Feature Extraction with Discrete Non-Separable Shearlet Transform and Its Application to Surface Inspection of Continuous Casting Slabs
Total Page:16
File Type:pdf, Size:1020Kb
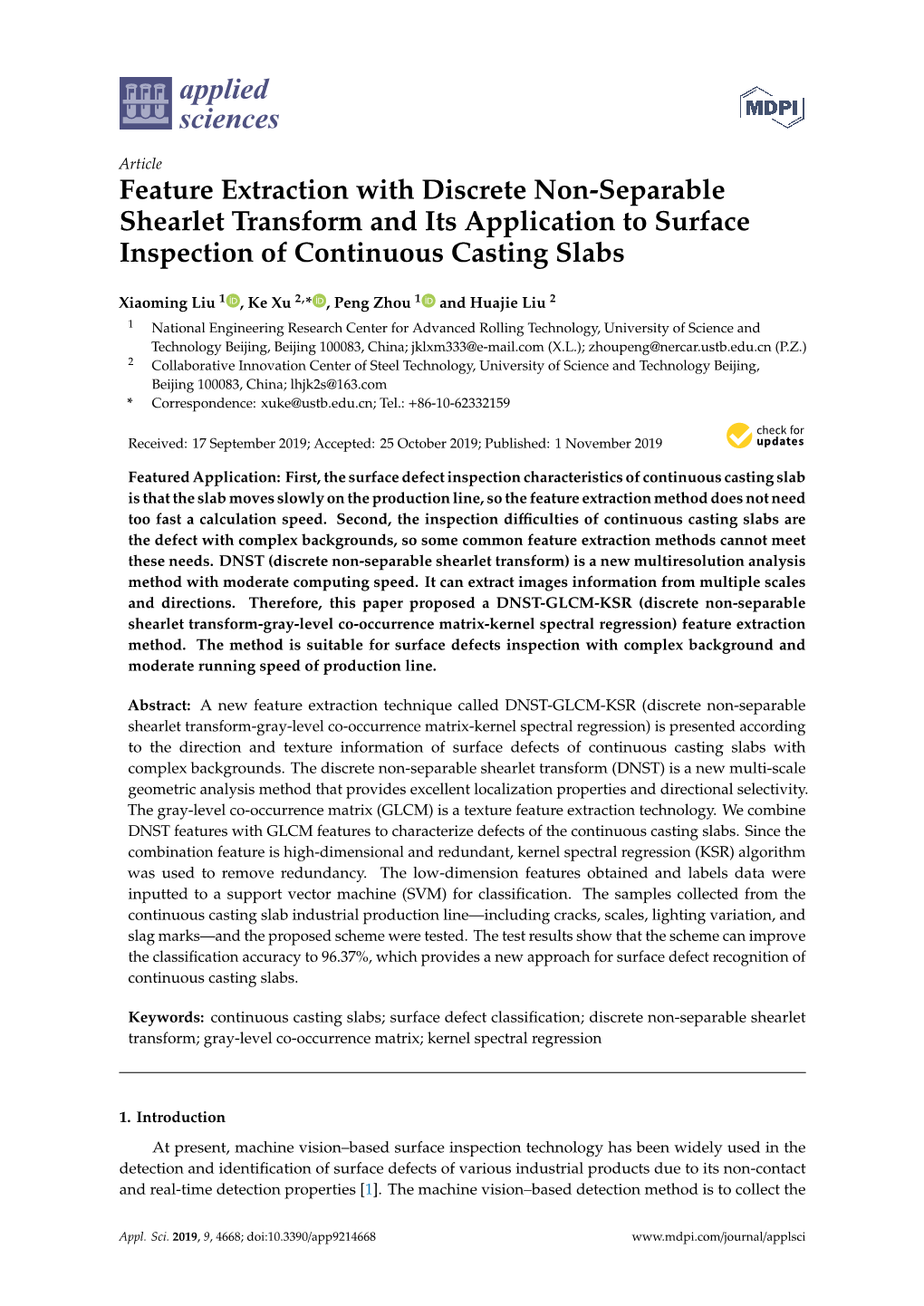
Load more
Recommended publications
-
Image Denoising Using Wavelet and Shearlet Transform
[Kumar et. al., Vol.5 (Iss.4: RACEEE), April, 2017] ISSN- 2350-0530(O), ISSN- 2394-3629(P) ICV (Index Copernicus Value) 2015: 71.21 IF: 4.321 (CosmosImpactFactor), 2.532 (I2OR) InfoBase Index IBI Factor 3.86 Recent Advances in Communication, Electronics & Electrical Engineering RACEEE - 17 IMAGE DENOISING USING WAVELET AND SHEARLET TRANSFORM 1 2 3 4 5 Bharath Kumar S , Kavyashree S , Ananth V Naik , Kavyashree C.L , Gayathri K.M 1,2,3,4 UG Students, Department of Electronics and Communication Engineering, School of Engineering and Technology, Jain University, Bangalore-562112, India 5 Assistant Professor, Department of Electronics and Communication Engineering, School of Engineering and Technology, Jain University, Bangalore-562112, India DOI: https://doi.org/10.29121/granthaalayah.v5.i4RACEEE.2017.3316 Abstract Image plays an important role in this present technological world which further leads to progress in multimedia communication, various research field related to image processing, etc. The images are corrupted due to various noises which occur in nature and poor performance of electronic devices. The various types of noise patterns observed in the image are Gaussian, salt and pepper, speckle etc. due to which the image is attenuated or amplified. The main challenge lies in removing these noises. We use various denoising techniques in removal of noise in order to retrieve the original information from the image. Wavelet transforms are one of the denoising algorithms used as conventional methods. This algorithm is used to capture the image along different directions in limited manner which becomes the main disadvantage of using this algorithm. In this work we propose a technique by integrating Wavelet and Shearlet transform which effectively removes the noise to the maximum extent and restores the image by edge detection which can be identified. -
Digital Shearlet Transforms
Digital Shearlet Transforms Gitta Kutyniok, Wang-Q Lim, and Xiaosheng Zhuang Abstract Over the past years, various representation systems which sparsely approximate functions governed by anisotropic features such as edges in images have been proposed. We exemplarily mention the systems of contourlets, curvelets, and shearlets. Alongside the theoretical devel- opment of these systems, algorithmic realizations of the associated transforms were provided. However, one of the most common shortcomings of these frameworks is the lack of providing a unified treatment of the continuum and digital world, i.e., allowing a digital theory to be a natural digitization of the continuum theory. In fact, shearlet systems are the only systems so far which satisfy this property, yet still deliver optimally sparse approximations of cartoon-like images. In this chapter, we provide an introduction to digital shearlet theory with a particular focus on a unified treatment of the continuum and digital realm. In our survey we will present the implementations of two shearlet transforms, one based on band-limited shearlets and the other based on compactly supported shearlets. We will moreover discuss various quantitative measures, which allow an objective comparison with other directional transforms and an objec- tive tuning of parameters. The codes for both presented transforms as well as the framework for quantifying performance are provided in the Matlab toolbox ShearLab. 1 Introduction One key property of wavelets, which enabled their success as a universal methodology for signal processing, is the unified treatment of the continuum and digital world. In fact, the wavelet transform can be implemented by a natural digitization of the continuum theory, thus providing a theoretical foundation for the digital transform. -
Light Field Reconstruction Using Shearlet Transform
1 Light Field Reconstruction Using Shearlet Transform Suren Vagharshakyan, Robert Bregovic and Atanas Gotchev, Member, IEEE Abstract—In this article we develop an image based rendering technique based on light field reconstruction from a limited set of perspective views acquired by cameras. Our approach utilizes sparse representation of epipolar-plane images in a directionally sensitive transform domain, obtained by an adapted discrete shearlet transform. The used iterative thresholding algorithm provides high-quality reconstruction results for relatively big disparities between neighboring views. The generated densely sampled light field of a given 3D scene is thus suitable for all applications which requires light field reconstruction. The proposed algorithm is compared favorably against state of the art depth image based rendering techniques. Index Terms—Image-based rendering, light field reconstruction, shearlets, frames, view synthesis. F 1 INTRODUCTION YNTHESIS of intermediate views from a given set of needs to sample the LF such that the disparity between S captured views of a 3D visual scene is usually referred neighboring views is less than one pixel [9]. Hereafter, to as image-based rendering (IBR) [1]. The scene is typically we will refer to such sampling as dense sampling and to captured by a limited number of cameras which form a the correspondingly sampled LF as densely sampled LF. In rather coarse set of multiview images. However, denser set order to capture a densely sampled LF, the required distance of images (i.e. intermediate views) is required in immersive between neighboring camera positions can be estimated visual applications such as free viewpoint television (FVT) based on the minimal scene depth (zmin) and the camera and virtual reality (VR) aimed at creating the perception of resolution. -
Image Denoising Using Hard Threshold Techniques On
ISSN No.: 2454- 2024 (online) International Journal of Technical Research & Science IMAGE DENOISING USING HARD THRESHOLD TECHNIQUES ON WAVELET TRANSFORM AND SHEARLET TRANSFORM Ankita Yadav, Riya Fagna, Aparna Vyas E-Mail Id: [email protected] Department of Mathematics, Manav Rachna University, Faridabad, Haryana, India Abstract- In this data age century with increment in the modern technology there is a development in the theory of multidimensional data to provide the higher directional sensitivity in imaging. A numeric image is a portrayal of a real image which is taken as a set of numbers that can be gathered and picked up by a digital computer. In order to decode the image into numbers it is divided into small segments called pixels (picture elements). Whenever there is a transmission of images or due to some environment factor there is an addition of noise to the images takes place that ultimately results in the reduction of originality of the image. It is very important to remove the noise from the images so that it is safeguard. Shearlets are a multiscale foundation which authorize efficient encoding of anisotropic feature in multivariate problem classes. In this paper, we have set forth the noise removal transform by hard thresholding for denoising. We can denoise the noisy image by wiping out the fine details, to enhance the quality of the images. Keywords: Wavelets, Wavelet Transform, Shearlet, Shearlet Transform, Image De- noising. 1. INTRODUCTION Digital images are the aggregation of pictures elements called pixel. Each pixel contains location and intensity values. These Digital images get corrupted or noisy by the imaging device or due to external environment in transmission or digitization procedures, then the resultant image is called noise image and to maintain the originality of the image it is very important to eliminate the noise from the image. -
Wavelet and Shearlet-Based Image Representations for Visual Servoing Lesley-Ann Duflot, Rafael Reisenhofer, Brahim Tamadazte, Nicolas Andreff, Alexandre Krupa
Wavelet and Shearlet-based Image Representations for Visual Servoing Lesley-Ann Duflot, Rafael Reisenhofer, Brahim Tamadazte, Nicolas Andreff, Alexandre Krupa To cite this version: Lesley-Ann Duflot, Rafael Reisenhofer, Brahim Tamadazte, Nicolas Andreff, Alexandre Krupa. Wavelet and Shearlet-based Image Representations for Visual Servoing. The International Journal of Robotics Research, SAGE Publications, 2019, 38 (4), pp.422-450. 10.1177/0278364918769739. hal-01735241 HAL Id: hal-01735241 https://hal.archives-ouvertes.fr/hal-01735241 Submitted on 15 Mar 2018 HAL is a multi-disciplinary open access L’archive ouverte pluridisciplinaire HAL, est archive for the deposit and dissemination of sci- destinée au dépôt et à la diffusion de documents entific research documents, whether they are pub- scientifiques de niveau recherche, publiés ou non, lished or not. The documents may come from émanant des établissements d’enseignement et de teaching and research institutions in France or recherche français ou étrangers, des laboratoires abroad, or from public or private research centers. publics ou privés. Wavelet and Shearlet-based Image Representations for Visual Servoing Lesley-Ann Duflot1,2, Rafael Reisenhofer3, Brahim Tamadazte2, Nicolas Andreff2 and Alexandre Krupa1 1L. A. Duflot and A. Krupa are with Univ Rennes, Inria, CNRS, IRISA. Campus universitaire de Beaulieu, Rennes 35042, France 2L. A. Duflot, B. Tamadazte and N. Andreff are with FEMTO-ST, AS2M, Univ. Bourgogne Franche-Comte,´ Univ. de Franche-Comte/CNRS/ENSMM,´ 25000 Besanc¸on, France 3R. Reisenhofer is with the University of Bremen, Computational Data Analysis, Fachbereich 3, Postfach 330440, 28334 Bremen, Germany Corresponding author: [email protected] Abstract A visual servoing scheme consists of a closed-loop control approach which uses visual information feedback to control the motion of a robotic system. -
The Complex Shearlet Transform and Applications to Image Quality Assessment
Technische Universität Berlin Fachgruppe Angewandte Funktionalanalysis The Complex Shearlet Transform and Applications to Image Quality Assessment Master Thesis by Rafael Reisenhofer 18. Juli 2014 – 17. Oktober 2014 Primary reviewer: Prof. Dr. Gitta Kutyniok Secondary reviewer: Dr. Wang-Q Lim Supervisor: Prof. Dr. Gitta Kutyniok Rafael Reisenhofer Beusselstraße 64 10553 Berlin Hiermit erkläre ich, dass ich die vorliegende Arbeit selbstständig und eigenhändig sowie ohne unerlaubte fremde Hilfe und ausschließlich unter Verwendung der aufgeführten Quellen und Hilfsmittel angefertigt habe. Berlin, den 17. Oktober 2014 Rafael Reisenhofer Contents List of Figures 5 1 Introduction 7 2 Complex Shearlet Transforms 9 2.1 From Fourier to Shearlets via an Analysis of Optimality . ........ 10 2.1.1 FourierAnalysis........................... 14 2.1.2 Wavelets............................... 20 2.1.2.1 Wavelets in Two Dimensions . 26 2.1.3 Shearlets............................... 27 2.2 Wavelet and Shearlet Transforms . 33 2.3 Complex Wavelet and Shearlet Transforms . ... 34 3 Complex Shearlet Transforms and the Visual Cortex 41 4 Applications 45 4.1 EdgeDetection ............................... 45 4.1.1 PhaseCongruency ......................... 47 4.1.2 Detection of Singularities With Pairs of Symmetric and Odd- SymmetricWavelets ........................ 51 4.1.3 Edge Detection With Pairs of Symmetric and Odd-Symmetric Shearlets............................... 56 4.2 ImageQualityAssessment . 62 4.2.1 Structural Similarity Index (SSIM) . 63 4.2.2 Complex Shearlet-Based Image Similarity Measure . .... 67 4.2.3 NumericalResults ......................... 71 5 Discussion 75 A Some Definitions and Formulas 79 A.1.1 PolynomialDepthSearch . 81 References 83 3 4 List of Figures 2.1 A piecewise smooth function and a cartoon like image . ...... 11 2.2 ExampleofFouriermodes. -
SAR Interferogram Filtering of Shearlet Domain Based on Interferometric Phase Statistics
applied sciences Article SAR Interferogram Filtering of Shearlet Domain Based on Interferometric Phase Statistics Yonghong He 1,2, Jianjun Zhu 1,*, Haiqiang Fu 1, Qinghua Xie 1, Bing Xu 1 and Bing Zhang 1 1 School of Geosciences and Info-Physics, Central South University, Changsha 410083, China; [email protected] (Y.H.); [email protected] (H.F.); [email protected] (Q.X.); [email protected] (B.X.); [email protected] (B.Z.) 2 School of Civil and Environmental Engineering, Hunan University of Science and Engineering, Yongzhou 425199, China * Correspondence: [email protected]; Tel.: +86-731-8887-9510 Academic Editor: Ting-Chung Poon Received: 21 November 2016; Accepted: 17 January 2017; Published: 4 February 2017 Abstract: This paper presents a new filtering approach for Synthetic Aperture Radar (SAR) interferometric phase noise reduction in the shearlet domain, depending on the coherent statistical characteristics. Shearlets provide a multidirectional and multiscale decomposition that have advantages over wavelet filtering methods when dealing with noisy phase fringes. Phase noise in SAR interferograms is directly related to the interferometric coherence and the look number of the interferogram. Therefore, an optimal interferogram filter should incorporate information from both of them. The proposed method combines the phase noise standard deviation with the shearlet transform. Experimental results show that the proposed method can reduce the interferogram noise while maintaining the spatial resolution, especially in areas with low coherence. Keywords: phase filtering; phase statistics; shearlet; coherence; Interferometric SAR (InSAR) 1. Introduction Interferometric Synthetic Aperture Radar (InSAR) has proven to be an effective technology for creating a digital elevation model (DEM) and detecting ground deformation [1], so it has been widely applied in the study of seismic deformation, volcanic activity, glacial drift, urban subsidence and landslides [2,3]. -
Wavelet and Shearlet-Based Image Representations for Visual Servoing
Wavelet and Shearlet-based Image Representations for Visual Servoing Lesley-Ann Duflot1,2, Rafael Reisenhofer3, Brahim Tamadazte2, Nicolas Andreff2 and Alexandre Krupa1 1L. A. Duflot and A. Krupa are with Univ Rennes, Inria, CNRS, IRISA. Campus universitaire de Beaulieu, Rennes 35042, France 2L. A. Duflot, B. Tamadazte and N. Andreff are with FEMTO-ST, AS2M, Univ. Bourgogne Franche-Comte,´ Univ. de Franche-Comte/CNRS/ENSMM,´ 25000 Besanc¸on, France 3R. Reisenhofer is with the University of Bremen, Computational Data Analysis, Fachbereich 3, Postfach 330440, 28334 Bremen, Germany Corresponding author: [email protected] Abstract A visual servoing scheme consists of a closed-loop control approach which uses visual information feedback to control the motion of a robotic system. Probably the most popular visual servoing method is image-based visual servoing (IBVS). This kind of method uses geometric visual features extracted from the image to design the control law. However, extracting, matching and tracking geometric visual features over time significantly limits the versatility of visual servoing controllers in various industrial and medical applications, in particular for ”low-structured” medical images, e.g., ultrasounds and opti- cal coherence tomography modalities. In order to overcome the limits of conventional IBVS, one can consider novel visual servoing paradigms known as “direct” or “featureless” approaches. This paper deals with the development of a new generation of direct visual servoing methods in which the signal control inputs are the coefficients of a multiscale image representation. In particular, we consider the use of multiscale image representations that are based on discrete wavelet and shearlet transforms. Up to now, one of the main obstacles in the investigation of multiscale image representations for visual ser- voing schemes was the issue of obtaining an analytical formulation of the interaction matrix that links the variation of wavelet and shearlet coefficients to the spatial velocity of the camera and the robot. -
Construction of Compactly Supported Shearlet Frames
CONSTRUCTION OF COMPACTLY SUPPORTED SHEARLET FRAMES PISAMAI KITTIPOOM, GITTA KUTYNIOK, AND WANG-Q LIM Abstract. Shearlet tight frames have been extensively studied during the last years due to their optimal approximation properties of cartoon-like images and their unified treatment of the continuum and digital setting. However, these studies only concerned shearlet tight frames generated by a band-limited shearlet, whereas for practical purposes compact support in spatial domain is crucial. In this paper, we focus on cone-adapted shearlet systems which – accounting for stabil- ity questions – are associated with a general irregular set of parameters. We first derive sufficient conditions for such cone-adapted irregular shearlet systems to form a frame and provide explicit estimates for their frame bounds. Secondly, exploring these results and using specifically designed wavelet scaling functions and filters, we construct a family of cone-adapted shearlet frames consisting of compactly supported shearlets. For this family, we derive estimates for the ratio of their frame bounds and prove that they provide opti- mally sparse approximations of cartoon-like images. Finally, we discuss an implementation strategy for the shearlet transform based on compactly supported shearlets. We further show that an optimally sparse N-term approximation of an M M cartoon-like image can be derived with asymptotic computational cost O(M 2(1+τ)) for× some positive constant τ depending on M and N. 1. Introduction Over the last 20 years wavelets have established themselves as a key methodology for efficiently representing signals or operators with applications ranging from more theoretical tasks such as adaptive schemes for solving elliptic partial differential equations to more practically tasks such as data compression. -
Image Separation Using Wavelets and Shearlets
Image Separation using Wavelets and Shearlets Gitta Kutyniok and Wang-Q Lim Institute of Mathematics, University of Osnabr¨uck, 49069 Osnabr¨uck, Germany kutyniok,[email protected] Abstract. In this paper, we present an image separation method for separating images into point- and curvelike parts by employing a com- bined dictionary consisting of wavelets and compactly supported shear- lets utilizing the fact that they sparsely represent point and curvilinear singularities, respectively. Our methodology is based on the very recently introduced mathematical theory of geometric separation, which shows that highly precise separation of the morphologically distinct features of points and curves can be achieved by ℓ1 minimization. Finally, we present some experimental results showing the effectiveness of our algorithm, in particular, the ability to accurately separate points from curves even if the curvature is relatively large due to the excellent localization property of compactly supported shearlets. Keywords: Geometric separation, ℓ1 minimization, sparse approxima- tion, shearlets, wavelets 1 Introduction The task of separating an image into its morphologically different contents has recently drawn a lot of attention in the research community due to its signif- icance for applications. In neurobiological imaging, it would, for instance, be desirable to separate ’spines’ (pointlike objects) from ’dendrites’ (curvelike ob- jects) in order to analyze them independently aiming to detect characteristics of Alzheimer disease. Also, in astronomical imaging, astronomers would often like to separate stars from filaments for further analysis, hence again separating point- from curvelike structures. Successful methodologies for efficiently and ac- curately solving this task can in fact be applied to a much broader range of areas in science and technology including medical imaging, surveillance, and speech processing. -
3D Discrete Shearlet Transform and Video Processing Pooran Singh Negi and Demetrio Labate
IEEE TRANSACTIONS ON IMAGE PROCESSING 1 3D Discrete Shearlet Transform and Video Processing Pooran Singh Negi and Demetrio Labate Abstract—In this paper, we introduce a digital implementation Up to the log-like factor, this is the optimal approximation rate, of the 3D shearlet transform and illustrate its application to in the sense that no other orthonormal systems or even frames problems of video denoising and enhancement. The shearlet can achieve a rate better than M −2. By contrast, wavelet representation is a multiscale pyramid of well-localized wave- −1 forms defined at various locations and orientations, which was approximations can only achieve a rate M for functions in introduced to overcome the limitations of traditional multiscale this class [3]. Concerning the topic of sparse approximations, it systems in dealing with multidimensional data. While the shearlet is important to recall that the relevance of this notion goes far approach shares the general philosophy of curvelets and sur- beyond the applications to compression. In fact, constructing facelets, it is based on a very different mathematical framework sparse representations for data in a certain class entails the which is derived from the theory of affine systems and uses shearing matrices rather than rotations. This allows a natural intimate understanding of their true nature and structure, so transition from the continuous to the digital setting and a that sparse representations also provide the most effective tool more flexible mathematical structure. The 3D digital shearlet for tasks such as feature extraction and pattern recognition [6], transform algorithm presented in this paper consists in a cascade [7]. -
Medical Video Coding Based on 2Nd-Generation Wavelets: Performance Evaluation
electronics Article Medical Video Coding Based on 2nd-Generation Wavelets: Performance Evaluation Merzak Ferroukhi 1, Abdeldjalil Ouahabi 2,3,* , Mokhtar Attari 1, Yassine Habchi 4 and Abdelmalik Taleb-Ahmed 5 1 Laboratory of Instrumentation, Faculty of Electronics and Computers, University of Sciences and Technology Houari Boumediene, 16111 Algiers, Algeria; [email protected] (M.F.); [email protected] (M.A.) 2 Polytech Tours, Imaging and Brain, INSERM U930, University of Tours, 37200 Tours, France 3 Computer Science Department, LIMPAF, University of Bouira, 10000 Bouira, Algeria 4 Electrical Engineering Department, LTIT, Bechar University, 08000 Bechar, Algeria; [email protected] 5 IEMN DOAE UMR CNRS 8520, UPHF, 59313 Valenciennes, France; [email protected] * Correspondence: [email protected]; Tel.: +33-603894463 Received: 5 October 2018; Accepted: 8 January 2019; Published: 14 January 2019 Abstract: The operations of digitization, transmission and storage of medical data, particularly images, require increasingly effective encoding methods not only in terms of compression ratio and flow of information but also in terms of visual quality. At first, there was DCT (discrete cosine transform) then DWT (discrete wavelet transform) and their associated standards in terms of coding and image compression. The 2nd-generation wavelets seeks to be positioned and confronted by the image and video coding methods currently used. It is in this context that we suggest a method combining bandelets and the SPIHT (set partitioning in hierarchical trees) algorithm. There are two main reasons for our approach: the first lies in the nature of the bandelet transform to take advantage of capturing the geometrical complexity of the image structure.