Detection of Microcracks in Concrete Cured at Elevated Temperature
Total Page:16
File Type:pdf, Size:1020Kb
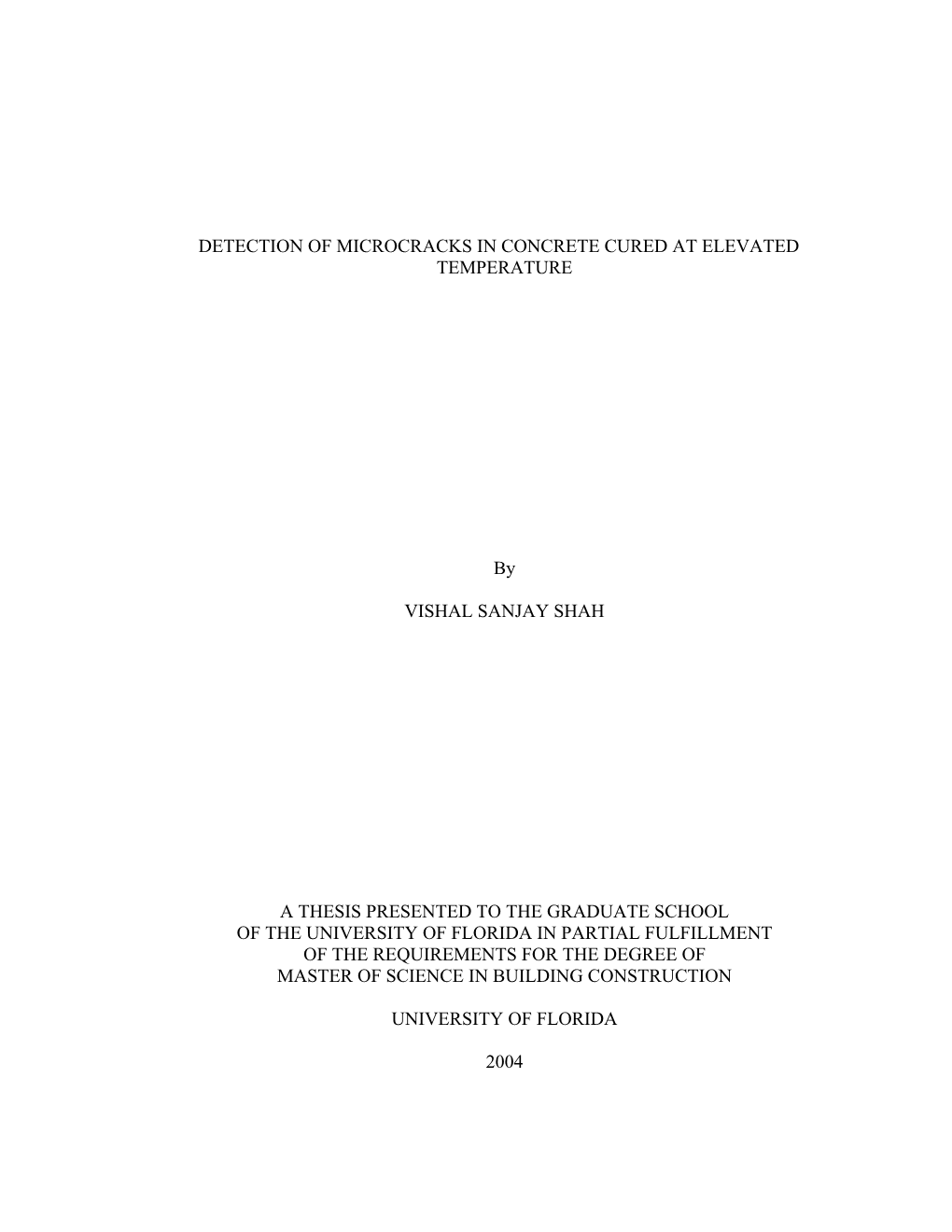
Load more
Recommended publications
-
What Is Polished Concrete?
THE BENEFITS AND BEAUTY OF POLISHED CONCRETE TRAINING OVERVIEW What is Polished Concrete? Different Applications of Polished Concrete Problems with Conventional Flooring Benefits of Polished Concrete-A Summary Floor System Options WHAT IS POLISHED CONCRETE? Polished concrete is a process which enhances the natural beauty of existing concrete by hardening and polishing the concrete. There are two primary methods to creating this shine: Topical or Mechanical. The aesthetic value of these two processes are not equal, and it is important that customers understand this. •A Topical Polish is an inexpensive process that will give the surface of the concrete a smooth, sealed appearance. The concrete will retain it’s course texture, and any inconsistencies in the surface will remain visible. •A Mechanical Polish will grind and seal the surface of the concrete, giving the appearance of a rich stone-like finish with a deep sheen luster. The surface will be flattened, and ground smooth to remove any course texture or ridges. MECHANICAL POLISHING • A mechanical grinding and polishing process that utilizes industrial diamond tools and penetrating chemical hardeners to level, densify, polish & seal the concrete floor surface. • Mechanical polishing offers clients a deep, rich luster finish, a flattened surface, and a glossy appearance. MECHANICAL POLISHING Summary of Benefits-Mechanical Polishing • Competitive first cost • Low annual maintenance cost • Low life cycle cost • Ideal for new construction or restoration projects • Little down time during -
Polished Concrete GC Checklist and Client Agreement Form
Process and Procedures The owner, architect, superintendent, or owner’s representative must be present for sign off approvals at 3 stages: sample approval, walk through approval, and final approval. Absence of representation represents a forfeit to augment the sample and subsequent install. Absence of a signature followed by request to change the finished product will incur an additional fee. Process overview: 1. Approval estimate 2. Properly contract and all documentation turned in 3. Contractor/owner to read and abide by GC Checklist 4. Schedule RBC start date a minimum of (4) weeks in advance 5. Change of schedule issued by “Contractor” is subject to RBC next availability 6. Change in scope, work order or PO will be subject to an approved change order either onsite or issued by either parties office and agreed upon by both parties. Change orders are subject to re-scheduling 7. Arrange to be present or to have alternate decision makers as indicated below for sign offs of sample approvals, walkthrough/progress approvals, and final inspection approvals. Failure to do so will be subject to procedures indicated below. 8. Unless otherwise noted, all installations are final and do not require, nor have they been estimated for a re mobilization. Request to return post installation will be charged accordingly. 9. Post installation flooring must be cleaned using RBC General Cleaner or written approval substitute. Failure to do so will void your warranty unless otherwise stated. It is mandatory that the end user be given this warranty info and any retained cleaning supplies governed by RBC warranty regulations. -
Polished Concrete Flooring Projects Surge
ARTICLE REPRINT Construction Specifier May 2016 POLISHED CONCRETE FLOORING PROJECTS SURGE CSA-based cement products Portland cement has been the standard for many years, but it always brings certain challenges. It shrinks excessively, cannot be accelerated without negative effects, can be susceptible to attack by prevalent chemicals, and reacts destructively with certain aggregates. Using calcium products based in calcium sulfoaluminate cement can help solve these problems. CSA cements are manufactured with similar raw materials, equipment, and processes used to make portland cement. The chemistry includes Corning Museum of Glass – Corning, NY calcium sulfoaluminate (C4A3S) and dicalcium silicate (C2S). The C4A3S compound hydrates to Projects throughout the United States showcase form beneficial ettringite—a strong, needle- how construction materials are playing a like crystal that forms very quickly to give supporting role in industries where new technology the material its quick-setting and high-early- rollouts, tight timelines, and sustainable design are strength properties. “ the new norm. Fast-setting, calcium sulfoaluminate Calcium (CSA) cement-based products are increasingly Another significant aspect of the chemistry is the key to achieving demands for both new and the absence of tricalcium aluminate (C3A), which sulfoaluminate renovated construction. would be present in portland cement and makes that material susceptible to sulfate attack. The Constant implementation of new technologies fact CSA cement products have little or no C3A (CSA) cement- means less standardization across industries makes it very durable in sulfate environments. and greater uniqueness on the jobsite. Unfamiliar workflows and logistics, unusual jobsite When CSA cement is used in concrete, it provides based products are conditions, and untried building systems are day- superior performance in terms of rapid strength to-day realities. -
Polished Concrete an in Depth Design to Understanding the Process for Better Design and Implementation 1
Polished Concrete An In Depth Design to Understanding the Process for Better Design and Implementation 1- Friday, December 7, 12 Copyright Material This presentation is protected by U.S. and International Copyright laws. Reproduction and/or use is strictly prohibited. Concrete Polishing Association of America 2012 © 1- Friday, December 7, 12 ConcreteConcrete PolishingPolishing AssociationAssociation - IntroductionIntroduction 1- Friday, December 7, 12 Board of Directors Chemical Manufacturers Greg Schweitz L&M Chemical Company Scott Metzger Metzger / McGuire Joe Reardon Prosoco Equipment Manufacturers Eric Gallup Substrate Technology Marcus Turek SASE Company Stephen Spengler Aztec Products 1- Friday, December 7, 12 Dye / Stain Manufacturers • Carl Cabot American Decorative Concrete Abrasive Manufacturer • Jeff Tchakarov Diamond Tool Supply, Inc. Architectural Representative • Walter Scarborough Hall / Building Information President-CSI Dallas Chapter 1- Friday, December 7, 12 Board of Directors- Contractor Members • Roy Bowman Concrete Visions Inc. (Chairman) • Leonard Hartford Carolina Concrete Floor Polishing (Co-Chair) • Shawn Halverson Surfacing Solutions (Secretary) • Shawn Weaver Concrete Floor Systems (Treasurer) • Scott Truax Middle Georgia Concrete • John Jones Budget Maintenance • Mike Payne Mike Payne & Associates • Leonard Hartford Carolina Concrete Floor Polishing • John Wucinich Finial Finish • Tim Burgess Burgess Concrete 1- Friday, December 7, 12 Over 400 contractors throughout • Alberta • Saudi Arabia • USA • Trinidad -
Download Manual
INDUSTRIAL TILE AND PAVER APPLICATIONS TECHNICAL DESIGN MANUAL LATICRETE Technical Services Department Globally Proven Construction Solutions Cover Photo: Vintage copper kettle in brewery - Belgium Photo Courtesy of Tatiana Popova © 1998, 2011, 2020 LATICRETE International, Inc. All rights reserved. No part of this publication (except for previously published articles and industry references) may be reproduced or transmitted in any form or by any means, electronic or mechanical, without the written per- mission of LATICRETE International, Inc. The information and recommendations contained herein are based on the experience of the author and LATICRETE International, Inc. While we believe the information presented in these documents to be correct, LATICRETE International and its employees assume no responsibility for its accuracy or for the opinions expressed herein. The information contained in this publication should not be used or relied upon for any specific application or project without competent examination by qualified professionals and verification of its accuracy, suitability, and applicability. Users of information from this publication assume all liability arising from such use. Industrial Tile and Pavers Applications– Technical Manual ©2020 LATICRETE International, Inc. 2 Industrial Tile and Paver Applications – Technical Design Manual Contents SECTION 1 INTRODUCTION ....................................................................................................................................9 1.1 Preface 1.2 Industrial -
High-Gloss Finishes, Creating New Floors with Polished Concrete
Creating new floors with polished concrete Special Reprint ith advancements in concrete surface treatments, polishing equipment, and Wconcrete coloring materials, the best features of classic terrazzo and other hard floor surface finishes can now be attained in contemporary polished concrete flooring. Diamond polishing as a finish is a relatively recent concept for the construction industry. Just over a decade ago, diamond-grinding equipment was primarily used as a surface prep tool for concrete floors prior to the by Howard Jancy, CSI, CDT, and application of epoxy and urethane coatings. Greg Schwietz, CSI, CDT Versions of the same equipment were also used for polishing marble and other stone tile floors. With rapid advancements in abrasive diamond technology and the availability of more reliable and durable equipment, the final ingredient—a chemical hardener—was added The walkway of this fitness center is to make the expense of diamond polishing a polished concrete with single-dye color. It is a non-slip, 'high-traction' floor, a viable option in terms of service life and low certification made by the National Floor maintenance costs. Almost immediately, Safety Institute (NFSI). creating an attractive, high-gloss surface requiring a minimum of ongoing maintenance became the desire of many building owners. Polishing is suitable for refurbishing old concrete flooring or producing new durable, low-maintenance, high-gloss installations. This process provides design professionals with a cost-effective flooring option that can accommodate tight budgets and creative design. As such, it can be found in schools, retail stores, public buildings, and malls, as well as high-traffic warehouses and industrial buildings. -
Eco-Friendly Product ARCHITECTURAL & DECORATIVE
ARCHITECTURAL & DECORATIVE CONCRETE Eco-Friendly Product JK WHITE CEMENT CEM I - APPLICATION ISO 9001 ISO 14001 BUREAU VERITAS Our product complies to : Certification CEM I - 1922 - CPR - 0353 CEM II - 1922 - CPR - 0417 ISO 9001 : 2008 & ISO 14001 : 2004 Certified Company !"#$$%&'()*%+)',-.*/)0%1.,/*)2)% Introduction ‘If you want something new, you have to stop doing something old’ Concrete is one of the most widely used construction materials in the world. One special subset is called architectural and decorative concrete, which refers to a substance that provides an aesthetic finish and structural capabilities in one. This material is made to be seen. Whether creating broad expanses or minute details, concrete permanently captures the chosen look. Achieving an architectural or decorative appearance usually requires that something different be done to the concrete. Whether that involves special forms, spe- cial finishing techniques, or special ingredients, the variety of effects is almost unlimited. rchitectural and Decorative Concrete with JK White Cement :- A Decorative concrete is the use of concrete as not simply a utili- tarian medium for construction but as an aesthetic enhancement to a structure, while still serving its function as an integral part of the building itself such as floors, walls, driveways and patios. The transformation of concrete into decorative concrete is achieved through the use of a variety of materials that may be applied during the pouring process or after the concrete is cured, these materials and/or systems -
Setting a Standard for Decorative Concrete the ACI’S New Guide Shows What’S Possible and Tells Contractors How to Accomplish It
42 D+D AUGUST 2014 Decorative concrete requires special materials and methods to achieve a consistent, high-quality aesthetic finish. Here, a mix of integral color and penetrating, reactive stain turns concrete into a design element at the Morton Arboretum, Lisle, Ill. Photo courtesy of Butterfield Color. Q+ Got a concrete problem? Concrete A Ask the experts: [email protected]. Setting a Standard for Decorative Concrete The ACI’s new guide shows what’s possible and tells contractors how to accomplish it. By Jamie Farny, Portland Cement Association, colored concrete can amount to more than 30 percent in some and Larry Rowland, Lehigh White Cement Co. major metropolitan markets. Some ready-mix concrete producers add pigment to 50 percent or more of their products. Q: What can I offer customers to help their concrete projects re- Yet many installers remain unaware of decorative concrete’s po- ally stand out — and help my business stand apart from the tential or don’t know proper installation methods. Owners may not competition? get the results they seek. Some find decorative concrete cost-pro- Decorative concrete is often described as one of the fastest grow- hibitive. ing segments of the concrete industry. While estimates are un- Recognizing these knowledge gaps, in December the American available for the overall quantity of decorative concrete installed, Concrete Institute (ACI) published a comprehensive guide to the 43 Concrete Q+A materials and methods used to produce decorative concrete finishes. With input from all segments of the industry, ACI Committee 310, Decorative Concrete, de- veloped the 45-page Guide to Decorative Concrete (ACI 310R-13) on materials and techniques for imparting aesthetic finishes to concrete flatwork. -
1. Concrete Masonry Units 2. Glazed Units 3
SECTION 04 22 00 CONCRETE UNIT MASONRY PART 1 GENERAL 1.1 SUMMARY A. Section Includes: 1. Concrete masonry units 2. Glazed Units 3. Reinforcement, anchorages, and accessories. 4. Procedure and preparation for exposed concrete 5. Observation and Required Special Inspections 6. Mock up panel B. Products Installed but not Furnished Under this Section: 1. Section 03 21 00 - Concrete Reinforcement 2. Section 05 50 00 - Metal Fabrications: Loose steel lintels. 3. Section 07 62 00 - Sheet Metal Flashings and Trim. C. Related Sections: 1. Section 01 40 00 - Quality Control: Required Special Inspections 2. Section 03 30 00 - Cast-In-Place Concrete: grout. 3. Section 04 05 13 - Mortar 4. Section 07 27 26 - Fluid-Applied Weather Barrier System 5. Section 07 19 00 - Water Repellent Coating 6. Section 07 21 00 - Insulation 7. Section 07 92 00 - Joint Sealers: Rod and sealant at control joints. 8. Section 09 91 00 - Painting and Finishing. 9. Section 09 97 26 - Special Coatings 1.2 REFERENCES A. ASTM C90 - Hollow Load-Bearing Concrete Masonry Units. B. ASTM C145 - Solid Load-Bearing Concrete Masonry Units. C. Hot and Cold Weather Masonry Construction Guide - Recommended Practices and Guide Specifications for Hot & Cold Weather Masonry Construction. D. ASTM A153 – Zinc Coating (Hot Dip) 1.3 PERFORMANCE REQUIREMENTS A. Provide unit masonry that develops the following installed compressive strengths (fm) at 28 days. 1. For Concrete Unit Masonry: As follows, based on net area: a. F’m = 2000 psi (13.1 Mpa). 04 22 00-1 City of Bentonville Animal Services Bentonville, AR 1.4 SUBMITTAL A. -
Param SSL Semi Self-Leveling Concrete Topping (Over Gypsum / Lightweight Concrete Toppings)
Param SSL semi self-leveling concrete topping (over gypsum / lightweight concrete toppings) DESCRIPTION INSTALLATION STEPS Param SSL is Portland cement based semi self-leveling concrete PRIMING topping when mixed with water produces a unique high strength ■ Prime the substrate with CP1000, acrylic primer. It must be flooring surface. It is designed to resurface existing concrete applied over entire substrate that is at least at 50°F. or any hard wearing surface like ceramic, vinyl tiles or gypsum ■ Apply with a garden sprayer and then spread with a broom or based underlayments. Param SSL can be trowelled and burnished mop to assist complete coverage and penetration. to create a smooth hand applied polished concrete floor. It is ■ designed for residential and commercial interior spaces. Param At least two coats of primer are recommended allowing 6 to 8 SSL can be integrally colored with Colorfast or Dyes. hours between the coats. Porous substrate like gypsum based underlayments may need at least 3 coats of CP1000. ■ An incorrectly primed surface may result in pinholes in Param ADVANTAGES SSL and cause accelerated and incomplete hydration. ■ Creates a real concrete look and feel ■ MIXING & INSTALLATION Applied at only 1/8” thick – adds very little weight to the ■ Mix 4.6 liters of CP1000 with 1 bag of Param SSL. The water structure requirements may vary slightly depending upon the ambient ■ Can be integrally colored with Colorfast temperature and humidity. ■ ■ Achieves excellent results with chemicals stains (acid stains), Integral color Colorfast can be mixed with Param SSL. Adding dyes or water based stains more than 2 cups of Colorfast per bag of Param SSL may result in undesirable outcomes. -
Drafting an Understanding of Densified and Polished Concrete” (ICC09E) Presentation Notes
“Drafting an Understanding of Densified and Polished Concrete” (ICC09E) Presentation Notes Slide 1: Title Slide Slide 2: Course Description Slide 3: Learning Objectives Slide 4: What is Concrete? Take a little bit of rock, sand and water, add some cement and you’ve produced just about the most natural flooring and building product available. What was good enough for the Romans over 2000 years ago is still good enough for us today. Concrete is a mixture of cements (11%), course aggregate (41%), sand (26%), water (16%), and naturally entrapped air (6%). Additives may be included in the mix design to enhance certain properties. Focus will be on the most standard flooring mix design – ASTM C150 Type I for portland cement. It is important to be aware of all negative ramifications when including admixtures to a mix when densifying and polishing. Admixtures benefits range from improving strength, workability and cure time, to enhancing waterproofing and aesthetics. For polished concrete, it is important not to include air entrainment, and to minimize the amount of fly ash replacement for cement. Note: You can’t polish air, and fly ash extends the strength gain out to as much as 90 days, in addition to altering the color and having reduced workability Slide 5: Concrete Flatness and Finishing Help Determine the Final Outcome Finishing techniques, screeding techniques (laser screed vs. manual screed), edge finishing vs. machine finishing, and flatness of the concrete all influence the final outcome of the polished concrete. Slide 6: Concrete Flatness Determines the Overall Look and Aggregate Exposure (1) The flatness of the concrete directly influences the outcome of the grind and polish. -
Taking the Measure of Polished Concrete
8 D+D NOVEMBER 2014 Testing + Evaluation Taking the Measure of Polished Concrete A new standard may hold the key to uniformity in polished concrete floors. easure what it has not been able to precisely define By Christopher Bennett, is measura- the polish level on any proven, accept- ble, and make able, repeatable scale. Husqvarna measurable This means that a specified 800-grit “ what is finish, for example, can vary widely in not so.” appearance from one floor to another, That advice based on diamonds used, or even finish comesM from Galileo, often noted as the fa- coats. Whether or not the contractor has ther of modern science. actually delivered the 800-grit finish has Unfortunately, this sound guidance has sometimes been a matter of opinion and not always been heeded in the exposed even legal dispute. concrete flooring industry. The Concrete Sawing and Drilling As- Many products and systems claim to sociation (CSDA) believes that gloss lev- solve the persistent problem of varying, els shouldn’t be a matter of opinion, but unpredictable results on polished con- should be based on measurable, quantifi- crete floors. There’s little “concrete” able standards. evidence, however, to support one manu- To that end, the organization pub- facturer’s claim versus another’s. lished CSDA ST-115 in October 2013, a “Grit” is often used to rate gloss val- quantitative standard on measuring ues of polished concrete floors. It’s been roughness averages (Ra). The idea is that the main method for communicating de- such a standard can help design profes- sign intent for well over a decade.