Supportability Challenges, Metrics, and Key Decisions for Future Human Spaceflight
Total Page:16
File Type:pdf, Size:1020Kb
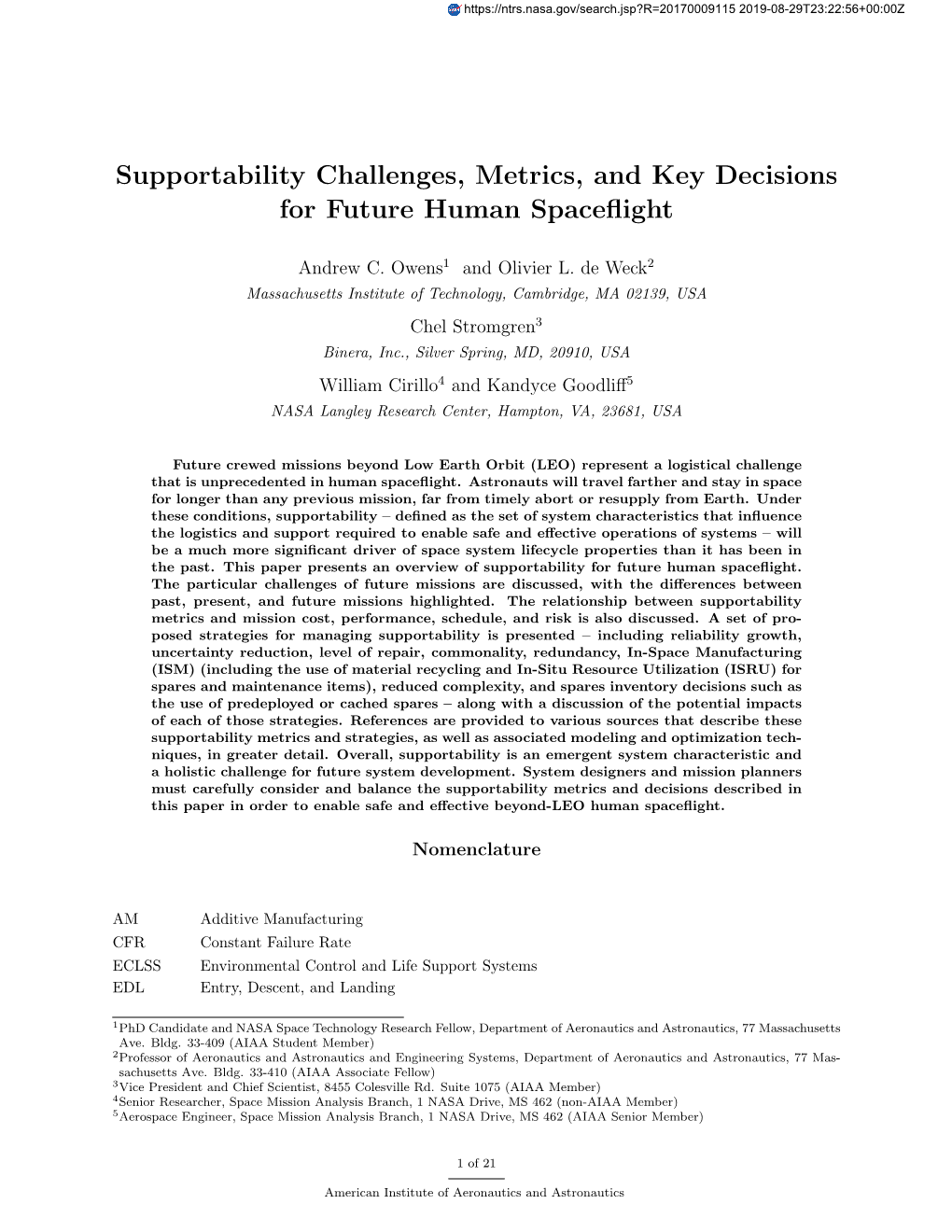
Load more
Recommended publications
-
Status of International Space Station
NASA and the International Space Station Sam Scimemi Director, International Space Station HEO NAC Human Exploration and Operations Kennedy Space Center NASA Headquarters December 10, 2013 The Internaonal Space Staon is essen+al to mee+ng the Naon’s goals in space Returning benefits to humanity through research Enabling a self-sustaining commercial LEO market Laying the foundaon for long-duraon spaceflight beyond LEO Leading the world in an exploraon partnership 2 3 “Time works so hard for us, if only we can let it.” Tana French Time to complete a study in orbit – 2 weeks to 5+ years Time from comple+on of study in orbit to first publicaon – 1 to 3 years for majority of inves+gaons Time from publicaon or patent to product being in the marketplace – 3 to 20 years (shorter for technologies, longer for drug development) 4 Historical Micro-G Research Perspec+ve Exploratory Survey Applicaon 1994-1998 1998 2011 1973-1979 1981-2011 Assembly Complete ~1.5 years of produc+ve on-orbit micro-g research M. Uhran, Posi+oning the ISS for the U+lizaon Era 5 Some of the Benefits to Humanity To-date • Discoveries – Cool flames vaporize without visible flame in space (Combustion and Flame) – Human immune cells adapt to weightlessness (J. Leukocyte Biology) – MAXI black hole swallowing star (Nature) – Vision impacts and intracranial pressure (Opthalmology) – Microbial virulence (Proc. Nat. Acad. Sci.) • Technology Spinoffs – NeuroArm image-guided robot for neurosurgery translates Canadarm • Results with poten2al human benefits technology to the operation room -
A Researcher's Guide to Earth Observations
National Aeronautics and Space Administration A Researcher’s Guide to: Earth Observations This International Space Station (ISS) Researcher’s Guide is published by the NASA ISS Program Science Office. Authors: William L. Stefanov, Ph.D. Lindsey A. Jones Atalanda K. Cameron Lisa A. Vanderbloemen, Ph.D Cynthia A. Evans, Ph.D. Executive Editor: Bryan Dansberry Technical Editor: Carrie Gilder Designer: Cory Duke Published: June 11, 2013 Revision: January 2020 Cover and back cover: a. Photograph of the Japanese Experiment Module Exposed Facility (JEM-EF). This photo was taken using External High Definition Camera (EHDC) 1 during Expedition 56 on June 4, 2018. b. Photograph of the Momotombo Volcano taken on July 10, 2018. This active stratovolcano is located in western Nicaragua and was described as “the smoking terror” in 1902. The geothermal field that surrounds this volcano creates ideal conditions to produce thermal renewable energy. c. Photograph of the Betsiboka River Delta in Madagascar taken on June 29, 2018. This river is comprised of interwoven channels carrying sediment from the mountains into Bombetoka Bay and the Mozambique Channel. The heavy islands of built-up sediment were formed as a result of heavy deforestation on Madagascar since the 1950s. 2 The Lab is Open Orbiting the Earth at almost 5 miles per second, a structure exists that is nearly the size of a football field and weighs almost a million pounds. The International Space Station (ISS) is a testament to international cooperation and significant achievements in engineering. Beyond all of this, the ISS is a truly unique research platform. The possibilities of what can be discovered by conducting research on the ISS are endless and have the potential to contribute to the greater good of life on Earth and inspire generations of researchers to come. -
Ground Testing for Development of Environmental Control and Life Support Systems for Long Duration Human Space Exploration Missions
48th International Conference on Environmental Systems ICES-2018-5 8-12 July 2018, Albuquerque, New Mexico Ground Testing for Development of Environmental Control and Life Support Systems for Long Duration Human Space Exploration Missions Donald L. Henninger, PhD1 NASA Johnson Space Center, 2101 NASA Parkway, Houston, Texas, 77058 ECLS systems for very long-duration human missions to deep space will be designed to operate reliably for many years and will never be returned to Earth. The need for high reliability/maintainability is driven by unsympathetic abort scenarios. Abort from a Mars mission could be as long as 450 days to return to Earth. Simply put, the goal of an ECLSS is to duplicate the functions the Earth provides in terms of human living and working on our home planet but without the benefit of the Earth’s large buffers – the atmospheres, the oceans and land masses. With small buffers, a space-based ECLSS must operate as a true dynamic system rather than independent processors taking things from tanks, processing them, and then returning them to product tanks. Vital is a development process that allows for a logical sequence of validating successful development (maturation) in a stepwise manner with key performance parameters (KPPs) at each step; especially KPPs for technologies evaluated in a full systems context with human crews on Earth and on space platforms such as the International Space Station (ISS). This paper will explore the implications of such an approach to ECLSS development and the types and roles of ground and space-based testing necessary to develop a highly reliable life support system for long duration human exploration missions. -
Humanity and Space
10/17/2012!! !!!!!! Project Number: MH-1207 Humanity and Space An Interactive Qualifying Project Submitted to WORCESTER POLYTECHNIC INSTITUTE In partial fulfillment for the Degree of Bachelor of Science by: Matthew Beck Jillian Chalke Matthew Chase Julia Rugo Professor Mayer H. Humi, Project Advisor Abstract Our IQP investigates the possible functionality of another celestial body as an alternate home for mankind. This project explores the necessary technological advances for moving forward into the future of space travel and human development on the Moon and Mars. Mars is the optimal candidate for future human colonization and a stepping stone towards humanity’s expansion into outer space. Our group concluded space travel and interplanetary exploration is possible, however international political cooperation and stability is necessary for such accomplishments. 2 Executive Summary This report provides insight into extraterrestrial exploration and colonization with regards to technology and human biology. Multiple locations have been taken into consideration for potential development, with such qualifying specifications as resources, atmospheric conditions, hazards, and the environment. Methods of analysis include essential research through online media and library resources, an interview with NASA about the upcoming Curiosity mission to Mars, and the assessment of data through mathematical equations. Our findings concerning the human aspect of space exploration state that humanity is not yet ready politically and will not be able to biologically withstand the hazards of long-term space travel. Additionally, in the field of robotics, we have the necessary hardware to implement adequate operational systems yet humanity lacks the software to implement rudimentary Artificial Intelligence. Findings regarding the physics behind rocketry and space navigation have revealed that the science of spacecraft is well-established. -
Agenzia Spaziale Italiana Piano Triennale Delle Attività 2017-2019
Agenzia Spaziale Italiana Piano Triennale delle Attività 2017-2019 Piano Triennale delle Attività 2017-2019 Sommario 1 ATTIVITÀ SVOLTE NEL PERIODO PRECEDENTE 5 1.1 OSSERVAZIONE DELLA TERRA 5 1.2 TELECOMUNICAZIONI, NAVIGAZIONE E SALVAGUARDIA DELLO SPAZIO 9 1.3 LANCIATORI TRASPORTO SPAZIALE E PROGRAMMA PRORA 11 1.4 VOLO UMANO E MICROGRAVITÀ 12 1.5 ESPLORAZIONE E OSSERVAZIONE DELL’UNIVERSO 13 2 STRATEGIE E POLITICHE 16 2.1 LA NUOVA POLITICA SPAZIALE NAZIONALE 16 2.2 PIANO STRATEGICO NAZIONALE SULLA SPACE ECONOMY 16 2.2.1 Attuazione del Piano Space Economy e coinvolgimento dell’ASI 17 2.3 IL PIANO NAZIONALE DELLA RICERCA 19 2.4 IL DOCUMENTO DI VISIONE STRATEGICA 20 2.5 IL PIANO INTEGRATO DELLE PERFORMANCE 22 2.6 SEMPLIFICAZIONE DELLE ATTIVITÀ DEGLI ENTI PUBBLICI DI RICERCA 24 3 RICERCA E SVILUPPO PER LE APPLICAZIONI DELLA NEW SPACE ECONOMY 28 3.1 MIRROR GALILEO 28 3.2 MIRROR COPERNICUS 30 3.3 PROGRAMMI NAZIONALI PRS GALILEO 33 3.4 PROGRAMMA DI SUPPORTO A SST 35 4 INFRASTRUTTURE E TECNOLOGIE PER LA NEW SPACE ECONOMY 37 4.1 INFRASTRUTTURE SPAZIALI STRATEGICHE PER IL CITTADINO E IL SISTEMA PRODUTTIVO 37 4.1.1 Infrastrutture per Osservazione della Terra 37 4.1.2 Infrastrutture di Telecomunicazioni 39 4.1.3 Infrastrutture per la Navigazione Satellitare 43 4.2 INFRASTRUTTURE SPAZIALI PER L’ESPLORAZIONE UMANA E ROBOTICA DELLO SPAZIO 44 4.2.1 ISS e altre strutture per ricerca in microgravità 44 4.2.2 Infrastrutture per l’esplorazione umana oltre la Low Earth Orbit (LEO) 46 4.3 INFRASTRUTTURE DI LANCIO E RIENTRO A TERRA 48 4.3.1 Sistema Vega 48 4.3.2 -
2020 to 2021 Overview
50th International Conference on Environmental Systems ICES-2021-384 12-15 July 2021 NASA Environmental Control and Life Support Technology Development for Exploration: 2020 to 2021 Overview James Lee Broyan, Jr.,1 Laura Shaw2, Melissa McKinley3, Catlin Meyer4, and Michael K. Ewert5 NASA Johnson Space Center, Houston, Texas 77058 Walter F Schneider6 NASA Marshall Space Flight Center, Huntsville, AL, 35812 Marit Meyer7, Gary A. Ruff8 NASA Glenn Research Center, Cleveland, OH 44135 Andrew C. Owens9 NASA Langley Research Center, Hampton, VA 23681 and Robyn L. Gatens10 NASA Headquarters, Washington, D.C. 20546 This paper provides an overview of NASA supported activities developing Environmental Control and Life Support (ECLSS) technologies in the following capability areas: life support, environmental monitoring, fire safety, and logistics. NASA has been refining technology needs for deep space missions including Gateway, lunar surface, Mars transit, and Mars surface missions. Validating technologies in relevant environments, both in low earth orbit (LEO) and ground tests is critical in understanding technology performance and long duration performance. On-orbit and ground tests inform NASA’s technology decisions to fill exploration gaps. NASA has multiple technology projects across the technology readiness spectrum with potential to fill or partially fill exploration gaps. For each capability area, this paper will describe select capability gaps, NASA technology project maturation over the past year, and how key performance parameters (KPPs) are being used to measure the degree of capability gap closure. KPPs are evolving but they still provide a useful measure in communicating progress and identifying development needs to 1 ECLSS-CHP Systems Capability Lead Deputy, Crew & Thermal Systems Division, 2101 NASA Parkway, Mail Stop EC7, Houston, TX, 77058. -
Research Project Report 2 ... Final3.Pdf
Multimodal learning analytics on sustained attention by measuring ambient noise Jeffrey Pronk Responsible Professor: Marcus Specht (PhD) Supervisor: Yoon Lee (PhD candidate) Peer group members: Giuseppe Deininger (BSc student) Jurriaan Den Toonder (BSc student) Sven van der Voort (BSc student) I Abstract In this research, a learner’s sustained attention in the remote learning context will be studied by collecting data from different sensors. By combining the results of these sensors in a multi-modal analytics tool, the estimation of the learner’s sustained at- tention can hopefully be improved. This research will mainly focus on microphone recordings of ambient sound in a learners room. The main research question of this re- search was "How can ambient noise sensing aid in a multi-modal analytics tool to track sustained attention?". The multi-modal learning analytics tool, if accurate enough, could potentially be used by teachers to make their material more engaging and could help learner’s to keep their focus while performing a learning task (Schneider et al., 2015). The research resulted in a model with 61% accuracy. This percentage needs to be further researched, since because of the COVID situation, not enough data could be collected to train the model. Because of the relatively low accuracy of the model, it was found that ambient noise sensing can aid the multi-modal analytics tool to some extent by adding some data-points it is certain about, when the mobile movement tracking model does not detect a distraction. If the model improves in future research, the model could be able to help mobile movement tracking model, even if the mobile movement tracking model already predicts a distraction with bigger then 50% certainty. -
Space Station” IMAX Film
“Space Station” IMAX Film Theme: Learning to Work, and Live, in Space The educational value of NASM Theater programming is that the stunning visual images displayed engage the interest and desire to learn in students of all ages. The programs do not substitute for an in-depth learning experience, but they do facilitate learning and provide a framework for additional study elaborations, both as part of the Museum visit and afterward. See the “Alignment with Standards” table for details regarding how “Space Station!” and its associated classroom extensions, meet specific national standards of learning. What you will see in the “Space Station” program: • How astronauts train • What it is like to live and work in Space aboard the International Space Station (ISS) Things to look for when watching “Space Station”: • Notice how quickly astronauts adapt to free fall conditions and life on the ISS • Reasons humans go to the cost, risk, and effort to work in Space • The importance of “the little things” in keeping astronauts productive so far from home Learning Elaboration While Visiting the National Air and Space Museum Perhaps the first stop to expand on your “Space Station” experience should be the Skylab Orbiting Laboratory, entered from the second floor overlooking the Space Race Gallery. Skylab was America’s first space station, launched in 1973 and visited by three different three-man crews. It fell back to Earth in 1979. The Skylab on display was the back-up for the Skylab that was launched; the Skylab program was cancelled before it was -
The Next Steps for Environmental Control and Life Support Systems Development for Deep Space Exploration
48th International Conference on Environmental Systems ICES-2018-276 8-12 July 2018, Albuquerque, New Mexico The Next Steps for Environmental Control and Life Support Systems Development for Deep Space Exploration Mark Jernigan1 NASA Johnson Space Center, Houston, TX 77058 Robyn Gatens2 and Jitendra Joshi3 NASA Headquarters, Washington, D.C. 20546 and Jay Perry4 NASA Marshall Space Flight Center, Huntsville, AL 35812 Throughout the life of the International Space Station (ISS), NASA has developed, deliv- ered and operated a suite of progressively more capable environmental control and life support system (ECLSS) components and assemblies. These efforts have resulted in substan- tially reducing the supply chain necessary to sustain crews in flight and garnering invaluable lessons for sustained long term operations of the equipment. Currently, the ISS provides a unique platform for understanding the effects of the environment on the hardware. NASA’s strategy, already underway, is to evolve the ISS ECLSS into the Exploration ECLSS and perform a long-duration demonstration on ISS in preparation for deep space missions. This includes demonstrations of upgrades and/or new capabilities for waste management, atmos- phere revitalization, water recovery, and environmental monitoring. Within the Advanced Exploration Systems Program under the Next Space Technologies for Exploration Partner- ships (NextSTEP) model, NASA intends to revise the architecture developed for ISS to make the systems completely independent of the Earth supply chain for the duration of a deep space crewed mission by increasing robustness, including prospective system monitoring to anticipate failures, designing for maintenance, repair and refurbishment, reducing spare part count through use of common components, and grouping subsystems into modular pal- lets to minimize interfaces and reduce complexity. -
Status of ISS Water Management and Recovery
Status of ISS Water Management and Recovery Layne Carter1 NASA Marshall Space Flight Center, Huntsville, AL 35812 Christopher Brown2 NASA Johnson Space Center, Houston, TX 77058 Nicole Orozco3 The Boeing Company, Houston, TX 77058 Water management on ISS is responsible for the provision of water to the crew for drinking water, food preparation, and hygiene, to the Oxygen Generation System (OGS) for oxygen production via electrolysis, to the Waste & Hygiene Compartment (WHC) for flush water, and for experiments on ISS. This paper summarizes water management activities on the ISS US Segment, and provides a status of the performance and issues related to the operation of the Water Processor Assembly (WPA) and Urine Processor Assembly (UPA). This paper summarizes the on-orbit status as of June 2013, and describes the technical challenges encountered and lessons learned over the past year. I. Introduction he International Space Station (ISS) Water Recovery and Management (WRM) System insures availability of T potable water for crew drinking and hygiene, oxygen generation, urinal flush water, and payloads as required. To support this function, waste water is collected in the form of crew urine, humidity condensate, and Sabatier product water, and subsequently processed by the Water Recovery System (WRS) to potable water. This product water is provided to the potable bus for the various users, and is stored in water bags for future use when the potable bus needs supplementing. The WRS is comprised of the Urine Processor Assembly (UPA) and Water Processor Assembly (WPA), which are located in two ISPR racks, named WRS#1 and WRS#2. -
Case Studies in Crewed Spacecraft Environmental Control and Life Support System Process Compatibility and Cabin Environmental Impact
https://ntrs.nasa.gov/search.jsp?R=20180002400 2019-08-29T17:42:57+00:00Z National Aeronautics and NASA/TP—2017–219846 Space Administration IS02 George C. Marshall Space Flight Center Huntsville, Alabama 35812 Case Studies in Crewed Spacecraft Environmental Control and Life Support System Process Compatibility and Cabin Environmental Impact J.L. Perry Marshall Space Flight Center, Huntsville, Alabama December 2017 The NASA STI Program…in Profile Since its founding, NASA has been dedicated to the • CONFERENCE PUBLICATION. Collected advancement of aeronautics and space science. The papers from scientific and technical conferences, NASA Scientific and Technical Information (STI) symposia, seminars, or other meetings sponsored Program Office plays a key part in helping NASA or cosponsored by NASA. maintain this important role. • SPECIAL PUBLICATION. Scientific, technical, The NASA STI Program Office is operated by or historical information from NASA programs, Langley Research Center, the lead center for projects, and mission, often concerned with NASA’s scientific and technical information. The subjects having substantial public interest. NASA STI Program Office provides access to the NASA STI Database, the largest collection of • TECHNICAL TRANSLATION. aeronautical and space science STI in the world. English-language translations of foreign The Program Office is also NASA’s institutional scientific and technical material pertinent to mechanism for disseminating the results of its NASA’s mission. research and development activities. These results are published by NASA in the NASA STI Report Specialized services that complement the STI Series, which includes the following report types: Program Office’s diverse offerings include creating custom thesauri, building customized databases, • TECHNICAL PUBLICATION. -
Developing a LSS for FP Into Deep Space Final
Developing an Advanced Life Support System for the Flexible Path into Deep Space Harry W. Jones* and Mark H. Kliss† NASA Ames Research Center, Moffett Field, CA, 94035-0001 Long duration human missions beyond low Earth orbit, such as a permanent lunar base, an asteroid rendezvous, or exploring Mars, will use recycling life support systems to preclude supplying large amounts of metabolic consumables. The International Space Station (ISS) life support design provides a historic guiding basis for future systems, but both its system architecture and the subsystem technologies should be reconsidered. Different technologies for the functional subsystems have been investigated and some past alternates appear better for flexible path destinations beyond low Earth orbit. There is a need to develop more capable technologies that provide lower mass, increased closure, and higher reliability. A major objective of redesigning the life support system for the flexible path is achieving the maintainability and ultra-reliability necessary for deep space operations. Nomenclature 2BMS = Two Bed Molecular Sieve 4BMS = Four Bed Molecular Sieve AES = Air Evaporation System ALS = Advanced Life Support ARS = Atmosphere Revitalization System AWS = Air and Water System CDRA = Carbon Dioxide Removal Assembly cm = Crew member ECLSS = Environmental Control and Life Support Systems EDI = Electrodeionization EVA = Extravehicular Activity ESM = Equivalent System Mass ISS = International Space Station LCC = Life Cycle Cost LEO = Low Earth Orbit LOC = Loss of Crew NASA