Shrink-Wrapping.Pdf
Total Page:16
File Type:pdf, Size:1020Kb
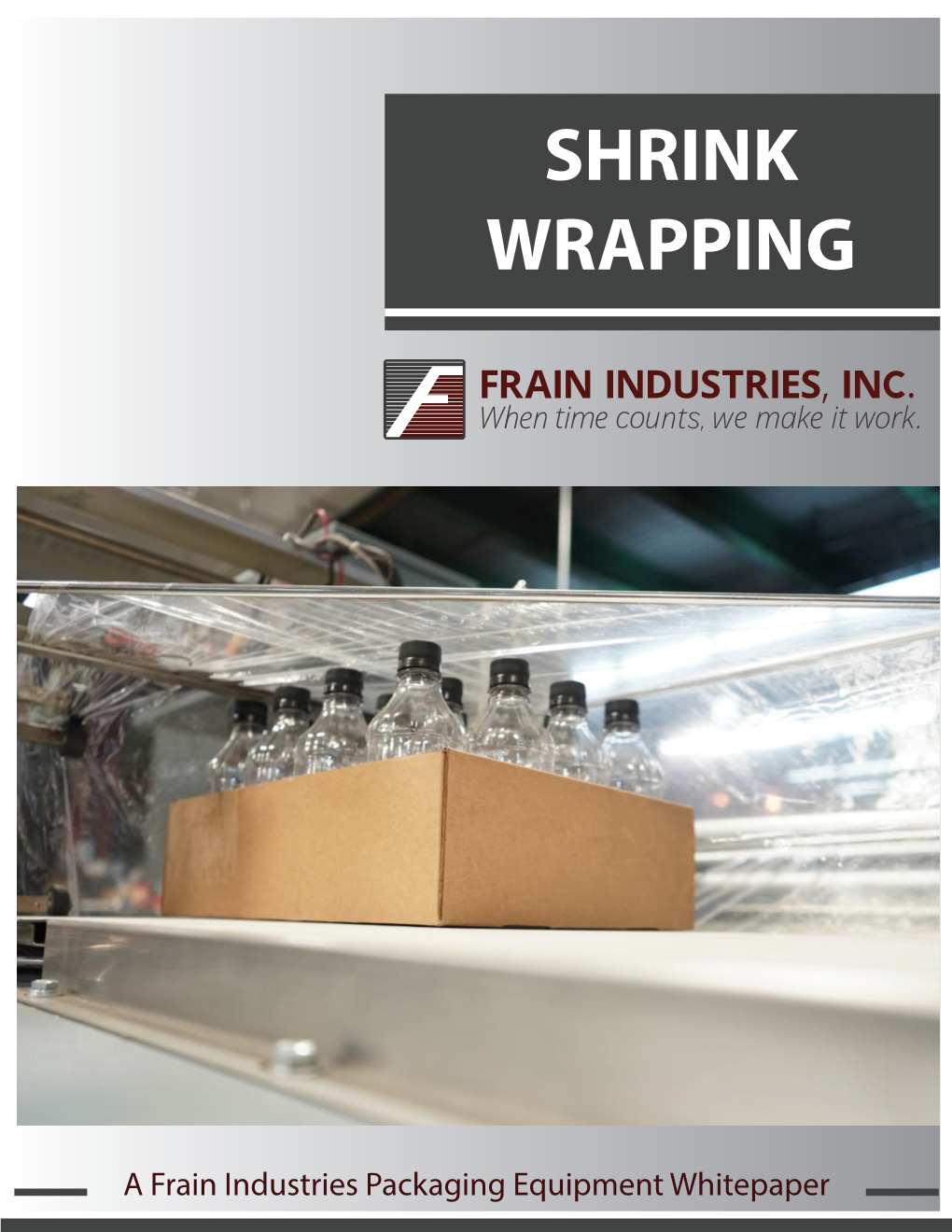
Load more
Recommended publications
-
Shrink Wrap Packaging
Shrink Wrap Packaging Versatile Shrink Wrap Solutions pacmachinery.com Shrink Packaging Basics Shrink packaging encapsulates a product with- in a tightly adhering layer of film. The process may Clamco 6800CS Side Sealer be accomplished by hand, or by using automatic or Intermittent motion, automatic side seal shrink wrapper semi-automatic packaging equipment. Creating a that offers exceptional return on investment. strong seal in the film is the first step. To achieve this, a hot knife or hot wire is pressed against the film to weld the seal together. The seal process has three variables: time, temperature, and pressure. Each may be adjusted to suit different film types. Once sealed in a film envelope, the package is passed through a heated shrink tunnel. When heated, the film softens and expands, and as the film cools it shrinks tight. The package exits the tunnel wrapped in a taught, secure, attractive film. There are several films from which you may Clamco 6700GLX Automatic L-Bar Sealer choose. Polyethylene is often used for bulk packaging; Outstanding speed, throughput and performance. Sealer Polyolefin is common in retail applications where allows for fast setup, alignment, and product transfer. crystal clarity is important. Polyvinyl Chloride (PVC) can be used as a pre-formed sleeve that is placed around a package and shrinks to conform. Ideal for bundling multiple parts in one secure package, shrink wrapping enhances visual appeal, maintains quality, and protects against tampering. Specifications 6700GLX 6800CS Speed (up to) 40 pkg/min 70 pkg/min Seal length (side) 18” 19.75” Seal length (front) 23” unlimited Maximum film width 23” 23.5” Maximum product height 7.5” 7.85” Sleve Wrappers Automatic Shrink Systems 7002ASW Automatic Sleeve Wrapper With ever-increasing production demands, Clamco This versatile automatic, sleeve wrapper-bundler can be used for meets the need with a family of automatic, high-speed, wrapping a wide range of products, from trays to cartons or bottles. -
Optimising High-Speed Shrink Wrapping of Frozen Pizzas
34 processing & packaging Optimising high-speed shrink wrapping of frozen pizzas Palermo’s Pizza’s high-speed shrink wrapping line is capable of side-sealing 150 frozen pizzas per minute with consistent high quality seals and near zero defect rate – 50% faster throughput than conventional side-seal frozen pizza shrink wrap lines. Frozen pizza remains one of the intact during wrapping. These method is that pizza toppings will most ubiquitous foods in the ingredients tend to shift around frequently fall underneath where typical American household. and fall to the bottom of the shrink the seal is being made, and Convenience, low price and a bag before sealing. compromise the integrity of the continually growing assortment of Additionally, frozen pizza being a seal. When the wrapped pizza options have made frozen pizza a low profile product has a high comes out of the tunnel, the lap favourite heat-and-serve choice capability for shingling while seal can be loose or open, but it is for households constrained by time travelling back-to-back on the very hard to detect. Usually it is and budgets. infeed conveyor before entering the customer who discovers that the pizza According to the American Frozen the wrapper. Shingling prompts they purchased has not been secu Food Institute, 66% of households poor infeed registration, resulting rely sealed. in the United States consumed in missed flights, double product To achieve a better quality seal on frozen pizza in 2010. With total bagging and broken crust. When frozen pizzas, food processors sales reaching US$3.2 billion running at high speeds, such as have utilised continuous motion (USD) in that year, this accounts 100 pizzas per minute, most infeed side-seal shrink wrappers. -
21 Tips for Troubleshooting Shrinkwrap & Equipment
Help for Diagnosing Shrink Packaging’s Leading Profit Busters From bad seals to burn-through, this handy guide It’s all part of our commitment to deliver shrink helps you address shrink packaging’s most common packaging’s best answers…the best experts…and the film/equipment issues. best bottom line. But don’t feel like you need to go it alone! Clysar SHRINK HELP HOTLINE: distributors and their trained field service technicians 1-888-4-Clysar are available 24/7 to support you with unrivaled Clysar supports distributors technical expertise. Call them to: and customers with technical • Troubleshoot reoccurring operating problems field specialists located and turn them into cost-saving solutions. throughout the country. • Transform profit-eating rejects into beautiful These knowledgeable display packages. advisors have years of experience troubleshooting • Fast-track new brand packages or film/equipment in thousands of shrink start-ups. operations, and are available • Add speed or capabilities to your existing shrink to provide technical operation. consultations via phone or • Improve uptime with preventive maintenance, on-site. training and more. WHAT TO CHECK WHEN GOOD SEALS GO BAD IS THE PROBLEM THE MACHINE OR THE PACKAGE? TIP #I: TIP #2: Start with the Do the One-Minute Big Three Seal Test 99% of all shrink packaging problems come down to three basic issues: 1. Temperature (too hot/cool) 2. Time (too much/little) 3. Pressure (incorrect seal pressure and tension) If you can correct these shrink fundamentals, you’re on your way to beautiful, trouble-free packages. The following tips give you more details on specific Here’s a quick test to help you determine if a bad actions you can take. -
Food Packaging Technology
FOOD PACKAGING TECHNOLOGY Edited by RICHARD COLES Consultant in Food Packaging, London DEREK MCDOWELL Head of Supply and Packaging Division Loughry College, Northern Ireland and MARK J. KIRWAN Consultant in Packaging Technology London Blackwell Publishing © 2003 by Blackwell Publishing Ltd Trademark Notice: Product or corporate names may be trademarks or registered Editorial Offices: trademarks, and are used only for identification 9600 Garsington Road, Oxford OX4 2DQ and explanation, without intent to infringe. Tel: +44 (0) 1865 776868 108 Cowley Road, Oxford OX4 1JF, UK First published 2003 Tel: +44 (0) 1865 791100 Blackwell Munksgaard, 1 Rosenørns Allè, Library of Congress Cataloging in P.O. Box 227, DK-1502 Copenhagen V, Publication Data Denmark A catalog record for this title is available Tel: +45 77 33 33 33 from the Library of Congress Blackwell Publishing Asia Pty Ltd, 550 Swanston Street, Carlton South, British Library Cataloguing in Victoria 3053, Australia Publication Data Tel: +61 (0)3 9347 0300 A catalogue record for this title is available Blackwell Publishing, 10 rue Casimir from the British Library Delavigne, 75006 Paris, France ISBN 1–84127–221–3 Tel: +33 1 53 10 33 10 Originated as Sheffield Academic Press Published in the USA and Canada (only) by Set in 10.5/12pt Times CRC Press LLC by Integra Software Services Pvt Ltd, 2000 Corporate Blvd., N.W. Pondicherry, India Boca Raton, FL 33431, USA Printed and bound in Great Britain, Orders from the USA and Canada (only) to using acid-free paper by CRC Press LLC MPG Books Ltd, Bodmin, Cornwall USA and Canada only: For further information on ISBN 0–8493–9788–X Blackwell Publishing, visit our website: The right of the Author to be identified as the www.blackwellpublishing.com Author of this Work has been asserted in accordance with the Copyright, Designs and Patents Act 1988. -
The Brand Owner's Guide to Shrink Sleeves
THE BRAND OWNER’S GUIDE TO SHRINK SLEEVES THE BRAND OWNER’S GUIDE TO SHRINK SLEEVES Shrink sleeves — if designed, printed and applied correctly — promise countless benefits to your brand: Product differentiation, 360-degree branding, improved appearance retention and maximum shelf impact. While maximizing shelf impact is the primary value-driver shrink sleeves provide to your total packaging system, they also bolster your container walls (allowing for the use of lightweight product containers) and enable easy incorporation of tamper-evident elements. And as technology matures and evolves, more and more premium beverage brands, personal care products and performance nutraceuticals are leveraging shrink sleeve bottle labels for enhanced shelf appeal. If you’re a brand owner considering sleeves for one of your product lines, this guide is a good place to start. It will answer questions like: • Why are brands in so many markets switching to sleeves? • What are some common applications? • What factors impact shrink sleeve costs? • How do I prevent graphics distortion on my shrink sleeves? Let’s get started. 2 THE BRAND OWNER’S GUIDE TO SHRINK SLEEVES Why are brands in so many markets switching to sleeves? Right now, improvements in shrink sleeve technology are fueling popularity, and popularity is fueling research into further improving capabilities. That’s a big reason shrink sleeve labels are one of the fastest-growing segments of the labeling industry, boasting an estimated annual growth rate of 6.5% over the next five years. Today, we’re able to engineer shrink sleeves to contour around almost any container shape, with enhanced abrasion, moisture and product resistance when compared to a surface printed label. -
Complete Chemical Plants for Sale for Shampoo, Toothpaste, Hair Oil
LID-0007536 - Complete Chemical Plants For Sale For Shampoo, Toothpaste, Hair Oil Etc Published on: 11 Aug, 2018 Category: Chemical and Pharmaceutical Machinery Location: Gujarat, India Specifications Overview Quantity Available : 1 Category : Chemical and Pharmaceutical Machinery Frequency : 50 Hz Sub-Category : Other Chemical and Pharmaceutical Machinery Phase : 3 Manufacturer : Indian Make Year : 0 Condition : Good Status : Decommissioned Description Complete Chemical Plants For Sale For Shampoo, Toothpaste, Hair Oil etc Plant is in Good condition Plant is manufactured in INDIA >>This Plant Includes following Machines:- SR DESCRIPTION OF GOODS QTY NO. TOOTH PASTE FILLING MACHINE 1 Paste Filling & Seeling Machine 65 Pcs/Min 2 2 Automatic Tube Filling Machine with Tube Holder, Heating Nozzles, S.S. 316 dosing cylinder, 0- 1 9 female stereos 3 Fully automatic tube filler 120 gan equipped with hot air sealing unit for Lami/Plastic tube 2 4 Fully automatic tube filler 120 gan equipped with hot air sealing unit with One Tube Size Parts 2 5 Fully automatic tube filler 120 gan equipped with hot air sealing unit with One Tube Size Parts 1 (Spring Dell) 6 Twin Head Lami Tube Filling Machine with One set of change parts for sealing 50 g. tubes 1 complete with S..S Covers, Tube Orientation device, Extra for S.S. 316 contact parts, extra change parts for 100g. Tubes. Tube holding cups, s.s. filling pump, hot air nozzle 70 Pcs/Min. 7 Twin Head Lami Tube Filling Machine with One set of change parts with S..S Covers, Tube 1 Orientation device 2 sets, Extra for S.S. -
Vacuum Packaging
Packaging as it Relates to Core Storage and Preservation What follows is an attempt to synthesize current information from a wide variety of sources into a useful guide to methods of core storage and preservation. It must be stressed that the focus of the packaging industry is twofold. The first is the relatively short term preservation of, mostly, food and medical products. The second is packaging for protection and display purposes. Clearly, neither of these industries address the specific needs and requirements of IODP, so we must be creative and eclectic in our selection of the most suitable products for our application. Moreover, we must be actively involved in the research, testing and development of new products and methods by partnership/involvement with other institutions, so that IODP can be at the forefront of this technology as befits our ethos. Section 1 - Vacuum Packaging Vacuum packing (or vacuum sealing) is a form of packaging that involves the removal of air (and sometimes its replacement) from a pouch or plastic container. Vacuum packaging provides several benefits: protection against dehydration; barrier against air or moisture; tamper evident protection; compressed packaging for fragmented cores; protection from dust and moisture. Types of Vacuum Sealing Equipment Non Chamber Vacuum Sealers These units vacuum and seal the pouches externally. Some units also come equipped with special external nozzles to allow for the vacuum packaging using plastic containers. Non Chamber Vacuum sealers are meant for low volumes, and are suitable for vacuum sealing products that have little or no moisture. However some units do have special collectors for products that have excess moisture. -
Table of Contents
1 TABLE OF CONTENTS Heat Shrink Wrap 4 - 16 Polyole n Shrink Rolls 5 - 11 Polyole n Shrink Bags 11 PVC Shrink Rolls 12 - 13 Polyethylene Shrink Bundling Rolls 13 PVC Shrink Tubing 14 PVC Shrink Bags 15 - 16 Shrink Wrap Machines 17 - 30 Heat Sealers 18 -19 Heat Guns 19 I Bar Sealers 20 - 21 L Bar Sealers 21 - 23 Chamber Shrink Wrap Machines 24 - 25 Combo Shrink Wrap Machines 25 - 27 Shrink Tunnels 27 - 30 Shrink Bundling Machines 31 - 32 Shrink Bundling Tunnel 32 Auto Shrink Bundler Combo 33 - 34 Conveyors 35 - 36 Rotary Conveyors 35 Skatewheel Conveyors 36 Gravity Conveyors 36 Belted Infeed Conveyors 37 3ft. Belted Infeed Conveyors 37 6ft. Belted Infeed Conveyors 37 Pallet Stretch Film 39-53 Hand Stretch Film 40 - 44 Extended Core Stretch Film 44 - 45 Bundling Stretch Film 46 - 47 Machine Stretch Film 48 - 53 Stretch Film Dispensers 54 - 55 Stretch Wrap Machines 56 - 64 Packaging Tape 65 - 69 Hand Packaging Tape 63 - 67 Tape Dispensers 68 Machine Packaging Tape 69 Tape Machines 70 3 1-800-441-5090 | 4781 Highway 319 West · Austin, Arkansas 72007 TABLE OF CONTENTS Strapping 71-76 Machine Polypro Strapping 72 - 73 Hand Polypro Strapping 74 Hand Polyester Strapping 75 Strapping Kit/Buckles 76 Strapping Machines 77 - 78 Laundry Film 79 Laundry Wrapping Machine 80 Perforated Plastic Cling & Shrink Rolls 81 - 82 Poly Bags & Tubing 83 - 96 Poly Bags 84 - 93 Poly Tubing 94 - 96 Poly Sheeting 97 - 98 Pallet Covers 99 - 100 Vacuum Packaging 101 - 112 Vacuum Bags 102 - 105 Black Vacuum Bags 106 Vacuum Zipper Bags 107 Notched Vacuum Bags 107 Meat Vacuum Bags w/Black Background 108 3 Mil Vacuum Tubing 108 Vacuum Sealers 110 - 112 Food Packaging 113 - 116 Aluminum Foil Rolls & Sheets 113 - 116 Food Cling Wrap 117 Meat Film & Machines 118 - 119 4 1-800-441-5090 | 4781 Highway 319 West · Austin, Arkansas 72007 POLYOLEFIN SHRINK WRAP What is Polyole n? (Poly·ole· n) is a plastic polymer, the root word ole n refers to any member of the alkene series. -
Damark Packaging Inc
OPERATIONS MANUAL MAXIPAK SHRINK SYSTEM PLEXPACK CORP. 2045 Midland Avenue, Toronto, ON, Canada M1P 3E2 Phone: 416-609-8011 Toll Free: 1-800-265-1775 Fax: 416-298-4328 [email protected] www.damarkpackaging.com 1 TABLE OF CONTENTS SECTION PAGE # 1 Introduction 3 2 Initial Inspection 4 3 Safety and Warranty 5 4 Electrical Connections 7 5 Operation 8 6 Routine Maintenance 11 7 Trouble Shooting 14 8 Parts List 16 9 Electrical Schematics 17 2 SECTION 1 INTRODUCTION SHRINK PACKAGING Simply stated, shrink packaging is a method of combining, enhancing or protecting products in an attractive, economical way. The most versatile and widely used equipment in shrink packaging is the L-Sealer/Shrink Tunnel combination. Used together, these two machines form the normal system but it is important to remember that they can be used alone quite effectively using specific techniques. These various other forms of shrink packaging are too complicated for this brief summary, but can be explained by your Damark distributor. The L-Sealer utilizes a supply of centre folded film to form a loose fitting bag around a product. This process can be accomplished with an operator or, with more advanced Damark machines, completely automatically. From the L-Sealer, the package is either pushed or conveyed onto the Shrink Tunnel conveyor. Even on the simplest and least expensive Damark system, the Shrink Tunnel is completely automatic. The purpose of the Shrink Tunnel is to expose the film around the package to a flow of heated air (at a pre-set temperature) for a specific period of time. -
Packaging Machines & Supplies
PACKAGING MACHINES & SUPPLIES Interior Packaging Carton Closing Carton Marking Strapping/Tying Palletizing/Unitizing Stretch Wrapping Material Handling, Industrial Fastening & Supplies www.carlsonsystems.com www.midatlanticfasteners.com www.westerntool.com Our Company Serving the Packaging Industry Since 1947 Carlson Systems is a leading distributor of the most recog- Another acquisition occurred in 2013 nized brands of construction and packaging machines, tools with the addition of Western Tool and supplies in the industry – supported by our network Supply Company. Western Tool Supply of service and repair technicians. The company has evolved was founded in 1982, with its head- over the past 66 years to encompass over 60 locations in the quarters in Salem, Oregon. The United States and Mexico. addition of Western Tool Supply expanded Carlson Systems’ presence in the northwestern U.S. The companies were a This success story had its humble good fit because, like Carlson Systems, Western Tool beginning in Omaha, Nebraska, Supply had a strong devotion to customer satisfaction when in 1947, Carl and Julia through breadth of product, product expertise, and great Carlson founded Carlson Stapler order fulfillment, with the added benefit of tool and and Supply in the basement of equipment repair service. their home with nothing more than a $350 cash investment, a Focusing on fastening, packaging and product assembly used file cabinet, and their own systems, the offices and warehouses of Carlson Systems, enthusiasm. Mid-Atlantic Fasteners and Western Tool Supply serve thousands of customers across the country and into Mexico. A group of problem solvers, we provide ideas and solu- tions in both the products we offer and the methods we propose. -
TES Packaging Private Limited
+91-8048554036 TES Packaging Private Limited https://www.indiamart.com/tes-packaginghyderabad/ We are the manufacturer, supplier, exporter and trader of Banking Card Pouch, Education Document and many more. We also offer Automatic Shrink Packaging Solution. These products and services are provided at market leading price. About Us Commenced in the year 2006, our company Tes Packaging Pvt. Ltd. is a well known name in the market. We operate all our business activities from our headquarters located at Hyderabad, Telangana (India). We are the leading manufacturer, supplier, trader, and exporter of a wide range of products such as Banking Card Pouch, Bank Account Paper Accessories, Education Document, Mail Envelopes, Graphic Designing Accessories, Brand Wristband and more. Additionally, we are also the service provider of Printing Service. We exports upto 20 % of our products to Qatar, Australia, Bangladesh, Nepal and Kuwait. Tes Packaging Pvt. Ltd. believes in truth, to become the most trusted solution provider in the business of packaging and printing domain. It helps organizations improve their packaging efficiency, reduce packaging costs, supply quality packaging products and services from world class suppliers and provide designing services of our products range. The company has built relationships, make best effort to make them last and integrate itself in to their customer’s operations to become a partner-in-progress. Tes Packaging Pvt. Ltd. is managed by a team of young professionals who have expertise in printing and packaging domain -
Heidelberg Business Media Gmbh Verlag
D 51178; ISSN: 1438-9452 17.04.17 No.04 MAGAZINE FOR BOTTLERS AND BOTTLE-MAKERS 2017 IN THE AMERICAS, ASIA, EUROPE AND ALL AROUND THE PLANET PETplanet is read in more than 140 countries MARKETsurvey Palletising and shrink Page fi lm machinery 40 Page 56 Page 42 www.petpla.net APPLY A Perfect Match. If you‘re looking for outstanding closure solutions for your applications, don’t look any further: End-to-end expertise, inventiveness and state- of-the-art technologies enable us to develop ideal solutions for your projects. That’s how we guarantee you the perfect beverage closure. www.corvaglia.ch corvaglia_imageanzeigen_2016.indd 4 11.02.16 16:22 3 imprint EDITORIAL PUBLISHER Alexander Büchler, Managing Director HEAD OFFICE heidelberg business media GmbH Bunsenstr. 14 69115 Heidelberg, Germany Dear friends of phone: +49 6221-65108-0 fax: +49 6221-65108-28 PETplaner Insider, [email protected] Exciting things are in prospect at the NPE next year. Here are some EDITORIAL highlights. On May 7–11 2018, in Orlando, FL, USA , “the bottle zone“ Kay Barton (www.npe.org/bottlezone) will be taking place, for the fi rst time at the trade Heike Fischer Gabriele Kosmehl fair. With joint support from the SPI, drinktec and PETplanet Insider, all Michael Maruschke exhibitors will be focusing on the theme of plastic bottles. Previously, bot- Ruari McCallion tles were spread out over the entire site, but now the visitor interested in Waldemar Schmitke this sector will be able to fi nd everything under one roof. Highlighting this Anthony Withers fresh approach, the NPE has now published, together with the Plastics Association, a market analysis entitled “Plastic bottles today - Innovating to WikiPETia.info reach today’s consumer”.