Oxy-Gasoline Torch
Total Page:16
File Type:pdf, Size:1020Kb
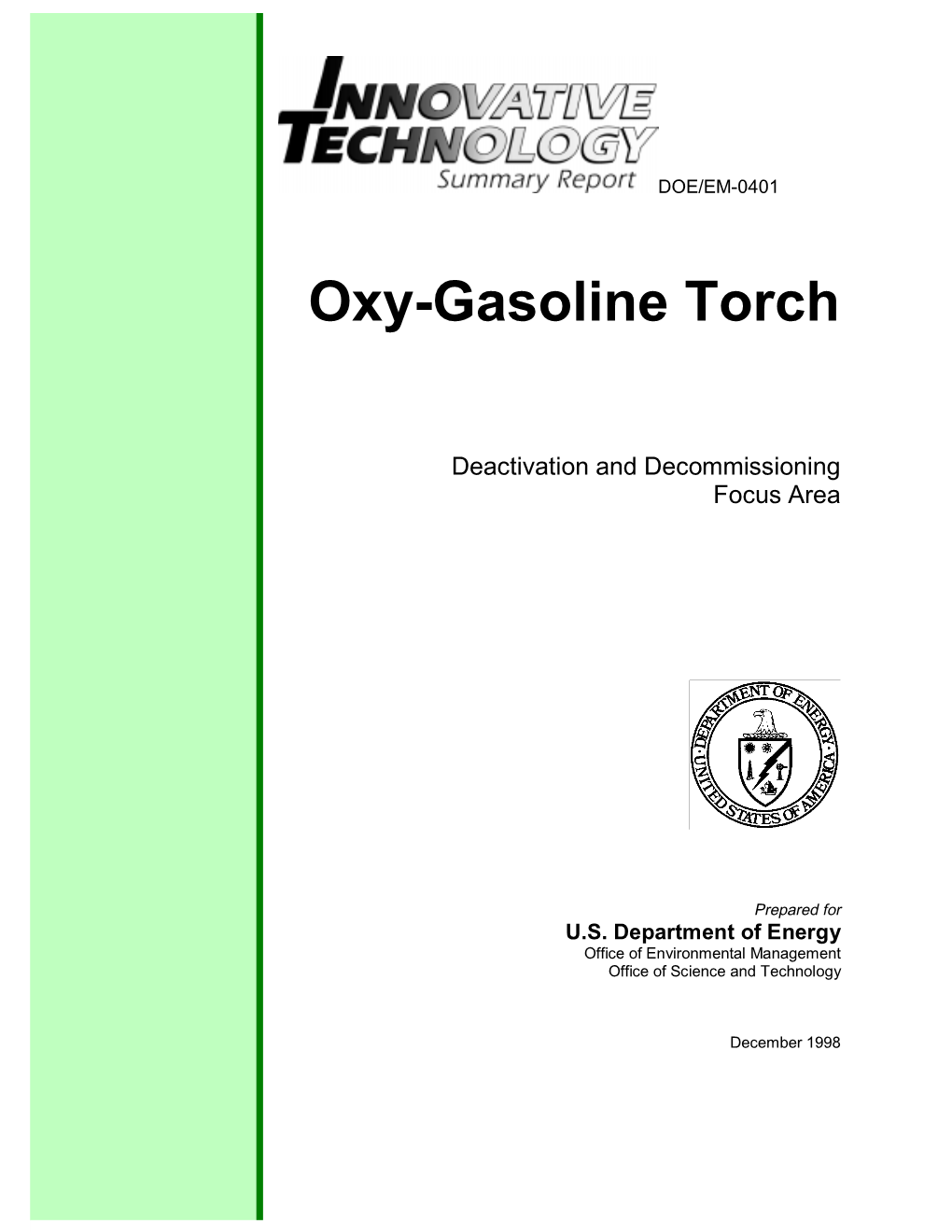
Load more
Recommended publications
-
Turner Brass Olympic Torch Collection
Turner Brass Olympic Torch Collection 2006.009 DeKalb County History Center Sycamore, IL 60178 Descriptive Summary Creator: Tracy Brindle, Intern Date Created: June 2013 Title: Turner Brass Olympic Torch Collection Date Span: 1976-1996 Physical Description: Two record boxes: Turner Brass Collection Box 1 & 2 File folder in Map Case Drawer 04, Diagrams Administrative Information Restrictions: None Related Collections: 2001.6, 2003.014, 2004.176, 2004.177, 2004.178, 2004.180, 2004.181, 2004.182, 2004.382, 2004.402, 2005.06, 2005.457, 2005.462, 2005.669, 2006.121, 2007.20, 2008.29, 2008.31, 2008.58, 2008.77, 2008.97, 2009.051, 2009.103, 2009.119, 2010.116, 2011.51, 2010.117, 2011.079, 2012.012, 2012.015, 2013.010.05 Acquisition Information: Gift Preferred Citation: Turner Brass Olympic Torch Collection, Sycamore History Museum Archives, Sycamore, IL Collection Description Biographical/Historical Note: The Turner Brass Works was founded in 1871 by E.F. Turner on the north side of Chicago, IL. Several years later, the company was purchased by Charles Reckitt, who made arrangements for Tuner Brass to relocate to Sycamore in the fall of 1906. The factory, located on the south side of Sycamore at 821 Park Avenue, was completed in the summer of 1907. The True Republican 1 (Nov. 28, 1906) reported that it was the first of its kind in terms of industry to appear in Sycamore. At the time, there were 230 workers employed in the factory. The company relocated to Sycamore for a bonus of $10,000. The company issued around 30 catalogues, including “Automobile Cycle and Power Boat Specialties,” “Foot and Pressure Pumps,” “Repair Parts for Electric Arc Lamps,” “Hardware Specialties,” “Brass Fixtures and Lantern,” “Gasoline Vapor Lamps,” “Machinery Name Plates,” “Gasoline Thermo-Light Outfit and Dental Appliances.” Their catalogues boasted that they were the “largest concern in the world manufacturing these goods.” The employees held a Reception and Ball and invited the people of Sycamore as their guests. -
Industrial Equipment Catalog
Outfits: 4-7Cutting Attachments: 8-9 Handles: 9-16 Classic . .4 V-Series . .8,9 V-315C/V-100C . .9,10 Port-A-Torch . .5 73-3 . .8 Model 43-2 . .10,11 Cutter-Pac . .5 72-3 . .8 Model 85 . .10,12 Shielding Gas Kit . .6 39-3F . .8 Model 18-5 . .10,13 V-Series . .6,7 49-3F . .8 Model 50 . .10,14 71-3 . .8 Model 16 / 19-6 . .10,15 Model 15 . .10,16 Welding, Brazing & Heating Tips Machine Cutting: 36-38 FlashBack Arrestors: 39 Acetylene Welding, Brazing, Heating Tips 31 Straight Line Cutter . .36 Flash Back Arrestors, Quick Connectors, Alternate Fuel Tips, Brazing & Light Heating 33 Model 80 Jumbo . .36 Check Valves . .39 K-43, 89-3, 81-12 34 Model 98-6 & Accessories . .37 2290 HMP, 2290 H, 2393 Tip Tube, RBP-43 35 Machine Cutting Guide . .38 This year marks the 100th Anniversary of Welding's founder, Lorne Campbell, Jr., Harris Calorific. From a small shop on served as President until the 1950's when Cleveland Ohio’s west side to our high-tech Clarence Taylor assumed the position. factory in Gainesville, Georgia, Harris History is as impressive as the products we produce. After World War II, the company found new markets for its products in research HARRIS CALORIFIC CO., a pioneer in the laboratories, aircraft and missile production of gas welding and cutting manufacturers. Under Clarence Taylor, apparatus was founded by John Harris, who Harris expanded national distribution, discovered the oxy-acetylene method of developed new equipment, stepped up cutting in 1899 while conducting research on advertising, and established subsidiaries the manufacture of synthetic rubies. -
HOT SHOT (Propane Torch) Model SPC-500
OPERATING INSTRUCTIONS Model # AND OWNER’S MANUAL SPC-500 READ INSTRUCTIONS CAREFULLY: Read and follow all instructions. Place instructions in a safe place for future reference. Do not allow anyone who has not read these instructions to assemble, light, adjust or operate this tool. HOT SHOT (Propane Torch) Model SPC-500 05/13 Revision L2 #72615 Read and understand instructions before use! FOR YOUR SAFETY! Retain this information for future reference. If you smell gas: (Under certain conditions odor may fade (Refer to page 6) - Shut off gas to the device. - DO NOT try to light appliance. - Extinguish any open flame. - Check the device for leaks using soapy water. - DO NOT attempt to relight the device until all leaks are repaired and there is no gas smell. DO NOT use this device in areas where gasoline or other liquids having flammable vapors are stored or used. CAUTION: This device is intended for outdoor use only. NEVER direct torch flame toward hose or gas tank. DO NOT leave torch unattended while in operation. DO NOT stand or prop the torch on the burner end while in operation. Always use the striker provided. Never use a match or lighter to ignite torch. DO NOT apply heat or flame to tank to check for leaks or to increase gas pressure. DO NOT lift tank by the valve. When not in use the gas should be turned off at the LP gas tank(s). CAUTION – In daylight, torch flame is barely visible. DO NOT place hand or body part in the path of the flame while lighting or operating torch. -
13849Q Soft Flame Propane Torch.Indd
Part #13849 SOFT FLAME PROPANE TORCH INSTRUCTIONS The Eastwood Soft Flame Propane Torch is a precision-engineered, professional quality, Propane ATTACHING TO PROPANE OR MAPP GAS CYLINDER or Mapp Gas-powered torch incorporating a Stainless Steel fl ame tube and nozzle for rugged use and long life. Provides a soft, dispersed fl ame suitable for use with body solder and plastic forming. Fits • Obtain a 1 lb. cylinder of good quality Propane or Mapp gas fuel. standard 1 lb. propane and Mapp gas cylinders. Features a built-in 360° regulator to allow for fully • Be sure the regulator/fl ame control knob is securely closed. inverted torch use and battery-free piezoelectric ignition. • Fully read and understand manufacturer’s instructions on gas cylinder before using. Propane and Mapp Gas are highly fl ammable. Do not allow near spark or fl ame sources. • Attach to cylinder in a well ventilated area. WARNINGS • Used with highly fl ammable propane or Mapp gas fuel under pressure. Gas should be kept OPERATION away from spark and fl ame sources. Do not store or expose to temperatures above 100°F or prolonged sunlight IGNITION • Follow all gas cylinder manufacturer’s directions when attaching torch unit to cylinder. • Open the regulator/fl ame control knob about ½ turn in a counter-clockwise direction then • Always wear protective eye gear and fl ame resistant gloves when using the torch. quickly push in sharply on the ignition button. This will ignite the fl ame. • The heated tip and fl ame can reach temperatures in excess of 2300°F. Do not allow tip or fl ame • Rotate the regulator/fl ame control knob in a counter-clockwise direction further to achieve a to come in contact with exposed fl esh or fl ammable surfaces. -
Instant on Trigger Start Torches – Professional Series Cutting
Fuel Gas Equipment Bernzomatic Vendor Code: BOM Torches Cutting, Welding and Brazing Torch Kit POWERCELL™ Fuel System • Oxygen/ MAPP® The Bernzomatic trigger start torch kit with POWERCELL™ fuel system packs all • Hazardous material charges may apply. of the power and performance of a full size torch at half the size. • Kit includes burner wand, hose, oxygen regulator, fuel gas valve cylinder It is the most compact, lightweight and easy 1 stand, MG9 16 oz. MAPP® Gas cylinder, OX9 1.1 cubic foot oxygen cylinder, to use propane torch available anywhere. spark lighter and 5 brazing/welding rods. Use it to solder or thaw copper pipe. Part No. OXOKC Loosen rusted bolts. Strip paint. • Hazardous material charges may apply. • Large diameter fl ame is perfect for multiple applications. • Adjustable fl ame control. • Trigger start for easy lighting. • Easy to reach tight spaces. Part No. TSPC8KC- 6 pack POWERCELL™ fuel cylinders Part No. 0PC8- 6 per carton Instant On Trigger Start Torches – Professional Series Bernzomatic’s fi nest torches feature instant on trigger start igniters and are regulated for cold weather use. All products are fast, easy to use and are considered ideal for all types of soldering and brazing projects. Product features include stainless steel burn tubes for compatibility with both MAPP® and propane gases. Trigger-Start Flame Control Torch Trigger-Start Torch • MAPP®/ Propane • MAPP®/ Propane • Pressure regulated for optimal gas consumption, • Instant On-Off trigger increases fuel savings and convenience. heat output and to burn upside down. • Lock button keeps torch lit for fi nger-free use. • Instant On-Off trigger improves fuel savings and convenience. -
Torch-Applied Roof System Safety Student Manual Certified Roofing
Certified Roofing Torch Applicator Program Torch-applied Roof System Safety Student Manual 03/2020 Certified Roofing Torch Applicator Program—Torch-applied Roof System Safety Student Manual National Roofing Contractors Association Midwest Roofing Contractors Association 10255 W. Higgins Road, Suite 600 2077 Embury Park Road Rosemont, IL 60018-5607 Dayton, OH 45414 (847) 299-9070 Toll Free: (800) 497-6722 Fax: (847) 299-1183 Fax: (937) 278-0317 Email: [email protected] Email: [email protected] www.nrca.net www.mrca.org Published by the National Roofing Contractors Association and Midwest Roofing Contractors Association ©2018 by the National Roofing Contractors Association and Midwest Roofing Contractors Association All rights reserved Published 2018 Printed in the United States of America No part of this publication may be reproduced or distributed in any form or by any means or stored in a database or retrieval system without prior written permission of the publishers. 03/2020 Certified Roofing Torch Applicator Program Torch-applied Roof System Safety Student Manual 03/2020 Certified Roofing Torch Applicator Program—Torch-applied Roof System Safety Student Manual Table of Contents Preface Certified Roofing Torch Applicator Program ................................................................................................................. i Foreword ....................................................................................................................................................................... ii Purpose ......................................................................................................................................................................... -
Welding and Cutting Torches - Light Version Page 2
Welding and cutting torches - light version page 2 Welding and cutting torches - standard version page 4 3-tube cutting torches and attachments (nozzle mix type) page 7 Pressure regulators page 8 Safety devices/ quick couplings page 11 Accessories page 12 Complete soldering, welding and cutting outfits / cylinder trolleys page 14 Propane equipment page 16 -1- Welding and cutting torches - light version The light version of our welding and cutting torch is suitable for all welding applications up to 14 mm material thickness and cutting up to 60 mm material thickness. The equipment is available as complete sets or as individual parts and, with the wide range of accessories, adapts to practically all requirements. The equipment is light in weight, easy to handle and of an attractive nickel- plated design. Art. 3901 Light handle (275 g) in forged brass, nickel plated, with red moulded handle and fixed hose connectors, 5 or 6 mm. This handle accomodates all welding, cutting and heating leads listed below (spigot diameter 14 mm) Art. 3901 Art. 3909 to Art. 3916 The handle is also available with screwed hose connections, 5 or 6 mm Art. 3902 Welding head no 1 0,5 – 1 mm Art. 3911 Welding head no 2 1 – 2 mm Art. 3912 Welding head no 3 2 – 4 mm Art. 3913 Welding head no 4 4 – 6 mm Art. 3914 Welding head no 5 6 – 9 mm Art. 3915 Welding head no 6 9 – 14 mm Art. 3916 The heads for the light handle are also available for the following fuel gases: propane, hydrogen and natural gas. -
Flame Flame Tt Ools & Ools & Aa Ccessoriesccessories
Air-Acetylene Equipment FEATHER FLAME ACETYLENE KIT TARGET® TIPS NGA3 • Very hot turbine flame • Tips have a filter and removable orifice • Tips fit NGG-4 handle • Interchangeable with other quick disconnect style tips • Unique mixer design cuts brazing time by 30% over conventional tips • Adjustable tips that do not burn up • Made of heavy stainless steel and brass Economically priced air fuel kit which has a tip design that produces Flame Soft Silver excellent flame characteristics for soldering and light brazing. Part No. Diameter (In.) Solder (In.) Solder (In.) CCESSORIES NGA2 1/4 1/8 to 1/2 1/8 to 1/4 CCESSORIES Contains NHA12 hose, NEA1G regulator, NAA1 handle and NBA4 Kit. NGA3 5/16 3/8 to 1 1/8 1/8 to 1/2 A A Part No. Tip Regulator Fitting NGA5 5/16 7/8 to 1 5/8 3/8 to 7/8 NKA37H NBA4 “B” Cylinder NGA8 3/8 1 1/8 to 2 5/8 5/8 to 1 1/8 NGA11 7/16 1 5/8 to 3 3/8 7/8 to 1 5/8 NGA14 1/2 2 1/8 to 4 1/8 1 1/8 to 2 1/8 TARGET® TORCH ACETYLENE KITS NGA32 3/4 3 1/8 to 6 1/8 1 5/8 to 4 1/8 EZE-LITE® TIPS OOLS & OOLS & T T NGA3L • Innovative spark igniting turbine flame tip ignites with the push of a button NKX4B • Interchangeable with other quick disconnect tips • Removable/cleanable orifice These kits feature the very hot compact adjustable Target® tips • Fits NGG4 handle for professional soldering and brazing applications. -
Propane Torch Model #MH500PT
OPERATING INSTRUCTIONS Model # AND OWNER’S MANUAL MH500PT READ INSTRUCTIONS CAREFULLY: Read and follow all instructions. Place instructions in a safe place for future reference. Do not allow anyone who has not read these instructions to assemble, light, adjust or operate this tool. Propane Torch Model #MH500PT MR. HEATER INC., 4560 W. 160TH ST., CLEVELAND, OHIO 44135 • 216-881-5500 04/03 Revision L1 #72615 Read and understand instructions before use! FOR YOUR SAFETY! Retain this information for future reference. If you smell gas: - Shut off gas to the device. - DO NOT try to light appliance. - Extinguish any open flame. - Check the device for leaks using soapy water. - DO NOT attempt to relight the device until all leaks are repaired and there is no gas smell. DO NOT use this device in areas where gasoline or other liquids having flammable vapors are stored or used. CAUTION: This device is intended for outdoor use only. NEVER direct torch flame toward hose or gas tank. DO NOT leave torch unattended while in operation. DO NOT stand or prop the torch on the burner end while in operation. Always use the striker provided. Never use a match or lighter to ignite torch. DO NOT apply heat or flame to tank to check for leaks or to increase gas pressure. DO NOT lift tank by the valve. When not in use the gas should be turned off at the LP gas tank(s). CAUTION – In daylight, torch flame is barely visible. DO NOT place hand or body part in the path of the flame while lighting or operating torch. -
Torches & Torch Kits
PROCORE — Torches & Torch Kits PCR/3842 MULTI-FUNCTION PEN TORCHES 3UHFLVLRQEXWDQHWRUFKNLWV(DVLO\UH¿OOHG$GMXVWDEOHÀDPHFRQWUROOHU3RUWDEOHFRPSDFWDQGOLJKWZHLJKW8VHVLQFOXGHVROGHULQJZHOGLQJKRWNQLIHFXWWLQJVPDOOSOXPELQJDSSOLFDWLRQV engraving, circuit board repairs, loosening rusted parts, and heating electrical connection •Includes case and interchangeable tips 30-70 WATT PRECISION PEN 30-70 WATT PRECISION PEN 25-80 WATT PRECISION PEN 30-120 WATT PRECISION PEN BUTANE TORCH KIT BUTANE TORCH KIT BUTANE TORCH KIT BUTANE TORCH KIT Includes: Includes: Includes: Includes: •30-120 watt precision pen torch •30-70 watt precision pen torch •30-70 watt precision pen torch •25-80 watt precision pen torch 6HOILJQLWLRQZLWKDGMXVWDEOHÀDPH Filters & Regulators 0DQXDOLJQLWLRQZLWK¿QJHUWLSDGMXVWDEOHÀDPH 0DQXDOLJQLWLRQZLWK¿QJHUWLSDGMXVWDEOHÀDPH 0DQXDOLJQLWLRQZLWK¿QJHUWLS $QWLÀDUHDQGZLQGUHVLVWDQWGHVLJQ •6 mL fuel tank capacity •11 mL fuel tank capacity DGMXVWDEOHÀDPH •High temperature up to 1300°C Air Accessories / Tire Service / Tire Accessories / Air •Soldering tip, hot blower tip, •Soldering tip, hot blower tip, polyfoam •11 mL fuel tank capacity •Portable, cordless, and lightweight – works polyfoam cutting tip, needle tip, cutting tip, needle tip, double sharp •Soldering tip, hot blower tip, polyfoam at any angle •Built-in stand •8 mL fuel tank double sharp tip, hot knife tip, rosin tip, hot knife tip, rosin solder coil, cap, cutting tip, needle tip, double sharp capacity with fuel level window solder coil, cap, integrated sponge, integrated sponge, and safety stand. tip, hot knife tip, rosin solder coil, cap, •Soldering tip, hot blower tip, polyfoam cutting and safety stand. Part No. 19-1024. integrated sponge, and safety stand. tip, needle tip, double sharp tip, hot knife tip, Part No. 19-1022. Part No. 19-1026. cap, integrated sponge, and safety stand. Part No. -
Precision Made Solder Ring Fittings Connect with Confidence Connect with Confidence
PRECISION MADE SOLDER RING FITTINGS CONNECT WITH CONFIDENCE CONNECT WITH CONFIDENCE With a wealth of expertise and the broadest range of solutions and systems on the market, Pegler Yorkshire’s Connect products mean you’ll complete your installation as seamlessly, efficiently and effectively as possible. TOTAL FUNCTIONALITY, COMPLETE EFFICIENCY Pegler Yorkshire’s range of Connect solutions offer innovatively designed, efficient and reliable products and systems that reduce installation time and cost without compromising quality, aesthetics or reliability. Our Tectite, Henco and XPress product ranges are designed to perform faultlessly in a variety of applications and environments – so you can always be sure to connect with confidence whatever your challenge. GLOBAL EXPERIENCE, COMBINED EXPERTISE With over 100 years of manufacturing and innovation combined with extensive industry knowledge and worldwide market experience, Pegler Yorkshire offers the most advanced and complete Connect & Control systems on a global scale. As one of Britain’s largest and most respected manufacturers and suppliers of products for the plumbing and heating industries, Pegler Yorkshire is confident we can provide you with all the connection, control and support your project needs. For more information visit www.pegleryorkshire.co.uk 2 CONTENTS 1.0 PRODUCT RANGE OVERVIEW The Yorkshire range 4-8 Standards, approvals and guarantees 9 2.0 PRODUCT RANGE DETAILS Pegler Yorkshire is pleased to be General range 10-29 associated with several influential industry organisations: -
Model 50100 500,000 Btu Propane Torch
Thank you for your purchase! We hope you enjoy your torch! Need a longer hose for your torch? Looking for other great Hot Max accessories for your torch or our other products? Check out our website for our current product offering. Idle Boost / Fuel Saver Valve Model 24206 Hot Max Extension Hoses Model 24200 - 10’ LP Hose or MODEL 50100 Model 24201 - 25’ LP Hose 500,000 BTU PROPANE TORCH Hot Max Garden Torch Model GTORCH KDAR Company 3671 New Town Blvd St. Charles, MO 63301 (636) 493-9920 M-F 8 AM to 5 PM, CST INSTRUCTION MANUAL www.hotmaxtorches.com MODEL 50100 PROPANE TORCH ASSEMBLY, TESTING, AND OPERATING INSTRUCTIONS TROUBLE SHOOTING PLEASE READ AND RETAIN THIS INFORMATION FOR FUTURE REFERENCE Problem #3 - The flame adjusting valve is not working. DO NOT OPERATE this torch unless you have been properly trained or are under the supervi- sion of someone in its proper use. Read and understand all instructions before attempting to Possible Solutions: use! 1. If you can not get full flow out of the torch with the flame adjusting valve FOR YOUR SAFETY! all the way open, then the POL safety valve has probably detected too much gas flow and restricted the gas flow. To reset the POL safety valve, turn the This device is intended for outdoor use only with adequate ventilation. LP gas cylinder valve completely off (clockwise), then open the flame This torch is designed for use with a vapor-withdrawal liquid propane (LP) gas cylinder 10 adjusting valve to release any pressure in the hose (or remove the POL pound size and larger with an OPD valve.