Black Soldier Fly Biowaste Processing a Step-By-Step Guide – 2Nd Edition
Total Page:16
File Type:pdf, Size:1020Kb
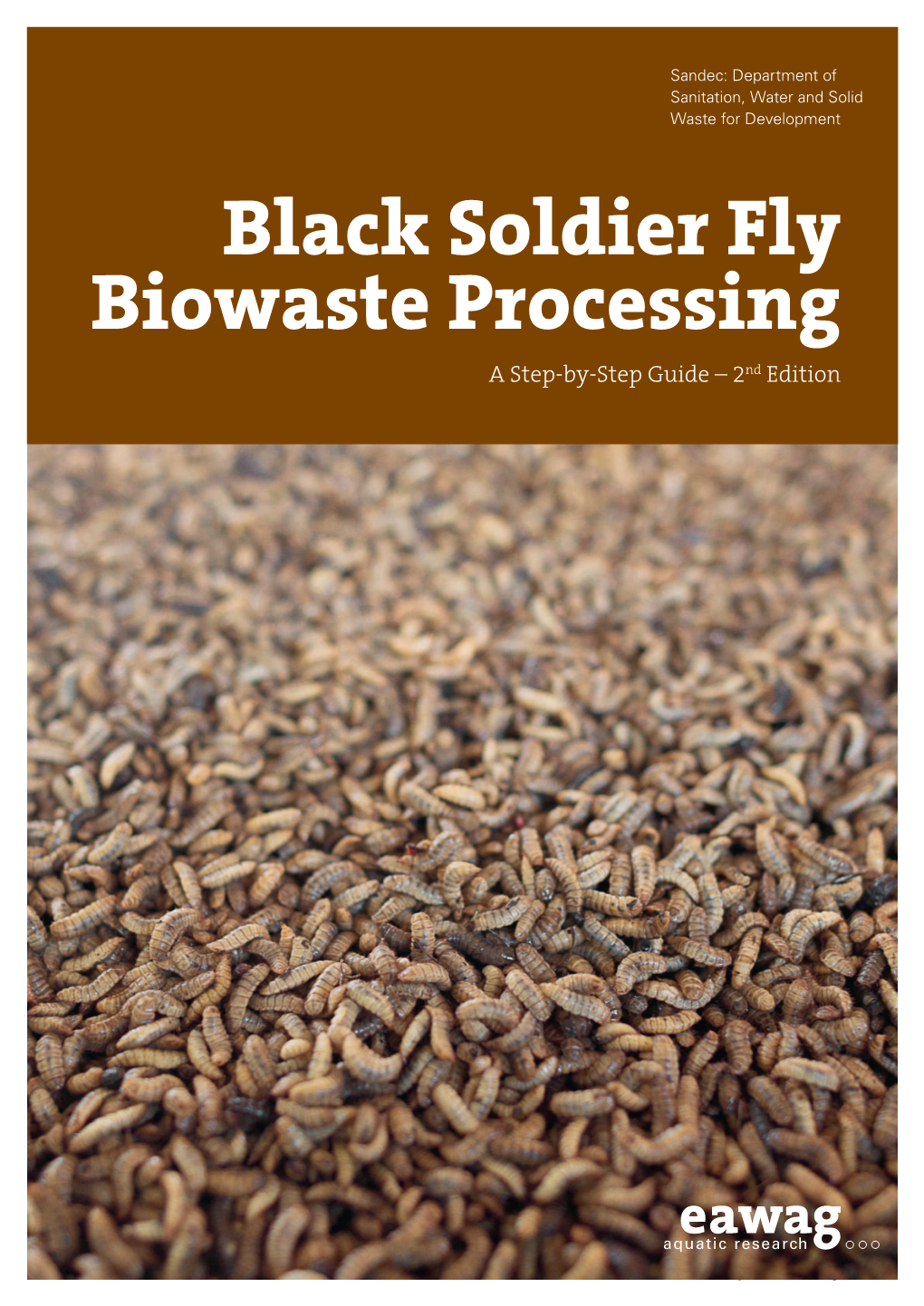
Load more
Recommended publications
-
Holistic Sustainability Assessment of an Improved Organic Waste Collection System and Its Valorization Through Insects
HOLISTIC SUSTAINABILITY ASSESSMENT OF AN IMPROVED ORGANIC WASTE COLLECTION SYSTEM AND ITS VALORIZATION THROUGH INSECTS ECO-INNOVATIVE SOLUTIONS FOR GHENT AND DESTELBERGEN. Number of words: 23 314 María Ignacia Rodríguez Escobar Student number: 01808626 Academic promotor: Prof. dr. ir. Jo Dewulf Non-academic supervisor: Tom Claeys (IVAGO) Tutors: Dr. ir. Sue Ellen Taelman , Dr. David Sanjuan Delmás Master’s Dissertation submitted to Ghent University in partial fulfilment of the requirements for the degree of International Master of Science in Sustainable and Innovative Natural Resource Management Academic Year: 2019 - 2020 Deze pagina is niet beschikbaar omdat ze persoonsgegevens bevat. Universiteitsbibliotheek Gent, 2020. This page is not available because it contains personal information. Ghent University, Library, 2020. Acknowledgements This master thesis has been the culmination of my studies of International Master of Science in Sustainable and Innovative Natural Resource Management (SINReM) at Ghent University, Uppsala Universitet, and Technische Universität Bergakademie Freiberg, with the valuable support of the EIT Raw Materials through the EIT AVSA scholarship. This thesis has come under the promotion of Prof. Jo Dewulf, to whom I would like to express gratitude for always pushing and challenging me with critical questioning and constructive suggestions. Furthermore, I would like to extend these acknowledgements to my two supervisors, Dr. ir. Sue Ellen Taelman and Dr. David Sanjuan Delmás, because without their constant support, questioning and coaching, this work could not have been possible. Both of them were extremely present along the way and were always more than available to answer all my doubts and questions. I would like to also thank Tom Claeys who listened carefully to my propositions, suggested more ideas to look at and was of course key for the data collection of this thesis. -
Hermetia Illucens): from Technology to Business Gabrielle Joly and Josiane Nikiema About the Resource Recovery & Reuse Series
RESOURCE RECOVERY & REUSE SERIES 16 ISSN 2478-0529 Global Experiences on Waste Processing with Black 16 Soldier Fly (Hermetia illucens): From Technology to Business Gabrielle Joly and Josiane Nikiema About the Resource Recovery & Reuse Series Resource Recovery and Reuse (RRR) is a subprogram of the CGIAR Research Program on Water, Land and Ecosystems (WLE) dedicated to applied research on the safe recovery of water, nutrients and energy from domestic and agro-industrial waste streams. This subprogram aims to create impact through different lines of action research, including (i) developing and testing scalable RRR business models, (ii) assessing and mitigating risks from RRR for public health and the environment, (iii) supporting public and private entities with innovative approaches for the safe reuse of wastewater and organic waste, and (iv) improving rural-urban linkages and resource allocations while minimizing the negative urban footprint on the peri-urban environment. This subprogram works closely with the World Health Organization (WHO), Food and Agriculture Organization of the United Nations (FAO), United Nations Environment Programme (UNEP), United Nations University (UNU), and many national and international partners across the globe. The RRR series of documents present summaries and reviews of the subprogram’s research and resulting application guidelines, targeting development experts and others in the research for development continuum. IN PARTNERSHIP WITH: RESOURCE RECOVERY & REUSE SERIES 16 Global Experiences on Waste Processing with Black Soldier Fly (Hermetia illucens): From Technology to Business Gabrielle Joly and Josiane Nikiema The authors Joly, G.; Nikiema, J. 2019. Global experiences on waste processing with black soldier fly (Hermetia illucens): from Ms. -
The Capability of Black Soldier Fly, Hermetia Illuncens, to Consume Some Weeds in Vegetable Field
The Capability of Black Soldier Fly, Hermetia Illuncens, to Consume Some Weeds in Vegetable Field Y Sanjaya1, Suhara2, M. Nurjhani3, M Halimah4 { [email protected]} Biologi Department, Universitas Pendidikan Indonesia, Jl.Dr. Setiabudi N0.229, Bandung, Indonesia1,2,3, Biology Study program, Univeritas Pasundan Jl. Taman Sari No. 6-8, Bandung, Indonesia4 Abstract. Weed in the agriculture field is needed to reduce. So It is need something environmentally tool to conserve agriculture. One promising uses Black Soldier Fly (BSF) larvae. The larvae capability to consume some weeds were presented. Descriptive research was conducted by investigating the role of BSF on some weeds i.e ki rinyuh (Chromolaena odorata), Babadotan (Ageratum conyzoides), rumput gajah (Pennisetum purpreum). Each was given BSF larvae with 150 g, 200 gr and 250 gr of weight on 500 gr weed, The result showed that BSF larvae at 150 g of weight convert weed between 80- 100%, on 200 mg convert 75 % – 97 %, on 250 mg can convert 80 % -100 % in four day. The mortality of BSF larvae on Chromolaena odorata was 10 %, Ageratum conyzoides was 6 %, Pennisetum purpreum was 0 %. This showed BSF larvae can be converted weed into BSFlarvae biomass. Keywords: Hermetia illucens, weeds, weight, bioconversion 1 Introduction The waste product is a big problem in Indonesia. Various wastes have not been systematically resolved including the remnants of weeds. Weed is a plant that grows and competes with competing plants in terms of obtaining nutrients. To overcome this, farmers usually deal with it by weeding and stacking it, sometimes even burning. In large numbers, weeds will be a problem for the environment and sources of pests and diseases [1]. -
RAFFAELLO COSSU Detritusjournal.Com
01 VOLUME 01 / March 2018 VOLUME 01 / March 2018 01 / March VOLUME CONTENTS Editorial SIGNIFICANCE OF IMPLEMENTING DECENTRALIZED BIO- GAS SOLUTIONS IN INDIA: A VIABLE PATHWAY FOR BIOBA- WHY THIS JOURNAL? WHY THIS NAME? SED ECONOMY R. Cossu ............................................................................ 1 S. Begum, G.R. Anupoju, S. Sridhar, S.K. Bhargava, V. Jegatheesanv and N. Esthiagi ..................................... 75 Waste generation SPATIAL AND NON-SPATIAL ANALYSIS OF SOCIO-DEMO- Landfill mining GRAPHIC ASPECTS INFLUENCING MUNICIPAL SOLID WA- INVESTIGATION OF MUNICIPAL SOLID WASTE (MSW) AND STE GENERATION IN THE CZECH REPUBLIC INDUSTRIAL LANDFILLS AS A POTENTIAL SOURCE OF SE- K. Rybova, B. Burcin and J. Slavik .................................... 3 CONDARY RAW MATERIALS H. Särkkä, T. Kaartinen, E. Hannus, S. Hirvonen, Bioconversion T. Valjus, J. Lerssi, G.A. Dino, P. Rossetti, Z. Griffiths, A COMPARATIVE STUDY OF ISSUES, CHALLENGES AND S.T. Wagland and F. Coulon ............................................. 83 STRATEGIES OF BIO-WASTE MANAGEMENT IN INDIA AND A DECISION SUPPORT TOOL FOR ENHANCED LANDFILL and Residues Resources - MultidisciplinaryDETRITUS Journal for Waste ITALY MINING S.K. Ghosh and F. Di Maria ............................................... 8 G. Pastre, Z. Griffiths, J. Val, A.M. Tasiu, E.V. Camacho-Dominguez, S. Wagland and F. Coulon .... 91 Waste to material resources RECYCLING OF WASTE PLASTICS DISPOSED OF IN LAND- FROM PILOT TO FULL SCALE OPERATION OF A WASTE-TO-PRO- FILLS: THE EFFECT OF WASHING TREATMENT TEIN TREATMENT FACILITY K. Tameda, M. Hanashima, N.-h. Lee, E.-a. Cho, C. Zurbrügg, B. Dortmans, A. Fadhila, B. Verstappen and M. Kawashimaf and S. Higuchi ....................................... 102 S. Diener ............................................................................ 18 INNOVATIVE TECHNOLOGIES FOR PHOSPHORUS RECOVERY Old landfills FROM SEWAGE SLUDGE ASH OLD MUNICIPAL AND INDUSTRIAL WASTE LANDFILLS: M. -
The Role of Black Soldier Fly, Hermetia Illucens (L.) (Diptera: Stratiomyidae) in Sustainable Waste Management in Northern Climates
University of Windsor Scholarship at UWindsor Electronic Theses and Dissertations Theses, Dissertations, and Major Papers 2012 The Role of Black Soldier Fly, Hermetia illucens (L.) (Diptera: Stratiomyidae) in Sustainable Waste Management in Northern Climates Luis Alvarez University of Windsor Follow this and additional works at: https://scholar.uwindsor.ca/etd Recommended Citation Alvarez, Luis, "The Role of Black Soldier Fly, Hermetia illucens (L.) (Diptera: Stratiomyidae) in Sustainable Waste Management in Northern Climates" (2012). Electronic Theses and Dissertations. 402. https://scholar.uwindsor.ca/etd/402 This online database contains the full-text of PhD dissertations and Masters’ theses of University of Windsor students from 1954 forward. These documents are made available for personal study and research purposes only, in accordance with the Canadian Copyright Act and the Creative Commons license—CC BY-NC-ND (Attribution, Non-Commercial, No Derivative Works). Under this license, works must always be attributed to the copyright holder (original author), cannot be used for any commercial purposes, and may not be altered. Any other use would require the permission of the copyright holder. Students may inquire about withdrawing their dissertation and/or thesis from this database. For additional inquiries, please contact the repository administrator via email ([email protected]) or by telephone at 519-253-3000ext. 3208. The Role of Black Soldier Fly, Hermetia illucens (L.) (Diptera: Stratiomyidae) in Sustainable Waste Management in Northern Climates by Luis Alvarez M.A.Sc., P.Eng. A Dissertation Submitted to the Faculty of Graduate Studies through Civil and Environmental Engineering in Partial Fulfillment of the Requirements for the Degree of Doctor of Philosophy at the University of Windsor Windsor, Ontario, Canada 2012 © 2012 Luis Alvarez The Role of Black Soldier Fly, Hermetia illucens (L.) (Diptera: Stratiomyidae) in Sustainable Waste Management in Northern Climates by Luis Alvarez APPROVED BY: __________________________________________________ Dr. -
On the Road to Zero Waste Successes and Lessons Global Alliance for Incinerator Alternatives from Around the World Global Anti-Incinerator Alliance
ON THE ROAD to ZEro WASTE SUCCEssES AND LEssONS Global Alliance for Incinerator Alternatives FROM AROUND THE WORLD Global Anti-Incinerator Alliance Global Alliance for Incinerator Alternatives Global Anti-Incinerator Alliance GAIA is a worldwide alliance of more than 650 grassroots groups, non-governmental organizations, and individuals in over 90 countries whose ultimate vision is a just, toxic-free world without incineration. GAIA Secretariat GAIA Latin America Unit 330, Eagle Court Condominium c/o Observatorio Latinoamericano de 26 Matalino Street Conflictos Ambientales (OLCA) Barangay Central Alonso Ovalle 1618 Of. A. Quezon City, Philippines Santiago, Chile Telefax: +632-436 4733 Email: [email protected] Email: [email protected] GAIA U.S. & Canada GAIA Europe 1958 University Avenue Email: [email protected] Berkeley, CA 94704 USA Phone: +1-510-883-9490 Fax: +1-510-883-9493 Email: [email protected] Global Alliance for Incinerator Alternatives Global Anti-Incinerator Alliance www.no-burn.org June 2012 COVER ClocKwise FRom top left: Alaminos (Anne Larracas), Buenos Aires (Cooperativa El Ceibo), Hernani (Gipuzkoa Zero Zabor), Mumbai (Michael Atkin), Flanders (OVAM), San Francisco (Larry Strong), Pune (Amit Thavaraj), Taiwan (Allianz SE), La Pintana (DIGA) Design and Layout by Design Action Collective Global Alliance for Incinerator Alternatives Authors andGlobal Anti-Incinerator Contributors Alliance Cecilia Allen is a sociologist active in environmental health and justice organizations with a particular interest in waste management; she was part of GAIA’s coordination team for eight years. Virali Gokaldas has a background in environmental science and business management with a focus on the green economy; she advises social ventures and nonprofits on operational improvements and growth of new programs, products, and services. -
(Diptera: Stratiomyidae) Larval Development
DIRECT INJURY,MYIASIS,FORENSICS Influence of Resources on Hermetia illucens (Diptera: Stratiomyidae) Larval Development 1,2 3 1 TRINH T. X. NGUYEN, JEFFERY K. TOMBERLIN, AND SHERAH VANLAERHOVEN J. Med. Entomol. 50(4): 898Ð906 (2013); DOI: http://dx.doi.org/10.1603/ME12260 ABSTRACT Arthropod development can be used to determine the time of colonization of human remains to infer a minimum postmortem interval. The black soldier ßy, Hermetia illucens L. (Diptera: Stratiomyidae) is native to North America and is unique in that its larvae can consume a wide range of decomposing organic material, including carrion. Larvae development was observed on six re- sources: control poultry feed, liver, manure, kitchen waste, fruits and vegetables, and Þsh rendering. Larvae fed manure were shorter, weighed less, and took longer to develop. Kitchen waste produced longer and heavier larvae, whereas larvae fed Þsh had almost 100% mortality. Black soldier ßies can colonize human remains, which in many instances can coincide with food and organic wastes. Therefore, it is necessary to understand black soldier ßy development on different food resources other than carrion tissue to properly estimate their age when recovered from human remains. KEY WORDS forensic entomology, development time, food resource, minimum postmortem in- terval, waste management Forensic entomologists use arthropod evidence col- veloped up to 2 d slower than larvae reared on other lected from human remains to estimate the period of experimental tissues, such as lung, kidney, heart, and insect activity and infer time of colonization (Benecke brain. Similarly, Lucilia sericata (Meigen) (Diptera: 2001). The time of colonization is a portion of the Calliphoridae) developed at a faster rate, and were postcolonization interval, which equates to the min- larger, when fed pork instead of beef (Clark et al. -
The Role of Black Soldier Fly, Hermetia Illucens (L.) (Diptera: Stratiomyidae) in Sustainable Waste Management in Northern Climates Luis Alvarez University of Windsor
University of Windsor Scholarship at UWindsor Electronic Theses and Dissertations 2012 The Role of Black Soldier Fly, Hermetia illucens (L.) (Diptera: Stratiomyidae) in Sustainable Waste Management in Northern Climates Luis Alvarez University of Windsor Follow this and additional works at: http://scholar.uwindsor.ca/etd Recommended Citation Alvarez, Luis, "The Role of Black Soldier Fly, Hermetia illucens (L.) (Diptera: Stratiomyidae) in Sustainable Waste Management in Northern Climates" (2012). Electronic Theses and Dissertations. Paper 402. This online database contains the full-text of PhD dissertations and Masters’ theses of University of Windsor students from 1954 forward. These documents are made available for personal study and research purposes only, in accordance with the Canadian Copyright Act and the Creative Commons license—CC BY-NC-ND (Attribution, Non-Commercial, No Derivative Works). Under this license, works must always be attributed to the copyright holder (original author), cannot be used for any commercial purposes, and may not be altered. Any other use would require the permission of the copyright holder. Students may inquire about withdrawing their dissertation and/or thesis from this database. For additional inquiries, please contact the repository administrator via email ([email protected]) or by telephone at 519-253-3000ext. 3208. The Role of Black Soldier Fly, Hermetia illucens (L.) (Diptera: Stratiomyidae) in Sustainable Waste Management in Northern Climates by Luis Alvarez M.A.Sc., P.Eng. A Dissertation Submitted to the Faculty of Graduate Studies through Civil and Environmental Engineering in Partial Fulfillment of the Requirements for the Degree of Doctor of Philosophy at the University of Windsor Windsor, Ontario, Canada 2012 © 2012 Luis Alvarez The Role of Black Soldier Fly, Hermetia illucens (L.) (Diptera: Stratiomyidae) in Sustainable Waste Management in Northern Climates by Luis Alvarez APPROVED BY: __________________________________________________ Dr. -
Effects of Microplastics and Salinity on Food Waste Processing by Black
Cho et al. Journal of Ecology and Environment (2020) 44:7 Journal of Ecology https://doi.org/10.1186/s41610-020-0148-x and Environment RESEARCH Open Access Effects of microplastics and salinity on food waste processing by black soldier fly (Hermetia illucens) larvae Sam Cho1, Chul-Hwan Kim1, Min-Ji Kim2 and Haegeun Chung1* Abstract Background: The black soldier fly (Hermetia illucens) is gaining attention as an efficient decomposer of food waste. However, recalcitrant compounds such as plastics mixed into food waste may have negative effects on its growth and survival. Moreover, its efficiency of food waste degradation may also be affected by plastics. In addition, salt (NaCl) can also be present in high concentrations, which also reduces the efficiency of H. illucens-mediated food waste treatment. In this study, we assessed the growth of black soldier fly larvae (BSFL) reared on food waste containing polyethylene (PE) and polystyrene (PS) and NaCl. The weight of BSFL was measured every 2–4 days. Survival and substrate reduction rates and pupation ratio were determined at the end of the experiment. Results: The total larval weight of Hermetia illucens reared on food waste containing PS was greater than that of the control on days 20 and 24. However, the survival rate was lower in the group treated with 5% PS, as was substrate reduction in all PS-treated groups. The weight of BSFL reared on food waste containing PE was lower than that of the control on day 6. PE in food waste did not affect the survival rate, but the pupation ratio increased and substrate consumption decreased with increasing PE concentrations. -
A Growth Kinetics Model for Black Soldier Fly (Hermetia Illucens) Larvae
International Journal of Technology 12(1) 207-216 (2021) Received June 2020 / Revised July 2020 / Accepted November 2020 International Journal of Technology http://ijtech.eng.ui.ac.id A Growth Kinetics Model for Black Soldier Fly (Hermetia illucens) Larvae Agus Prasetya1, Robby Darmawan1, Thya Laurencia Benedita Araujo1, Himawan Tri Bayu Murti Petrus1*, Felix Arie Setiawan2** 1Department of Chemical Engineering, Universitas Gadjah Mada, Jl. Grafika No. 2, Kampus UGM Bulaksumur, Yogyakarta 55281, Indonesia 2Department of Chemical Engineering, Universitas Jember, Jl. Kalimantan No. 37, Jember, Jawa Timur 68121, Indonesia Abstract. Known as a promising protein source, black soldier fly (BSF) larva has attracted the attention of many researchers. BSF larvae have the ability to convert organic waste into protein. However, the growth modeling of this process has not been studied previously. Hence, this study generated a BSF larvae growth model to explain BSF larvae production. Vegetable and fruit waste collected from the Gamping fruit market was used as the growth media. The weight of larvae and the leftover substrate were measured for 20 days. The substrate consumed was related to larvae body mass. The model was properly fitted with R-squared values of 0.9988 and 0.9312 for the substrate consumption and larvae growth, respectively. The value of the kinetics constants in this study were 0.847 ± 0.018 g 0.5 day-1 for k1; 0.058 ± 0.019 g-0.5 day-1 for k2; and 0.007 ± 0.013 g-1.0 day- 1 for k3. Keywords: Black soldier fly; Growth model kinetics; Larvae; Organic waste 1. Introduction Municipal solid waste (MSW) has become an interesting issue in the sustainable development of human life (Gabriel Andari Kristanto, 2015). -
Biodegradation of Heterogeneous Mixture of Organic Fraction of Municipal Solid Waste by Black Soldier Fly Larvae
IJISET - International Journal of Innovative Science, Engineering & Technology, Vol. 5 Issue 3, March 2018 ISSN (Online) 2348 – 7968 www.ijiset.com Biodegradation of Heterogeneous Mixture of Organic Fraction of Municipal Solid Waste by Black Soldier Fly Larvae (Hermetia Illucens) under the Tropical Climate Conditions Daniel Sarpong1*, Sampson. Oduro. Kwarteng1, Samuel. Fosu. Gyasi,2 Richard. Buamah1, Emmanuel. Donkor, 1 Emmanuel. Yaw. Botchway1 & Samuel. Acquah1 1 Kwame Nkrumah University of Science and Technology, Kumasi, Ghana 2University of Energy & Natural Resources, Sunyani, Ghana. *Email of corresponding author: [email protected]; Mobile Tel: +233-244488440 Abstract Municipal organic solid waste (MOSW) generation 2.5, 3.0, 3.5, to 4 and control of 2} kg) of is increasing at a faster pace in both developed and heterogeneous mixture of municipal organic solid developing countries due to uncontrolled growth of waste from market, restaurant and households. Each population, urbanization as well as changes in of the set up received equal number of viable larvae production and consumption. Improper disposal of (2,000) which were 5 day old. Waste reduction organic waste pose a huge problem, especially in potential was then measured in terms of total the developing countries due to unavailability of carbon, mass and nutrient (nitrogen, phosphorus low-cost waste treatment technologies. In the past, and potassium) variation after 14 days. Results of vermicomposting and microbial waste degradation the waste reduction potential of the Hermetia has not been promising. Therefore, there is the need Illucens showed that, the highest waste reduction of to look for alternative biodegradation technology 59.4 % (dry matter) was measured at a feeding rate that would be able to deal with the huge volumes of of 107 mg/larvae/day and this was significant (p = organic waste generated from the municipalities. -
From Pilot to Full Scale Operation of a Waste-To-Protein Treatment Facility
From Pilot to Full Scale Operation of a Waste-to-Protein Treatment Facility Christian Zurbrügg, Bram Dortmans, Audinisa Fadhila, Stefan Diener Just one slide on the rationale Waste management is still a challenge in low income settings Organic solid waste is 50-80% of waste mass and is yet hardly recovered and recycled Strategies and policies are more and more including aspects of circular economy Current organic waste recovery/recycling still faces a «value chain» challenge Compost typically has limited value and customers are not where the product is Biogas often suffers from cheap energy competition Char production (or biomass fuel) is promising but limited to dry materials How else can we create value from waste? Lohri C.R., et al. (2017). Treatment technologies for urban solid biowaste to Possibilities create value products – a review with focus on low and middle income settings. Reviews in Environmental Science and Bio/Technology. 16/1, pp 81–130. P H Y S I C O - T H E R M O – B I O L O G I C A L D I R E C T C H E M I C A L C H E M I C A L T R E A T M E N T U S E T R E A T M E N T T R E A T M E N T T E C H N O L O G I E S P R O C E S S E S Direct Direct Com‐ Vermi‐ Black An‐ Fer‐ Trans‐ Lique‐ Direct Densi‐ Pyro‐ Gasifi‐ land animal post‐ compost‐ Soldier Fly aerobic men‐ esteri‐ fact‐ com‐ fication lysis cation application feed bustion ing ing treatment digestion tation fication ion P R O D U C T S Gly‐ Worms Resi‐ Digest‐ Pellets/ due ate cerol briquettes Bio‐ethanol Bio‐ Bio‐ Compost Larvae Biogas Char Gas diesel oil Meat/fish