Torque Coordinated Control in Engine Starting Process for a Single-Motor
Total Page:16
File Type:pdf, Size:1020Kb
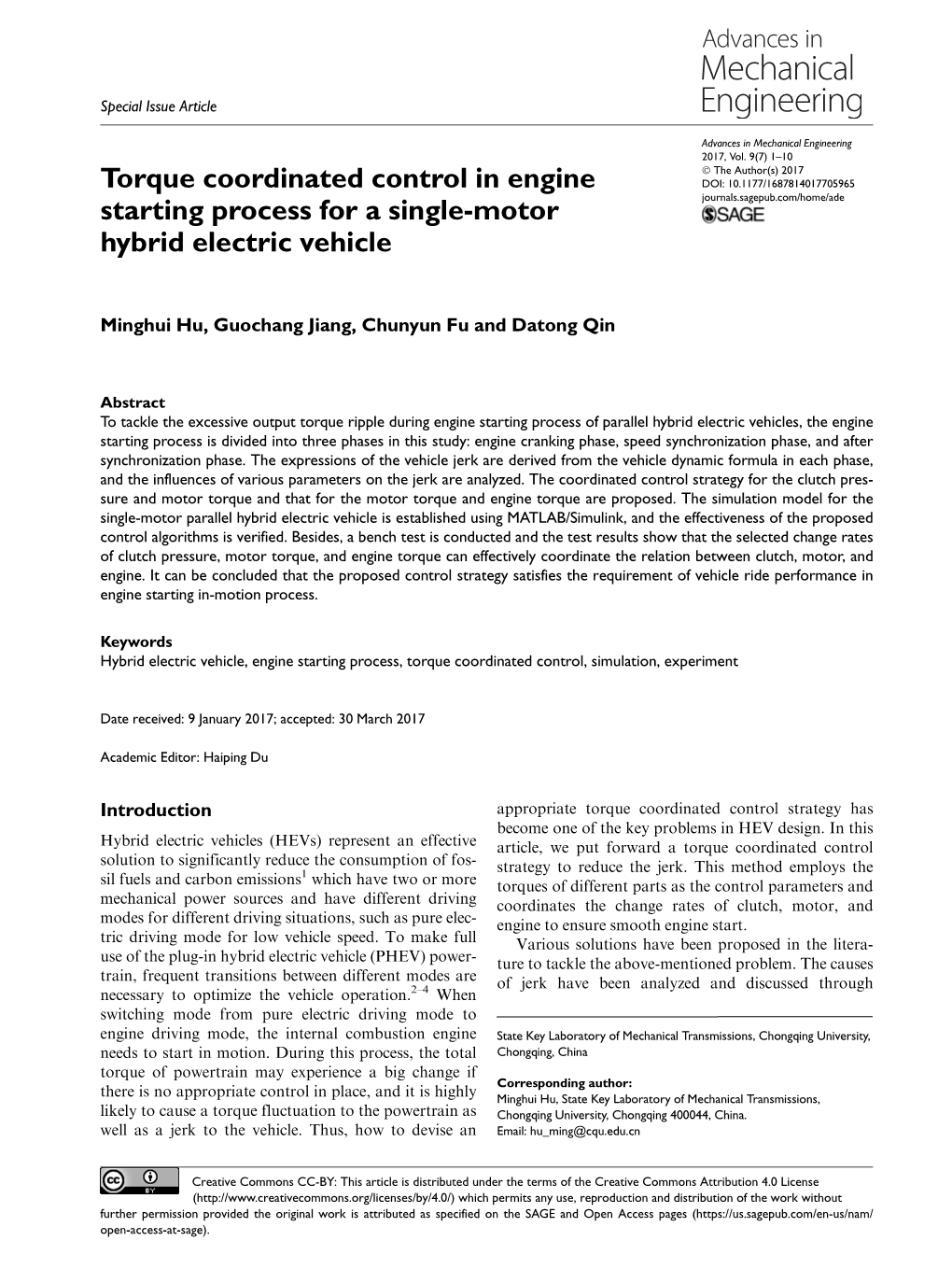
Load more
Recommended publications
-
Accelerometers Used in the Measurement of Jerk, Snap, and Crackle
Accelerometers used in the measurement of jerk, snap, and crackle David Eager Faculty of Engineering and IT, University of Technology Sydney, PO Box 123 Broadway, Australia ABSTRACT Accelerometers are traditionally used in acoustics for the measurement of vibration. Higher derivatives of motion are rarely considered when measuring vibration. This paper presents a novel usage of a triaxial accelerometer to measure acceleration and use these data to explain jerk and higher derivatives of motion. We are all familiar with the terms displacement, velocity and acceleration but few of us are familiar with the term jerk and even fewer of us are familiar with the terms snap and crackle. We experience velocity when we are displaced with respect to time and acceleration when we change our velocity. We do not feel velocity, but rather the change of velocity i.e. acceleration which is brought about by the force exerted on our body. Similarly, we feel jerk and higher derivatives when the force on our body experiences changes abruptly with respect to time. The results from a gymnastic trampolinist where the acceleration data were collected at 100 Hz using a device attached to the chest are pre- sented and discussed. In particular the higher derivates of the Force total eQuation are extended and discussed, 3 3 4 4 5 5 namely: ijerk∙d x/dt , rsnap∙d x/dt , ncrackle∙d x/dt etc. 1 INTRODUCTION We are exposed to a wide variety of external motion and movement on a daily basis. From driving a car to catching an elevator, our bodies are repeatedly exposed to external forces acting upon us, leading to acceleration. -
AN00118-000 Motion Profiles.Doc
A N00118-000 - Motion Profiles Related Applications or Terminology Supported Controllers ■ Trapezoidal Velocity Profile NextMovePCI NextMoveBXII ■ S-Ramped Velocity Profile NextMoveST NextMoveES Overview MintDriveII The motion of moving objects can be specified by a number of Flex+DriveII parameters, which together define the Motion Profile. These parameters are: Relevant Keywords Speed: The rate of change of position PROFILEMODE Acceleration: The rate of change of speed during an SPEED ACCEL increase of speed. DECEL Deceleration: The rate of change of speed during a ACCELJERK decrease of speed. DECELJERK Jerk: The rate of change of acceleration or deceleration. Trapezoidal Profile A trapezoidal profile is typically made up of three sections, an acceleration phase, a constant velocity phase and a deceleration phase. Velocity Time Acceleration Constant Velocity Deceleration © Baldor UK Ltd 2003 1 of 6 AN00118-000 Motion Profiles.doc The graph is a plot of velocity against time for a trapezoidal profile; the name reflects the shape of the profile. For a positional move from rest, the velocity increases at the rate defined by acceleration until it reaches the slew speed. The velocity will then remain constant until the deceleration point, where the velocity will then decrease to a halt at the rate specified by deceleration. S-Ramped Profile An s-ramped profile can be considered as a super set of the trapezoidal profile. It typically is made up of seven sections, four jerk phases on top of the acceleration phase, constant velocity phase and deceleration phase. Velocity Time Acceleration Constant Velocity Deceleration The graph is a plot of velocity against time for an s-curve profile; again the name reflects the shape of the profile. -
On Fast Jerk–, Acceleration– and Velocity–Restricted Motion Functions for Online Trajectory Generation
robotics Article On Fast Jerk–, Acceleration– and Velocity–Restricted Motion Functions for Online Trajectory Generation Burkhard Alpers Department of Mechanical Engineering, Aalen University, D-73430 Aalen, Germany; [email protected] Abstract: Finding fast motion functions to get from an initial state (distance, velocity, acceleration) to a final one has been of interest for decades. For a solution to be practically relevant, restrictions on jerk, acceleration and velocity have to be taken into account. Such solutions use optimization algorithms or try to directly construct a motion function allowing online trajectory generation. In this contribution, we follow the latter strategy and present an approach which first deals with the situation where initial and final accelerations are 0, and then relates the general case as much as possible to this situation. This leads to a classification with just four major cases. A continuity argument guarantees full coverage of all situations which is not the case or is not clear for other available algorithms. We present several examples that show the variety of different situations and, thus, the complexity of the task. We also describe an implementation in MATLAB® and results from a huge number of test runs regarding accuracy and efficiency, thus demonstrating that the algorithm is suitable for online trajectory generation. Keywords: online trajectory generation; fast motion functions; seven segment profile; jerk restriction 1. Introduction Citation: Alpers, B. On Fast Jerk–, Acceleration– and Velocity–Restricted For achieving high throughput in handling machines, one of the most basic tasks Motion Functions for Online consists of quickly moving from one position to the next one, taking into account machine Trajectory Generation. -
Jerk and Hyperjerk in a Rotating Frame of Reference
Jerk and Hyperjerk in a Rotating Frame of Reference Amelia Carolina Sparavigna Department of Applied Science and Technology, Politecnico di Torino, Italy. Abstract: Jerk is the derivative of acceleration with respect to time and then it is the third order derivative of the position vector. Hyperjerks are the n-th order derivatives with n>3. This paper describes the relations, for jerks and hyperjerks, between the quantities measured in an inertial frame of reference and those observed in a rotating frame. These relations can be interesting for teaching purposes. Keywords: Rotating frames, Physics education research. 1. Introduction Jerk is the rate of change of acceleration, that is, it is the derivative of acceleration with respect to time [1,2]. In teaching physics, jerk is often completely neglected; however, as remarked in the Ref.1, it is a physical quantity having a great importance in practical engineering, because it is involved in mechanisms having rotating or sliding pieces, such as cams and genevas. For this reason, jerks are commonly found in models for the design of robotic arms. Moreover, these derivatives of acceleration are also considered in the planning of tracks and roads, in particular of the track transition curves [3]. Let us note that, besides in mechanics and transport engineering, jerks can be used in the study of several electromagnetic systems, as proposed in the Ref.4. Jerks of the geomagnetic field are investigated too, to understand the dynamics of the Earth’s fluid, iron-rich outer core [5]. Jerks and hyperjerks - jerks having a n-th order derivative with n>3 - are also attractive for researchers that are studying the behaviour of complex systems. -
Speed Profile Optimization for Enhanced Passenger Comfort: an Optimal Control Approach Yuyang Wang, Jean-Rémy Chardonnet, Frédéric Merienne
Speed Profile Optimization for Enhanced Passenger Comfort: An Optimal Control Approach Yuyang Wang, Jean-Rémy Chardonnet, Frédéric Merienne To cite this version: Yuyang Wang, Jean-Rémy Chardonnet, Frédéric Merienne. Speed Profile Optimization for Enhanced Passenger Comfort: An Optimal Control Approach. 2018 21st International Conference on Intelligent Transportation Systems (ITSC), Nov 2018, Maui, Hawaii, United States. pp.723-728. hal-01963942 HAL Id: hal-01963942 https://hal.archives-ouvertes.fr/hal-01963942 Submitted on 21 Dec 2018 HAL is a multi-disciplinary open access L’archive ouverte pluridisciplinaire HAL, est archive for the deposit and dissemination of sci- destinée au dépôt et à la diffusion de documents entific research documents, whether they are pub- scientifiques de niveau recherche, publiés ou non, lished or not. The documents may come from émanant des établissements d’enseignement et de teaching and research institutions in France or recherche français ou étrangers, des laboratoires abroad, or from public or private research centers. publics ou privés. Speed Profile Optimization for Enhanced Passenger Comfort: An Optimal Control Approach Yuyang Wangy, Jean-Remy´ Chardonnet and Fred´ eric´ Merienne Abstract— Autonomous vehicles are expected to start reach- We propose a novel approach in which we generate a glob- ing the market within the next years. However in practical ally lowest jerk trajectory with an optimized speed profile applications, navigation inside dynamic environments has to following also the same comfort constraints as defined in take many factors such as speed control, safety and comfort into consideration, which is more paramount for both passengers the ISO 2631-1 standard [5]. We achieve this by introducing and pedestrians. -
An Alternative Approach to Jerk in Motion Along a Space Curve with Applications
JOURNAL OF THEORETICAL AND APPLIED MECHANICS 57, 2, pp. 435-444, Warsaw 2019 DOI: 10.15632/jtam-pl/104595 AN ALTERNATIVE APPROACH TO JERK IN MOTION ALONG A SPACE CURVE WITH APPLICATIONS Kahraman Esen Ozen¨ Sakarya University, Mathematics Department, Sakarya, Turkey; e-mail: [email protected] Furkan Semih Dundar¨ Boˇgazi¸ci University, Physics Department, Istanbul, Turkey; e-mail: [email protected] Murat Tosun Sakarya University, Mathematics Department, Sakarya, Turkey; e-mail: [email protected] Jerk is the time derivative of an acceleration vector and, hence, the third time derivative of the position vector. In this paper, we consider a particle moving in the three dimensional Euclidean space and resolve its jerk vector along the tangential direction, radial direction in the osculating plane and the other radial direction in the rectifying plane. Also, the case for planar motion in space is given as a corollary. Furthermore, motion of an electron under a constant magnetic field and motion of a particle along a logarithmic spiral curve are given as illustrative examples. The aforementioned decomposition is a new contribution to the field and it may be useful in some specific applications that may be considered in the future. Keywords: jerk, kinematics of a particle, plane and space curves 1. Introduction In Newtonian physics, the force acting on the particle is related to its acceleration through F = ma. The jerk J is the time derivative of the acceleration. Therefore, if the mass is constant, we have J = (1/m)dF/dt. If the time derivative of the force is nonzero, we have a nonzero jerk vector. -
The Jerk Vector in Projectile Motion
The jerk vector in projectile motion A. Tan and M. E. Edwards Department of Physics, Alabama A & M University, Normal, Alabama 35762, U.S.A. E-mail: [email protected] (Received 12 February 2011, accepted 29 June 2011) Abstract The existence of the jerk vector is investigated in projectile motion under gravity. The jerk vector is zero in the absence of air resistance, but comes into life when velocity-dependent air drag is present. The jerk vector is calculated when the air resistance is proportional to the velocity. It is found that the jerk vector maintains a constant sense in the upward and forward direction, with its magnitude attenuated exponentially as a function of time. Keywords: Jerk vector, Projectile motion, Air resistance. Resumen La existencia del vector reflejo es investigada en el movimiento de proyectiles en virtud de la gravedad. El vector reflejo es cero en ausencia de la resistencia del aire, pero vuelve a la vida cuando la resistencia del aire dependiente de la velocidad está presente. El vector reflejo es calculado cuando la resistencia del aire es proporcional a la velocidad. Se ha encontrado que el vector reflejo mantiene una sensación constante en la dirección hacia arriba y hacia delante, con su magnitud atenuada exponencialmente en función del tiempo. Palabras clave: Vector reflejo, Movimiento de proyectiles, Resistencia del aire. PACS: 45.50.-j, 45.50.Dd, 45.40.Gj, 45.40.Aa ISSN 1870-9095 I. INTRODUCTION projectile of mass m is projected with an initial velocity v0 making an angle α with the horizontal plane. In a Cartesian The vast majority of physical laws are represented by coordinate system x-y with the launch point at the origin, second order differential equations. -
A Note on the Acceleration and Jerk in Motion Along a Space Curve
DOI: 10.2478/auom-2020-0011 An. S¸t. Univ. Ovidius Constant¸a Vol. 28(1),2020, 151{164 A Note on the Acceleration and Jerk in Motion Along a Space Curve Kahraman Esen Ozen,¨ Mehmet G¨unerand Murat Tosun Abstract The resolution of the acceleration vector of a particle moving along a space curve is well known thanks to Siacci [1]. This resolution comprises two special oblique components which lie in the osculating plane of the curve. The jerk is the time derivative of acceleration vector. For the jerk vector of the aforementioned particle, a similar resolution is presented as a new contribution to field [2]. It comprises three special oblique components which lie in the osculating and rectifying planes. In this paper, we have studied the Siacci's resolution of the acceleration vector and aforementioned resolution of the jerk vector for the space curves which are equipped with the modified orthogonal frame. Moreover, we have given some illustrative examples to show how the our theorems work. 1 Introduction In Newtonian physics, it is well known that the force acting on a particle is concerned with its acceleration through the equation F = ma. A particle, which moves under the influence of arbitrary forces in 3-dimensional Euclidean space, has an acceleration which is obtained by the time derivative of the ve- locity vector, and thus by two time derivative of the position vector. For some applications, to state the acceleration vector as the sum of its tangential and Key Words: Kinematics of a particle , Space curves , Siacci , Jerk , Modified orthogonal frame. -
Modeling and Analysis for Driveline Jerk Control
Michigan Technological University Digital Commons @ Michigan Tech Dissertations, Master's Theses and Master's Reports 2018 MODELING AND ANALYSIS FOR DRIVELINE JERK CONTROL Prince Lakhani Michigan Technological University, [email protected] Copyright 2018 Prince Lakhani Recommended Citation Lakhani, Prince, "MODELING AND ANALYSIS FOR DRIVELINE JERK CONTROL", Open Access Master's Report, Michigan Technological University, 2018. https://doi.org/10.37099/mtu.dc.etdr/598 Follow this and additional works at: https://digitalcommons.mtu.edu/etdr Part of the Acoustics, Dynamics, and Controls Commons, Applied Mechanics Commons, Automotive Engineering Commons, and the Computer-Aided Engineering and Design Commons MODELING AND ANALYSIS FOR DRIVELINE JERK CONTROL By Prince A. Lakhani A REPORT Submitted in partial fulfillment of the requirements for the degree of MASTER OF SCIENCE In Mechanical Engineering MICHIGAN TECHNOLOGICAL UNIVERSITY 2018 © 2018 Prince A. Lakhani This report has been approved in partial fulfillment of the requirements for the Degree of MASTER OF SCIENCE in Mechanical Engineering. Department of Mechanical Engineering-Engineering Mechanics Report Co-advisor: Dr. Mahdi Shahbakhti Report Co-advisor: Dr. Darrell L. Robinette Committee Member: Dr. Mo Rastgaar Department Chair: Dr. William W. Predebon Table of Contents List of Figures............................................................................................................. vii Acknowledgements ..................................................................................................... -
Measuring Elevator System Inertia
Application Note DSD 412-105 SUBJECT: MEASURING ELEVATOR SYSTEM INERTIA The DSD412 dc drive has an internal digital velocity regulator specifically designed for repeatable position tracking of elevators during acceleration, running, and deceleration. It is simple to tune because it does not use the interacting P-I-D type adjustments often found with traditional regulators. But it does require knowledge of the system inertia, operating speeds, gear ratio, acceleration rates, and torque capability of the motor. These values are neither familiar nor necessarily available to the adjuster who is responsible for tuning up elevator performance, and at first may seem to be intimidating. However, a combined ratio of these parameters is what is needed, not the individual values. This ratio is the Per Unit Inertia of the system, and can be easily estimated and measured using the techniques listed below. The beauty of this method, and a digital regulator, is that once tuning of a particular hoistway is accomplished, a second identical hoistway can often be successfully tuned by merely entering in the same parameter values. PER UNIT INERTIA Per Unit Inertia is defined as the ratio of the strength required to accelerate the mass of all moving parts of the elevator system to rated speed versus the strength of the motor used to do it. When expressed in terms of rotation as geared to the motor shaft, the mathematical relationship is: ()()EquivRotatingInertia× ratedSpeed Jpu = ()RatedTorque The correct physics term for Equivalent Rotating Inertia is known as the Moment of Inertia. And Moment of Inertia X Angular Velocity = Angular Momentum. -
Trajectory Planning and Feedforward Design for Electromechanical Motion Systems
ARTICLE IN PRESS Control Engineering Practice 13 (2005) 145–157 Trajectory planning and feedforward design for electromechanical motion systems Paul Lambrechts*, Matthijs Boerlage, Maarten Steinbuch Control Systems Technology Group, Faculty of Mechanical Engineering, Eindhoven University of Technology, P.O. Box 513, 5600 MB Eindhoven, The Netherlands Received 14 February 2003; accepted 28 February 2004 Abstract This paper considers trajectory planning with given design constraints and design of a feedforward controller for single-axis motion control. A motivation is given for using fourth-order feedforward with fourth-order trajectories. An algorithm is given for calculating higher-order trajectories with bounds on all considered derivatives for point-to-point moves. It is shown that these trajectories are time-optimal in the most relevant cases. All required equations for fourth-order trajectory planning are derived. Implementation, discretization and quantization effects are considered. Simulations and hardware-in-the-loop experiments show superior effectiveness of fourth-order feedforward in comparison with lower-order feedforward. r 2004 Elsevier Ltd. All rights reserved. Keywords: Trajectory planning; Feedforward compensation; Motion; Point-to-point control; Industrial control; Numerical methods 1. Introduction * system compensation: to reduce or remove unwanted behaviour like measured disturbances or non-linear- Feedforward control is a well-known technique for ities, high-performance motion control problems as found in * feedback control: the processing of available measure- industry. It is, for instance, widely applied in robots, ments and calculation of input signals for actuation pick-and-place units and positioning systems. These devices to compensate for unknown disturbances and systems are often embedded in a factory automation unmodelled behaviour, scheme, which provides desired motion tasks to the * internal checks, diagnostics, safety issues, commu- considered system. -
Some Simple Chaotic Jerk Functions J
Some simple chaotic jerk functions J. C. Sprotta) Department of Physics, University of Wisconsin, Madison, Wisconsin 53706 ~Received 9 September 1996; accepted 3 January 1997! A numerical examination of third-order, one-dimensional, autonomous, ordinary differential equations with quadratic and cubic nonlinearities has uncovered a number of algebraically simple equations involving time-dependent accelerations ~jerks! that have chaotic solutions. Properties of some of these systems are described, and suggestions are given for further study. © 1997 American Association of Physics Teachers. I. INTRODUCTION ponents and two velocity components since the orbit lies in a plane. The equation of motion is nonlinear because the force One of the most remarkable recent developments in clas- is proportional to the inverse square of the separation. How- sical physics has been the realization that simple nonlinear ever, this system does not exhibit chaos because there are deterministic equations can have unpredictable ~chaotic! two constants of the motion—mechanical energy and angular long-term solutions. Chaos is now thought to be rather com- momentum—which reduce the phase-space dimension from mon in nature, and the study of nonlinear dynamics has four to two. With a third object, such as a second star, the brought new excitement to one of the oldest fields of science. planet’s motion can be chaotic, even when the motions are The widespread availability of inexpensive personal comput- coplanar, because the force on the planet is no longer central, ers has brought many new investigators to the subject, and and its angular momentum is thus not conserved. The three- important research problems are now readily accessible to body problem was known 100 years ago to have chaotic undergraduates.