Ibat 2.0-CIM01C2 Quick Guide
Total Page:16
File Type:pdf, Size:1020Kb
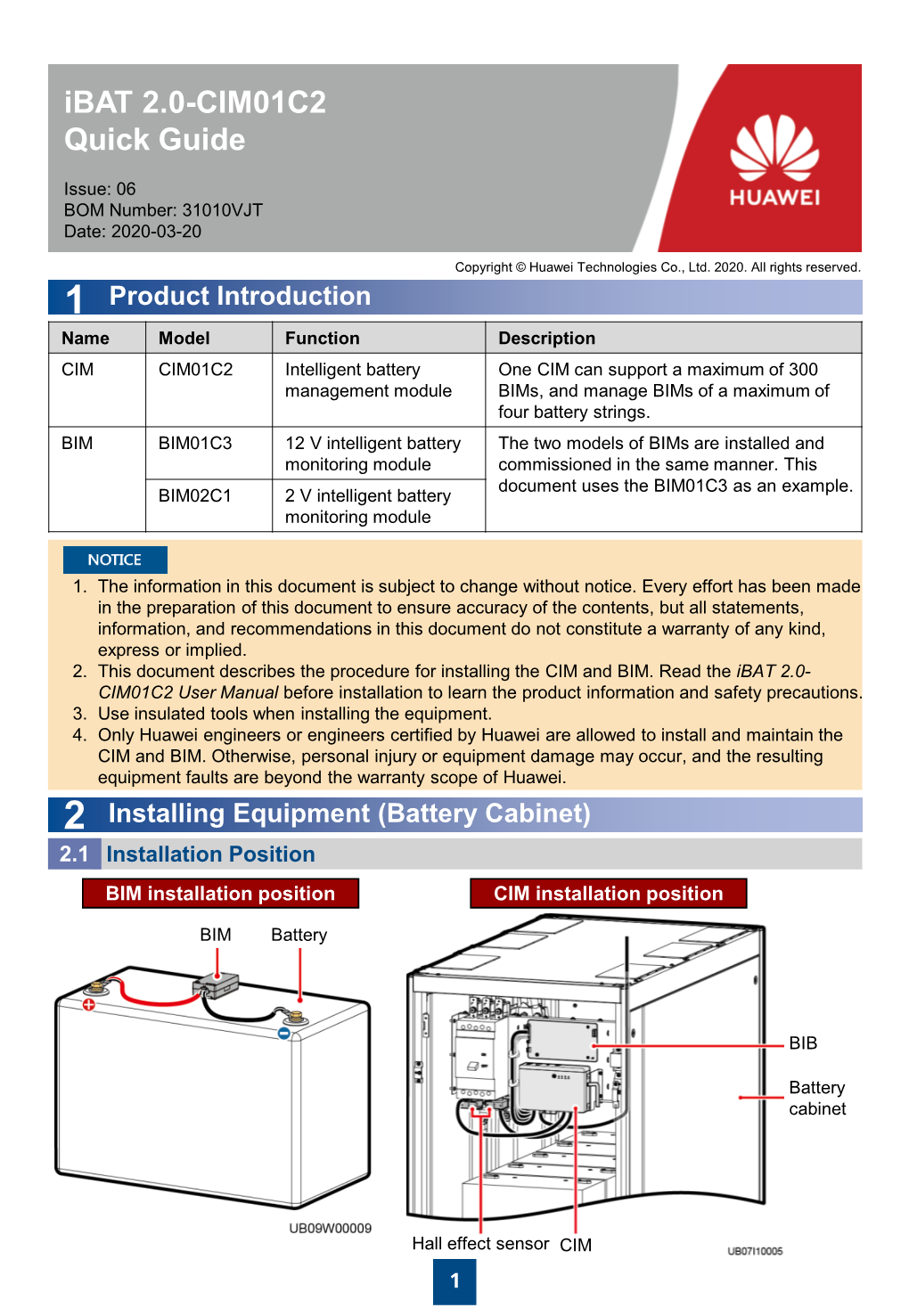
Load more
Recommended publications
-
Revenuesuite from Dmarc
www.beradio.conn May 2005 THE RADIO TECHNOLOGY6E41 D ES RF Engineering Preparations for AM IBOC Trends in Technology Inside automation RevenueSuitefrom dMarc After you've closed the logs, new RevenueSuite starts selling Tap the riches in your remnant inveitory. Ideal for your Scott SS32 or Maestro. Automatically. Effortlessly. Call.* more information. B nADC .11.1-1Nn DIAGNOSTICS I DATASERVICES I SARBANES-OXLEY I REVENUESUITE CHECK OUT OUR LATEST! The NEW AUDIOARTS D-75 DIGITAL RADIO CONSOLE A CLEAN, CLEAR on -air design: straightforward layout, easy tabletop installation, and best of all completely modular. A TRUE plug -and -play radio board from the Wheatstone digital design team! 4--IleAUDIOARTs EAIGIAIEERIAIG sales@wheatstone. corn / tel 252-638-7000 / www.audioarts.net Copyright C 2005 by Wheatstone Corporanon We're Reshaping The Future Of Radio From A Solid Foundation Of Leadership. The newest force in radio was forged from a rich heritage of leadership that is decades strong. We're bringing a breath of fresh air and a re -energized spirit to an industry we helped to build. At Team Harris Radio, we've brought together the industry's largest and most comprehensive range of products, services and people dedicated to advancirg radio.All working together in perfect harmony and focused on the success of your business.From our innovative products to our forward -looking services, management tools and expert support teams, we're dedicated to our mutual future of pioneering and growth. So whether you're audience is around the corner or around the worla, Harris Radio is on the air with the resources you need to succeed. -
Information Library for Solaris 2.6 (Intel Platform Edition)
Information Library for Solaris 2.6 (Intel Platform Edition) Sun Microsystems, Inc. 2550 Garcia Avenue Mountain View, CA 94043-1100 U.S.A. Part No: 805-0037–10 August 1997 Copyright 1997 Sun Microsystems, Inc. 901 San Antonio Road, Palo Alto, California 94303-4900 U.S.A. All rights reserved. This product or document is protected by copyright and distributed under licenses restricting its use, copying, distribution, and decompilation. No part of this product or document may be reproduced in any form by any means without prior written authorization of Sun and its licensors, if any. Third-party software, including font technology, is copyrighted and licensed from Sun suppliers. Parts of the product may be derived from Berkeley BSD systems, licensed from the University of California. UNIX is a registered trademark in the U.S. and other countries, exclusively licensed through X/Open Company, Ltd. Sun, Sun Microsystems, the Sun logo, SunSoft, SunDocs, SunExpress, , JavaSoft, SunOS, Solstice, SunATM, Online: DiskSuite, JumpStart, AnswerBook, AnswerBook2, Java, HotJava, Java Developer Kit, Enterprise Agents, OpenWindows, Power Management, XGL, XIL, SunVideo, SunButtons, SunDial, PEX, NFS, Admintools, AdminSuite, AutoClient, PC Card, ToolTalk, DeskSet, VISUAL, Direct Xlib, CacheFS, WebNFS, Web Start Solaris, and Solstice DiskSuite are trademarks, registered trademarks, or service marks of Sun Microsystems, Inc. in the U.S. and other countries. All SPARC trademarks are used under license and are trademarks or registered trademarks of SPARC International, Inc. in the U.S. and other countries. Products bearing SPARC trademarks are based upon an architecture developed by Sun Microsystems, Inc. PostScript is a trademark of Adobe Systems, Incorporated, which may be registered in certain juridisdictions. -
Automated Software Testing in an Embedded Real-Time System
Final Thesis Automated Software Testing in an Embedded Real-Time System by Johan Andersson and Katrin Andersson LITH-IDA-EX--07/046--SE 2007-08-17 Linköping University Department of Computer and Information Science Final Thesis Automated Software Testing in an Embedded Real-Time System by Johan Andersson and Katrin Andersson LITH-IDA-EX--07/046--SE 2007-08-17 Supervisor:Mariam Kamkar, Linköping University Guido Reinartzt, IVU Traffic Technologies AG Examiner: Mariam Kamkar, Linköping University Datum Avdelning, Institution Date Division, department Institutionen för datavetenskap Department of Computer and 2007-08-16 Information Science Linköpings universitet Språk Rapporttyp ISBN Language Report category Svenska/Swedish Licentiatavhandling ISRN LITH-IDA- EX--07/046--SE X Engelska/English X Examensarbete C-uppsats Serietitel och serienummer ISSN D-uppsats Title of series, numbering Övrig rapport URL för elektronisk version http://www.ep.liu.se/ Titel Title Automated Software Testing in an Embedded Real-Time System Författare Author Johan Andersson Katrin Andersson Sammanfattning Abstract Today, automated software testing has been implemented successfully in many systems, howev- er there does still exist relatively unexplored areas as how automated testing can be implemented in a real-time embedded system. This problem has been the foundation for the work in this master thesis, to investigate the possibility to implement an automated software testing process for the testing of an embedded real-time system at IVU Traffic Technologies AG in Aachen, Germany. The system that has been the test object is the on board system i.box. This report contains the result of a literature study in order to present the foundation behind the solution to the problem of the thesis. -
(12) Patent Application Publication (10) Pub. No.: US 2007/0206737 A1 Hickman (43) Pub
US 20070206737A1 (19) United States (12) Patent Application Publication (10) Pub. No.: US 2007/0206737 A1 Hickman (43) Pub. Date: Sep. 6, 2007 (54) METHOD AND APPARATUS FOR (52) U.S. Cl. .......................................................... 379/93.02 ACCESSING AWIDE AREANETWORK (76) Inventor: Paul L. Hickman, Los Altos Hills, CA (57)57 ABSTRACT (US) A Voice web browser system includes a telephone, an access system coupled to a TCP/IP network, a telephone system ESOF6.s' NicLLECTUAL coupling the telephone to the access system, and a speech PROPERTY to-text system for “reading text that had been sent over the STRATEGIES GROUP PC dba TIPS GROUP TCP/IP network to the telephone user. Preferably, the access P. O. BOX 1639 system receives TCP/IP packets from web pages accessible iOS ALTOS, CA 94023-1639 (US) over the TCP/IP network and parses the HTML code of the 9 web pages into text and non-text portions. Such that the text (21) Appl. No.: 11/606,400 portion can be read to the telephone U.S. A computer implemented process for obtaining web page information (22) Filed: Nov. 27, 2006 over a TCP/IP network includes implementing a connection of a telephone user to an access system that is coupled to a Related U.S. Application Data TCP/IP network, detecting a selection of at least one navi gation command by the telephone user to access a web page (63) Continuation of application No. 09/633,497 filed on accessible over the TCP/IP network, and navigating over the Aug. 7, E.R. N C.E.", a TCP/IP network to the web page in response to the naviga continuation of application No. -
Tuning Into a Radio Station
Details on AM/FM reception Tuning into a Radio Station Tuning automatically 1. Press TUNER on the main unit several times to select either "AM" or "FM". 2. Press TUNING MODE so that the "AUTO" indicator on the display lights. 3. Press TUNING to start automatic tuning. Searching automatically stops when a station is found. When tuned into a radio station, the " TUNED " indicator on the display lights. When tuned into an FM radio station, the "FM STEREO" indicator lights. No sound is output while the " TUNED " indicator is off. When the signal from an FM radio station is weak: Radio wave may be weak depending on the building structure and environmental conditions. In that case, perform the manual tuning procedure as explained in the next section, "Tuning manually", to manually select the desired station. Tuning manually 1. Press TUNER on the main unit several times to select either "AM" or "FM". 2. Press TUNING MODE so that the "AUTO" indicator on the display goes off. 3. Press TUNING to select the desired radio station. The frequency changes by 1 step each time you press the button. The frequency changes continuously if the button is held down and stops when the button is released. Tune by looking at the display. To return to automatic tuning: Press TUNING MODE on the main unit again. The unit automatically tunes into a radio station. Normally "AUTO" should be displayed. Tuning to the frequency directly It allows you to directly enter the frequency of the radio station you want to listen to. 1. Press TUNER on the remote controller several times to select either "AM" or "FM". -
Note to Users
NOTE TO USERS The original manuscript received by UMI contains pages with indistinct andlor slanted print. Pages were microfilmed as received. This reproduction is the best copy available Time-based Management and Visualization of Personal Electronic Information Kelvin Shek Yiu A thesis submitted in conformity with the requirements for the degree of Master of Applied Science Graduate Department of Electncal and Cornputer Engineering University of Toronto O Copyright by Kelvin Shek Yiu, 1997. National Library Bibliothéque nationale 1*1 of Canada du Canada Acquisitions and Acquisitions et Bibliographie Seivices services bibliographiques 395 Wellington Street 395. rue Wellington OtiawaON KlAOlr(4 OttawaON K1AON4 Canada Canada The author has granted a non- L'auteur a accordé une licence non exclusive licence allowing the exclusive permettant à la National Library of Canada to Bibliothèque nationale du Canada de reproduce, loan, distribute or sell reproduire, prêter, distribuer ou copies of ths thesis in microform, vendre des copies de cette thèse sous paper or electronic formats. la forme de microfiche/film, de reproduction sur papier ou sur format électronique. The author retains ownershp of the L'auteur conserve la propriété du copyright in ths thesis. Neither the droit d'auteur qui protège cette thèse. thesis nor substantial extracts fiom it Ni la thèse ni des extraits substantiels may be printed or otheMrise de celle-ci ne doivent être imprimés reproduced without the author's ou autrement reproduits sans son permission. autorisation. Abstract TimeStore is a personal information management system that takes advantage of human autobiographical memory. information such as email messages, tasks, calendar events, and notes are plotted on a two dimensional graph where time is displayed dong the x-axis and the names of message sender are listed dong the y-mis. -
The Internet and World-Wide-Web: Potential Benefits to Rural Schools
DOCUMENT RESUME ED 401 064 RC 020 760 AUTHOR Barker, Bruce O. TITLE The Internet and World-Wide-Web: Potential Benefits to Rural Schools. PUB DATE Oct 95 NOTE 9p.; Presented at the Annual Conference of the National Rural Education Association (87th, Salt Lake City, UT, October 4-8, 1995). PUB TYPE Speeches/Conference Papers (150) Information Analyses (070) Viewpoints (Opinion/Position Papers, Essays, etc.) (120) EDRS PRICE MF01/PC01 Plus Postage. DESCRIPTORS *Access to Information; *Computer Networks; *Computer Uses in Education; *Educational Benefits; Electronic Mail; Elementary Secondary Education; Gateway Systems; Information Networks; *Internet; *Online Systems; Rural Schools; World Wide Web IDENTIFIERS National Information Infrastructure ABSTRACT The Internet is a decentralized collection of computer networks managed by separate groups using a common set of technical standards. The Internet has tremendous potential as an educational resource by providing access to networking through worldwide electronic mail, various databases, and electronic bulletin boards; collaborative investigation across geographic and political boundaries; and a wide range of resources that can be used at times convenient to the user. The Internet's resources can be grouped into three categories: messaging, which includes e-mail and discussion groups; remote login, which permits a user to access another computer's information; and file exchange, the transfer of information accessed from another computer to the user's computer. The Internet can benefit small rural schools by providing access to the same information heretofore available only to affluent schools. Drawbacks include slow access, the "additive" nature of the Internet, and the fact that the Internet is uncensored. Some schools have policies that permit access to controversial information only when permission is granted and the purpose and educational value have been identified. -
Choosing the Radio Station
AM/FM Radio Receiving Function Choosing the Radio Station Tuning into stations automatically 1. Press AM or FM on the unit to select either "AM" or "FM". 2. Press TUNING MODE, so that the "AUTO" indicator on the display lights. 3. Press TUNING . The automatic search for a radio station starts. Searching stops when one is found. When tuned into a radio station, the " TUNED " lights on the display lights. If FM stereo broadcasting is tuned, the "FM STEREO" indicator lights. No sound is output while the " TUNED " indicator is off. When the signal from an FM radio station is weak: Depending on the structure of the building and the surrounding environment, the radio wave condition is different and it may be impossible to get good reception. In that case, manually tune into the radio station of your choice by referring to the next section. Tuning into stations manually 1. Press AM or FM on the unit to select either "AM" or "FM". 2. Press TUNING MODE, so that the "AUTO" indicator on the display goes off. 3. Press and hold TUNING to select the desired radio station. The frequency changes by 1 step each time you press the button. The frequency changes continuously if the button is held down and stops when released. Tune by looking at the display. To return to the method for tuning into stations automatically: Press TUNING MODE again on the main unit. FM stereo broadcasting is automatically tuned. Normally, leave the indicator in "AUTO". Tuning into stations by frequency It allows you to directly enter the frequency of the radio station you want to listen to. -
Lesson 1 - Computer Networks and Internet - Overview
Computer Networking and Management Computer Networking and Management Lesson 1 - Computer Networks and Internet - Overview Introduction | What is the Internet? | What is a protocol? | The Network Edge | The Network Core | Access Networks | Physical Media | Delay and Loss in Packet-Switched Networks | Protocol Layers and Their Service Models | Internet History Lesson Outline Introduction Physical Media What Is the Internet:’ Nuts And Bolts View' Some Popular Physical Media What Is the Internet: A Service View Twisted Pair Copper Wire What Is A Protocol? Coaxial Cable A Human Analogy Broadband Coaxial Cable A Human Protocol and a Computer Network Fibre Optics Protocol Terrestrial and Satellite Radio Channels Network Protocols Delay and Loss in Packet-Switched Networks The Network Edge Types of Delay End Systems, Clients and Servers Comparing Transmission and Propagation Delay End-System Interaction Queuing Delay (Revisited) Connectionless and Connection -Oriented Services Real Internet Delays and Routes Connection-Oriented Service Protocol Layers and Their Service Models Connectionless Service Layer Functions The Network Core The Internet Protocol Stack, And Protocol Data Units Circuit Switching Application Layer Packet Switching Transport Layer Packet Switching Versus Circuit Switching Network Layer Routing Link Layer Virtual Circuit Networks Physical Layer Datagram Networks Internet History Access Networks Development and Demonstration of Early Packet Residential Access Networks Switching Principles: 1961-1972 A Hybrid Fire -Coax Access Network Internetworking and New Proprietary Networks: Company Access Networks 1972-1980 Mobile Access Networks Metcalfe’s Original Conception of the Ethernet Home Networks A Proliferation of Networks: 1980 -1990 Commercialization and the Web: The 1990s GOTO TOP Introduction Page 1 of 44 Computer Networking and Management This lesson provides a broad overview of the Computer Networking and the Internet. -
IBOX V4 Manuel De Mise En Service Version 4
IBOX V4 Manuel de mise en service Version 4 1. Introduction Merci d'avoir choisi IBOX V4 pour vos applications de contrôle d'accès. Ce manuel contient les informations détaillées pour l'installation de votre IBOX V4. IBOX V4 est un serveur intégrant une application professionnelle destinée à la gestion d'équipements de contrôle d'accès et d’automatismes. Ces équipements sont les suivants: Contrôleur pour 2 lecteurs de badges réf. XM200 et modules d’extension 8E/8S XM8 (maxi. 4 modules XM8 par contrôleur XM200). Votre environnement de travail est basé sur une interface WEB qui vous permettra d'accéder à l'IBOX V4 depuis n'importe quel poste de travail (sur réseau local ou distant) à l’aide de votre navigateur WEB MOZILLA FIREFOX, GOOGLE CHROME, SAFARI ou OPERA (Internet Explorer n’est pas compatible). L'application utilisée est développée sur Linux pour vous garantir une stabilité à toute épreuve. Tableau des possibilités offertes par les équipements de contrôle d'accès XM200 XM8 Utilisateurs 16 000 - Evénements 8 000 - Entrées alarme 2 8 TOR Sorties alarme 2 8 relais 0,5A Bus de terrain RS485 RS485 Tableau des possibilités offertes par IBOX V4 Utilisateurs 16 000 Evénements Illimité – Dépend de la taille du disque dur Opérateurs Illimité – Dépend de la taille du disque dur Exports Format CSV Sauvegardes Paramétrables - En local et sur serveur FTP ou RSYNC Connectivité 1 x TCP/IP accès interface de gestion - 1 x TCP/IP dédié pour XM200DiP Bus de terrain 1 x RS485 extensible à 8 avec distributeur D8RS IBOX V.4.1.1 - jan. -
Washington Apple Pi Journal, March-April 2000
March I April 2000 $4.95 The Journal of Washington Apple Pi, Ltd. Not Lawrence's MacWorld _ 5 Warner Brothers Scene Preview _ ____ _ __ 20 Font of Wisdom _____ 21 Print Explosion _ _ ___ 24 Keeping Your Digital Images VAG Rounded Bold, Zapf Dingbats Organized 27 PUPIL PIU!CING WllU VDUYt Pll!CTllRO t'IUVIUI!' Ull ITC Anna Nikon CoolPix 950 _ ___ 30 8QU~ The •hort und F at llll to Madrone EXPRESSNET _____ 38 fRuiTcAkE DisposAl WE doN'T ASk, NEitlt ER sltould yo Peignot Demi Learning to Network with the CONTAINER Ina Russell Square Air Port 42 Linux on Virtual PC _ _ __ 44 DoubleClick _ _ _ __ 78 Surfer Beware 111 _____ 61 Bethesda Computers & Networks, Inc. A Tradition of Sales, Sen1ice & Support - 16 years experience, 24 Hour Tum Around 301-652-5108 iMac $1,199 ( /~/ i?>' ~ ~ 333 Mliz,32 MB RAM 56K Modem, 6GB HD HP LJ 4000N printer $1,399 17 Pages per 111i11111 e, Jet Direct card \il~'f/ (Etliem et card), 1200dpi, 8 MB RAM PowerMac G3 $1,599 PowerMac G3 300 Mliz, 64 Mil RAM 6Gl1 HD, 24X CD-ROM PowerMac G3 $2,499 PowerMac G3 350 Mliz, 128 MB RAM, Monitors extra Zip Drive, 12GB HD, 24X CD-ROM 4350 East West Highway, Suite IOI Apple Authorized VAR Dealer and Service Center Bethesda, MD 20814 We service Tektronix, HP. PC's, Mac clones Email: bcnc@s ysuet.net Data Recovery and Service Contract Services Weekdays 10 am- 6 pm, Sat. 1 I am -4pm World's Greatest Books! 90+ Updaters for 6S 9! Now you can own 100 OS 9 adds dozens of of the world's greatest features to the Macin books for only $39.95! tosh, but you must Here are the most signifi update many software cant writings of Shake speare, Mark Twain, applications and exten Emily Bronte, Arthur sions to ensure compat Conan Doyle, Jack Lon ibility with OS 9. -
Chikyu Kankyo Taisaku Gijutsu No Kenkyu Joho Netw
\rirj .-r'l- O’ 7 NEDO-GET-9615 6 \ ¥« 9 3 H MTMiTlQjJ OF THIS DOCUMENT IS UNUMffES foreign ms paoHiBHEDpr- 0T JL % J\s — • m # a# DISCLAIMER Portions of this document may be illegible electronic image products. Images are produced from the best available original document. 8 NEDO-GET-961 5 itti # ti # CD #22 « 9 ¥ 3 MUSA Ab # # ta # # R # # % # (NEDo) m-rn&A (RITE) r%m 6. jo^T, 1997 # 12 ^ (c# 3 igwm#rm&##Tim#f a c 2: & & 6o 9 ##wwm - - ###### - - X%TA#m(DL< - ##A ^LT^(CXy.%A^#AL^^(DmA% y-%$rM^A4cL. RITE(D^ (ychfxym (DfM#tcj;9x;%TA#A#<Dl5@A#&%W4;: L^. tc&ip, X/<—(DM### 9 3 ^ mmmA Oj p S e 5P % # # # a& # 4 E- m= 3| Nkffl^-a 4 S ffl ifc 4 ~a ^ Wr 4 4 # (%>*#: 1 ^il # rr # V2 W 3$ SF 4$ m B > mil & M 4 4 <3 [ f HA $= v* S # X" M I S tlro^ m"O Tm 14 X H * s 3¥ s| ^ # w o o o § & m S Jan m m ll! X- $ H Wt § 4 H> 14 $ # # # X # # H i JBD ## r iin £fa u # % ^ ##0 4 % V °> 4 [ m m S $ 4 m # 3f #H 4 % v ..tESsss 4 # #S Si V # 4 $ Si yUin -\ 4 V 4 4 V 4 0 m m $ n 2p i ^ #H+ # ^ 4 [ # a ft $^ 14 * V B S's*r 4 4 $ 4 ^4 .III mill mill Xm V 4 M 5m f mi n£ ^ M> W> # 4 4 4 Xm pj % $ B # 4 f @ s# n ^ am am am # m # tw 4 4 4 Xm S _ ^ ^ ^ r # % s Ht Xm )# Xm 4 4i # )# JU ## (SUMARRY) ...................................................................................................