Construction Technology Used for the Reclamation of Seri Tanjung Pinang (Phase 2)
Total Page:16
File Type:pdf, Size:1020Kb
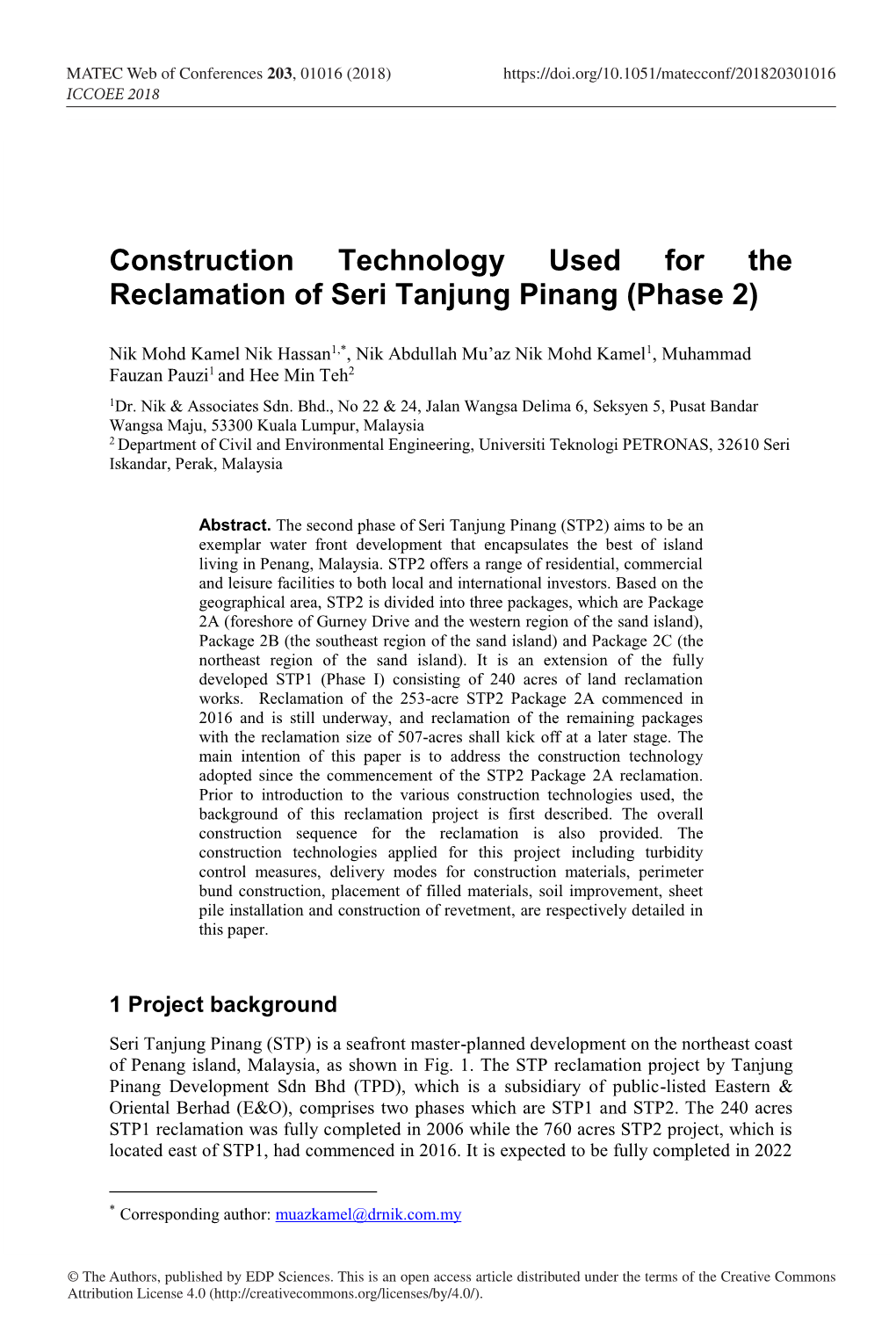
Load more
Recommended publications
-
Annual Report 2019 the E&O Group
ANNUAL REPORT 2019 THE E&O GROUP The E&O Group (Eastern & Oriental Berhad) is a listed company on Bursa Malaysia that has established a reputation as the premier lifestyle property developer of exclusive addresses for the discerning. In Kuala Lumpur, E&O’s landmark properties include The Mews, St Mary Residences, Dua Residency, Idamansara and Seventy Damansara, all located in the most prime and prestigious neighbourhoods of the capital city. In Penang, the award-winning Seri Tanjung Pinang (STP) is the island’s first masterplanned seafront development that is now a highly sought-after and thriving community to locals as well as expatriates from over 20 nationalities. Reclamation of the second phase of STP started in 2016 and is on-going. In Johor’s southern development corridor of Iskandar Malaysia, E&O has embarked on Avira, a 207-acre development within Bandar Medini Iskandar that has easy accessibility to the Second Link connection to Singapore. In its expansion overseas, E&O’s international foray into real estate investment and development is focused within prime locations in London, including Princes House along Kingsway, ESCA House in Bayswater, and a commercial property in Hammersmith. E&O’s leading position as a lifestyle developer is anchored by its niche in luxury hospitality derived from its namesake, the iconic Eastern & Oriental Hotel, a cherished heritage landmark in George Town established in 1885. The Group has further leveraged on its experience and expertise in hospitality management with the opening of E&O Residences serviced apartments in Kuala Lumpur. www.easternandoriental.com EXPECT NOTHING ORDINARY Enriched by our heritage, crafting legacies for the future Our inheritance of values such as grace, refinement and appreciation of beauty, has emboldened us to seek fresh interpretations of the old to forge ahead and create anew PURPOSE E&O designs and builds properties that cater to the lifestyle aspirations of discerning individuals. -
Sand Dunes Computer Animations and Paper Models by Tau Rho Alpha*, John P
Go Home U.S. DEPARTMENT OF THE INTERIOR U.S. GEOLOGICAL SURVEY Sand Dunes Computer animations and paper models By Tau Rho Alpha*, John P. Galloway*, and Scott W. Starratt* Open-file Report 98-131-A - This report is preliminary and has not been reviewed for conformity with U.S. Geological Survey editorial standards. Any use of trade, firm, or product names is for descriptive purposes only and does not imply endorsement by the U.S. Government. Although this program has been used by the U.S. Geological Survey, no warranty, expressed or implied, is made by the USGS as to the accuracy and functioning of the program and related program material, nor shall the fact of distribution constitute any such warranty, and no responsibility is assumed by the USGS in connection therewith. * U.S. Geological Survey Menlo Park, CA 94025 Comments encouraged tralpha @ omega? .wr.usgs .gov [email protected] [email protected] (gobackward) <j (goforward) Description of Report This report illustrates, through computer animations and paper models, why sand dunes can develop different forms. By studying the animations and the paper models, students will better understand the evolution of sand dunes, Included in the paper and diskette versions of this report are templates for making a paper models, instructions for there assembly, and a discussion of development of different forms of sand dunes. In addition, the diskette version includes animations of how different sand dunes develop. Many people provided help and encouragement in the development of this HyperCard stack, particularly David M. Rubin, Maura Hogan and Sue Priest. -
Soil Improvement/ Land Reclamation
Unearthing Sustainable www.nwbiosolids.org Solutions SOIL IMPROVEMENT/ Fact Sheet LAND RECLAMATION Biosolids provide nutrients and organic matter to damaged soils, enabling renewed plant growth. SEEKING SOLUTIONS Our collective footprint as humans has disturbed native landscapes and underlying soils. Heavy equipment used in construction can compact soils. Mining can result in loss of topsoil. Overgrazing disturbs native vegetation and wind and water erosion occurs when ecosystems are disturbed. Following this damage, soils are often unable to support plant life due to lack of nutrients and organic matter, compaction, altered pH and other ecosystem changes. BENEFITS OF BIOSOLIDS Disturbed soils can be restored and revitalized Before and after a reclamation with biosolids through the addition of organic matter. Nutrient-rich, organic biosolids replace lost can access over time. Soil, following biosolids topsoil and improve soil fertility and stability, application is better aerated and lighter. Water thus decreasing erosion and aiding in revegetation. enters into the soil rather than eroding off the soil Biosolids have been used successfully to reclaim surface. Unlike nutrients in commercial fertilizers, large construction sites, surface mines, parks nutrients added in the biosolids will stay in the and road cuts. Biosolids composts are an topsoil over time and the restored ecosystem excellent organic soil for building or renewing will prosper over time. wetlands. Wildlife habitat and rangelands have been restored using biosolids products. WHAT’S HAPPENING Here are some of the ways biosolids have HOW IT WORKS reclaimed damaged soils: Soil improvement and land reclamation projects use onetime or infrequent applications of large · Wildlife habitat enhancement - Invasive plants quantities of biosolids to increase the amount like Scotch broom and blackberry vines can of nutrients and organic matter in the poor or take over natural wildlife habitats. -
AML Pilot Program) for FY 2016 – FY 2017
Report on Abandoned Mine Land Reclamation Economic Development Pilot Program (AML Pilot Program) for FY 2016 – FY 2017 Prepared by the Office of Surface Mining Reclamation and Enforcement (OSMRE) Prepared by the OSMRE Program Support Directorate March 28, 2017 Page 1 of 18 I. Introduction and Background The Abandoned Mine Land Reclamation Economic Development Pilot Program (AML Pilot) for FY 2016 was authorized by Congress under the Consolidated Appropriations Act, 2016 (Public Law 114-113) and enacted on December 18, 2015. Administered by the Office of Surface Mining Reclamation and Enforcement (OSMRE), the AML Pilot provided $30 million of US Treasury Funds to each of the three Appalachian state AML Programs (Kentucky, Pennsylvania and West Virginia) which have the highest amount of unfunded coal-related problems that are classified as Priority 1 and Priority 2 abandoned mine lands sites and inventoried in the Enhanced Abandoned Mine Land Inventory System (e-AMLIS). The AML Pilot funds are to be used “for the reclamation of abandoned mine lands in conjunction with economic and community development and reuse goals”. This report describes implementation actions for the AML Pilot. II. Implementation of the AML Pilot Program OSMRE facilitated a meeting on February 24, 2016, in West Virginia with state AML Program staff from Kentucky, Pennsylvania and West Virginia to obtain input on the implementation on the AML Pilot Program. A second meeting was held on March 16, 2016, in Lexington, Kentucky to solicit input from additional stakeholders on the AML Pilot. OSMRE also participated in workshops with economic development organizations convened by the Appalachian Regional Commission (ARC) in the three states to provide information about the AML Pilot Program and to encourage state and local economic developers to identify opportunities to align and leverage their efforts with AML reclamation projects. -
Fehmarnbelt: a New Green Link Between Germany and Denmark
PROJECT FEHMARNBELT: A NEW GREEN LINK BETWEEN GERMANY AND DENMARK An aerial view of the Fehmarnbelt's site on the island of Fehmarn in Germany, situated adjacent to the Puttgarden ferry harbour. Photo Jan Kofod Winther Femern AS 6 TERRA ET AQUA The Fehmarnbelt Fixed Link is a joint Danish and To be built in northern Europe and connect German transport Scandinavia with Germany, the Fehmarnbelt infrastructure will be the world’s longest immersed tunnel. The infrastructure will close a major gap in the project across the European transport network, reduce the risk of Fehmarnbelt. shipping collisions, energy consumption and create a new region in Europe, while also fostering the development of new nature and recreational landscapes by Working with Nature concepts. Presentation of the project The Fehmarnbelt Fixed Link – the proposed eastern route between Germany and Denmark – has been planned for a long time in an effort to create a rapid connection between the two countries with a faster and shorter link (see Figure 1). It will also close a major gap in the Scandinavian-Mediterranean corridor which is part of the European transport network. Once opened, the journey for freight trains between Hamburg and Scandinavia will reduce by 160 kilometres. The Fehmarnbelt Fixed Link is a joint Danish and German transport infrastructure project across the Fehmarnbelt. Denmark is responsible for the planning, construction and operation of the Fehmarn Fixed Link. To carry out this task, the government of Denmark has established the company Femern A/S which is 100% owned by the Danish State and represented by the Danish Ministry of Transport. -
Why Did the Developers of Seri Tanjung Pinang Create a 5-Star, Purpose-Built Sales
AN OVERVIEW 1 Penang’s North-Eastern On the northeast coast of Penang Island, the sun is shining Jewel and deals are flowing, thanks to a residential project taking shape there. Greetings All materials published remain the property of The E&O Group Berhad. No Dear Friends of Seri Tanjung Pinang, part of this publication may be reproduced, stored in a retrieval system, or transmitted in any form nor by any means - graphics, electronics, mechanical, photocopying, recording - without prior written permission of the publisher. Every effort has been made to ensure the credits accurately comply with the information supplied. Welcome to Watercolour, our exciting newsletter devoted to the happenings and development of the seafront masterplanned development of Seri Tanjung Pinang. Written by Datin Adila Lim Lay Ying, Unlike in the past when the appetite had been for moderately-priced properties, the craving today For more information, please contact: a feature story from the Property section is for luxury units which, according to real estate professionals and developers, has been the flavour For those of you who have purchased the property in Seri Tanjung Pinang, I would like to of the New Straits Times - Saturday, since April 1, when the government decided to lift the Real Property Gains Tax (RPGT). congratulate you on your decision and welcome you to a new community lifestyle which will May 19, 2007. be the first to be experienced on this island and which will prove to be the envy of many who For as long as the economy sustains its growth path and the stock market stays bullish, their view is appreciate the finer things in life. -
Types of Landslides.Indd
Landslide Types and Processes andslides in the United States occur in all 50 States. The primary regions of landslide occurrence and potential are the coastal and mountainous areas of California, Oregon, Land Washington, the States comprising the intermountain west, and the mountainous and hilly regions of the Eastern United States. Alaska and Hawaii also experience all types of landslides. Landslides in the United States cause approximately $3.5 billion (year 2001 dollars) in dam- age, and kill between 25 and 50 people annually. Casualties in the United States are primar- ily caused by rockfalls, rock slides, and debris flows. Worldwide, landslides occur and cause thousands of casualties and billions in monetary losses annually. The information in this publication provides an introductory primer on understanding basic scientific facts about landslides—the different types of landslides, how they are initiated, and some basic information about how they can begin to be managed as a hazard. TYPES OF LANDSLIDES porate additional variables, such as the rate of movement and the water, air, or ice content of The term “landslide” describes a wide variety the landslide material. of processes that result in the downward and outward movement of slope-forming materials Although landslides are primarily associ- including rock, soil, artificial fill, or a com- ated with mountainous regions, they can bination of these. The materials may move also occur in areas of generally low relief. In by falling, toppling, sliding, spreading, or low-relief areas, landslides occur as cut-and- La Conchita, coastal area of southern Califor- flowing. Figure 1 shows a graphic illustration fill failures (roadway and building excava- nia. -
Gurney Wharf a Gift to Penang
槟政府2子公司招聘接受统考生 CHINESE NEW YEAR 唯一州政府正式聘请统考生 FESTIVITIES pg pg 6 1 FREE buletin Competency Accountability Transparency http:www.facebook.com/buletinmutiara March 1 - 15, 2016 http:www.facebook.com/cmlimguaneng ...there will be Gurney Wharf no more unpleasant sight and smell... a gift to Penang – Lim Story by Chan Lilian and Danny Ooi The proposed Gurney Wharf concept masterplan encompasses four distinct IMAGINE a sandy beach with lapping character areas: Seaside Retail F&B, waves and casuarina trees. Water Gardens, Beach and Coastal In place of the mud that one associates Grove. with Gurney Drive, a wharf like in other The Seaside Retail F&B celebrates cities in the world such as London, San Penang’s vibrant seafront brought to life Francisco and Hongkong will be the pride by elements such as a water-fronting of Penang. public promenade, seafront dining fa- “It is going to be the best in Malaysia. cilities including the island’s famed It is a sincere gift to the people of Penang. hawker fare and a pier walk. To be an international city, we must have The Water Gardens area will be de- a similar wharf,” Chief Minister Lim fined by lush gardens, ponds and wet- Guan Eng said during the launch of the lands with its most distinctive feature preview of the new seafront park Gurney being landscaped water gardens with Wharf in Gurney Plaza on Feb 27. innovative storm water filtration sys- Together with Lim were Bukit Bend- tems. era MP Zairil Khir Johari and exco Modelled after Singapore’s success member for Local Government, Traffic with this at Gardens on the Bay, this is Management and Flood Mitigation Chow By ME a pioneering system in Malaysia which Kon Yeow. -
Gabion Retaining Walls with Alternate Fill Materials
Gabion Retaining Walls with Alternate Fill Materials IGC 2009, Guntur, INDIA GABION RETAINING WALLS WITH ALTERNATE FILL MATERIALS K.S. Beena Reader, School of Engineering, Cochin University of Science and Technology, Cochin–682022, India. E-mail: [email protected] P.K. Jayasree Lecturer in Civil Engineering, College of Engineering, Trivandrum–695 016, India. E-mail: [email protected] ABSTRACT: Although gabions have been used from ancient times, it is only in the last few decades that their wide spread use has lead them to become an accepted construction material in Civil Engineering. Gabion retaining walls are mass gravity structure made up of strong mesh containers known as gabion boxes, filled with quarry stone. Considering the cost and scarcity of quarry stones, the replacement of it with some other cheaper material will make the construction more economical. This aspect is studied here. Considering the specific gravity, friction, cost and availability, quarry dust and red soil was selected as the fill material. Model gabion retaining walls were constructed for the purpose in which, different combinations of quarry dust, red soil and coarse aggregate were taken as the filling material. Analyzing the lateral deformations of various cases, it can be concluded that a 50%–50% combination of alternative material and aggregate will perform better than the coarse aggregate alone, considering the cost of construction. 1. INTRODUCTION dry stone gravity mass wall made of gabion boxes. They are cost effective, environmental friendly and durable structures. Retaining walls, one of the major geotechnical applications, Because of these reasons gabions are widely used now days are mainly used in the case of highways and railways to all over the world. -
Landslide Triggering Mechanisms
kChapter 4 GERALD F. WIECZOREK LANDSLIDE TRIGGERING MECHANISMS 1. INTRODUCTION 2.INTENSE RAINFALL andslides can have several causes, including Storms that produce intense rainfall for periods as L geological, morphological, physical, and hu- short as several hours or have a more moderate in- man (Alexander 1992; Cruden and Vames, Chap. tensity lasting several days have triggered abun- 3 in this report, p. 70), but only one trigger (Varnes dant landslides in many regions, for example, 1978, 26). By definition a trigger is an external California (Figures 4-1, 4-2, and 4-3). Well- stimulus such as intense rainfall, earthquake shak- documented studies that have revealed a close ing, volcanic eruption, storm waves, or rapid stream relationship between rainfall intensity and acti- erosion that causes a near-immediate response in vation of landslides include those from California the form of a landslide by rapidly increasing the (Campbell 1975; Ellen et al. 1988), North stresses or by reducing the strength of slope mate- Carolina (Gryta and Bartholomew 1983; Neary rials. In some cases landslides may occur without an and Swift 1987), Virginia (Kochel 1987; Gryta apparent attributable trigger because of a variety or and Bartholomew 1989; Jacobson et al. 1989), combination of causes, such as chemical or physi- Puerto Rico (Jibson 1989; Simon et al. 1990; cal weathering of materials, that gradually bring the Larsen and Torres Sanchez 1992)., and Hawaii slope to failure. The requisite short time frame of (Wilson et al. 1992; Ellen et al. 1993). cause and effect is the critical element in the iden- These studies show that shallow landslides in tification of a landslide trigger. -
Utilization of Locally Available Organic Matter to Improve Chemical Properties of Pyroclastic Materials from Mt
JOURNAL OF DEGRADED AND MINING LANDS MANAGEMENT ISSN: 2339-076X (p); 2502-2458 (e), Volume 4, Number 2 (January 2017): 717-721 DOI:10.15243/jdmlm.2017.042.717 Research Article Utilization of locally available organic matter to improve chemical properties of pyroclastic materials from Mt. Kelud of East Java S.R. Utami*, C. Agustina, K.S. Wicaksono, B.D. Prasojo, H. Hanifa Faculty of Agriculture, University of Brawijaya, Jl. Veteran 1, Malang 65145, Indonesia *corresponding author: [email protected] Abstract: Pandansari village, Ngantang District was severely affected by Mt. Kelud eruption in 2014. Almost all soil surfaces were covered by the eruption product, leading to serious problems for cultivation. Pyroclastic materials potentially have high content of nutrients, but they are not readily available to plants. As an attempt to improve chemical properties of the pyroclastic materials, we applied locally available organic matters, from four different sources, i.e. leaves of sweet potatoes, Tithonia diversifolia, maize, and cow manure. The pyroclastic materials were sieved at 2 mm, placed inside pots (50 x 50 x 50 cm3), until it reached 30 cm thick. The fresh leaves were chopped into 2 mm size and mixed with the pyroclastic materials at the dosage of 15 Mg/ha. They were incubated and kept at field condition. Selected chemical properties (pH, CEC, sum of basic cations, and the total contents of N, organic C, and available P) were measured before and after 90 days incubation. The results showed that after 90 days, organic matter application significantly increased pH, cation exchange capacity, organic C, and total exchangeable basic cations content. -
Slope Stability 101 Basic Concepts and NOT for Final Design Purposes! Slope Stability Analysis Basics
Slope Stability 101 Basic Concepts and NOT for Final Design Purposes! Slope Stability Analysis Basics Shear Strength of Soils Ability of soil to resist sliding on itself on the slope Angle of Repose definition n1. the maximum angle to the horizontal at which rocks, soil, etc, will remain without sliding Shear Strength Parameters and Soils Info Φ angle of internal friction C cohesion (clays are cohesive and sands are non-cohesive) Θ slope angle γ unit weight of soil Internal Angles of Friction Estimates for our use in example Silty sand Φ = 25 degrees Loose sand Φ = 30 degrees Medium to Dense sand Φ = 35 degrees Rock Riprap Φ = 40 degrees Slope Stability Analysis Basics Explore Site Geology Characterize soil shear strength Construct slope stability model Establish seepage and groundwater conditions Select loading condition Locate critical failure surface Iterate until minimum Factor of Safety (FS) is achieved Rules of Thumb and “Easy” Method of Estimating Slope Stability Geology and Soils Information Needed (from site or soils database) Check appropriate loading conditions (seeps, rapid drawdown, fluctuating water levels, flows) Select values to input for Φ and C Locate water table in slope (critical for evaluation!) 2:1 slopes are typically stable for less than 15 foot heights Note whether or not existing slopes are vegetated and stable Plan for a factor of safety (hazards evaluation) FS between 1.4 and 1.5 is typically adequate for our purposes No Flow Slope Stability Analysis FS = tan Φ / tan Θ Where Φ is the effective