses Recommended Citation Gallagher, Bonnie, "Treatise on combined metalworking techniques: forged elements and chased raised shapes" (1972). Thesis. Rochester Institute of Technology. Accessed from This Thesis is brought to you for free and open access by the Thesis/Dissertation Collections at RIT Scholar Works. It has been accepted for inclusion in Theses by an authorized administrator of RIT Scholar Works. For more information, please contact [email protected]. TREATISE ON COMBINED METALWORKING TECHNIQUES i FORGED ELEMENTS AND CHASED RAISED SHAPES TREATISE ON. COMBINED METALWORKING TECHNIQUES t FORGED ELEMENTS AND CHASED RAISED SHAPES BONNIE JEANNE GALLAGHER CANDIDATE FOR THE MASTER OF FINE ARTS IN THE COLLEGE OF FINE AND APPLIED ARTS OF THE ROCHESTER INSTITUTE OF TECHNOLOGY AUGUST ( 1972 ADVISOR: HANS CHRISTENSEN t " ^ <bV DEDICATION FORM MUST GIVE FORTH THE SPIRIT FORM IS THE MANNER IN WHICH THE SPIRIT IS EXPRESSED ELIEL SAARINAN IN MEMORY OF MY FATHER, WHO LONGED FOR HIS CHILDREN TO HAVE THE OPPORTUNITY TO HAVE THE EDUCATION HE NEVER HAD THE FORTUNE TO OBTAIN. vi PREFACE Although the processes of raising, forging, and chasing of metal have been covered in most technical books, to date there is no major source which deals with the functional and aesthetic requirements -
Antique Arms, Armour & Modern Sporting Guns
Antique Arms, Armour & Modern Sporting Guns Including the Max Gau Collection (Part I) Montpelier Street, London I 29 November 2018 Antique Arms, Armour & Modern Sporting Guns Including the Max Gau Collection (Part I) Montpelier Street, London | Thursday 29 November 2018, at 10.30am and 2pm Antique Arms & Armour: Lots 335 - 536 at 10.30am Modern Sporting Guns: Lots 540 - 806 at 2pm BONHAMS ENQUIRIES SALE NUMBERS IMPORTANT INFORMATION Montpelier Street Antique Arms & Armour 24660 Please note that lots of Iranian Knightsbridge, Director and Persian origin are subject London SW7 1HH David Williams CATALOGUE www.bonhams.com to US trade restrictions which +44 (0) 20 7393 3807 £20 currently prohibit their import +44 (0) 776 882 3711 mobile into the United States, with no VIEWING [email protected] Please see page 2 for bidder exemptions. Sunday 25 November information including after-sale 11am – 3pm Modern Sporting Guns collection and shipment Similar restrictions may apply Monday 26 November Head of Department to other lots. 9am – 7pm Patrick Hawes Please see back of catalogue Tuesday 27 November +44 (0) 20 7393 3815 for important notice to bidders It is the buyers responsibility 9am – 4.30pm +44 (0) 781 868 4869 mobile to satisfy themselves that the Wednesday 28 November [email protected] ILLUSTRATIONS lot being purchased may be 9am – 4.30pm Front cover: Lots 806, 792 & 779 imported into the country of Administrator Back cover: Lots 511 & 573 destination. Modern Sporting Guns Only Helen Abraham Inside front cover: Lot 522 Thursday 29 November +44 (0) 20 7393 3947 Inside back cover: Lot 799 The United States Government 9am – 12pm [email protected] has banned the import of ivory REGISTRATION into the USA. -
Hand-Forging and Wrought-Iron Ornamental Work
This is a digital copy of a book that was preserved for generations on library shelves before it was carefully scanned by Google as part of a project to make the world’s books discoverable online. It has survived long enough for the copyright to expire and the book to enter the public domain. A public domain book is one that was never subject to copyright or whose legal copyright term has expired. Whether a book is in the public domain may vary country to country. Public domain books are our gateways to the past, representing a wealth of history, culture and knowledge that’s often difficult to discover. Marks, notations and other marginalia present in the original volume will appear in this file - a reminder of this book’s long journey from the publisher to a library and finally to you. Usage guidelines Google is proud to partner with libraries to digitize public domain materials and make them widely accessible. Public domain books belong to the public and we are merely their custodians. Nevertheless, this work is expensive, so in order to keep providing this resource, we have taken steps to prevent abuse by commercial parties, including placing technical restrictions on automated querying. We also ask that you: + Make non-commercial use of the files We designed Google Book Search for use by individuals, and we request that you use these files for personal, non-commercial purposes. + Refrain from automated querying Do not send automated queries of any sort to Google’s system: If you are conducting research on machine translation, optical character recognition or other areas where access to a large amount of text is helpful, please contact us. -
Performance of Electroplated Copper Coating on Graphite Electrode in EDM Process
TNI Journal of Engineering and Technology Vol.8 No.1 January - June 2020 Performance of Electroplated Copper Coating on Graphite Electrode in EDM Process Nattawut Chindaladdha1* Don Kaewdook2 1*Master Program in Engineering Technology, Graduate School, Thai-Nichi Institute of Technology, Bangkok, Thailand, 10250 2Faculty of Engineering, Thai-Nichi Institute of Technology, Bangkok, Thailand, 10250 *Corresponding Author. E-mail address: [email protected] Received: 12 May 2020; Revised: 14 May 2020; Accepted: 21 May 2020 Published online: 25 June 2020 Abstract Electrical Discharge Machining (EDM) is a nonconventional manufacturing process whereby a desired shape is obtained by using electrical discharges. Material is removed from the workpiece by current discharges between tool-electrode and workpiece, separated by a dielectric liquid. Copper electroplating is the process to produce a layer of copper on the surface of the substrate in this research was used graphite which is the tool-electrode. The study aims to investigate the performance of EDM product which used graphite coated with the copper layer. The experiment designed by using Taguchi-grey relational approach based multi-response optimization to find the optimal electroplating parameters. The considered electroplating parameters including 3 parameters 2 levels, current density 3.7 A/dm2 and 5.4 A/dm2, electrolyte concentration 0.1 mol and 1.0 mol, plating time 3 hours and 5 hours. The electrode's machining performance of the surface roughness (SR) of workpiece, tool wear rate (TWR) and material removal rate (MRR) will be investigated and compared with the conventional copper electrode. Keywords: Copper electroplating, graphite electrode, EDM process, surface quality, wear rate 50 TNI Journal of Engineering and Technology Vol.8 No.1 January - June 2020 Performance of Electroplated Copper Coating on Graphite I. -
Metal Casting Terms and Definitions
Metal Casting Terms and Definitions Table of Contents A .................................................................................................................................................................... 2 B .................................................................................................................................................................... 2 C .................................................................................................................................................................... 2 D .................................................................................................................................................................... 4 E .................................................................................................................................................................... 5 F ..................................................................................................................................................................... 5 G .................................................................................................................................................................... 5 H .................................................................................................................................................................... 6 I .................................................................................................................................................................... -
GENERAL CONSIDERATIONS for DRILL SYSTEM DESIGN Ma1cohn Mellor and Paul V. Selhnann U.S. Army Cold Regions Research and Engineeri
Reproduced from Ice-Core Drilling edited by John F. Splettstoesser by permission of the University of Nebraska Press. Copyright 1976 by the University of Nebraska Press. Copyright renewed 2004 by the University of Nebraska Press. GENERAL CONSIDERATIONS FOR DRILL SYSTEM DESIGN Ma1cohn Mellor and Paul V. Selhnann U.S. Army Cold Regions Research and Engineering Laboratory Hanover, New Hampshire 03755 ABSTRACT Drilling systems are discussed in general terms, component functions common to all systems are identified, and a simple classification is drawn up in order to outline relations between penetra tion, material removal, hole wall support, and ground conditions. Energy and power requirements for penetration of ice and frozen ground are analyzed for both mechanical and thermal processes. Power requirements for removal of material and for hoisting of drill strings are considered, and total power requirements for complete systems are assessed. Performance data for drilling sys tems working in ice and frozen ground are reviewed, and results are analyzed to obtain specific energy values. Specific energy data are assembled for drag-bit cutting, normal impact and indenta tion, liquid jet attack, and thermal penetration. Torque and axial force capabilities of typical rotary drilling systems are reviewed and analyzed. The overall intent is to provide data and quan titative guidance that can lead to systematic design procedures for drilling systems for cold regions. INTRODUCTION Drilling involves an enormous range of highly specialized processes, products, and technolo gies, making it difficult to assimilate all the information required for solution of particular drill ing problems. This difficulty is very pronounced in the case of problems that involve frozen ground and massive ice, since existing drilling systems are likely to require modification to meet the special ground conditions. -
Manufacturing Technology I Unit I Metal Casting
MANUFACTURING TECHNOLOGY I UNIT I METAL CASTING PROCESSES Sand casting – Sand moulds - Type of patterns – Pattern materials – Pattern allowances – Types of Moulding sand – Properties – Core making – Methods of Sand testing – Moulding machines – Types of moulding machines - Melting furnaces – Working principle of Special casting processes – Shell – investment casting – Ceramic mould – Lost Wax process – Pressure die casting – Centrifugal casting – CO2 process – Sand Casting defects. UNIT II JOINING PROCESSES Fusion welding processes – Types of Gas welding – Equipments used – Flame characteristics – Filler and Flux materials - Arc welding equipments - Electrodes – Coating and specifications – Principles of Resistance welding – Spot/butt – Seam – Projection welding – Percusion welding – GS metal arc welding – Flux cored – Submerged arc welding – Electro slag welding – TIG welding – Principle and application of special welding processes – Plasma arc welding – Thermit welding – Electron beam welding – Friction welding – Diffusion welding – Weld defects – Brazing – Soldering process – Methods and process capabilities – Filler materials and fluxes – Types of Adhesive bonding. UNIT III BULK DEFORMATION PROCESSES Hot working and cold working of metals – Forging processes – Open impression and closed die forging – Characteristics of the process – Types of Forging Machines – Typical forging operations – Rolling of metals – Types of Rolling mills – Flat strip rolling – Shape rolling operations – Defects in rolled parts – Principle of rod and wire drawing – Tube drawing – Principles of Extrusion – Types of Extrusion – Hot and Cold extrusion – Equipments used. UNIT IV SHEET METAL PROCESSES Sheet metal characteristics – Typical shearing operations – Bending – Drawing operations – Stretch forming operations –– Formability of sheet metal – Test methods – Working principle and application of special forming processes – Hydro forming – Rubber pad forming – Metal spinning – Introduction to Explosive forming – Magnetic pulse forming – Peen forming – Super plastic forming. -
Ironworks and Iron Monuments Forges Et
IRONWORKS AND IRON MONUMENTS FORGES ET MONUMENTS EN FER I( ICCROM i ~ IRONWORKS AND IRON MONUMENTS study, conservation and adaptive use etude, conservation et reutilisation de FORGES ET MONUMENTS EN FER Symposium lronbridge, 23-25 • X •1984 ICCROM rome 1985 Editing: Cynthia Rockwell 'Monica Garcia Layout: Azar Soheil Jokilehto Organization and coordination: Giorgio Torraca Daniela Ferragni Jef Malliet © ICCROM 1985 Via di San Michele 13 00153 Rome RM, Italy Printed in Italy Sintesi Informazione S.r.l. CONTENTS page Introduction CROSSLEY David W. The conservation of monuments connected with the iron and steel industry in the Sheffield region. 1 PETRIE Angus J. The No.1 Smithery, Chatham Dockyard, 1805-1984 : 'Let your eye be your guide and your money the last thing you part with'. 15 BJORKENSTAM Nils The Swedish iron industry and its industrial heritage. 37 MAGNUSSON Gert The medieval blast furnace at Lapphyttan. 51 NISSER Marie Documentation and preservation of Swedish historic ironworks. 67 HAMON Francoise Les monuments historiques et la politique de protection des anciennes forges. 89 BELHOSTE Jean Francois L'inventaire des forges francaises et ses applications. 95 LECHERBONNIER Yannick Les forges de Basse Normandie : Conservation et reutilisation. A propos de deux exemples. 111 RIGNAULT Bernard Forges et hauts fourneaux en Bourgogne du Nord : un patrimoine au service de l'identite regionale. 123 LAMY Yvon Approche ethnologique et technologique d'un site siderurgique : La forge de Savignac-Ledrier (Dordogne). 149 BALL Norman R. A Canadian perspective on archives and industrial archaeology. 169 DE VRIES Dirk J. Iron making in the Netherlands. 177 iii page FERRAGNI Daniela, MALLIET Jef, TORRACA Giorgio The blast furnaces of Capalbio and Canino in the Italian Maremma. -
Alloys for Pressure Die Casting RHEINFELDEN ALLOYS
Primary Aluminium Alloys for Pressure Die Casting RHEINFELDEN ALLOYS Table of contents RHEINFELDEN ALLOYS – Aluminium Alloys for Pressure Die Casting General 2 ALUMINIUM RHEINFELDEN group 3 RHEINFELDEN FAST ALLOYS 4 Forms of delivery 5 Customer support and research and development 6 – 7 Aluminium casting alloys by RHEINFELDEN ALLOYS 8 – 9 Profile of the alloys for the die casters 10 Publications Alloys 11 – 20 Castasil ®-37 – AlSi9MnMoZr 21 – 24 Castasil ®-21 – AlSi9Sr 25 – 36 Silafont ®-36 – AlSi10MnMg 37 – 38 Silafont ®-38 – AlSi9MnMgZn 39 – 40 Castaman ®-35 – AlSi10MnMg 41 – 42 Thermodur ®-72/-73 – AlMg7Si3Mn – AlSi11Cu2Ni2Mg2Mn 43 – 53 Magsimal ®-59 – AlMg5Si2Mn Processing datasheets 54 Technical informations / Processing datasheets 55 Castasil ®-37 56 Castasil ®-21 57 Silafont ®-36 58 Silafont ®-38 59 Thermodur ®-72 60 Magsimal ®-59 Technical information 61 – 62 Surface coating 63 Joining techniques for die castings 64 Eight target levels for HPDC 65 Disclaimer and imprint 1 ALUMINIUM RHEINFELDEN group “Progress by tradition” Our policy ALUMINIUM RHEINFELDEN group: This history of aluminium Our RHEINFELDEN ALLOYS GmbH & Co. KG innovative char- in Germany started at Rheinfelden. In 1898 Europe’s first acter is what allows us to adapt rapidly to fast changing market river power station brought about the establishment of the first needs. The agility of a private family owned operated company, aluminium smelter in Germany, at Rheinfelden, Baden. the central geographic location in the European cast metal The company has always operated in three business segments market, the know-how and experience of our team, are factors and in October 2008 restructuring turned ALUMINIUM making a difference for Customers looking for reliable tradition RHEINFELDEN GmbH into a holding company and the former and modern innovation. -
WSR Vol 5 508.Indd
Coastal and Estuarine Hazardous Waste Site Reports Editors J. Gardiner1, B. Azzato2, M. Jacobi1, L. Harris1 1NOAA/OR&R/Coastal Protection and Restoration Division 2Azzato Communications Authors M. Hilgart3, S. Pollock3, B. Bergquist4 3Ridolfi Engineers Inc. 4EVS Environment Consultants NOAA National Oceanic and Atmospheric Administration NOS NOAA’s Ocean Service OR&R Office of Response and Restoration CPRD Coastal Protection and Restoration Division 7600 Sand Point Way NE Seattle, Washington 98115 September 2004 Coastal and Estuarine Hazardous Waste Site Reports Reviewers T. Dillon, S. Duncan, M. Geddes, M. Gielazyn H. Hillman, P. Knight, R. Mehran, L. Rosman, L. Sullivan Graphics K. Galimanis1 and R. Dailey2 14 Point Design 2EVS Environment Consultants NOAA National Oceanic and Atmospheric Administration NOS NOAA’s Ocean Service OR&R Office of Response and Restoration CPRD Coastal Protection and Restoration Division 7600 Sand Point Way NE Seattle, Washington 98115 September 2004 PLEASE CITE AS: B. Azzato, J. Gardiner, L. Harris, M. Jacobi, editors. 2004. Coastal and Estuarine Hazardous Waste Site Reports, September 2004. Seattle: Coastal Protection and Restoration Division, Office of Response and Restoration, National Oceanic and Atmospheric Administration. 128 pp. v Contents Acronyms and abbreviations..................................................................................................................vii Introduction ..............................................................................................................................................................ix -
Oriem Catalogue
December 2020 Edition Everything. Everywhere. Everytime. Mesh Bar Concrete Bar & Mesh Fitments Fitments We offer premium service and With three locations across Fitments have proven to be a range of concrete options to Sydney metro we’re sure to have a rushed item in the steel the industrial, commercial and your orders covered when it reinforcing industry, for this residential market. From owner comes to Mesh and Bar. All sizes reason most sizes of Lbars, Products builders, to large managed stocked in all locations, there’s Zbars, and ligatures are a Construction projects, you can think of us as no order we couldn’t handle. No standard off the shelf item. an extension of your business. job too big, no job too small. Reinforcing Reinforcing Everything you need. Construction Reinforcing Expansion & Accessories Products Accessories Jointing Mesh Page 4 Did you know Oriem carry a full Scheduled and included on all Being a reseller of the leading range of construction products take-offs, accessories as per brands, there’s nothing in Jointing Bar Page 8 manufactured by market job specifications are taken into this area we couldn’t help Expansion & Fitments Page 12 leaders. From messy clean- consideration, quantified and you with. Often expansion ups to stunning architectural quoted. Relieving this pressure and jointing options can be Construction Products Page 20 floors we got it covered. Repair from our customers gives them the make or break of project Reinforcing Accessories Page 130 mortars, self-levellers, polish to time to concentrate on more deadlines, speak to us with mixes, silicon’s and epoxy’s, our important things on the project how we could help you avoid Decorative Expansion & Jointing Page 148 Oriem Product Catalogue has and allowing us to do what potential road blocks and Decorative Page 178 our full list of products available we do best, being a one stop point you in the right direction Foundation Works & Slab Types Page 196 to you. -
The Arup Journal
THE ARUP JOURNAL \ 50TH ANNIVERSARY ISSUE~lt~ I Vol. 31 No.2 Editor: David J . Brown Front cover: 2/1996 Art Editor: Johannesburg Stadium Published by Desmond Wyeth FCSD (Photo: James Burland) THEARUP Ove Arup Partnership Deputy Editor: Back cover: 13 Fitzroy Street Helene Murphy London W1P 680 Brisbane Convention and Exhibition Centre Editorial: (Photo: Patrick Bingham Hall} Tel: +44 (0)1716361531 Tel: +44 (0)171 465 3828 JOURNAL Fax: +44 (0)171 580 3924 Fax: +44 (0)171 465 3716 0resund Link image: Nigel Whale Editorial This is the second of two special numbers of The Arup Journal to celebrate the 50th anniversary of the founding of the firm . Issue 1/1996 was de voted to recent projects in Brita,in and Ireland, in both of which countries Ove Arup started his consulting engineering practice simultaneously in 1946. Over the ensuing half-century, the work of the organisation he created has expanded 3 geographically and diversified into new fields of 31 activity to an extent beyond anything he could Brisbane have envisaged at the outset. This second cele Saving Convention and bratory Arup Journal includes recent projects in a landmark - Exhibition Centre five continents - North America, Europe, Asia, California style Ian Ainsworth Africa, and Australasia. The work described and Catherine Wells Tristram Carfrae illustrated here covers many different dis Bill Short ciplines, ranging from 'traditional' structural engineering in widely varied forms to civil engi neering works on the most massive scale; from the creation of energy-efficient internal building environments to the sophisticated analysis of a 11 single structural detail to help withstand earth 34 quakes; and from the architectural design and lnventure Place, engineering of a new stadium celebrating a City of Hope: Akron, Ohio reborn nation to planning a visionary bridge link Steel moment Raymond Crane between two Scandinavian countries.